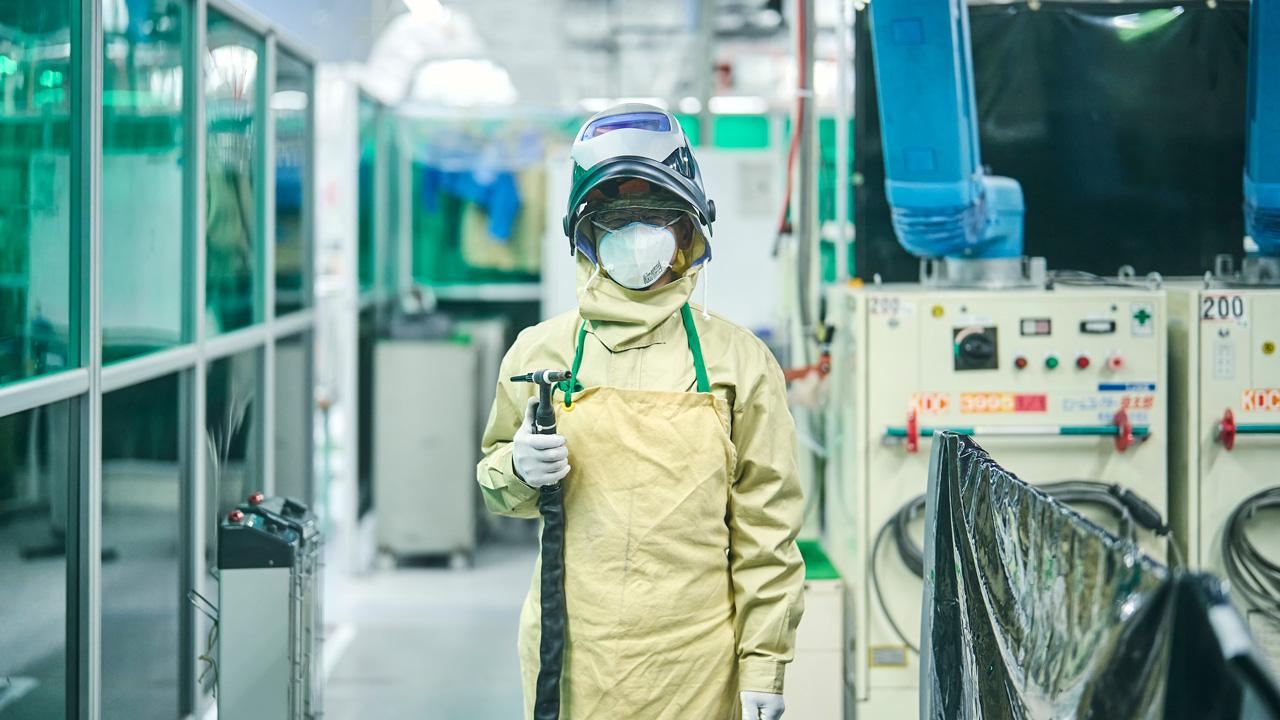
This is an ongoing series looking at the master artisans supporting the automotive industry. The 13th installment two-part article features an interview with a master welder using self-taught skills to join metal plates and aluminum through skillful use of temperatures over 5,000 degrees Celsius.
Welding apprentices working worldwide
Miki attracts student staff not just from plants around Japan, but around the world, who come to learn the very pinnacle of welding skills.
As we mentioned in part 1, Miki's specialty is press mold buildup welding, an essential technique for pressing body panels. Toyota has manufacturing lines pressing out body panels at plants all over the world, which means that those global plants have welders who need the skills he has to teach.
There is a world map on the wall of the Monozukuri Staff Development Center with dozens of photographs of students who have taken lessons from Miki and other instructors there, then went off to work all over the world.
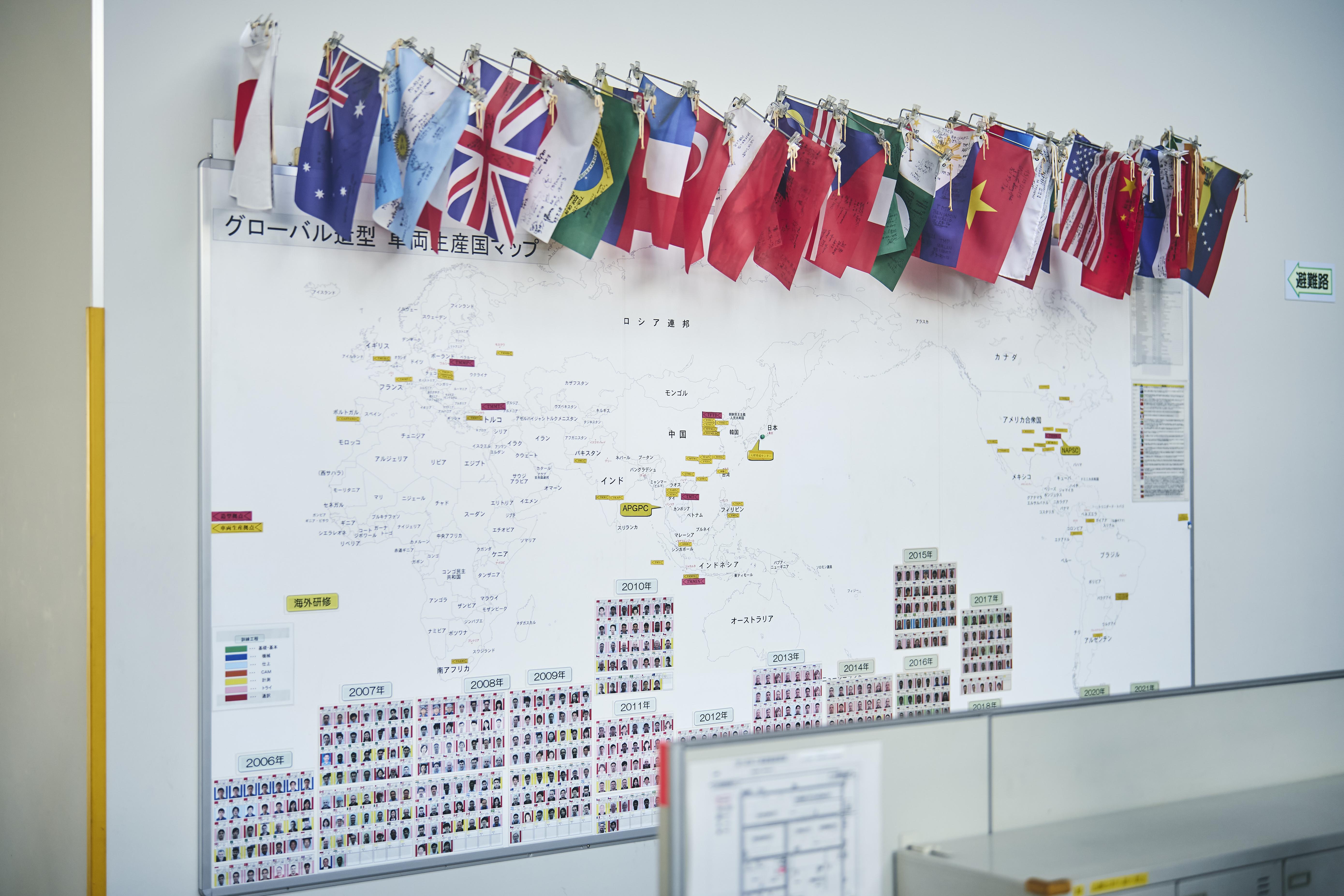
Miki has also had extended assignments assisting and teaching at overseas plants.
In 2010, he was stationed to teach at Toyota Argentina, and in 2012 he taught at Toyota Thailand.
All of this means that Miki has hundreds of apprentice welders active all over the world.
The most interesting job in the world
As an active trainer, Miki still teaches all kinds of welding skills to younger employees in a variety of departments. His work in practical training preserves and passes on the skills he taught himself.
At the same time, he handles inquiries from shops all through the company asking how to handle a certain kind of weld. But soon, he'll reach the retirement age of 65.
Miki
The job that stands out best in my memory is when I welded 3.2mm thick steel plates into a massive pool that was 6 meters long and about 2.5 meters across.
Press molds are finished by hardening through heat tempering, but only part of the mold needs hardening. So, we submerge the mold in the pool and only temper the parts that aren't submerged. That was the reason we needed that pool.
Back then, I was working in the hardening process, and the memory of how well it went is a good one.
Miki has been a welder his whole career since he joined Toyota at age 18, and looking back, he says that there is no job more interesting.
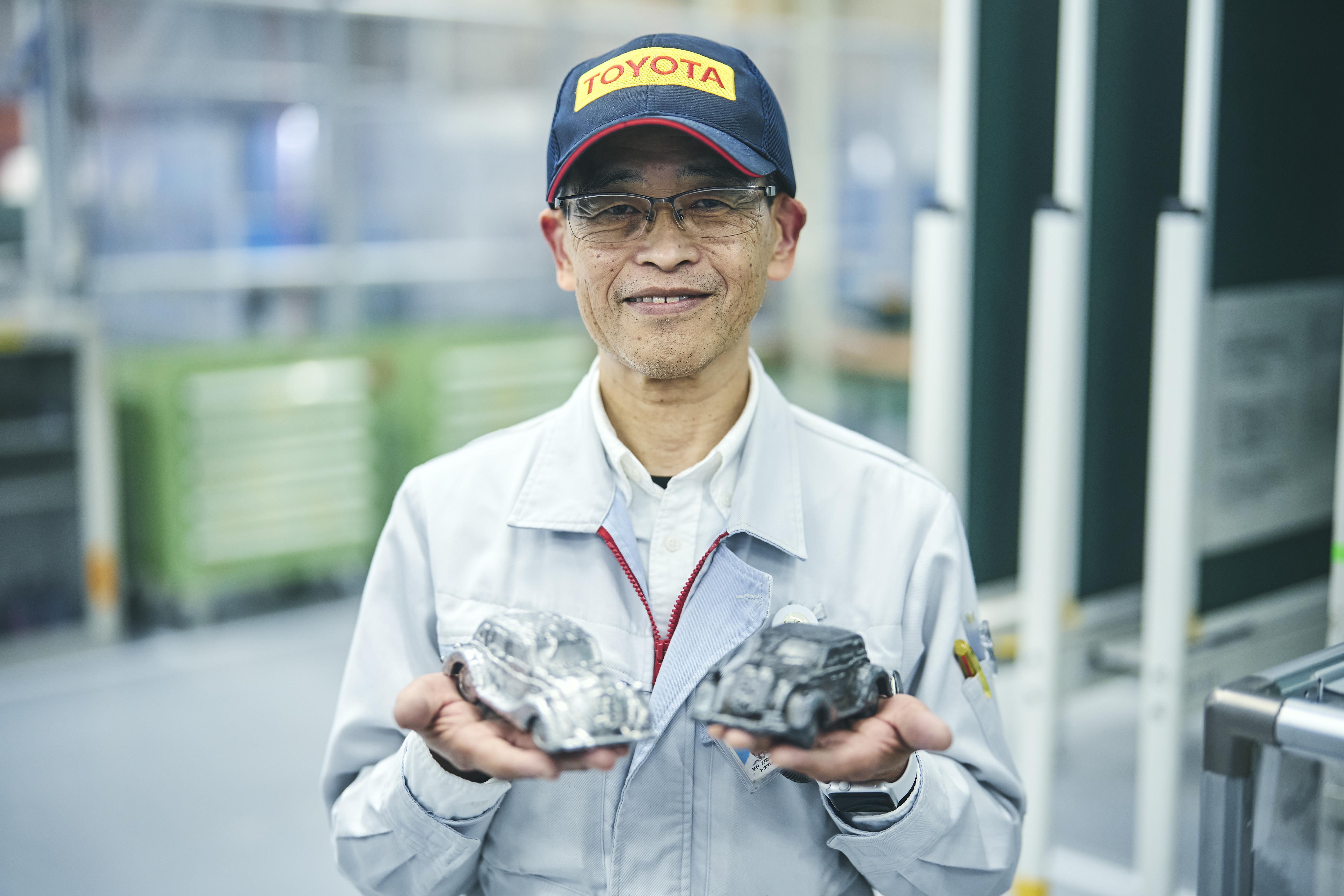
Miki
Welding is taking two pieces of metal and joining them completely. It’s low profile, behind-the scenes work, but there’s no skill more interesting.
Personally, I think it’s the most interesting job in the world. I want more people to know how interesting it is and learn how to do it.
Miki says he is fascinated by metal goods made using welding and tempering skills, like the hand-welded structural components of the TOKYO SKYTREE; railroad cars made through welding skills; and Japanese katana swords, which are finished through skillful tempering.
Miki
I don't think I've reached the pinnacle of welding work. But I do think I've made a good showing as I head into retirement. I love playing guitar as a hobby, and I really like folk music, so I think my next challenge might be the piano. I've already bought one!
All the students Miki has taught during his career as a master welder are out there in the world, and they are sure to keep the craft alive and evolving.
Written by Yasuhito Shibuya. Photos by Ken Takayanagi