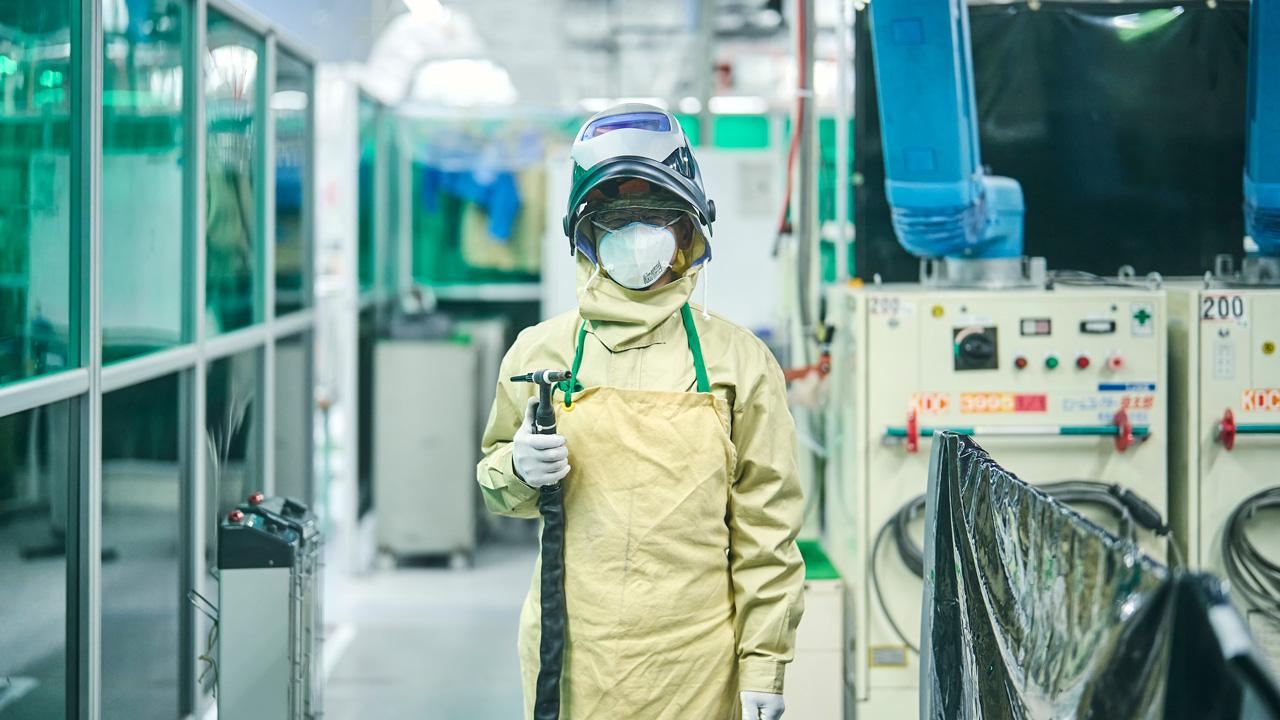
This is an ongoing series looking at the master artisans supporting the automotive industry. The 13th installment two-part article features an interview with a master welder using self-taught skills to join metal plates and aluminum through skillful use of temperatures over 5,000 degrees Celsius.
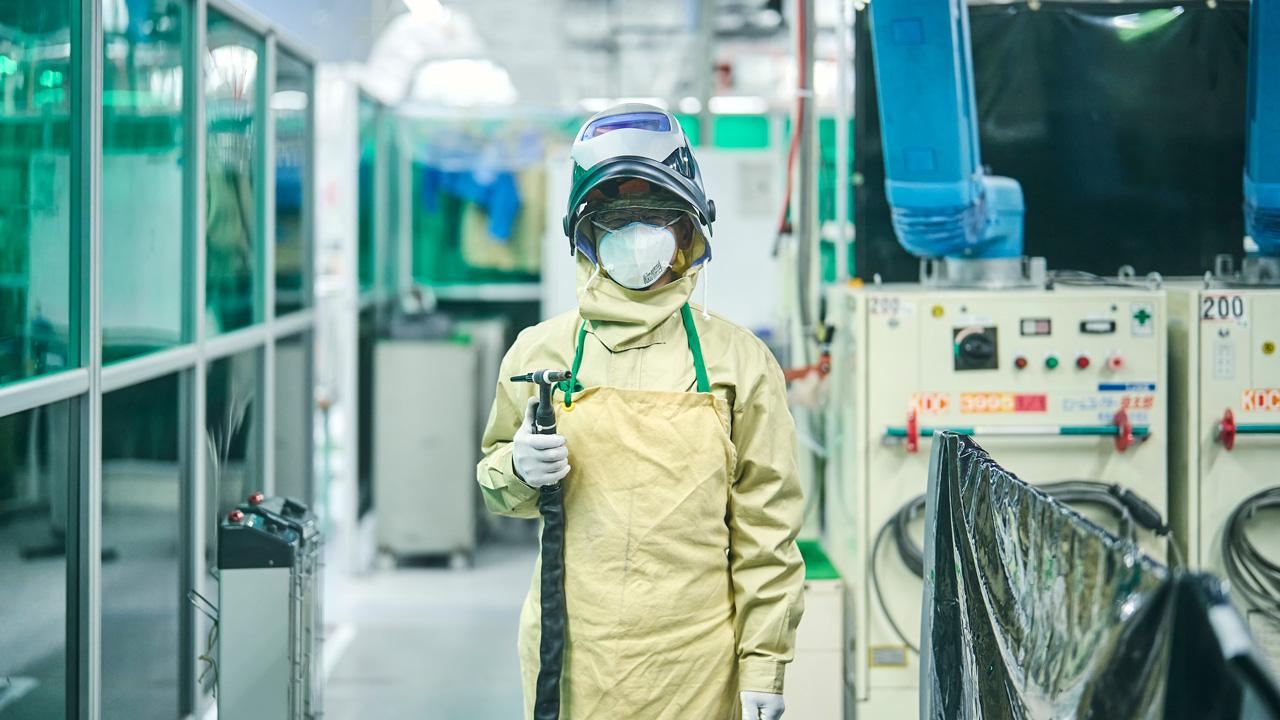
This is an ongoing series looking at the master artisans supporting the automotive industry. The 13 th installment two-part article features an interview with a master welder using self-taught skills to join metal plates and aluminum through skillful use of temperatures over 5,000 degrees Celsius.
These days, advancements in technology like 3D printing or AI are drawing attention, but the carmaking genba is a place where all kinds of manual labor still matter.
This Toyota Times series focuses on craft skills supporting Japanese carmaking by shining the spotlight on the artisans shoring up the automotive industry with craft skills to uncover the essence of traditional Japanese monozukuri (making things).
This time, we continue our introduction of Akira Miki, a master of the welding skills so essential to car manufacturing, and a trainer passing those skills to trainees all over the world.

#13 Master Welder Akira Miki Trains Future Global Welders (Part 2)
Senior expert in the Monozukuri Development Management Division, Skills Training Promotion Group
Full use of sight, hearing, smell, and touch
Miki, a welding senior expert, has been a trainer at the Motomachi Plant Monozukuri Staff Development Center since 2008. There, he trains young welders from all over the world in skills like the press mold buildup welding we discussed in part 1.
We asked Miki to demonstrate that buildup welding for us.
He donned his heat-resistant clothing and gloves and a helmet like something made for an astronaut, adjusted the dials on his welder, and sat at a workbench.
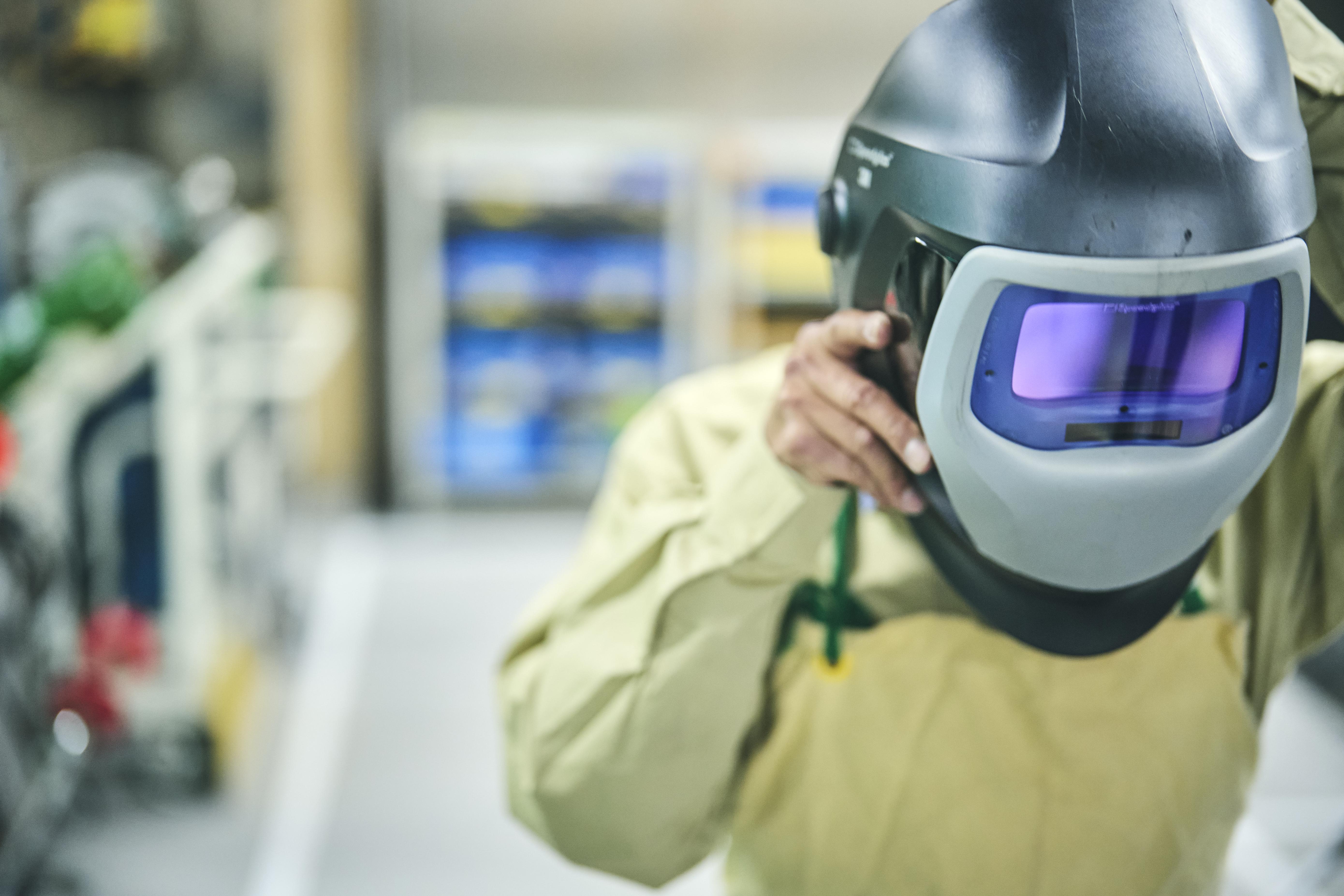
When he brought the welding rod (electrode) into contact with the steel plate and then withdrew it to keep a certain air gap, it discharged an electric arc. We watched through the dark glass of a welding mask as the steel plate and welding rod began to melt at temperatures of 5,000 to 6,000℃, making a pool of molten metal that glowed orange.
Since the light of arc welding is too bright for the naked eye, Miki has to gauge the condition of this molten metal pool through the dark goggles in his helmet as he moves his welding rod from right to left in a regular rhythm, smoothly welding the steel.
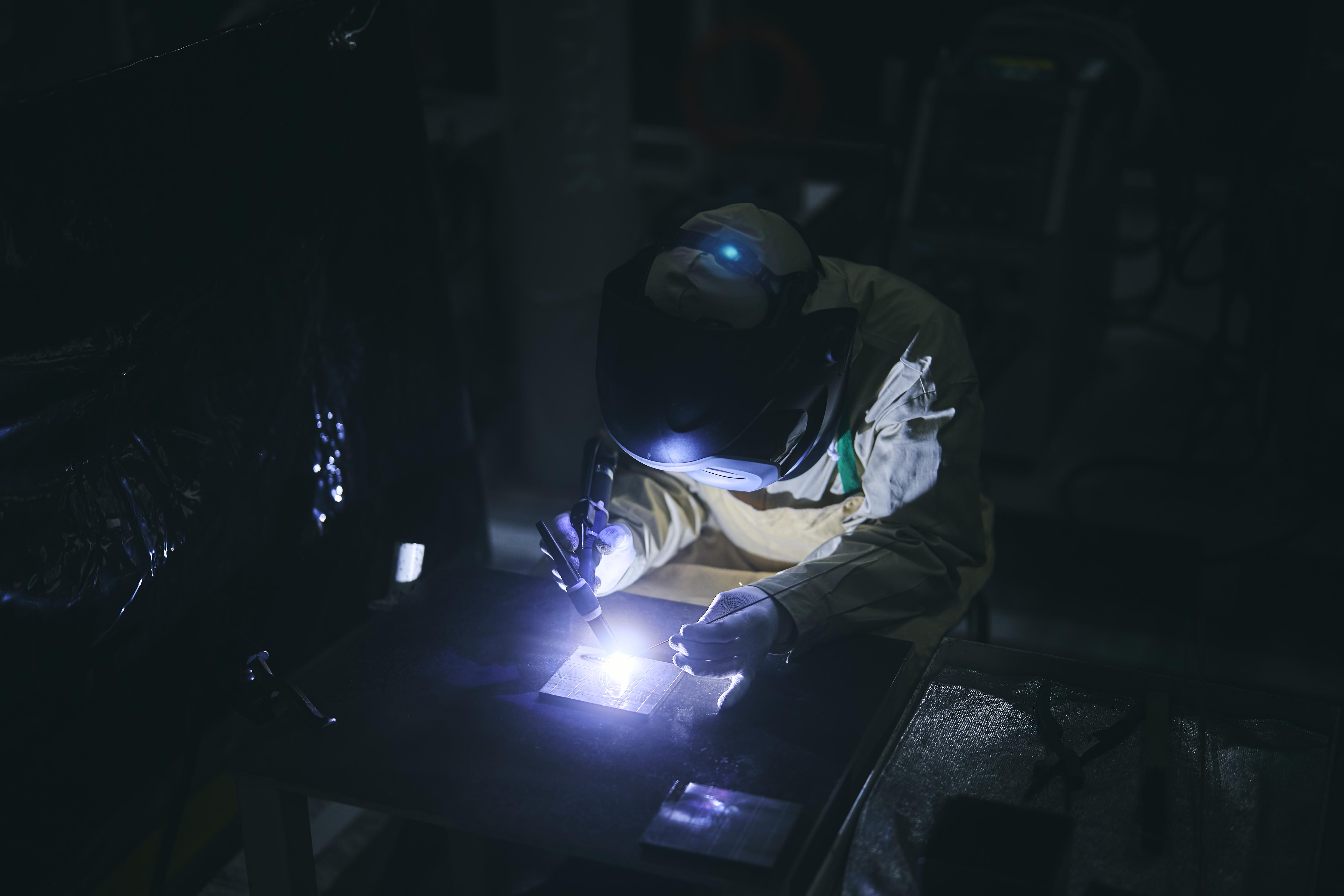
When he finishes, he uses a wire brush to knock away the coarse black slag from the welded section, revealing a smooth, beautifully rounded line of metal called a bead.
A less skilled welder might create slag that looks quite clean, but the bead beneath it will be uneven and the weld defective.
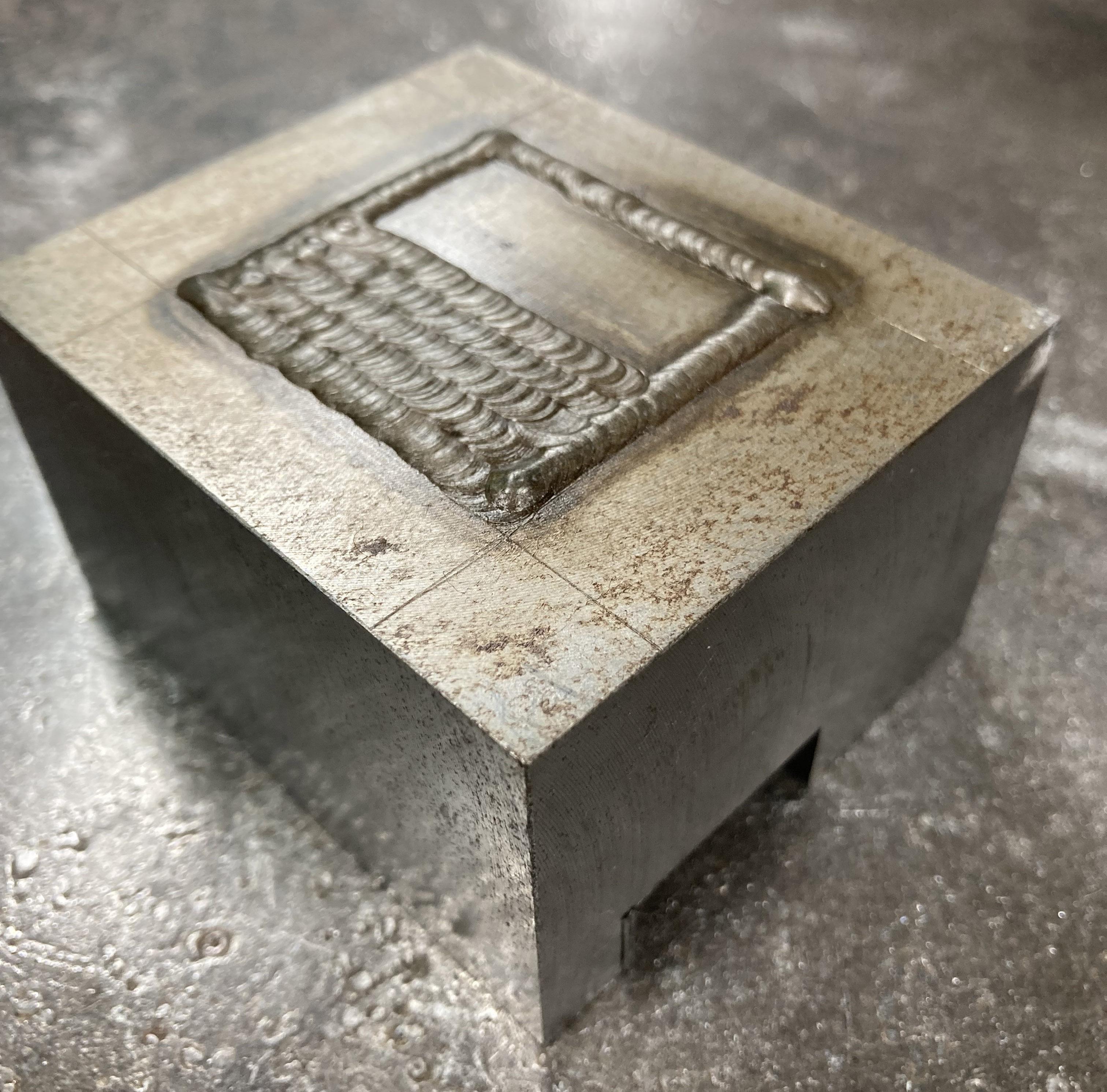
Miki
Changing the electric current levels adjusts the arc discharge intensity, and you have to adjust for the material to be welded, choose a proper rod material, change the angle, and adapt how you move.
From the start, it's difficult to simply melt the material by touching and withdrawing the rod slightly to keep the air gap.
For absolute beginners to welding, I offer clear, simple instructions like "set the current to 120A and touch the rod at an angle of 80 degrees."
The most important part of arc welding is to keep the pool of molten metal and rod even. Raising welding skills requires planning out how to adjust your current and rod angle to keep the pool under control.
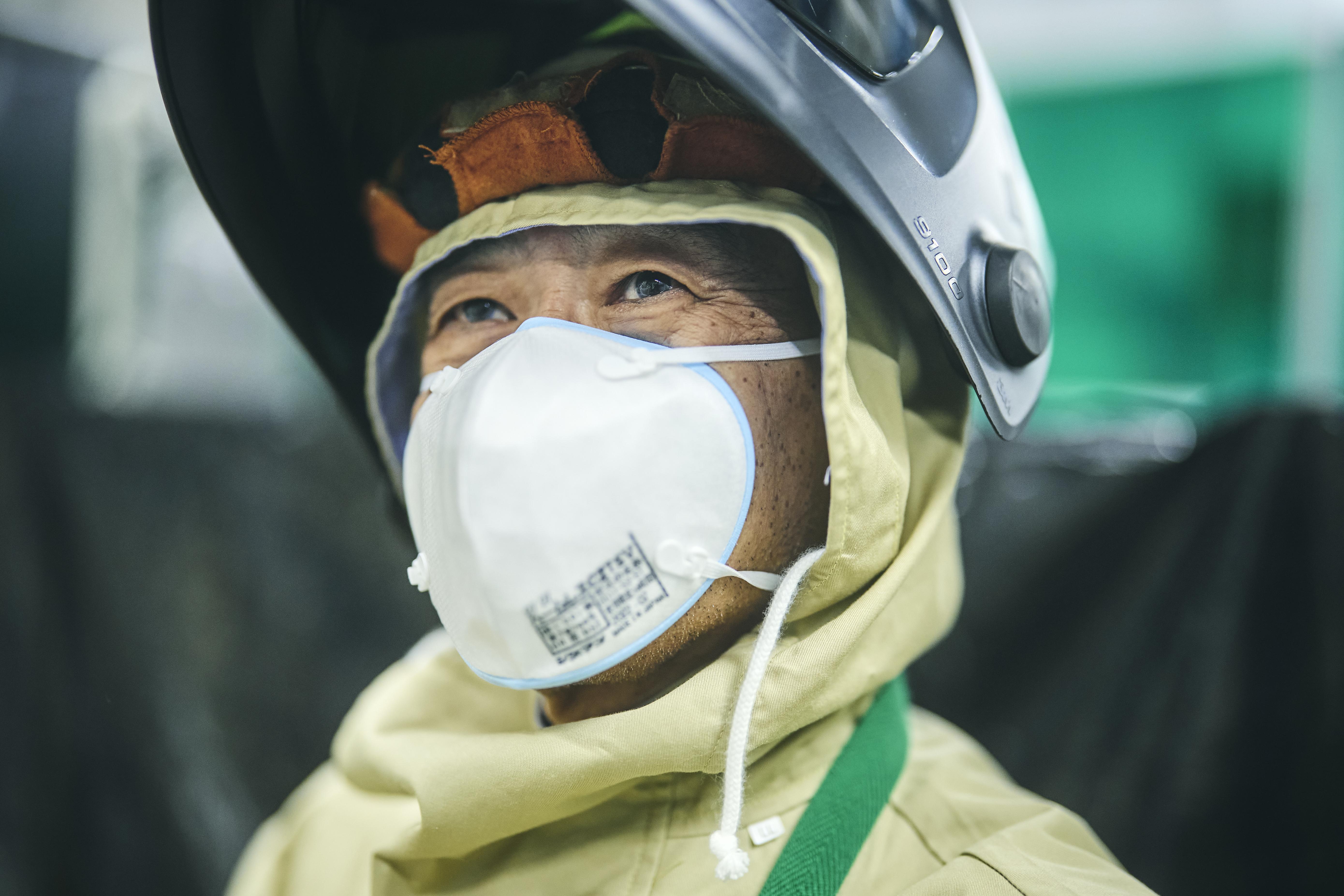
Miki says to be a good arc welder, you have to be able to visualize the pool, and the ability to do that or not is largely a matter of natural aptitude.
There are those who find themselves unable to visualize the pool, no matter how often they try, meaning they will never improve. To do so, it is important to be able to fully use and focus the senses of sight, hearing, smell, and touch on the job.
Miki
Sometimes when I'm welding, I get the sense that it's just not going right. It usually turns out that the material isn't of uniform quality.
Even JIS-certified materials have a wide range of quality. When that happens, you have to adapt how you weld by adjusting the current, the rod material, or how you move.
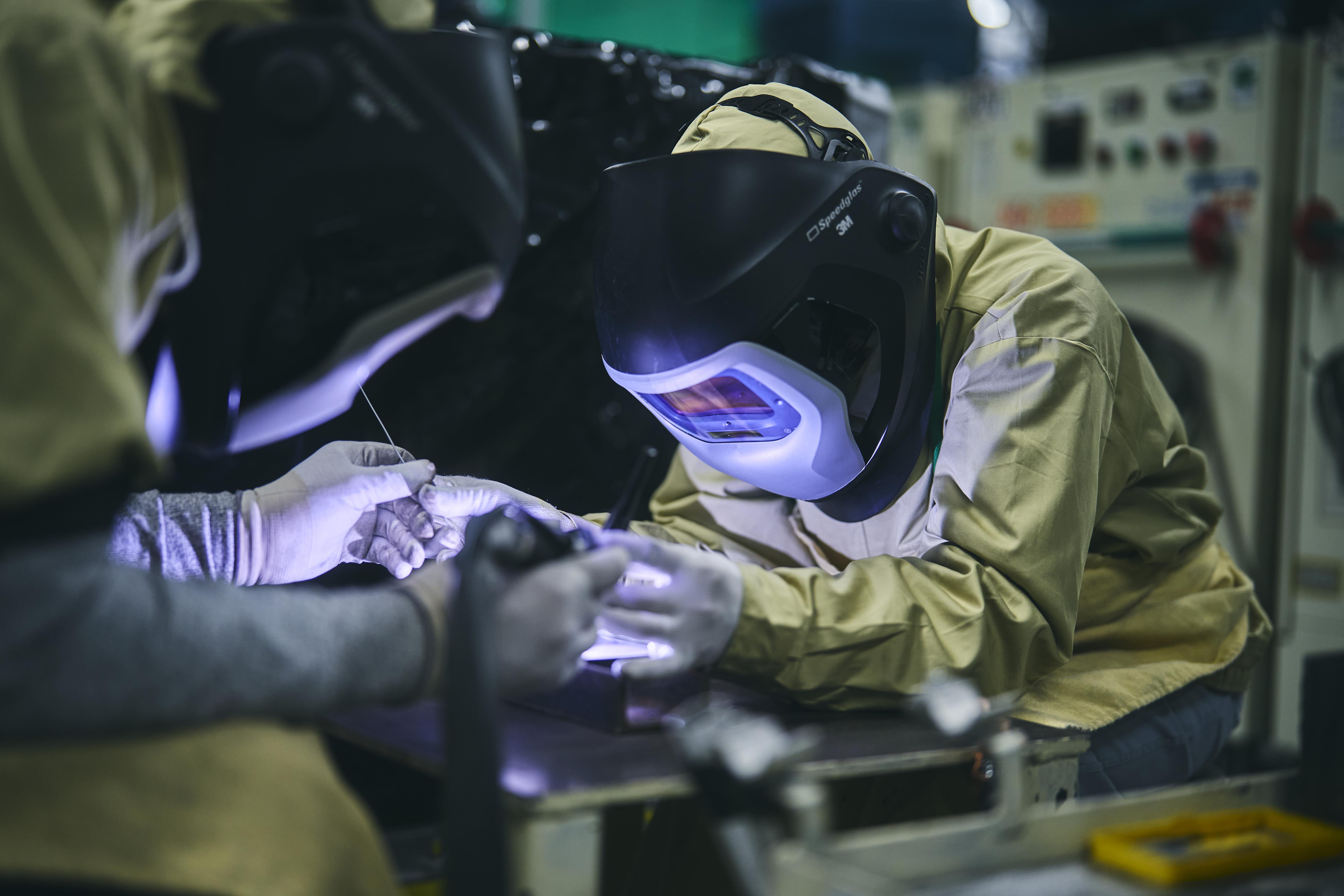
That is most likely because of incredibly tiny variations in the composition or crystalline structure of the surface. But to Miki, those variations can be sensed in the light of the arc, the color of the molten metal pool, and even the subtle sensations felt when the rod touches the metal.
Self-taught aluminum welding skills
Miki also makes sure to acquire new skills in anticipation of ongoing automotive electrification.
First and foremost is aluminum welding. Raw aluminum has a specific gravity 1/3 that of iron, and as electrification advances, it is becoming an even more essential metal.
He taught himself to weld it on his own and started supporting aluminum frame welding in 2018.
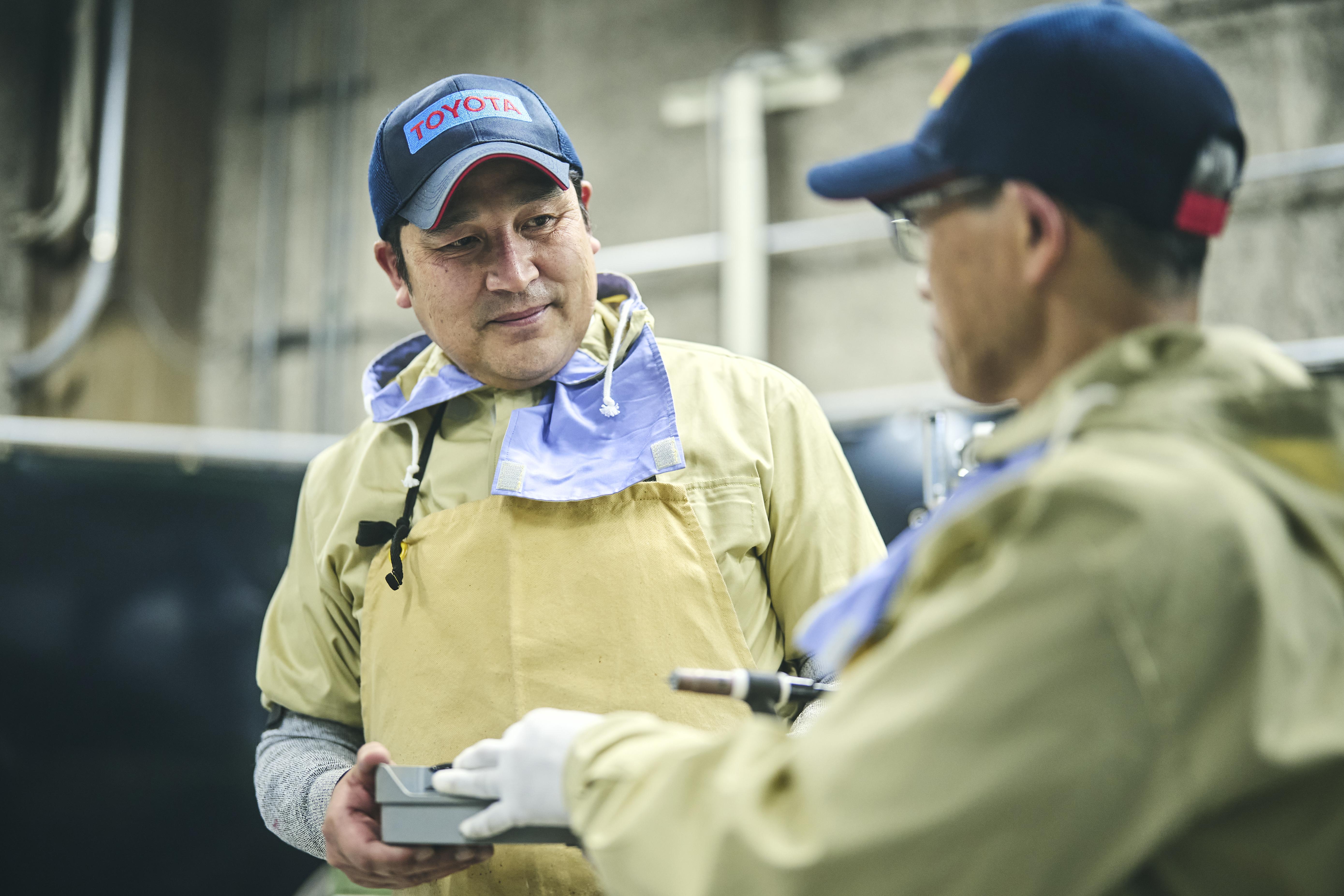
Miki
Welding aluminum is a totally different beast than iron or steel. Iron starts to melt at around 1,500℃, but aluminum melts at around 600℃.
But aluminum is also prone to forming oxidation on its surface during working, and that oxidized film won't melt until 2000℃. That's another complication that steel lacks.
Miki demonstrated aluminum welding along with Shigeru Nakamoto, who joined the Production Engineering Development Management Division in 1992. Nakamoto is a steel sheet welding expert and Miki's named successor.
Nakamoto is also a trainer for steel sheet welding. However, the enormous difference in aluminum welding means he still struggles with it. In this demonstration, his plate melted through and showed a large hole.
On the other hand, Miki's aluminum welding is as perfectly finished as his steel. For a second demonstration, Miki sat across from Nakamoto and guided both his hands through the welding. This time, there was no melt-through, and the finish was superb.
Miki
This is the best way to convey the subtle sense of welding. Ultimately, you just have to learn that the feeling is totally different from steel.
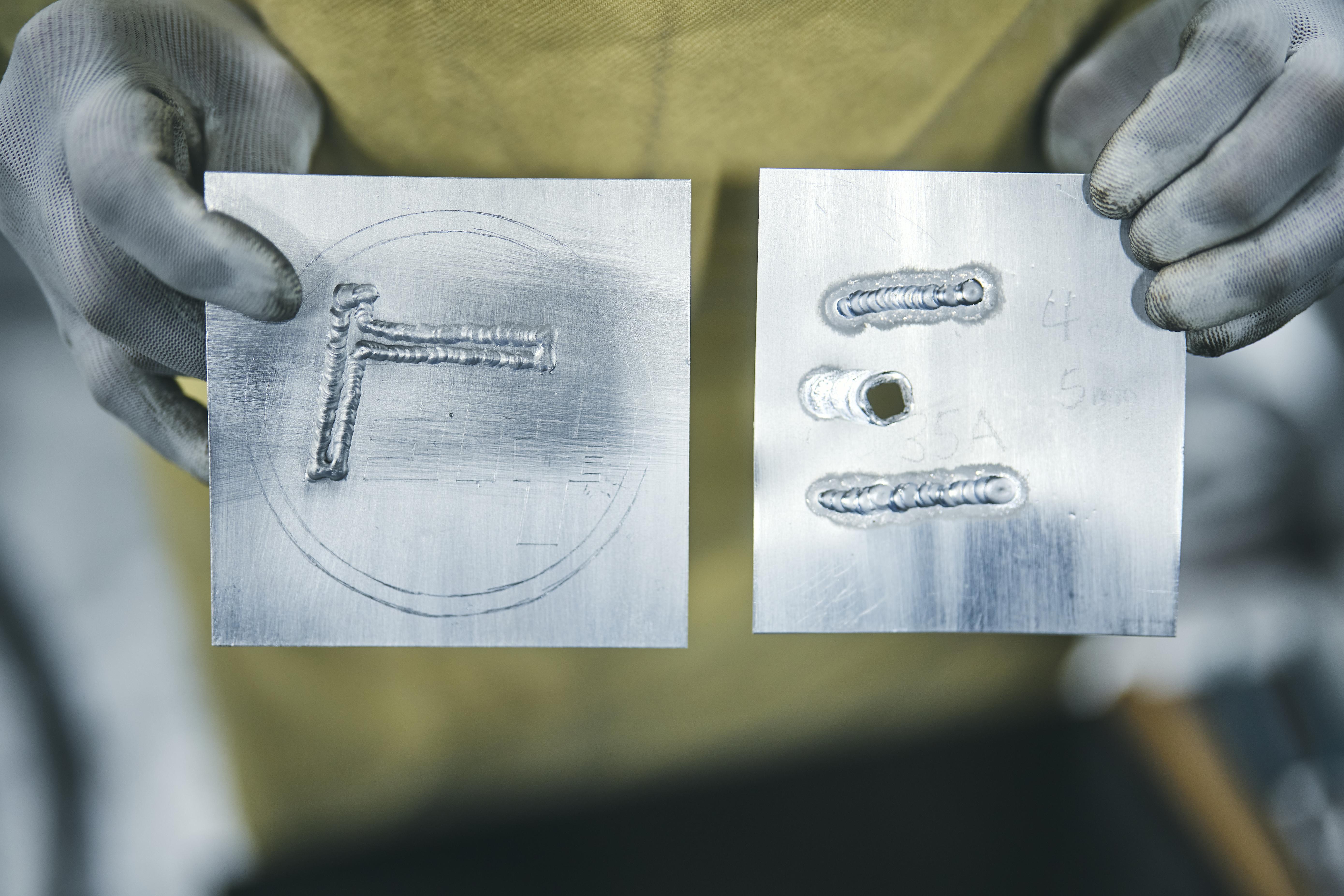
In one hidden corner of the Monozukuri Staff Development Center, in front of the welding booth where he teaches hand welding and finishing techniques, Miki displays astounding works of art produced through his welding skills.
Each one is enough to strike those with any welding knowledge speechless, including the aluminum plate on which he has welded "Toyota Times" in Japanese.
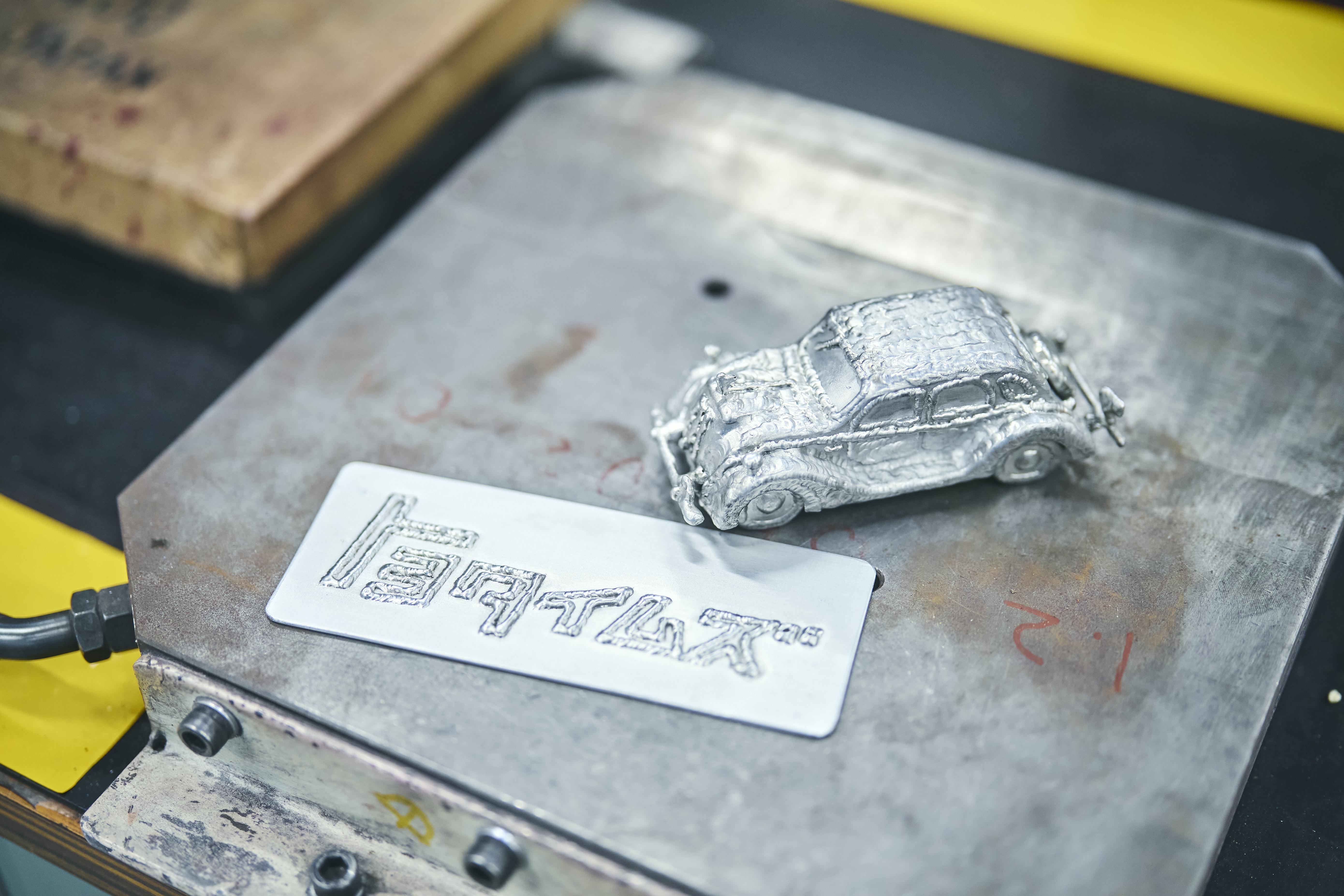