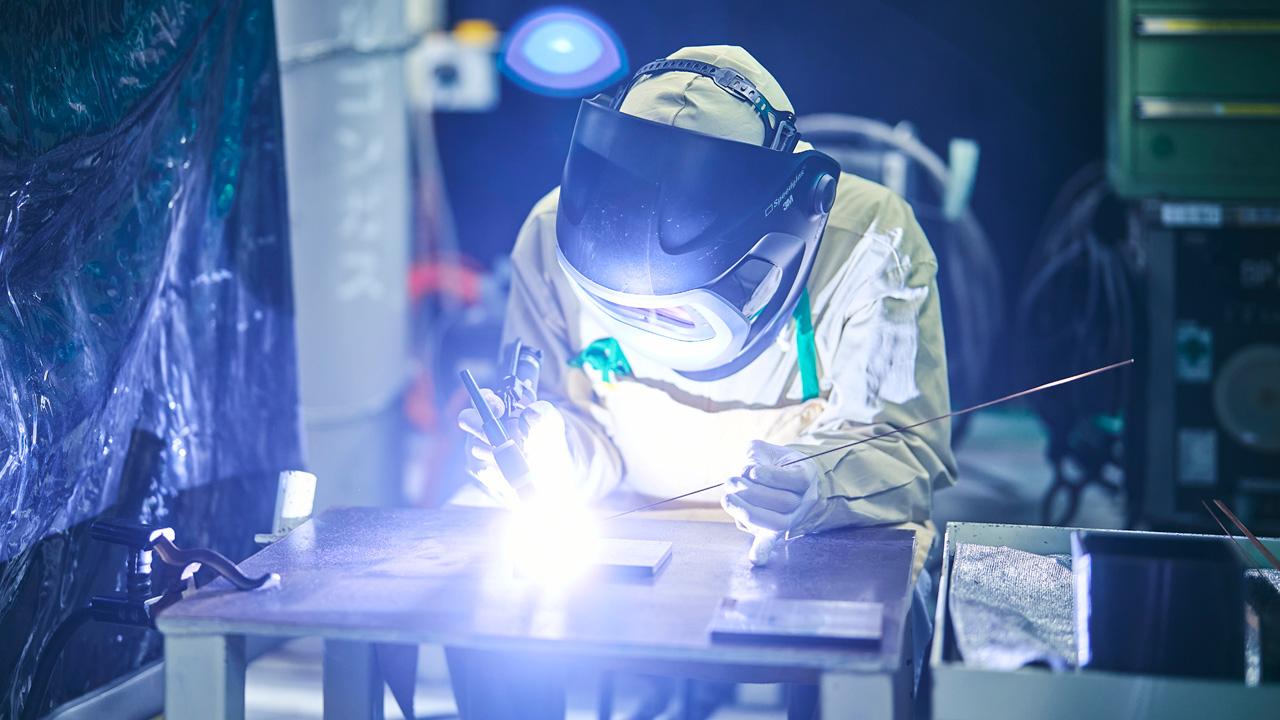
This is an ongoing series looking at the master artisans supporting the automotive industry. The 13th installment two-part article features an interview with a master welder using self-taught skills to join metal plates and aluminum through skillful use of temperatures over 5,000 degrees Celsius.
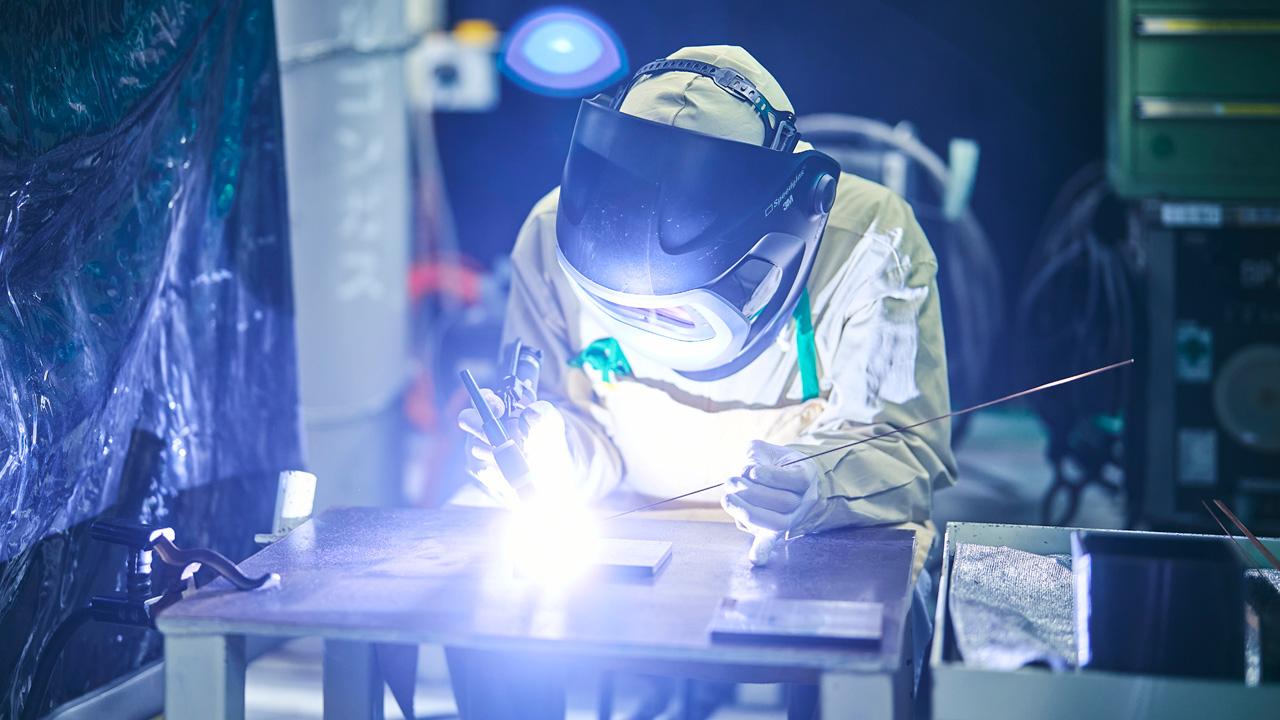
These days, advancements in technology like 3D printing or AI are drawing attention, but the carmaking genba is a place where all kinds of manual labor still matter.
This Toyota Times series focuses on craft skills supporting Japanese carmaking by shining the spotlight on the artisans shoring up the automotive industry with craft skills to uncover the essence of traditional Japanese monozukuri (making things).
Here, we present the first part of the story of Akira Miki, who has mastered welding skills essential for car manufacturing, such as mold buildup welding—which is a technique used to modify dies used in massive presses—and welding aluminum frames.
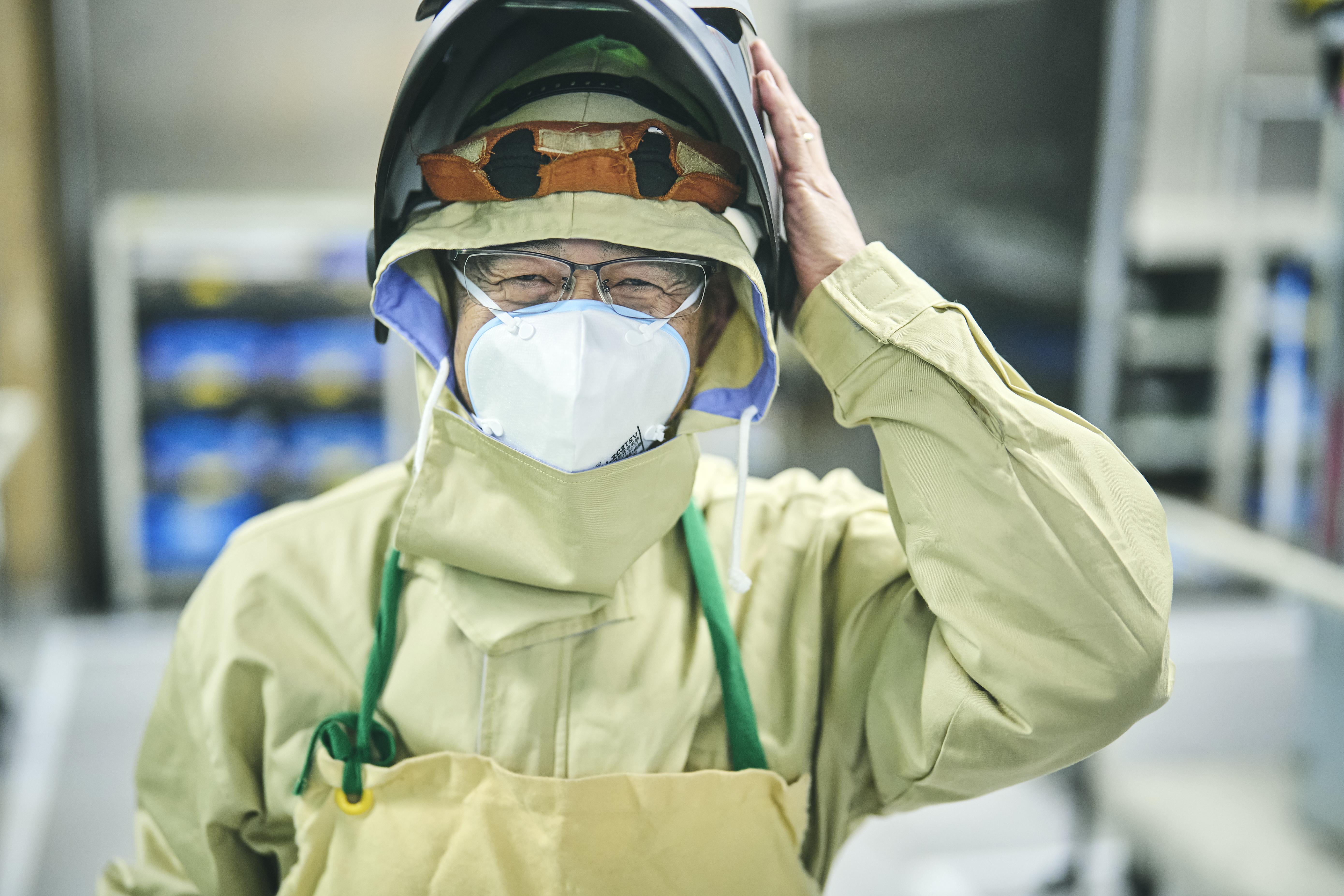
#13: Welding Master Akira Miki Hits 0.1mm Precision at 5000℃
Senior expert in the Production Engineering Development Management Division, Skills Training Promotion Group
Essential carmaking skills
Donning a welding helmet like an iron mask and heat-resistant clothing and gloves, the artisan steps up to his worktable and touches a welding rod to a plate of metal.
With a flash of light too intense for the naked eye, the hard metal around where the rod makes contact begins to glow red and melt. The rod melts with it, shortening as it does. This is welding. It is perhaps the most spectacular of all the many processes of machining.
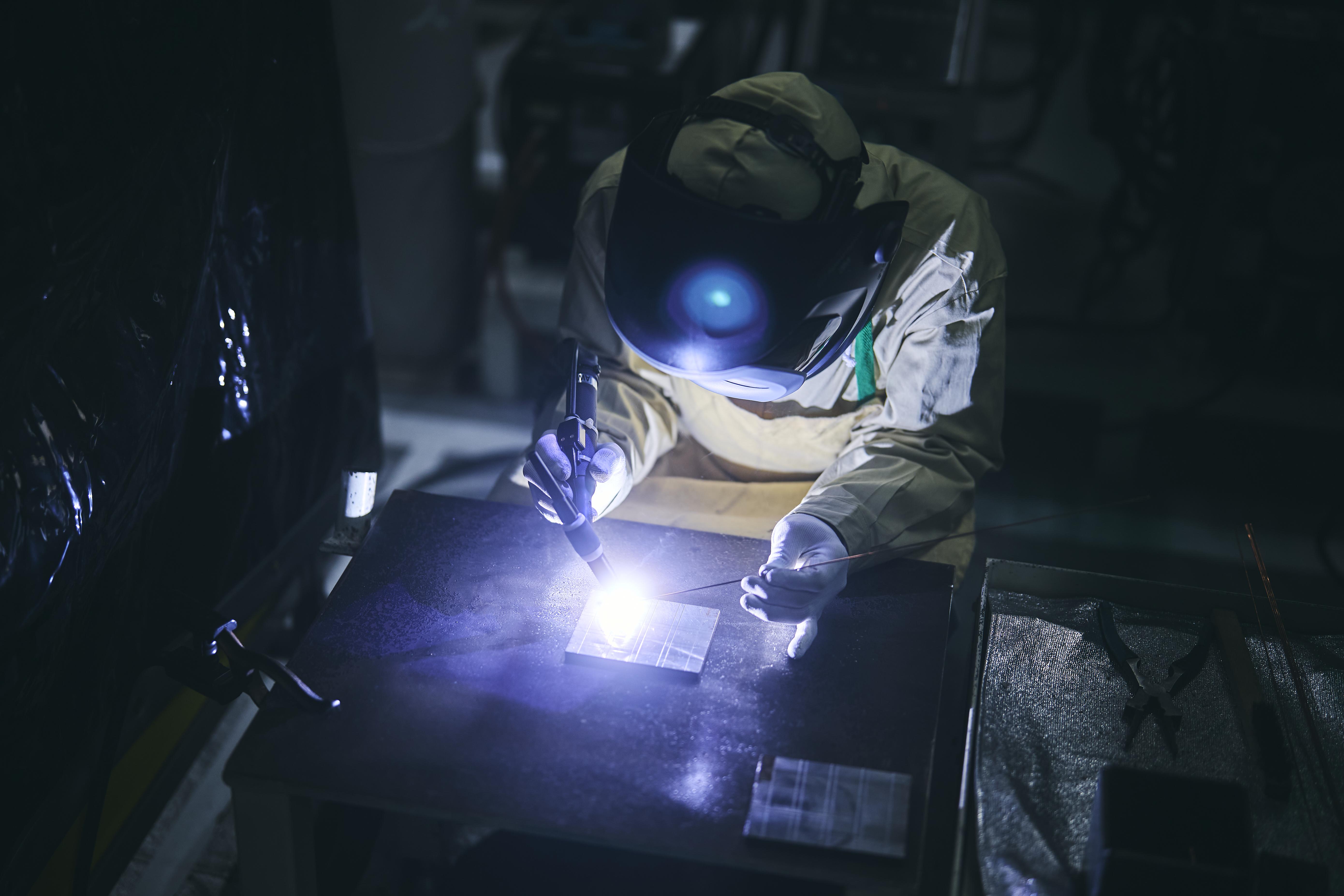
After a few dozen seconds of intense light and sharp, crackling sound, two pieces of metal are solidly joined.
The welded area is covered in a black ashy foam called slag, born from metal impurities. A quick scrub with a wire brush removes the slag to reveal a beautiful, rounded line of metal, called a bead. This marks the joint where the two plates of metal are now irrevocably joined.
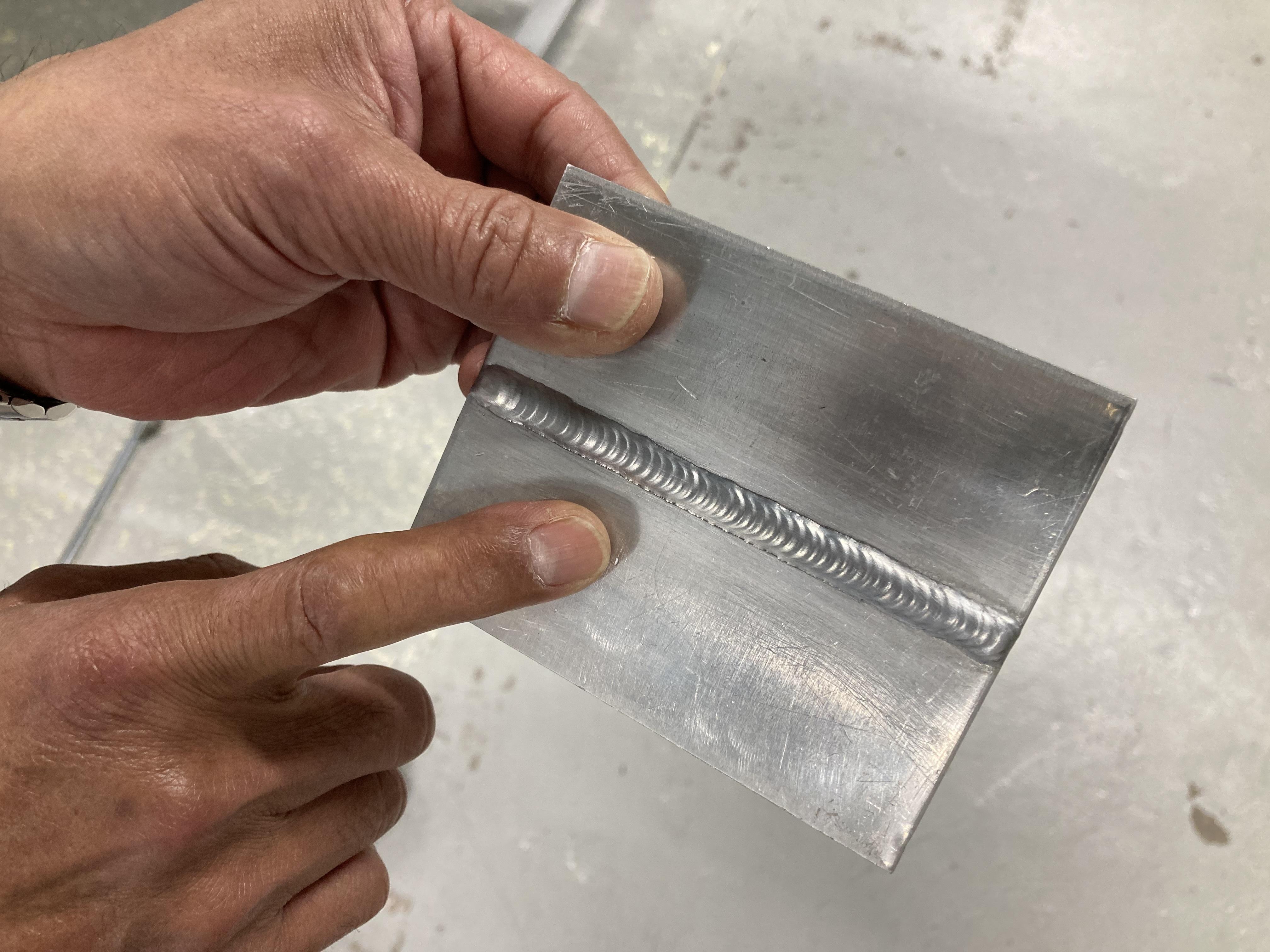
No matter what you are making, the process of joining two different pieces is essential. For making cars, welding is an indispensable skill that melts metal to fuse it at the molecular level.
The history of metal welding goes back to ancient times. Some records indicate that bronze welding techniques go all the way back to around 3,000 BCE in ancient Egypt or Mesopotamia, or perhaps the Shang or Zhou dynasties of China.
The electric "arc welding" most used today was first developed some 100 years ago.
When the welder's rod (electrode) meets the material to be welded, it completes an electric circuit and current flows through the electrode. When the rod is withdrawn to keep a certain air gap, a phenomenon called "arc discharge" is created between the material and rod. This ionizes the gas around that point, creating plasma.
This normally nonconductive gas can reach temperatures of 5,000 to 6,000 degrees Celsius and generates intensely bright light due to the electricity flowing between the rod and the material. Arc welding uses this high temperature to melt the target materials and the welding rod to join pieces together.
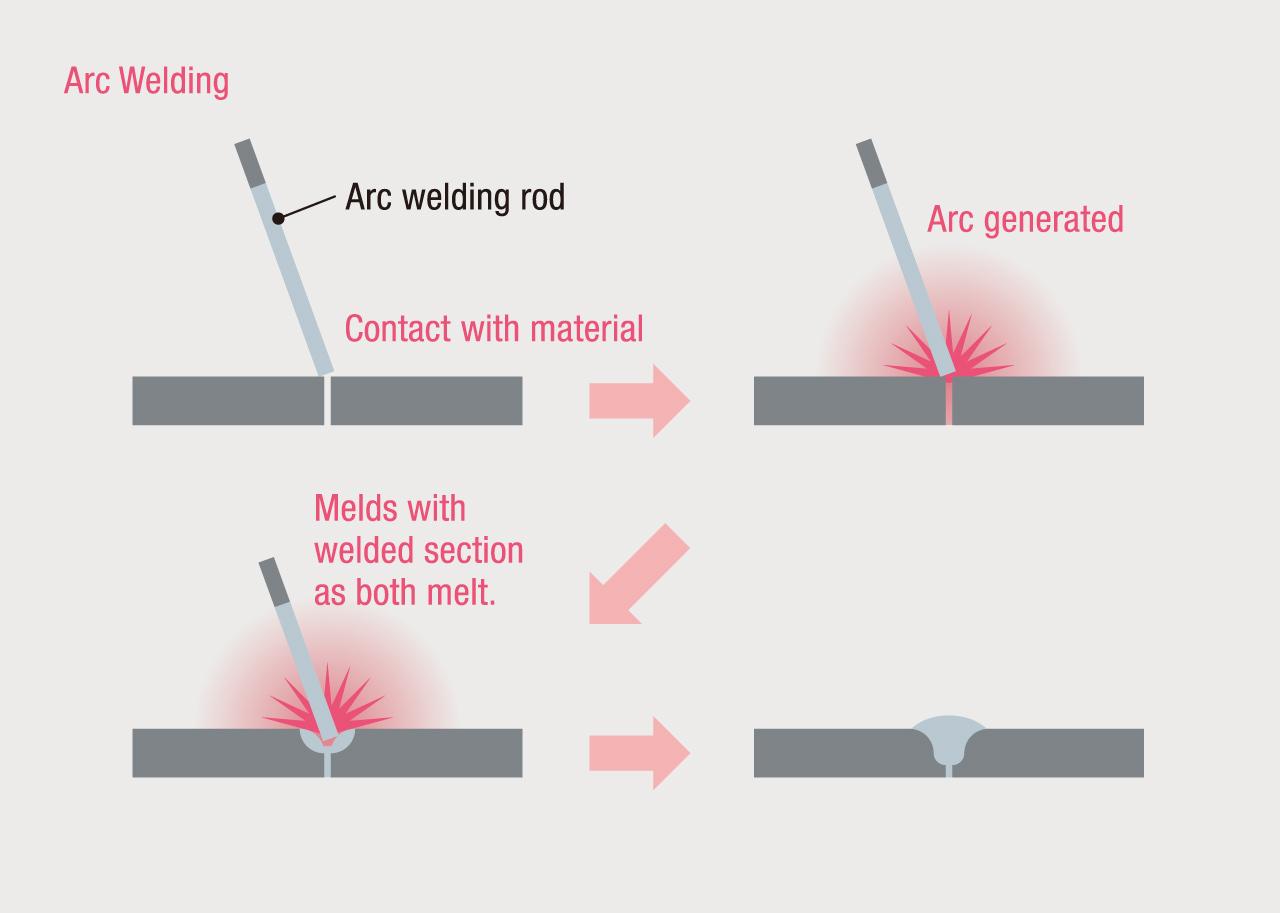
The melting process fuses the materials together, and as they cool down, the melted metals form a crystalline structure that is altered at the molecular level. This is why welding allows two materials to integrate so completely.
Toyota has artisans who have these skills. One of them is Akira Miki, a senior expert in the Production Engineering Development Management Division, Skills Training Promotion Group.
A workplace where no two jobs are the same
Miki was born on December 28, 1958, in Kan-onji City, Kagawa Prefecture. He liked making things early on and also liked the looks of motorcycles, so as a child he fell in love with building plastic models. His family moved to Yokkaichi City, Mie Prefecture, for his father's work, and Miki eventually enrolled in a technical high school there.
Miki
In those days, most people immediately started looking for jobs when they graduated high school. So, I figured that if I wanted to find a job someday, I should go to a technical high school. I did and enrolled in the mechanical engineering course.
I chose to apply at Toyota because I liked cars and wanted to put them together.
He was hoping for a position assembling cars, but when he formally joined on April 1, 1977, he was assigned to the welding team in what is now the Mobility Tooling Division. At the time, his only experience with welding was a practice training session at his high school.
Miki
The welding team was considered a hard, dirty, dangerous job at the time, and I wasn't sure I could actually do it.
I didn't get any training, either. I was just thrown out on the floor. It was a time when you were supposed to learn by watching your boss and senior workers.
Even when I asked them to teach me, people refused to share the important things. Those old-time craftsmen were all like that.
Miki's first assignment when he joined the company was to take sheet metal and weld it into a box to hold the tools of his job like the hammer, pliers, and torch for the gas welding common at the time.
He built his welding skills by making boxes for kaizen operations to make genba work more efficient, or welding sheet steel to make small molds.
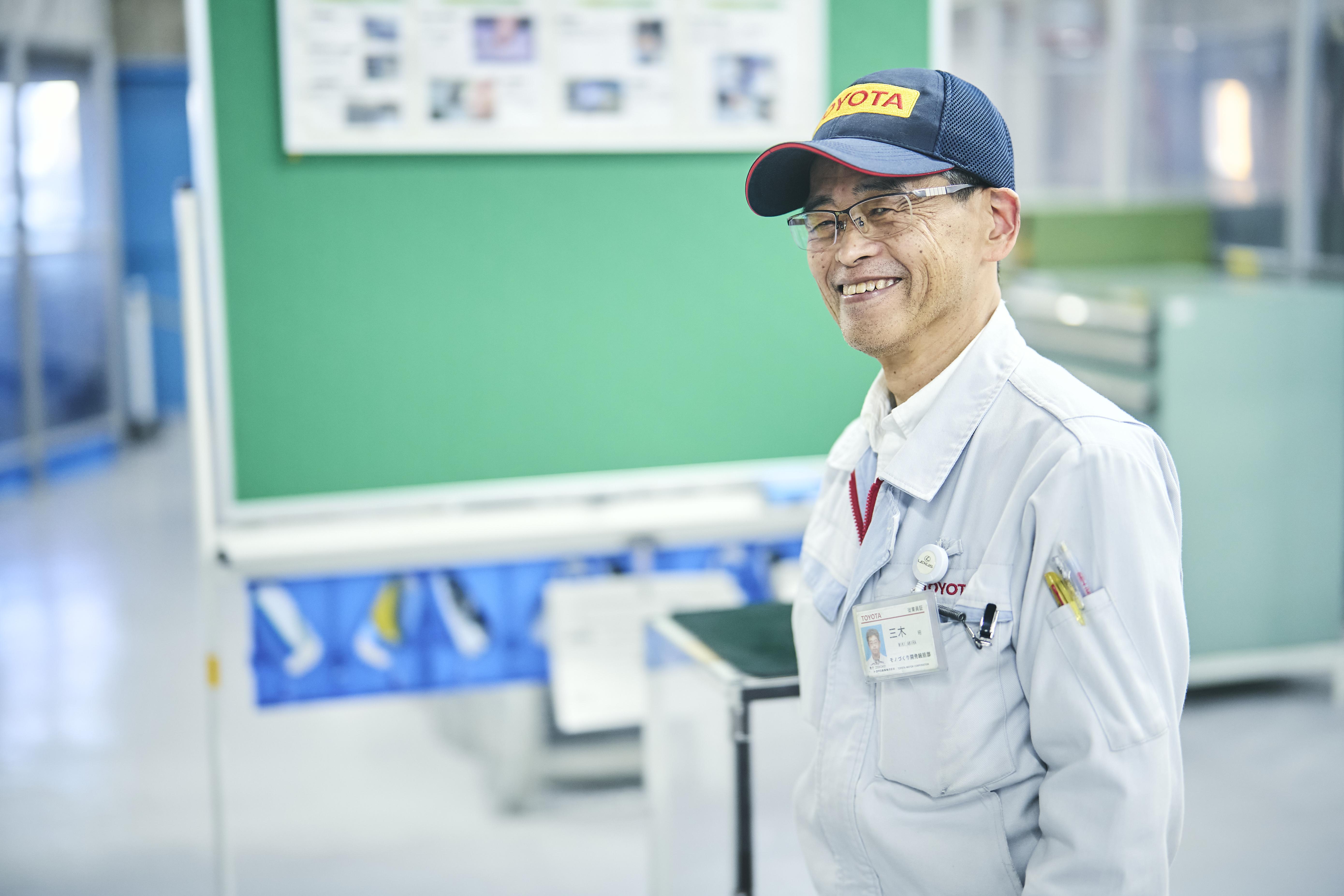
Miki
It really was hard, dirty, and dangerous, but as I kept at it, I found welding more and more interesting.
How was the first toolbox I made? It was too embarrassing to show anyone! The older workers were all really talented, so I felt I had to work hard just to catch up.
Miki spent time after work teaching himself, taking an active approach to gain and hone skills vital to carmaking like mold buildup welding, a technique used to correct defects in press dies, tempering, and using a torch to cut through heavy metal plates 10-20mm thick.
Miki
We never have the exact same job twice in our shop. For every job, we have to think of a new way to approach it. That's what makes it so interesting and right for me.