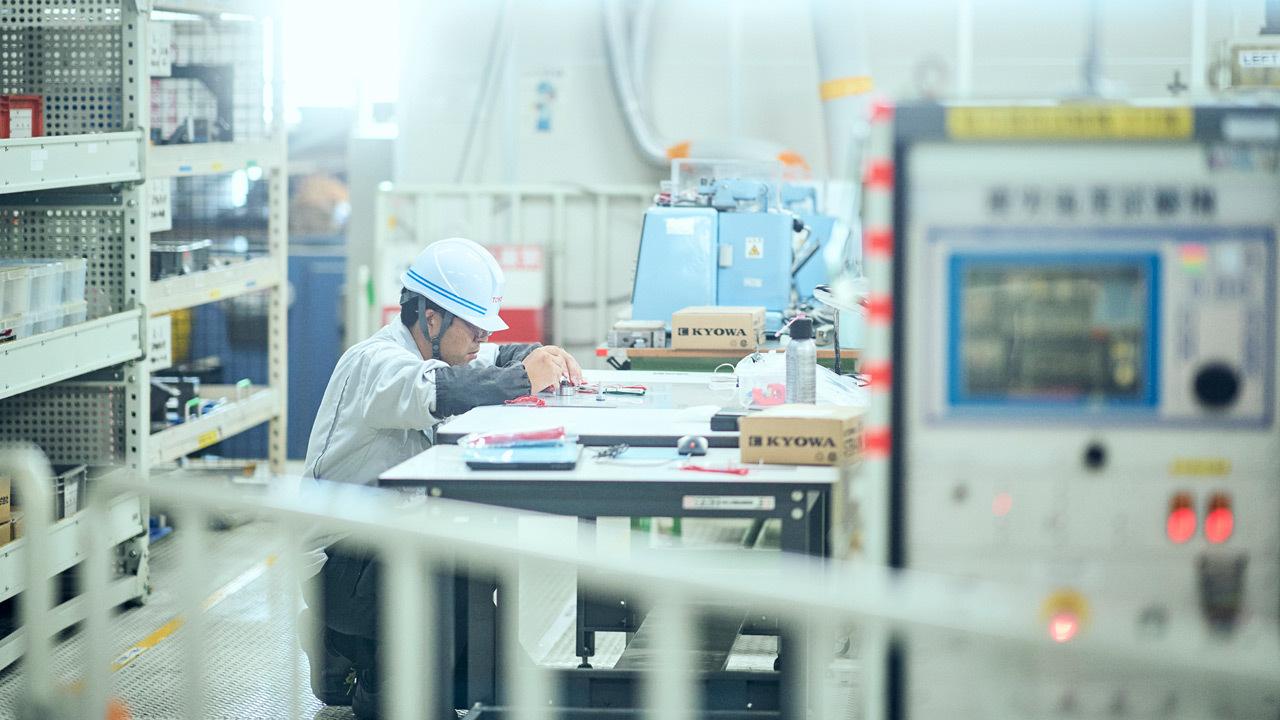
This two-part article takes a look at Takuya Okada, a master of the strain gauge whose unique expertise helps test the strength of chassis components.
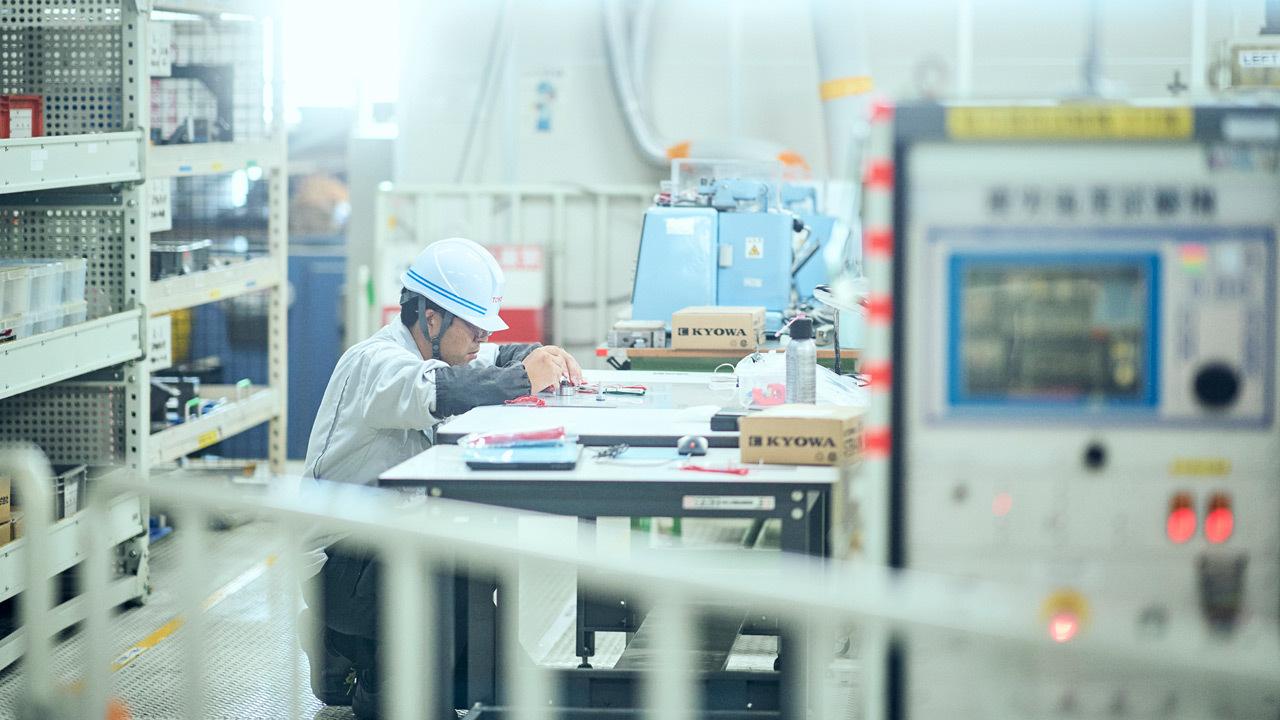
Handwork still plays an important role in today’s car manufacturing, even as technology like AI and 3D printing offer more advanced methods. This series features the craftsmanship of Japanese monozukuri (making things) through interviews with Toyota’s car-making masters.
This is the second part of the article which shines the spotlight on Takuya Okada, a young master of the strain gauge who uses his unique methods and expertise to test the strength of chassis components in Toyota’s car production facilities.

#12 Takuya Okada, a “master of the strain gauge” testing the strength of chassis components with unique expertise
Team Leader, Quality Assurance Team 4, Stamping Equipment Certification Section, Body Manufacturing Engineering Div., Tsutsumi Plant, Production Group, Toyota Motor Corporation
The challenge of selecting—and affixing—the right sensors
How exactly does Okada use strain gauges to test chassis strength? To find out, Toyota Times visited his Stamping Equipment Certification Section at the Tsutsumi Plant in Toyota City, Aichi.
“Strain gauges are single-use, and we stick them onto the object we want to measure with instant adhesives. The most basic type costs around 500 yen each. When I’m attaching them, instead of sitting in a chair I kneel on the floor so I can really get in the zone. I psych myself up to not make mistakes by chanting, ‘500 yen each, 500 yen each’ in my head (laughs). My hands are large so I had a hard time mastering how to stick them to tiny areas.”
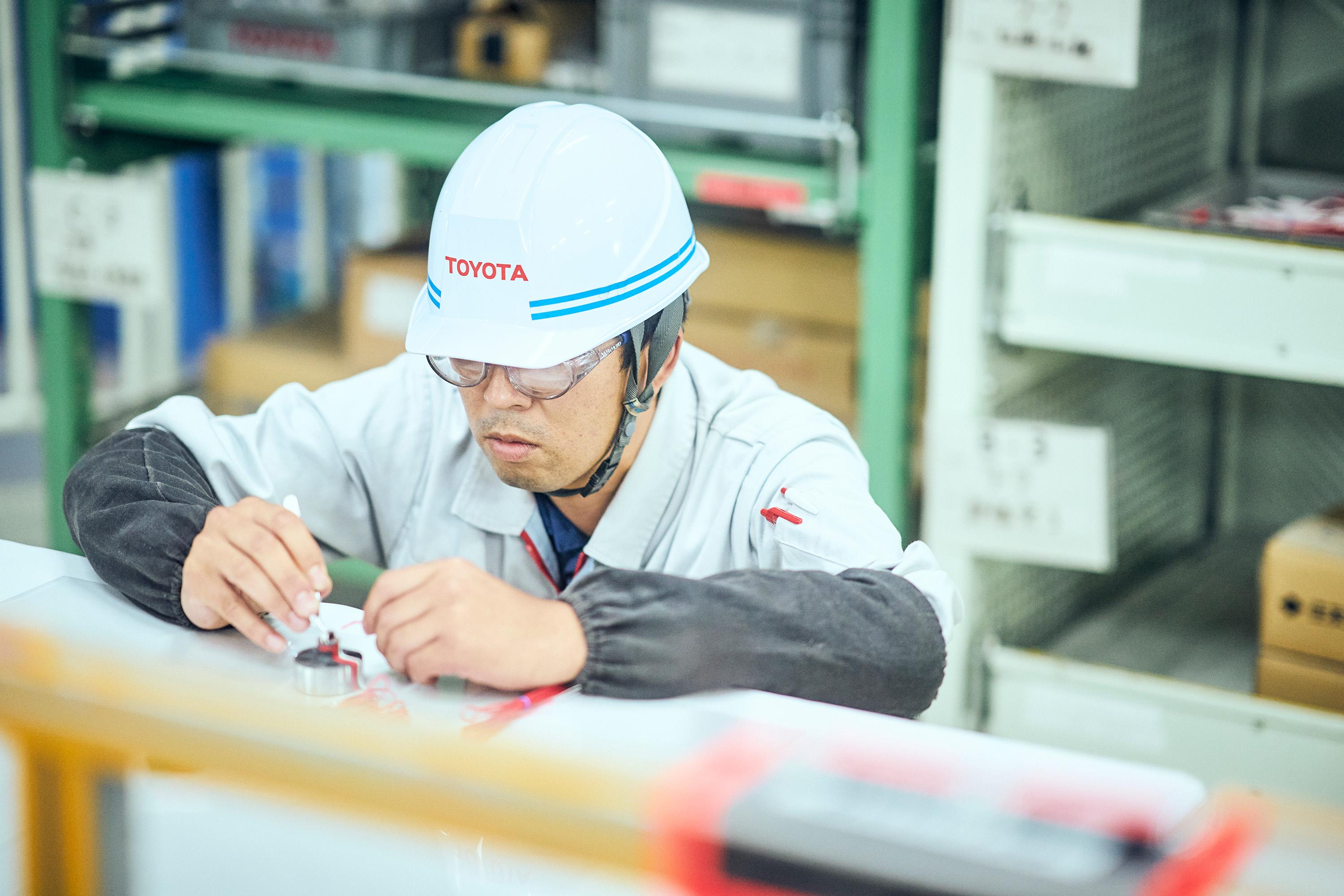
Okada demonstrated the process at his regular desk. He marks the spot where the gauge is to be affixed, applies a few drops of adhesive, and just like that the work is done.
But even their instructions admit that the hard part with strain gauges is using them well. Measurements vary greatly depending on where the gauge is placed. To measure a component's internal stresses (and thereby strength), a gauge must be set in an appropriate position on the object and in the right way. Of course, the fundamentals of placement and measurement methods are documented in the manuals, but this is only the beginning.
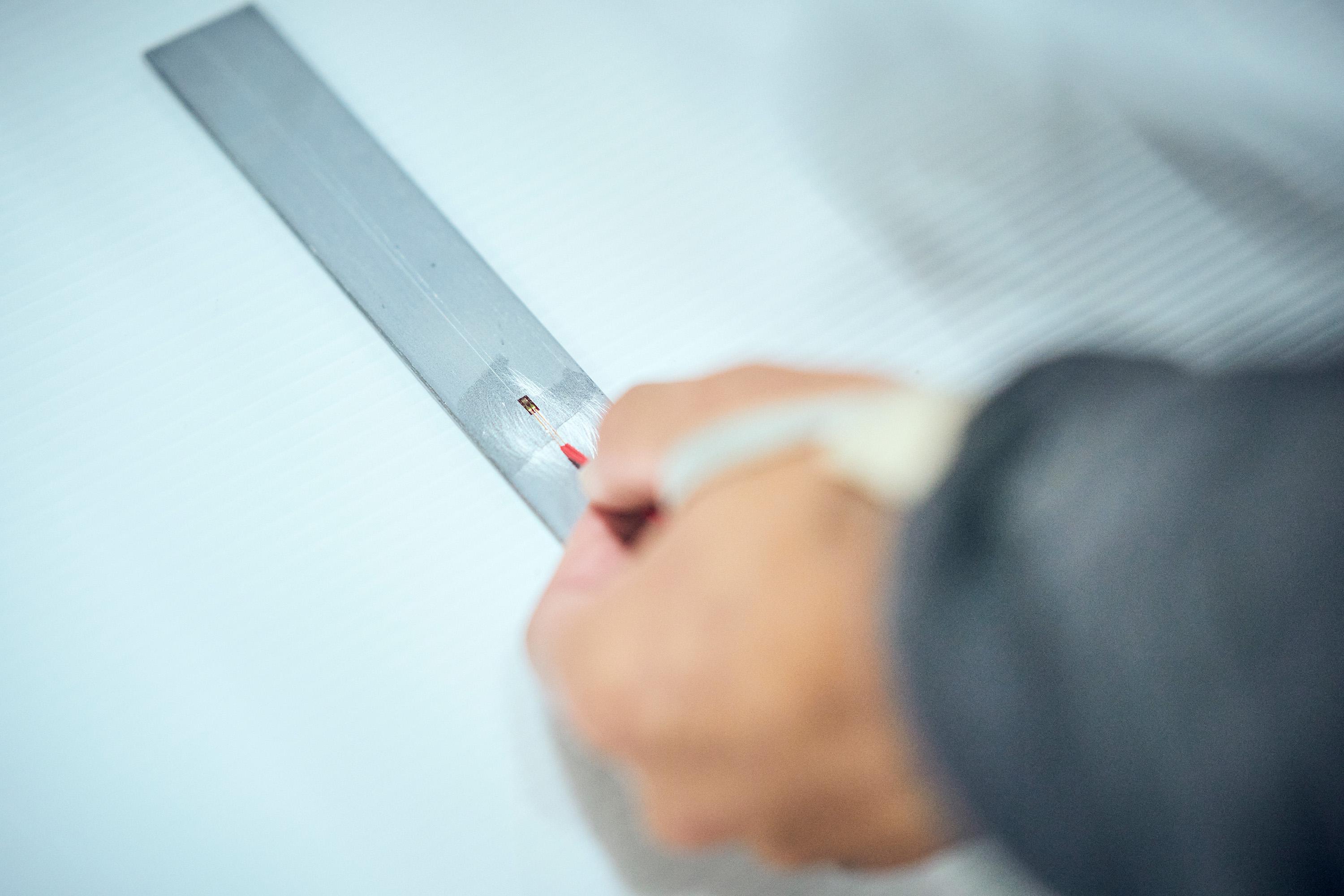
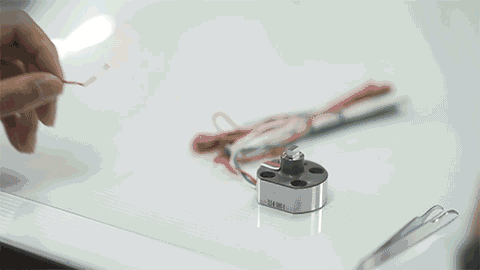
Strain gauges were first developed nearly 70 years ago and are widely used in various fields beyond manufacturing. Despite this, manufacturer manuals state that “users require extensive experience and expertise.” They must also be meticulous and creative in devising different jigs or tools according to the material and the purpose of measurement.
“The key is thoroughly considering the measurement configuration, purpose, and method. This holds true for other measuring instruments as well. As I’ve said, if you can’t take a proper measurement, you’re better off not measuring at all. And you can’t get an accurate measurement unless you have a clear idea of the principles involved. Knowledge of the material being tested is also essential.”
Visualizing what happens within parts
The main tests that Okada uses strain gauges for are fatigue strength and deformation strength tests for front and rear suspension components.
Chassis components are repeatedly subjected to large forces whenever a car accelerates, turns, or stops. Even if these forces fall within the scope anticipated from the design stage, repeat exposure causes invisible damage to build up within chassis parts made of steel or aluminum alloys, gradually degrading their strength. This is known as metal fatigue.
When metal fatigue exceeds a fixed threshold for the given material, tiny, invisible cracks and fractures occur within the part, reducing its strength and eventually causing it to break. This can have serious consequences, perhaps leading to an accident or making the car undrivable.
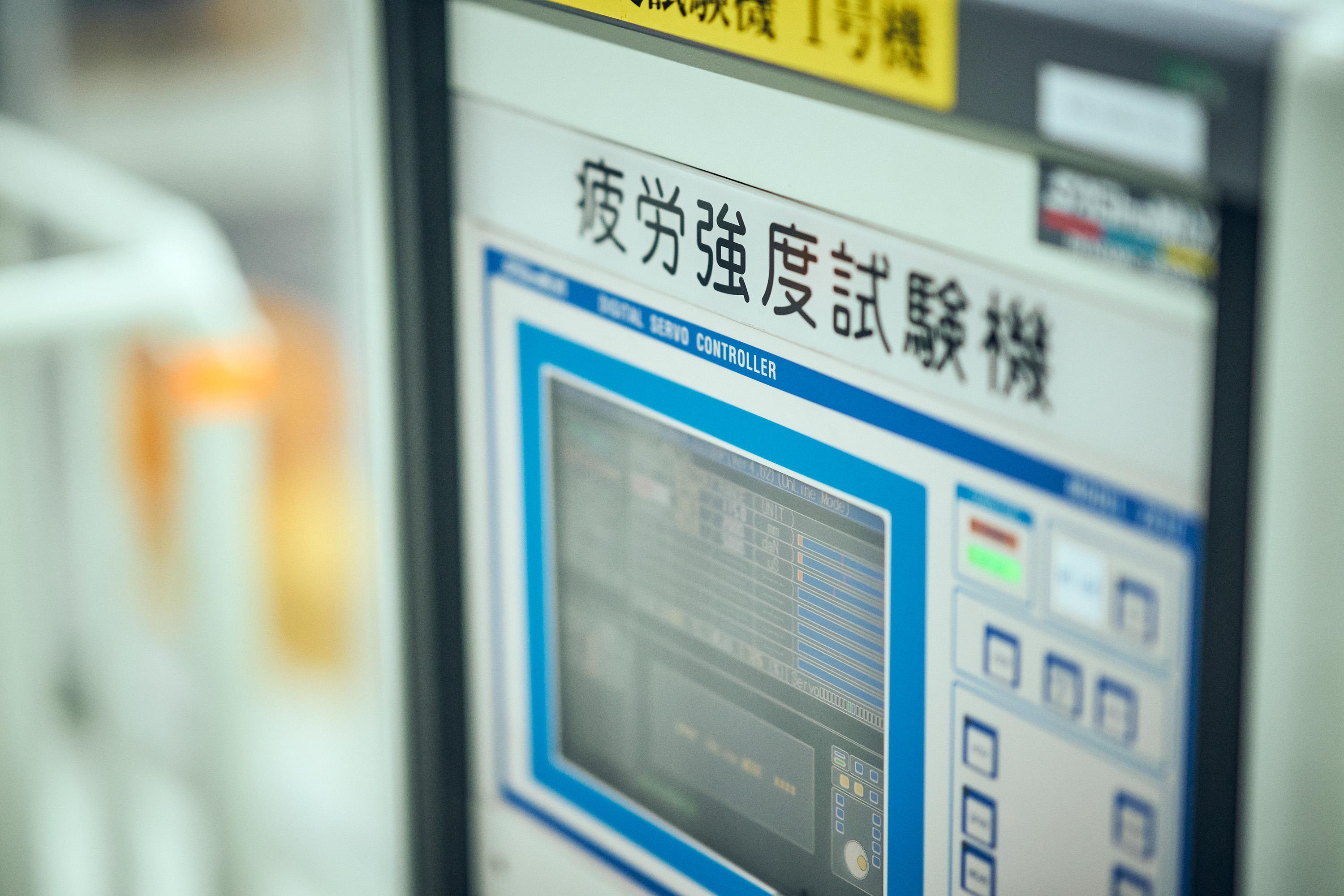
In a fatigue strength test, chassis components fitted with strain gauges are set up in a hydraulic testing machine that applies the same repetitive forces experienced during driving. The attached strain gauges can then measure the stresses that occur within the part and the resulting deformation. By repeating these tests many times while varying the magnitude and frequency of the forces, engineers can determine the strength limits of parts. This testing is crucial for ensuring that a car can be driven safely.
“The measurement data we obtain with strain gauges reveals what’s happening inside components, which is not visible from the outside. For example, if even a minuscule crack forms within the material, it will show up as a change in the numbers. The figures also tell us when a part is about to break—big changes in the values are soon followed by a bang!”
Fatigue testing includes longitudinal fatigue tests, which simulate the sudden starting and stopping of the vehicle; lateral fatigue tests, which simulate conditions during cornering; and tramp fatigue tests, which simulate the vertical movement of a car driving on ordinary roads or rough terrain.
The other main type is deformation strength testing, in which a testing machine reproduces the impact force transmitted to chassis components through the tires in irregular driving situations, such as a collision with the curb. This allows engineers to check how much damage parts sustain from a given force. Such testing is also essential for ensuring safety.
Since joining the company, Okada has devoted himself to gaining experience in strength testing. With his natural inquisitiveness, he has built on the expertise passed down by senior colleagues to establish his own measurement methods, using both strain gauges and various other instruments. One after another, Okada has found ways to make measurements that were previously deemed impossible.
Measuring the unmeasurable
Having earned himself a reputation, Okada is inundated with requests from various departments asking him to figure out how to test the strength of parts that can’t be measured with existing methods. People come to him after being told that “Okada will find a way.”
“I never want to say I can’t do it. There’s no such thing as ‘unmeasurable.’ I see that as a chance to show what I can do. Especially when people are trying to push the envelope in development, I want to do my part.”
One such job Okada remembers well is the real-time measurement of thermal strain in the painting process for body panels. To reduce noise within the car, a special rubberized coating is applied to the interior side of these panels. However, the process of drying this coating creates heat strain that causes unevenness in the panels.
To find a solution, the painting department turned to Okada to measure and analyze the thermal strain. What made this difficult was the heat resistance of strain gauges. Okada managed to carry out this impossible measurement by building a wooden box that acted as a thermal barrier and cooler for housing the gauges.
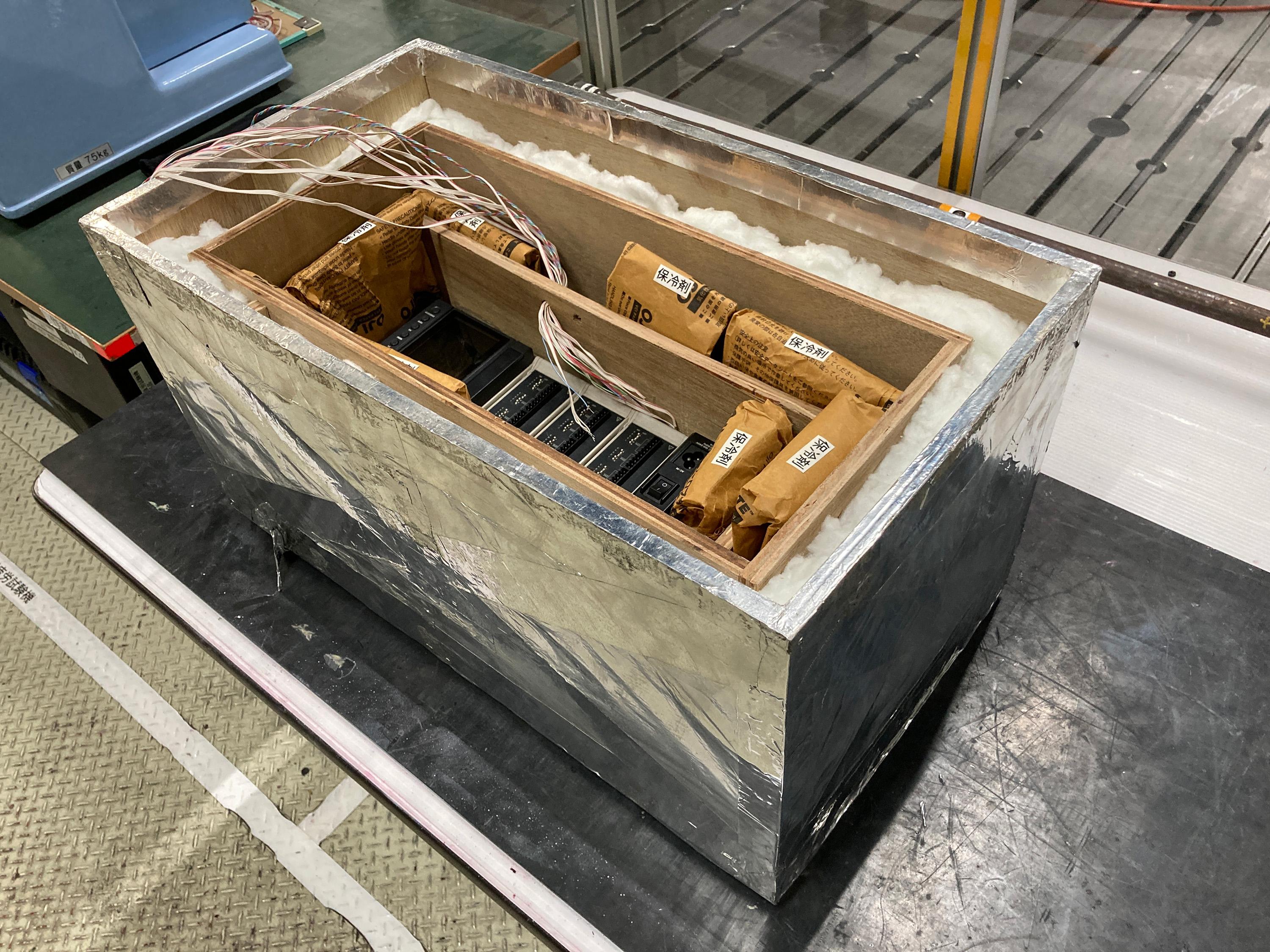
Developing prosthetics for Paralympians
Okada’s work as a master of the strain gauge also involves supporting athletes. Among Toyota’s roster of para-athletes is sprinter Keita Sato, who won a bronze medal in the 4x100m relay at the 2016 Rio Paralympics. In 2017, the company began developing a prosthetic blade for Sato.
“Before that, Sato was competing with commercially available prosthetics, which had durability issues. Then ‘Team Sato’ was formed within Toyota to develop a prosthetic blade which he could use for competition.”
However, when the project started up under the Production Engineering Planning Division, the team had no experience in building prosthetics, and began developing from scratch. As a result their first blade, completed in late 2017, lasted through only 20m of jogging before snapping.
“Our Body Manufacturing Engineering Division was not involved in this initial development, but in 2018 the team asked for help and I was able to join them.”
Okada and his Body Manufacturing Engineering Division colleagues were tasked with accurately grasping the stresses on the blade during running, and conducting tests to ensure that the prosthesis was sufficiently strong.
To achieve this, Okada placed strain gauges and various other sensors on the blade, and ran alongside Sato to gather data. He also performed fatigue tests on the blade being developed.

“Other members laughed at me, saying there was no way I could keep up with a 100m sprinter and that the sensor wires would snap. But of course, I expected as much. I just hoped I could get enough data before they broke,” says Okada with a smile.
Okada fed the data he obtained back to the blade manufacturing team, which was assisted by a prosthetist. By combining their car-making technology and expertise with the prosthetist’s skills, the team ultimately achieved its goal of creating a faster prosthetic blade that was also durable enough to last for three years and more than 360,000 steps.
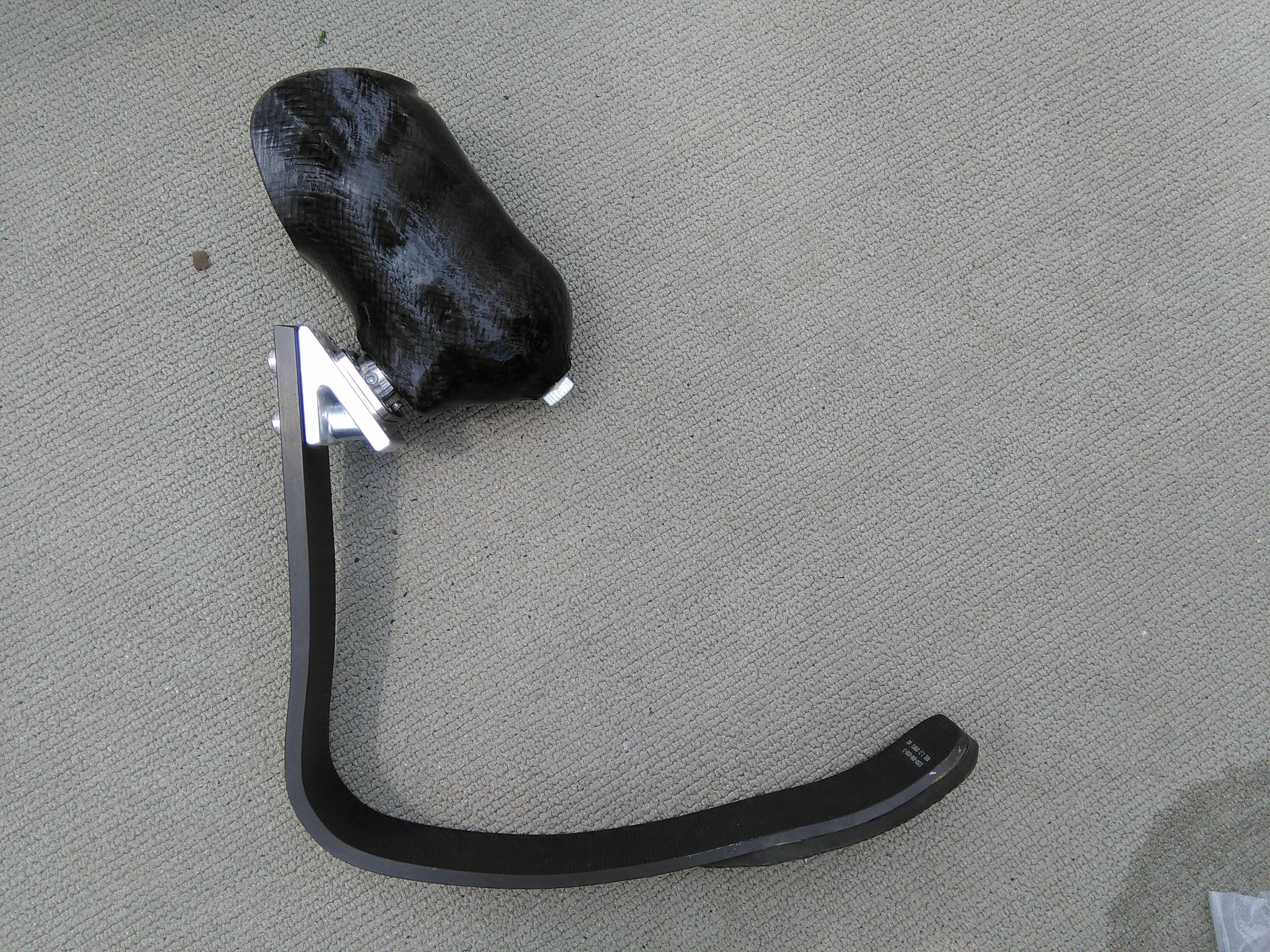
“Sato praised the blade for being easy to run in, and I hear he has shaved 0.21 seconds off his 100m time. Apparently, the prosthetist was so impressed by our approach to manufacturing that he went out and bought a Toyota.”
In developing the prosthetic blade, Okada worked with masters from various other fields unrelated to his regular duties, including design, machining, wooden forms, resin molding, carbon molding, and aerodynamic analysis. He says this invaluable experience led to a change in his values and perspective.
“The greatest benefit of working on the Tokyo 2020 Paralympic project was probably the experience of constantly receiving direct feedback from the athlete, i.e., the end user. In my regular work, I have no opportunities to speak directly with end users. Through this project, for the first time I was able to see what it means to approach things from the user’s perspective.”
Fostering the next generation while remaining on the front lines
Following these experiences, Okada is now focusing his efforts on training the next generation and honing his own skills.

“At the moment, I’m looking after two junior employees, both in their 20s. I give them daily lectures on correct measurement methods, but most importantly, I try to make sure they understand the principles and fundamentals of measurement. The procedures for taking measurements come later. They have grown remarkably and can now figure things out for themselves, even when it comes to using new equipment.”
Okada is not satisfied with being regarded as a master of the craft himself—he wants to keep nurturing younger employees until they too have earned the title. That said, Okada himself is still only in his late 30s. For many years to come, he hopes to continue taking on new challenges as an engineer on the front lines.
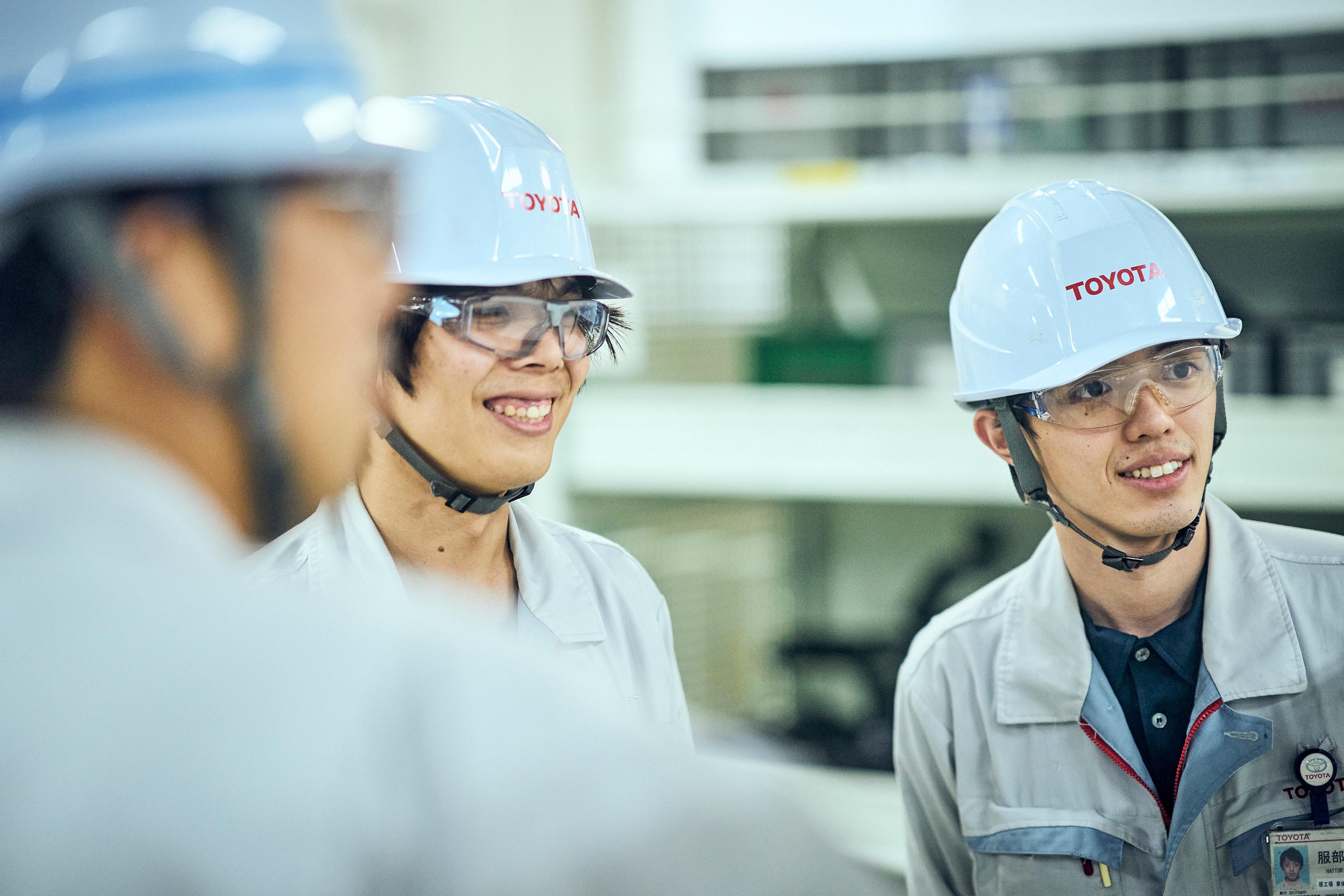
“The world of measurement is constantly evolving. We use the internet and publications to study up on the latest measuring devices and new materials being measured. Personally, I want to keep progressing, and I’d be delighted if my own knowledge could be helpful to many others.”
Takuya Okada, Toyota’s youthful master of the strain gauge. As word of his measurement skills spreads, more and more departments across the company come seeking Okada’s help. His efforts are also attracting attention beyond Toyota, including from the Society for Technology of Plasticity. The master’s work has only just begun.