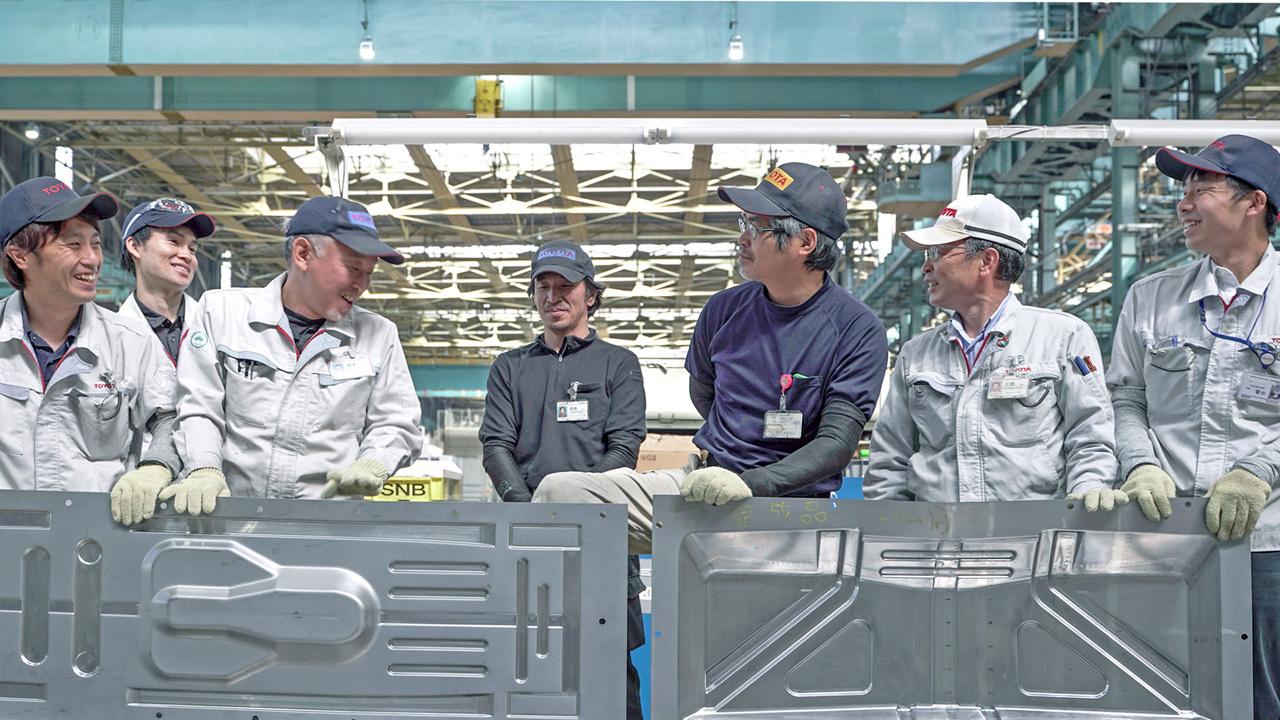
This series explores the project to restore a first-generation Crown, a car that embodies Toyota's origins. Part 6 reports on a groundbreaking process for rapidly reproducing corroded body panels at minimal cost.
The difficulty of preparing processing data
And yet, producing the Crown’s body panels with incremental forming was far from simple. Processing data created with 3D-CAD software is needed to instruct the computer-controlled automated forming machine on how to shape the material. Preparing this data proved a challenge.
The trio of Sato, Takahashi, and Takayama decided to begin by carefully examining the structure of the first-generation Crown’s body and its constituent panels.
Sato
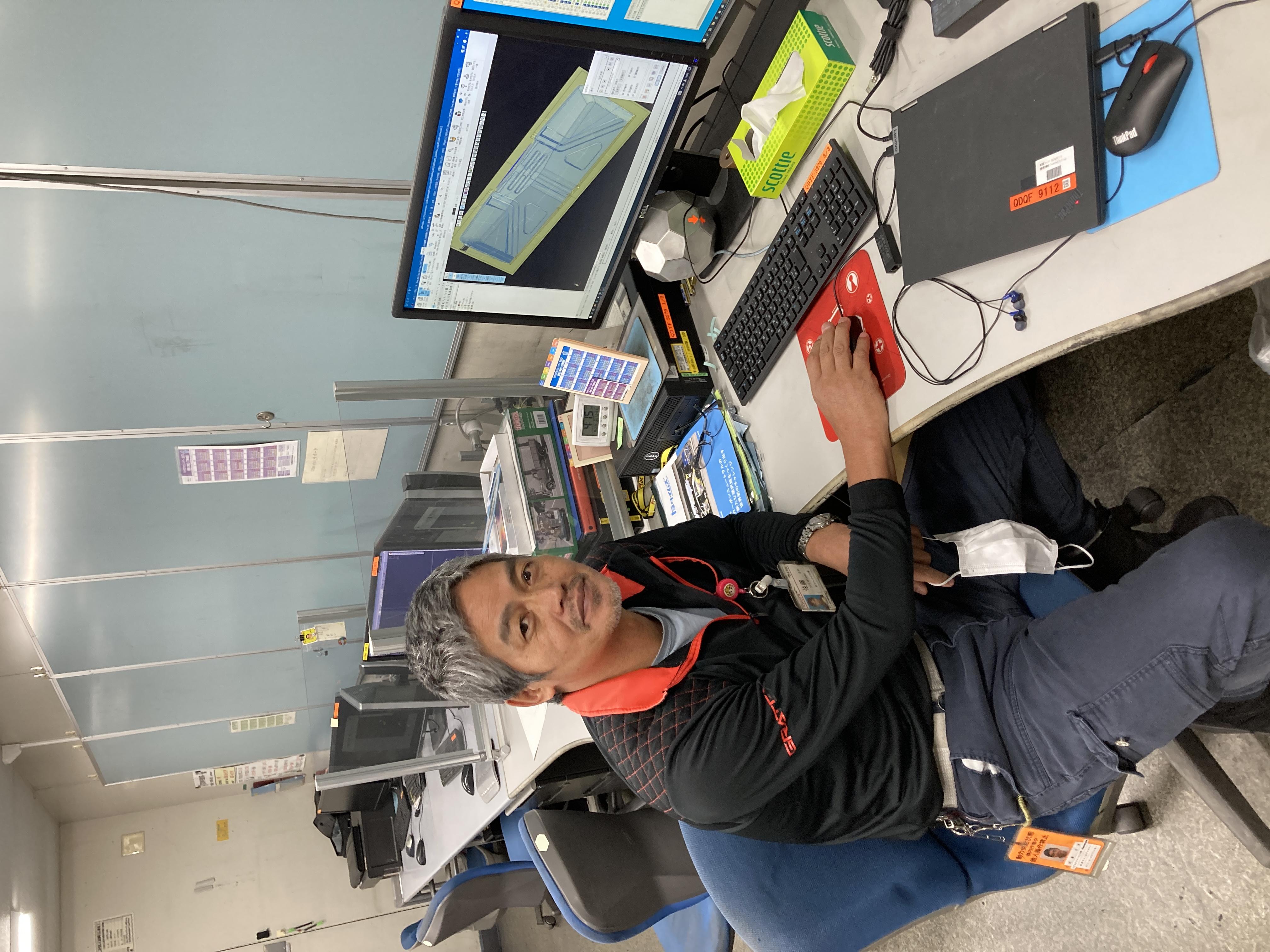
Examining the parts, I was struck by the expertise and skill of the body’s creators, and their dedication to manufacturing.
Despite the number of parts, they’re put together seamlessly thanks to superb welding and finishing.
The underbody structure is also completely different from what we have today. Whereas many parts are now integrated, the individual components had to be assembled back then, likely requiring more steps in the process. At the same time, we found that this process was well thought out to ensure efficiency.
Takahashi
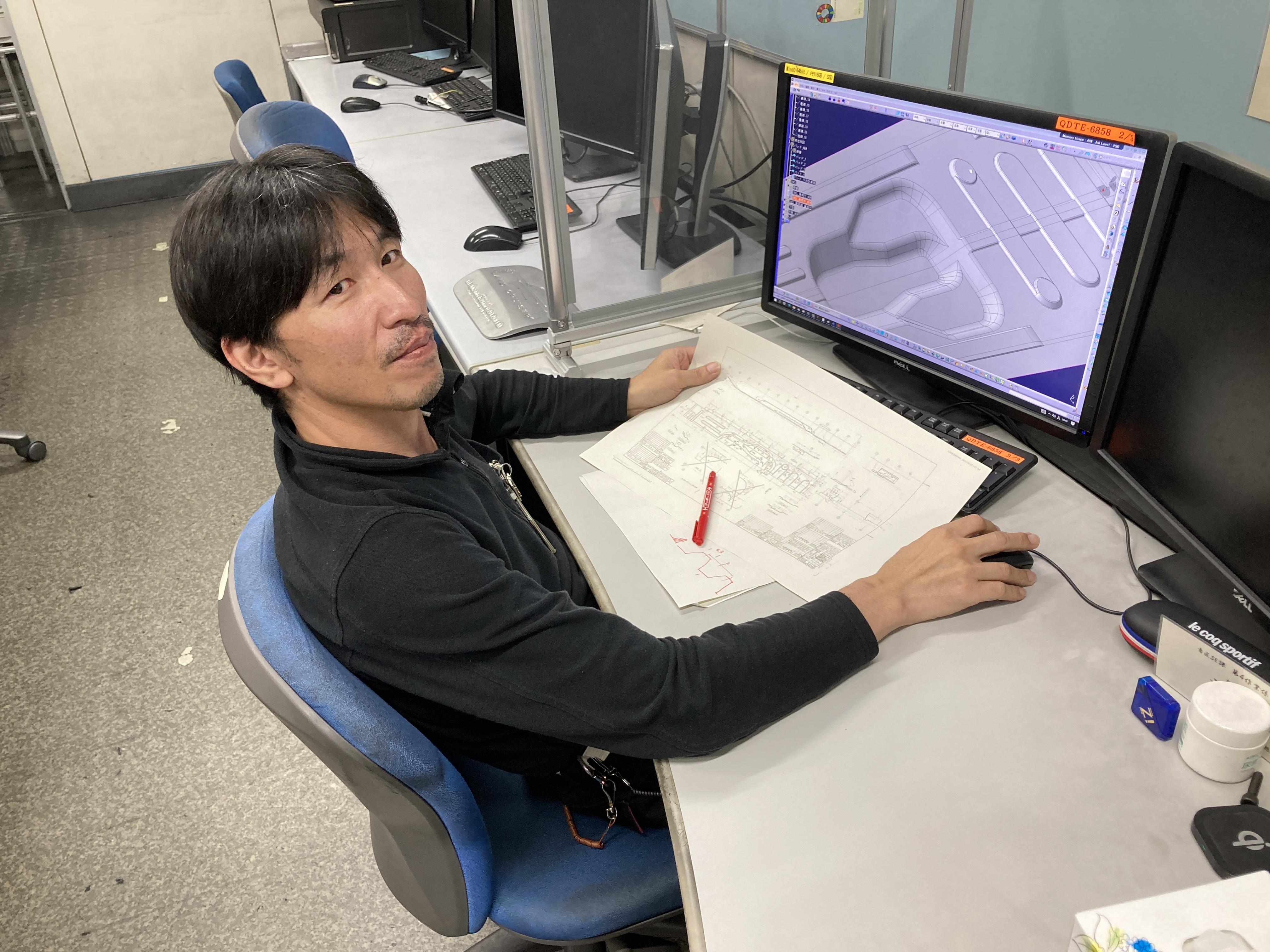
We initially tried to create the processing data through reverse engineering—that is, we attempted to measure the panels needing restoration and digitize their geometry.
However, the panels were too battered to allow for accurate measurements, and the data wasn’t precise enough.
So, we had to decipher and digitize the original drawings from scratch. Thanks to the National Skills experience from my youth, manufacturing items from blueprints was not so tough. After all, knowing how to read design drawings is a basic part of monozukuri.
Even so, those original drawings were, of course, done by hand—and revised multiple times to boot—making them rather troublesome to decipher.
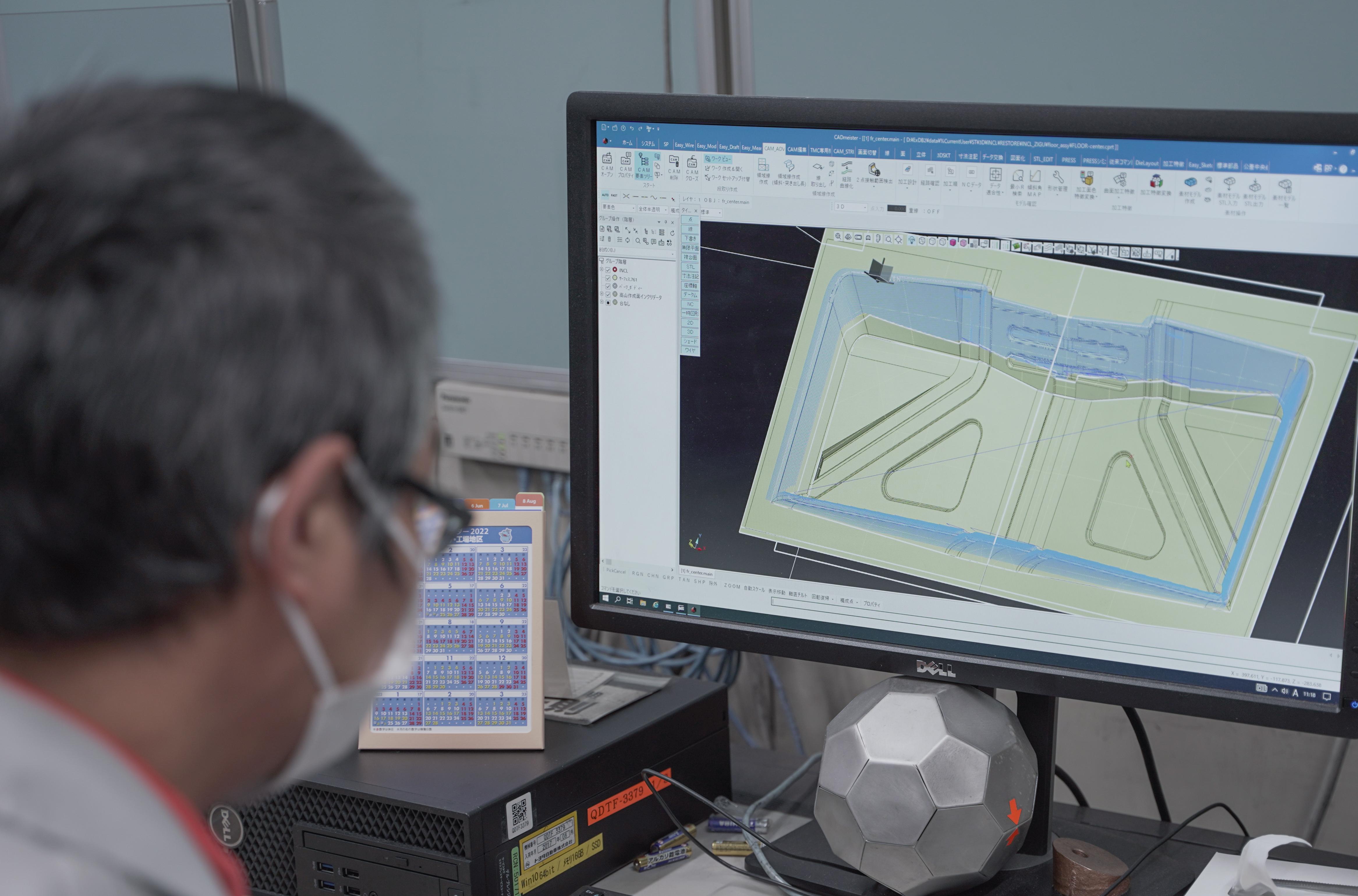
For the trio, this was in fact their first attempt at creating a complex panel shape from a single large piece of sheet metal.
The sheer amount of forming involved caused several panels to crack and crease during processing.
On each such occasion, the trio worked out why the problem had occurred in a particular section. Drawing on expertise cultivated through both stamping correction and sheet metal machining, they adjusted the input data and continued to fabricate body panels in an ongoing process of trial and error.
In another first, they also devised ways to improve efficiency by, for example, making two smaller parts together on a single sheet rather than separately.
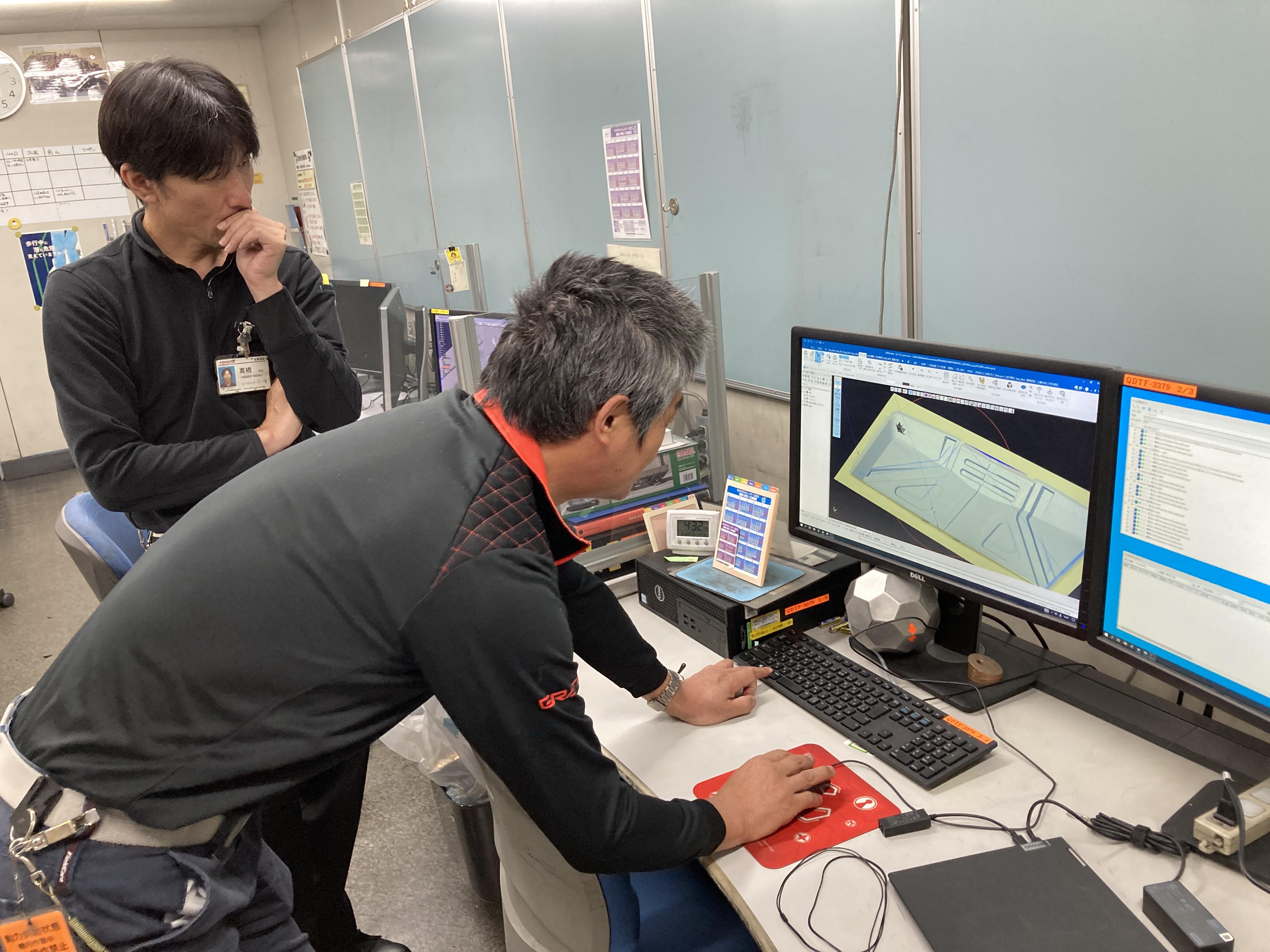
Vintage cars x cutting-edge technologies = the future of carmaking
Takayama is in his third year working with this technology at the Mobility Tooling Division. Before this, he had been part of the stamping team overseeing the press.
Like Sato and Takahashi, who assisted him, Takayama senses unlimited potential in this new technology.
Takayama
Unlike stamping, there are no molds, meaning you can modify a part as often as you like by changing the processing data.
If you identify a problem, you can simply revise the ball tool’s path and run it again. This is another feature of incremental forming.
To figure out how much force is needed in a particular spot when making a path, we draw on the knowledge of veteran sheet metal craftspeople.
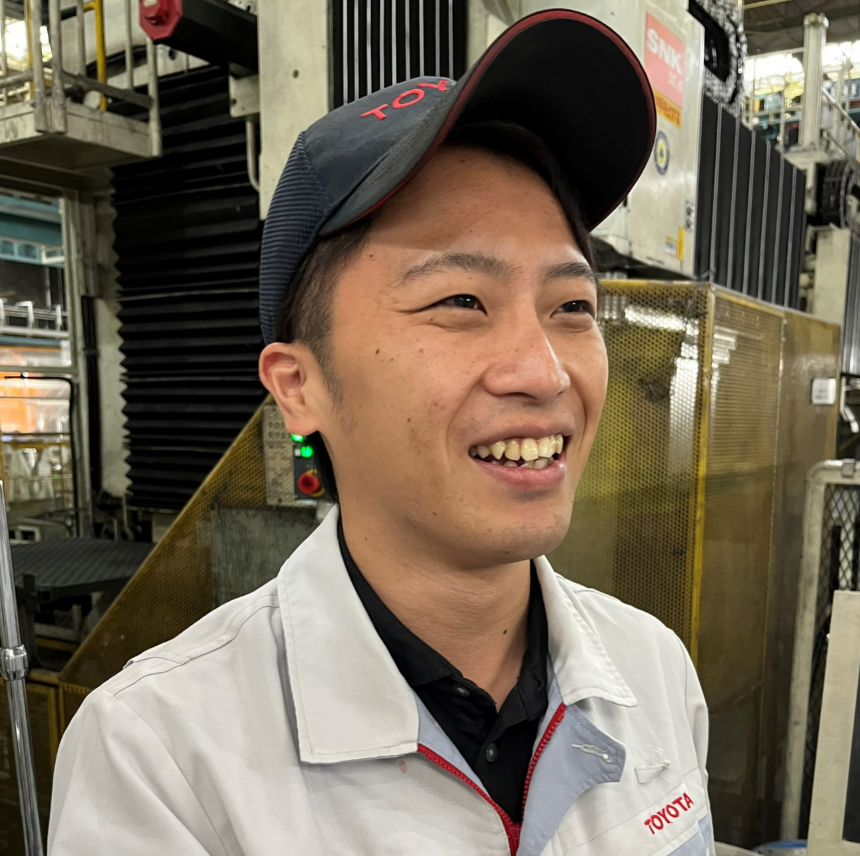
One issue for our partner companies and suppliers is having to retain old molds for many years in case they are needed to produce spare parts, and we are exploring whether incremental forming can provide a solution.
At present, incremental forming requires a jig in place of a base mold, and the cost can be driven down further by standardizing these jigs.
At Toyota, incremental forming is employed chiefly in the production of new Lexus and GR models. So far, it has been used to shape steel, aluminum, and other metals.
At the same time, the company is also striving to be the first in the world to apply the technology to plastic parts. One example is the front bumper canard for the Lexus LC “Edge” special edition model.
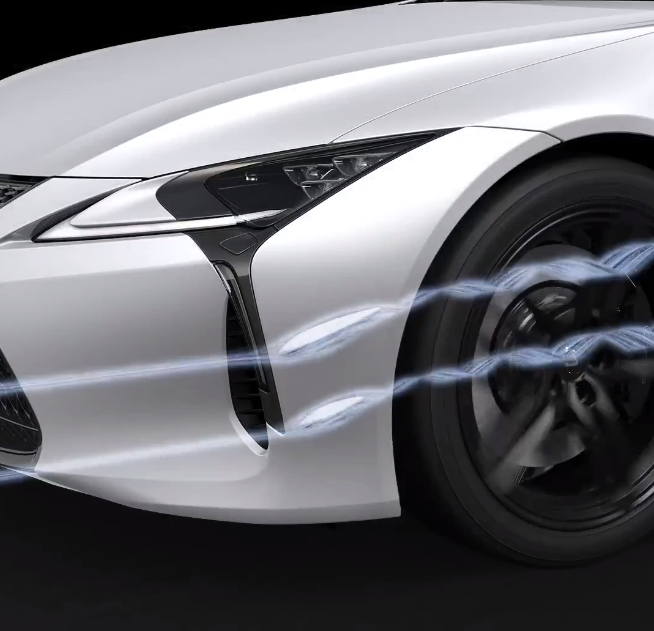
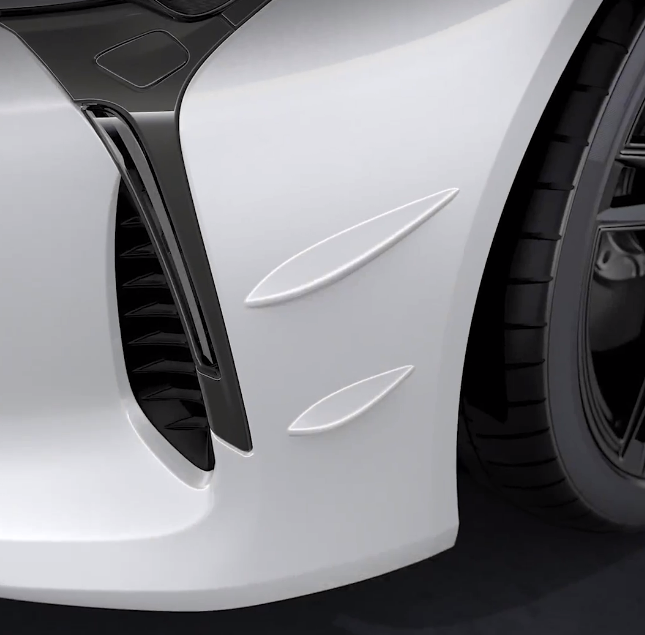
Takayama
I think that incremental forming of plastic parts can transform the future of carmaking. It would allow us to change the design of existing plastic parts, such as bumpers, at low cost.
In the future, we hope to offer new value by enabling customers to freely choose their preferred design from many options.
I want to continue honing my skills and the technology to help bring smiles to more customers.
The first-generation Crown can be regarded as the starting point for Toyota. The use of incremental forming to make body panels for this model is a perfect example of how the restoration project is not merely about reviving a vintage vehicle, but part of Toyota’s efforts to create a new future for carmaking and the role of cars in society.
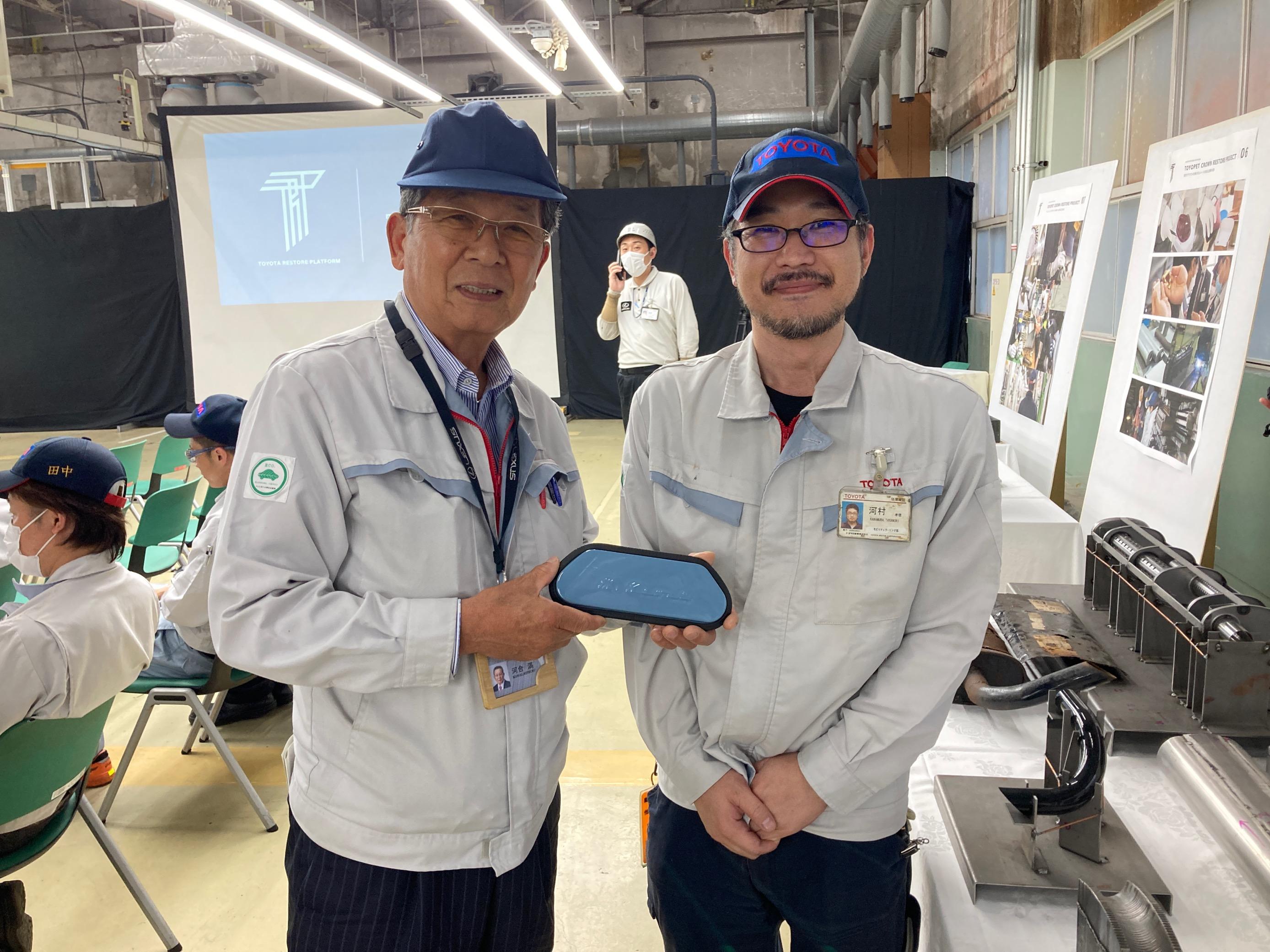
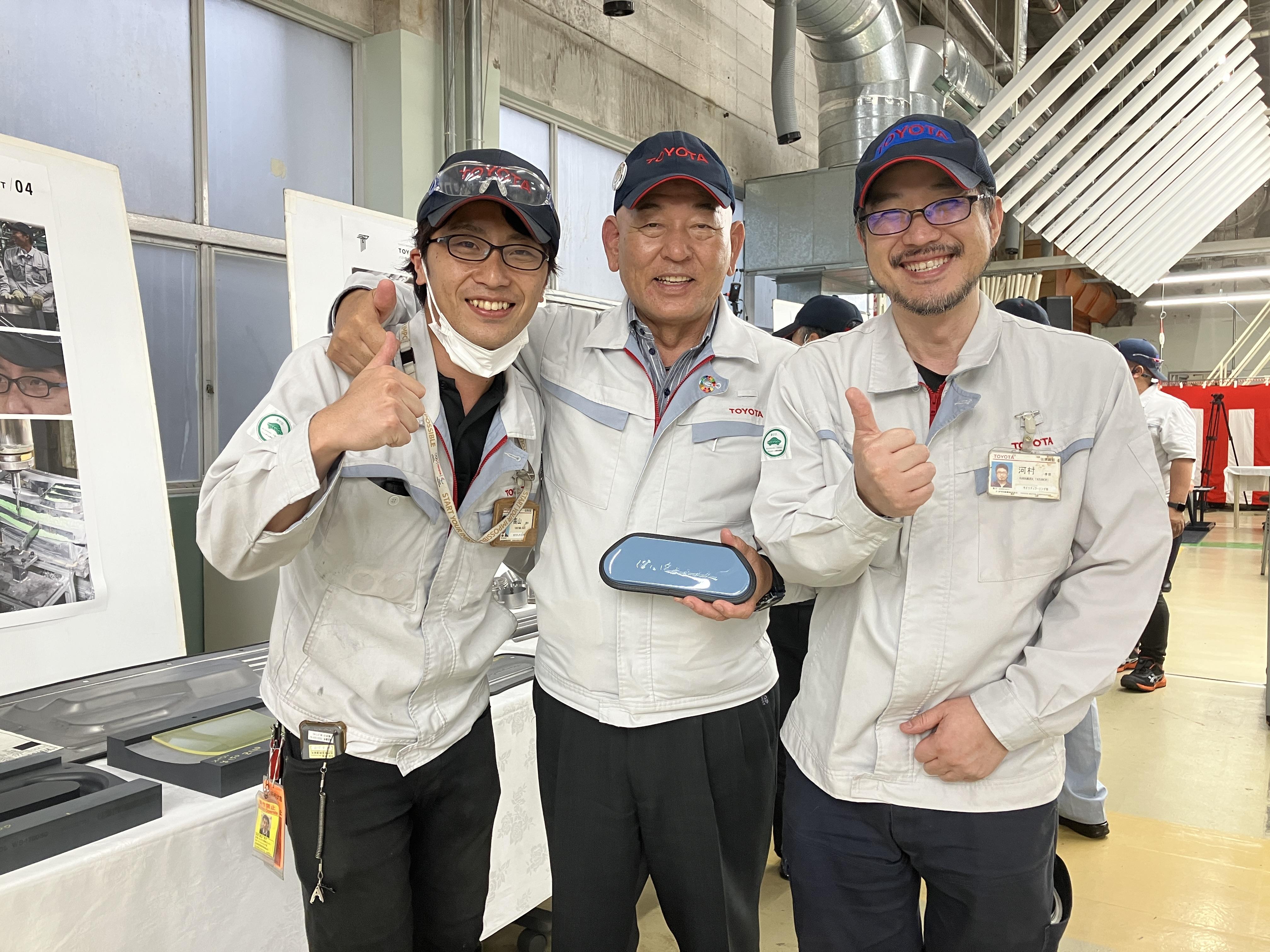
Part 7 of this series will look at how Toyota’s monozukuri DNA is being passed down to a younger generation of casting specialists.
(Text: Yasuhito Shibuya)