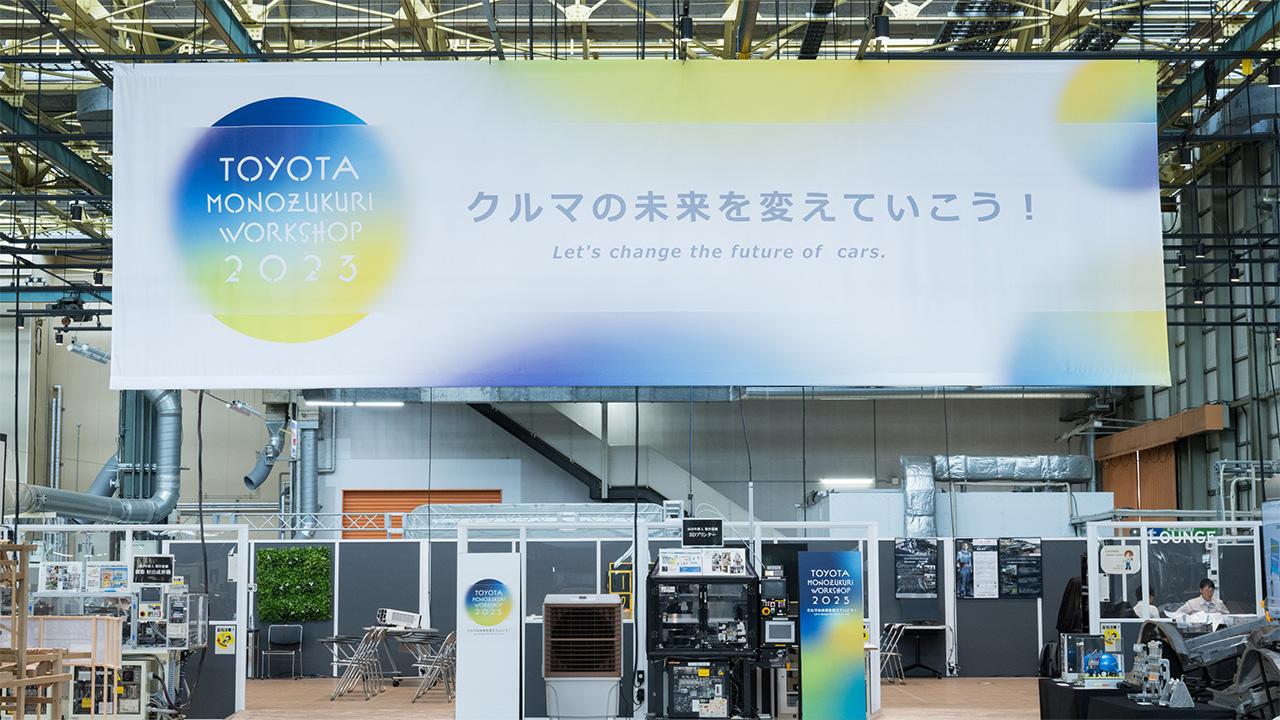
トヨタが誇る匠の技と革新技術で工程2分の1へ。クルマの未来を変えていく最新技術の数々を形にするモノづくりの現場を公開した。
ギガキャストに息づく匠の技能とTPS
鋳造部品を製造する明知工場は今年で50周年。6月の発表以降、注目されているギガキャスト*は、ここで開発が進められている。
*従来は数十に及ぶ部品と工程でつくっていた車体パーツを一体成型する技術。bZ4Xのリヤ部分であれば、86あった部品が1つになる。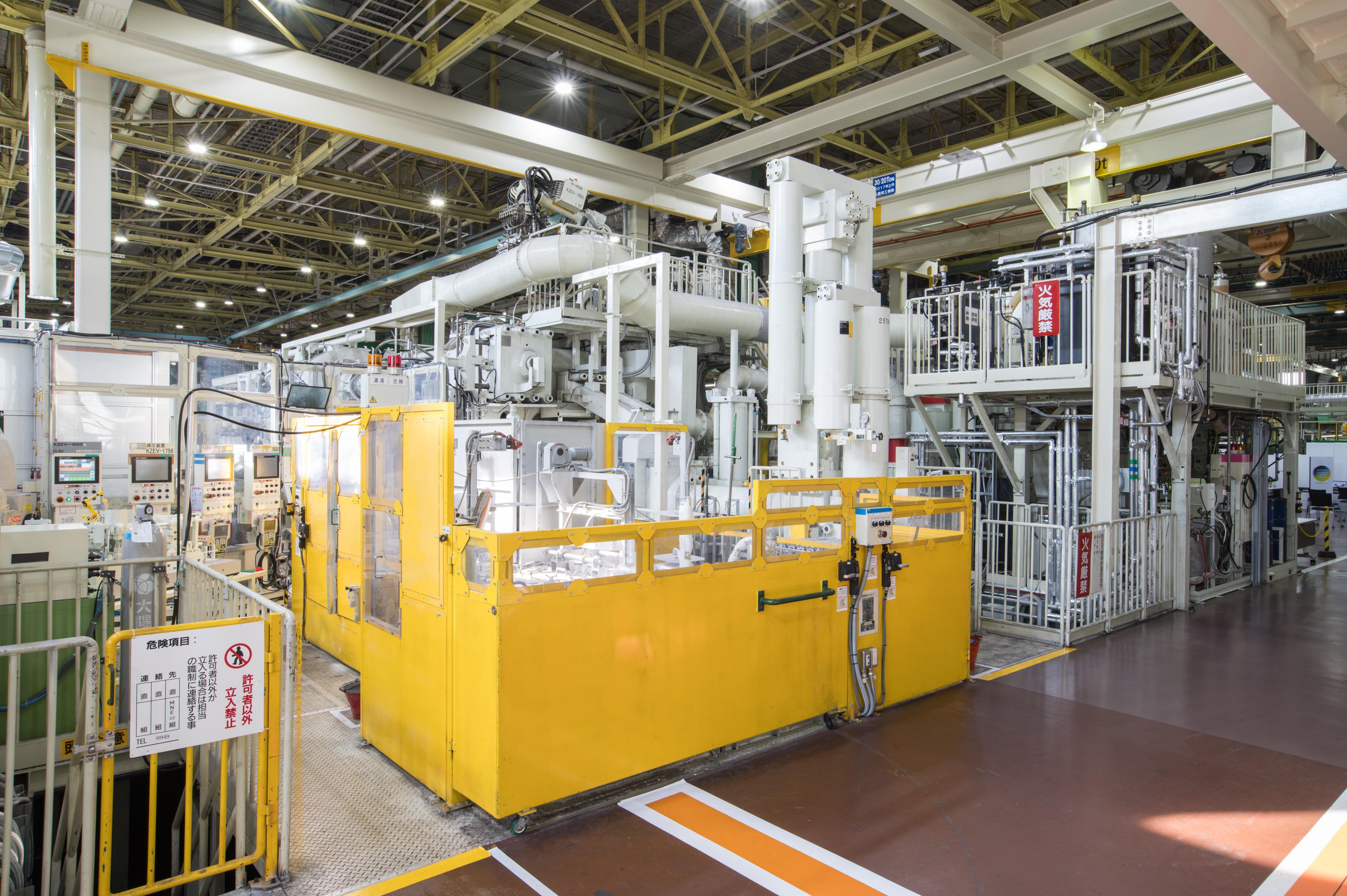
工程としては、まず、溶けたアルミ合金を高速・高圧で金型に射出。十数秒で700℃から250℃へと冷やし固めたのち、型を開いて一体成形した鋳造部品を取り出す。
現場では、ギガキャストを使った量産を見据え、2つのムダを減らして生産性を向上させる取り組みが紹介された。
1つ目のムダが、金型交換に要する「手待ちのムダ」だ。一般的な金型交換は、大型クレーンを使って24時間ほどかかることもある。これがギガキャストになると、金型の重量は100tを超え、さらにロスが発生する。
対してトヨタのギガキャストでは、金型を設備に設置したままの「汎用型」と車種ごとに異なる形状をした「専用型」に分割。交換する際は、コンパクトな専用型のみ汎用型から自動脱着する。
必要なときに、必要なものを、必要なだけ取り替えるジャスト・イン・タイムの型交換で、リードタイム20分以下を目指す。
この金型分割と自動脱着は、長年、自社で型設計から製作、メンテナンスを実施することで積み上げてきた改善の集合体。金型は鋳造の熱で膨張したり収縮したりすると汎用部と専用部がうまく合わず、専用部が外れなくなることもある。その隙間の寸法は金型の匠の技によって維持している。
2つ目のムダは「不良・手直しのムダ」。ギガキャストの解析技術に、トヨタはエンジンブロックなどの量産で蓄積してきた知見を反映した独自開発のシミュレーションソフトを活用。良品をつくるための条件や計算方法には、匠の技能も数値化して織り込まれている。
市販品を使うのが一般的な中、自社開発することで条件の追加や計算方法の変更にも対応可能に。事前に品質のつくり込みを行うことで、不良品の発生率低減につなげる。
鋳造を知り尽くした匠の技とムダを切り詰めリードタイムを極限まで短縮するTPS(トヨタ生産方式)の実践で新しいモノづくりをさらに改善、進化させていく。
知恵と工夫が可能にした混流生産ライン
元町工場は64年前に操業開始。現在、準備中のものも含め、9つの車種、4つのパワートレーン(動力源)、3つのボディタイプを1つのラインで流す、世界にも類を見ない混流生産工場だ。
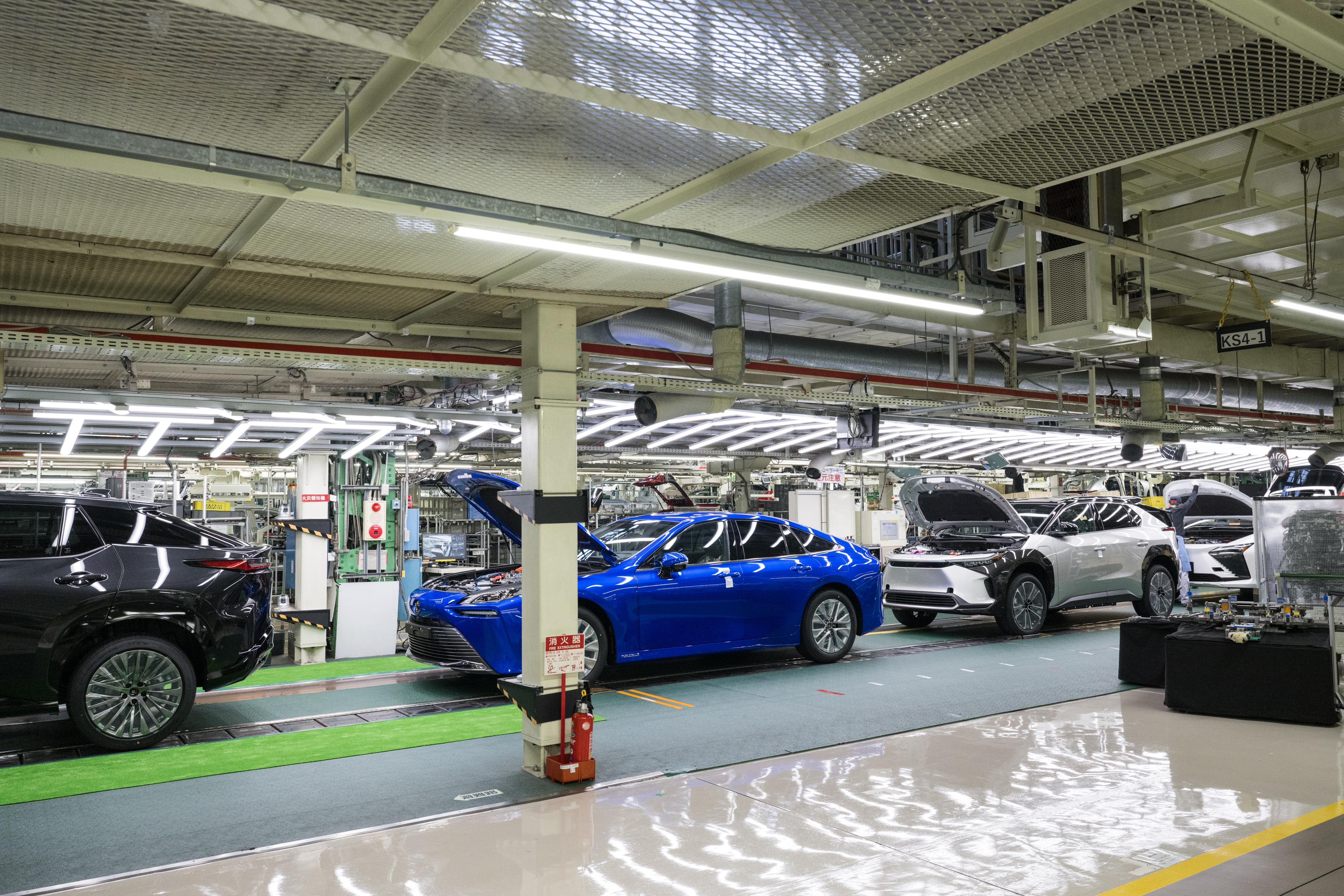
トヨタでは、TPSに基づき、同じ車種をまとめてつくるロット生産ではなく、オーダーの順番に基づいて、クルマをつくる「1個流し」の生産を行っている。
そのため、このラインでは、セダンの次にSUV、さらにはミニバンと形の違うクルマが次々と流れてくる。
当然のことながら、クルマが違えば、作業時間や工程に差が生まれる。しかし、お客様のニーズに応じて、作業時間が均等になるよう最適な工程編成を行い、工数差を吸収することで、効率を落とさない生産を行っている。
現場では、異なるパワーユニットを同じ工程で車両に組み付けるための工夫として「UM(Universal Modular)トレイ」と呼ばれる台車が活用されていた。
ラインには、HEVエンジン、e-Axle、FCスタックなど、形や重さも異なるパワーユニットが流れてくる。
それらを載せる台車はベース部分を共通化し、簡易的なアタッチメントを取り換えるだけで、どんなパワーユニットでも対応できる。まさに、現場と製造技術のエンジニアが一体で知恵を出し、1個流しに対応したアイテムだ。
その他にも混流生産を可能にしたさまざまな現場の工夫があった。詳しくは、過去のトヨタイムズの記事を参照してほしい。
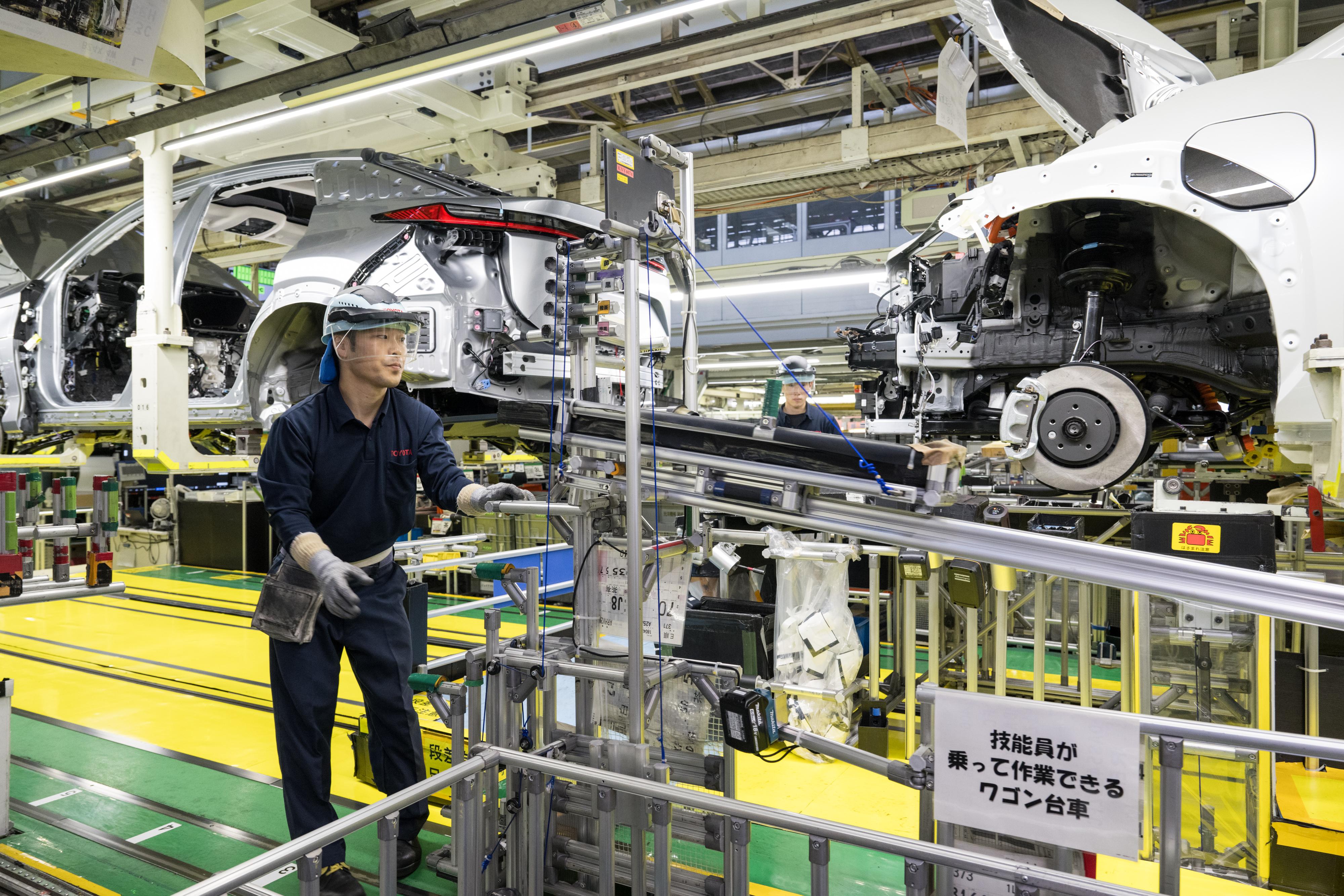
デジタルツインは設備づくり、人づくりにも
ここからは、工場の設備づくりにデジタル技術が活用されている事例を紹介したい。
通常、設備づくりにおいては、設計、部品加工、設備組付という流れを経てはじめて、現場の作業者が実物に触れることになる。
ところが、設計段階で図面ができても、部品を加工しようとしたら形状的に加工できない。設備を調整しようとしたら正しく動かない。設備を使う人からは「作業しにくい」という指摘が入るなど、さまざまに発生するやり直し、すなわち「不良・手直しのムダ」が、製作リードタイムの大きな割合を占めていた。
そこで現在、トヨタは3D図面を使い、設計図をつくり上げるタイミングで、後工程となる作業現場の従業員らも一緒に見ながら、知恵を出し合い、図面に織り込むプロセスをとっている。
つまり、設備づくりの工程全体をスルーでとらえ、働き方を改革。仕事の前出しと同期化でやり直しゼロを目指し、リードタイムの短縮に取り組んでいる。
貞宝工場では、手づくりの150インチのモニターに、実寸大の設備モデルを投影して、実際の作業の動きを検証することで、より完成度の高い図面をつくり込んでいる事例が紹介された。
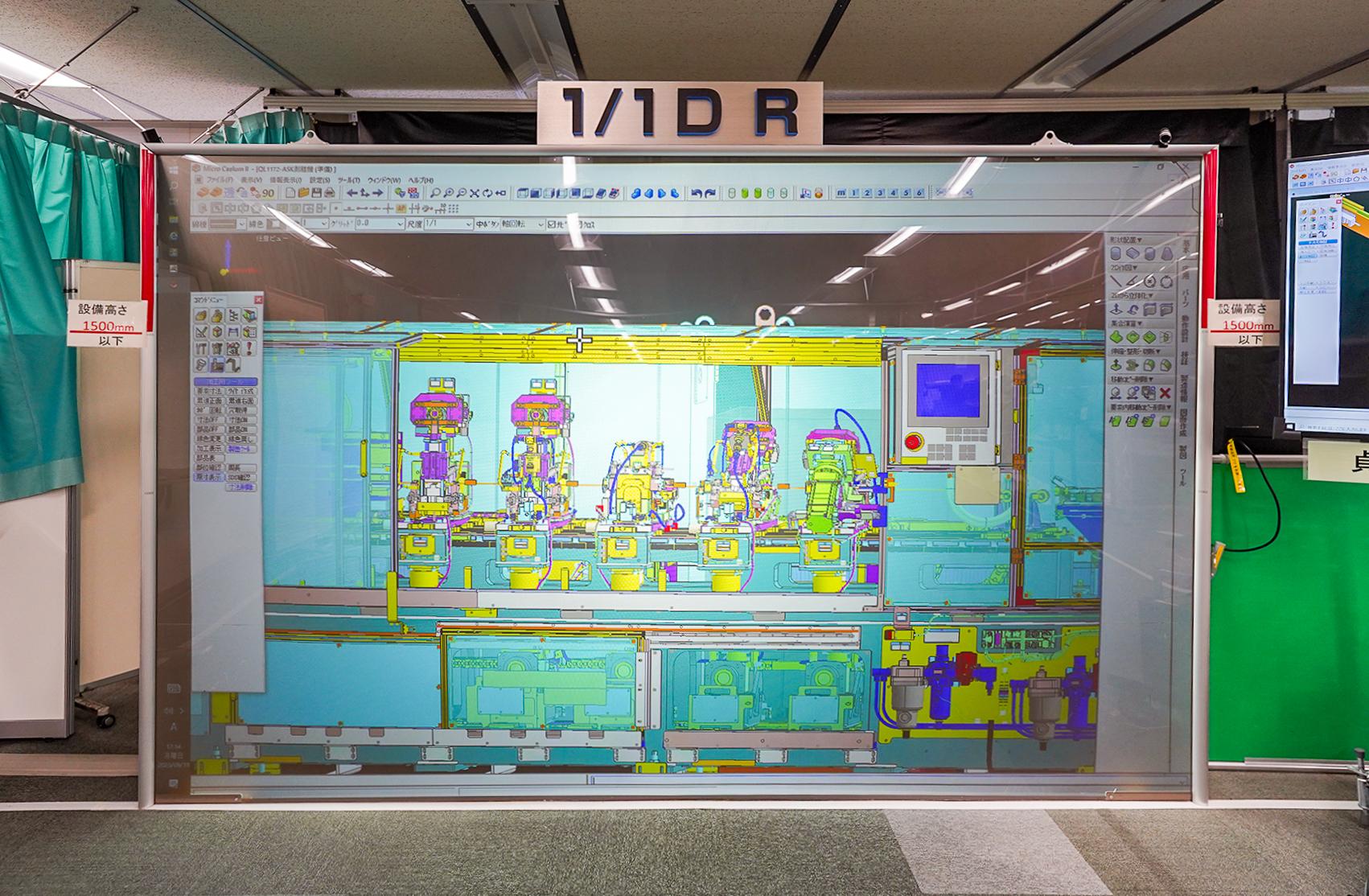
また、モニターだけではイメージできない機器の奥行きや、設備が工場にどのように設置されるかについても、デジタル技術を使ってイメージできるようにしている。
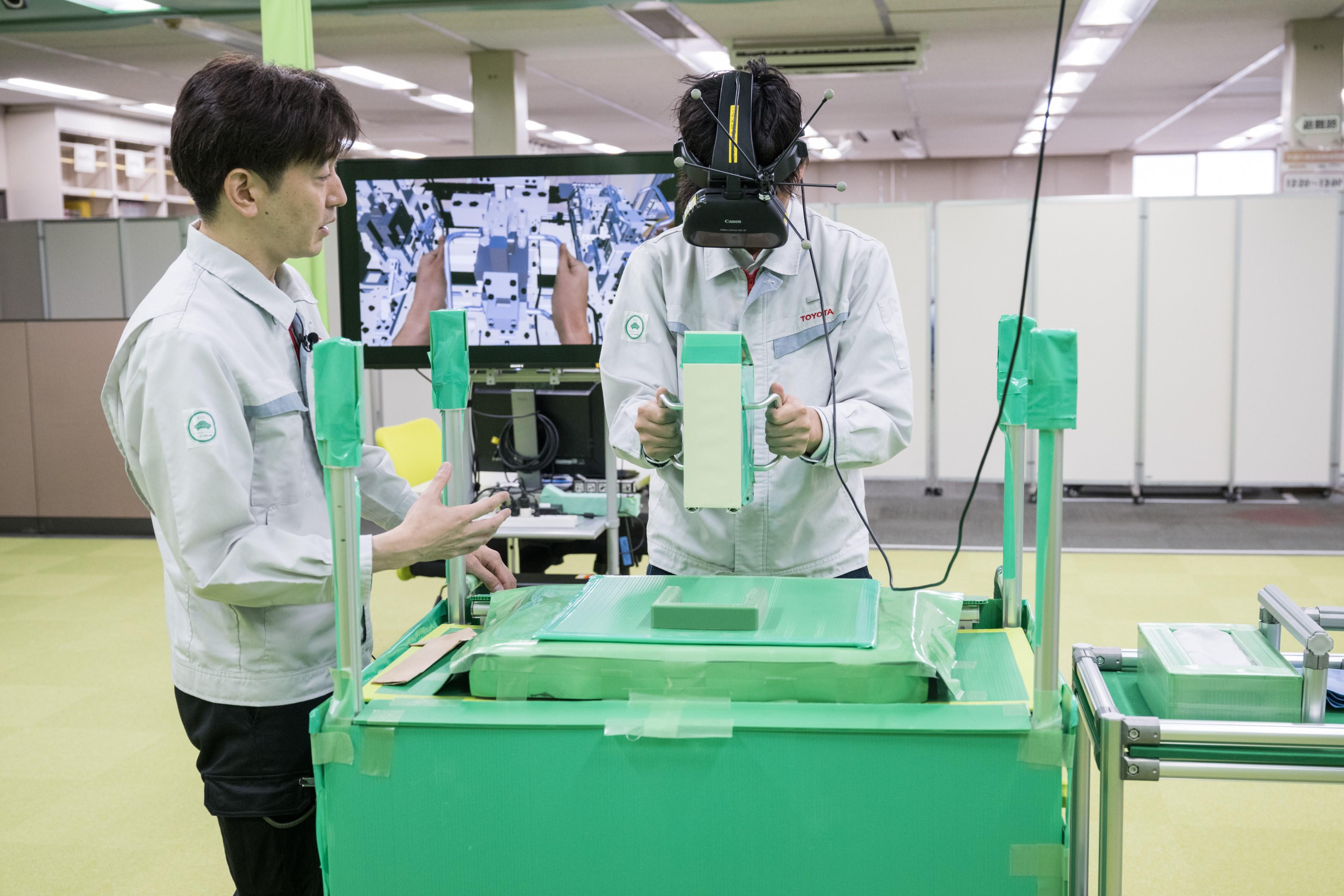
結果として仕事のやり直しは10分の1、製作リードタイムは2分の1に短縮。さらに、設備費は4分の3に低減された。
現在、このようなデジタル技術を活用したモノづくりをトヨタグループや協力メーカーへ展開し、グループ全体で競争力の最大化を図っている。
こうした技術が使われているのは、新しい設備の開発だけではない。
金属部品を生産する加工設備では、刃物投入の自動化をデジタル上で実現し、現場に転写した取り組みを紹介。
また、現場の人財育成では、言葉で伝えづらく、暗黙知となりがちな匠の技能をAR技術を使って身につけられるようにした訓練機なども紹介された。
これらはどちらも、現場でモノづくりをしてきた従業員が、デジタルを勉強して自らつくり上げたものだ。
モノづくり開発センターの近藤禎人センター長は「豊田章男会長の『3年でデジタル世界一になるぞ』という掛け声のもと、さまざまな現場で、働く人自らデジタルが使えるようになり、その土台ができてきた。こういった活動で生まれたものが、これから量産工場に展開されていくフェーズになってくるので期待してほしい」と語った。
一般的なデジタル活用では、デジタルで検討したものを現場に展開するという「一方通行」で終わっていることも少なくない中、トヨタでは、現場の改善をデジタル化し、さらに改善して、現場に戻す「双方向型デジタルツイン」で、常に進化し続ける工場を目指している。