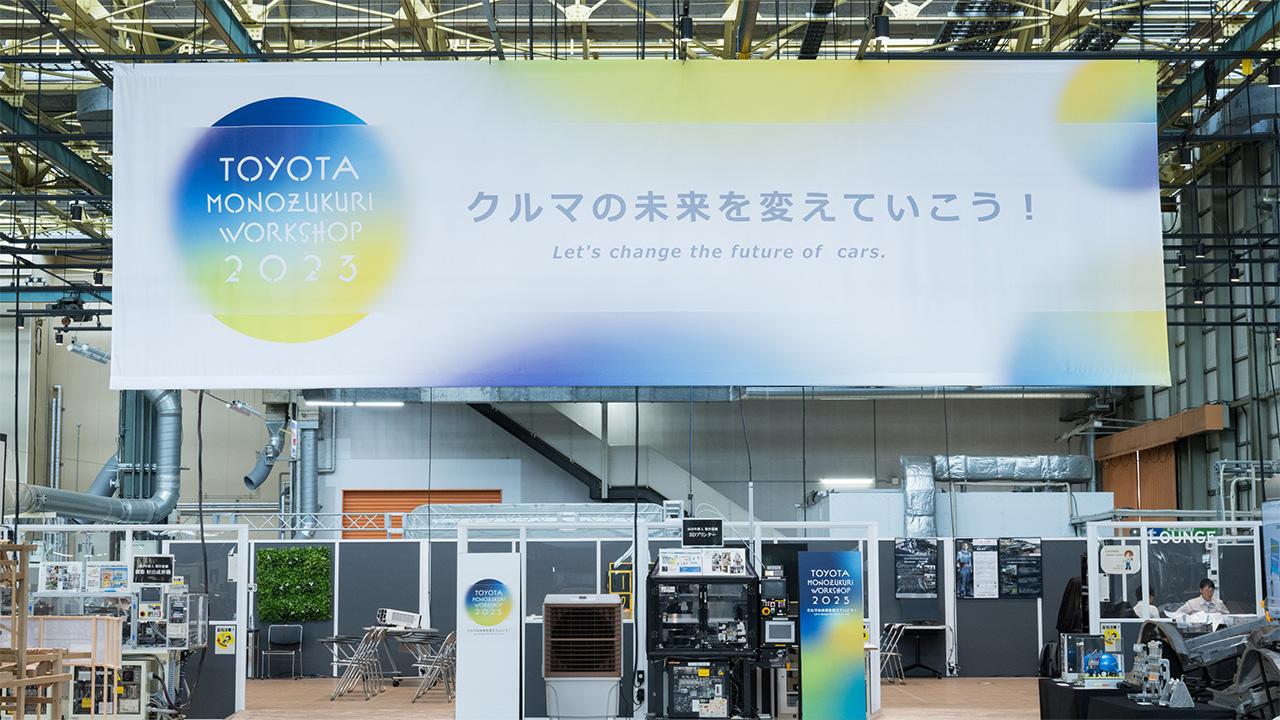
トヨタが誇る匠の技と革新技術で工程2分の1へ。クルマの未来を変えていく最新技術の数々を形にするモノづくりの現場を公開した。
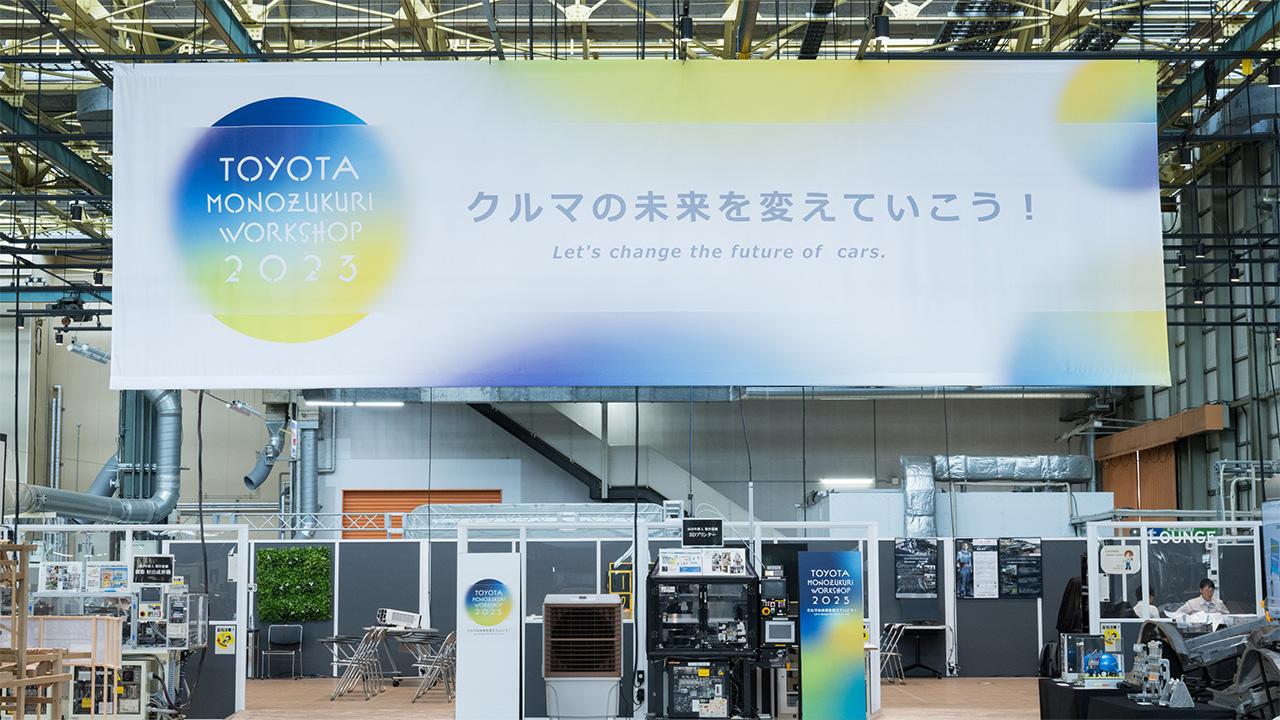
蒸気が上がる鋳造設備から現れた巨大部品。寸分違わず積み重なる電池。AR(拡張現実:Augmented Reality)で再現された匠の技――。
トヨタ自動車は9月、貞宝・元町(愛知県豊田市)・明知(同みよし市)の3工場を報道陣に公開した。
「モノづくりワークショップ」と銘打つ今回のイベント。6月の「テクニカルワークショップ」で発表した先進技術を形にするモノづくりを披露した。
貞宝工場は、「無」から「有」を生み出すスタートアップ拠点。クルマづくりを支える設備や工法、新しいモビリティをリードするモノづくりを担っている。
明知工場は、匠の技と革新技術が融合する鋳造工場。1,000分の1秒を争うモータースポーツのエンジン部品もここから生まれている。
元町工場は、マルチパスウェイの量産プラント。HEV(ハイブリッド車)、BEV(電気自動車)、FCEV(燃料電池車)など9つの車種を1つのラインでつくり出す。
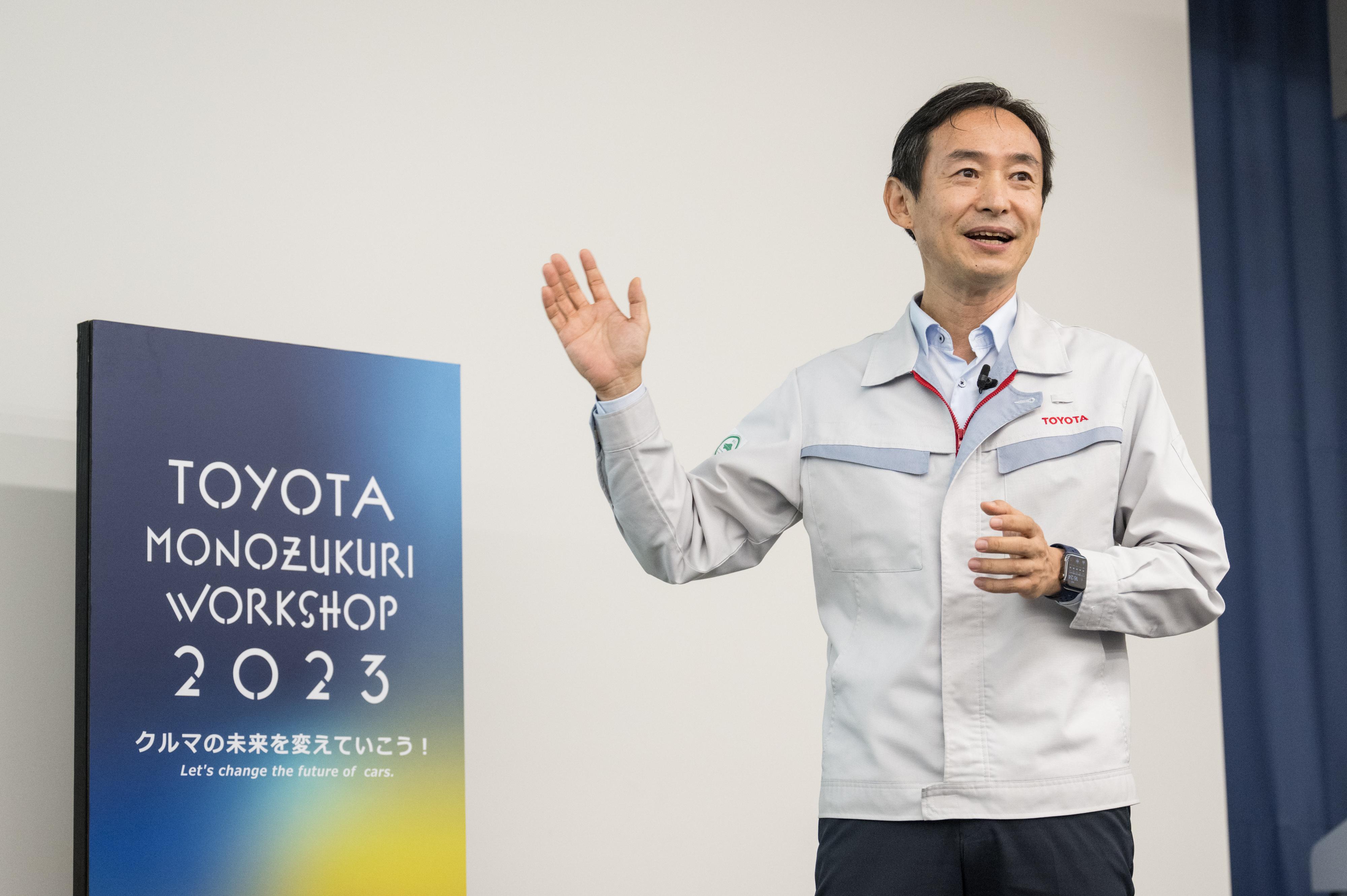
生産トップの新郷和晃CPO(Chief Production Officer)は「トヨタの持つ技とデジタル・革新技術で工程2分の1を実現する。開発と生産の垣根をなくし、新しいモビリティをすばやく提供し、工場のカーボンニュートラルや物流など、モノづくりの基盤の課題解決も一緒に行っていく」と決意を語った。
トヨタの技を受け継ぎ、デジタルとの融合により進化しようとするモノづくりの数々。トヨタイムズでは、今回公開された現場を紹介する。
クルマの未来を支える次世代電池ライン
6月のテクニカルワークショップで最も注目を集めたのが全固体電池をはじめとする、トヨタのバッテリー技術だった。その量産に向けて、準備を進めているのが貞宝工場だ。
これまでも、モーター、バッテリー、燃料電池など、新しい製品を生み出すための設備を製造してきた同工場では、設備設計から、組付、量産工場への導入までを担っている。
充電時間が短く、航続距離が長い全固体電池は、2027~2028年の実用化を目指して開発が進められており、製品とともに、量産工法の開発段階に入っている。
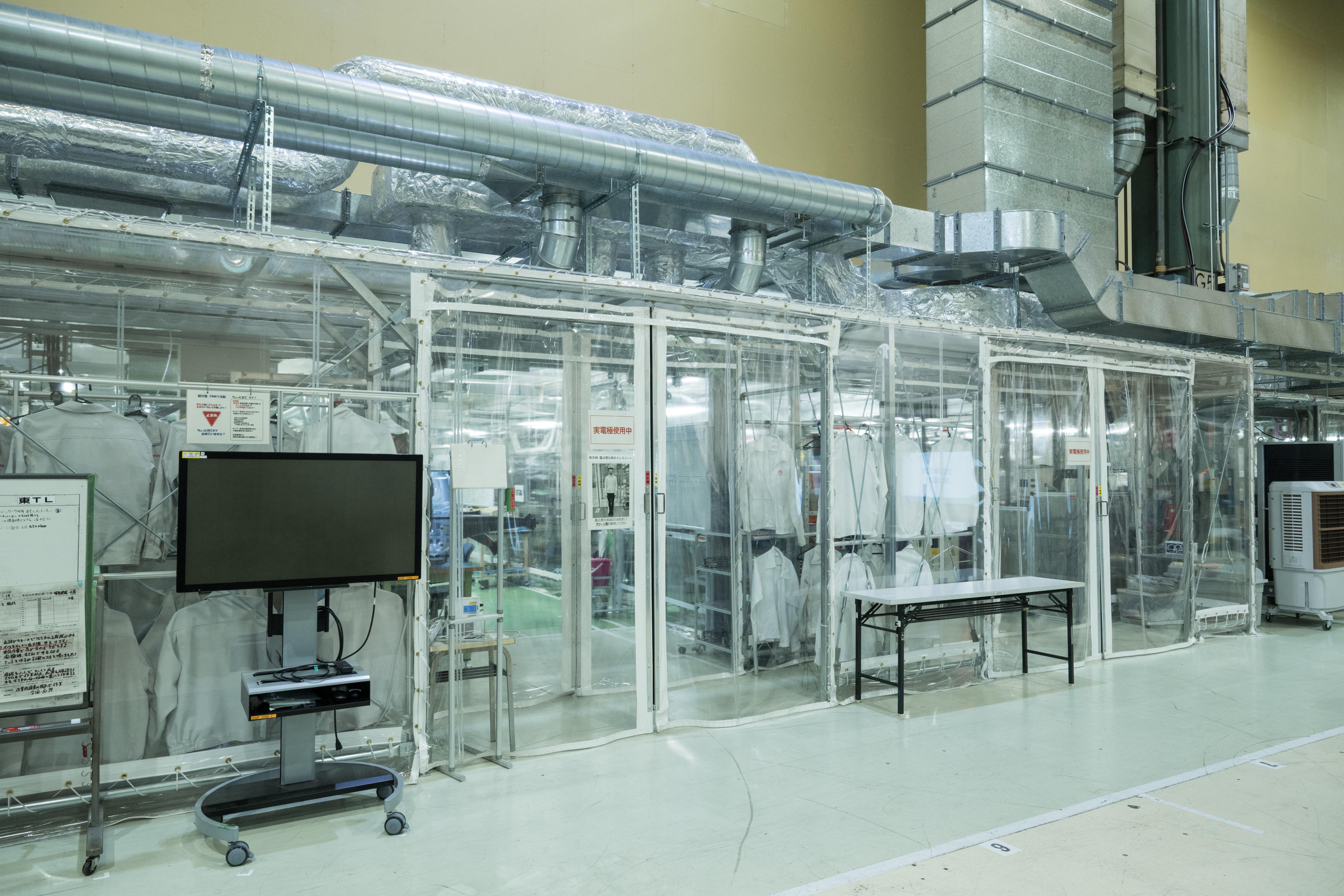
現行の電池は大きく分けて材料加工→電池加工→電池組立の工程でつくられる。
全固体電池でも順番は同じだが、特に電池組立工程では、速く、電池を傷つけず、精度よく積むことが性能を担保し、量産化する上でのキー技術となる。
そこで、開発した設備では、電池を積む際に、運んでいるパレットと受け取るパレットの流れる速さが同じ、すなわち、相対速度が0になるよう制御。
さらに、パレットと設備に備わったからくり機構によってズレを防ぎながら電池を受け渡す。このようにして、量産に不可欠な、高速・高精度での積層を実現している。
もう一つ、公開されたのが、超大型のバイポーラ構造をとる、次世代電池普及版の生産設備だ。
通常の電池は、1枚の集電体に正極か負極のどちらかを塗り、正極だけの集電体と負極だけの集電体の2枚1セットの構造をとっている(下図左)。対して、バイポーラでは1枚の集電体の表裏に正極と負極を塗るシンプルな構造をとっており、部品点数を3分の1に抑えることができる(同右)。
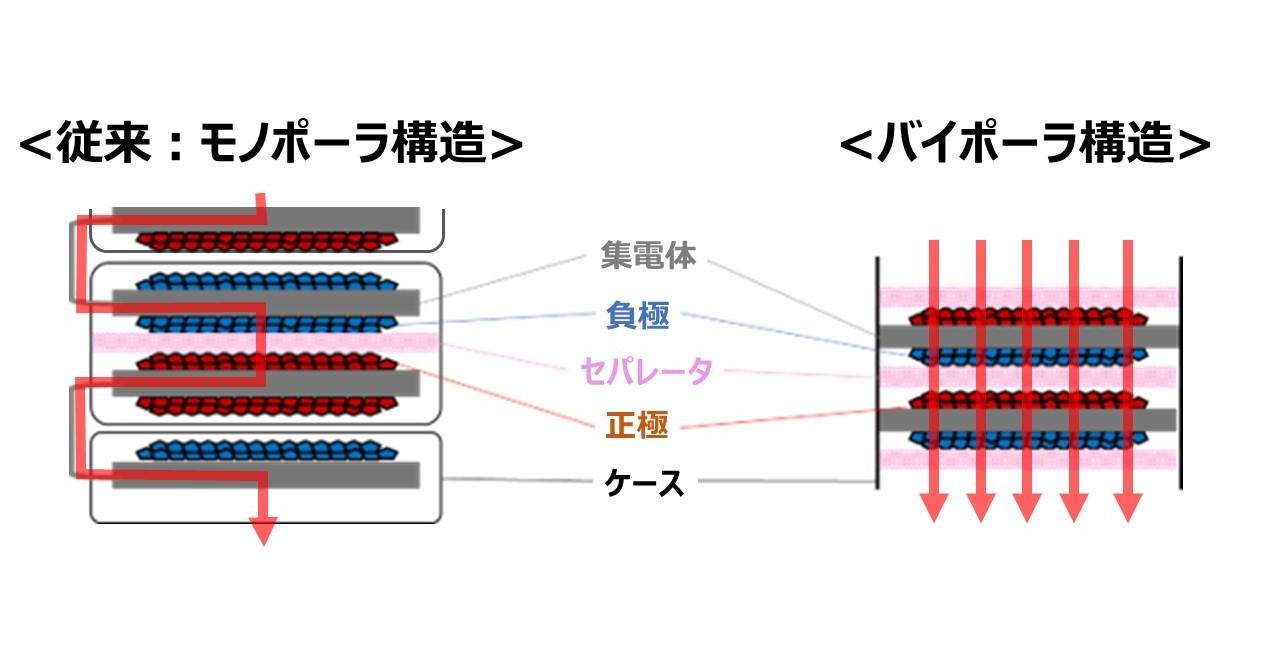
加えて、正極にニッケルやコバルトなどの希少金属を使わず、LFP(リン酸鉄リチウム)を用いることで材料費も削減。
エネルギー密度は下がるものの、バイポーラ構造による少部品化で得られた容積の分、集電体に塗るLFPを厚く塗ることで電池容量をカバーしている。
しかし、この電池を実現するうえでは、①材料を正極、負極に均一にきれいに塗る、②高速加工、③全てのセルを一度に密閉するという難しさがある。しかもそれをクルマに使えるだけの超大型電池で実現する必要があった。
このような課題を解決するため、HEVで培ってきた26年間の電池生産技術をベースに、バイポーラ型ニッケル水素電池での技術やノウハウ、FCEVで培ってきた精密塗工、さらにはデジタル技術も活用しながら開発を進めている。
自走組立ラインで工場の景色が変わる
6月にBEVファクトリーの加藤武郎プレジデントが打ち出した「BEVハーフ」構想。
「新モジュール構造と自走生産で工程と工場投資を2分の1に、さらに、デジタルツイン*の力で、生産準備に要するリードタイムを2分の1にする」と宣言した。
*双子のように現実世界をデジタル上に再現し、シミュレーションなどに役立てる方法。今回、元町工場で紹介された新モジュール構造では、アンダーボディ(車両前方のフレームからキャビン・トランクのフロアをあわせたボディ下部)をフロント、センター、リヤと大きく3つに分割し、それぞれ部品を組み付けていく。
車両の中に人が入り込んで組み付ける必要がなくなるため、作業効率の向上が見込まれている。
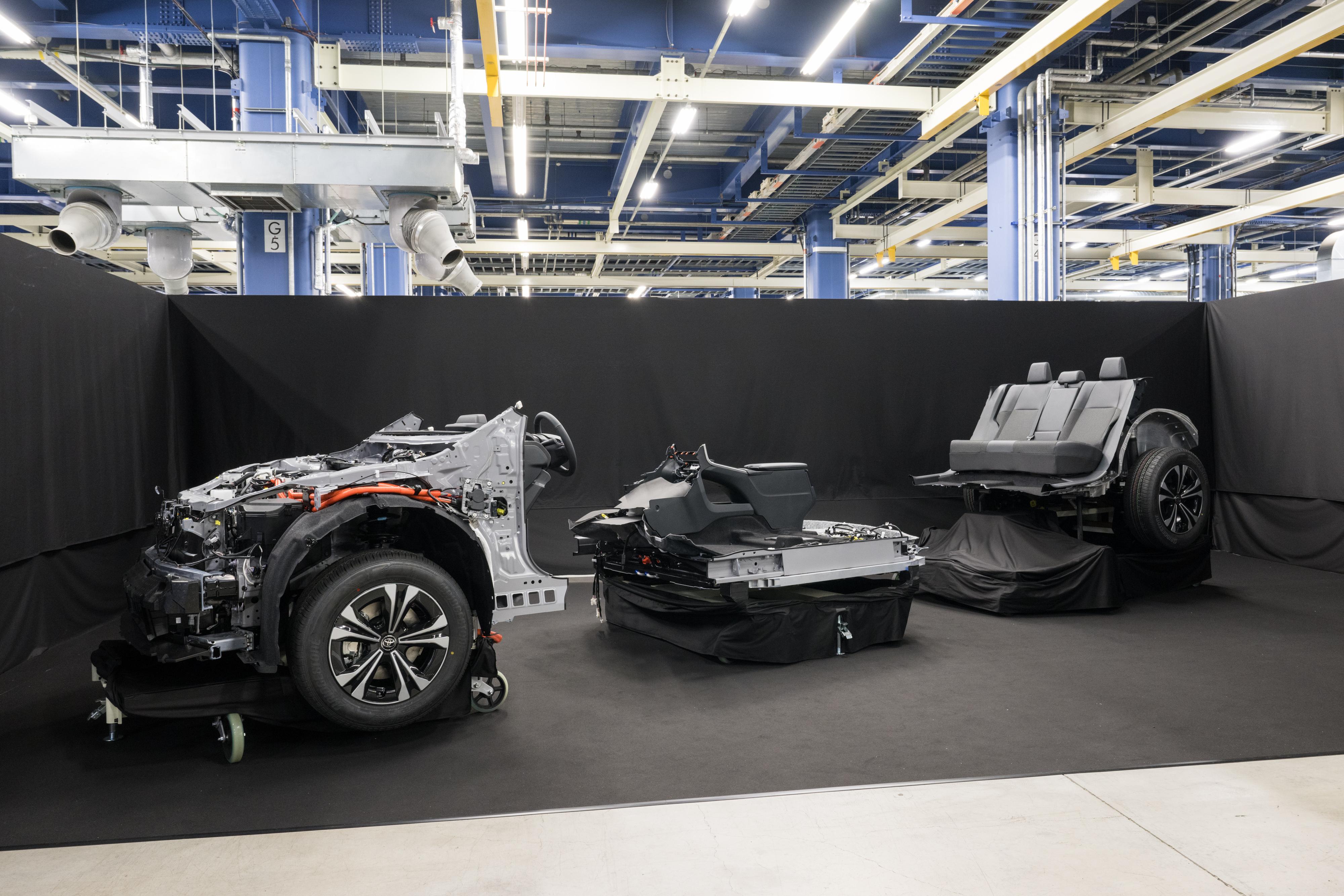
3つのモジュールごとに部品を組み付け、結合した後にクルマは自走。この新しい車両構造では、屋根もサイドパネルもついていない状態でシートの組み付けなどができるので、ロボットも単純な構造・動作となり、設備もシンプルになる。
この自走組立ラインには、トヨタがこれまで自動運転開発で培ってきたセンシング技術や車両制御技術が活用されている。
工場内のカメラがクルマを認識し、設定された経路を時速0.36kmで進むように制御。
車両を搬送する必要はなくなり、工場のレイアウトの自由度は増えた。設備投資は数十億円削減、新型車の切り替えにかかっていた年単位のリードタイムも大幅に短くなるという。
ノア・ヴォクシーの溶接工程の一部では、無人搬送ロボットを活用したシンプルなラインコンセプトが実証済みで、次世代BEVの設備開発に向けて、課題のフィードバックが図られている。

開発を担当した従業員は、「働く人にやさしく、リードタイムを短縮するとともに、コスト削減もできて、競争力を高めることができる」と狙いを語った。
工場設備と量産車の開発から生産まで、あらゆる工程を手の内化しているトヨタ。強みを生かし、できる限り重厚長大な搬送機をなくして、より柔軟に変化に対応できるよう、シンプルな作業、自動化を目指していく。