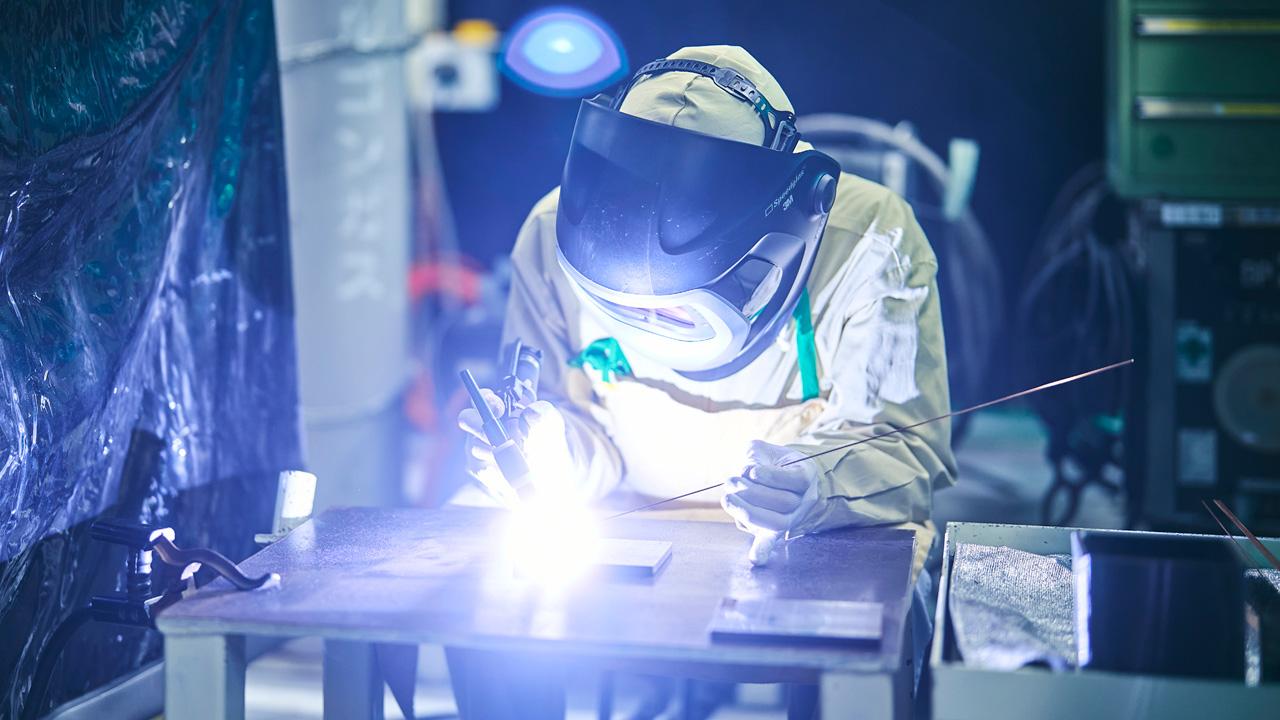
自動車業界を匠の技で支える「職人」特集。第13回は5000度の超高温を操り独自の技術で金属やアルミを接合する「溶接の匠」に話を聞く
トヨタ初の快挙
日々溶接の面白さ、難しさと向き合っていた三木に入社して9年目の1986年、大きな転機が訪れる。三木の技能を認めた上司から「溶接技術競技会に出てみないか」と声が掛かったのだ。
溶接技術競技会は、日本溶接協会があらゆる工業分野に欠かせない溶接技術の振興のために1954年から開催している競技会。溶接技能者が年に1度、全国から集まってその技能の頂点を競う。
それまでトヨタはこの溶接技術競技会に参加しているが、全国大会で3位以内の入賞がなかった(最高位は4位)。そして三木は社内で集められた技能者30人ほどの中から愛知県大会に出場できる4人のひとりに選ばれたが、大会では6位入賞の成績だった。
三木
全国大会には県大会で1位になった者しか行けないので、私は参加できませんでした。悔しいので翌年に再チャレンジして、全国大会の出場を目指しました。
当時、本社にあった学園本館に実習場がありました。腕自慢が集まって社内選考会をやって4位以内に入れると、その訓練場で1、2カ月、通常の仕事を免除されて技能の特訓を受ける。そして愛知県大会で優勝すると全国大会に行けるんです。
再チャレンジとなった1987年の溶接技術競技会で三木は愛知県大会1位を獲得。全国大会に出場して3位入賞を果たす。これはトヨタ自動車としては初の、記念すべき溶接技術大会での初入賞だった。
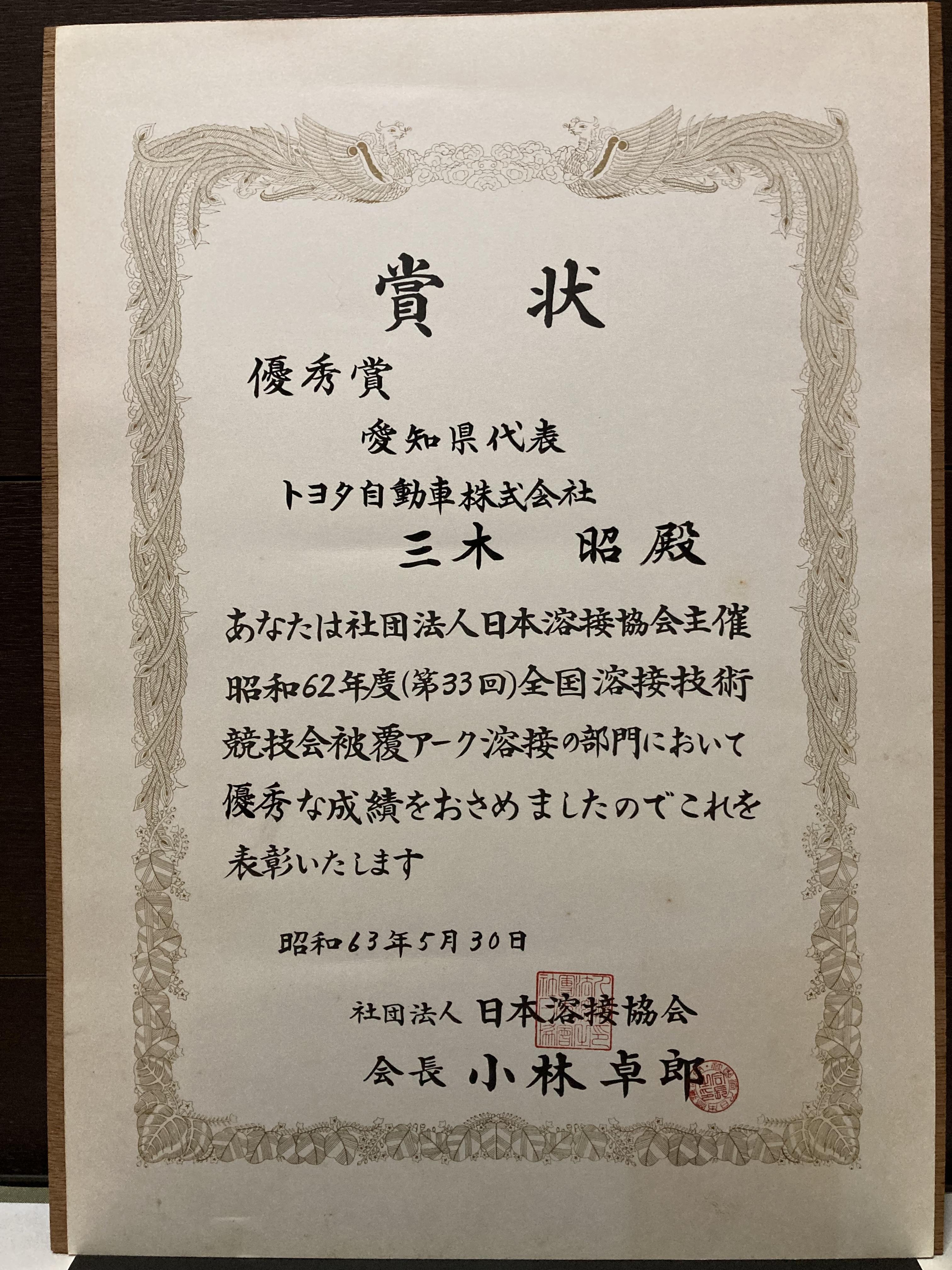
1988年から三木は人材開発部(現トヨタ技能者養成所)で、やはり溶接技術競技会に出場する後輩たちの指導員をしながら、さらに溶接の技能を磨いて、社内で「溶接の匠」として知られるようになる。
難易度最高峰、鋳物製金型の「肉盛り溶接」とは?
クルマづくりではさまざまな場面で溶接という技能が使われている。そしてさまざまな溶接の中でも三木が得意とする、現場が誰よりも三木を頼りにする溶接のひとつが、ボデーパネルを製造するための、長さ数メートル、重さ何10トンもあるプレス金型の肉盛り溶接だ。
なお、こうしたプレス金型がどのようなもので、どのように使われるかは、本連載の第5回「プレス金型製作の匠」で紹介しているので、ぜひそちらもお読みいただきたい。
ボデーパネルをつくるプレス金型には、1/1000㎜(=1ミクロン)単位の精度が求められる。プレス金型職人は、ボデーパネルのもととなる鋼板を何度も試しにプレスして、繊細な目と指先でプレス金型の表面の問題点を見つけ、切削工具やヤスリ、砥石を使って修正する。
だがこの金型の修正では、表面を削るばかりでなく、逆に盛り上げなければならない場合もある。そこで必要になるのが、鋳物製のプレス金型のへこんで足りない部分への金属素材の「肉盛り溶接」だ。
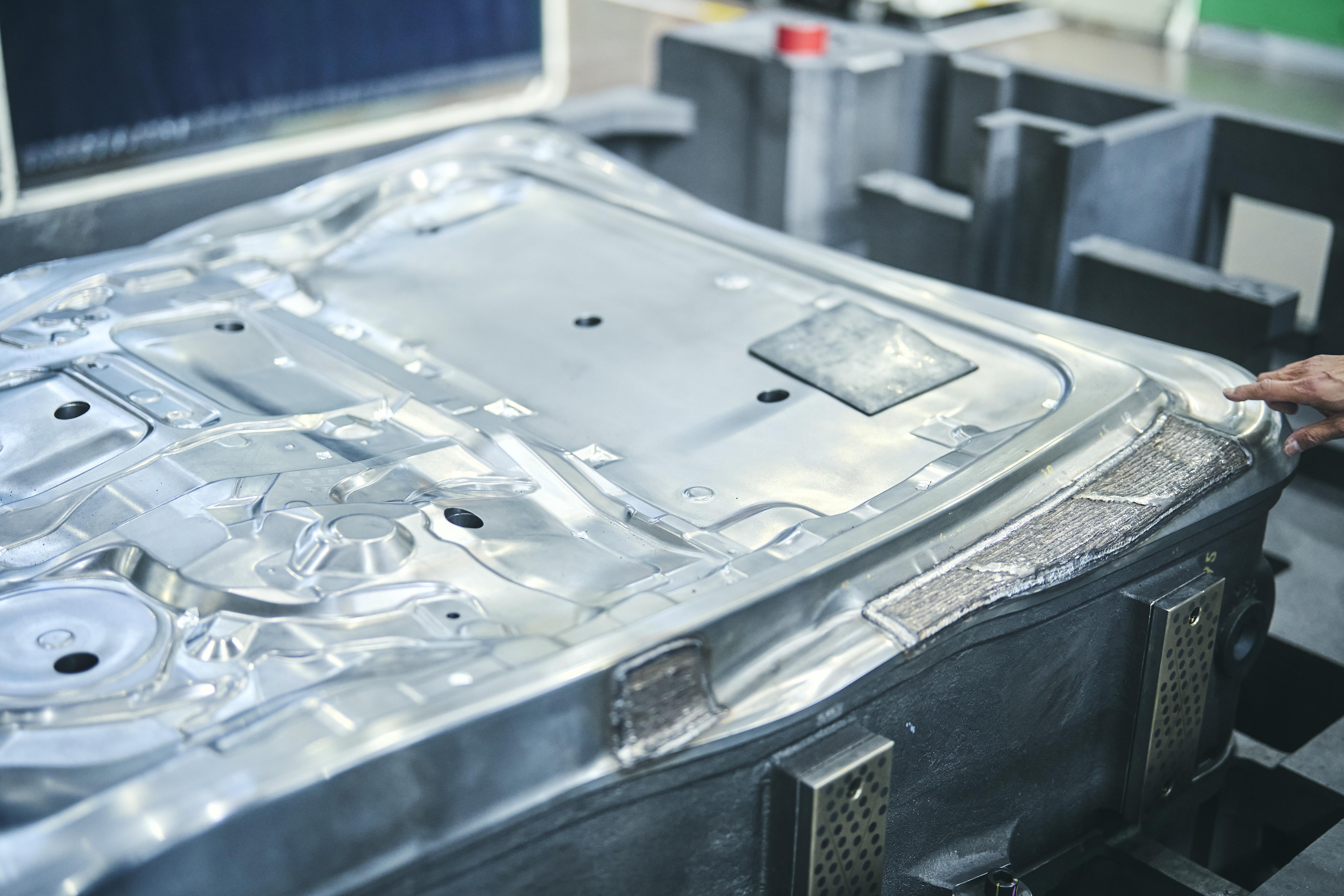
三木
一般的な鋼板より金属表面の素材のバラツキが多い鋳物への溶接は難しいものです。
しかも大型プレス機の金型には常に強い圧力が掛かるので、金型とそこに盛り上げて足す金属材料を完璧に一体化させないと、肉盛り箇所が脱落してパネルに不良が発生してしまいます。
また盛り上げ過ぎると、プレス金型の仕上げ加工が大変になってしまう。溶接が下手くそな人がやると、盛り上げ過ぎてボコボコになってしまう。
重要なのは必要な分だけできるだけ薄く盛り上げることです。金型の最終的な仕上げの精度を考えると、盛り上げるのは仕上げ加工のことを考えても0.1㎜程度の精度にしたい。しかも金型と完全に一体化させないと駄目です。
まあ、最終的には削るために盛り上げているわけだから、肉盛り溶接は黒子のような仕事。でも、クルマづくりの現場にはその大変さを理解してくれる人がいるからやりがいがあります。
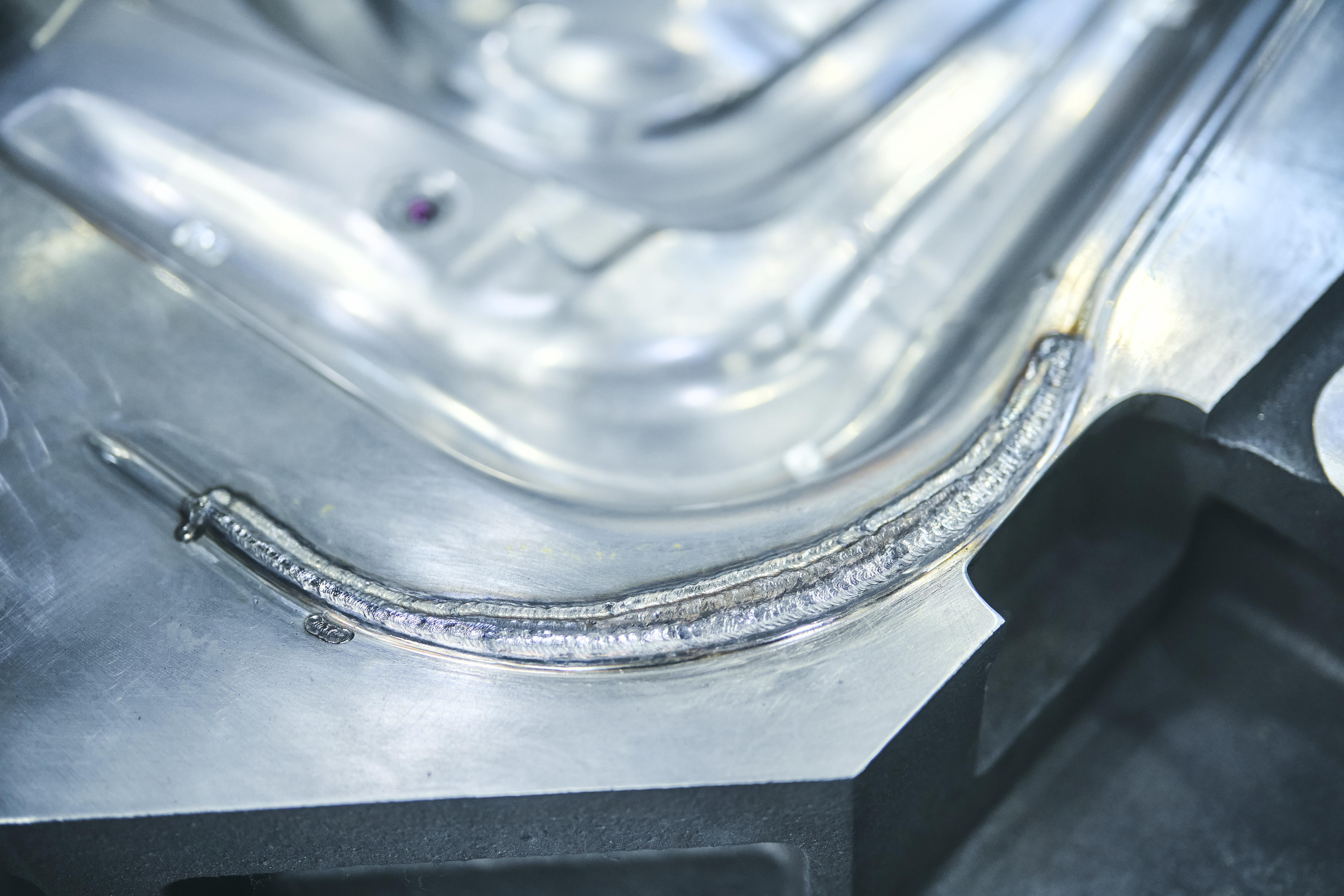
後編では三木が現在取り組んでいる人材育成と、最高難度のアルミ溶接、さらに三木が語る溶接という技能の魅力についてお伝えする。
(文・渋谷康人 写真・高柳健)