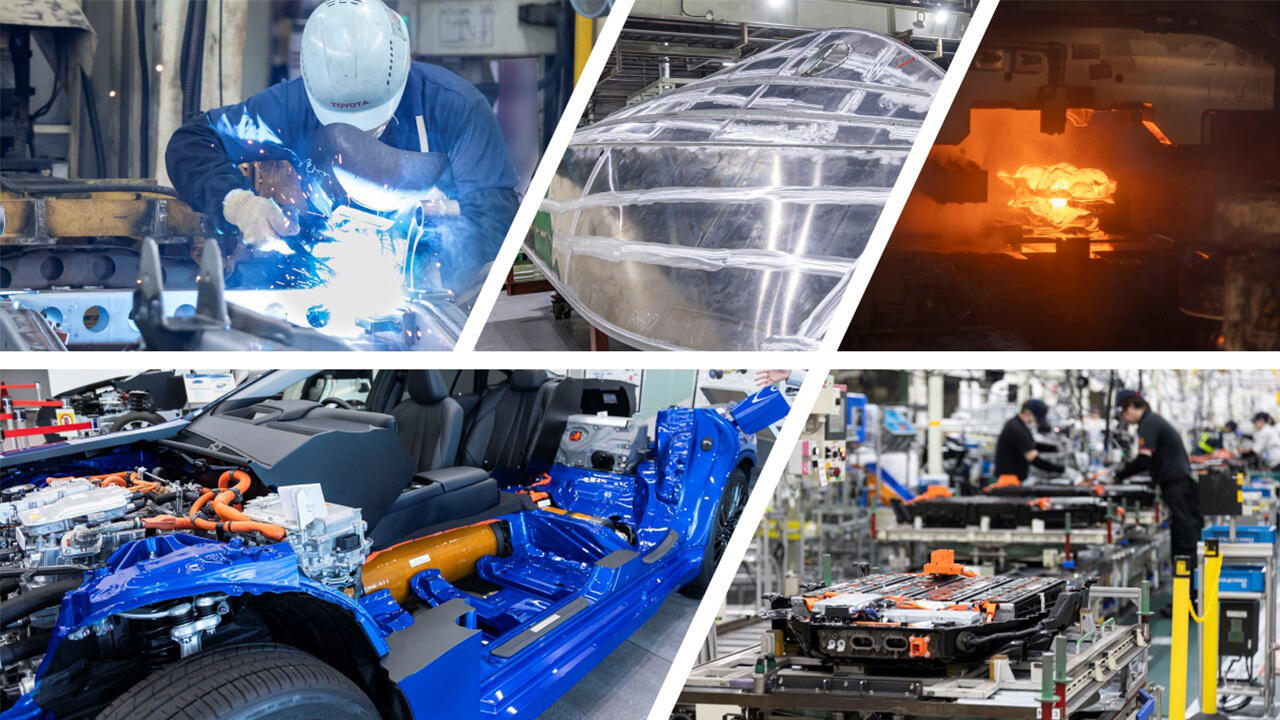
トヨタの各工場の歴史と、目指していく進化を紹介する連載シリーズ「トヨタ工場の継承と進化」。今回は、本社工場の現在と未来への挑戦を紹介。
【FC製造部】異物混入との果てしなき闘い
「100マイクロメートルの異物も許さない」。地道な分析とメンバーの意識改革、仕入先とのワンチームとなった活動で、異物不良率を劇的に改善させたのが、本社工場で最も新しい、2017年に設立されたFC製造部だ。
FC製造部が主に生産しているのは、第2世代MIRAIに搭載するFCスタック。
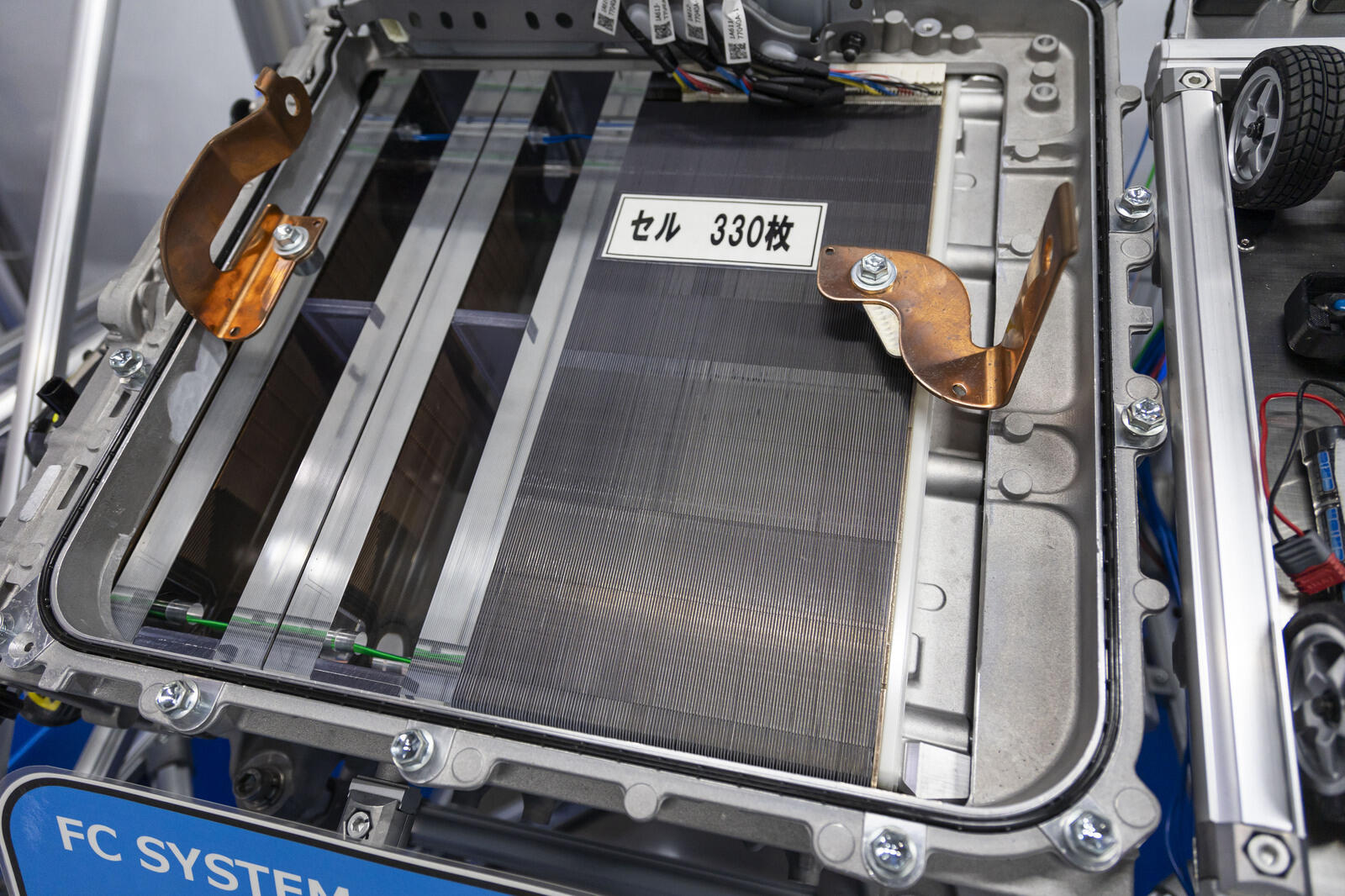
第2世代のFCスタックには、厚さ約1mmのセルが330枚並び、第1世代から比べて、大幅な性能向上を達成した。その一方で、セルの内部にわずか100マイクロメートル(米粒の50分の1ほど)の鉄異物が1つ混入するだけで、品質劣化を招いてしまうという。
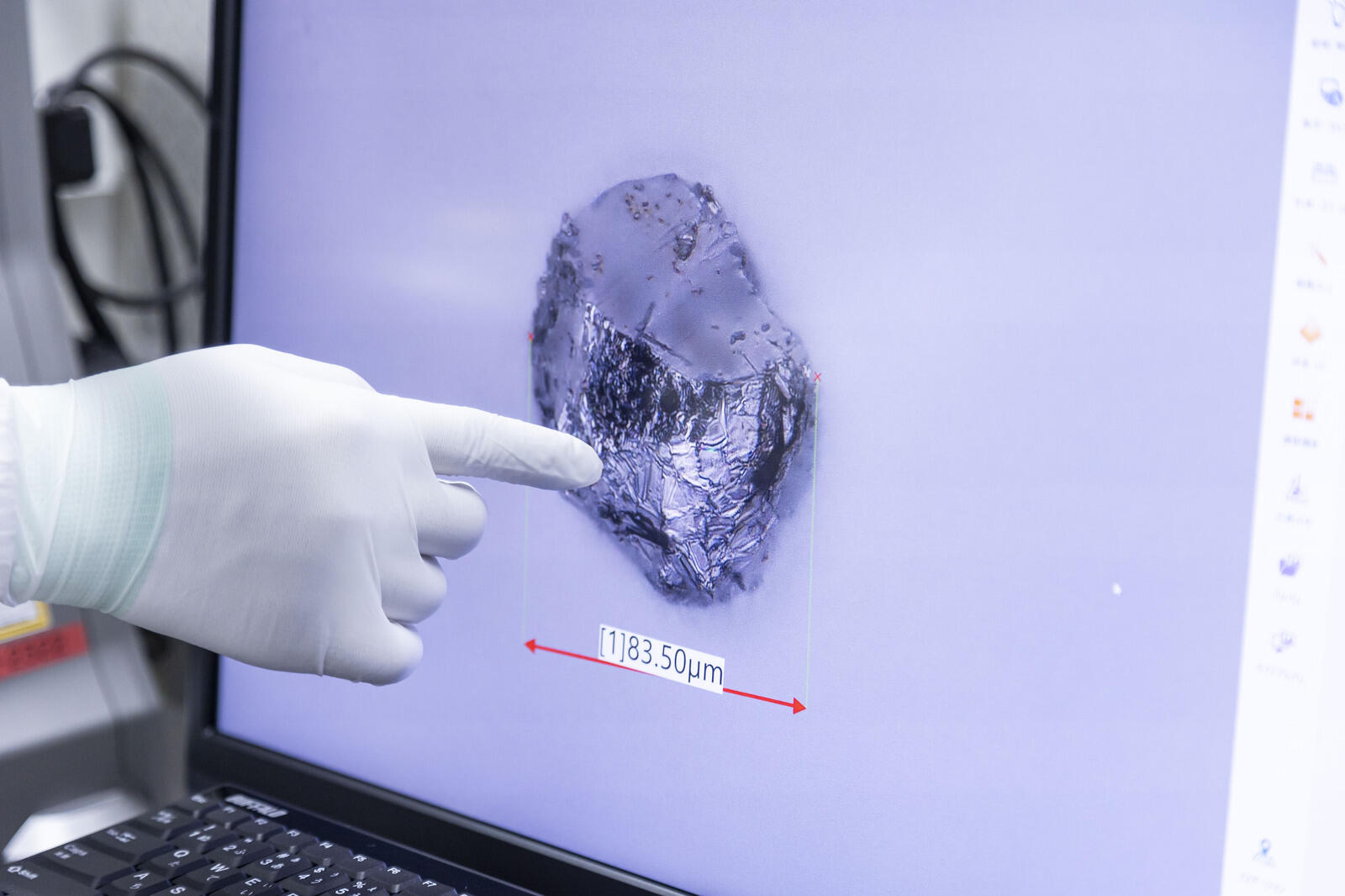
第2世代FCスタックの生産現場にとっては、今まで経験したことないような、クリーンな世界でモノづくりをする必要があった。
FC製造部 生産開発室 杉崎太亮 室長
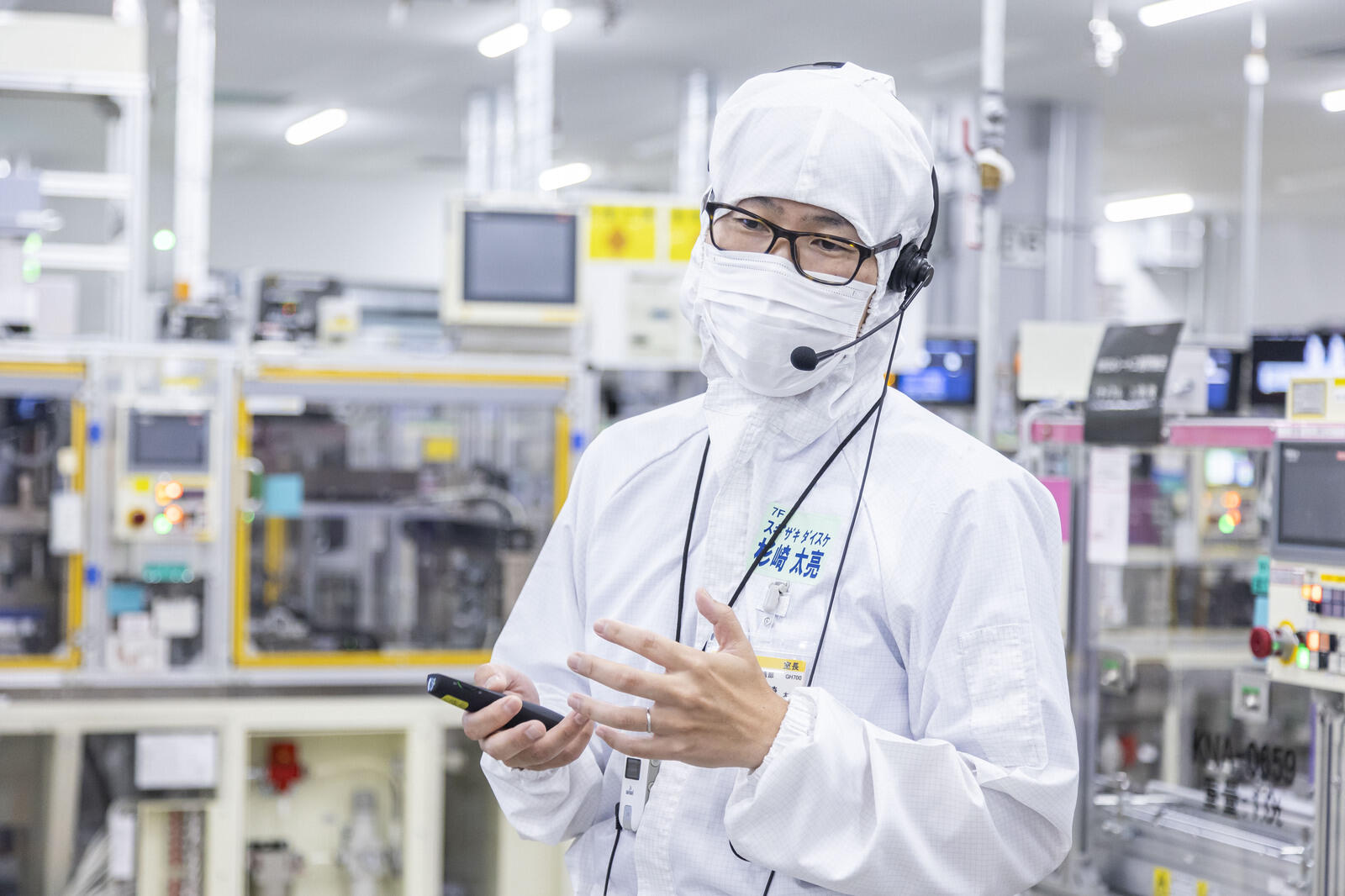
クリーンな生産現場というと、半導体の生産現場を思い浮かべてしまいますが、そうすると、きれいな空気をつくるための環境も、設備も莫大な投資がかかってしまう。
そうではなくて、私たちは100マイクロメーターの鉄異物がどのように動くのか? を可視化して、まずは“敵”の動きを「見える化」してみたのです。そうすると、鉄の異物は、半導体のようにフワフワ舞い続ける異物ではなく、基本的には落下して床に留まることが分かりました。
当初、「あれもこれも対策しなければいけない!」と、不安がっていた皆が「これなら戦える!対策できる!」と前を向き始めた瞬間です。
それからは、一人ひとりが、鉄の異物をどうすれば防げるのか?「持ち込まない、発生させない、発生したら除去する」のクリーン3原則の考えを元に、設計、生技(生産技術)、製造、品管(品質管理)、仕入先様、皆がひとつの目標に向かって動き出すことができたのです。私たちのその時の愛言葉は「ジャスト・イン・クリーン」。
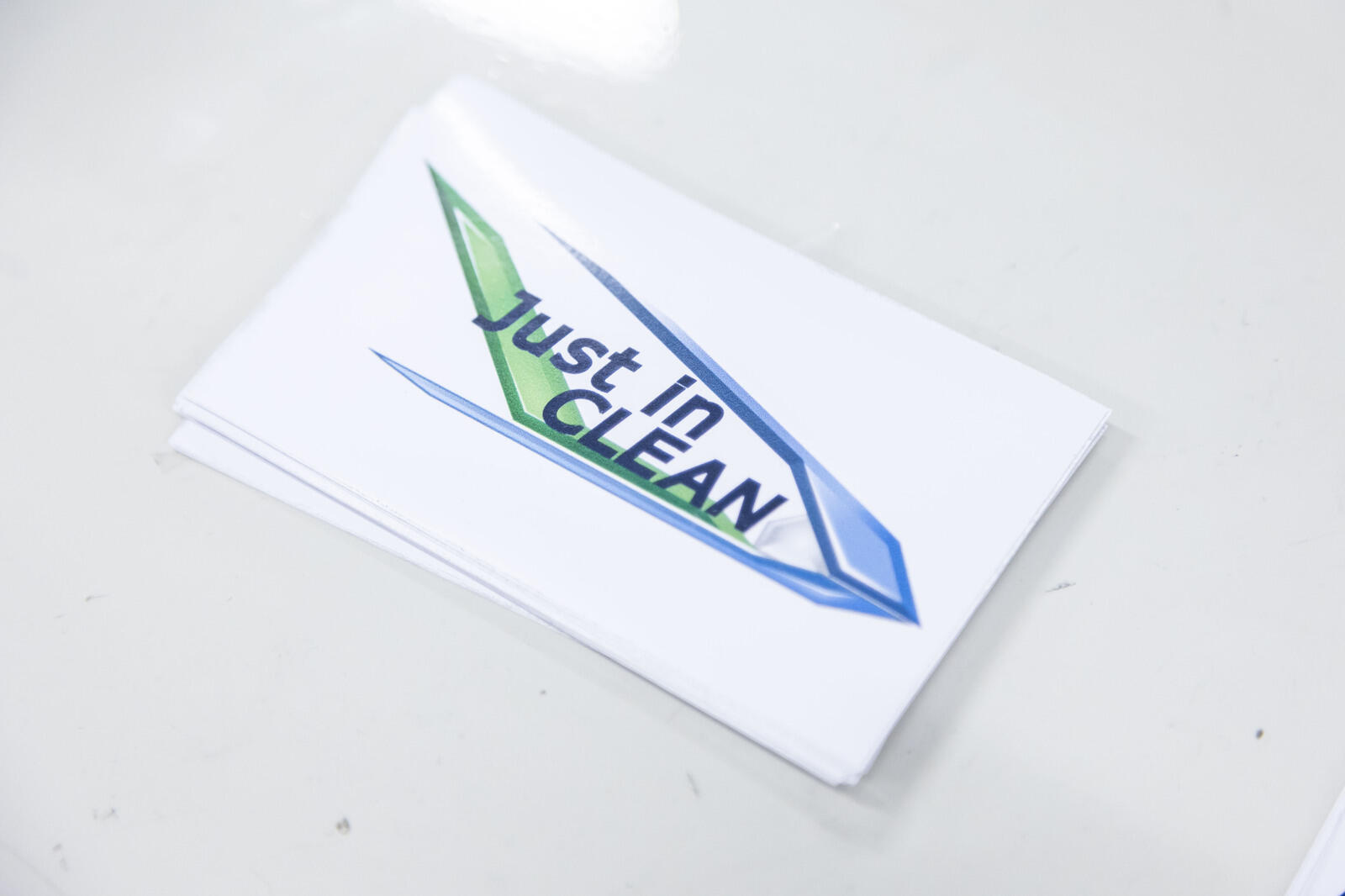
「必要なところに、必要なレベルだけ、必要なクリーン対策をする」。まさに「Use Brains Not Money*」の考えです。
*お金をかけずに知恵を出し合って解決を図る考え方
このように、設備や環境の異物対策はワンチームとなって取り組むことができたが、さらに大切なのは現場で働く「人の意識」だという。FCスタックのように化学反応で電気を生み出す製品にとって、異物は品質に直結するため、最後の砦は、現場力にかかっているのだ。そこで、現場の人のクリーン意識を醸成するために結成したのが「異物ラボ」。
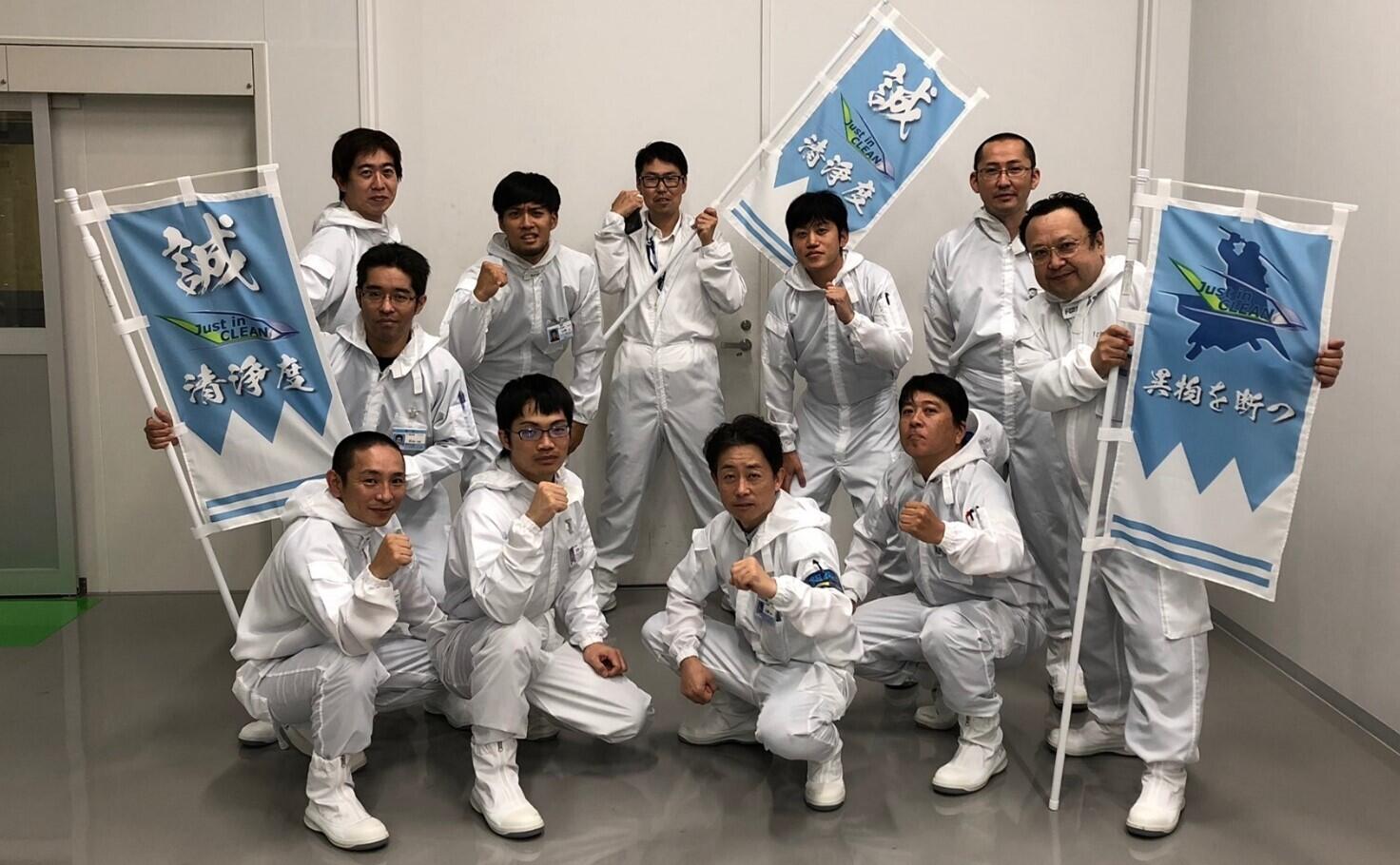
現場のメンバーで構成された彼らは、最先端の電子顕微鏡やX線分析器を操り、製品や設備で見つかった異物を素早く分析。数時間後には生産現場にフィードバックをして改善するという。
通常、分析メーカーに出すと1週間のリードタイムがかかる作業を、ものの1時間で結果を出してフィードバックすることができる。この最強の分析部隊を製造現場のど真ん中に置いたのだ。
また彼らは、それだけでなく、素材の仕入先における工程も自工程と捉え、何千枚という検体を分析し仕入先と共有することで、2020年2月では1%台だった不良率は、22年12月にそのは約100分の1まで改善している。
スローガンは「クリーン=品質=現場力」。現場にクリーンを保つ意識を根付かせ、改善する姿はトヨタの現場力そのものだ。
彼らは、FCの現場にとって無くてはならない存在となっている。
FC製造部 製造支援課 近藤政宏 組長
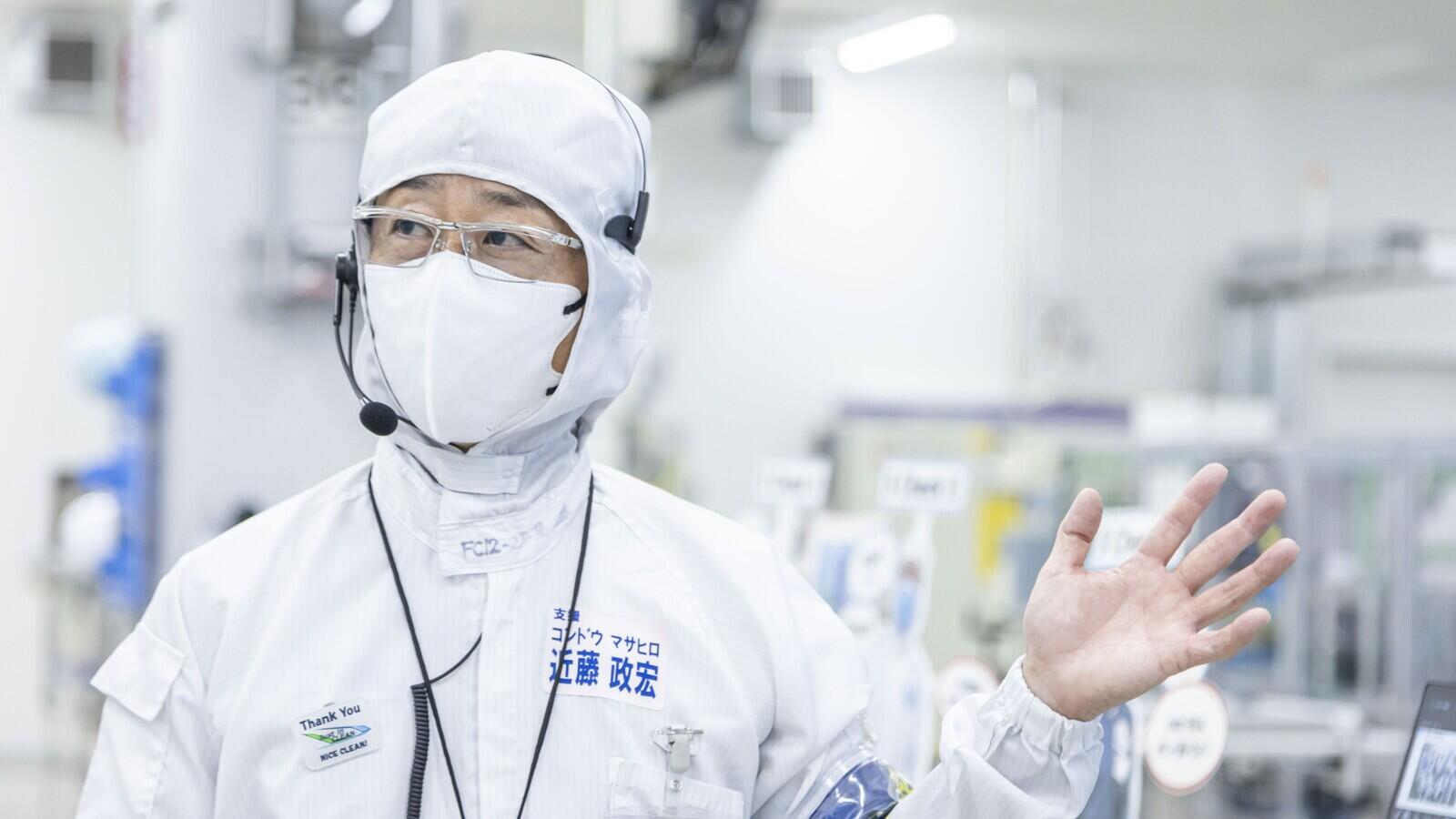
異物を発生させないために、ただ規制を設けるだけでは人の心は動かない。高品質を維持するために本当に大切なのは、全員のマインドを変えていくことです。
そのために異物ラボは、楽しみながらクリーンレベルを上げていこうという考えのもと、意識づくりを進めてきました。
結成当初に所属や職位の垣根なく、現場ワンチームで徹底した掃除を実施。以降も「こうすればもっと綺麗になる」、「異物が出ない」など知見を共有しあい、全員が共感をキーワードに結束できる職場づくりをしてきました。
人が育てば、現場も育つ。今では警察の鑑識が使うような分析装置を扱える人たちも増え、全員一丸となって楽しみながら改善を重ねています。
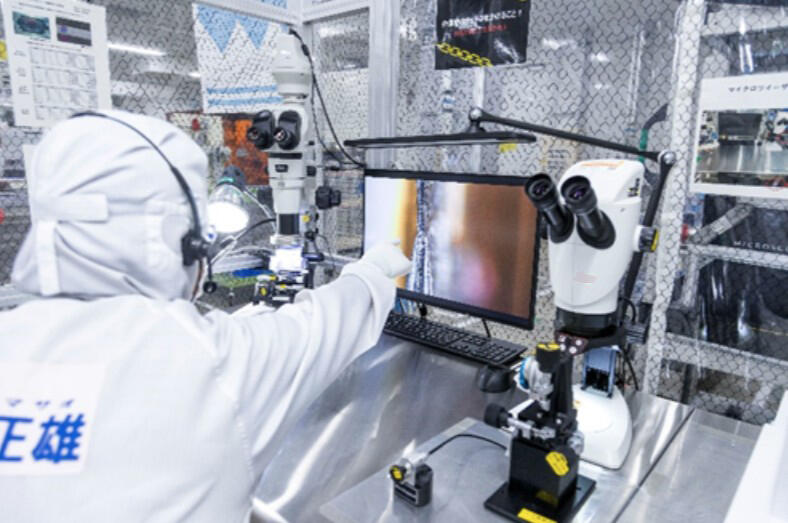
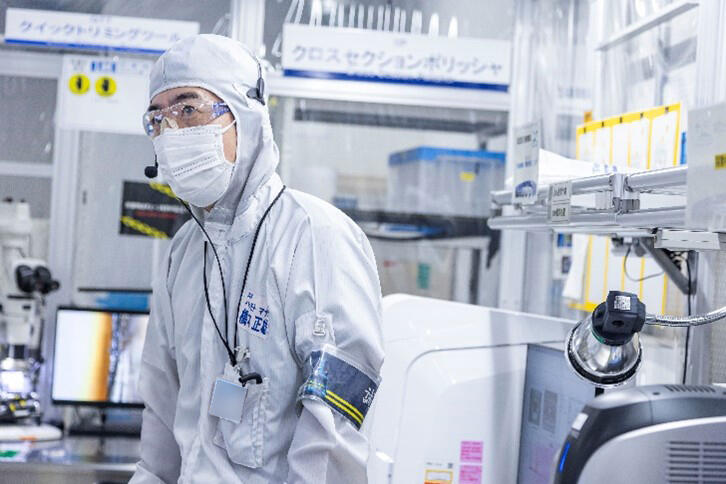
製造支援課の橋本正雄チームリーダーは元溶接工だったが、今では異物分析マイスターとして100マイクロメーターの異物を製品から摘出する技能を有する
MIRAIで培われた、FCスタックをはじめとするさまざまな技術は、鉄道や船舶、発電機など展開している。人も製品も進化の真っ只中だ。