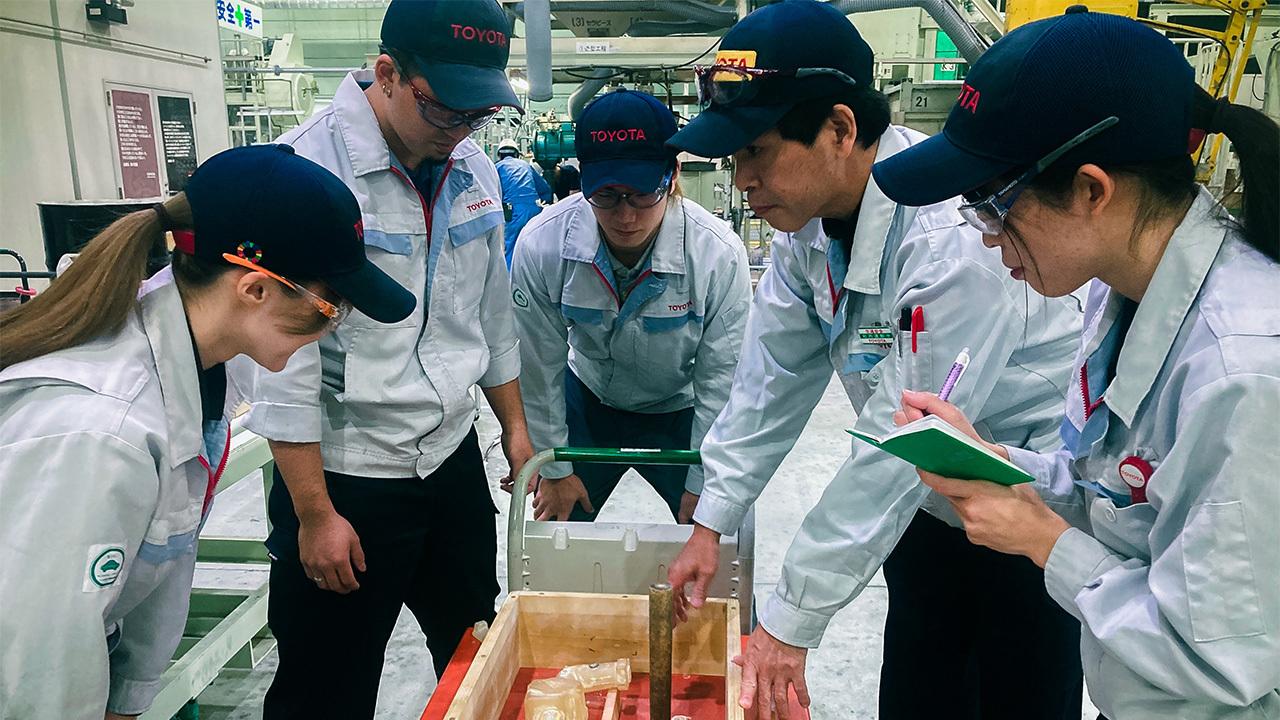
自動車業界が大変革期にある今、トヨタの原点に立ち返るべく始まった「初代クラウン・レストア・プロジェクト」。第7回では、内外装の加飾部品やランプ類の製作に挑んだベテランと若手の奮闘についてリポートする。
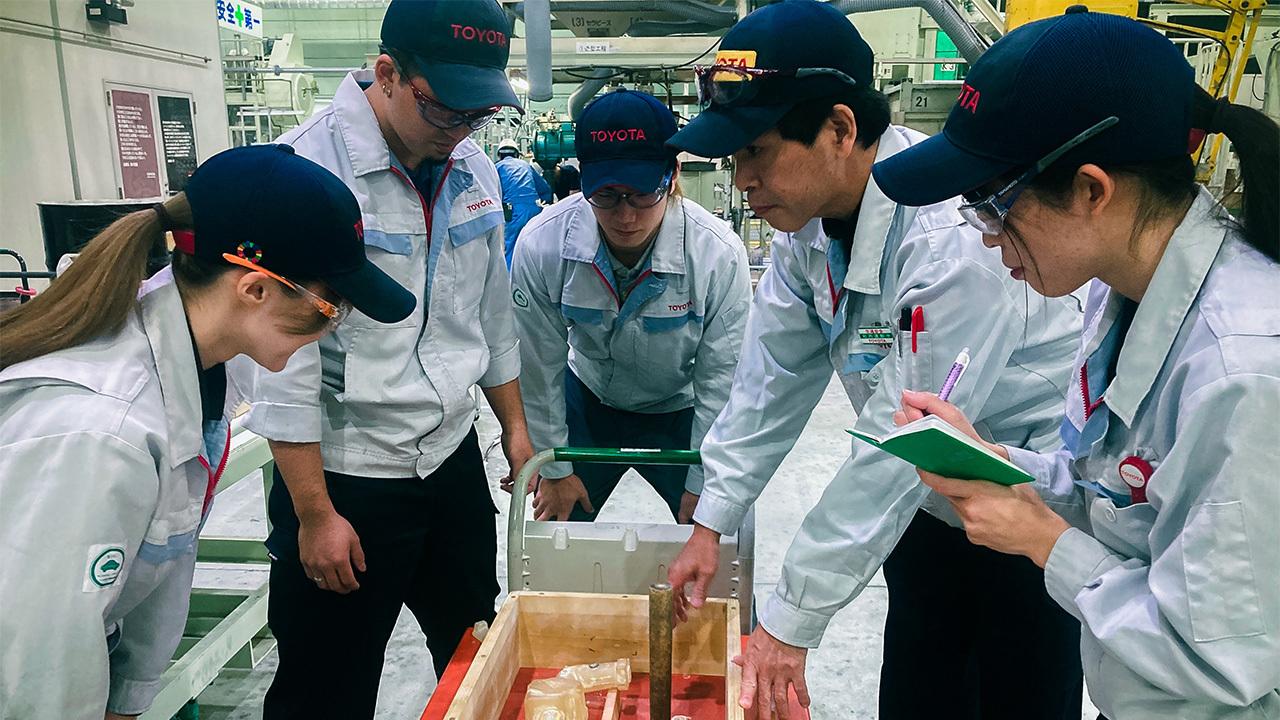
100年に一度の大変革期を迎えた自動車業界。トヨタ自動車ではあらゆる部門で前例のない画期的な取り組みがスタートしている。
そのひとつが2022年の春、社内の各生産工場から多彩な人材を集めて元町工場でスタートした「初代クラウン・レストア・プロジェクト」である。トヨタイムズでは、その意義とレストアの現場をリポートしていく。
第7回は初代クラウンのアイコンともいえる金属製の内外装の加飾部品や、ランプ類の製作に挑んだ素形材チームの首藤修治リーダーとメンバーの田中伸治、そして彼らの依頼を受けて、未経験のモノづくりに挑戦した素形材技術部の若手社員たちの奮闘をお届けする。
ベテランと若手による「ゼロからのモノづくり」
初代クラウンのレストアプロジェクトのメンバーは、SX(シニア・エキスパート)やEX(エキスパート)などの社内資格を持つ、高い技術と豊富な経験を誇るベテランの技能者ぞろい。
だがこのプロジェクトにとって、メンバーの同僚や後輩である中堅社員、若手社員たちの存在は欠かせない。そして彼らの活躍、つまり「ベテランから中堅、若手への技能伝承」は、このプロジェクトが当初から掲げた大きな目的のひとつでもあった。
なかでも今回、若手社員の活躍が目立ち、ベテランから若手への技能伝承で大きな成果を上げたのが、鋳造、鍛造、焼結、熱処理など、さまざまな技術を駆使してモノづくりを行っている素形材技術部だ。
素形材技術部は、金属をはじめ木材、石材、窯材、ゴム、ガラス、プラスチックなどの素材に熱や力を加えることで、さまざまな形状、機能を持つ部品をつくる部署だ。
首藤
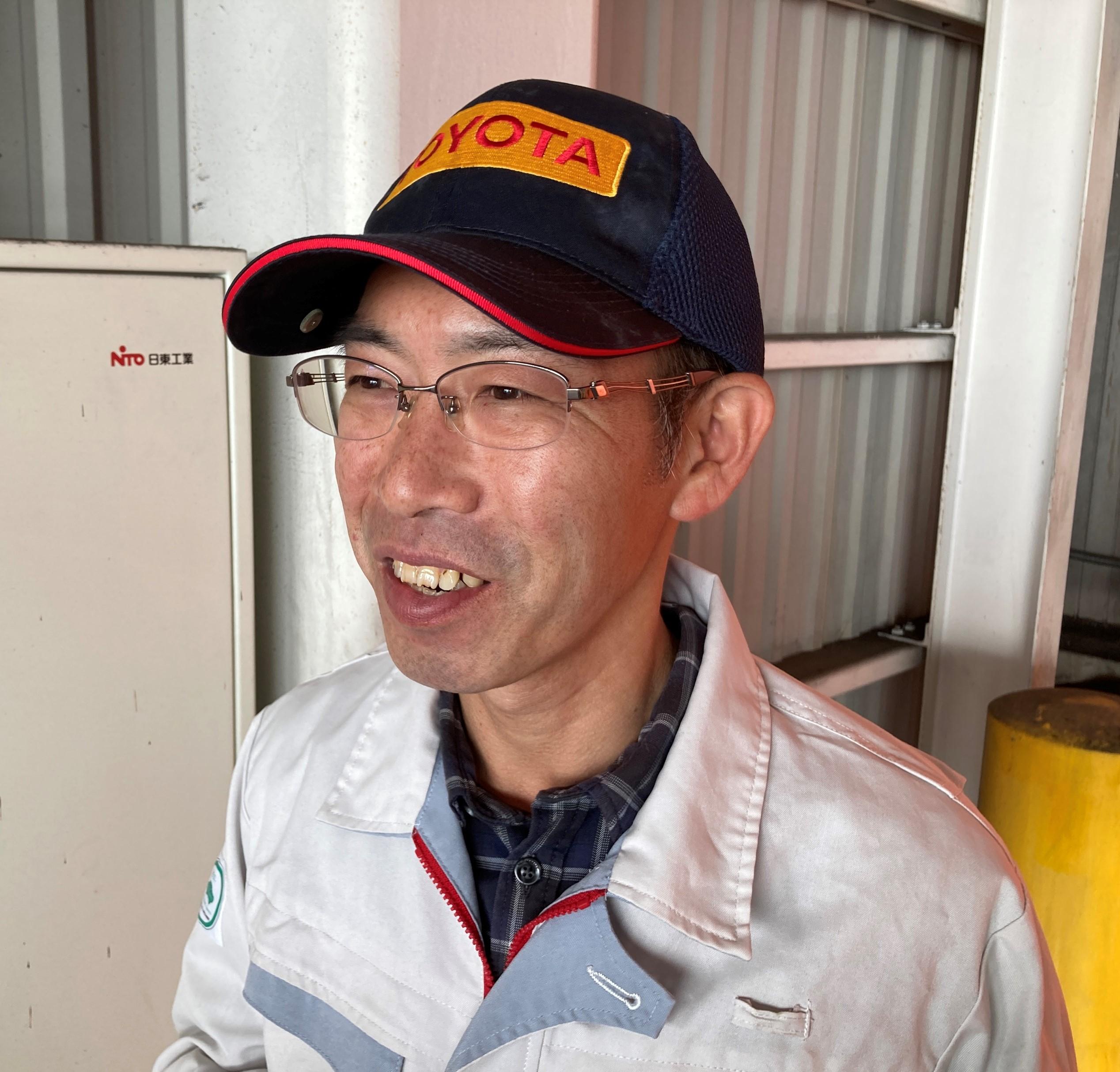
私は部品の鋳造に使う「型」に関わる仕事ほぼ一筋に取り組んできました。素形材技術部は、この型づくりを行う部署。この部署の後輩たちの協力と奮闘がなければ、私が担当した内外装の部品の調達は不可能だったと思います。
今回のレストアは、クルマを世に送り出したメーカー自身にしかできない「当時の新車以上の品質」の達成を目指していた。そのため、必要な部品をどのように調達するかが常に最大の課題だった。
さびによる腐食が深刻だったために、高技能者の達人技に加え、新しい金属の加工技術であるインクリメンタル成形によるパネルの再製造が必要だったボデーのレストア。
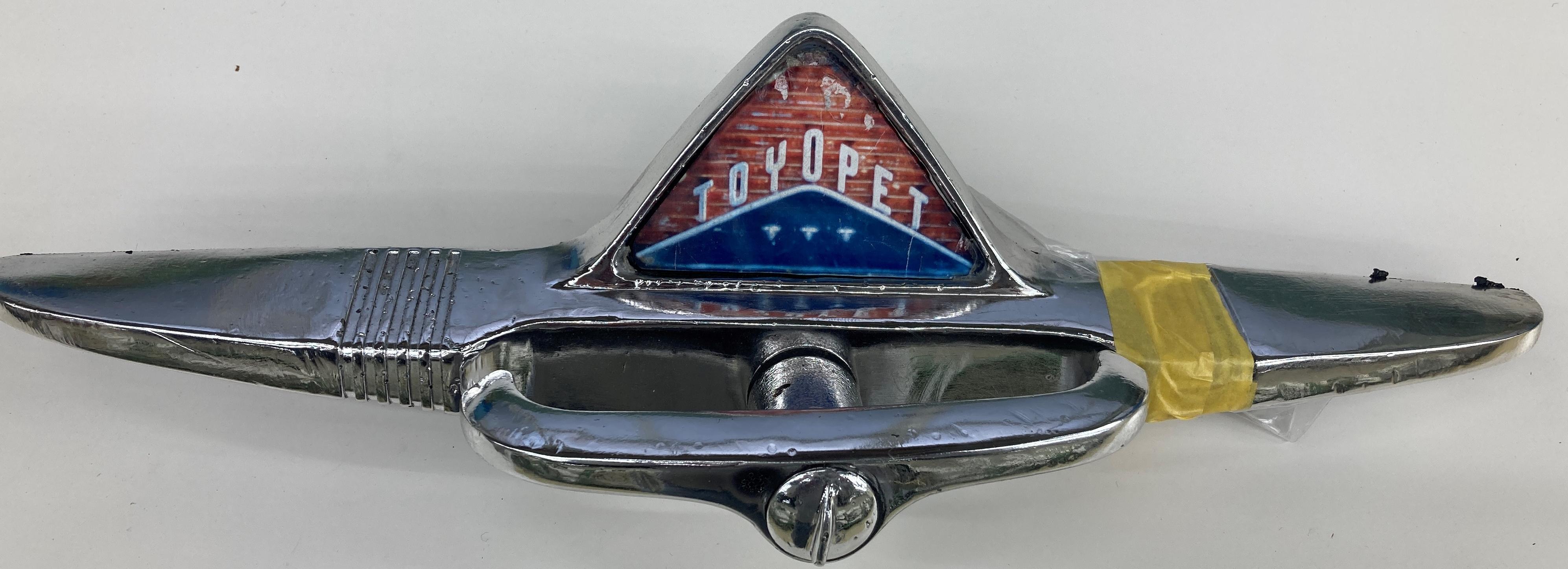
それと同様に、エンジンの主要部品であるインテークマニホールド、バンパーフロントグリル、ボデーのサイドマークやドアを開閉するためのハンドル、ボデーを取り巻いて華やかに輝くドアトリムなどガーニッシュ(内外装の加飾部品)のさび、安全装備として欠かせない前後のランプ類も経年変化による劣化が深刻だった。
田中
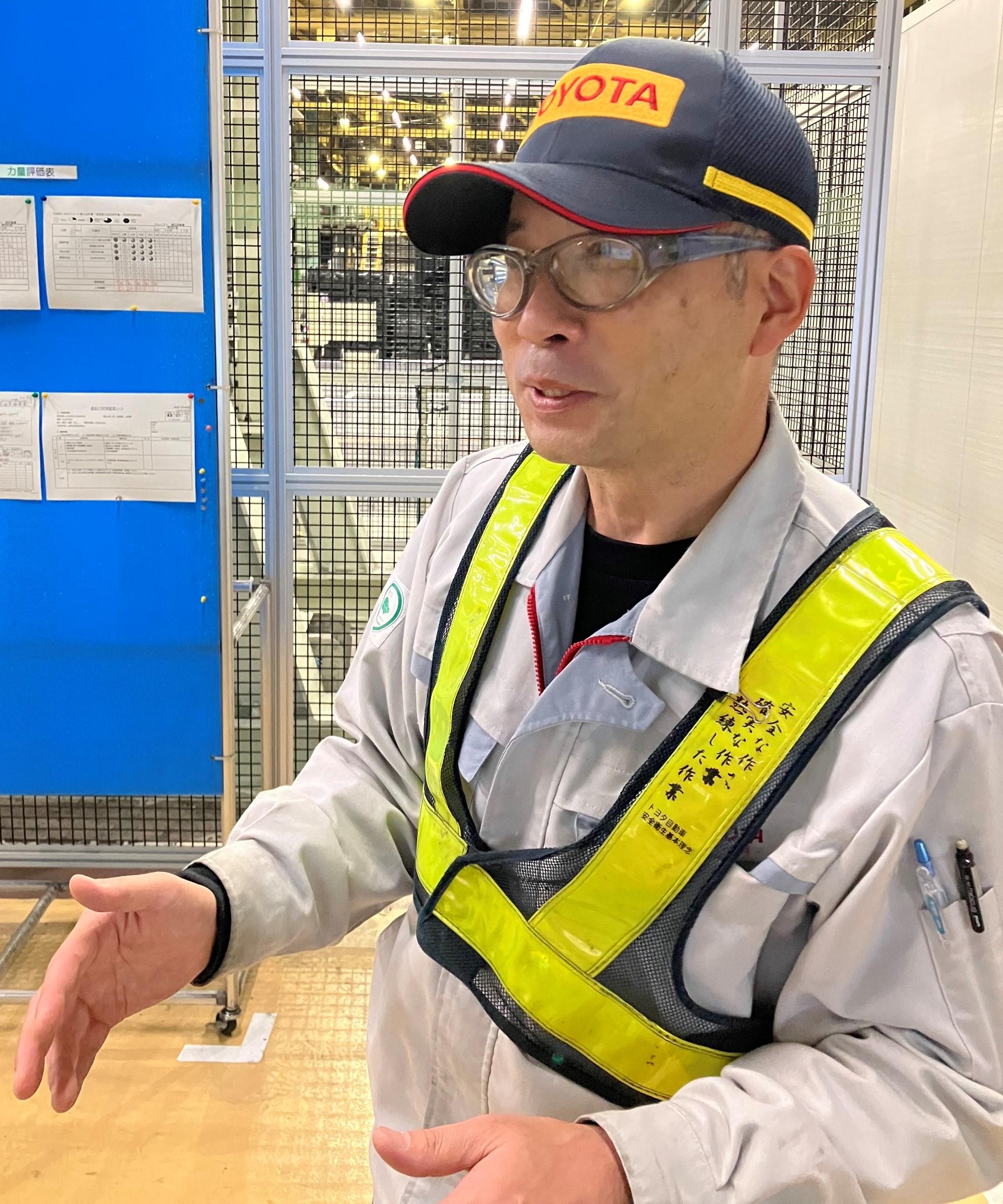
今のクルマと違って初代クラウンには、バンパーやフロントグリル、また内装部分にも鉄を素材にした加飾部品が多いのです。こうした部分もキラキラさせなければ、今回のレストアの目標は達成できません。ランプ類も含めて、とにかく新しく製作するしかない。そのことはハッキリしていました。
目指す形状を一気につくれる鋳造
首藤と田中は素形材技術部の所属で、ダイキャスト(金属鋳造法)のエキスパートでもある寺田直道を訪ね、まずは鋳造でエンジンに取り付ける吸気系の重要部品、インテークマニホールドなどをつくってほしいと依頼した。
寺田
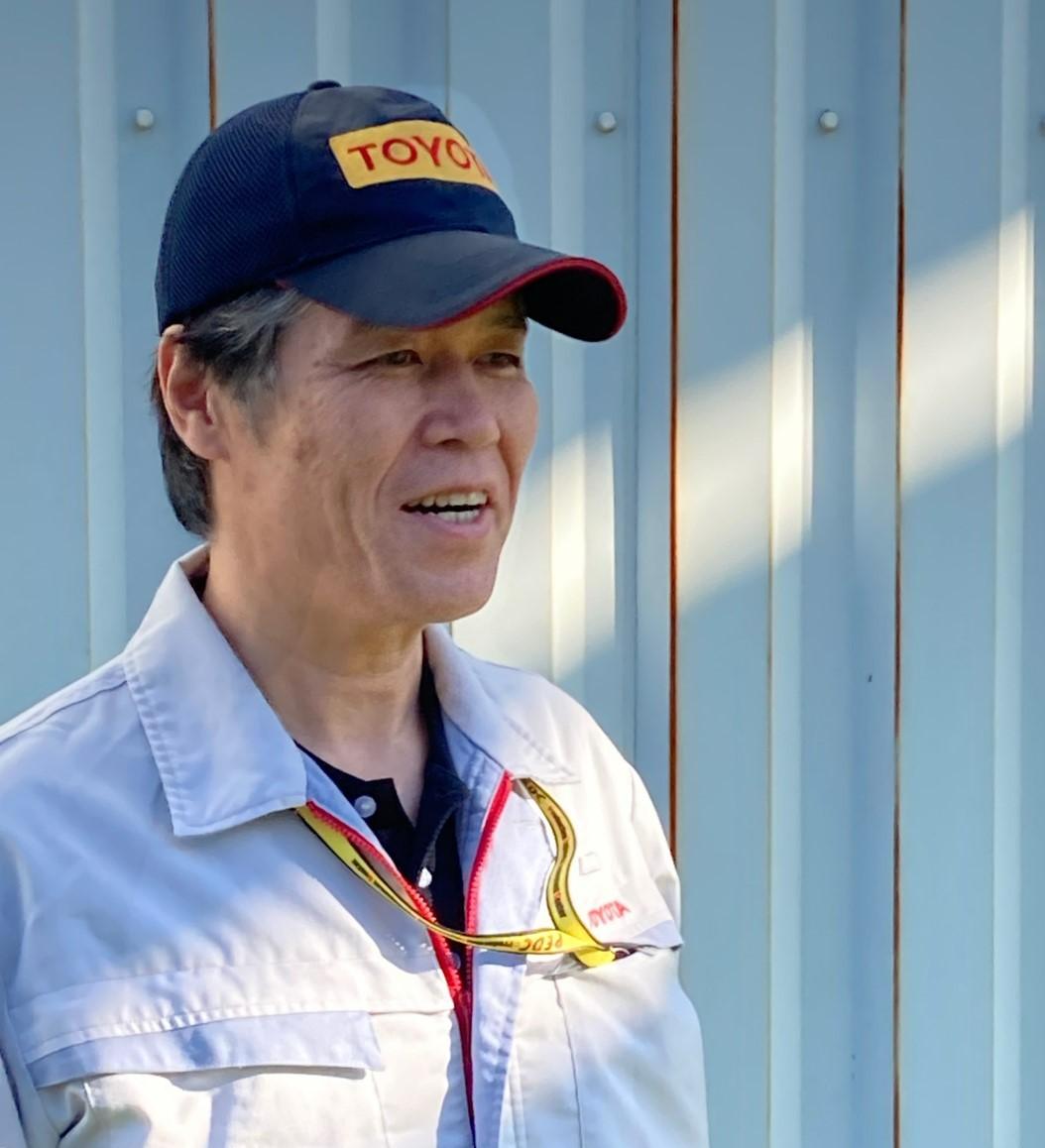
最初に話を聞いたとき、とにかく「良いモノをつくりたい」という首藤さんたちの情熱の熱量がすごかったのを、今でも鮮明に憶えています。
私自身はつなぎ役に徹して、素形材技術部でこの依頼にどのように応えるか、首藤さんを交えて相談しました。
素形材技術部でこの依頼を担当したのが、長門静香、矢島誠悟という若手メンバー。
そして彼らのサポート役を務めたのが「クルマづくりを支える職人たち」で「鋳造の達人」として登場したSXの元木清秀。さらにエキスパートの大橋淳だ。
元木
最初はインテークマニホールドやアルミ製の部品、全部で4つほどを鋳造で製作してほしいという話でした。鉄素材のインテークマニホールドの製作は17、8年前に「コロナ」のレストアで製作した記録があって、その方案(砂型の設計)が使えると思いました。
長門
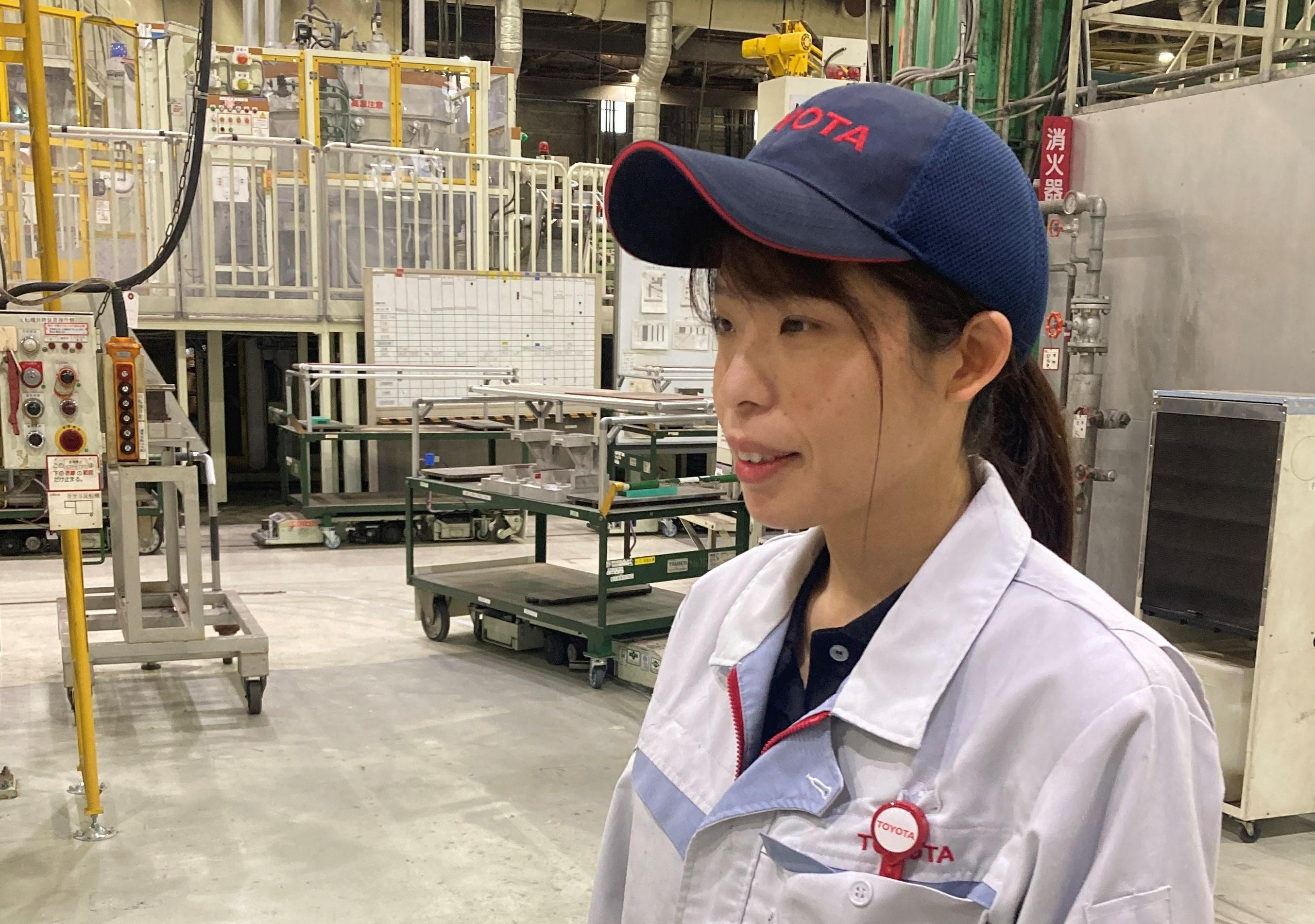
私はこれまで13年間、C-PODのサイドパネルやGRヤリス関連の試作、モータースポーツ用エンジンの鋳造用3Dプリンターを使った中子(鋳造の際、部品の中に空間をつくるために入れるもの)など、鋳造の砂型のモデリングや鋳造に関わる一連の作業を担当してきました。
昔ながらの「手込め」鋳造にも挑戦!
鋳造による部品製作には「型」が欠かせない。鋳造による部品製作は、まずこの型づくりから始まる。型は砂でつくられているので、砂型という。
砂型づくりは、木枠の中に砂型用の砂を入れ、部品の形をした模型などをその砂の中に埋めることから始まる。その後、砂が固まってから模型を取り出すと、砂の中に部品と同じ形状の空間ができる。
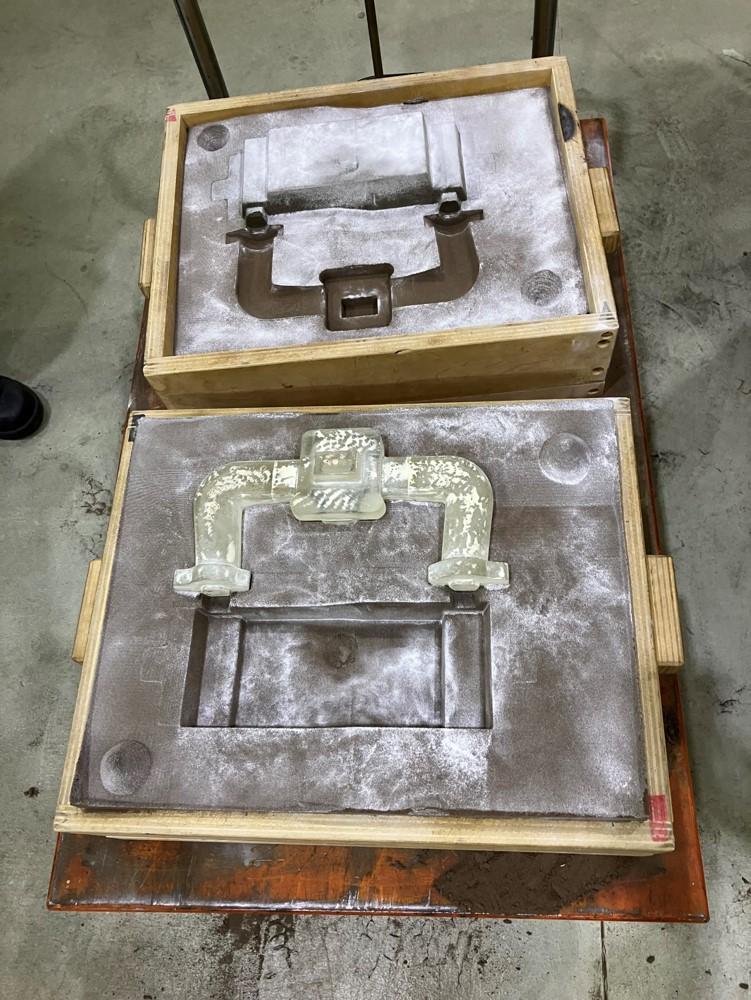
この空間に溶解させた金属などの素材を流し込むことで、金属を部品の形状に成形できる。切削による機械加工と違って、金属などの素材を一気に目指す形状に成形できる。これが鋳造という技術の素晴らしいところ。
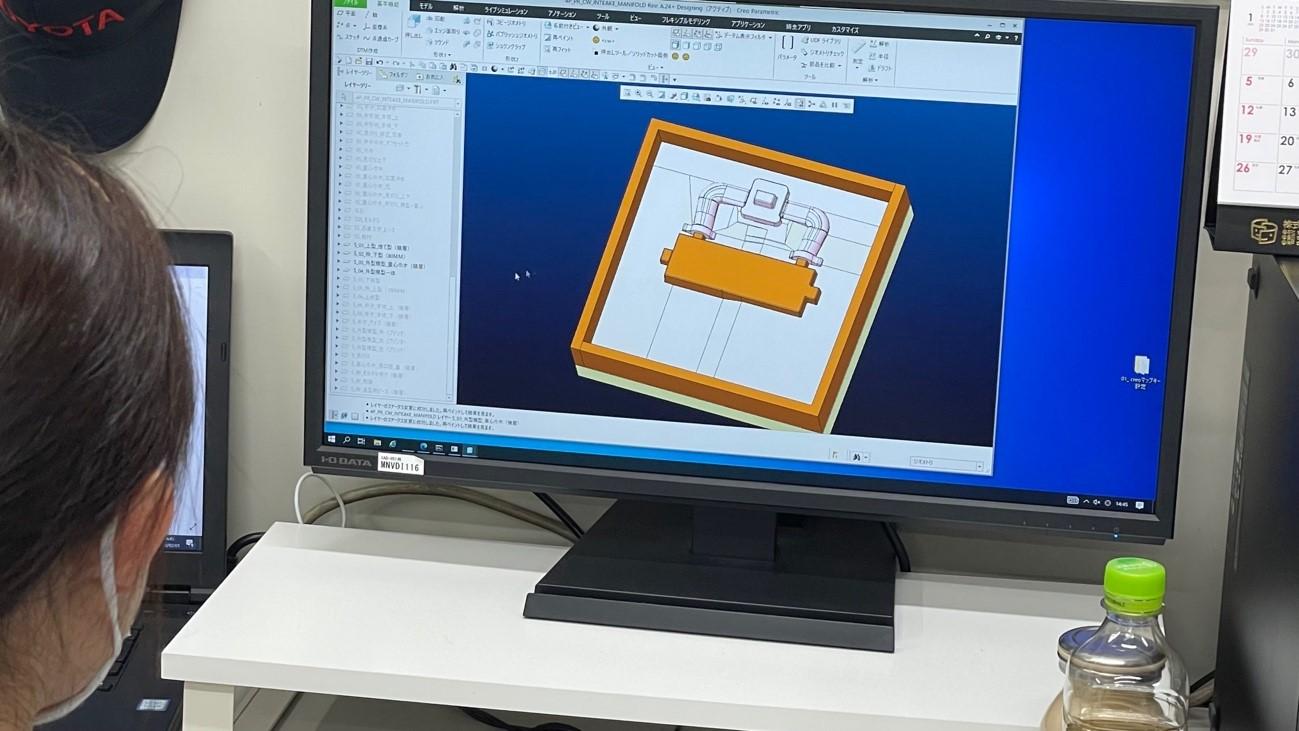
素形材技術部では、この砂型づくりに最新の鋳造用砂型3Dプリンターを使っている。3D-CADソフトでつくられた部品の設計データから、3Dプリンターが砂型をつくってくれるのだ。
今回、素形材技術部が製作を担当した部品の中には、昔の設計図が残されていて、そこから3Dの設計データをつくることができた部品もあった。だが、設計図が残されておらず、現物しかない部品もあった。
昔の設計図は2D図面しかなく、また図面表記や材料表記が今と異なる箇所があり読み解くのに大変苦労した。通常業務では製品の3D設計データが既にあり、そこから型の3D設計データを作成するが、今回、2D図面を読み取り、製品の3D設計データをつくり、型の設計データを仕上げるという初めての試みであった。
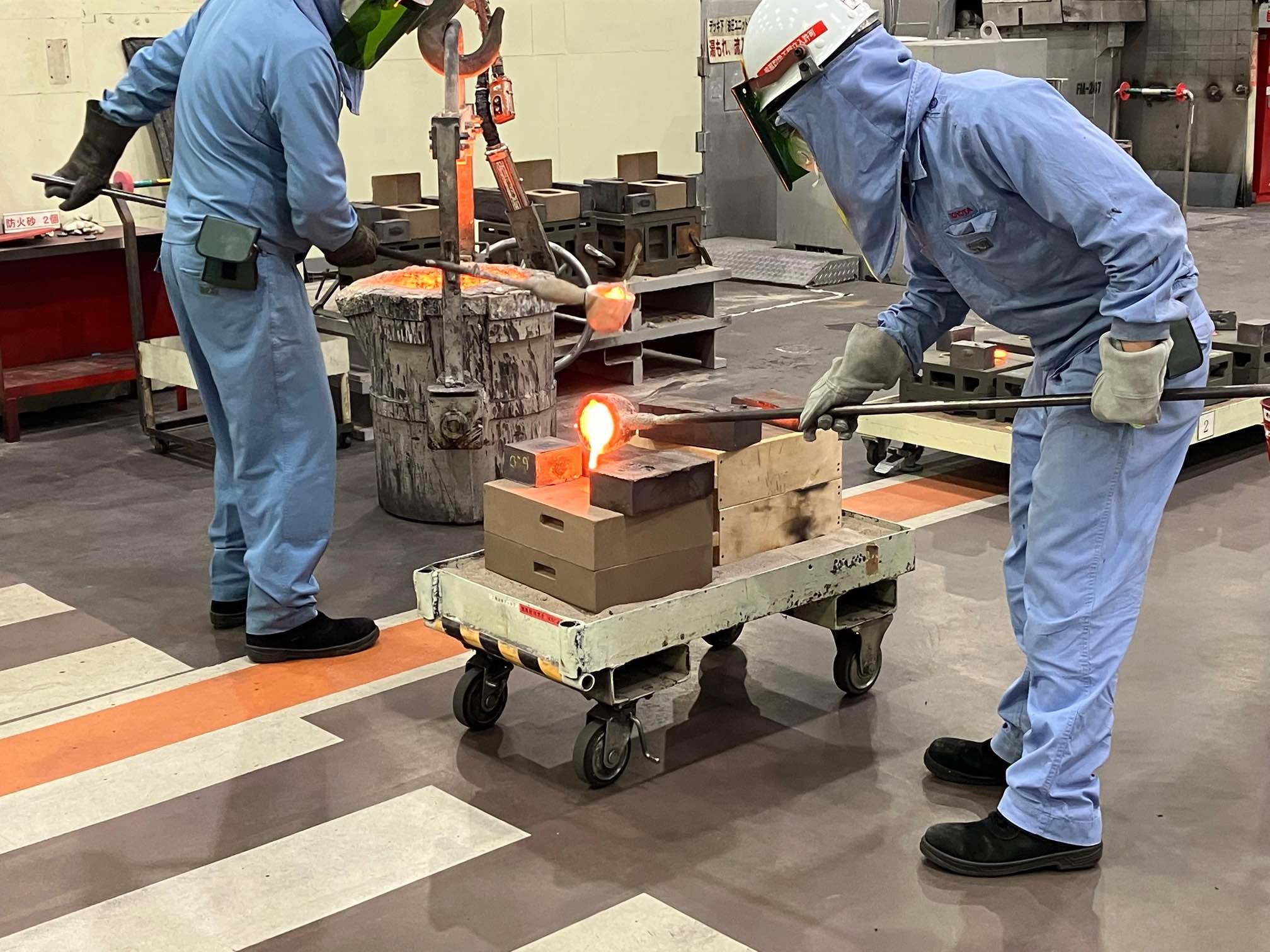
難航した亜鉛合金製部品の鋳造
素形材技術部が製作を担当する部品は、元木が語っているように数点だけのはずだった。
だが長門ら素形材技術部のメンバーは話を聞くうちに、「良いモノをつくりたい」という首藤の情熱に感銘を受けて、さらに多くの部品製作を引き受けた。
その中には、社内トップクラスの鋳造のエキスパートである元木にとっても未経験の、サイドマーク、トランク開閉ハンドル部など亜鉛合金製の部品もあった。
元木
亜鉛合金による部品づくりは僕らも未経験。なので、うまくいかなければアルミ合金で。それでもうまくいかなければ鋳鉄で、という話をしていたんです。でも首藤さんが「できればぜひオリジナルと同じ亜鉛合金の鋳物でつくってほしい」という。
この首藤さんの情熱に動かされた長門さんが「やってみます!」と、いつの間にか引き受けてしまったんです(笑)。これが大変でした。
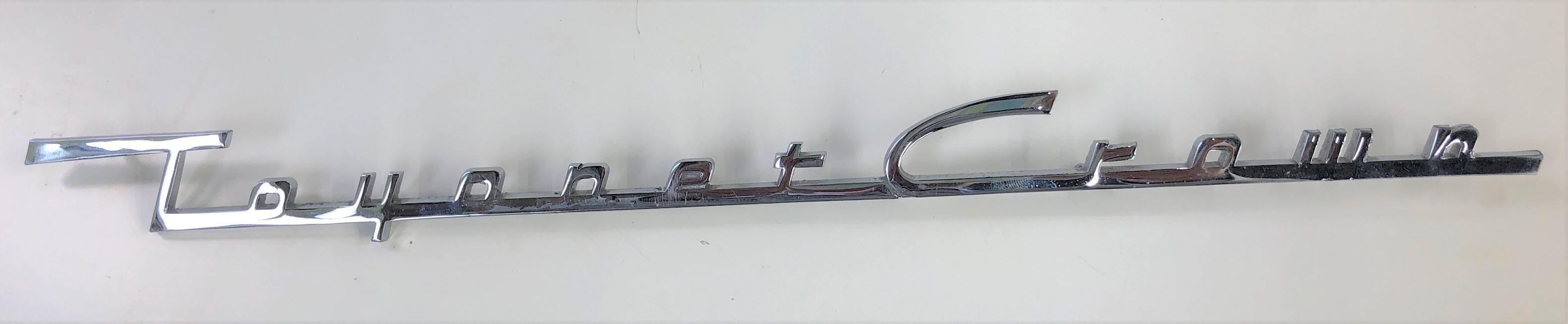
亜鉛合金は融点が低く、湯回り性が良いため、鉄やアルミより複雑なカタチのもの、薄肉のものをつくりやすい。しかも美しく、熱伝導率も強度も硬度も高く、また衝撃に強く、振動を吸収するという特徴もある。そのため、初代クラウンでもこの亜鉛合金がサイドマークやサイドモールなどの加飾部品に使われている。
だが、亜鉛合金の部品を砂型鋳造で製作する技術やノウハウは、トヨタ社内ではすでに「失われた技術」になっていた。長門や元木は首藤の情熱に押されて、この「失われた技術」の復活に挑戦することになったのだ。
元木
鋳造のノウハウは素材によって大きく異なります。亜鉛合金は一言で表現すれば「質が悪い」素材。これまでの鋳鉄やアルミ合金のノウハウが通用しない。
何度やってもひび割れたり、内部に鋳巣(ちゅうす※空洞のこと)ができたり、表面に凹凸ができたりしてキレイに仕上がらない。昔の部品をチェックしてみると、実は表面はかなり凹凸がありました。
亜鉛合金は凝固収縮が、元木や長門たちが慣れている鋳鉄やアルミ合金よりも大きい。また融解する温度も低いので、その分、砂型の中で固まる際に温度にムラができて、不具合も起きやすい。
長門たちは元木の指導を受けながら、方案(砂型の中に金属をどのように流すかという設計)や冷却方法を工夫するなどしてこの難問に取り組んだ。

長門
表面にも鋳巣ができてしまうので、最終的には砂型を寸法よりも1㎜大きくつくって、仕上がった鋳物をNC(数値制御)加工機で削って仕上げることにしました。
だがそれでも問題は続いた。亜鉛合金でつくった部品の表面に、どうしても細かな穴ができてしまうのだ。この穴を埋めて平らにしなければ、メッキをかけても奇麗に仕上がらない。
首藤や素形材技術部のスタッフたちは、この問題の解決法を社内外で探し回った。そして、最終的にアンチモンという金属でつくった1.6㎜径の溶接棒を0.3㎜径になるまで引き伸ばして細くし、レーザー溶接で表面に溶接して穴を埋めることで、ようやく満足できる部品が仕上がった。
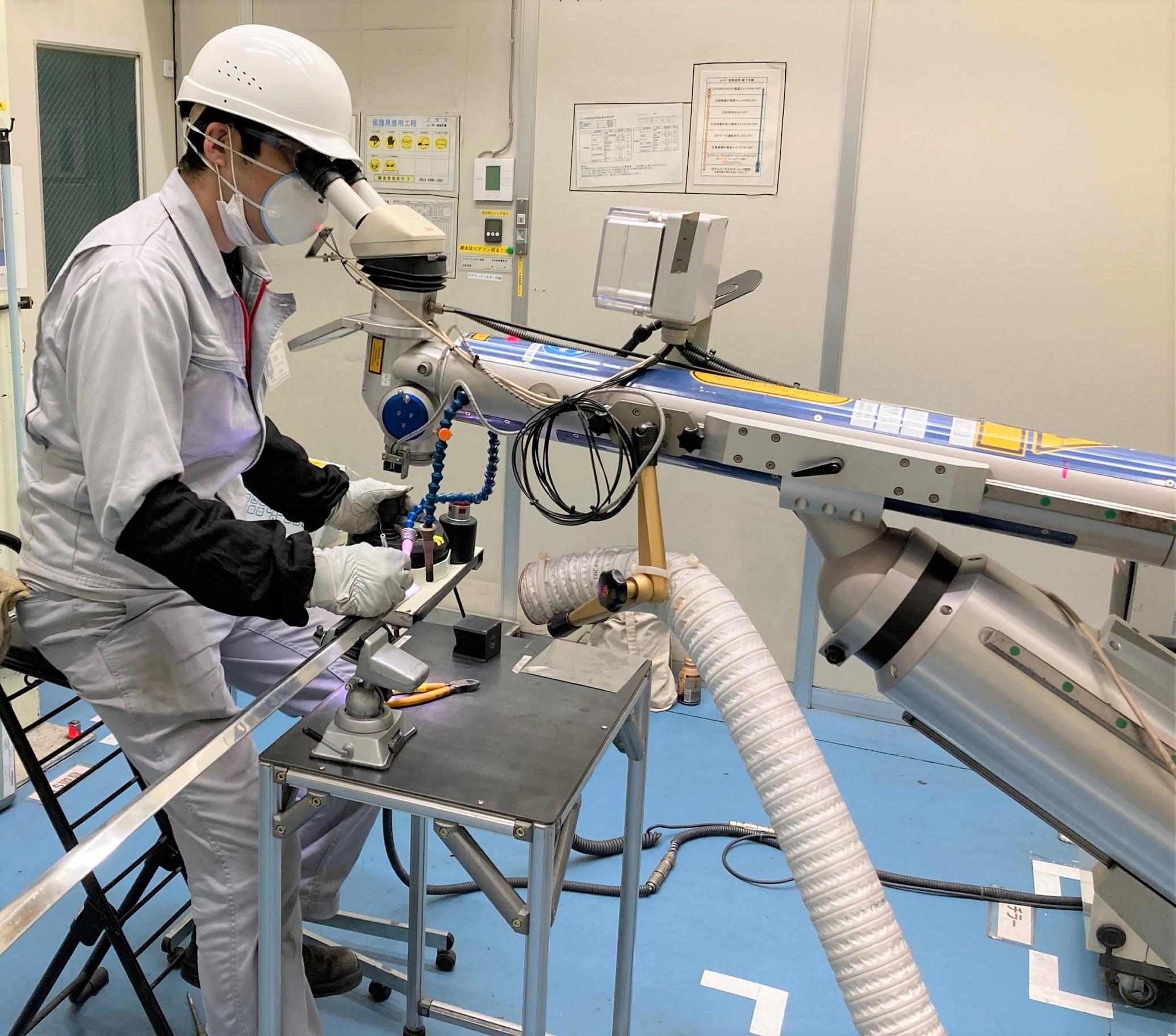

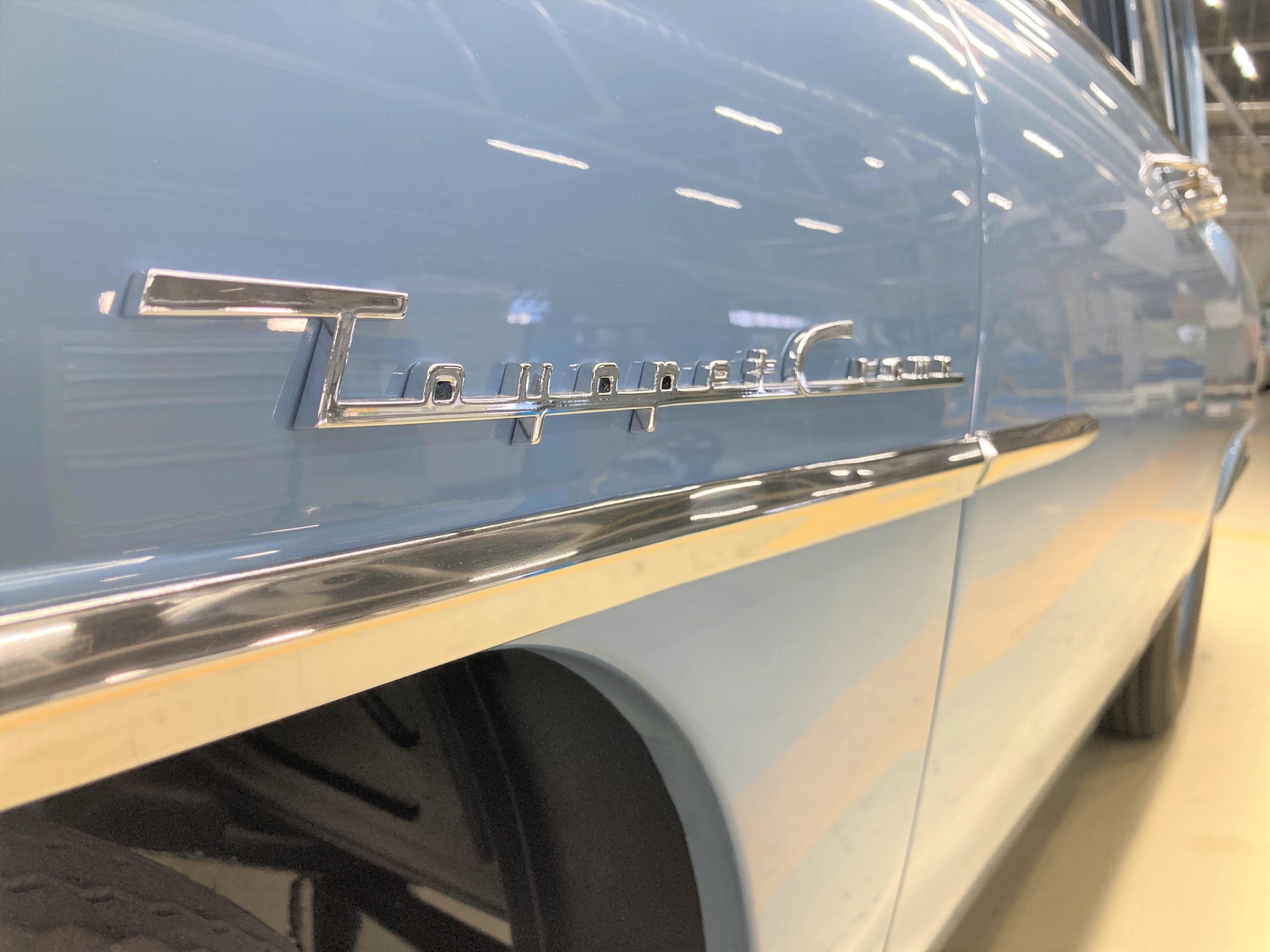
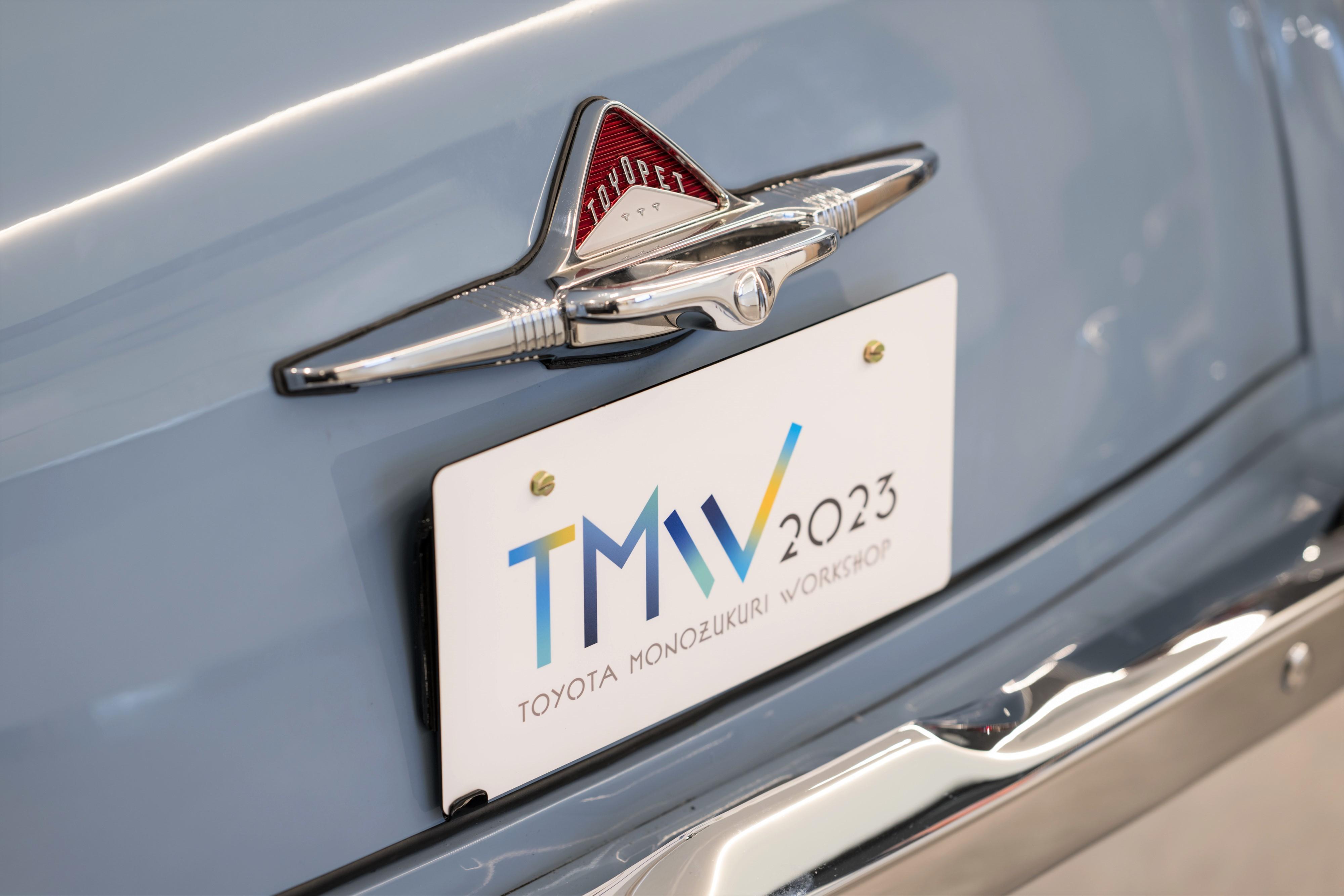
素形材技術部の協力でランプ類も完成
プロジェクトチームの田中伸治が取り組んでいた、テールランプをはじめとするランプ類の復元・製造も、素形材技術部の協力なしには実現できなかった。
テールランプの樹脂カバーは経年劣化でヒビが入ってしまったものも多く、再利用はできない。そのうえ、詳細な設計図も残されていない。こちらも現物をお手本に、何とかつくるしかない。
田中
私は入社してから現在まで、明知工場の鋳造部門一筋に仕事をしてきました。そこでつくっていたのは足回りやデファレンシャルギアなど、金属部品の製造です。
レストアプロジェクトのメンバーとして、ランプ類の担当になったとき「どうやってつくるか」から考えることになりました。
ランプ類も「型」を使ってつくるもの。だから当初は「製品の素材が鋳鉄から樹脂に、型も砂型から別の素材になっただけだ」と考えて取り組んだのです。
設計図がないため、田中は初代クラウンから取り外したランプ類の樹脂部品の現物を型取りして「型づくり」から作業を始めた。
アクリル樹脂は合成樹脂の中でも優れた透明性と耐候性が特徴で、建材から電子部品、道路標識、さらに塗料まで、日常のさまざまなアイテムに使われている。だから、その種類も驚くほど多い。来る日も来る日もさまざまな種類のアクリル樹脂を試した。
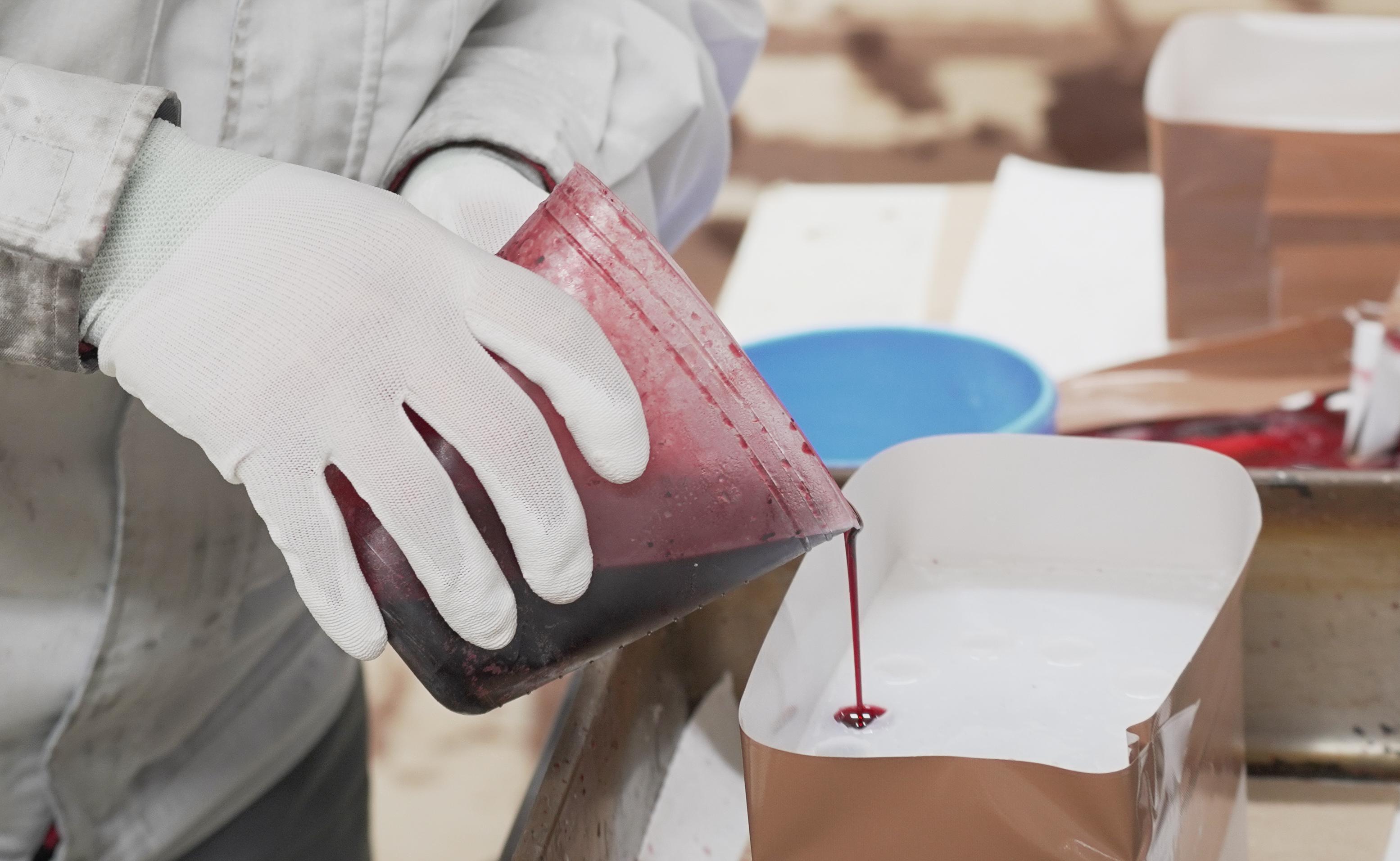
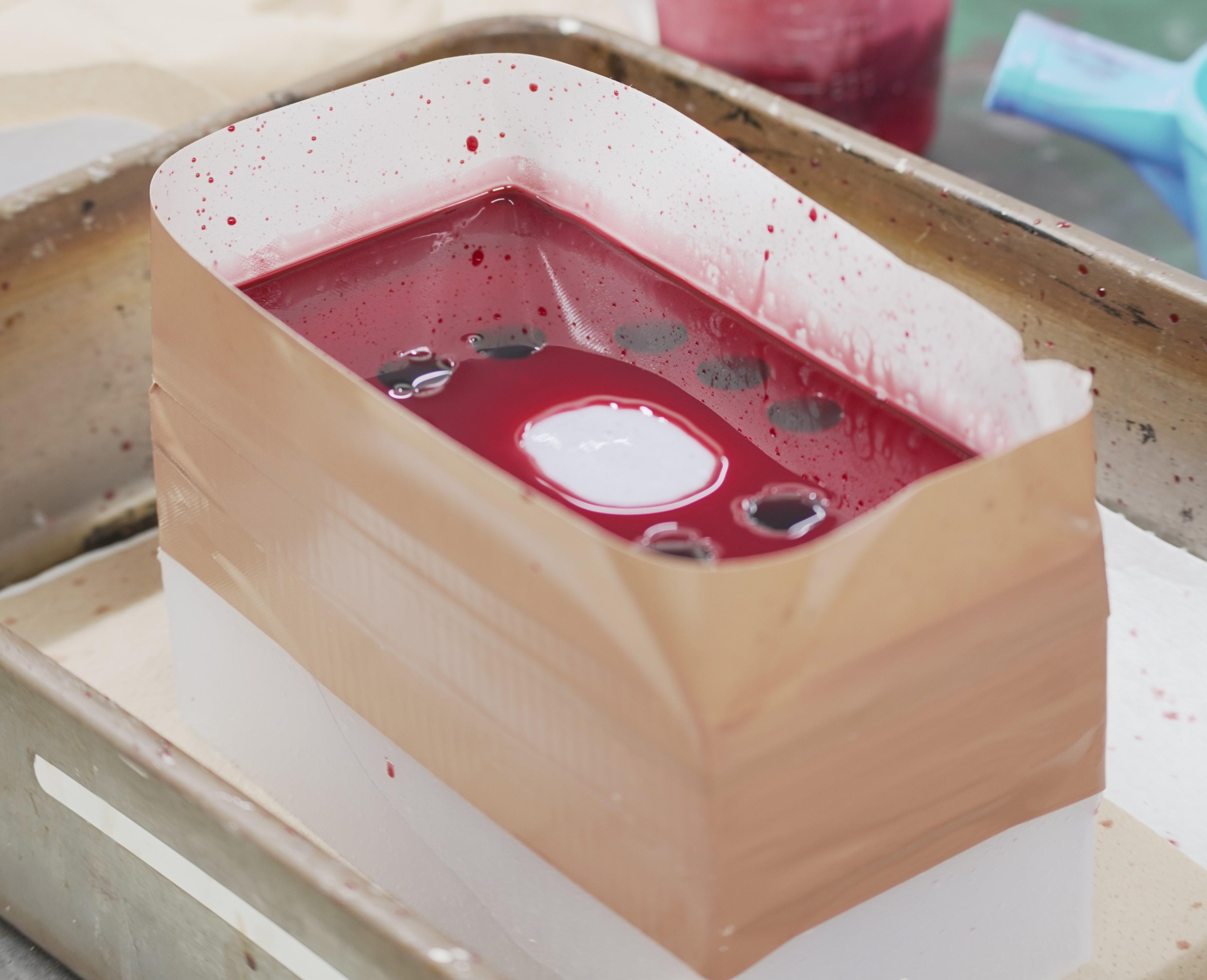
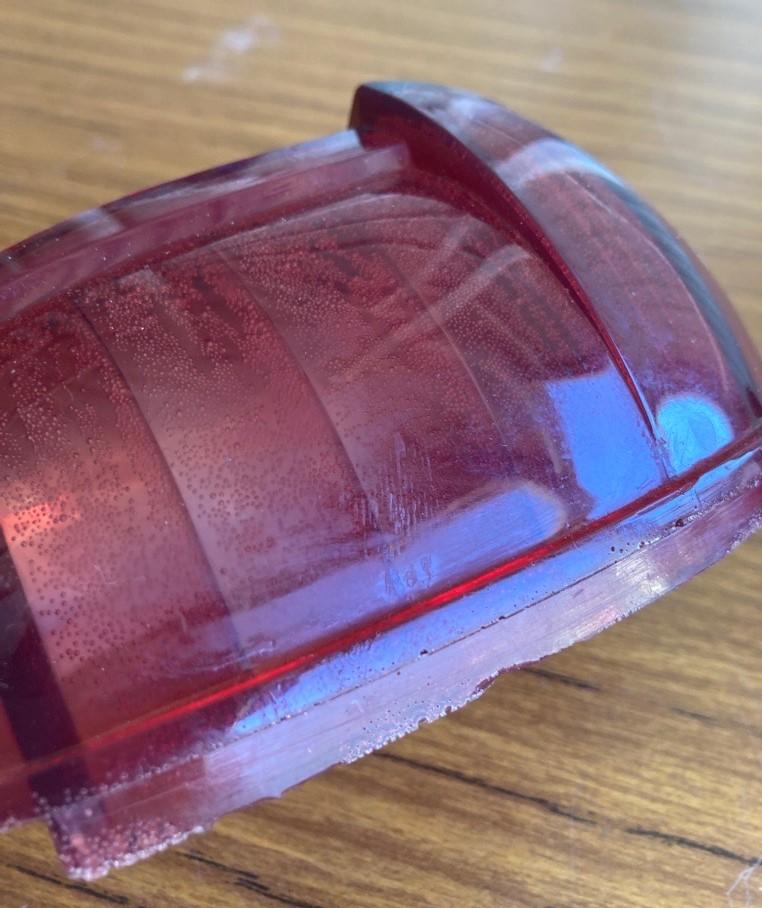
だが何度やっても、思った通りの形にならない。田中は素形材技術部に相談した。ここでは試作車やモータースポーツのレースカーの樹脂部品の製作も行われていたからだ。そして同部の若手、小野敦司とこの問題の解決に取り組んだ。
試行錯誤を繰り返したふたりは、「これなら行ける!」というアクリル樹脂素材にたどり着いた。
だが、問題は続いた。成形した部品の中にどうしても気泡ができてしまうのだ。見た目はもちろんのこと、強度的にも問題があるので、何とか樹脂の中の気泡を取り除かなければならない。

実はこの「樹脂の中の気泡」を取り除く技術やノウハウも素形材技術部が持っていた。かつて樹脂部品の開発のために使われた「脱泡装置」が残されていたのだ。
田中
樹脂を真空状態にして、その中から気泡が抜けるようにする「真空引き」という作業を行うのですが、2度3度と繰り返してとことん抜かないと、気泡が樹脂の中に残ってしまいます。
何度も失敗を重ねて、型の形状や冷却方法を工夫することで、何とかランプ類の樹脂の中の気泡をなくすことができました。
ランプ類のリプロダクトでは、もうひとつ、大きな壁があった。それは樹脂カバーの色だ。テールランプやウインカーの樹脂カバーの色を、何とかオリジナルにできるだけ近づけたい。
田中たちは社内や社外のさまざまな人たちにアドバイスを求めてこの「オリジナル色の再現」に取り組んだ。
そして最終的に、樹脂の着色のために混ぜる材料を変更し、その量を0.1g単位で細かく調整することで、ついにオリジナルのテールランプやウインカーと同じ色の再現に成功した。
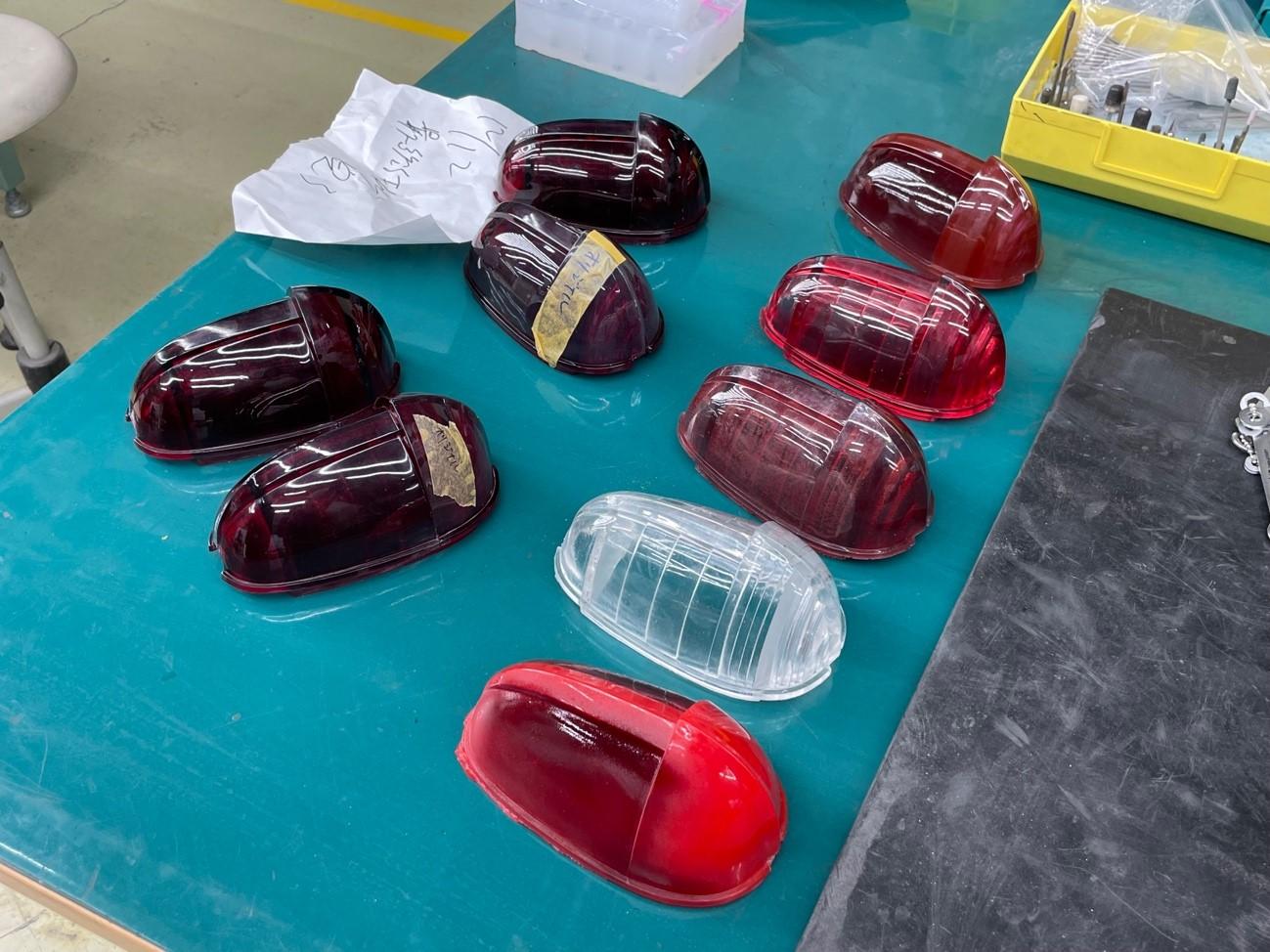
素形材技術の伝統と素晴らしさを実感
素形材技術部の若手の活躍と協力で、オリジナル以上の完成度を実現した金属製の内外装の加飾部品とランプ類の製作。彼らの活躍なしに、このミッションは不可能だった。
そしてこの経験は彼ら素形材技術部の若手にとっても、自分たちの技術や技能を見直す貴重な経験になったという。
長門
私たち素形材技術部のメンバーは普段から元木さんをはじめ、社内の鋳造のエキスパートと相談しながら型製作をしていますが、工程ごとに人が変わるため個人ではあまり接点がない場合もあります。
でも今回、元木さんたちと一緒に仕事をすることで、日常の業務では絶対にできない体験、これまで知らなかった数多くのことを学ぶことができました。今回得たことを、しっかり後輩たちに伝えていきたいと思います。
また、この仕事を素形材技術部に依頼した首藤にとっても、今回の経験は自身が入社以来手掛けてきた仕事を見直すきっかけになったという。
首藤
すでにあるモノを加工するのではなく、素材から直接、つまり「ゼロの状態から」モノづくりができるのが、素形材技術部の強み。
私は入社以来、この素形材技術に関連する仕事をしてきましたが、今回、この技術の素晴らしさを再確認してうれしく、また誇りに思いました。
約70年前に初代クラウンを手掛けた人々の「より良いものをつくりたい」というモノづくりの情熱は、首藤たちプロジェクトメンバーに受け継がれ、さらにトヨタの未来を担う若手に引き継がれた。
この情熱は間違いなく、初代クラウンのような画期的な「何か」を生み出すに違いない。
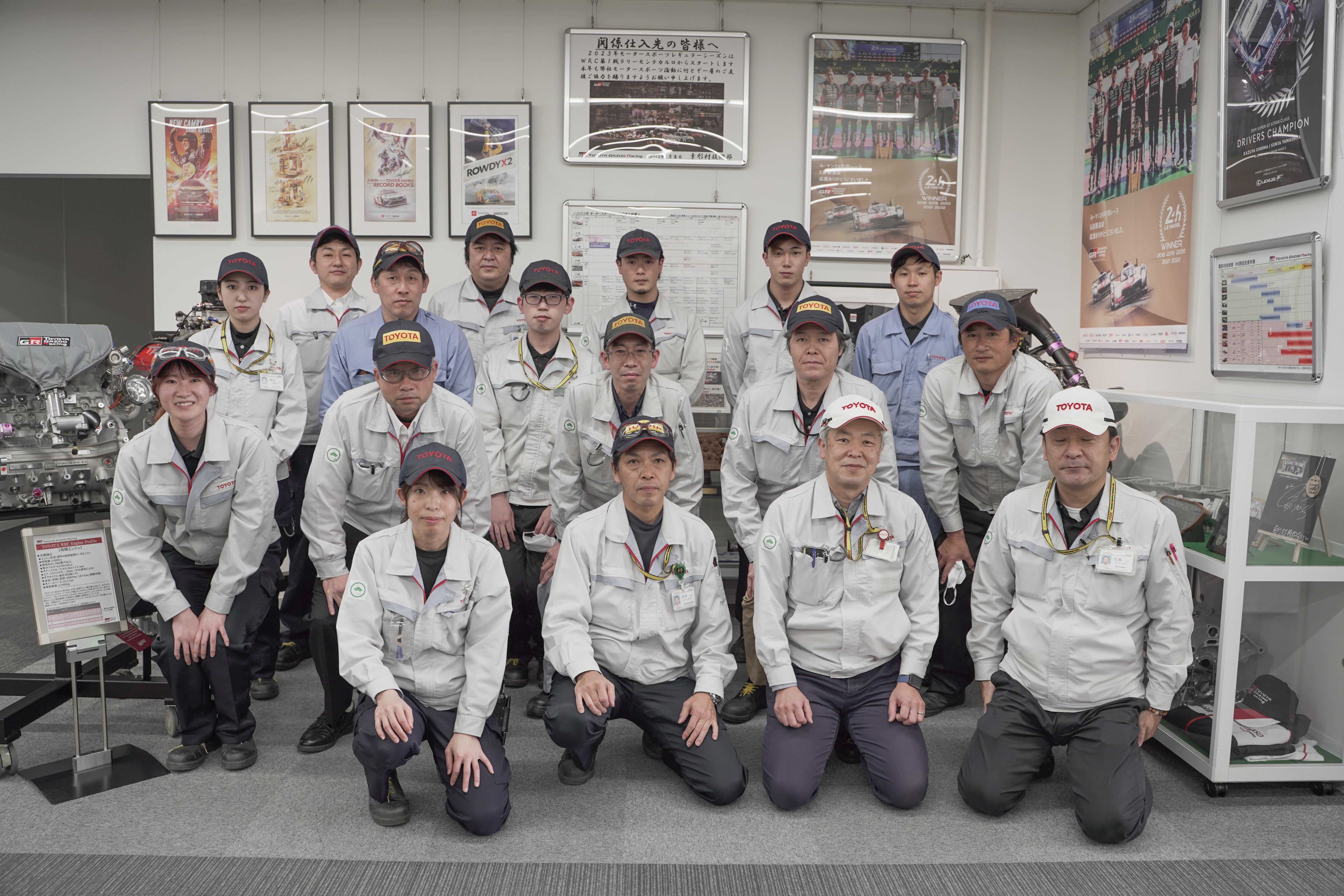
(文・渋谷康人)