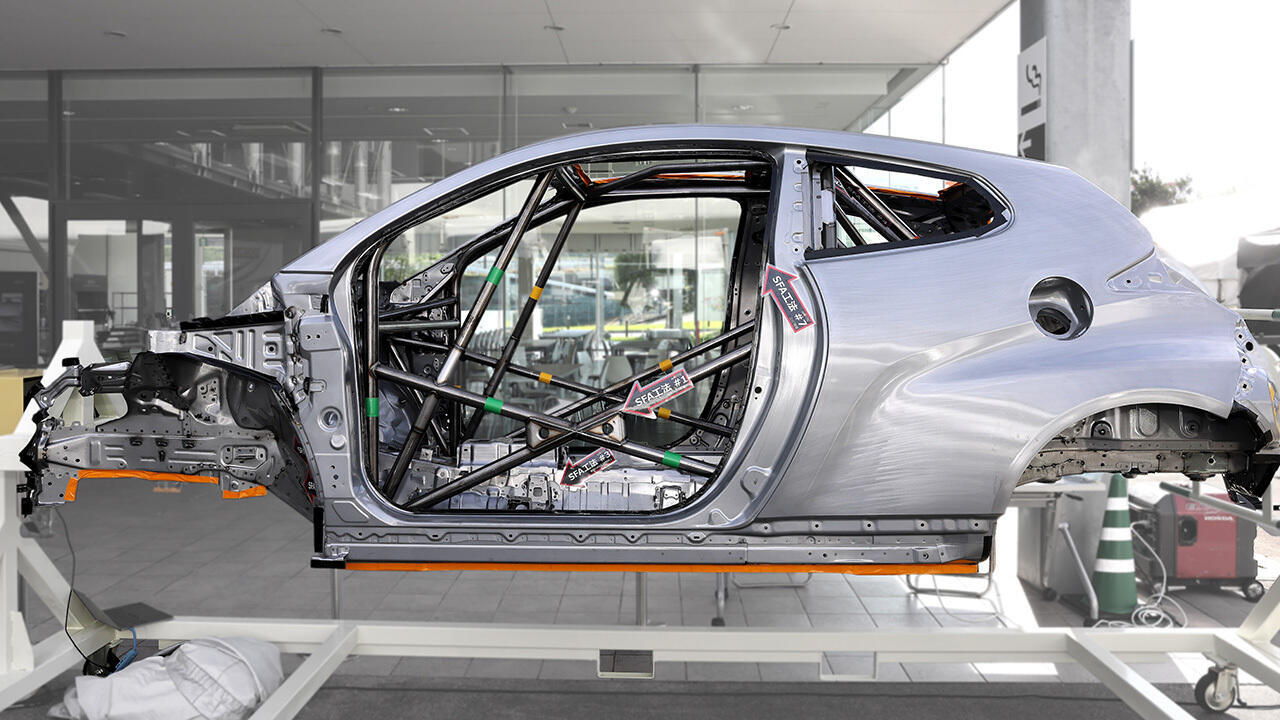
Toyota is tackling the challenges faced by motorsports and working to expand their reach. At a recent Super Taikyu event, the company unveiled a world-first welding technology.
Done in three days
The “slow and careful” approach to welding allows roll cages to be built almost exactly as designed, with no distortion. It has also changed how the cars are assembled.
In the past, technicians would fit each piece by hand over a span of two to three weeks. With the new method, the roll cage can be made as a subassembly * .
*A process that involves combining components prior to assembling the product into its finished form.
The welding process is broken down into three stages to improve workability.
The roll cage is divided into three modules, each assembled outside the vehicle body (0.5 days)
↓
Modules are mounted within the body (1.5 days)
↓
Welding onto the body (additional welding, 1 day)
The combination of SFA and subassembly shrinks working time from two to three weeks down to three days.
The highest praise
The new SFA method greatly boosted the body rigidity of the GR Yaris. Some drivers, however, now found it to be “too rigid.”
When a car is steered around a corner, the body flexes to absorb the forces in tandem with its suspension. With a stiffer body, the suspension now has to do more of the work. While the breadth of suspension tuning has expanded, the team is still searching for optimal settings.
Yet for those who led the development, the drivers’ reaction was “the best,” said Shibata, and “the highest praise,” said Project General Manager Kawakita. Lowering rigidity is simply a matter of adjusting the number of reinforcement points—finding ways to increase it was the hard part.
Making motorsports sustainable
The use of robots promises to cut down costs as well as roll cage production times.
But as Kawakita stresses, “We certainly aren’t developing this to take jobs away from our welders.”
Project General Manager Kawakita
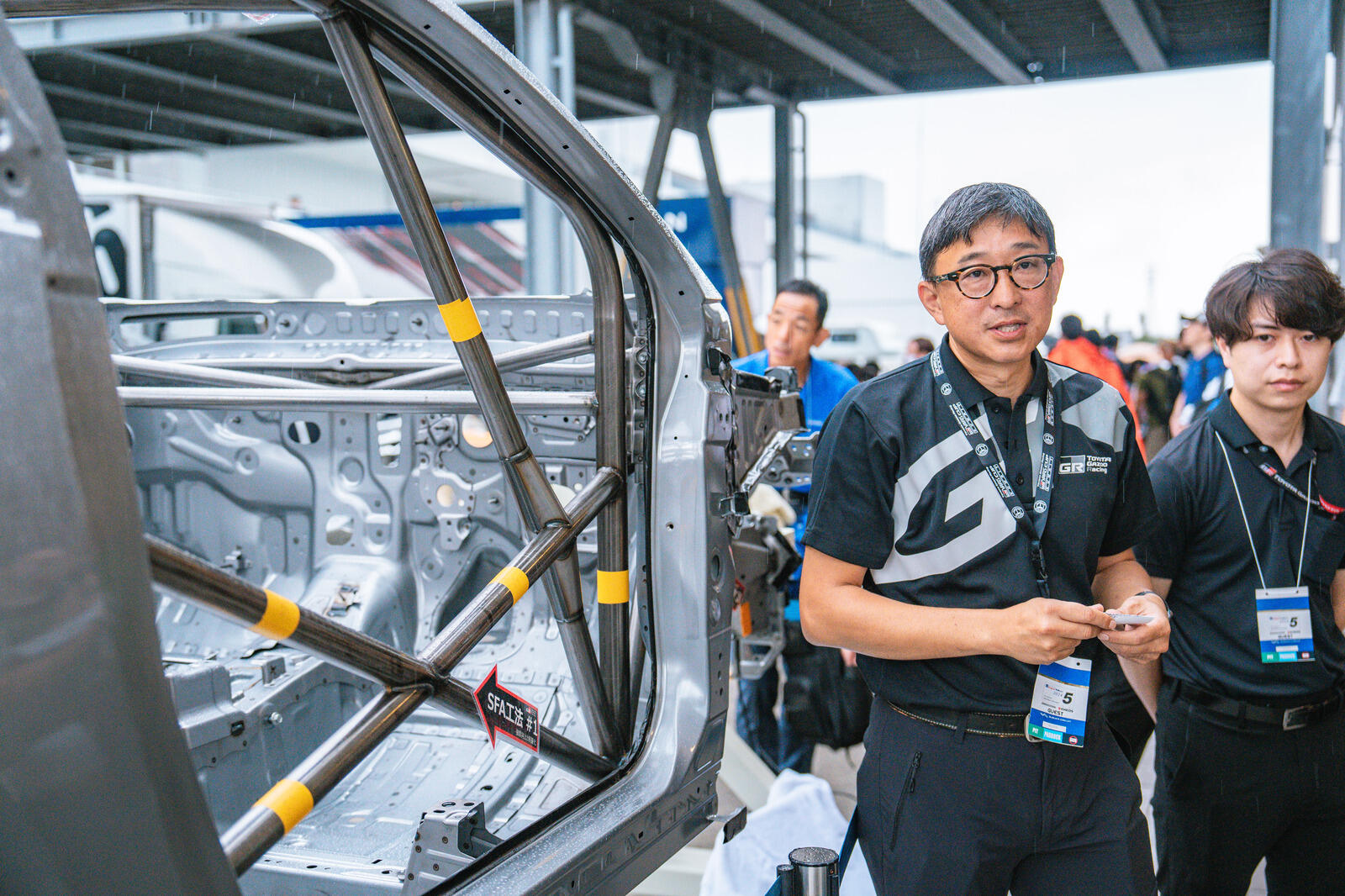
Even if the body dimensions are correct, slight deviations will always exist. If you build a roll cage without accounting for those variations, the top WRC (World Rally Championship) drivers in Finland and elsewhere will say the car doesn’t feel good.
Since this is something our robots can’t handle, ultimately, there will be a greater need for skilled welders who know about driving, and today’s master welders can make more time to focus on such areas.
At the same time, I think entry-level racers will be pleased that we can provide a body in white with a roll cage quickly and at a lower cost.
As Morizo has said, we certainly aren’t developing this to take jobs away from our welders.
It’s easy to view the situation that way—even at our Suzuka display, some commented that this would cost them their jobs.
But that’s not the case. We want to enable them to do more tuning for the entry class, amongst other things. Unless we communicate that this is what we are aiming for, people will get the wrong impression.
“I’m sure there are many people who love rally and motorsports but feel the bar is too high,” remarked Morizo after driving the first GR Yaris Rally2. “I hope GR can lead the way in providing opportunities for those who don’t know how to get involved.”
The newly unveiled SFA method will surely help lower the barriers to participation in motorsports.
After Suzuka, the GR Yaris, with its SFA-assembled roll cage, also competed in Round 6 in Okayama the following month.
These two races are just the beginning. For Toyota, motorsports will continue to serve as a platform for honing new technologies.