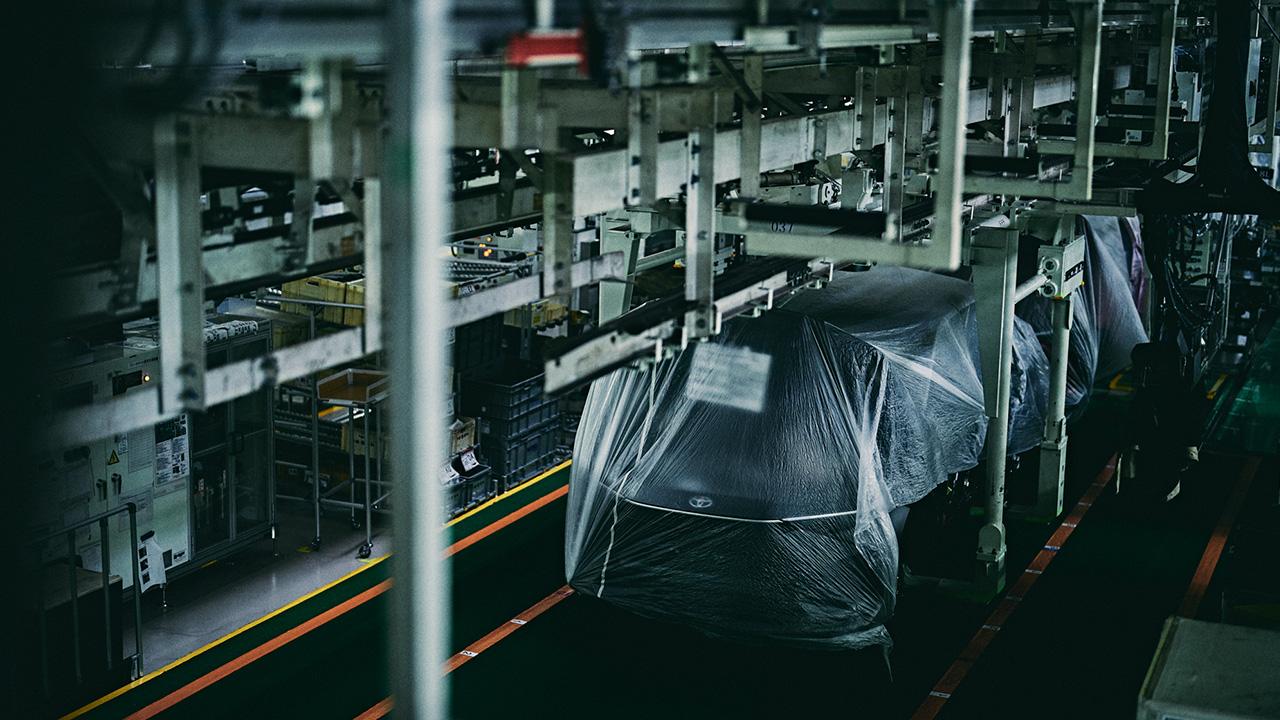
Customers are awaiting delivery, and workers are eager to make cars--a look at the pressures affecting Toyota's production genba.
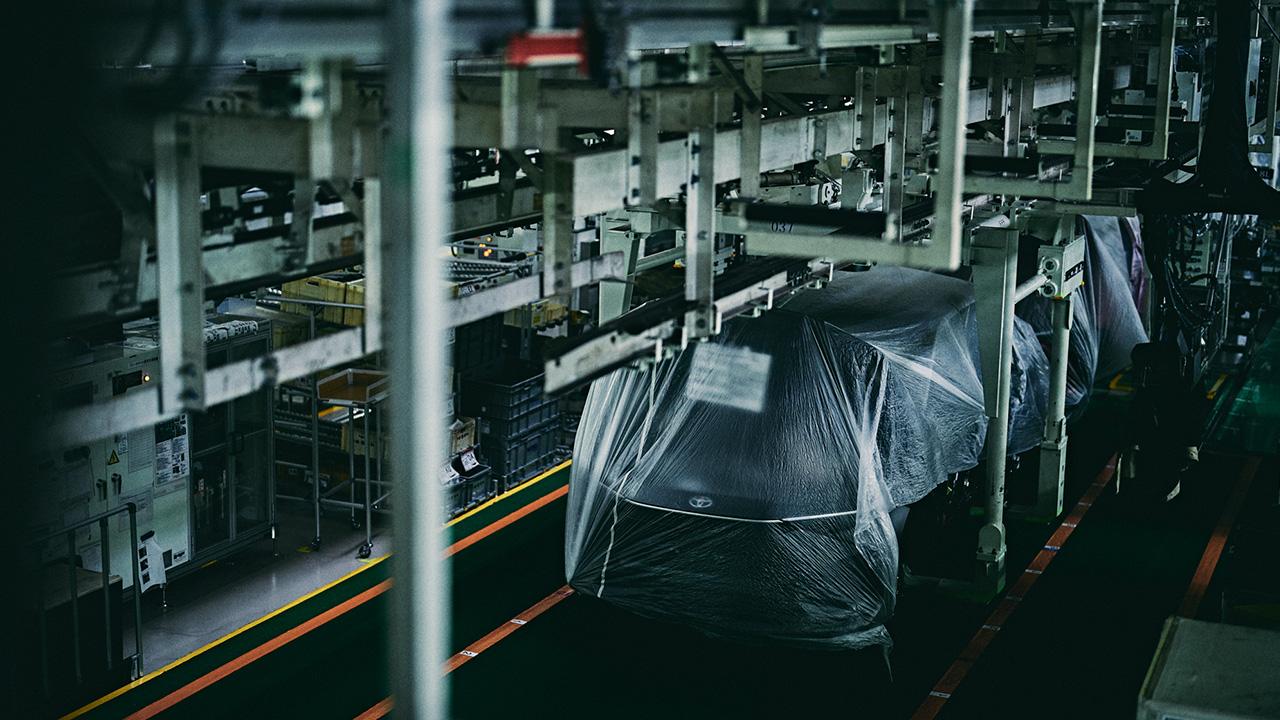
“I’ll be completely honest with you.”
These words, uttered at the outset of the interview, demonstrated the resolve at Toyota’s genba (production frontlines). Yuji Akari, Final Assembly Division Deputy General Manager at the Motomatchi Plant, spoke candidly about the situation inside the plant where the unabating pandemic and chip shortages have brought car production to a standstill.
New cars kept under wraps
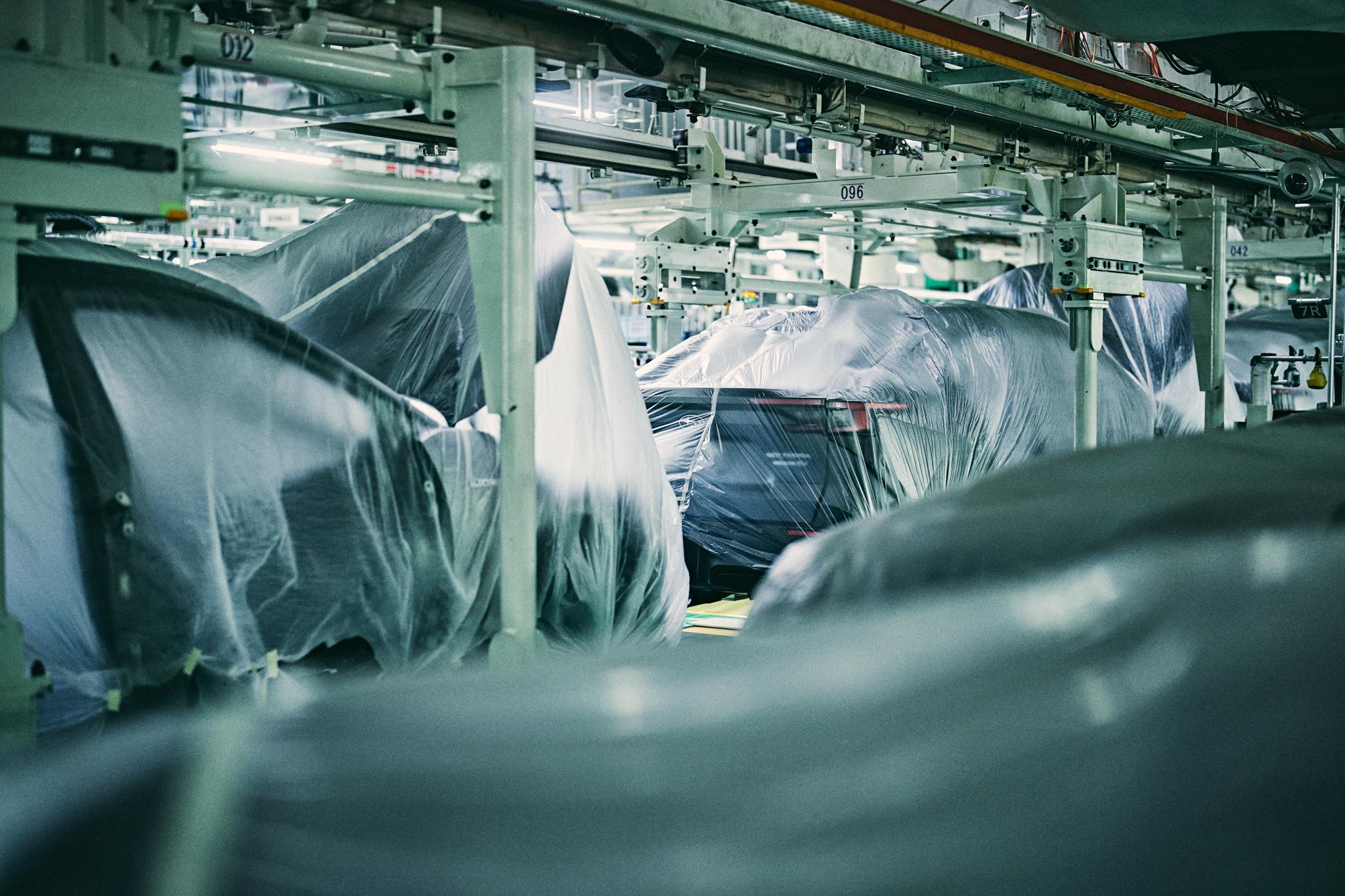
When Toyota Times visited the plant in July, it was instantly clear that something wasn’t right. The bustling plant that had once teemed with life was completely silent. On the assembly lines, countless cars stood covered in plastic where they had halted.
Many customers across Japan are excitedly awaiting delivery of their new vehicles. Toyota’s dealers and parts suppliers are also waiting. Everyone is eager for cars to roll off the line as soon as possible. And yet, they can’t.
Those words—“I’ll be completely honest with you”—revealed a desire to avoid sugarcoating the difficult situation and a sincere commitment to the customers, dealers, and suppliers affected.
This article is a true-to-life account of experiences on the genba.
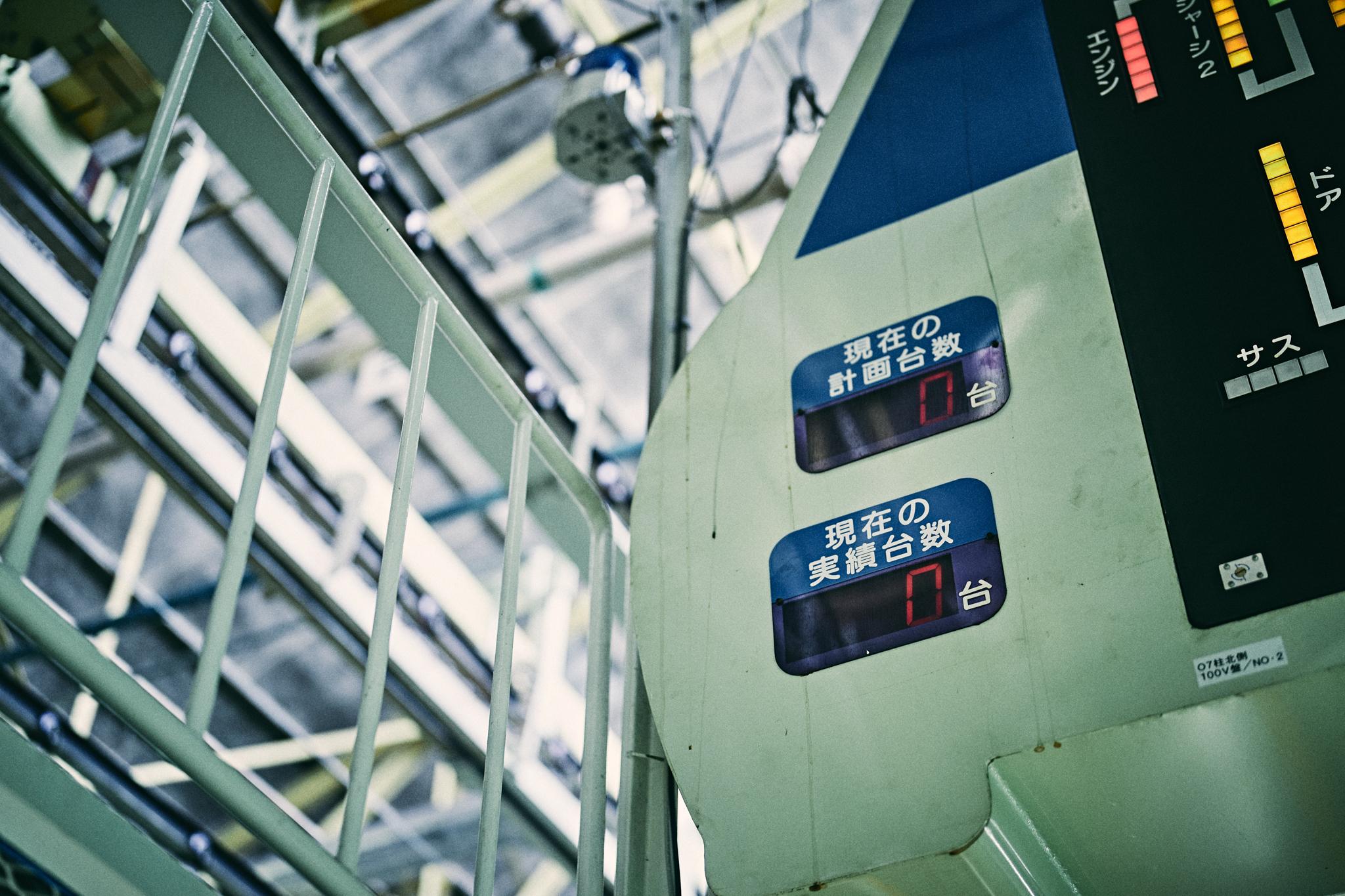
Sad to see a silent plant
The Motomachi Plant opened in 1959, the dawn of the passenger car era. Currently, it has around 5,500 workers, making models such as the Crown, bZ4X, and Mirai. But the plant had to suspend operations for more than two months between late June and early September.
“I’m as old as this plant,” says Akari, who has spent most of his working life at Motomachi. He began speaking of the ongoing shutdown, “I would love to say that the stoppage has allowed us to do many things we normally can’t do, but….”
Yuji Akari, Deputy General Manager
Our group and team leaders have been running training drills for their members on the stopped lines. There are still things we can do even without the lines running.
We’re also undertaking kaizen efforts to improve car-making processes in keeping with the 4S approach (Sort, Set in Order, Shine, Standardize). We’re also investing in the future in the form of personnel development. Unfortunately, we don’t have moving lines to teach them things they can immediately use in their jobs.
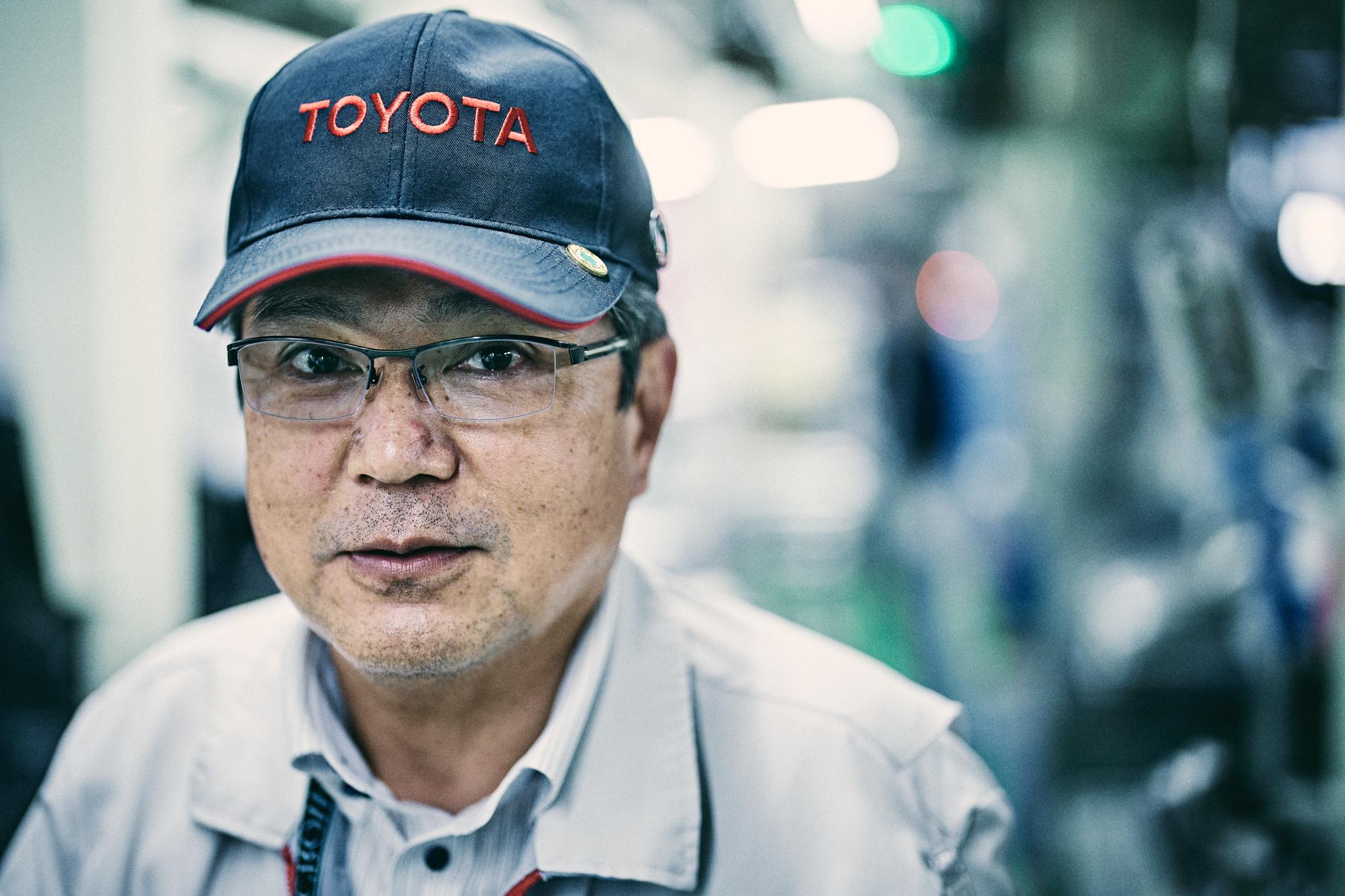
It’s sad to see. A dark, silent plant is no plant at all. And it really hurts to know that we’re keeping our customers waiting.
Those sentiments were shared by Seiichiro Kaneda, Akari’s colleague. He also explained how the plant’s personnel were making use of the downtime.
Seiichiro Kaneda, Manager
In terms of safety and quality, we’re reviewing our goals from scratch, seeing how past events have shaped what we do now and adjusting systems for what lies ahead.
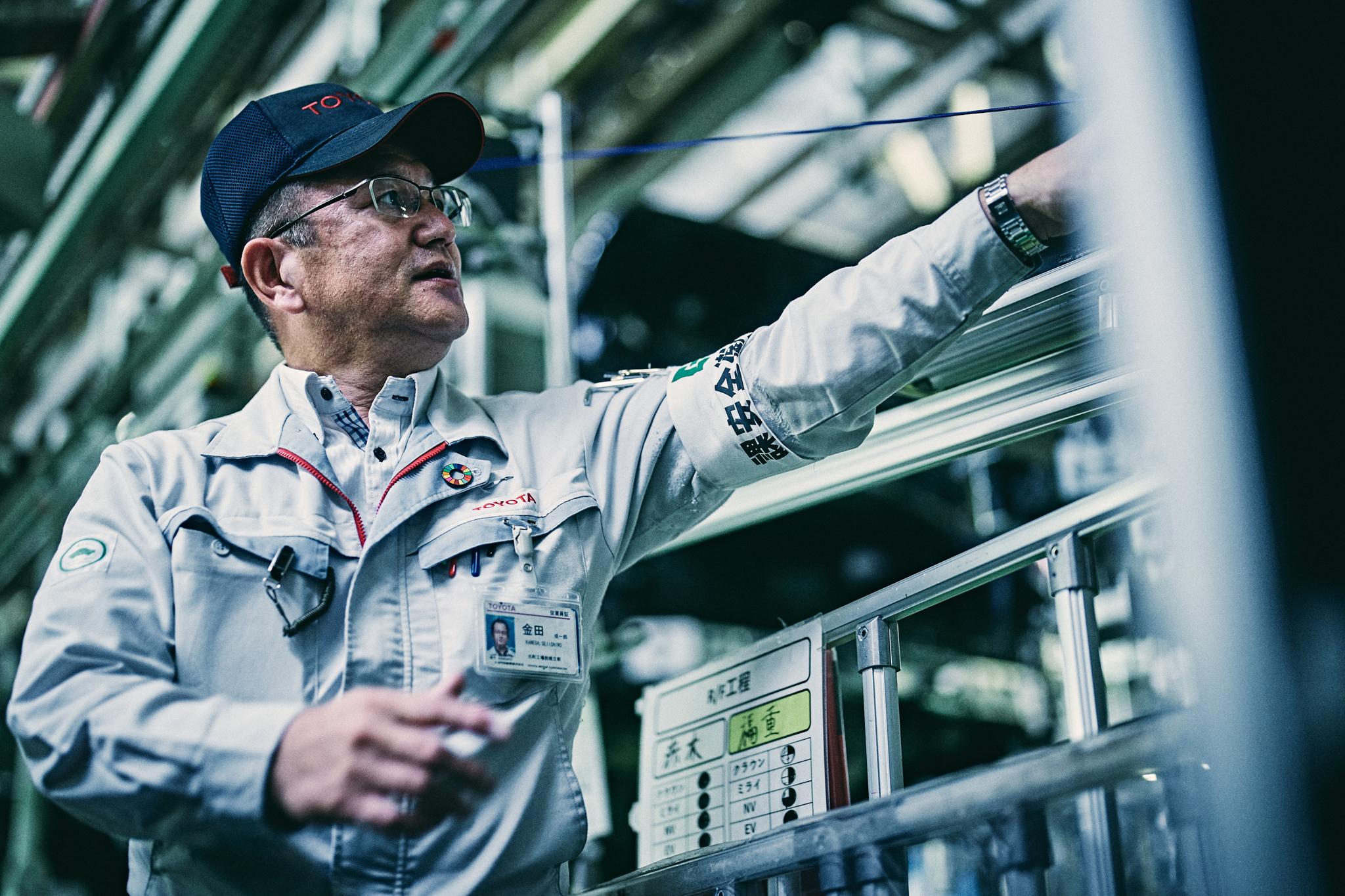
We have time to review things we were too busy to check before. We can get a proper understanding of past mistakes. And we can do it as many times as we need, senior and junior staff working together. We’re improving our structure so people can act with greater autonomy, rather than being told what to do, because they understand our goals.
Supervisors step up for their staff
If you can’t make cars, improve the workplace. Substantial kaizen efforts could be seen throughout the plant.
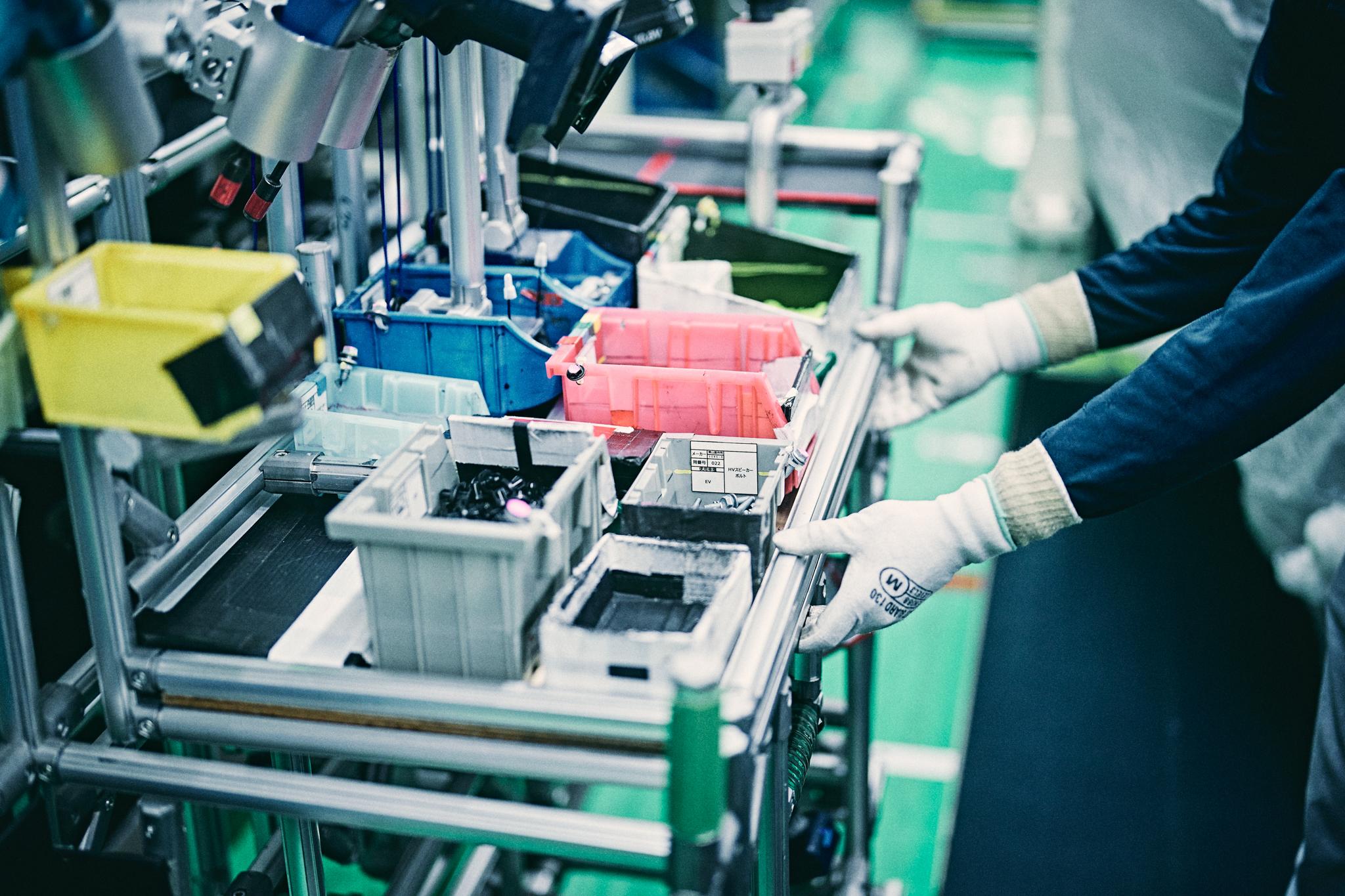
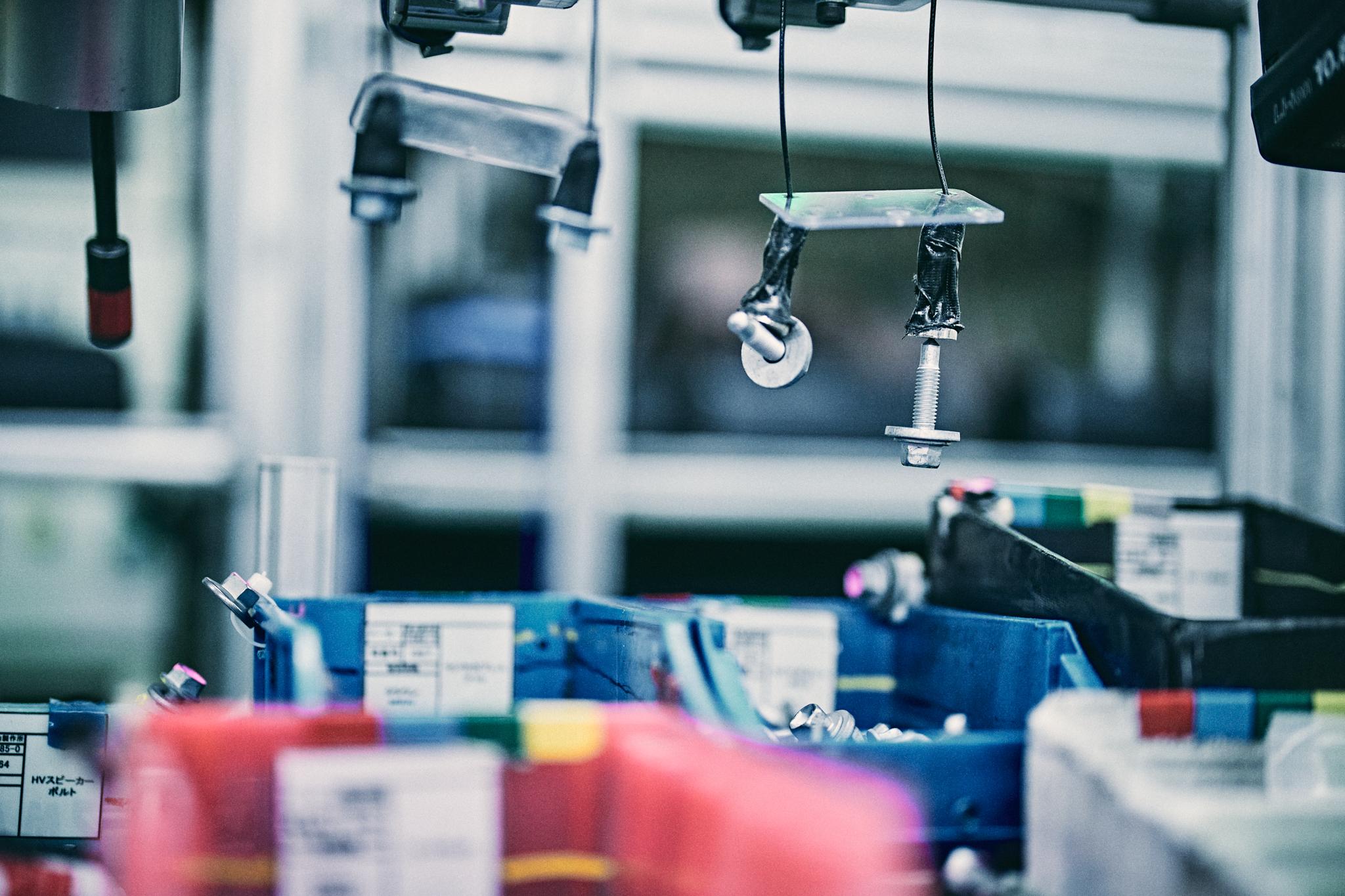
Keigo Adachi developed the improvements pictured above with materials from around the plant after asking colleagues to share tasks they found troublesome. He is also among those awaiting delivery of their purchased cars. “Just as I can’t wait to see my car, I want all our customers to get theirs as soon as possible. It’s very frustrating being unable to make cars.”
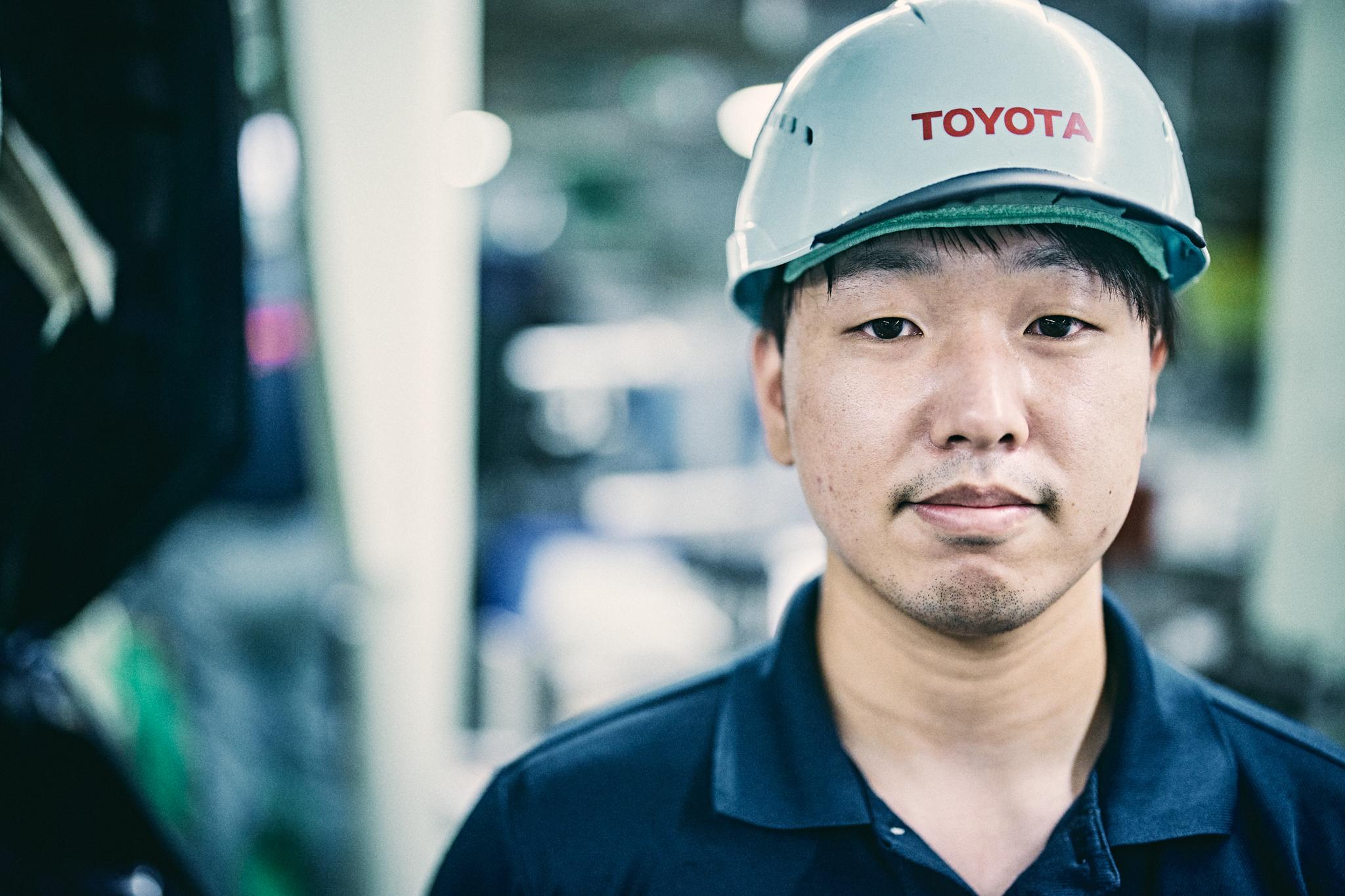
In many spots around the plant, workers could be found deep in conversation. Like the improvements Adachi devised, other good ideas are constantly being shared between teams, seeking to raise the bar in all aspects of operation, from safety and quality to productivity and staff development.
Akari says, “Supervisors make improvements based on suggestions from their teams, and by explaining these ideas to others, they grow as well.”
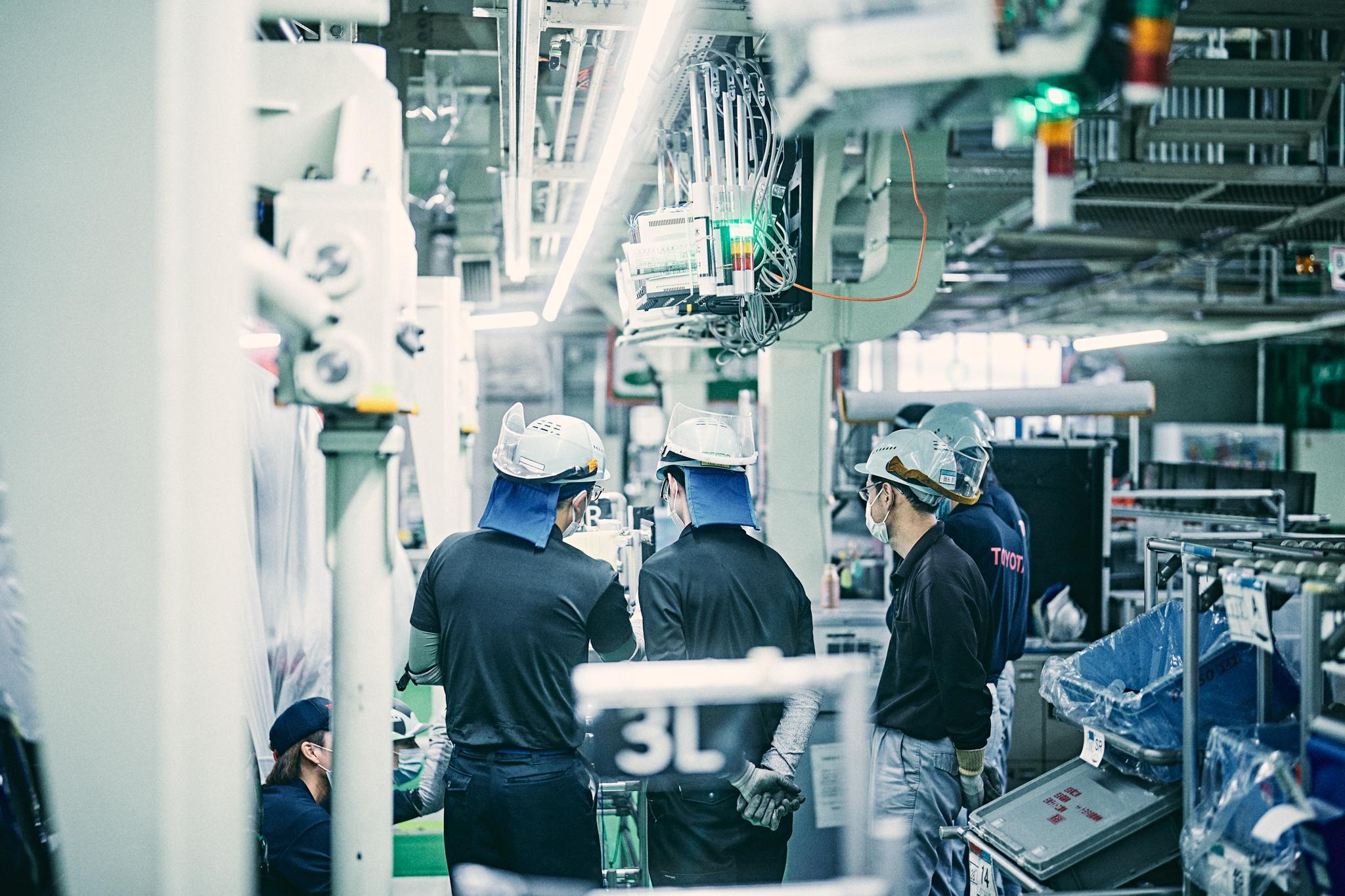
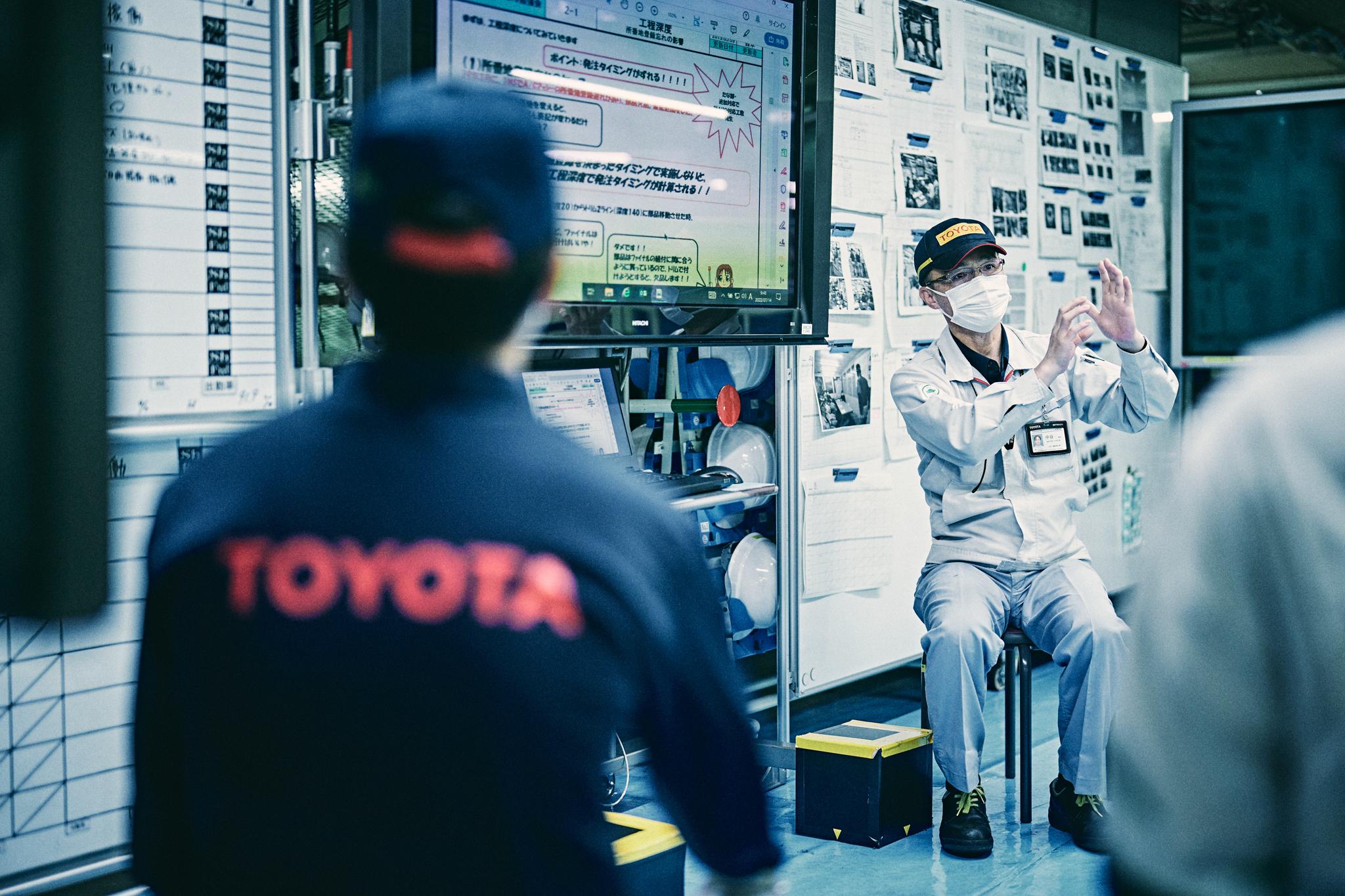
Future uncertainty clashes with a commitment to customers, dealers, and suppliers
Toyota’s plants do more than just assemble cars. The teams that deliver parts from suppliers to each production line also play an important role. Katsuhisa Sakai heads the Logistics Section of the Motomachi Plant Final Assembly Division.
Katsuhisa Sakai, Manager
To be honest, the shutdowns initially gave us a chance to catch our breath. But after a couple more repetitions, the younger employees began to worry about what was going on. Production facilities are extremely good at handling set tasks, in set quantities, within set timeframes. But when it comes to figuring out what to do, that can pose a challenge.
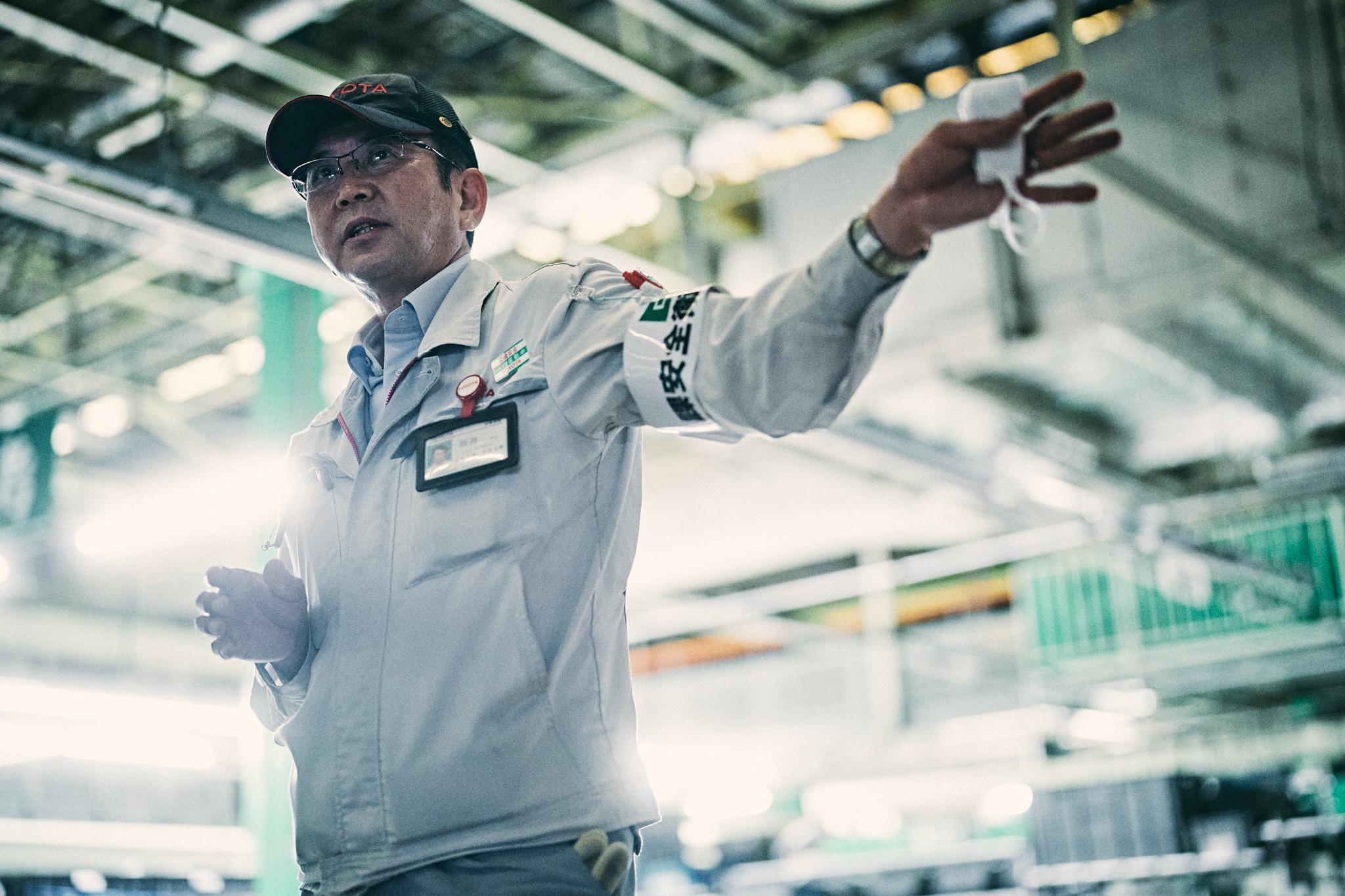
That said, even in logistics, we’ve managed significant improvements. Gaining a new understanding of things we thought we knew enough has transformed how we approach our work.
Each day, the Motomachi Plant receives some 1,300 crates of parts while sending back the same number of empty containers. In the first half of the year, an increase in the workload and types of parts led to errors. Crates were returned with components still inside, forcing suppliers to make extra deliveries of the missing parts on short notice.
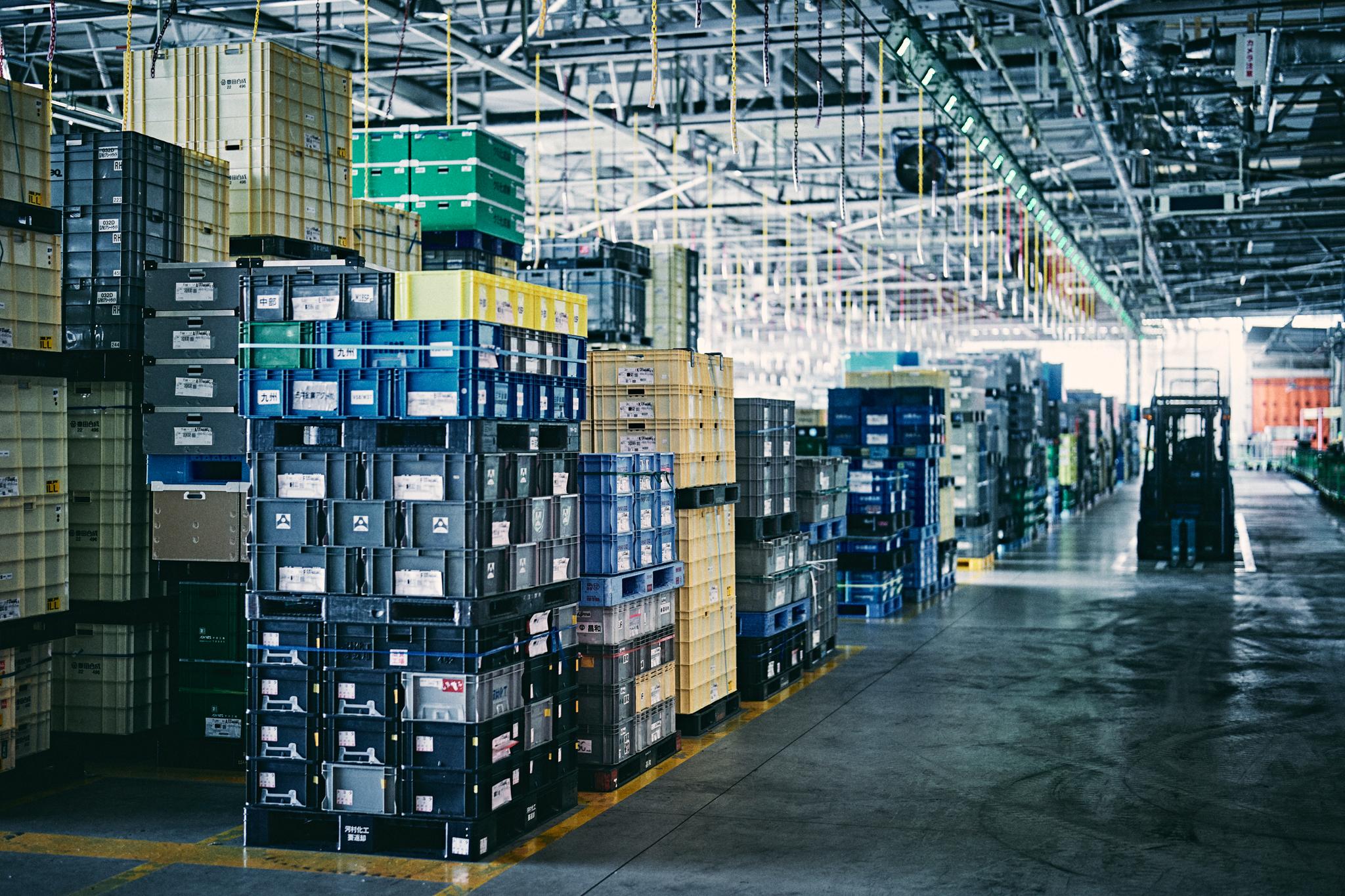
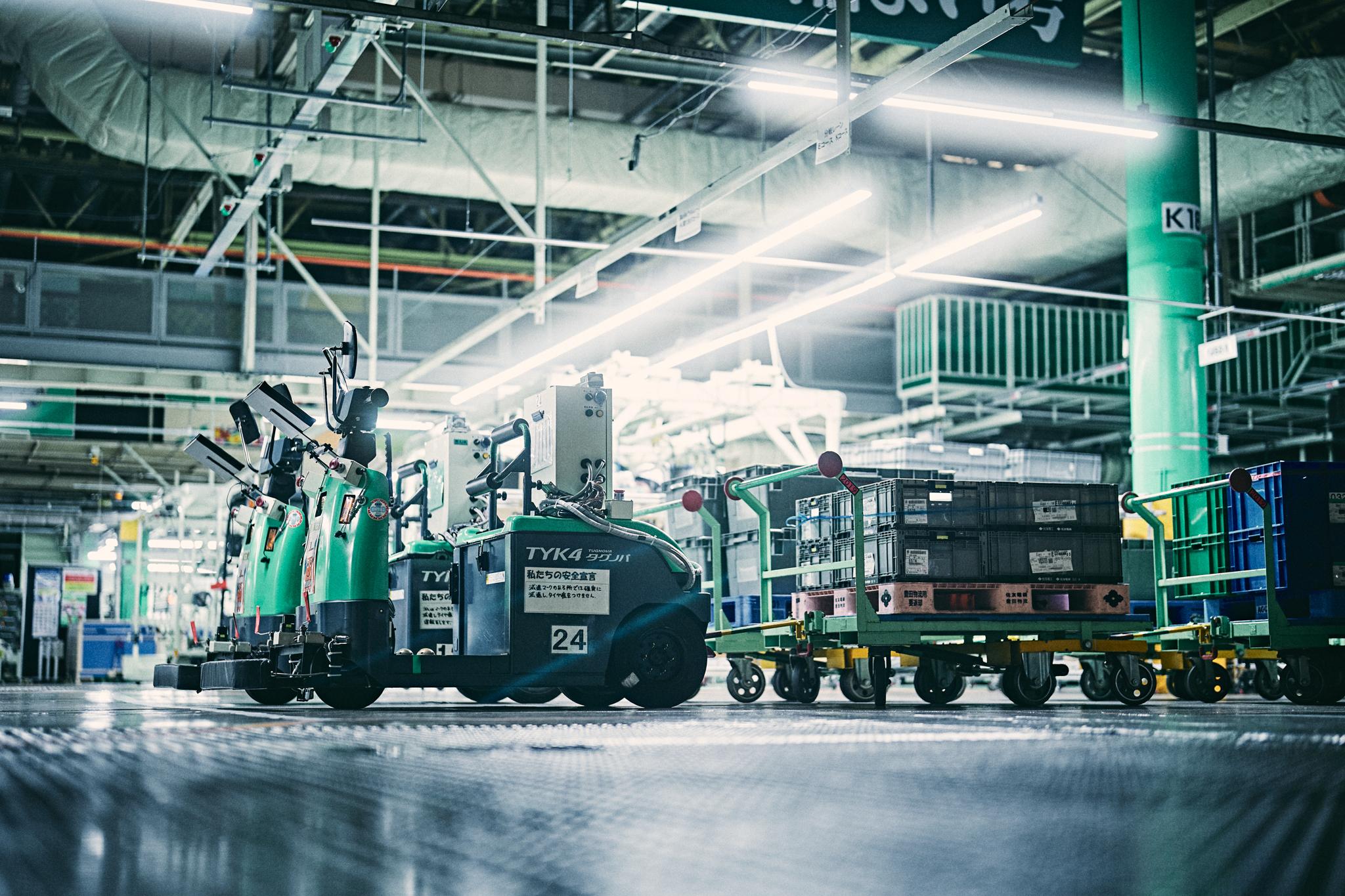
The team’s younger members set about eliminating such mistakes on their own initiative, creating videos outlining the key points in procedures so that even inexperienced newcomers can easily gain a proper grasp of standard tasks. These videos serve as kinds of textbooks that anyone can use as a quick reference.
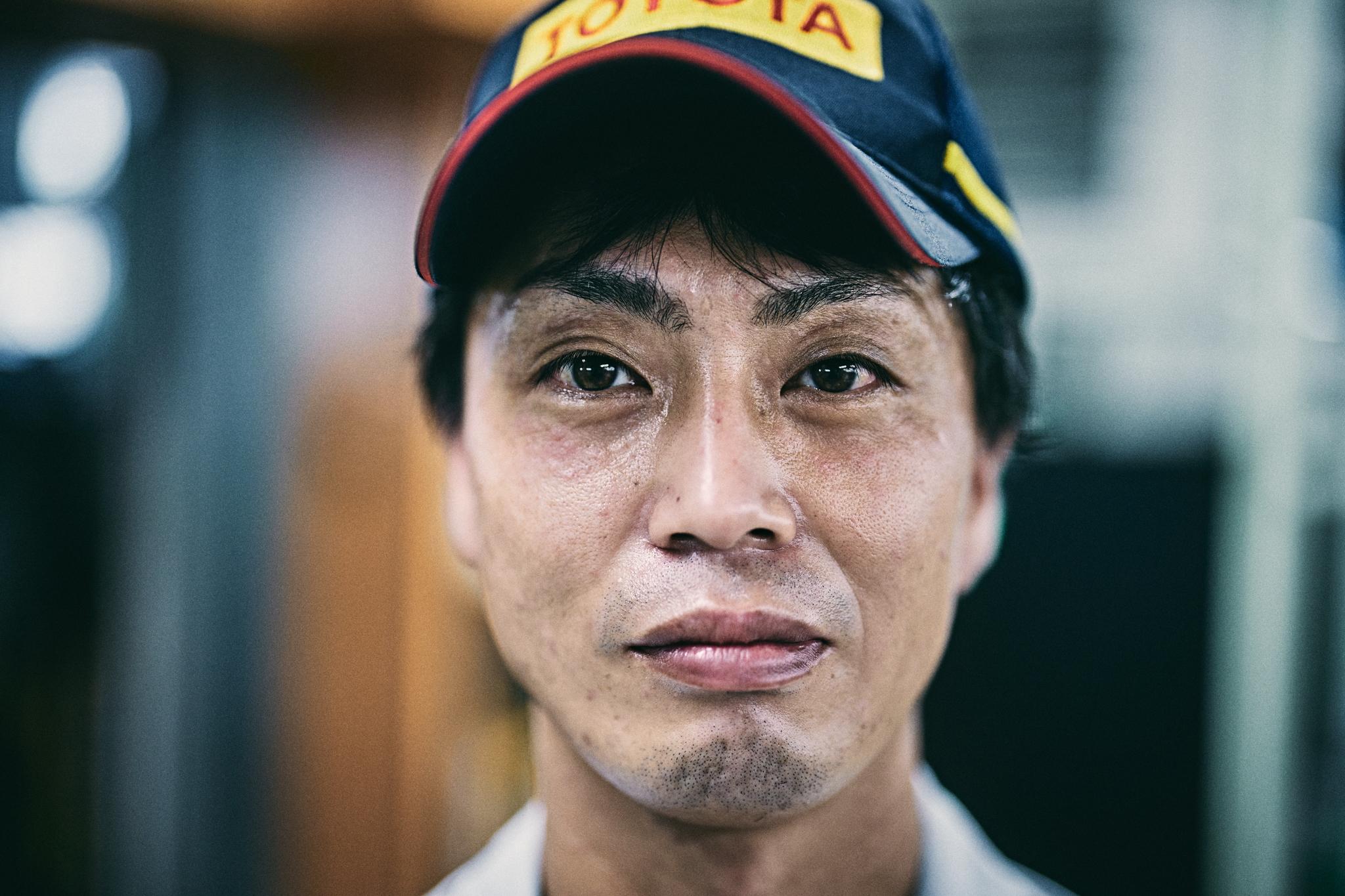
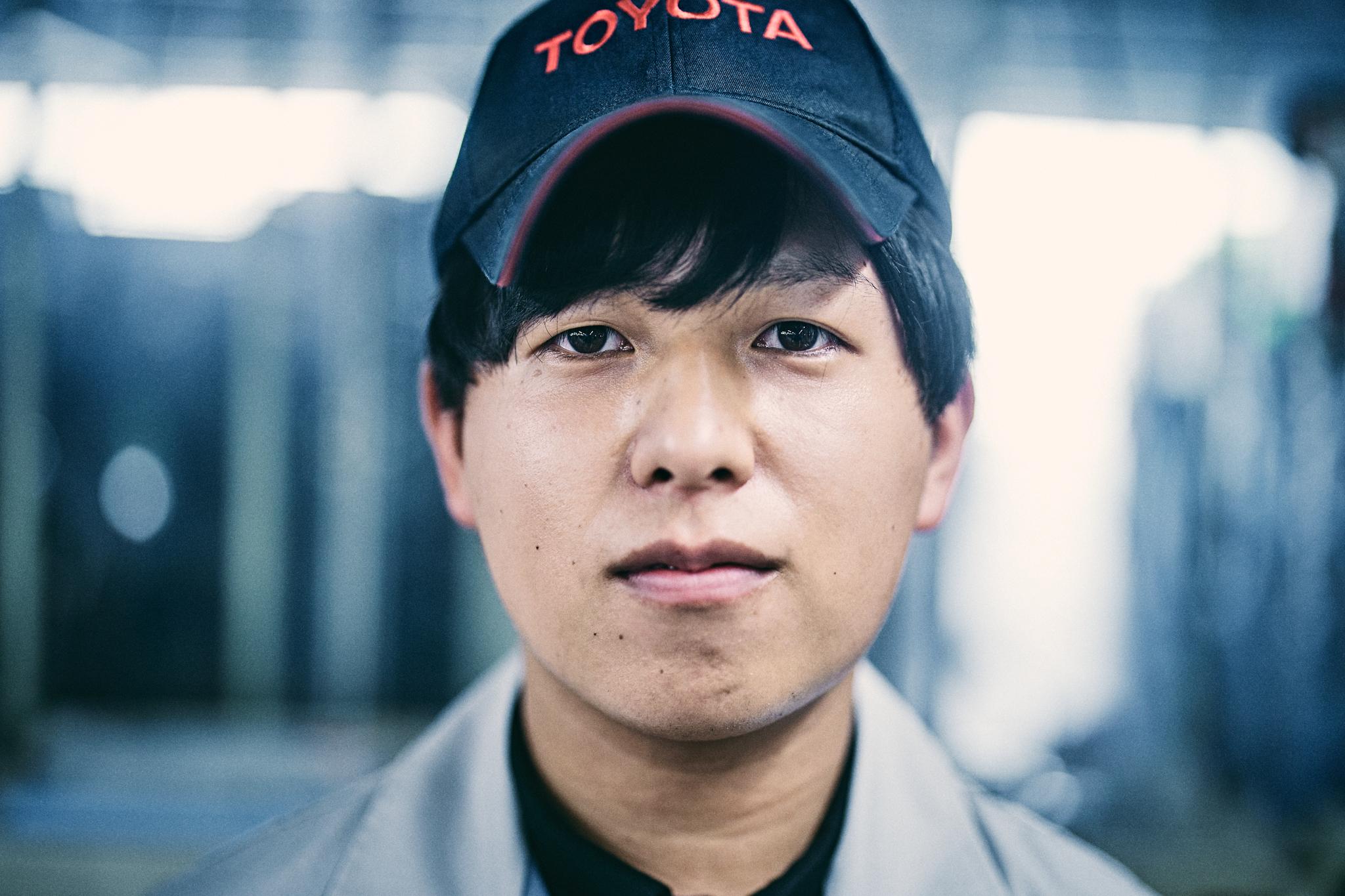
Small mistakes by plant personnel can cause trouble for those working at suppliers and potentially result in important parts being unnecessarily scrapped. The logistics team held more discussions to boost accountability among all members, including newcomers.
Toyota regards its suppliers as “branch plants,” with the goal of co-existence and co-prosperity. Previously unable to ensure that every worker embraced this philosophy, the Motomachi Plant now had the time to reflect and nurture the individuals who will carry it forward.
Even so, the production floor is awash with unease about how long plant stoppages will last. Shinnosuke Kayamori shared what’s been on his mind.
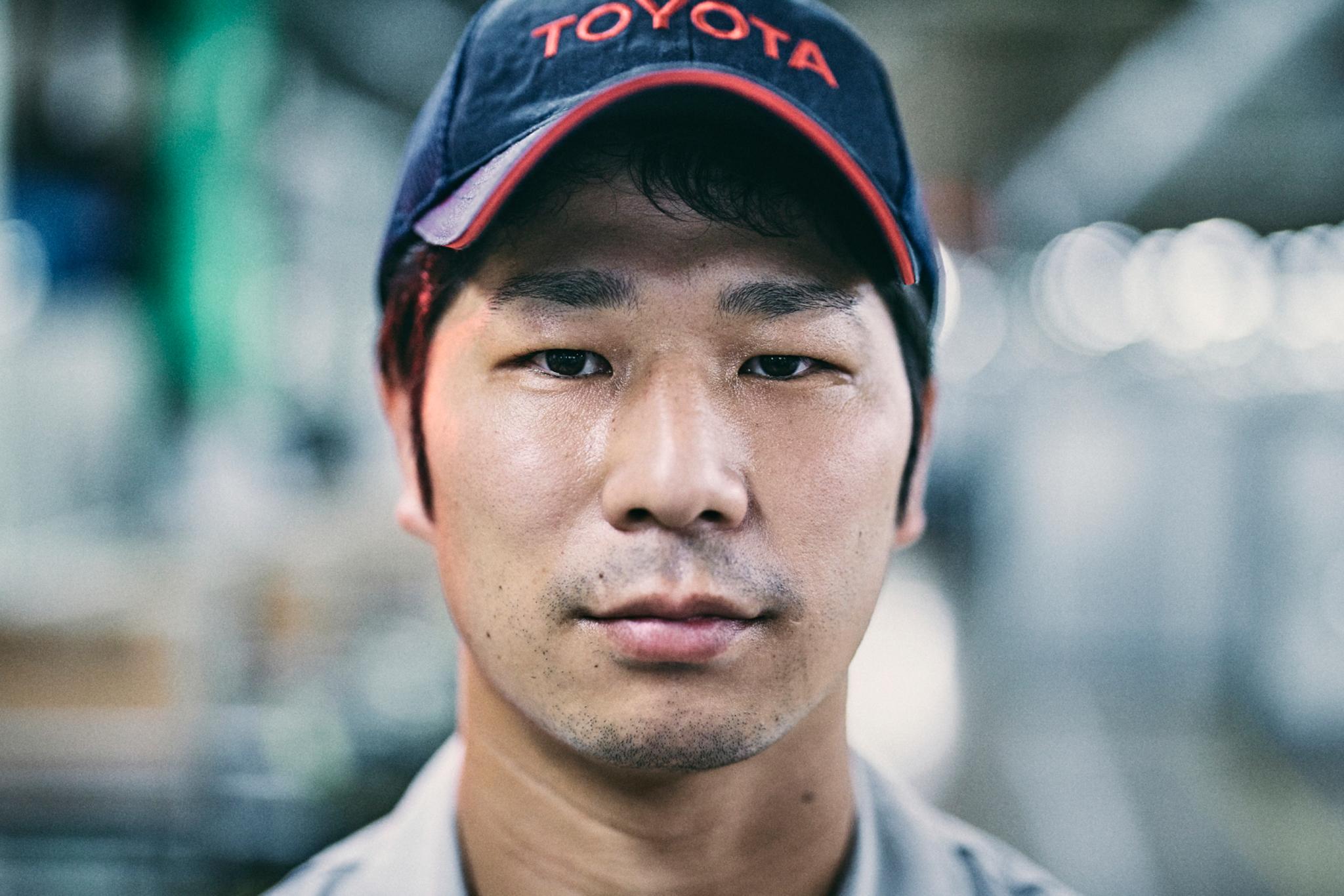
“You don’t know until the last minute whether you should go in to work or take the day off,” he said. “We had temporary workers and colleagues from other departments coming in to help, and these different circumstances sometimes risked harming team motivation.” Despite this, he says, “Because the pandemic and chip shortages are problems beyond my control, I am focusing on what I can do to make improvements.”
Such kaizen efforts extend beyond the plant walls. Line No.1 at the Motomachi Plant produces four models with different powertrains. This requires a large number of parts, some of which have to be picked up from elsewhere in the plant and transported to the production line on 10-ton trucks. The team challenged itself to figure out ways of handling an oil leak from these trucks.
Since the only point of reference was a printed manual for 4-ton trucks, video guides were created so that many team members could learn how to respond if something went wrong with these new vehicles.
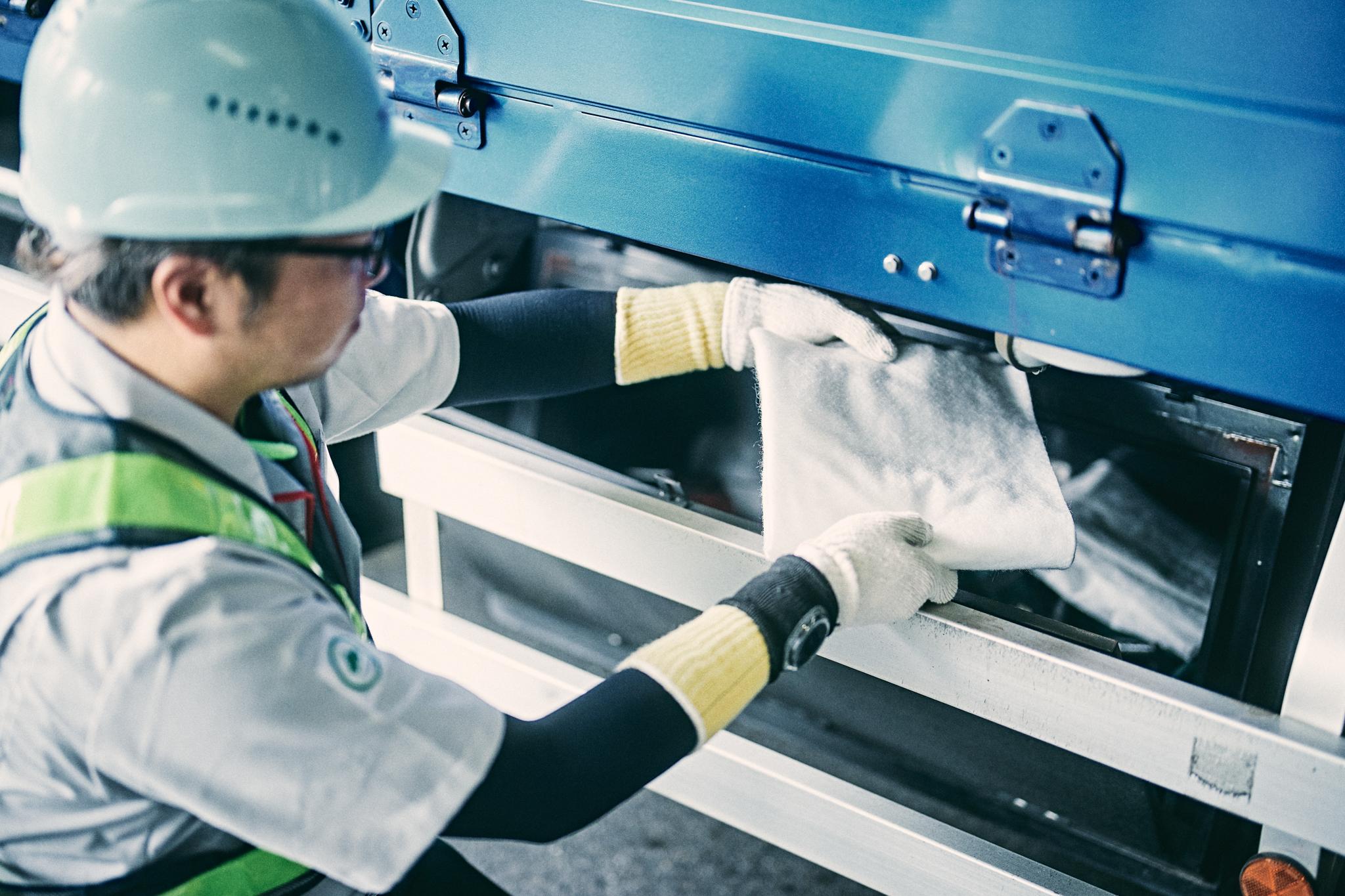
This initiative was led by Team Leader Ikuo Matsushita, who used the plant’s downtime to earn a large vehicle license. “I’m usually too busy to get new licenses, but I was able to make the most of this period,” he reflects.
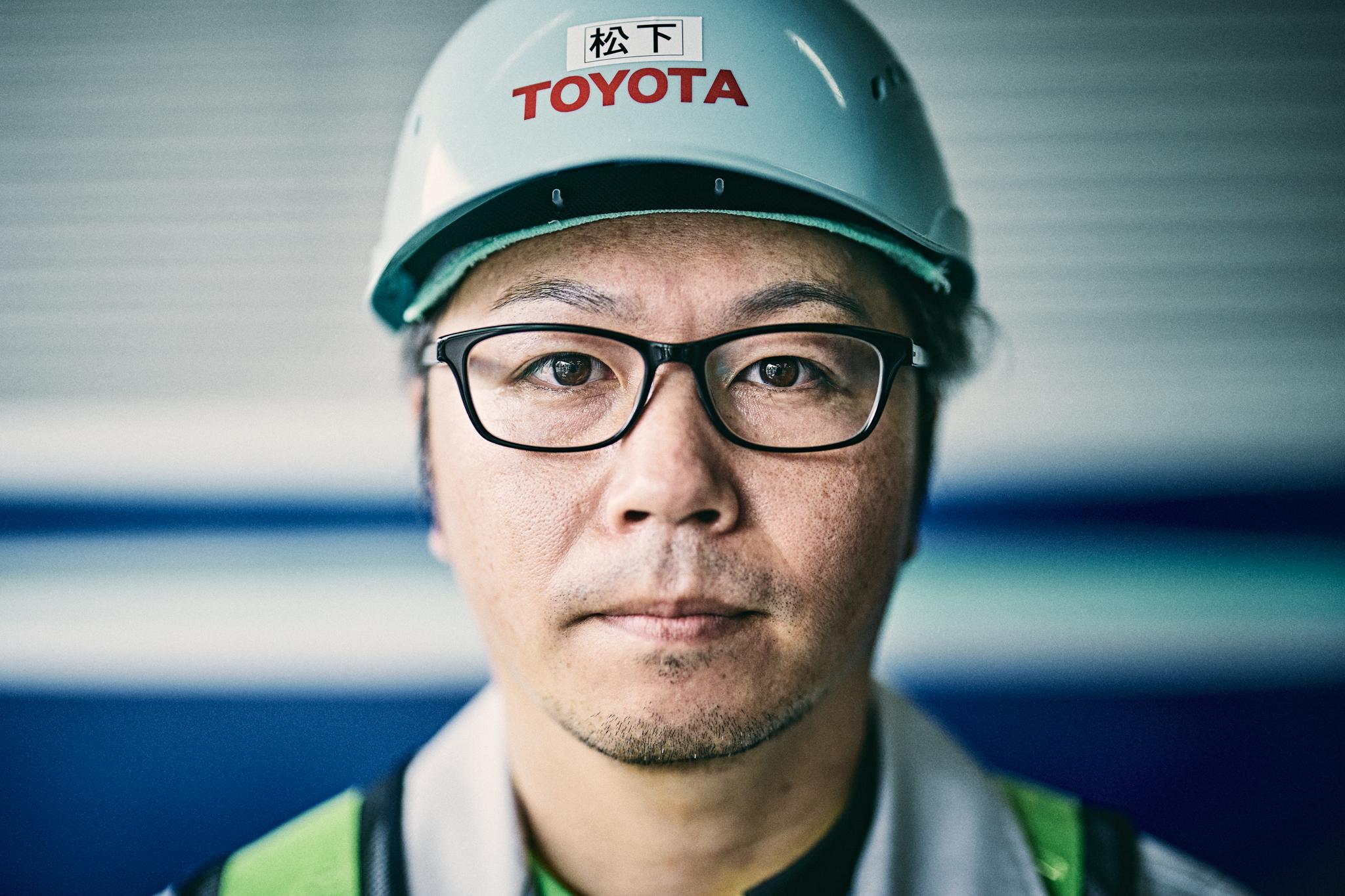
Although the production lines aren’t running, the plant workers who make things for a living refuse to stand still. Regardless of the situation, they keep doing what they can to improve their conditions.
The unprecedented length of this crisis makes for an uncertain future, giving rise to unbounded anxieties. Through it all, however, the shared determination to deliver cars to customers as soon as possible remains constant. And the efforts of the hard-working people at Toyota’s genba continue to underpin the creation of ever-better cars.
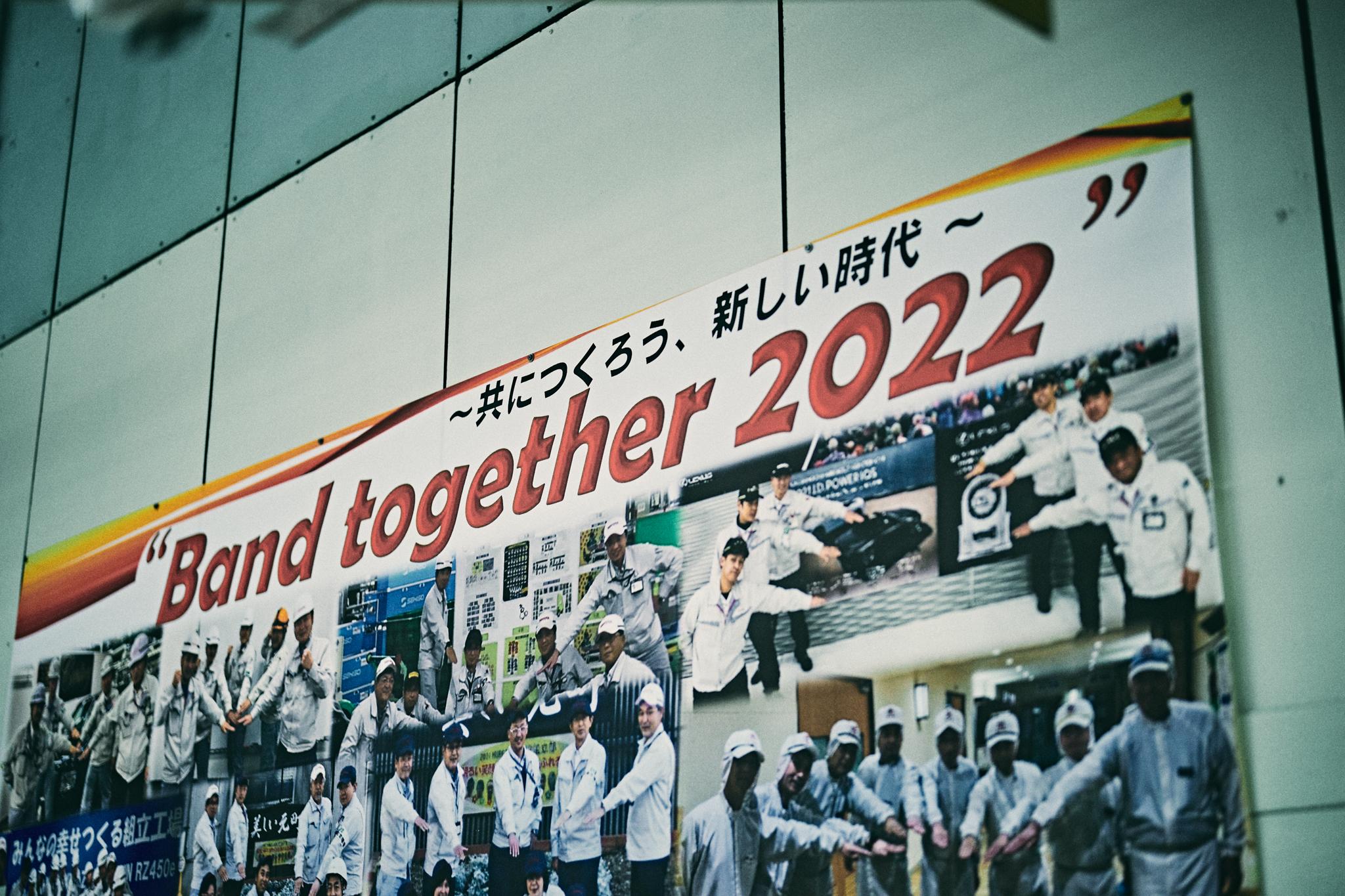