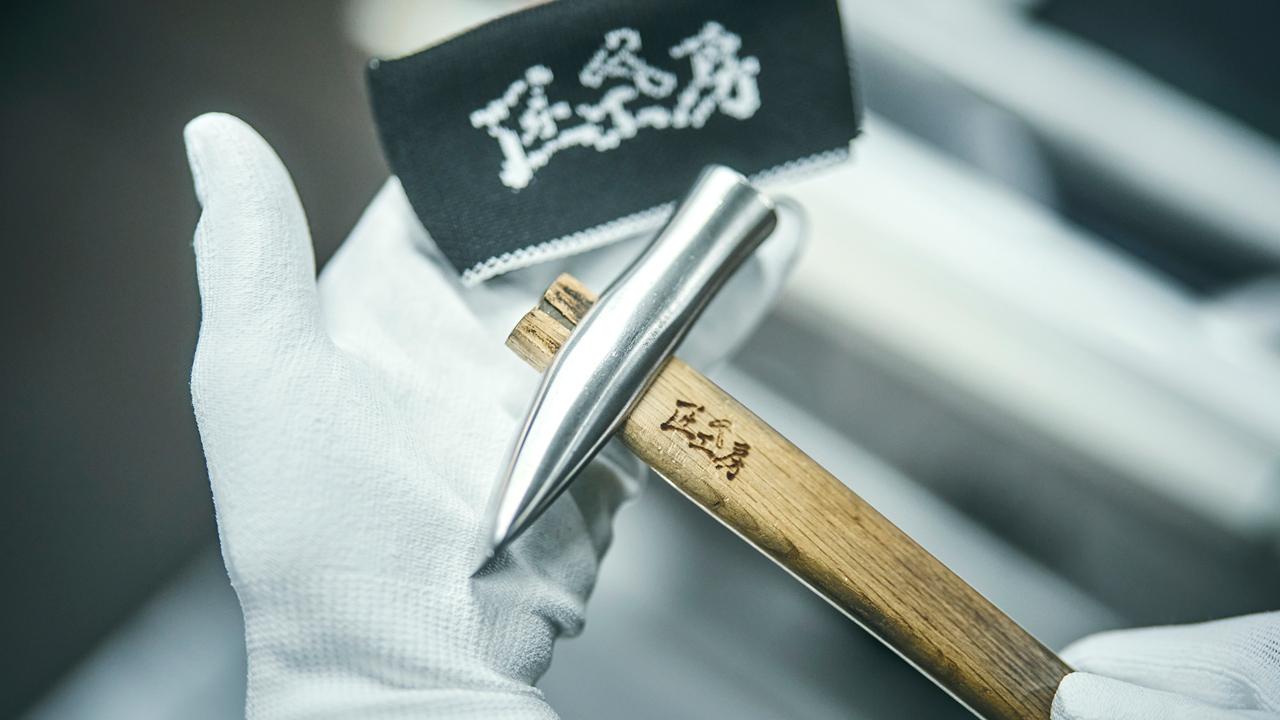
An ongoing series showcasing the master artisans who sustain the automotive industry.
This special installment shines the spotlight on the Takumi Kobo, which harnesses the sheet metal craftsmanship and monozukuri spirit passed down since Toyota's founding.
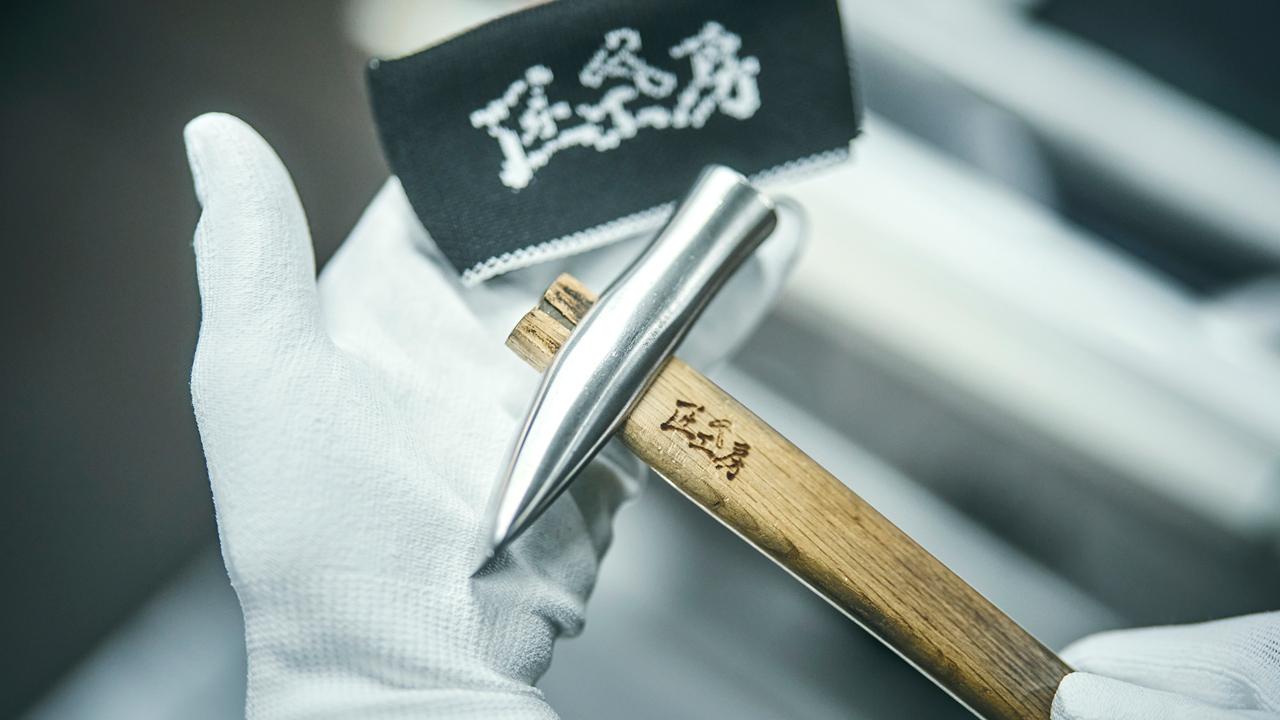
Handwork still plays an important role in today’s car manufacturing, even as technology like AI and 3D printing offer more advanced methods.
This series features the craftsmanship of Japanese monozukuri (manufacturing) through interviews with Toyota’s carmaking masters.
This special installment shines the spotlight on the Takumi Kobo, which seeks to create fascinating cars and accessories by harnessing the sheet metal craftsmanship and monozukuri spirit passed down through generations since Toyota’s founding.
In part one, two key figures who helped launch the Takumi Kobo share the backstory and significance of its founding.
In the spirit of a traditional craftsperson’s workshop
In a building on the grounds of Toyota’s head office, a roughly 60 square meters space has been partitioned off with wood-paneled walls.
Hanging neatly on these walls are various sizes of hammers and wooden mallets. Racks and display cases house a diverse array of decorative metal objects, from miniature cars to bonsai, flowers, fruits, origami cranes, samurai helmets, and baseball gloves. What looks at first like a studio for traditional crafts is actually the Takumi Kobo workshop.
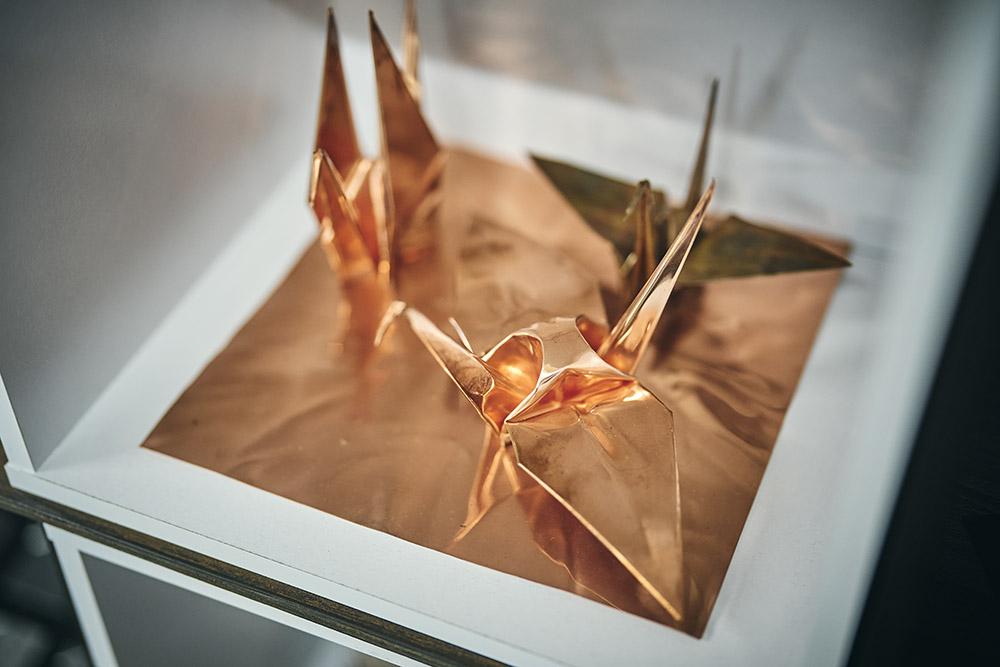


The new Century, unveiled in September 2023, features an optional takumi scuff plate named the Masame.
Masame refers to the wood grain pattern found near the center of cedar and cypress logs, among others, when they are cut vertically. The Century’s scuff plate design imitates these neat, straight grains.
This scuff plate was turned into a product by the Technical Development & Prototype Division’s Takumi Kobo, who partnered with like-minded colleagues inside and outside the company. Takumi Kobo craftspeople create each unique scuff plate by hammering the design onto stainless steel plates, line by line.

The Technical Development & Prototype Division handles everything from developing the latest manufacturing methods and digital technologies to producing vehicle prototypes. This unit shapes Toyota’s monozukuri future through both cutting-edge technologies and skilled craftsmanship.
Within this division, the Takumi Kobo was created in April 2022. Members consist of sheet metal takumi (artisans) from the division’s Prototype Body Production Section, along with technicians responsible for devising and arranging new projects in collaboration with relevant units inside and outside Toyota. Together, they turn takumi skills into vehicles and products.
Toyota’s uniquely human-centered approach to monozukuri
“Sheet metal working is a vital skill in Toyota’s carmaking, having undergone continuous inheritance and evolution since the company's founding,” tells Yuto Tanaka, Project Manager at the Technical Development & Prototype Division’s Strategy and Planning Group. As a technician, he was one of the key figures behind the Takumi Kobo’s creation.

Building prototype vehicles is an essential part of car development, and the task of fabricating prototype bodies falls to craftspeople with outstanding sheet metal skills.
Generally, body parts for production cars are mass-produced using vast press machines. To make a small batch of prototypes, however, craftspeople hammer metal sheets into the desired shapes by hand, relying on their skills to create elaborate forms.
Ever since sheet metal craftspeople produced the body for Toyota’s first prototype car, the Model A1, in 1935, these skills have been passed down through successive takumi generations.
“In recent years, advances in stamping technology have spurred a shift from working sheet metal by hand to more efficient press forming, even for prototype bodies,” says Hitoshi Tsuchiya of the Prototype Body Production Section. “This is changing what is required of sheet metal technicians on the front lines of manufacturing.”

Tsuchiya, who worked with Tanaka to establish the Takumi Kobo, joined Toyota in 1997 after graduating from its Technical Skills Academy. Since those youthful days, he has displayed the full potential of his brilliant sheet metal talents, winning in the Autobody Repair category at both national and international WorldSkills competitions.
“No matter how far press technologies advance and enable more efficient carmaking, sheet metal skills cannot be allowed to die out if we want to create innovative shapes and varied cars to satisfy increasingly diverse customer needs.”
Both Tanaka and Tsuchiya share this sentiment.
Tanaka
Sheet metal craftspeople like Tsuchiya can achieve forms beyond the capabilities of today’s press machines. Steel sheets and other body materials are elongated during forming. As stamping applies force from a fixed direction, when making complex 3D shapes the material can be extended to the point of cracking in certain areas.
On the other hand, a sheet metal craftsperson working by hand can expand the piece uniformly, creating forms that push right to the limits of the material's elongation. This is because, as they work, they consider the direction and way of striking the metal such that it doesn’t crack or distort.
In other words, utilizing the skills of artisans like Tsuchiya allows us to freely create body shapes that are more three-dimensional and more deeply sculpted.
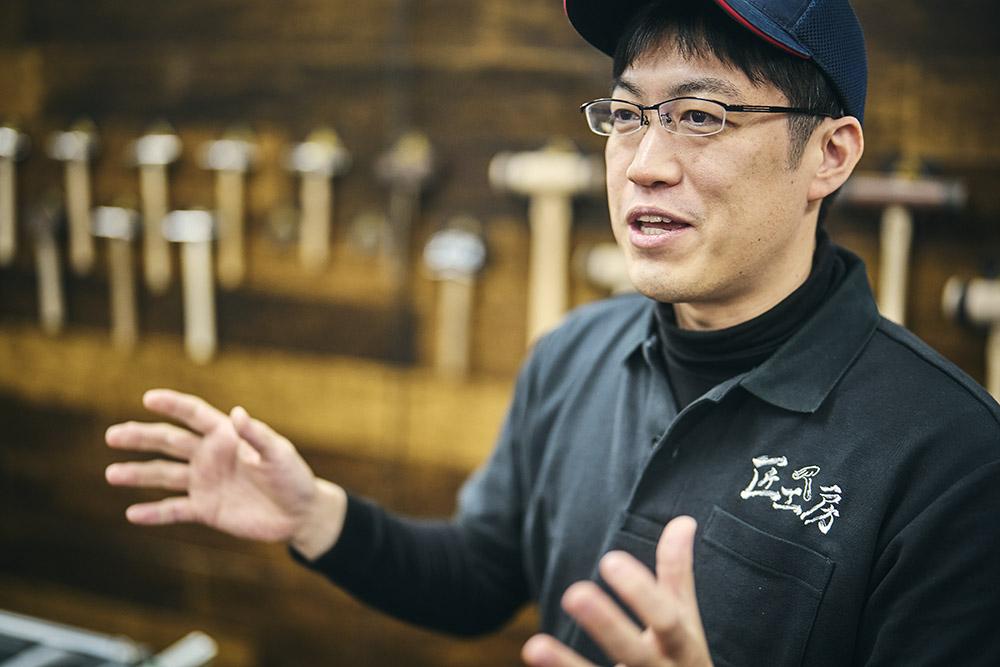
I believe that incorporating takumi skills, along with their expertise and sensibilities, into computer simulations and machine processing leads to better carmaking.
If this helps the machines advance, then next, it’s up to the takumi to hone their skills further so they surpass them. Toyota places great value in passing on skills and nurturing craftspeople through this cycle, ensuring our products continue to evolve.
Tsuchiya
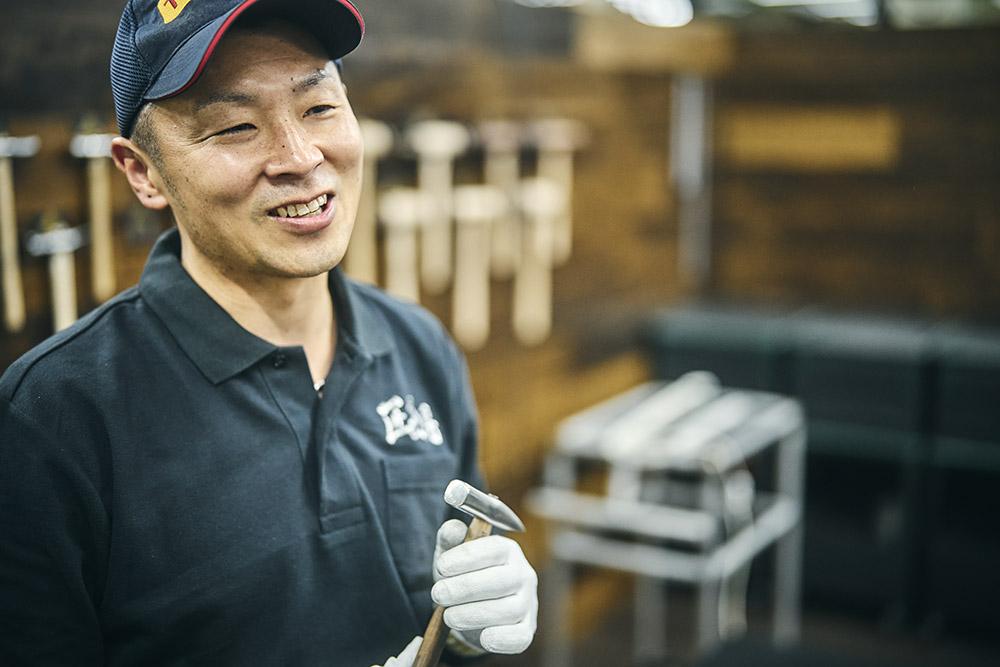
This is how I interpret the idea of “human-centered monozukuri,” which Oyaji Kawai (Executive Fellow Mitsuru Kawai) always emphasizes. If monozukuri keeps evolving, I believe the value of takumi skills will never become outdated, as people across different generations feel the allure to carry them forward.
As members of the Prototype Body Production Section, we are working hard to pass on these skills in the hope of contributing, at least in some small part, to Toyota’s unique approach to carmaking.
Craftsmanship creates new value
The Prototype Body Production Section strives to bring the underlying skills behind sheet metal craftsmanship into the future through various initiatives, such as building trophies for the company relay race and making bodies for event cars exhibited at toy shows.
In fact, the various metal pieces on display at the Takumi Kobo workshop were crafted by the artisans under their own initiative as a way to hone and preserve their skills.
Tanaka
These objects gave me a true appreciation for the metalworking skills of Tsuchiya and his colleagues. In particular, I remember the first time I held an apple that, aside from the stem, had been crafted from a single sheet. The way the craftsperson had achieved a uniquely handmade warmth in the item’s appearance and texture by finely balancing surface unevenness with the metal’s luster left a deep impression on me.
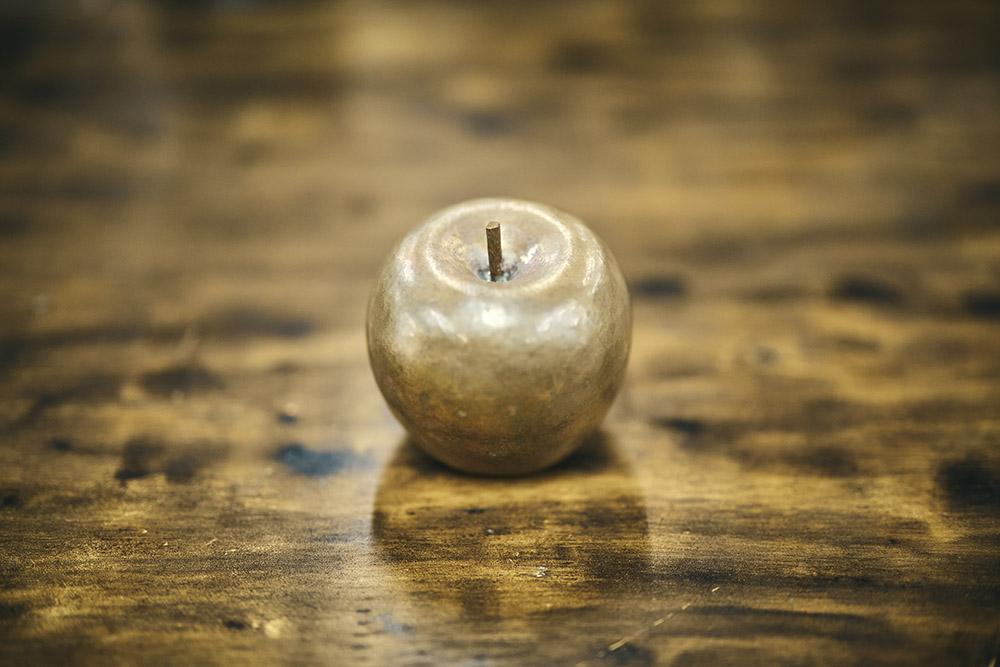
At university, Tanaka studied the cutting-edge field of applied laser physics through to the graduate level.
Since joining Toyota in 2012, he has always worked with the latest tech, first in developing advanced technologies using Computer Aided Engineering (CAE) at the Production Engineering Development Division, and later being seconded to a German 3D printing venture.
Having grown up watching his father run a small-scale factory business, Tanaka says that since his student days, he has aspired to contribute to Japanese manufacturing.
Tanaka and Tsuchiya met in January 2021 when Tanaka’s Monozukuri Technology Development Division merged with the Prototyping Division, where Tsuchiya and his colleagues worked, forming the new Technical Development & Prototype Division.
Tanaka
Today, as carmaking and customer values change with the times, the approach to developing personnel and the skills required are also changing accordingly. Rather than lose these wonderful takumi skills, however, we wanted to see if we could carry them forward and evolve them in a way that boosts the value of Toyota’s brand and the products we offer customers. That’s why we proposed setting up the Takumi Kobo.
Tsuchiya
As I’ve mentioned, in the carmaking genba, there are fewer and fewer opportunities to form pieces by hand. Meanwhile, with a growing number of highly skilled veterans retiring from the company, I felt it was time for me to take on a new challenge.
As covered in our Toyota Times series, Tsuchiya’s Prototype Body Production Section members were also in charge of body fabrication for the Toyopet Racer restoration project.
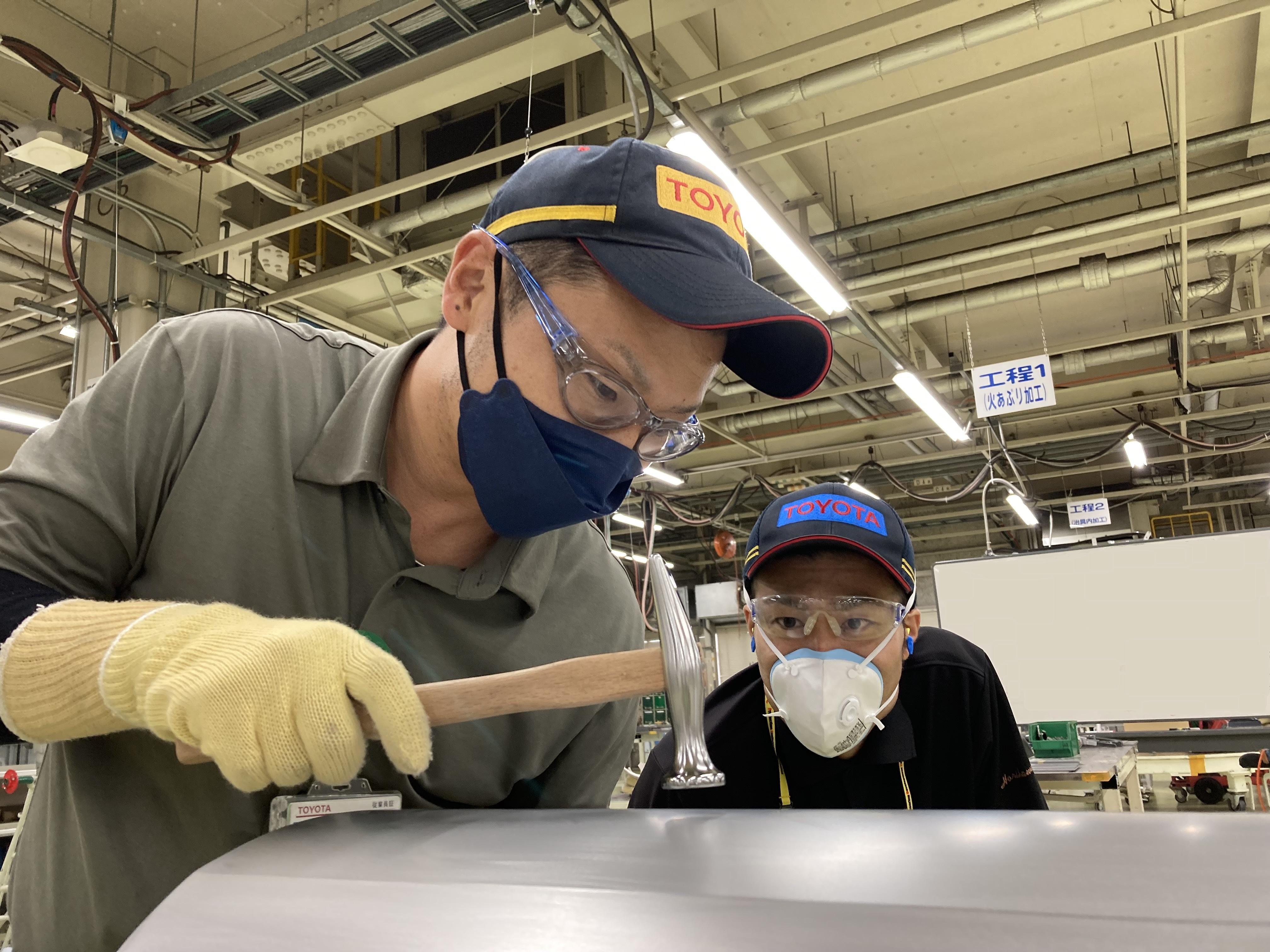
Amid worries about passing on his skills, Tsuchiya says that joining the project offered a chance to take a new step forward.
Oyaji Kawai leaves his mark on the Takumi Kobo name
Together with their superiors at the time and the team’s current members, Tanaka and Tsuchiya held extensive discussions about the Takumi Kobo’s role. By doing so, they came up with these three focal areas for their activities:
1)Inheritance and evolution of takumi skills
2)Providing new value to customers by striving to develop products that harness takumi skills, in the process nurturing personnel capable of creating such products
3)Creating user experiences and other customer touchpoints that help them appreciate the appeal and fun of monozukuri
Tanaka
Toyota’s carmaking is partly driven by the desire to align with the values and needs of our customers, offering products that can make every one of them happy even in an increasingly diverse world.
In line with this mindset, we wanted to offer customers unique value through monozukuri that replaces conventional mass production with the skills honed by takumi artisans.
For this type of monozukuri to work we must find people, both inside Toyota and beyond, to collaborate with us in creating products. In that sense, we wanted to use Takumi Kobo as a platform for building connections.
At the same time, by creating customer touchpoints, we hope to receive direct feedback and offer monozukuri experiences that will bring makers and customers together in the process of developing products.
Tanaka and his team began by creating customer touchpoints, which meant taking part in circuit driving events for Lexus owners and organizing hands-on metalworking sessions at housing exhibitions, with assistance from group company Toyota Smile Life.
They also set about exploring product ideas, including a prototype scuff plate that utilized sheet metal skills, which was displayed at the Gunma Parts Show in September 2021. The excellent response from visitors revealed the potential of such takumi-crafted products.

These humble efforts bore fruit, leading to the Takumi Kobo launch in April 2022, and the release of the scuff plate as an optional add-on for the new Century.
Visitors to the workshop we described earlier are greeted by the words “Takumi Kobo” in bold lettering on the wood-paneled wall. While looking at first glance like the work of a distinguished calligrapher, the lettering was, in fact, done by Oyaji Kawai, who happily took up Tsuchiya’s request.

Tsuchiya
As our activities gradually got going, with new product discussions and metalworking sessions for customers, I had a chance to talk with Mitsuru Kawai.
I explained what we were doing and told him that, given Toyota’s many highly skilled people, we wanted to team up to create a new way of working, focused on turning takumi craftsmanship into products.
He endorsed our efforts and wrote the Takumi Kobo logo for us.
Oyaji Kawai is the personification of Toyota’s monozukuri, so his support for our Takumi Kobo activities made us both proud and even more determined.
Having earned Oyaji Kawai’s seal of approval, how did the Takumi Kobo turn the Century scuff plate into a product? Part two of this article traces the team’s journey.