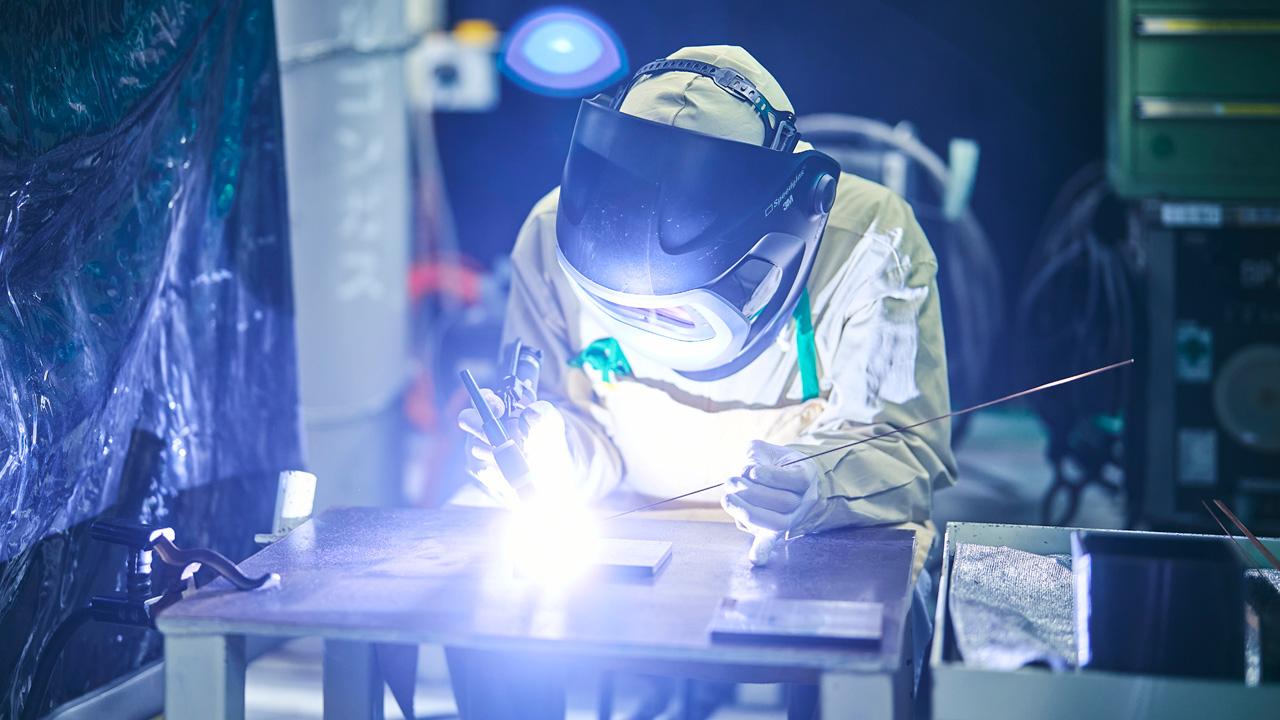
This is an ongoing series looking at the master artisans supporting the automotive industry. The 13th installment two-part article features an interview with a master welder using self-taught skills to join metal plates and aluminum through skillful use of temperatures over 5,000 degrees Celsius.
A Toyota first
In 1986, Miki's ninth year of dealing with the fun and difficulty of welding at Toyota, he was faced with a massive turn of events. His boss, who had finally approved of his skills, asked if he was interested in trying out for the Japan Welding Competition.
This competition is sponsored by the Japan Welding Engineering Society to promote the welding skills so vital to all kinds of manufacturing fields. It started in 1954, and once a year brings welders from all over Japan to test their skills in direct competition.
Toyota had participated in the Japan Welding Competition, but had never managed to finish in the top three of the national competition (their highest finish was 4 th ). Miki was selected as one of four representatives to enter the Aichi prefectural round out of 30 engineers gathered within the company, but finished 6 th in the competition.
Miki
Only those placing first at the local prefectural rounds can go on to the nationals, so I couldn't go. The frustration drove me to try again the next year so I could make the finals.
At the time, the head office had an academy with a training center. When I took fourth in a little competition between the company's top guns, I spent one or two months practicing every night after work. Then, I took first at the Aichi Prefecture competition and went on to the nationals.
In his second attempt at the Welding Competition, Miki took first at the Aichi prefectural round, and then he went on to take third at the nationals. That was the first time anyone from Toyota placed so high, an event worth remembering.
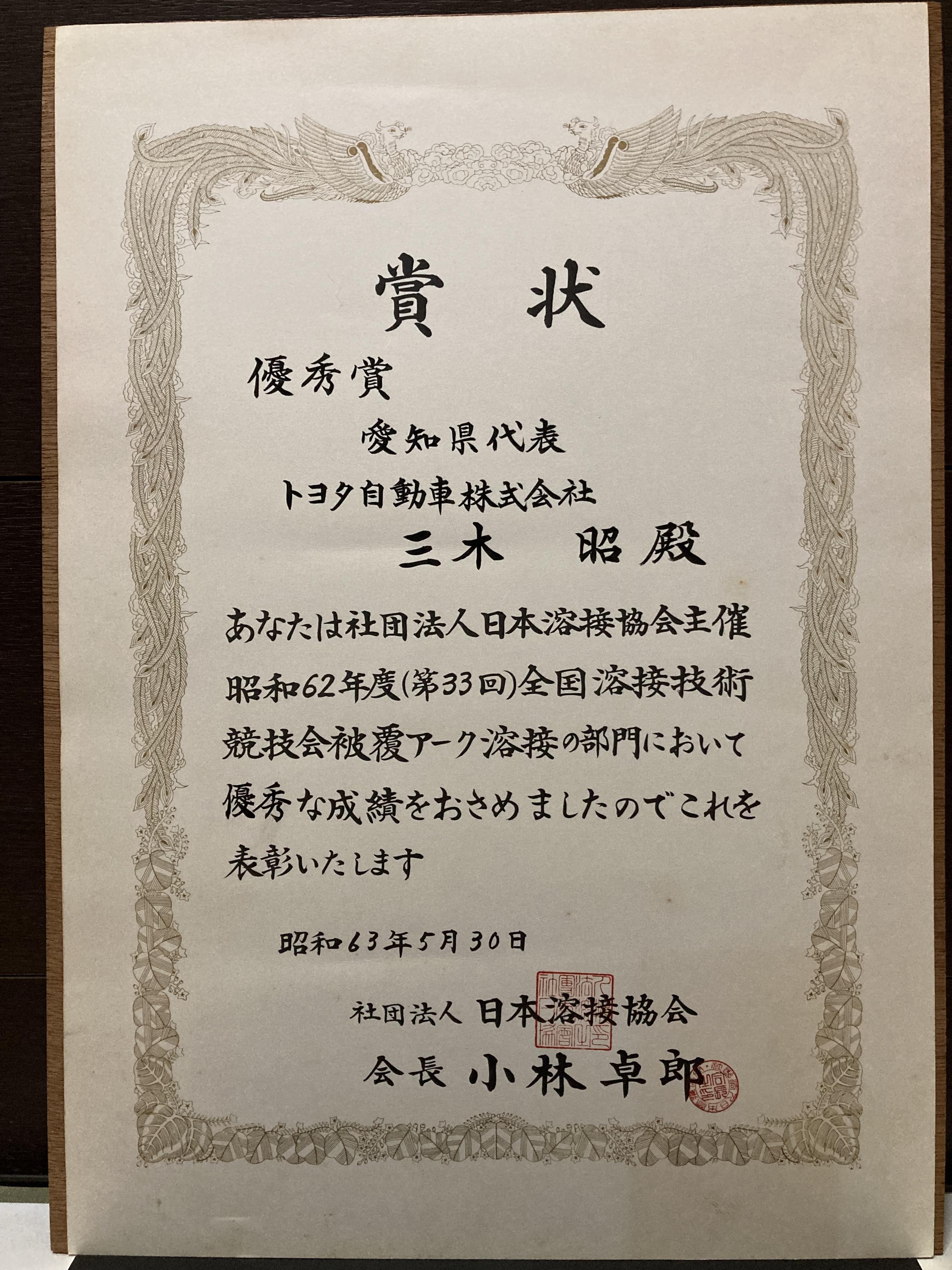
Since 1988, Miki has taught welding at the Toyota Technical Skills Training School, helping younger employees hoping to try for the Welding Competition, while continuing to brush up his own skills. He is known company-wide as a master welder.
Buildup welding on cast metal molds: the peak of welding difficulty?
The skill of welding is used in all kinds of elements of carmaking. One in which Miki is particularly skilled and for which he has become the go-to technician, is buildup welding on press molds. These massive dies, which can be several meters long and weigh over tens of metric tonnes, are used in pressing body panels.
We introduced these press molds and how they are used in part 5 of this series, "#5 Yasunobu Wada, a master of press molding."
Press molds for body panels require precision at the micron, or 1/1000mm, level. Master press molders try out their presses on sheet metal over and over to identify tiny issues with the molds using their eyes and fingertips, then adjusting them using cutting tools, files, and grindstones.
But adjusting those surfaces is not only a matter of shaving them down, at times the opposite work is needed. For that, someone must fill in surface depressions using buildup welding.
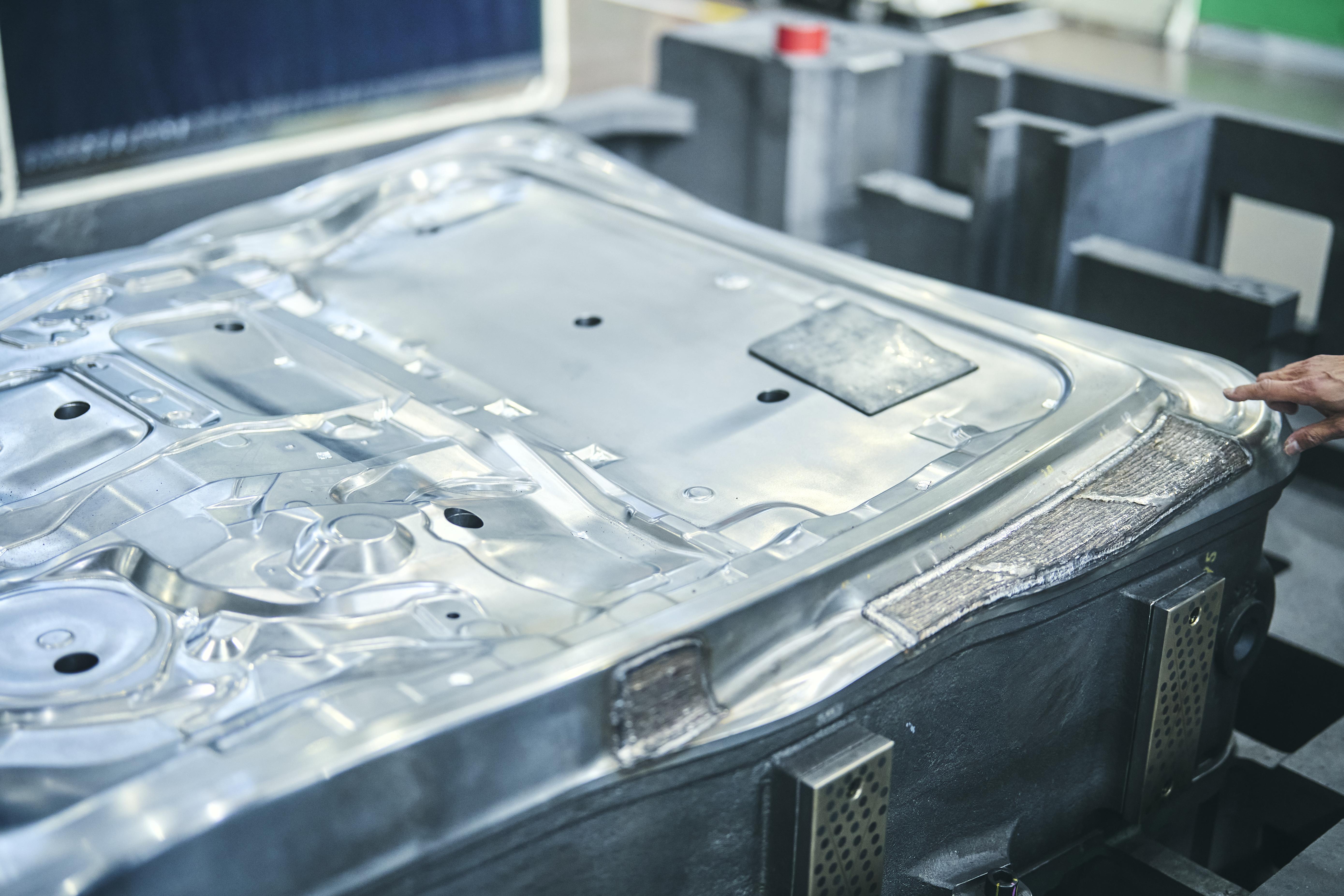
Miki
Welding on cast iron, which has much more surface variation than other metal types, is difficult.
And in these massive presses the molds are under enormous pressure, so you have to add welding material the same hardness as the mold, otherwise the buildup weld will collapse and ruin the panel.
And if you build it up too much, you'll make the press mold finishing process that much more difficult. A less skilled welder will end up with too much buildup and a big lump there.
The key is building up thinly, adding only the bare minimum. Thinking about the precision needed in finishing, the tolerance for buildup should be at the 0.1 mm level. And if you don't completely integrate it with the surrounding mold, it's no good.
I suppose since buildup welding ends up shaved down during finishing, it's basically all back-stage work. But it's worth it if there are people at the carmaking genba who understand just how tough it is.
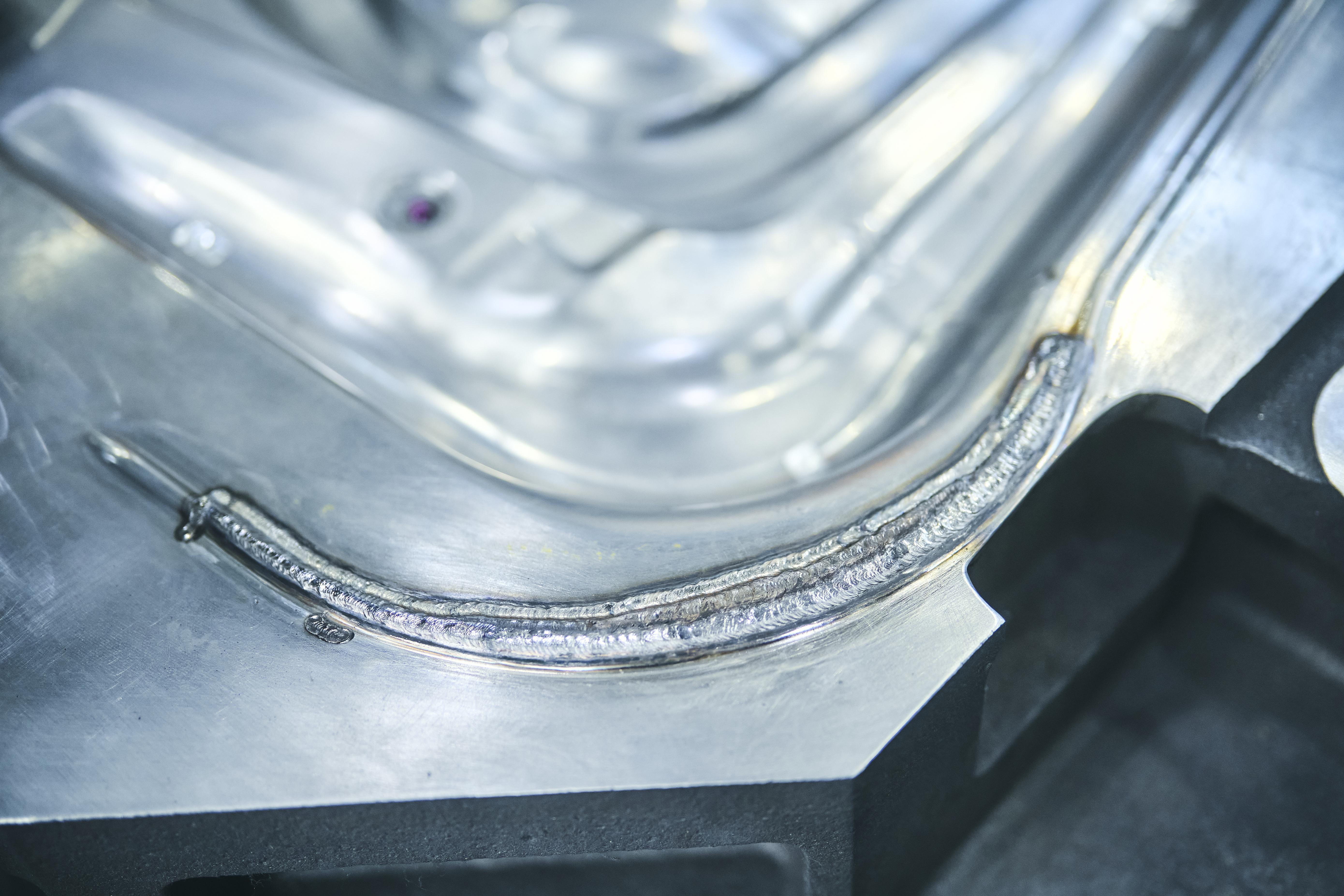
In part 2 of this article, we'll look at the training Miki is offering now, high-difficulty aluminum welding, and share more of the appeals of welding through the eyes of master welder Miki.
Written by Yasuhito Shibuya. Photos by Ken Takayanagi