
This two-part article features Teppei Hayashi, a master of cutting tools that play an indispensable role in car manufacturing.

Handwork still plays an important role in today’s car manufacturing, even as technology like 3D printing offers more advanced methods. This series features craftsmanship of Japanese monozukuri (making things) through interviews with Toyota’s car-making masters.
This article features a master of cutting tool maintenance.

#10: Teppei Hayashi, a master of cutting tools that play an indispensable role in machining
Group Leader, Powertrain Manufacturing Fundamental Engineering Div., Toyota Motor Corporation
Cutting tools play an important role in car manufacturing
There’s an old Japanese saying that goes, “You can tell the skill of craftspeople by looking at their tools.” This indicates how important tools are in monozukuri, which is why tool maintenance is a fundamental part of hand work. Many of them even make tools themselves.
The cutting tools used in car-making equipment differ in scale from those used in handwork. As cars are masses of metalworking, individual parts are cast or forged into a rough shape and then processed through enormous machining equipment with cutting tools.

The precision of any individual cutting tool used in the equipment determines the precision of the parts being produced, which affects the basic car functions of running, turning, and stopping.
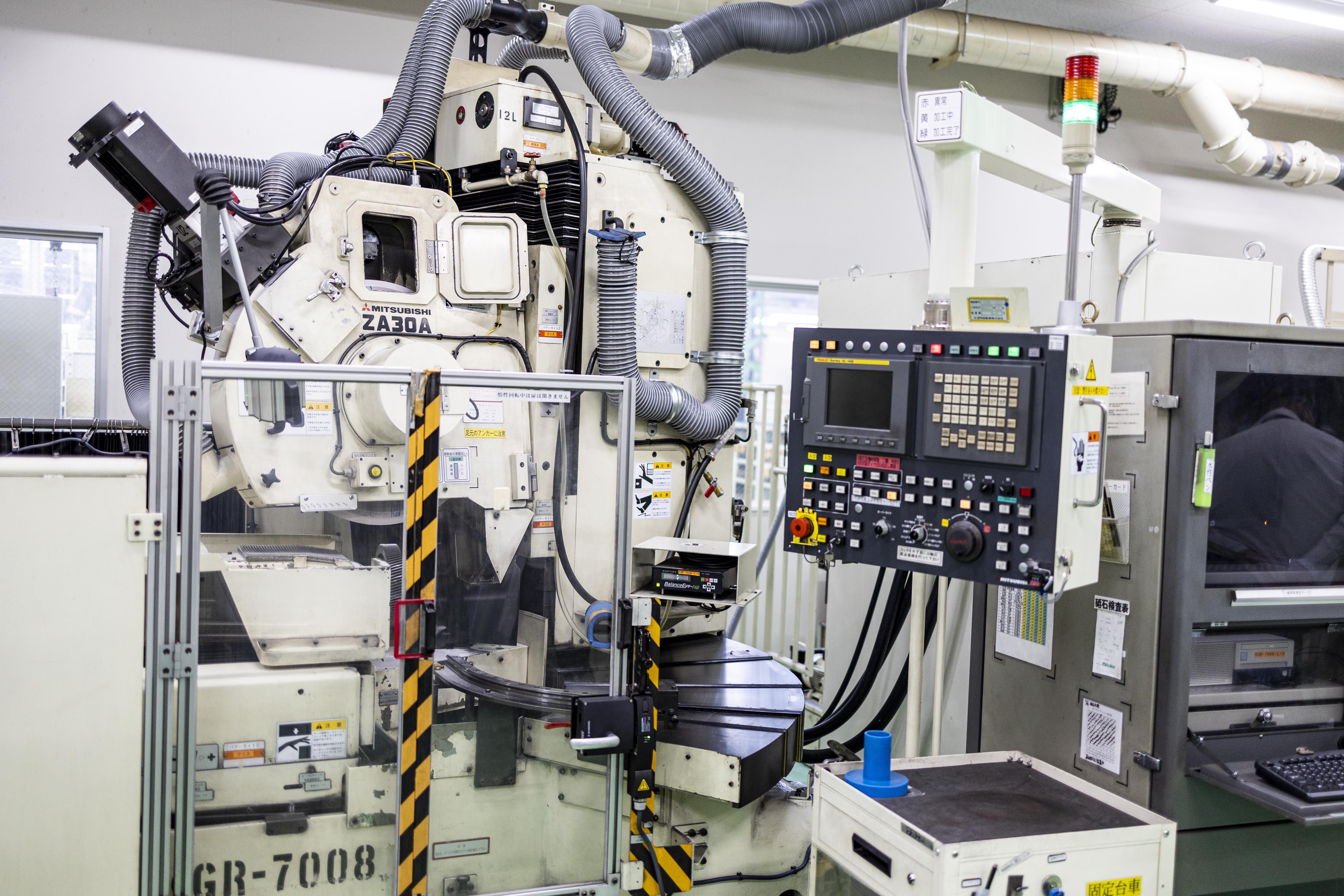
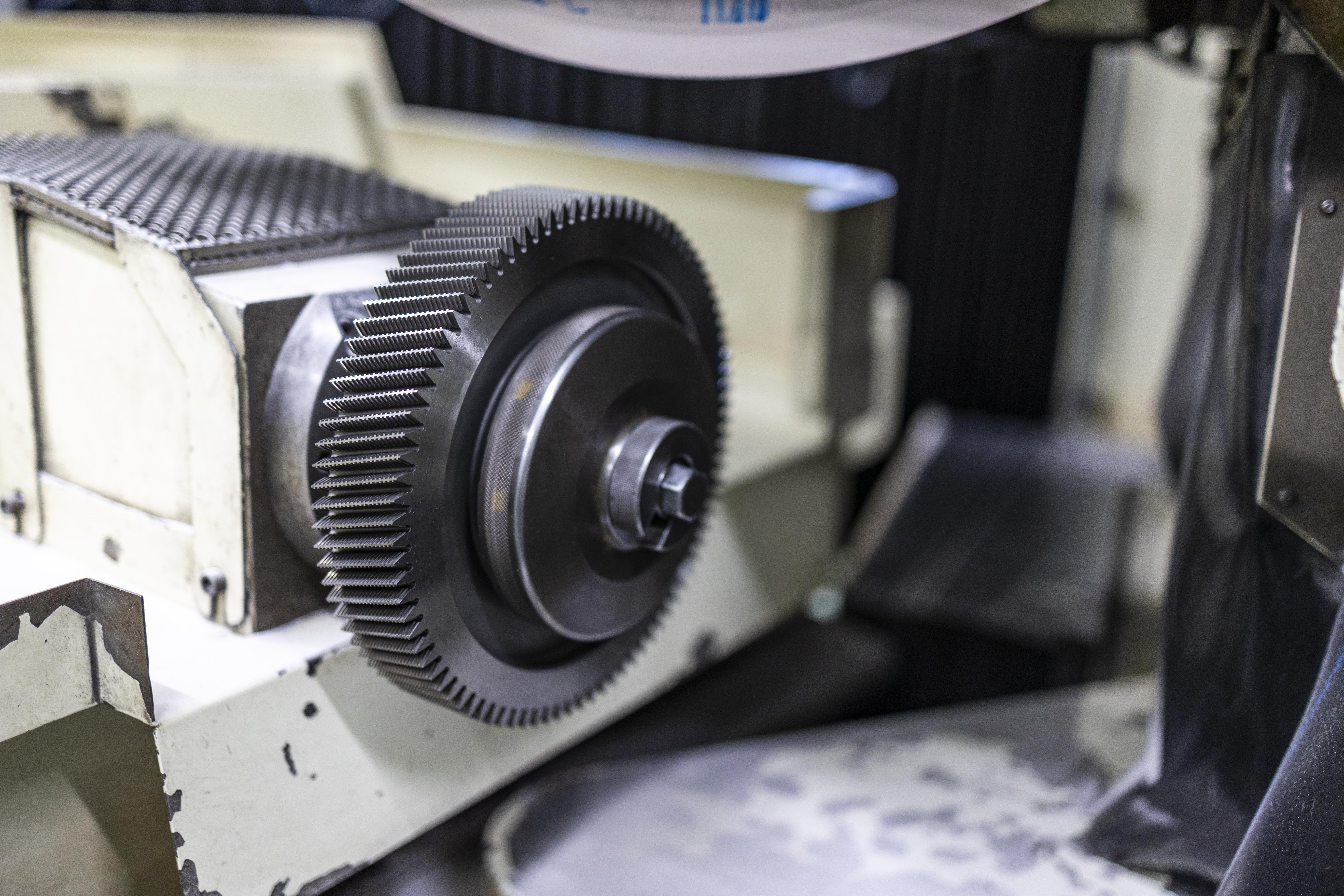
No matter how tough or durable any individual cutting tool might be, using it will lead to wear and functional deterioration. That is why sharpening and grinding maintenance is essential for cutting tools. Generally, the operator in charge of any given piece of machining equipment handles cutting tool maintenance. The skill and speed of this work differ greatly depending on how experienced the operator is, and the differences can affect the production quality and efficiency.
That is why Toyota has a department specialized in sharpening and grinding processes. It is a place for machining and cutting tool specialists who know well how to maximize performance, extend life, and properly manage the equipment and cutting tools. Teppei Hayashi in Powertrain Manufacturing Fundamental Division is one of those specialists.
Brainchild of Taiichi Ohno, an original TPS organizer

This tool-maintenance specialist department has its roots in the Tool Regrind Section established in 1951. Taiichi Ono, known for his leading role in forming the Toyota Production System (TPS), proposed starting this group to improve production efficiency and eliminate waste.
Putting cutting tool maintenance and management in one place helps minimize the loss and waste of expensive tools and enables sharing of knowledge across divisions. Above all, it helps reduce the burden on those in charge of the work floor. The larger the production scale, the greater the benefit this offers. It is an essential department supporting TPS on the car-making genba (frontlines).
Currently, Toyota’s eight plants in Japan have this department respectively, including Hayashi’s office at the Honsha plant. Each location has 15 to 20 staff members, for a total of about 200 people working alternating day and night shifts. And this staff maintains some 2.3 million cutting tools a year.
In addition, 15 Toyota plants outside of Japan have a similar group, where approximately 400 members perform maintenance on around 5 million cutting tools annually.
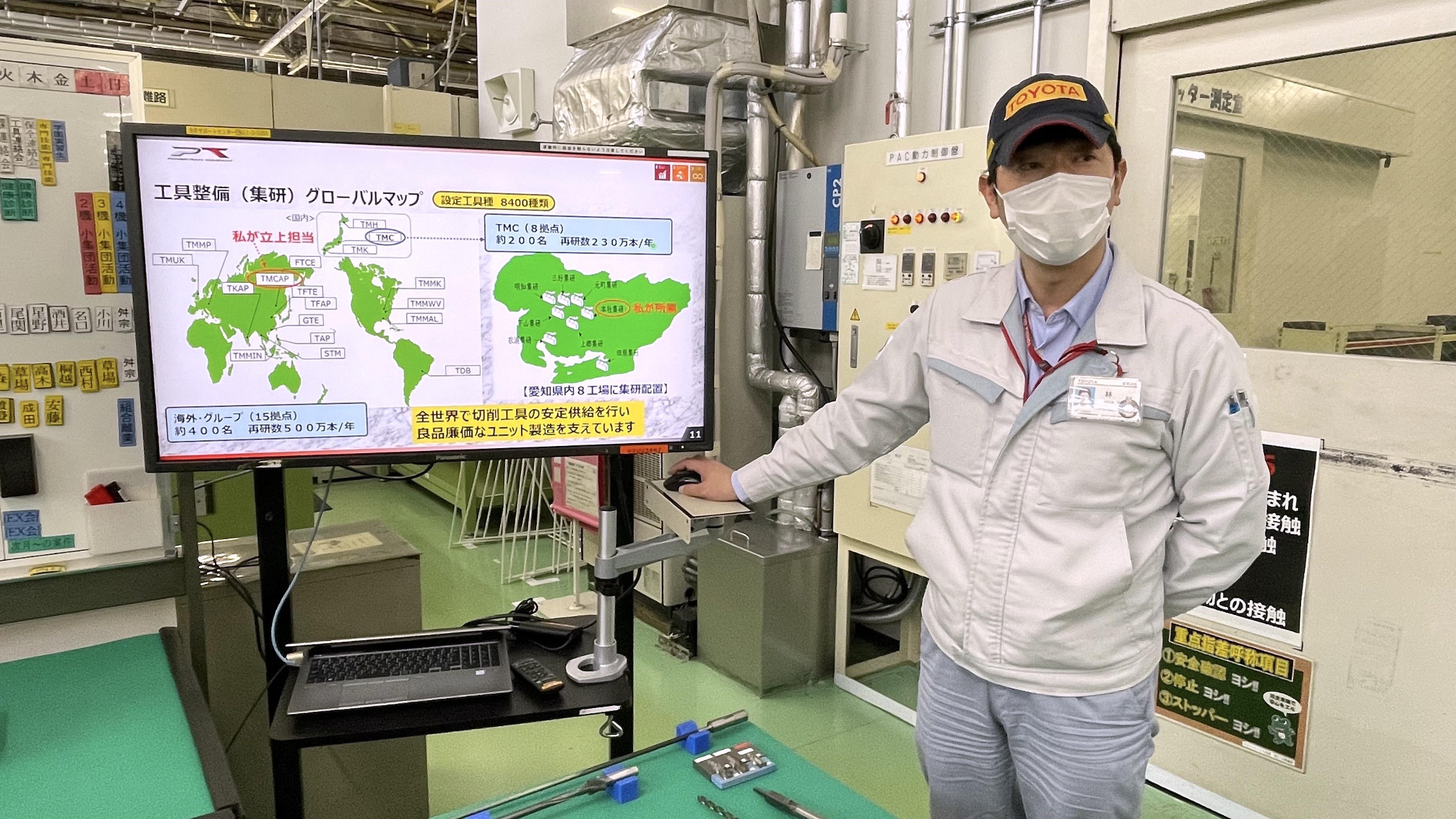
Childhood dream of making cars
Hayashi was born in 1973 in the city of Kitakyushu, Fukuoka Prefecture. After graduating from high school, he attended a one-year professional course at Toyota Technical Skills Academy and started working at Toyota in 1993. He joined the Production Engineering Division No. 1 and was placed in the Miyoshi Plant. Ever since, he has dedicated himself to tool maintenance work.
“I liked vehicles when I was a child and enjoyed taking my bike apart and putting it back together or building radio-controlled cars. I especially loved cars, and I wanted to work for a car company in the future. I even wrote that I wanted to become a car maker in my elementary school graduation book.”
There is an automobile factory in Hayashi’s home prefecture of Fukuoka, but he chose the professional course at Toyota’s academy in Aichi Prefecture. It was partly because his father was a true fan of Toyota cars like the Carina and Corolla, and also because he wanted to move away from his hometown and learn something different. During pre-placement training at the Academy, he had experience in tool-maintenance work.
Honing sharpening skills
When he joined Toyota, the maintenance work was much busier than it is today because the lifespan of cutting tools was much shorter and machining equipment cutting tools were not integrated and consolidated.
“We’d sharpen cutting tools and send them off to the genba, and they’d wear out and come right back. And back then, a single piece of equipment would have multiple cutting tools attached, so there were a number of tools, leading to a heavy workload. There wasn’t much time to rest. We were always up and moving.”
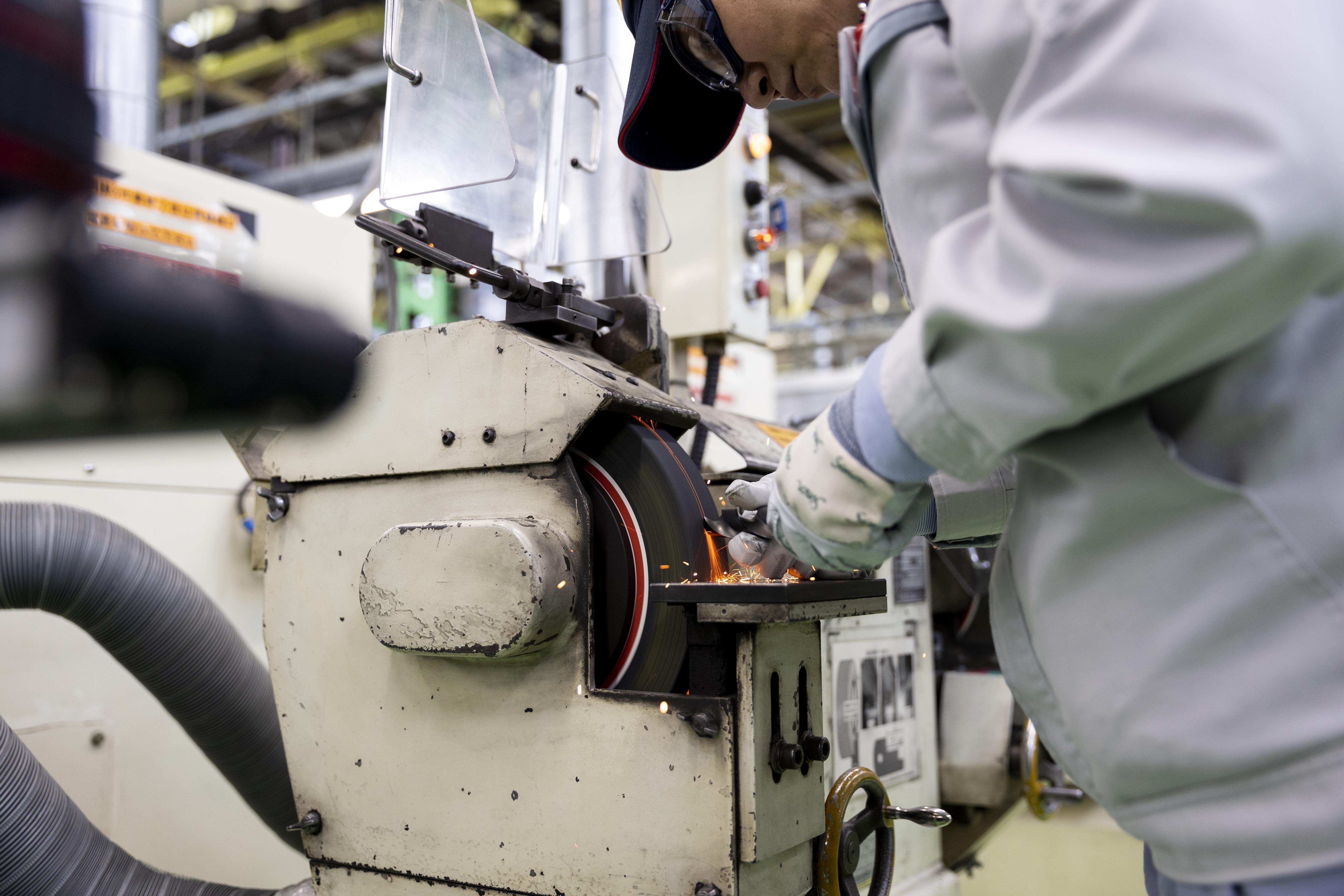
Hayashi’s group currently handles around 8,400 different kinds of cutting tools. In the past, with less automated machinery, the number was much higher, and most required maintenance by hand. Much of the work depended on the workers’ less definable skills and abilities, including knacks and experience. Senior workers taught new workers basics on how to use equipment but were less eager to share more.
“At the time, skills were something you had to acquire on your own. Now that I think about it, maybe they didn’t teach much of that because they were so busy with their own work. They were just trying hard to finish everything in their areas as quickly as possible.”
Hayashi started out just constantly sharpening lots of simple tools, and he observed his seniors as they worked on more difficult ones to learn those trickier techniques. Some of those senior workers were so skilled that genba operators would put in specific requests, saying they would only use tools sharpened by a given employee.
Improving and developing tools as a leader
In 2000, at the age of 26 and in his eighth year with the company, Hayashi moved from Miyoshi to the Honsha Plant, and he got a license as a vocational training instructor that same year. Then, in 2002, he passed the national licensing board’s Machining Equipment Cutting Tool Sharpening Level 1 exam.

“I was in charge of tools related to the car undercarriage at the Miyoshi Plant. I took responsibility of tools for drivetrain and hybrid system monozukuri at the Honsha Plant. It takes around three years to acquire the basic skills for tool maintenance work and about seven years for more advanced skill levels. At the time, I was still learning a lot.”
From around 2006, at the age of 32, Hayashi approached a new task, working on ways to reduce costs and improve cutting tools. He also got involved in prototype development, motorsports work, and maintaining tools needed for future car manufacturing.
“We can improve machining efficiency and edge durability by refining cutting edge shape and applying different coatings to their surface. Even prototype tools can offer a drastic improvement to work efficiency.”
They work on tool improvements themselves and together with tool manufacturers.

Responsible for more than maintenance
Hayashi’s group is also responsible for cutting tool management. Centralized management can help reduce waste, and they use the Kanban System from TPS for this.


“Cutting tools are expensive and keeping track of their location can help reduce waste. It’s important to determine the limits of use since resharpening becomes less effective at some point. Machining stoppage would lead to enormous losses, so we need to order a new one when that limit approaches.
Hayashi says that visiting the production floor and frequent communication is essential for proper management. If a cutting tool causes problems in a piece of machining equipment, he contemplates solutions in cooperation with the genba manager and tool manufacturers.
Another duty of his group is to establish overseas tool-maintenance facilities. Hayashi was responsible for setting up the center at the Toyota Motor (Changshu) Auto Parts Co., Ltd in China, which opened in July 2014.
He recalls, “It was challenging to start a center from scratch in terms of people, goods, and systems, and it was a valuable experience that I could not have had in Japan.”
The second part features Hayashi’s efforts and challenges in passing on the defining skills to the future generation.
(Text: Yasuhito Shibuya, Photo: Yuqi Zhang)