
This two-part article features Teppei Hayashi, a master of cutting tools that play an indispensable role in car manufacturing.

After introducing Teppei Hayashi and his work in part 1, this article features his important work as a master with defining skills.
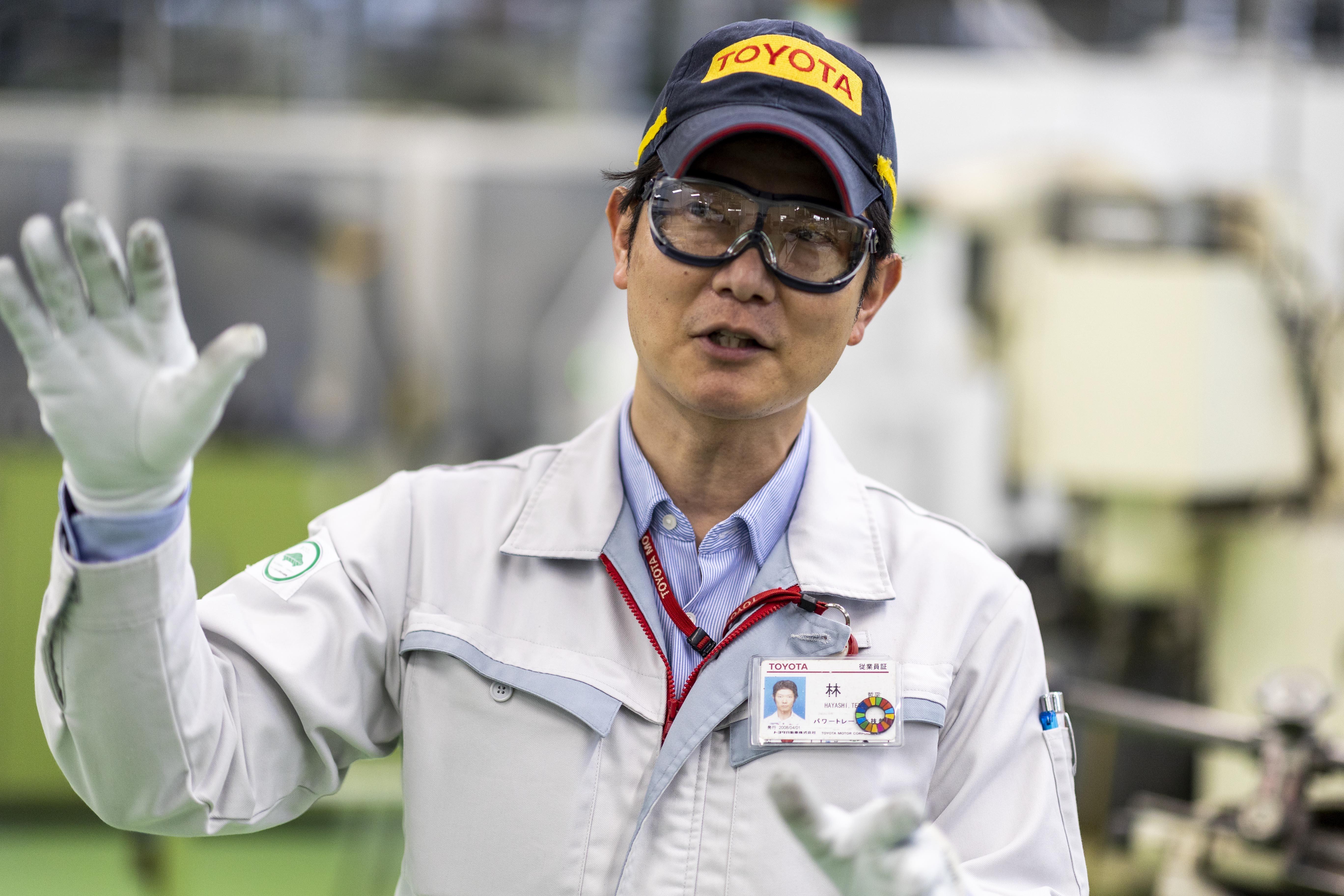
#10: Teppei Hayashi, a master of cutting tools that play an indispensable role in machining
Group Leader, Powertrain Manufacturing Fundamental Engineering Div., Toyota Motor Corporation
Taking cutting tool sharpening skills into the future
Teppei Hayashi works on maintaining, managing, improving, and developing cutting tools used in car manufacturing, particularly in powertrain production.
He has another significant duty for Toyota’s future car making: to pass down the skills, intuition, and knack of making and maintaining cutting tools to future generations.
At present, manual machining equipment, which uses sharpened tools set into hand-driven machinery, is almost unseen at the genba except for prototype production. Since the introduction in the 1990s of automated numerically controlled (NC) machine tools, those large pieces of equipment have played a leading role in machining at production sites.
That means that not only has hand-machined metal disappeared from production floors, but so has manual sharpening work and maintenance. If nothing is done, this will result in losing the basic sharpening techniques, intuition, and experience that the tool maintenance group has built on for decades.
Intuition and knack still essential for sharpening
The Honsha Plant tool-maintenance center is the only one among all seven that has facilities for learning how to use manual machine cutting tools, as well as helping acquire the innate skills and knowledge for their maintenance.
Members can grasp basic principles and learn the various uses of different cutting tools, how to create cutting edges by hand, and maintenance methods. Employees with less experience receive training opportunities, such as how to make and maintain drills.

“It’s easy when machining goes smoothly on the production floor, but when a problem occurs with an automated machine, you need to solve the problem. To determine the root cause, you have to truly grasp the principles of what’s happening inside the equipment. Otherwise, you can’t solve anything.”
It is important to understand what is happening with the material and cutting tools inside the machine, why, and how an improvement could be made. Hayashi says that requires a thorough knowledge of features and characteristics of the basic cutting tools, the skills to maintain them by hand, and sensitivity granted by innate intuition and knack.
“There is always a possibility of automatic equipment breaking down. Even in such a situation, you need to ensure that production goes on using manually sharpened cutting tools, the same as the automatic equipment. That’s why we must pass down all the skills and abilities needed for hand-maintaining cutting tools.”
Hayashi takes care to ensure that young employees have an opportunity to acquire the skills like he did back in the day.
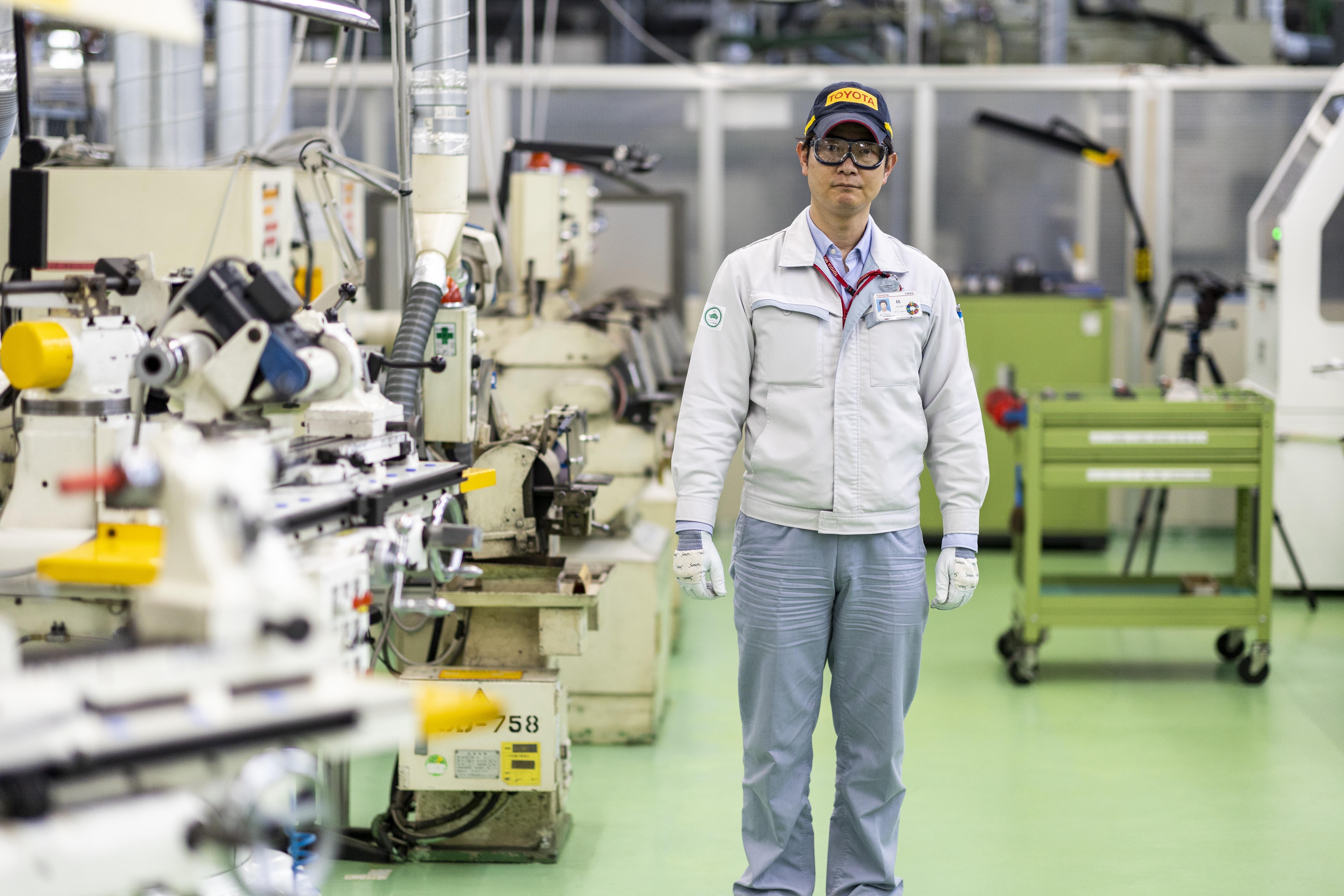
“Looking back on my life, I’ve been lucky. I’ve worked on both manual and automatic equipment and experienced all kinds of cutting tools.”
As primary production equipment has shifted from manual to automatic NC and CNC machining, cutting tool maintenance has also grown more automated.
From the 1950s to the 1980s, as cutting tools were primarily sharpened by hand, the work was guided by the specialist’s sensibilities honed on the job. However, the 1990s brought an increased reliance on NC equipment, and now, plants use micromachining equipment that can precision-grind tools to 1/10,000th of a millimeter.
The skills required for operating manual machines are increasingly less relevant now. However, it is still essential to have people with skills and senses who can use and maintain old manual machines if there ever comes a time when the automated equipment breaks down.
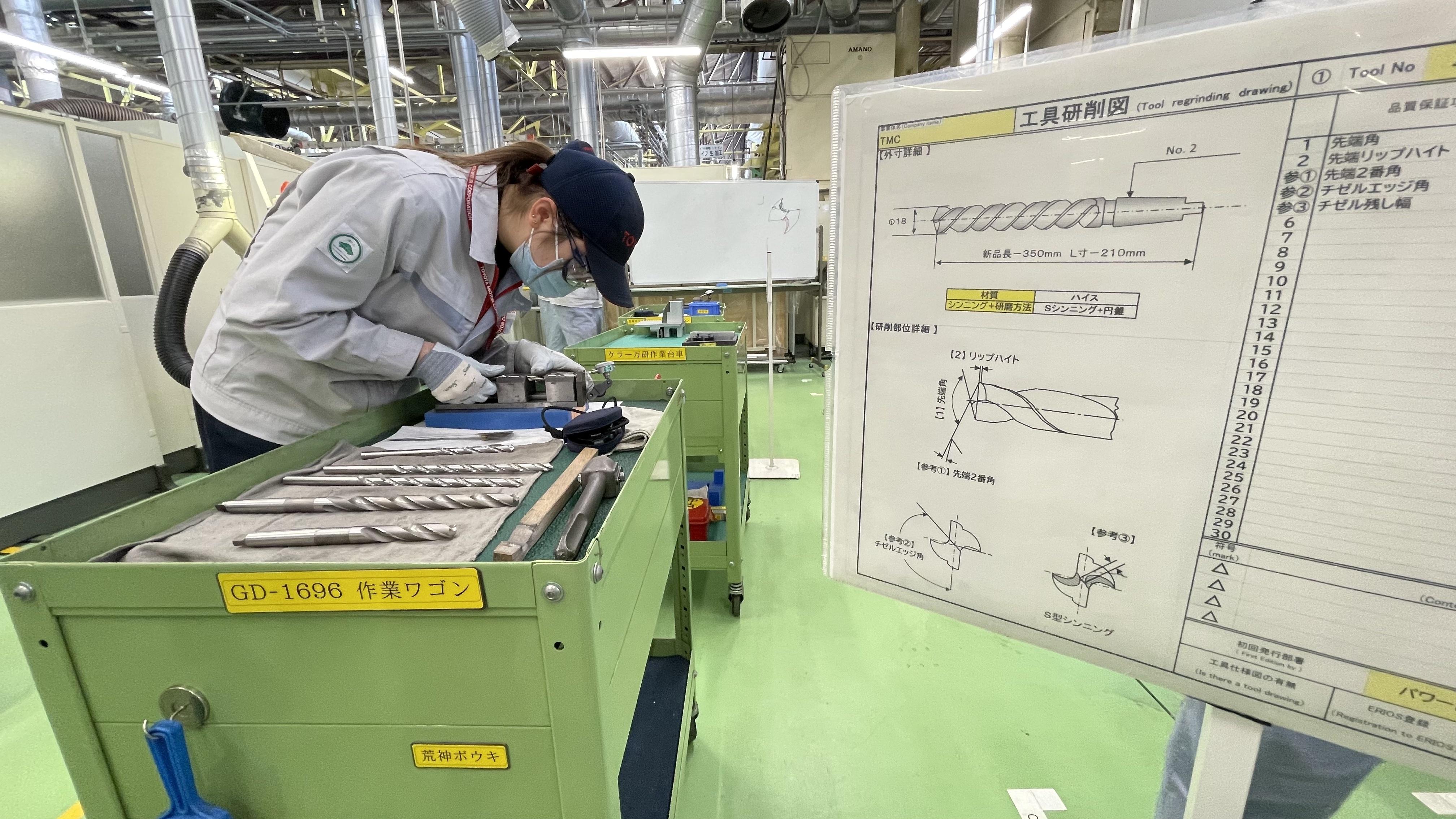
“When I joined the workplace, senior employees told me that all five senses are important in maintaining machining equipment and cutting tools. The appearance, the feedback in your hands, the color of the sparks and the surface when grinding, and the grinder face call all help tell you if the edge is in good condition or not.”
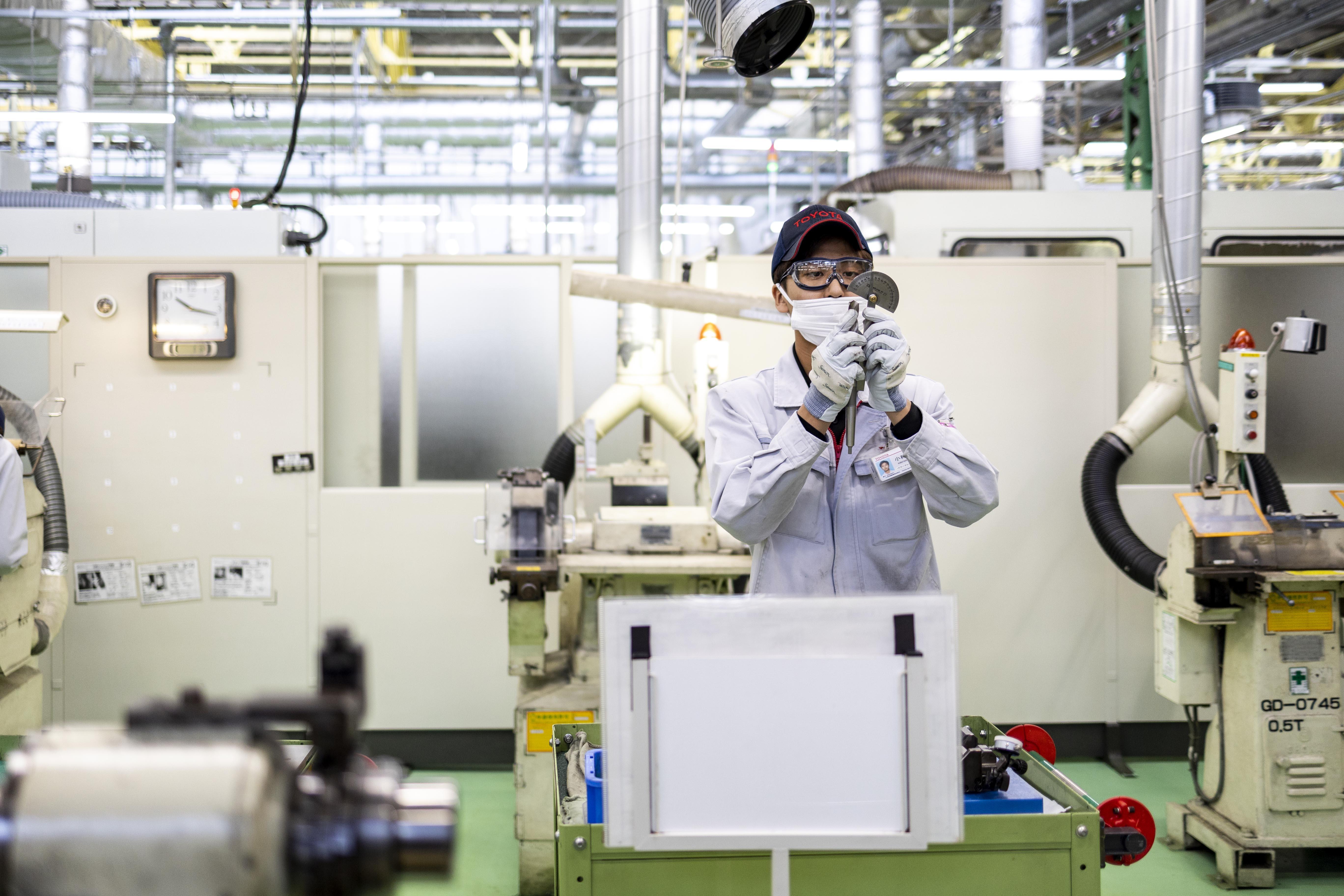
For example, machining metal often generates sparks. Ordinary people cannot judge whether that’s good or bad, but generating sparks causes heat to build up in the raw material, which is undesirable during machining, so it’s best to avoid sparks. Additionally, the raw material’s color and smell can also be helpful clues in judging the success or failure of any machining process.
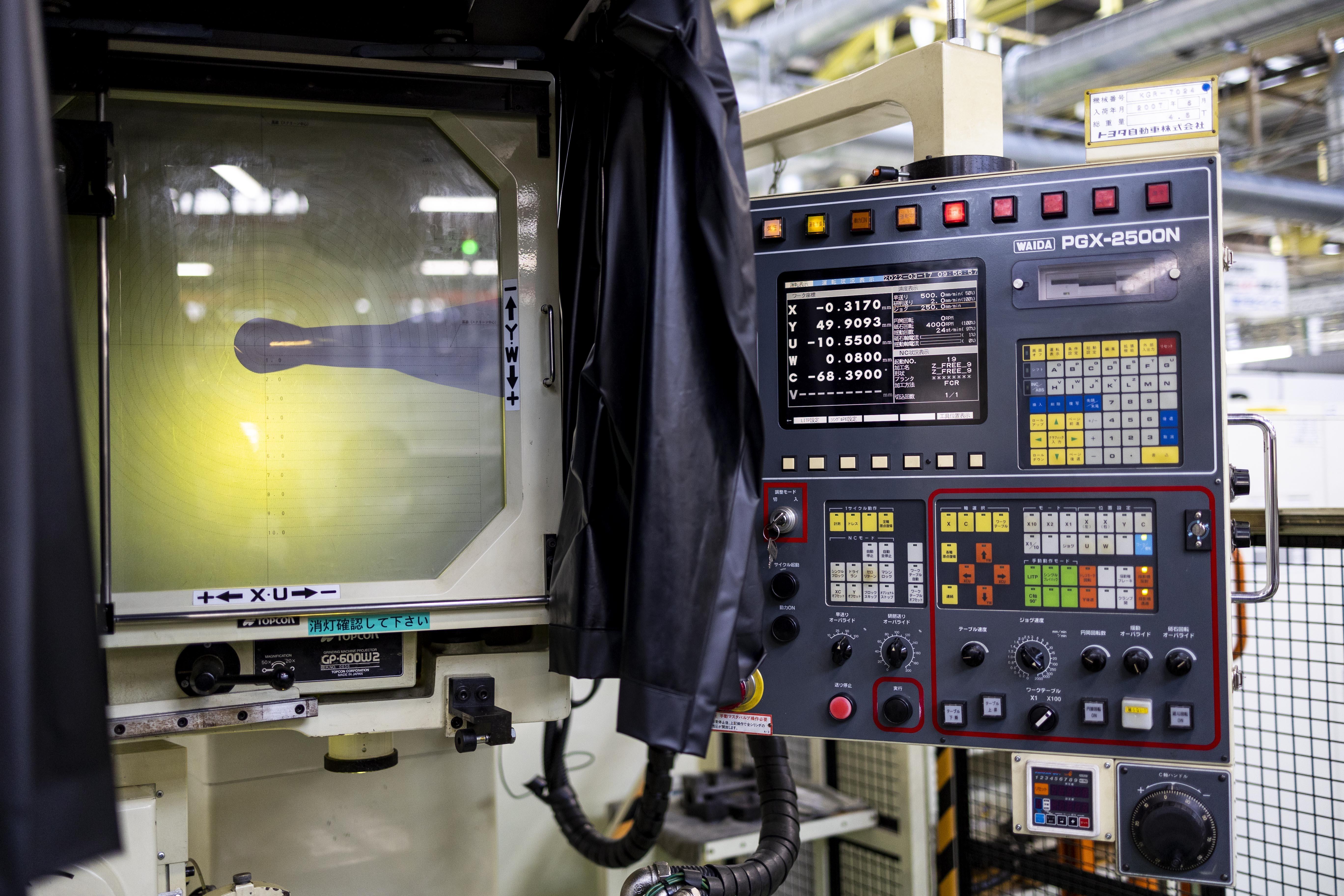
For training, there is a measuring device to check the precise dimensions of sharpened edges and a grinder that projects a magnified view of cutting tool tips during sharpening and grinding. Members use both their own eyes and such tools to precisely shape blade edges.
Cutting tools as works of art
Hayashi demonstrated center-point grinding, a way of shaping drill bit tips to reduce burr waste formation around the exit when drilling thin sheets.
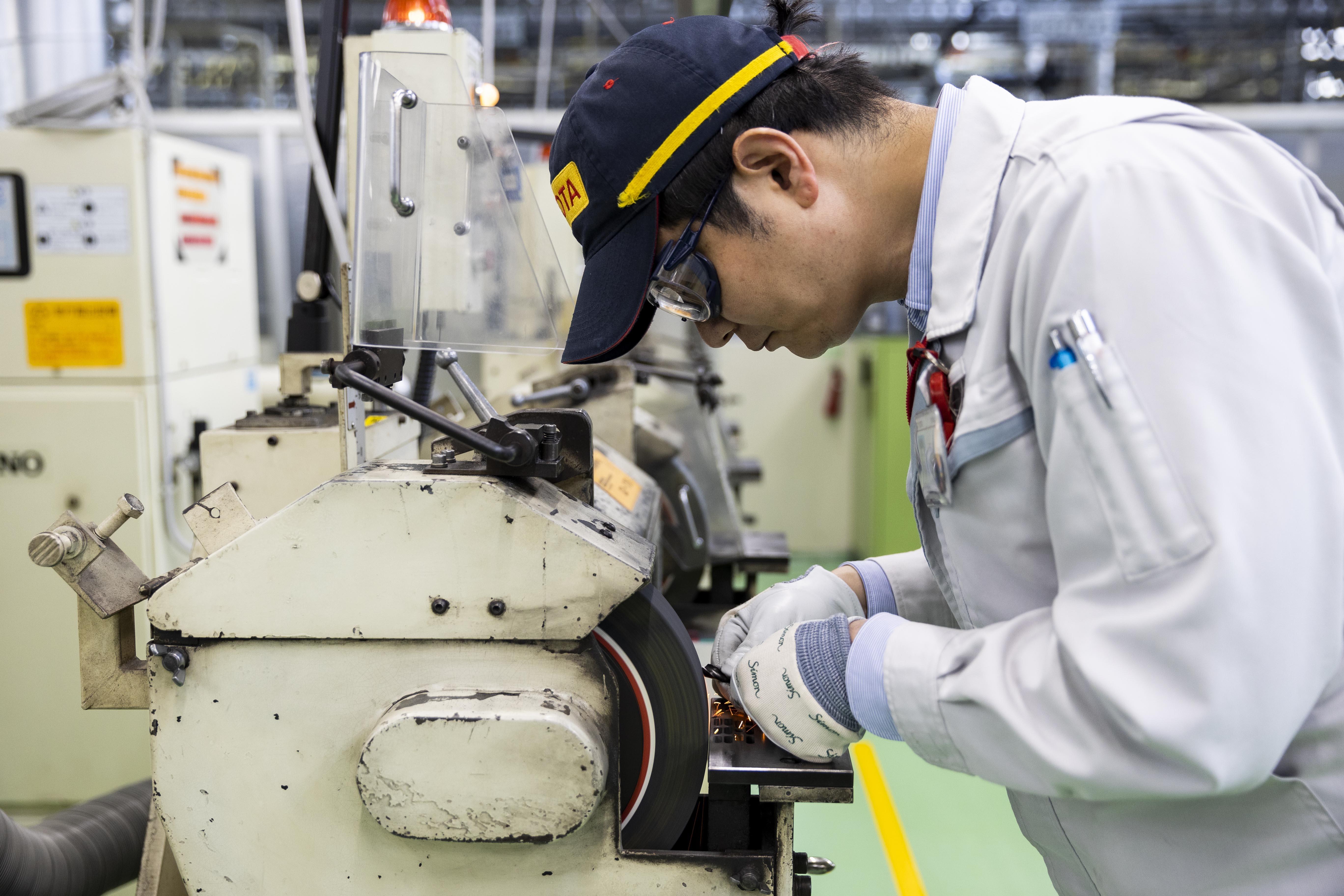
Center-point grinding reshapes the center of the drill bit tip into a chisel shape and the two sides of the tip into a square pyramid shape to let the center protrude. Hayashi completed this tricky grinding by hand within an incredible time.
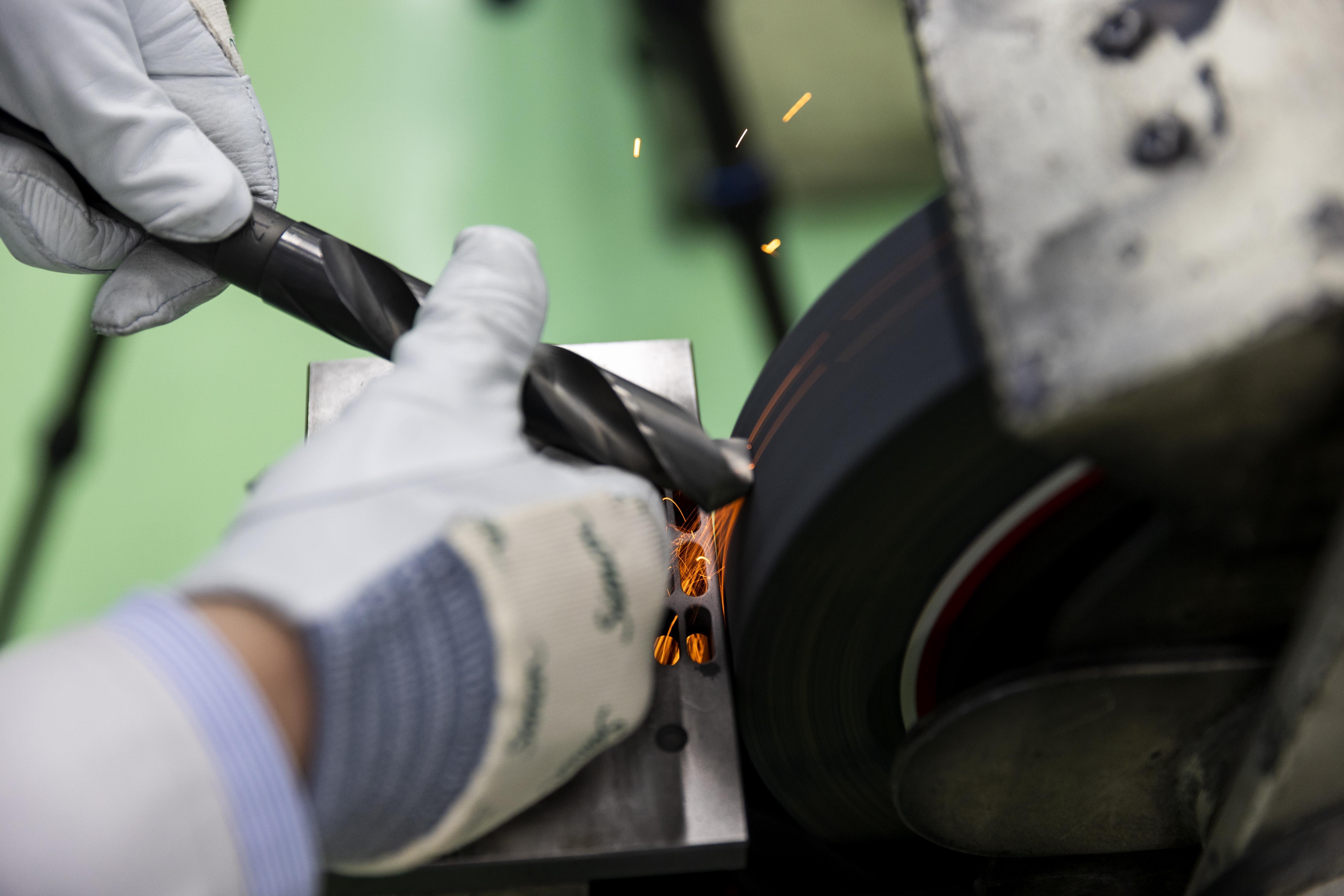
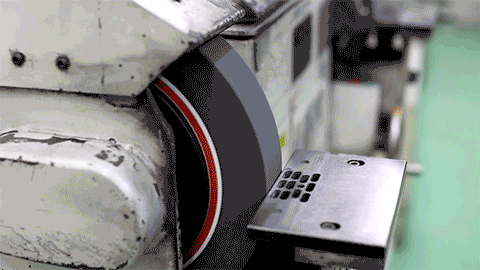
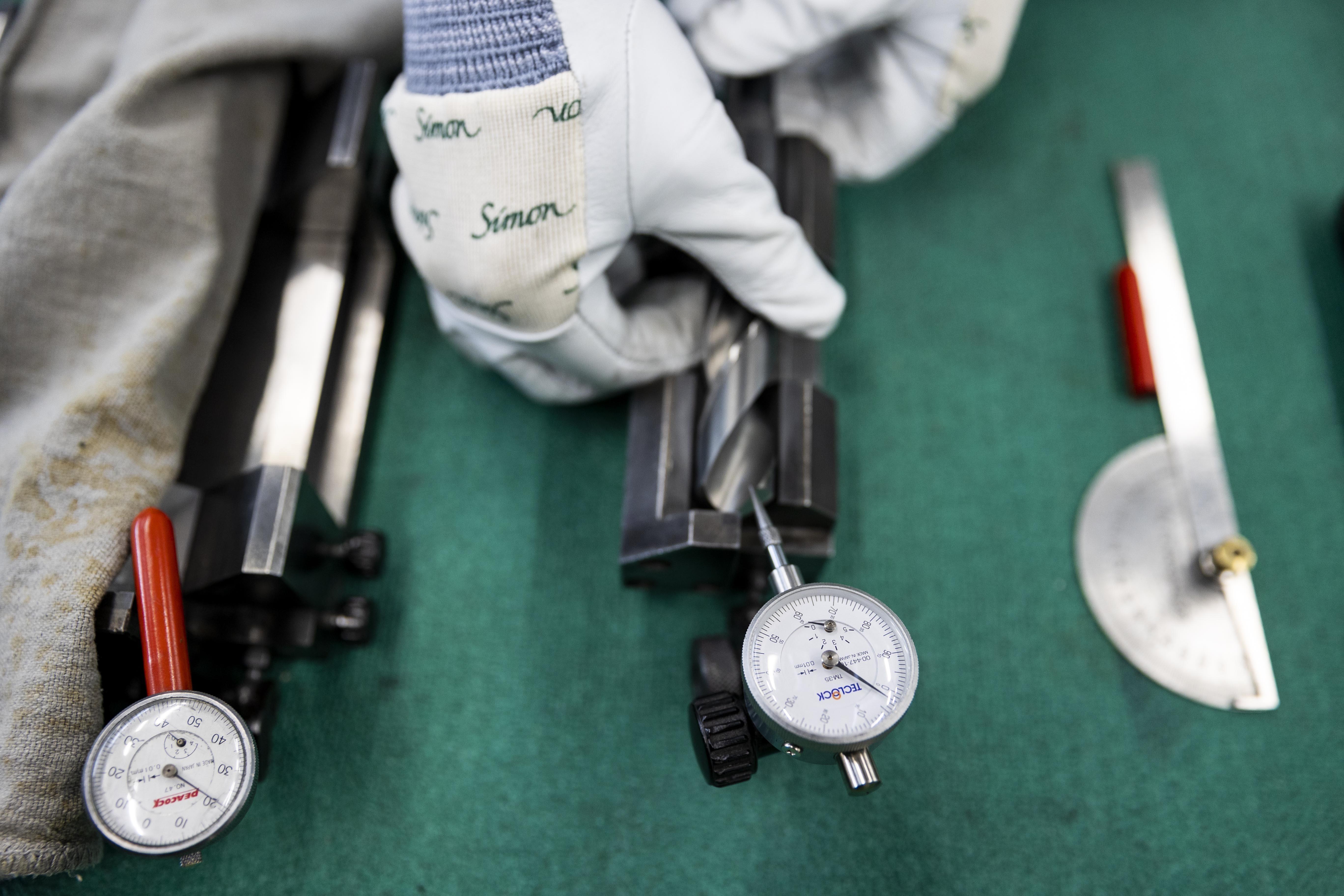
“This work depends greatly on manual dexterity, but more important is a desire to create. Every individual’s skills, innate abilities, and senses differ. We can give the trainee hints but can’t take them through every step. Everyone has to think and explore for themselves.”
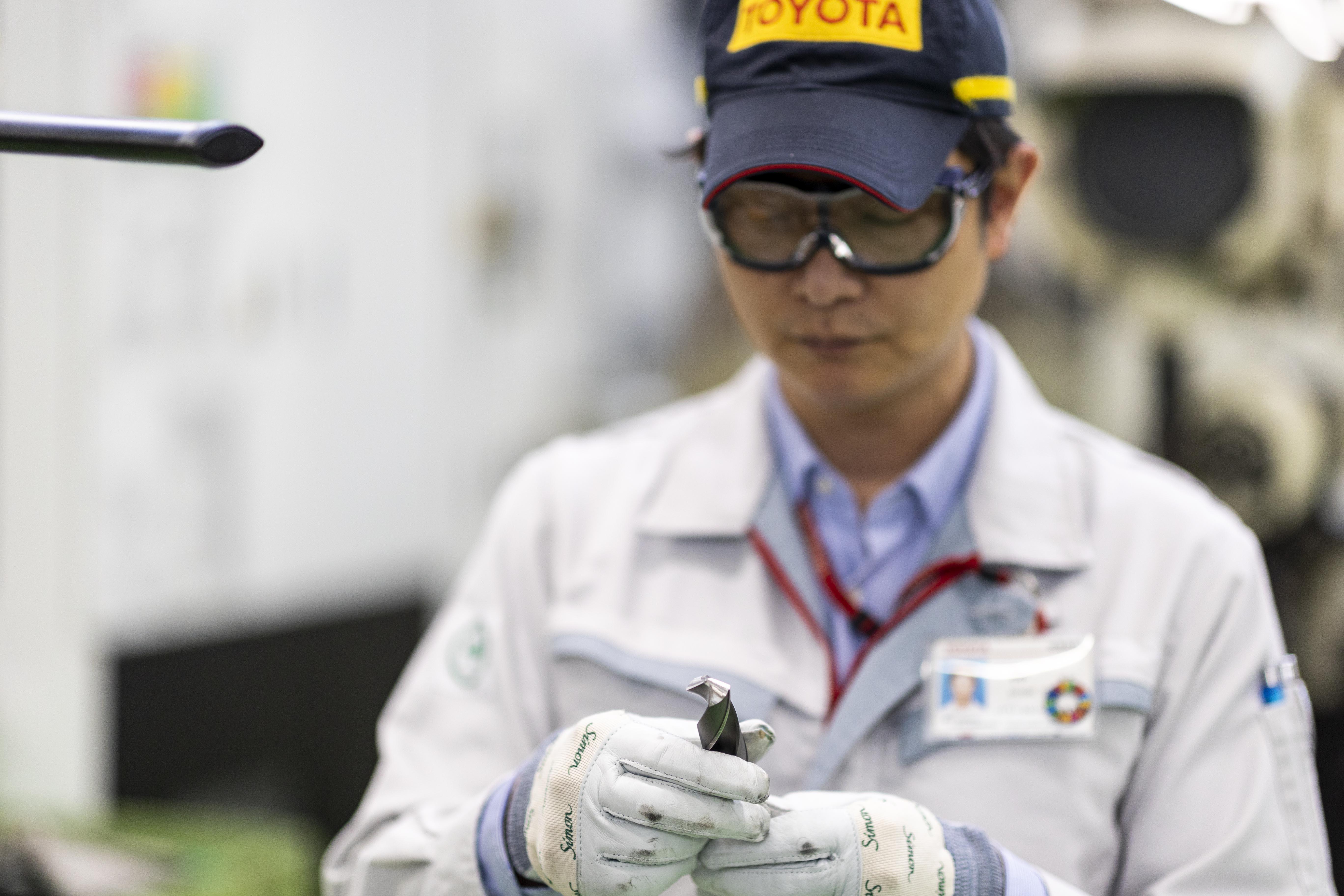
Hayashi’s work on the drill’s cutting edge was simply beautiful. Every single cutting tool he showed during this interview revealed surprising beauty, either on its edge or surface.
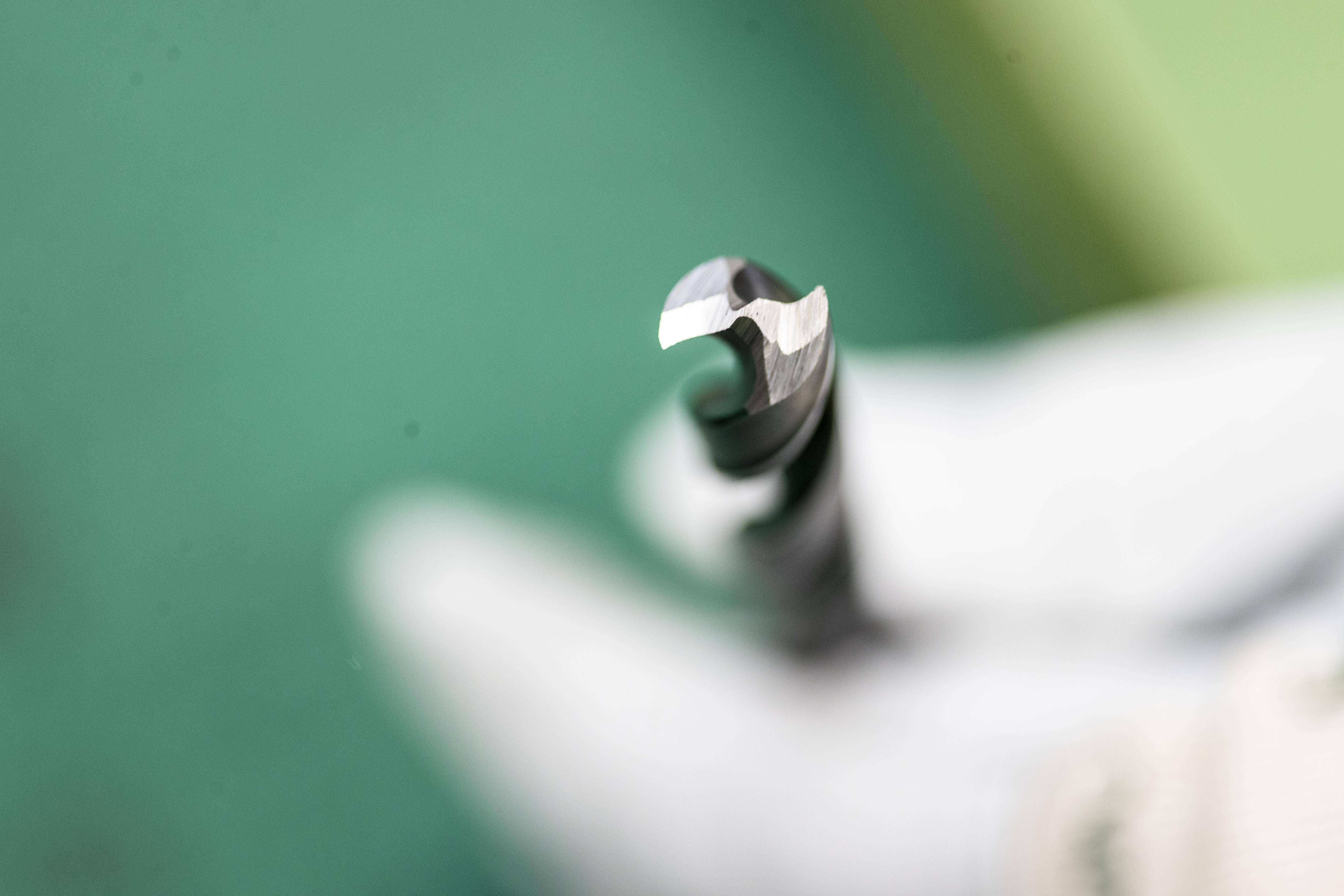
Many people have no chance to see the cutting tools of final products, but in fact, the tools are indeed works of art full of skills and craftsmanship built up in the history of machining. All Toyota cars are made using such artworks.
The craft of maintaining and restoring these works of practical art underpins Toyota’s monozukuri, and that work’s value will surely remain unchanged in the future.
A once-in-a-century transformational period
The automotive industry is now in a once-in-a-century transformational period. Hayashi and other members continue to pass on their cutting tool skills to the future generation, but they’re also starting to take on new challenges to prepare for the future.
One of those challenges is developing novel cutting tools for use in prototyping. Creating specialized tools for new tasks can help dramatically accelerate work.
“Tool manufacturers won’t accept specialized tool development without a large order lot. Outsourcing the development is costly and time-consuming, too. Making small batches of tools in-house can reduce both time and cost, so we can immediately do any necessary improvements and refinements.”
As cars continue toward electrification, the car materials change as well, resulting in diverse needs for processing novel materials and shapes.
“As electrification progresses, fewer parts related to the metal powertrain will be needed. The variety and number of cutting tools will also decrease. But that also means that we’ll need new cutting tools. Electrifying cars will not eliminate the need for a vehicle body. The materials may change, but the shaping tools and molds will remain.”
Hayashi says that he would like to turn his group’s know-how to totally new fields both in and outside Toyota, in hopes of contributing to even better and more appealing monozukuri.
“I want to develop a consulting business as a professional in shaping and sharpening, both inside and outside the company. The more I learn, the more I see how deep these topics are. New materials and new processing methods are showing up one after another. That’s why studying never ends.”
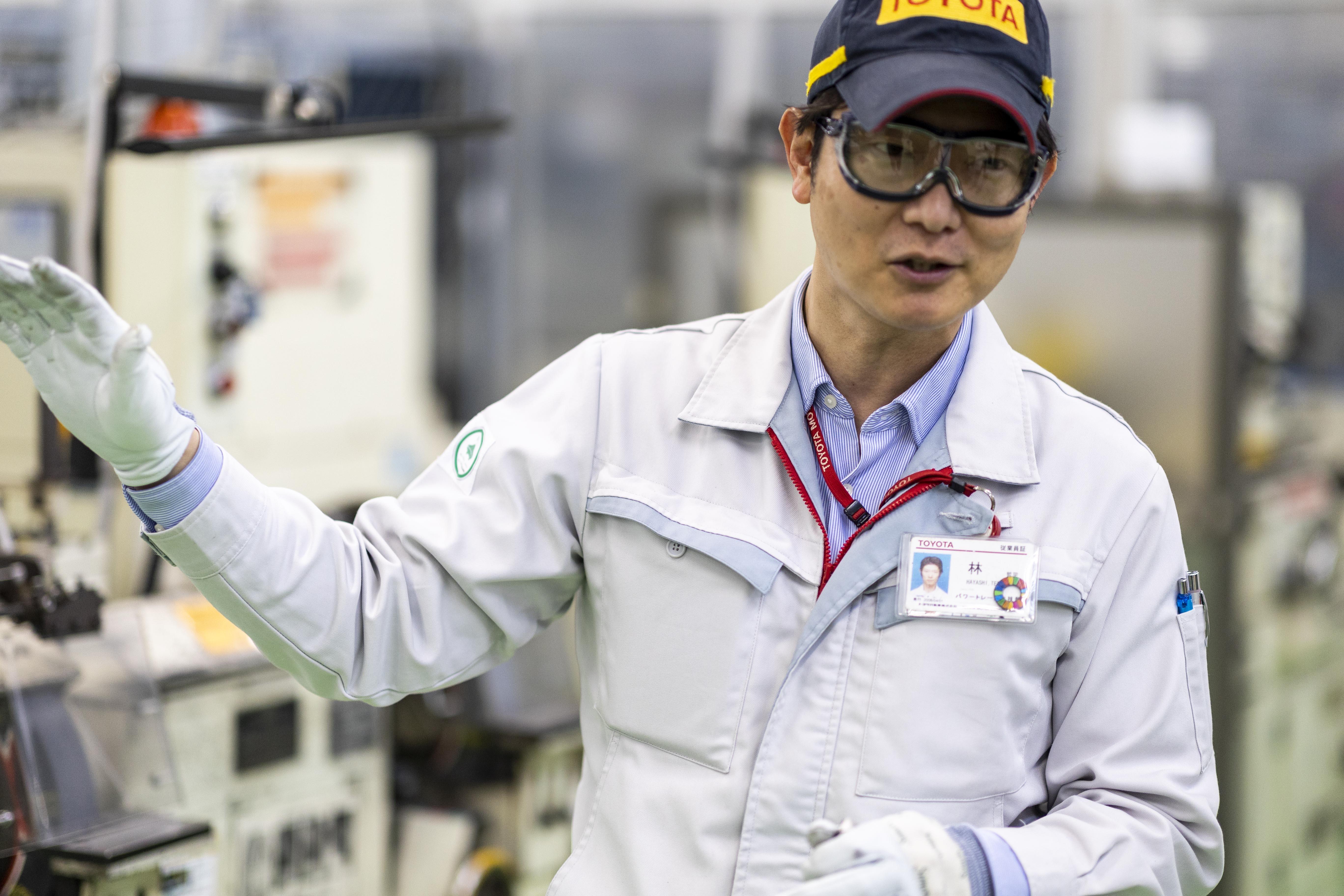
As car manufacturing moves into the future, Hayashi’s challenges as a master of cutting tools are far from over.
(Text: Yasuhito Shibuya, Photo: Yuqi Zhang)