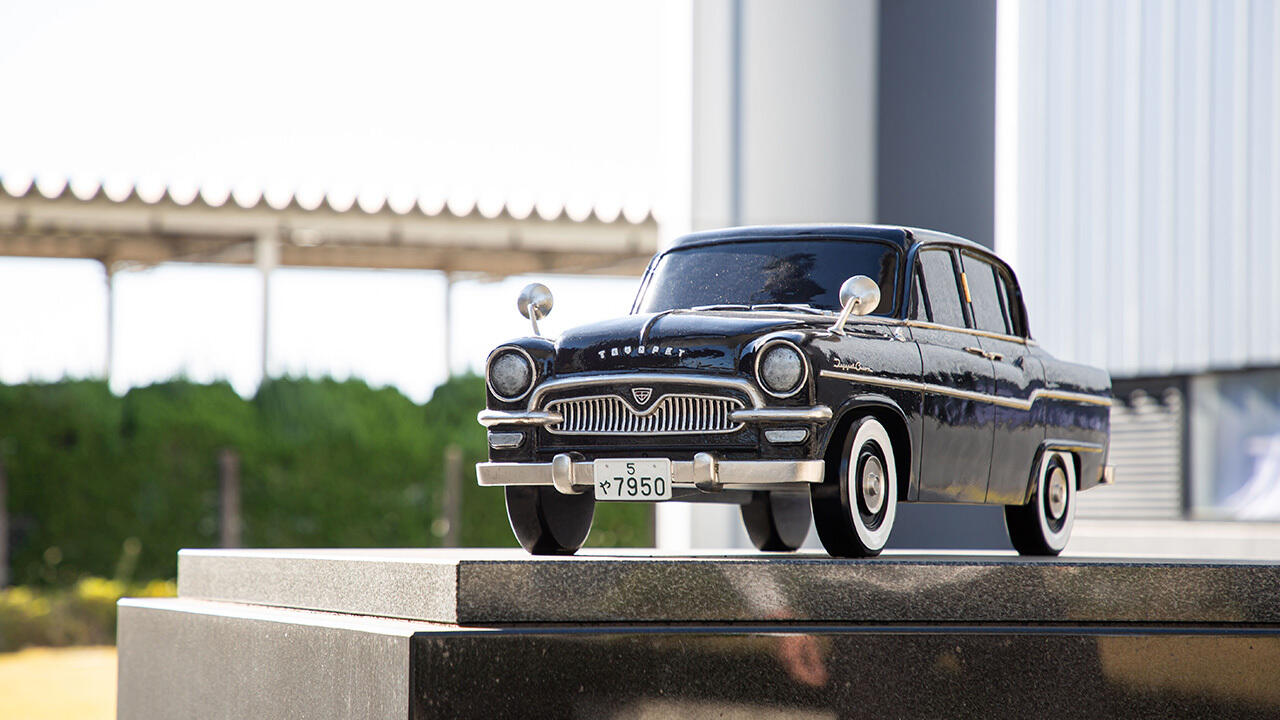
In the five years since 2020, Toyota's Motomachi Plant has launched 15 different car models. We unravel the plant's history to see how its unique spirit and skills have been passed down to this day.
Committed to getting the job done
Though far from smooth sailing, Motomachi’s journey gave rise to high-mix, low-volume production. One essential element in this approach is mixed model production lines that handle vehicles of different shapes and powertrains.
Kazuhiro Kitai, manager of Assembly Section No.1, explains.
Kazuhiro Kitai, Manager, Assembly Section No.1, Final Assembly Division
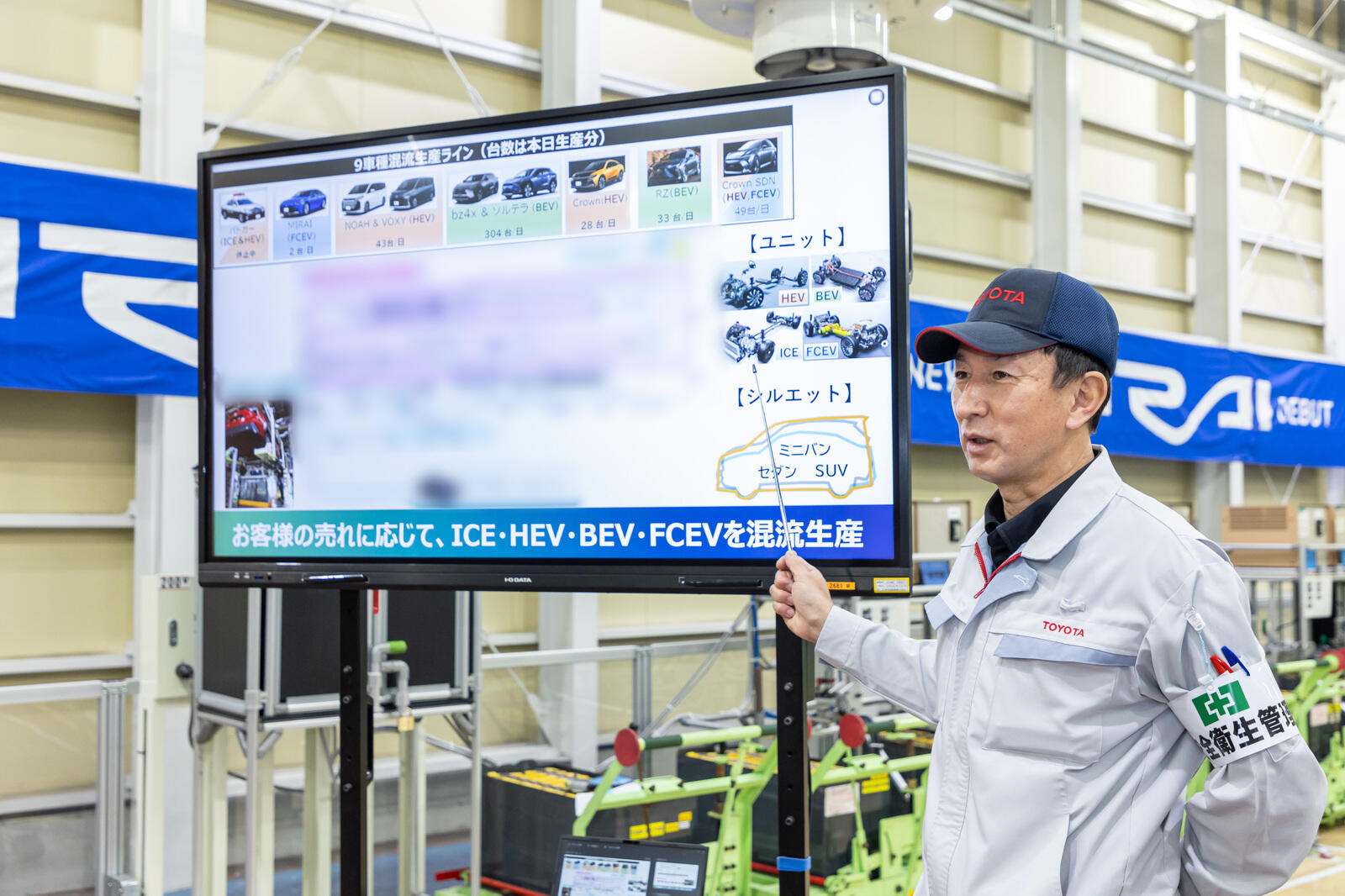
All of us who work here have made various improvements to enable a multi-pathway approach. In an age of diversity, I don’t think it would be possible without creating more worker-friendly processes and making efforts to ensure that people find fulfillment in their work.
Take the installation of a rear door wiring harness, for example. In sedan models, the task can be done in a regular standing position, but for taller minivan-type vehicles it requires a stepladder.
In the case of SUVs, the size of the rear door means that workers must climb inside the vehicle. Because working in a stooped posture is physically demanding, the plant devised mobile steps that include a seat.
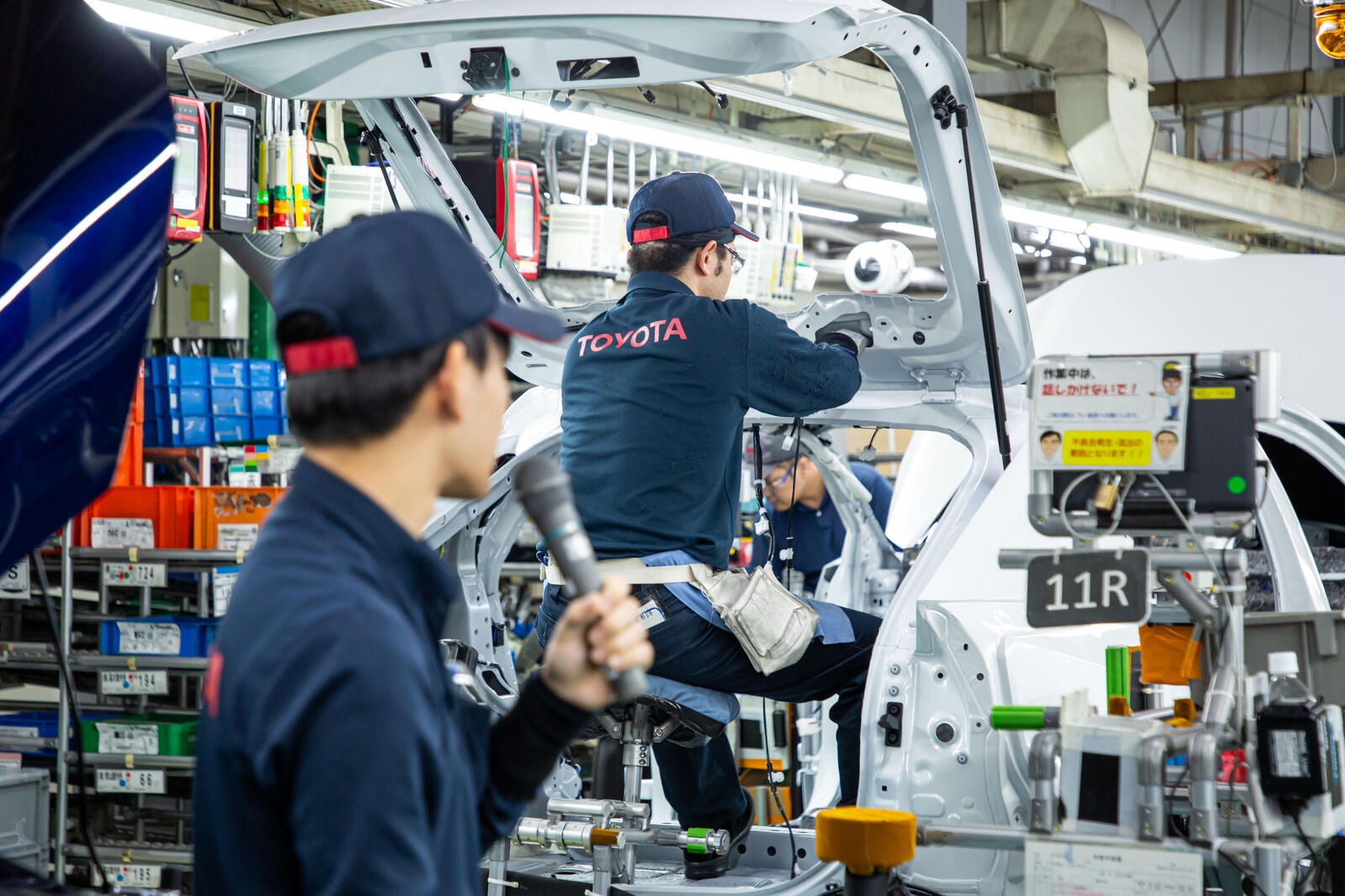
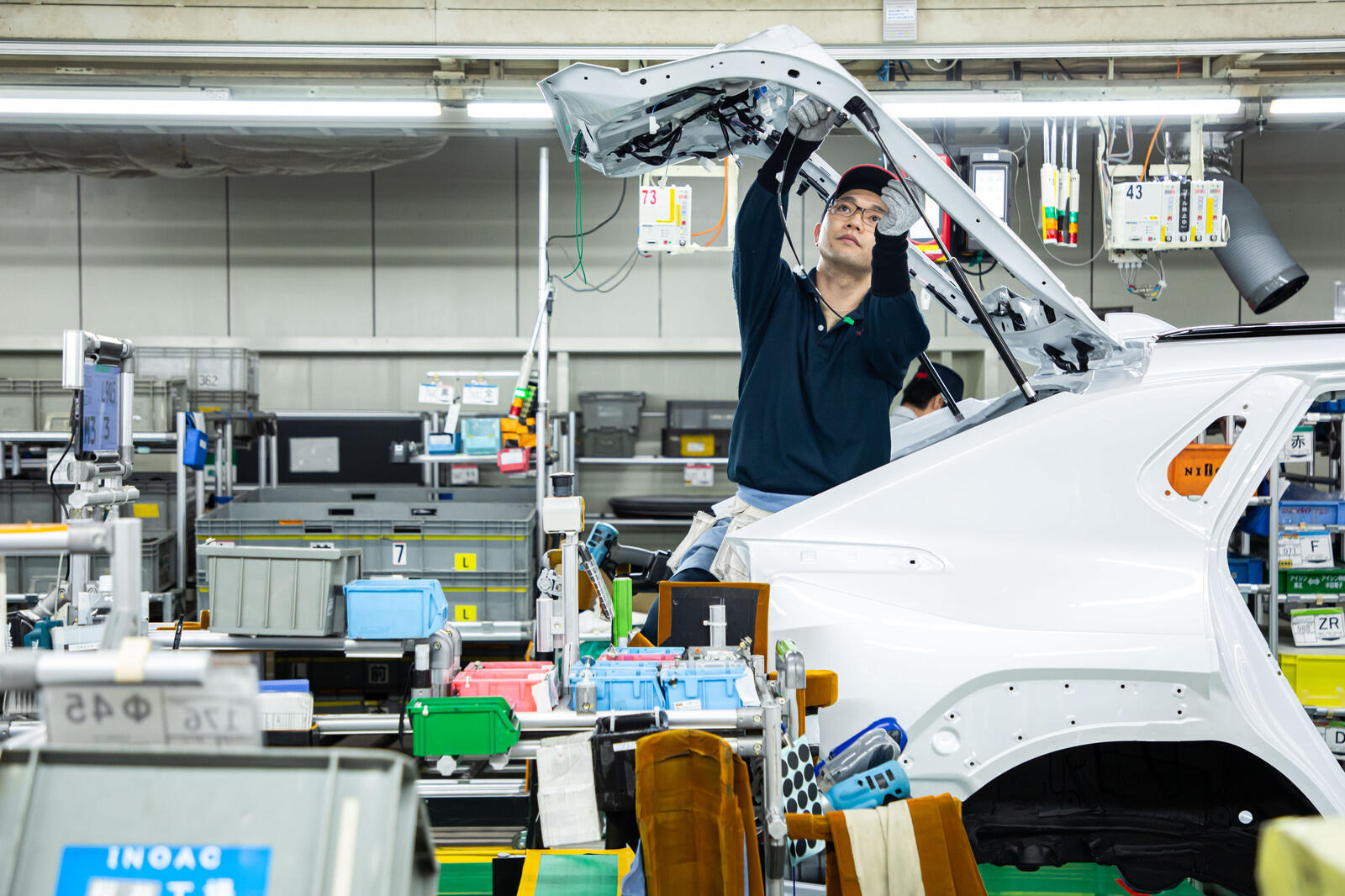
More than just a simple stool, this seat is designed for stability, with springs that compress under weight. It also rotates, allowing workers to turn their bodies so that the harness they are installing is always directly in front of them. All these improvements were made with workers in mind.
Motomachi’s “whatever it takes” spirit also led to low-volume specialty production work.
The plant is home to the GR Factory, which produces models like the GR Yaris and GR Corolla, and recently also the Lexus LBX Morizo RR.
This line agilely applies the ever-better carmaking expertise gained through motorsports into the production process.
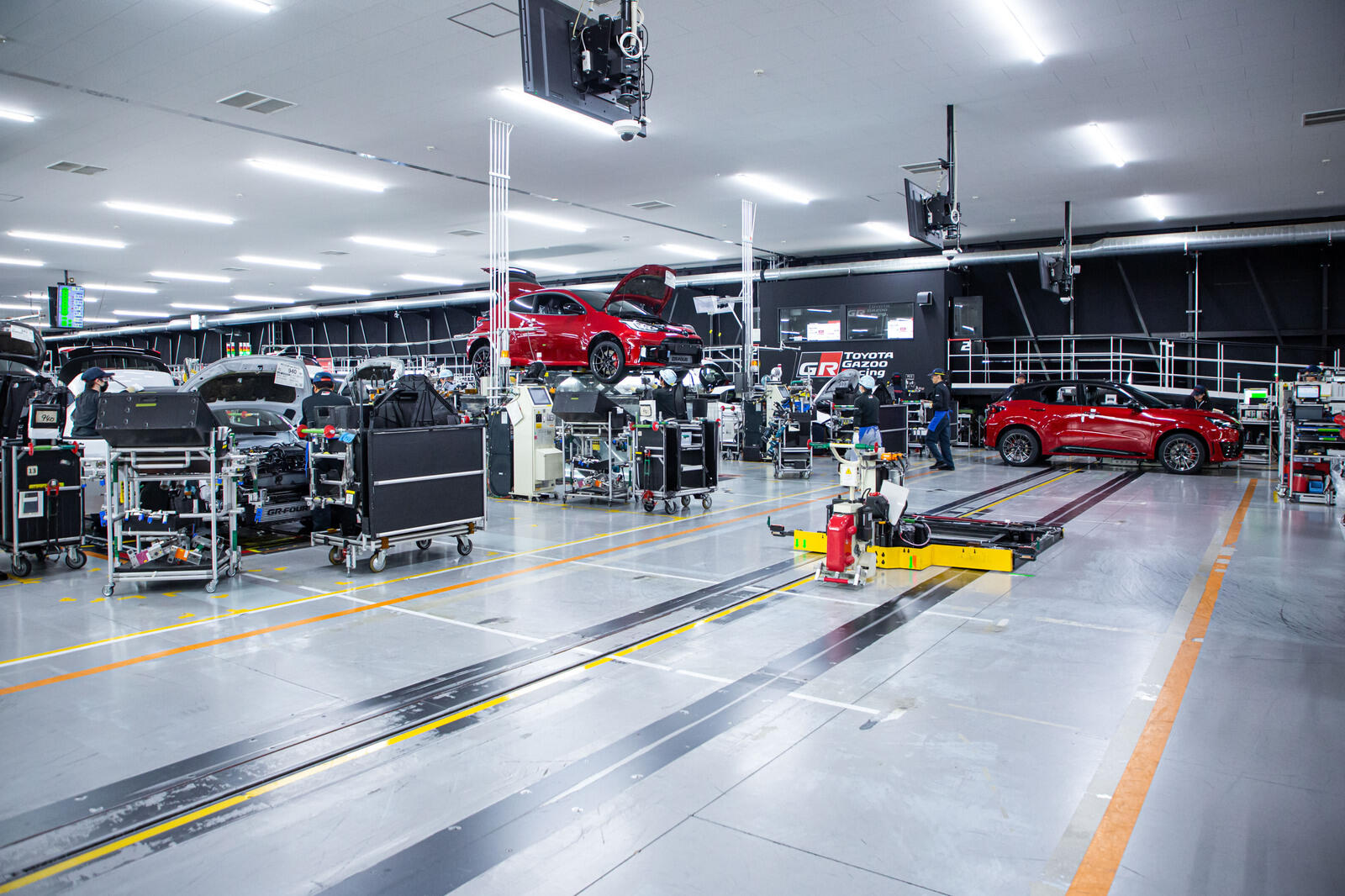
The big difference here is the level of quality, with racetrack-ready monozukuri being replicated on a mass-production line.
For any manufactured goods, dimensions will vary within a set tolerance range. Yet even minor deviations that pose no problems in a production car can have a big impact on results in racing, where vehicles are pushed to the limits of performance.
At the GR Factory, with guidance from professional racing drivers, the team strives to eliminate such deviations.
When attaching suspension components to the body, for example, technicians use a system that takes three-dimensional measurements of bolt hole positions and matches components to compensate for any slight deviations from the standard values.
Then during assembly, a jig is used to adjust the positioning at the sub-millimeter level—too small to be seen—to completely overcome individual differences between components.
Still more astonishingly, the line is set up to ensure that a car’s steering wheel is not turned until the wheels undergo alignment. The vehicle proceeds in a perfectly straight line so as not to throw off the high precision and balance built in during assembly.
Even when assembly is complete and the car moves on to the final inspection, it is redirected using a turntable so that the inspector does not need to turn the steering wheel.
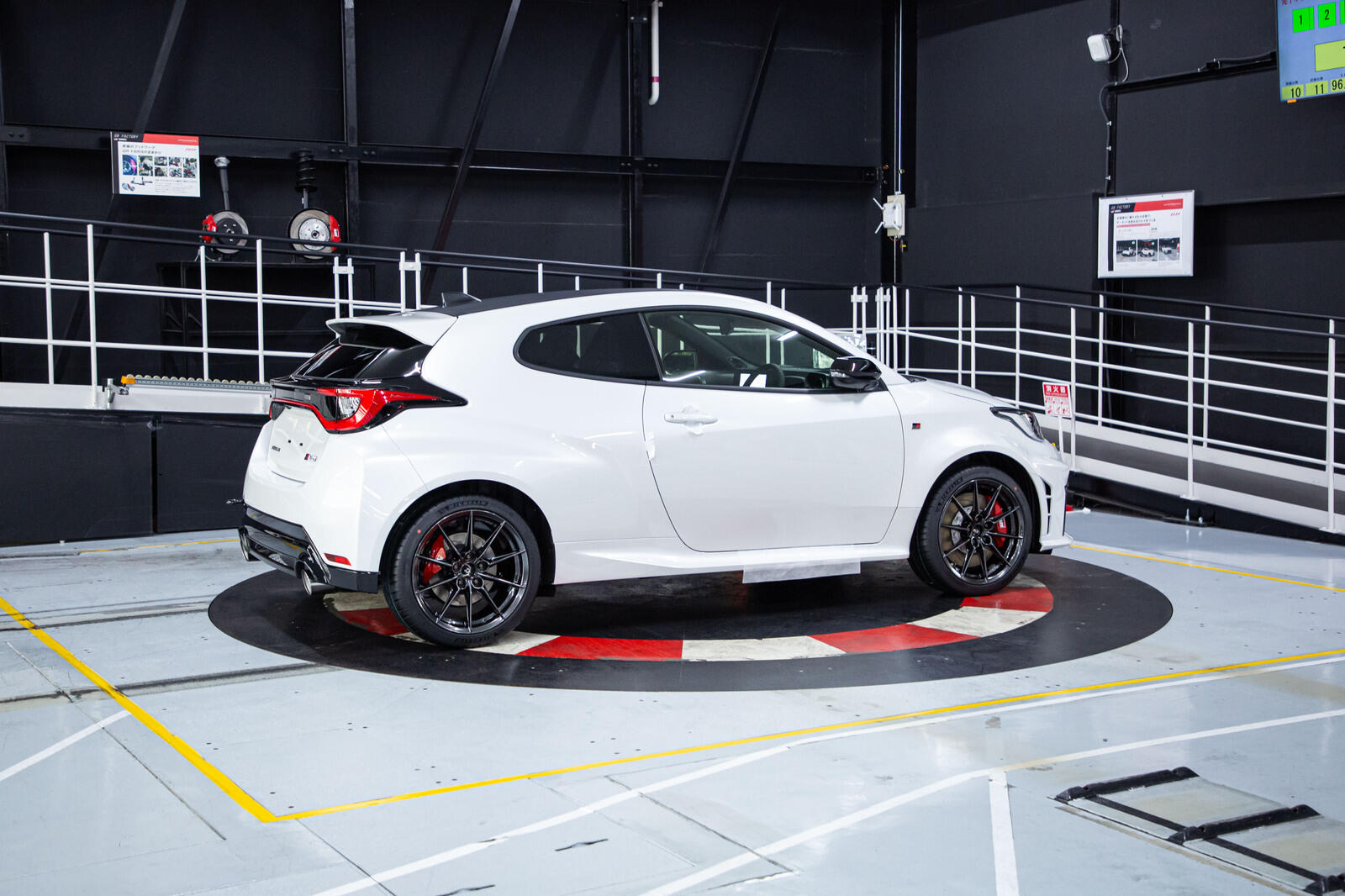
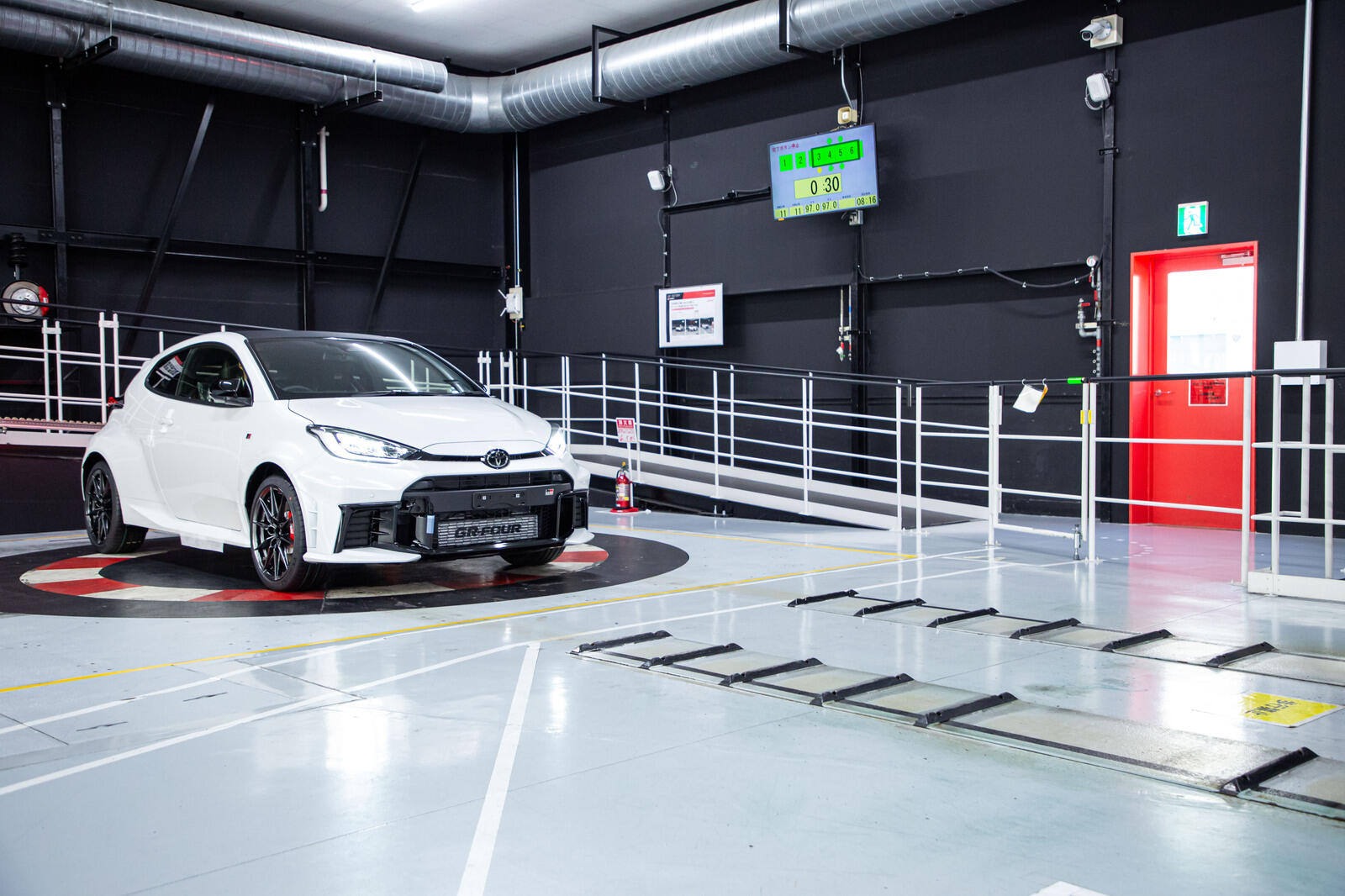
Immediately before wheel alignment, the car is taken over bumps to shake out any distortion in the suspension.
Shifting this meticulous car-by-car manufacturing approach onto a mass-production line was an unprecedented challenge. Kenta Sugiura, manager of Assembly Section No.3, spoke of the genba’s dedication in overseeing a line that must constantly evolve to meet the needs of motorsport.
Kenta Sugiura, Manager, Assembly Section No.3, Final Assembly Division

Some of the feedback we get from Morizo and Toyota’s racing drivers seems like a tall order. But rather than saying we can’t do it, the GR team is committed to figuring out how to make things happen. Our job doesn’t end when the line is ready—just like our cars, we must keep evolving.
Intentionally preserving hands-on processes
“A robot will only write as neatly as it is taught. If you want a robot to write nicely, you have to teach it with good handwriting. And to do that, you need to train people who can write even more beautifully.”
This is how Oyaji Mitsuru Kawai (Executive Fellow), a 61-year veteran of the monozukuri genba, describes the relationship between skill and technology.
Motomachi Plant General Manager Yoshihisa Miyabe explains how these skills underpin the manufacturing cycle.
Yoshihisa Miyabe, Plant General Manager
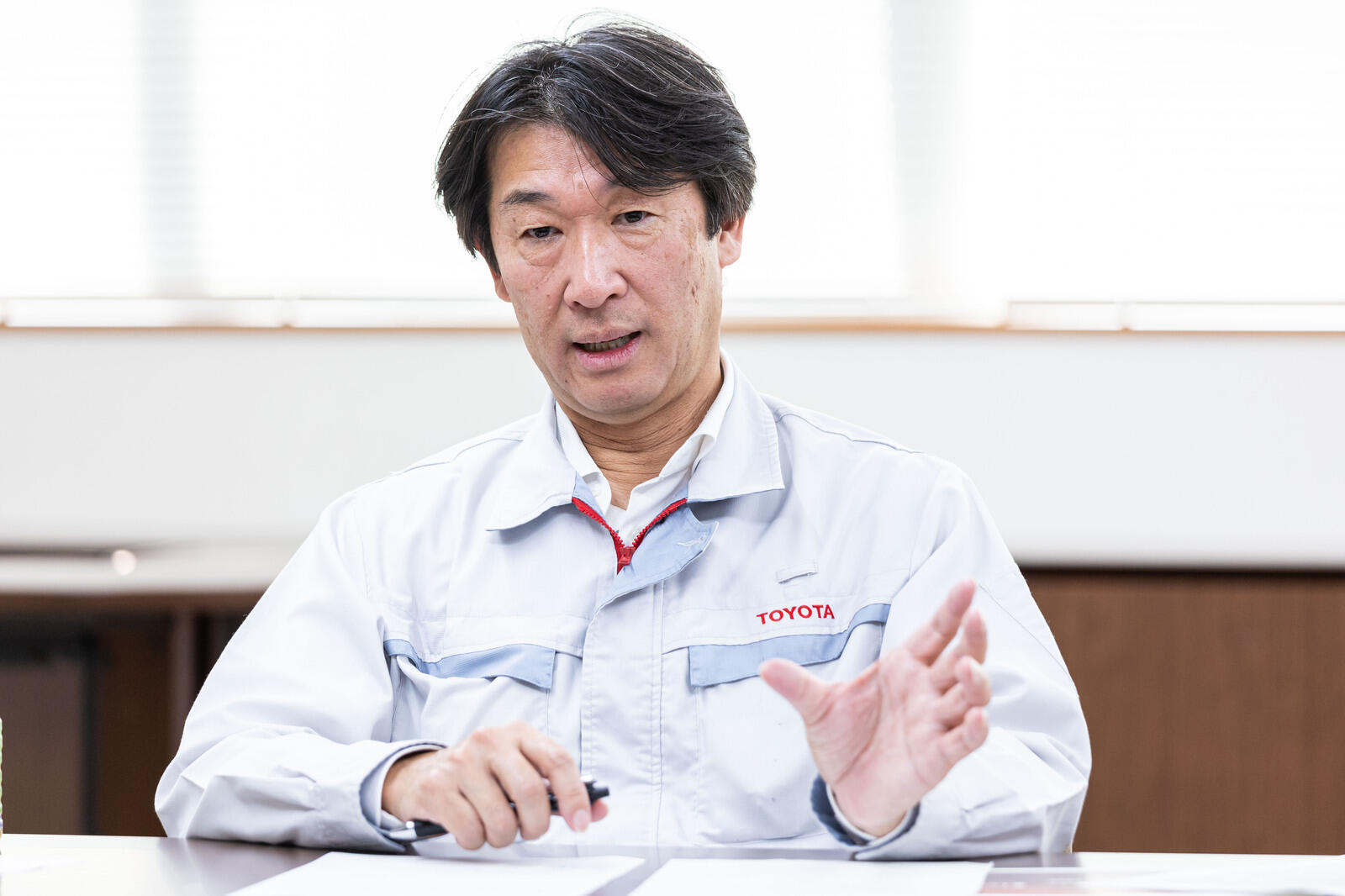
At present, many of our genba personnel still come from a generation that made things by hand, so we can create the programs to train robots. A few decades from now, however, if we are only left with people who have never done the tasks themselves, we won’t be able to do that. It’s important that the shift to AI and automation is driven by the people who are most familiar with our cars and processes.
Handling brands such as GR, which are not focused on volumes, puts the Motomachi Plant in a unique position to intentionally preserve manual processes.
Let’s take a look at some of the craft that is being passed down with this mindset.
At Motomachi, delivering low-volume, high-mix production involves using many stamping dies—currently the figure stands at 985. A die maintenance team is tasked with the daily upkeep needed to sustain production.
For example, when a blade for cutting steel plates becomes chipped or worn out, it is refurbished by welding and machining. Welding in particular is a task that relies on the skills and instincts of the technician. Such skills also greatly impact the speed of repairs and the durability of dies.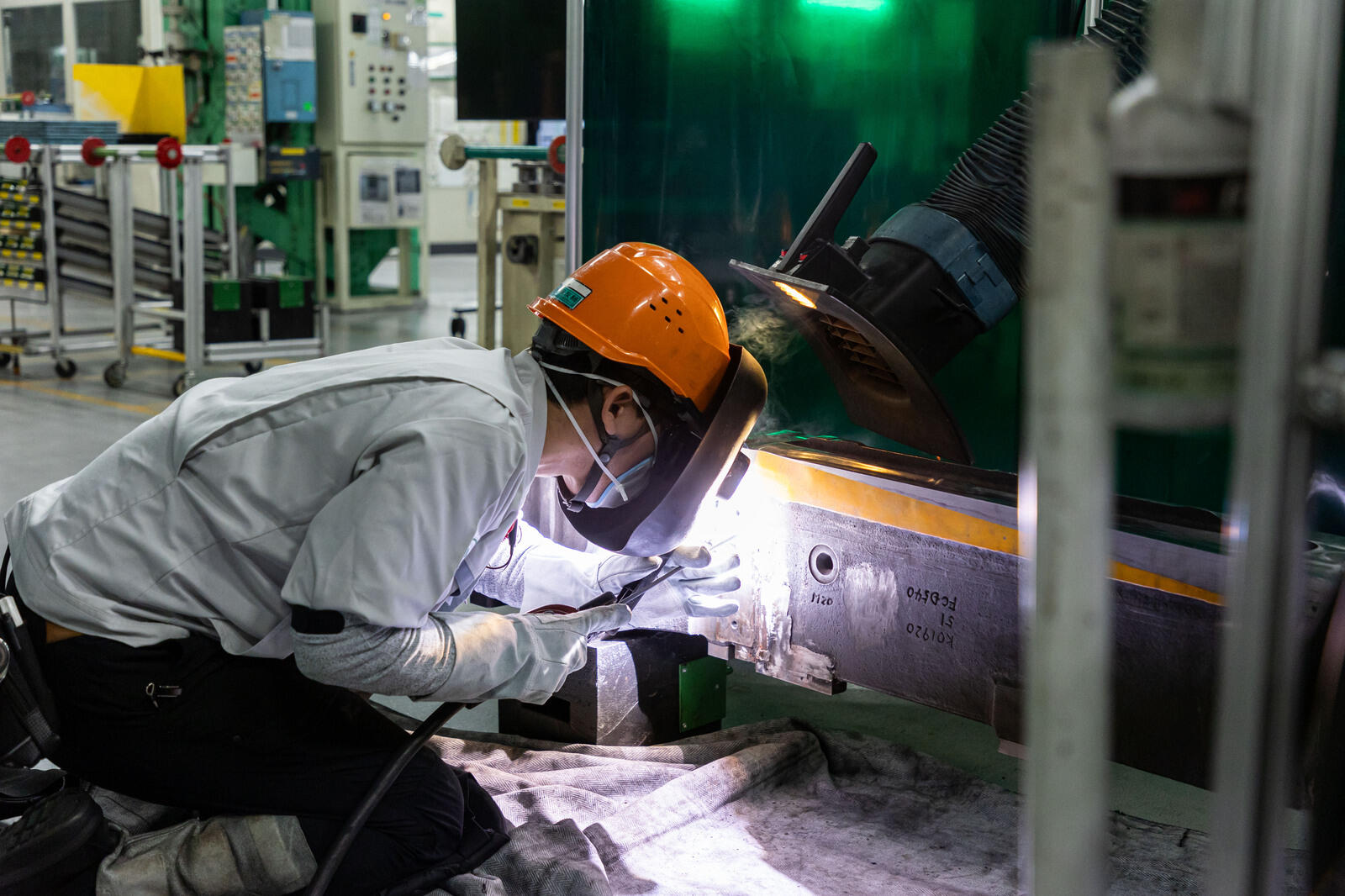
Yusuke Kosaki, who is part of the plant’s Stamping Section, has even participated in national welding competitions. He says he inherited more than just skills from senior colleagues.
Yusuke Kosaki, Stamping Section, Body Manufacturing Division
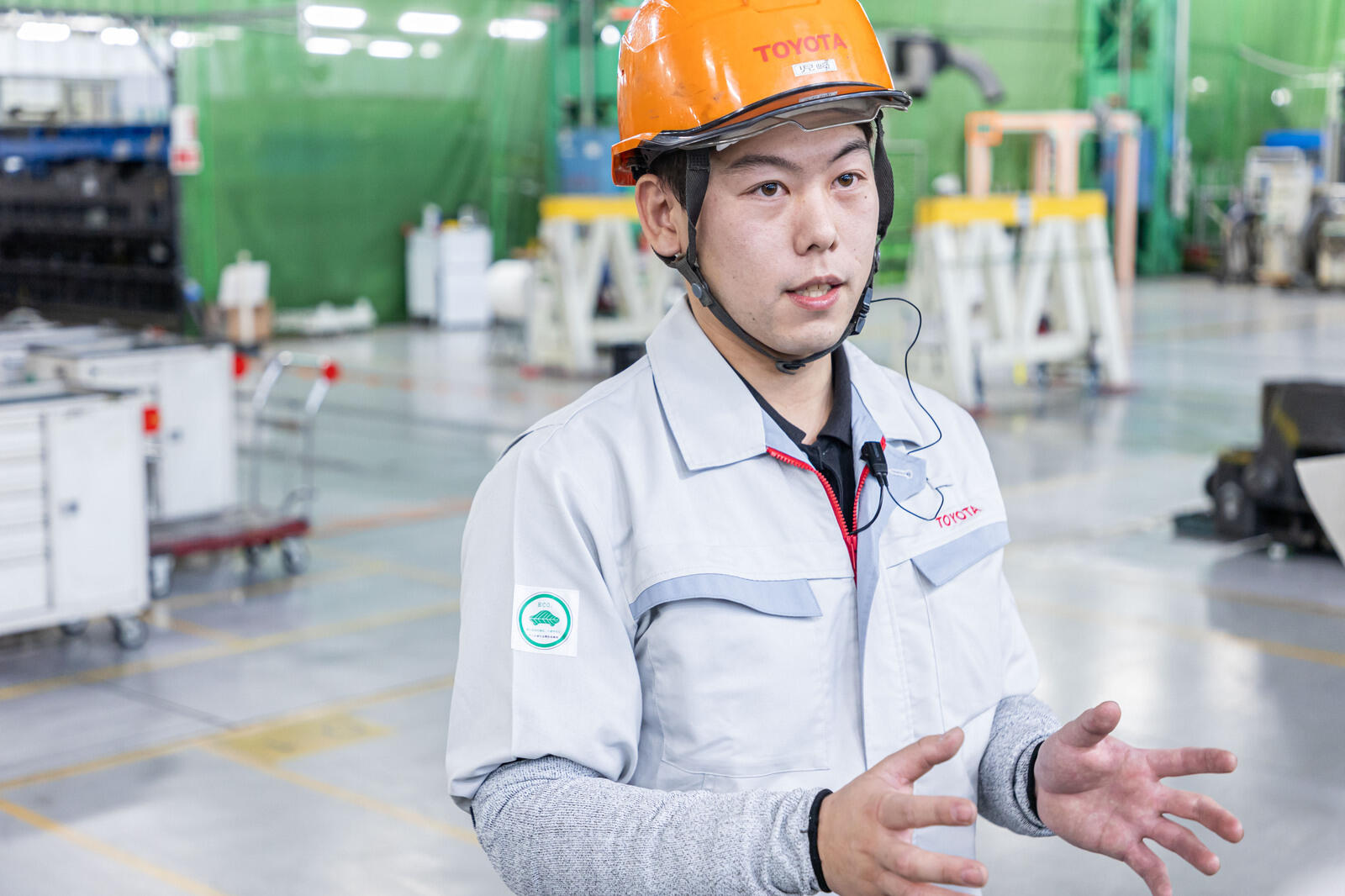
When I view work by older colleagues on the factory floor or at welding competitions, I can see not only how well things are made, but also the person’s devotion to what they are trying to create. Since I realized that this is crucial for improving skills, I have paid more attention to the tools and environment, as well as my own mental and physical state. My work has become more polished as a result. It’s a lot of fun. I hope that younger welders will also devote themselves to the task. That’s the message I want to share.
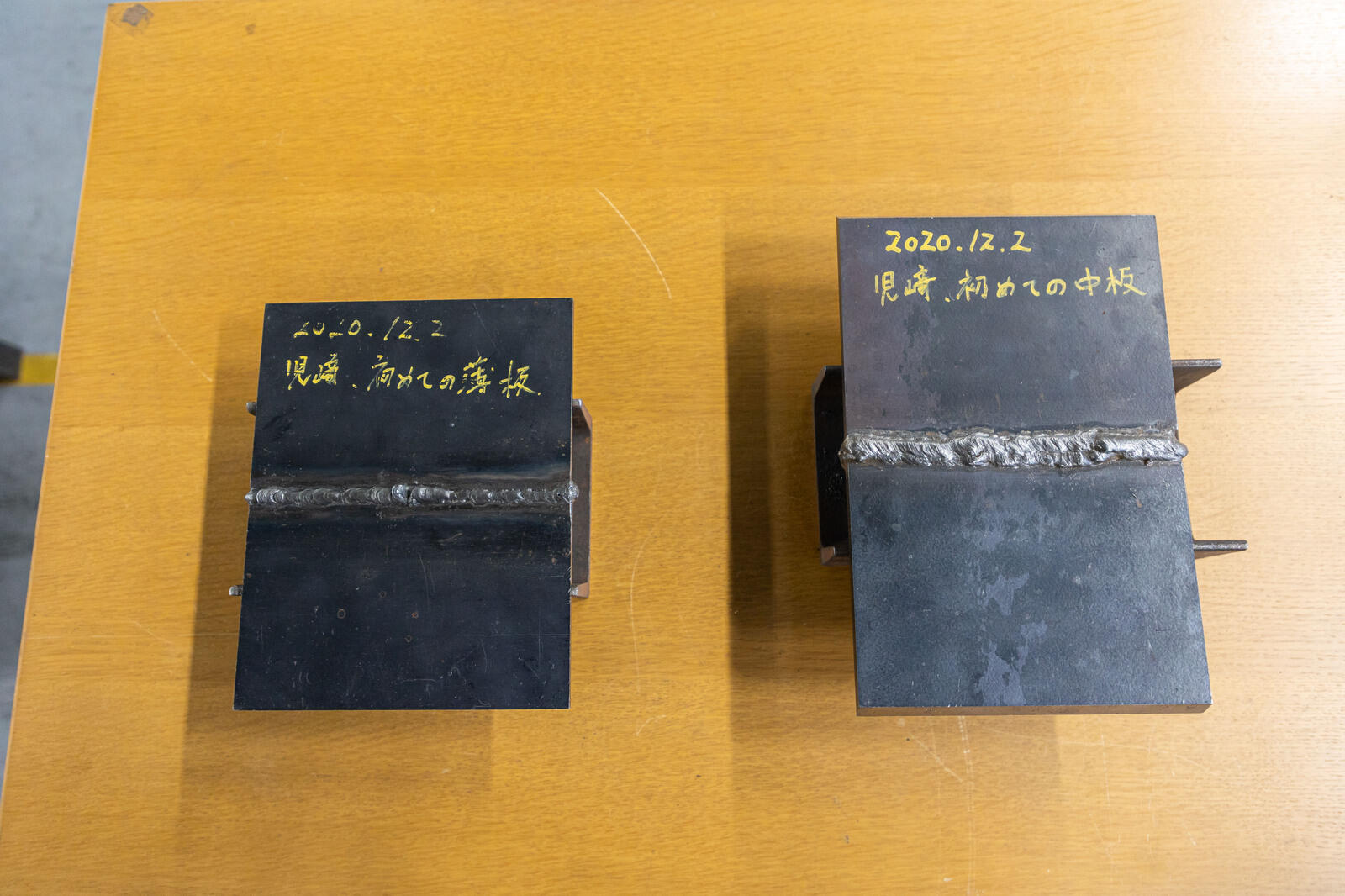
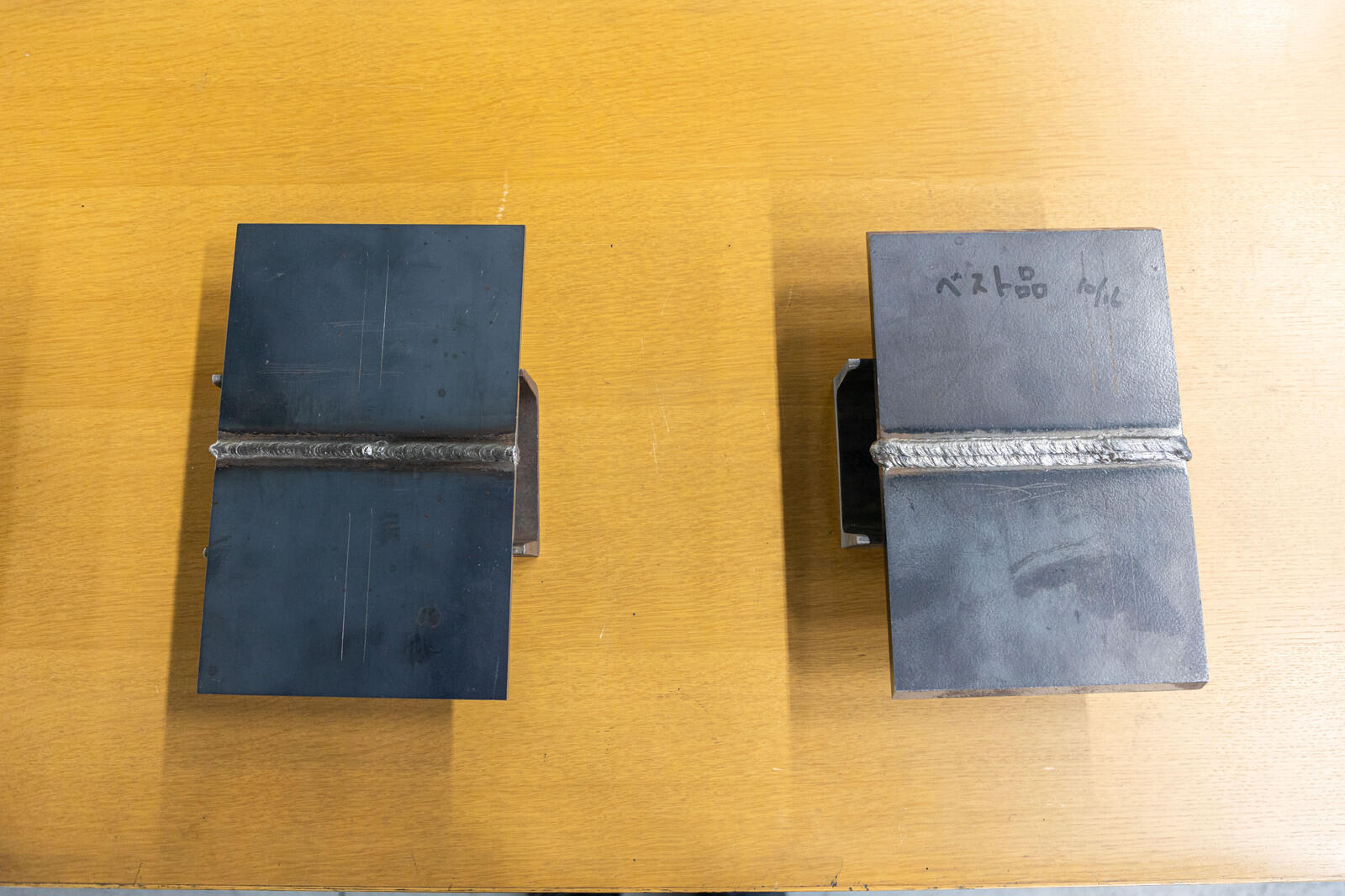
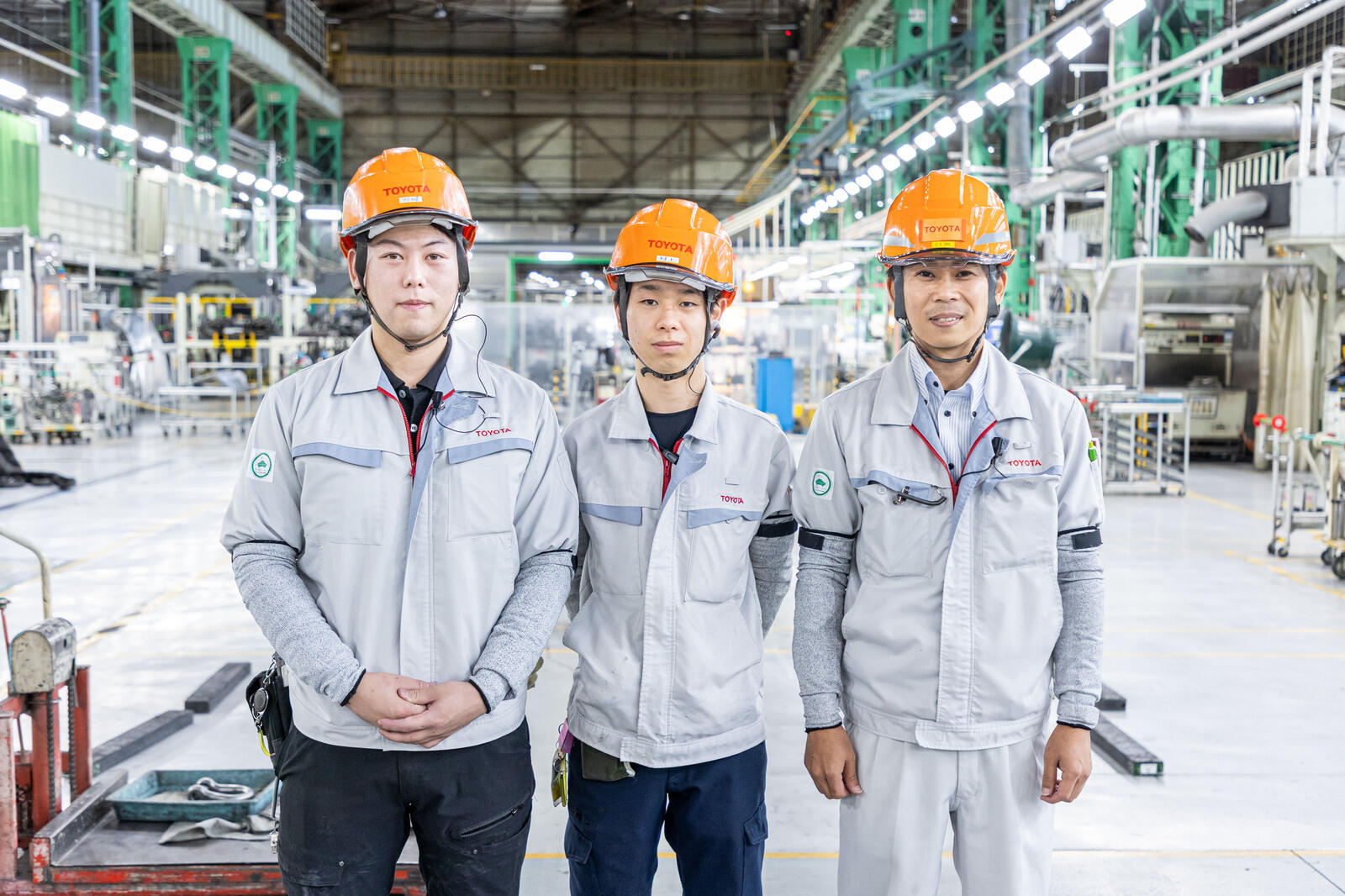
The Motomachi Plant also houses a much smaller workshop, where figures move around a space that is far quieter than the mass-production lines.
It is here that the Century, Toyota’s flagship model, is handcrafted by a select team of takumi, the company’s master technicians.
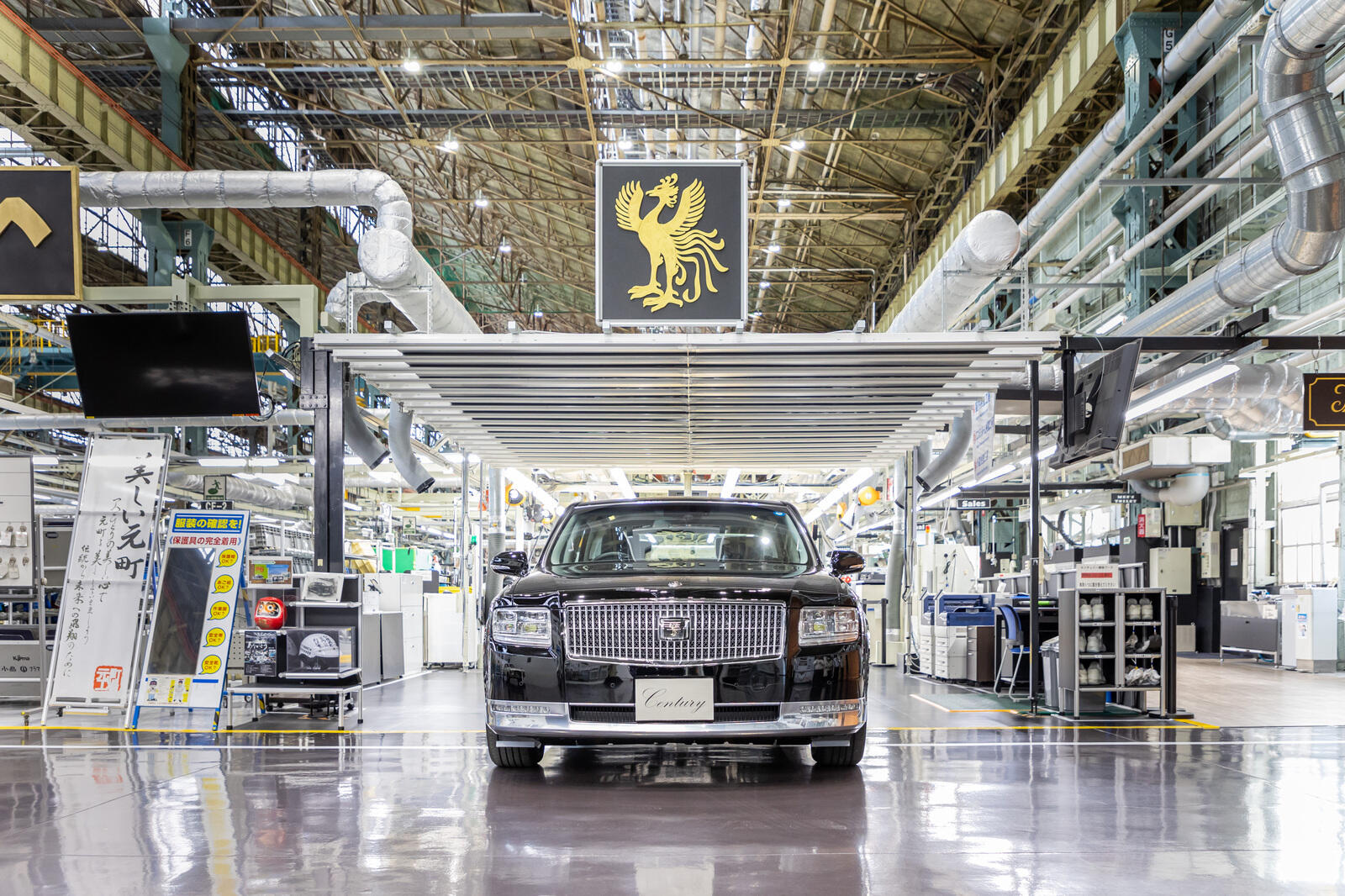
Four craftspeople spend three days producing a single vehicle on an assembly line bearing the model’s striking phoenix emblem. Using check sheets, they assess the quality of each car with their own eyes.
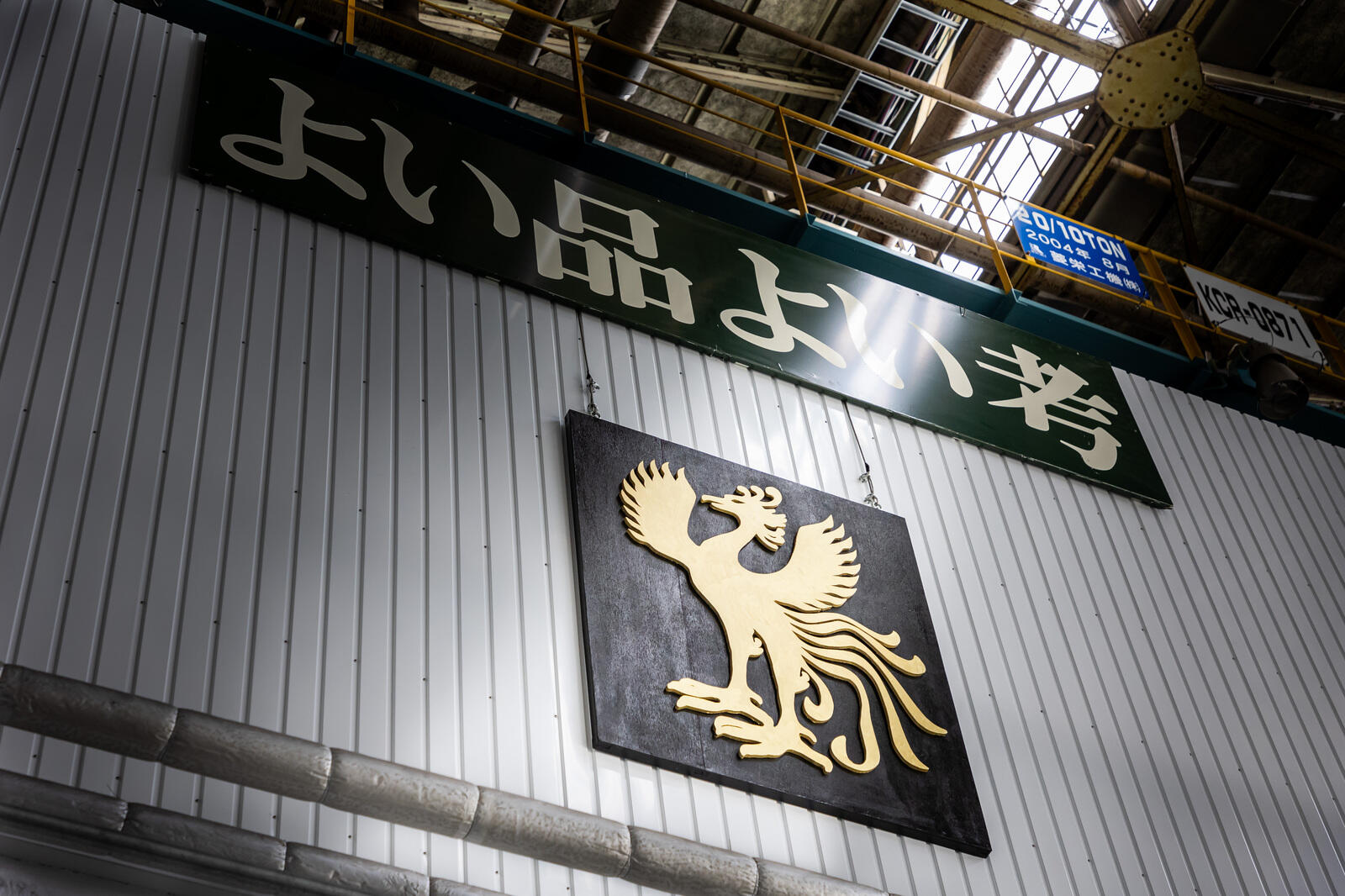
Toyota Times visited the workshop where the Century is painted for this article. We were greeted by the body of a Century, standing majestically in the brightly lit space, and a worker wearing a cleanroom suit with an eye-catching phoenix on the chest.
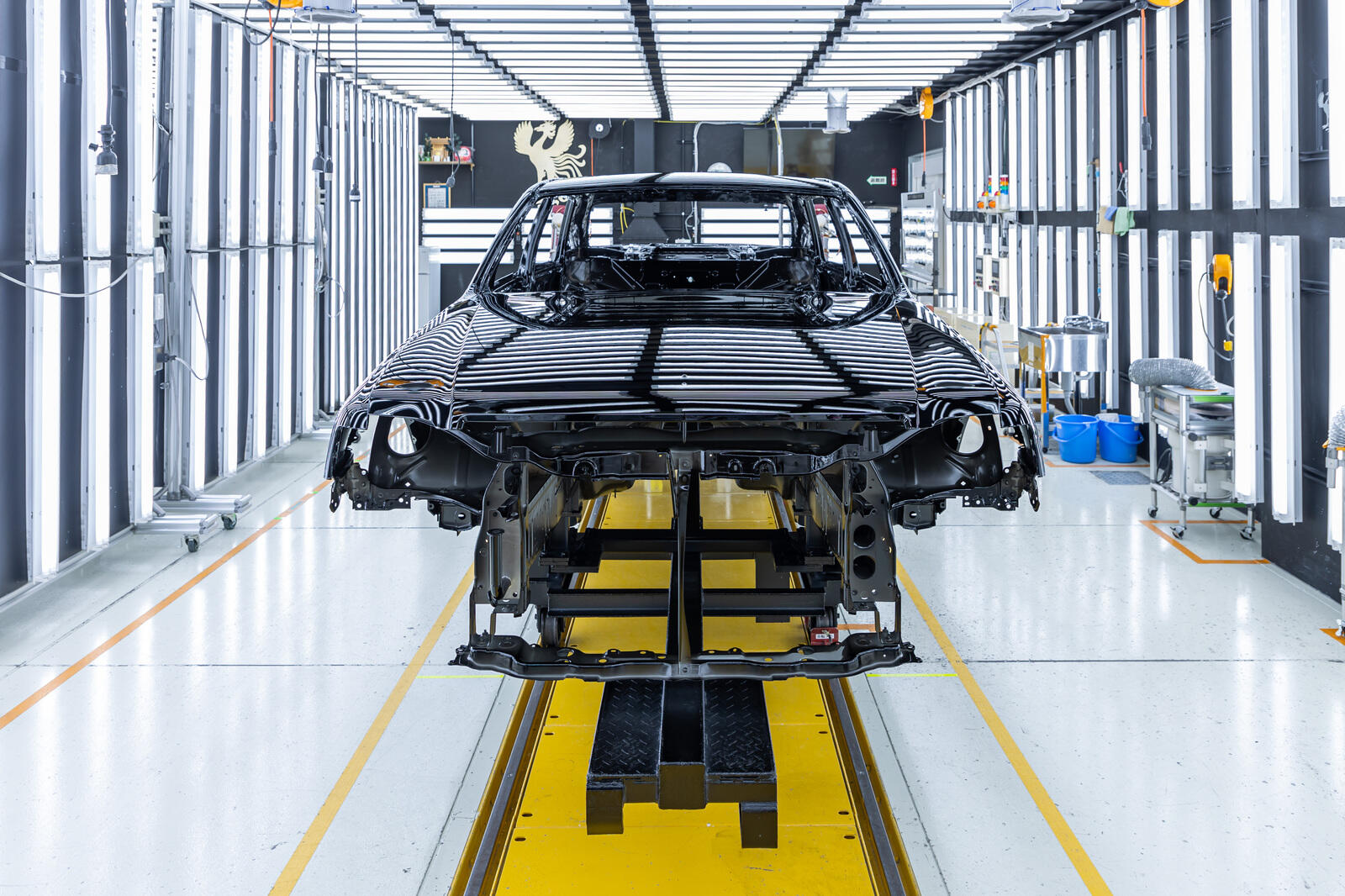
Masami Yunoki, group leader of the Surface Finishing & Plastic Division’s Painting Section, was part of a small group that spent time at the Toyota Motor East Japan (TMEJ) Higashi-Fuji Plant, which originally produced the Century, inheriting its spirit and the necessary skills.
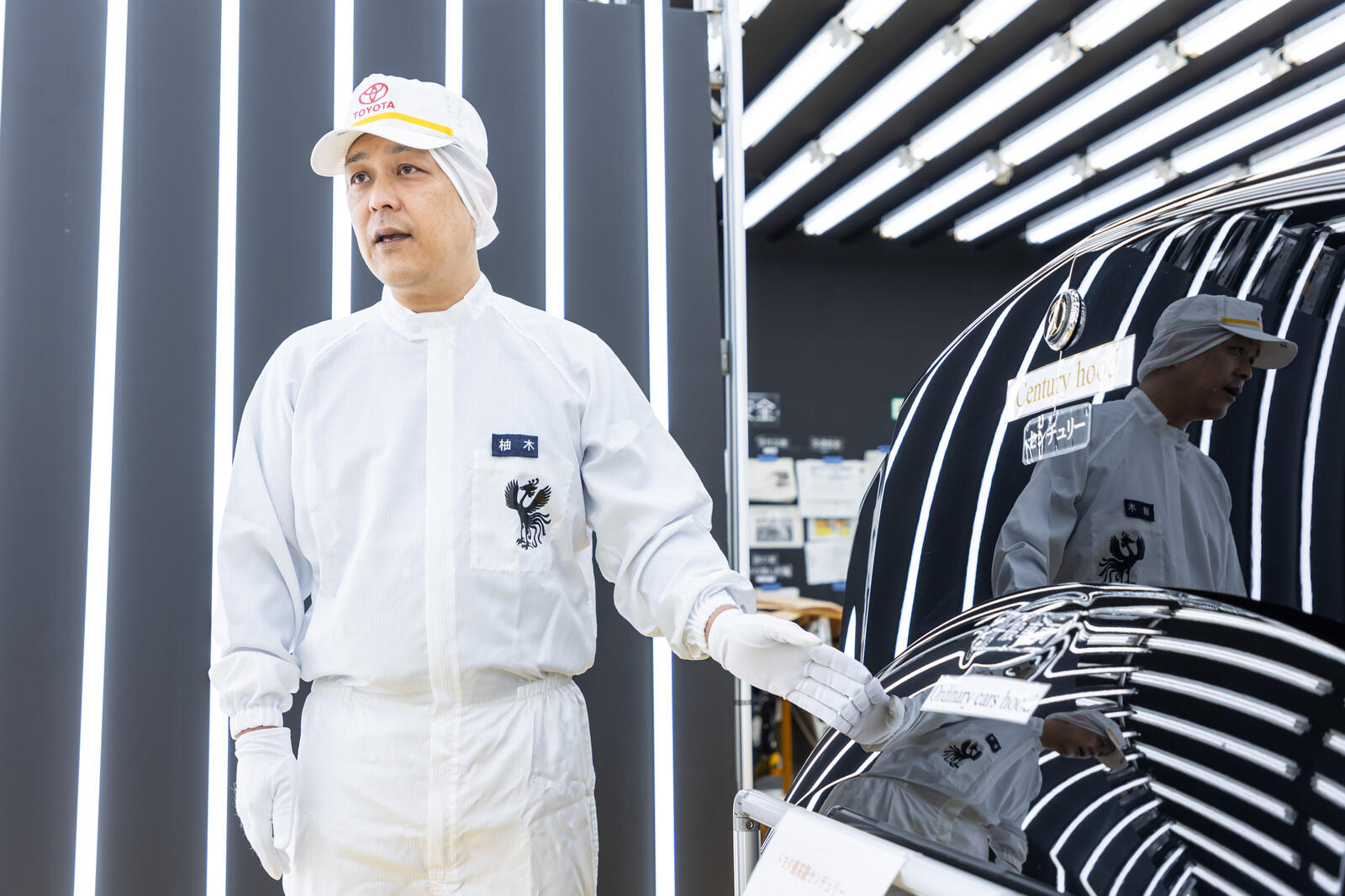
One quality that distinguishes the Century from other cars is the “surface grade,” referring to the beautiful finish of the vehicle’s body. The standard for the Century is a rank of five, which requires that painted surfaces reflect light without distortion, meaning the body can act like a mirror.
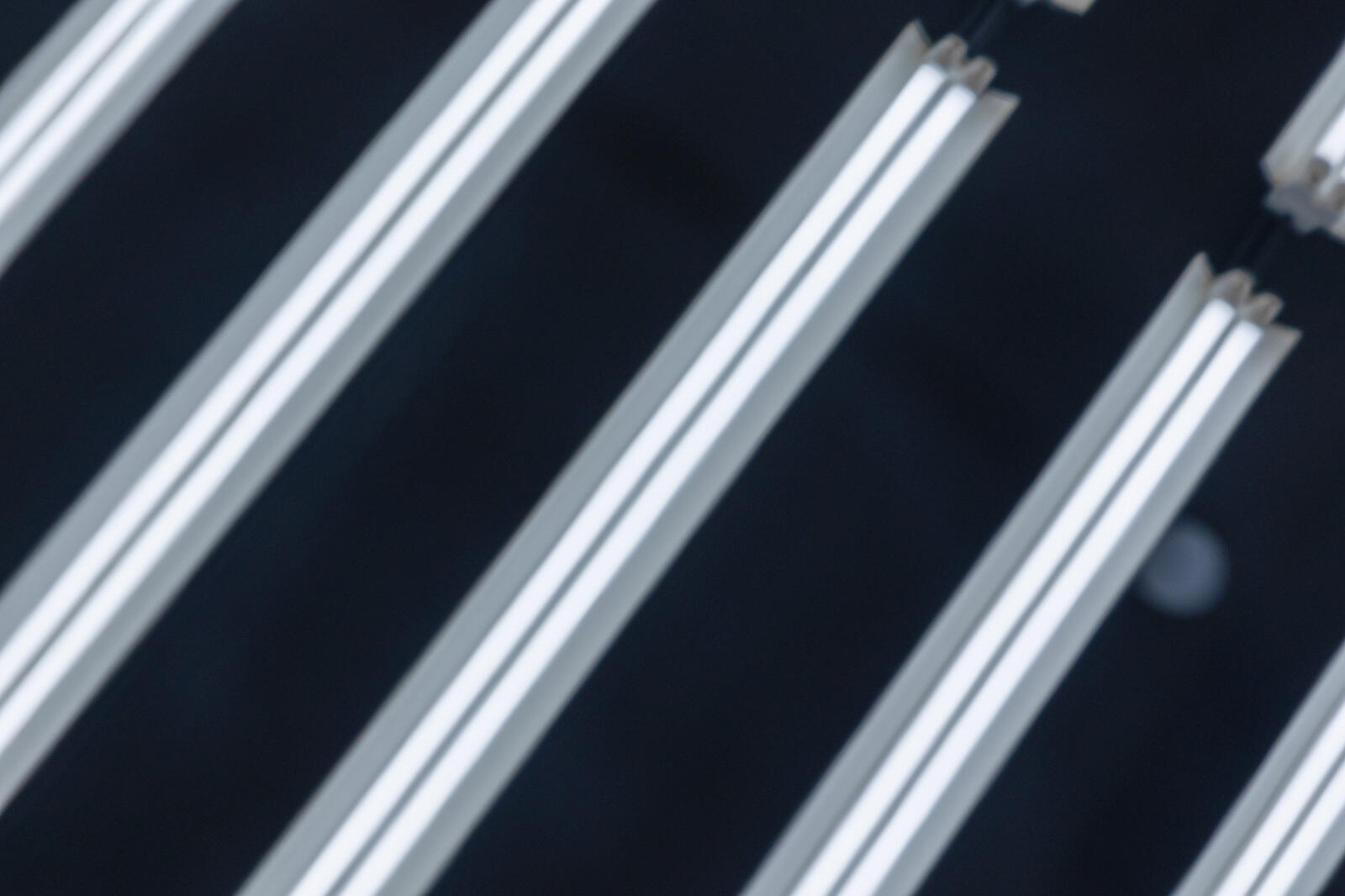
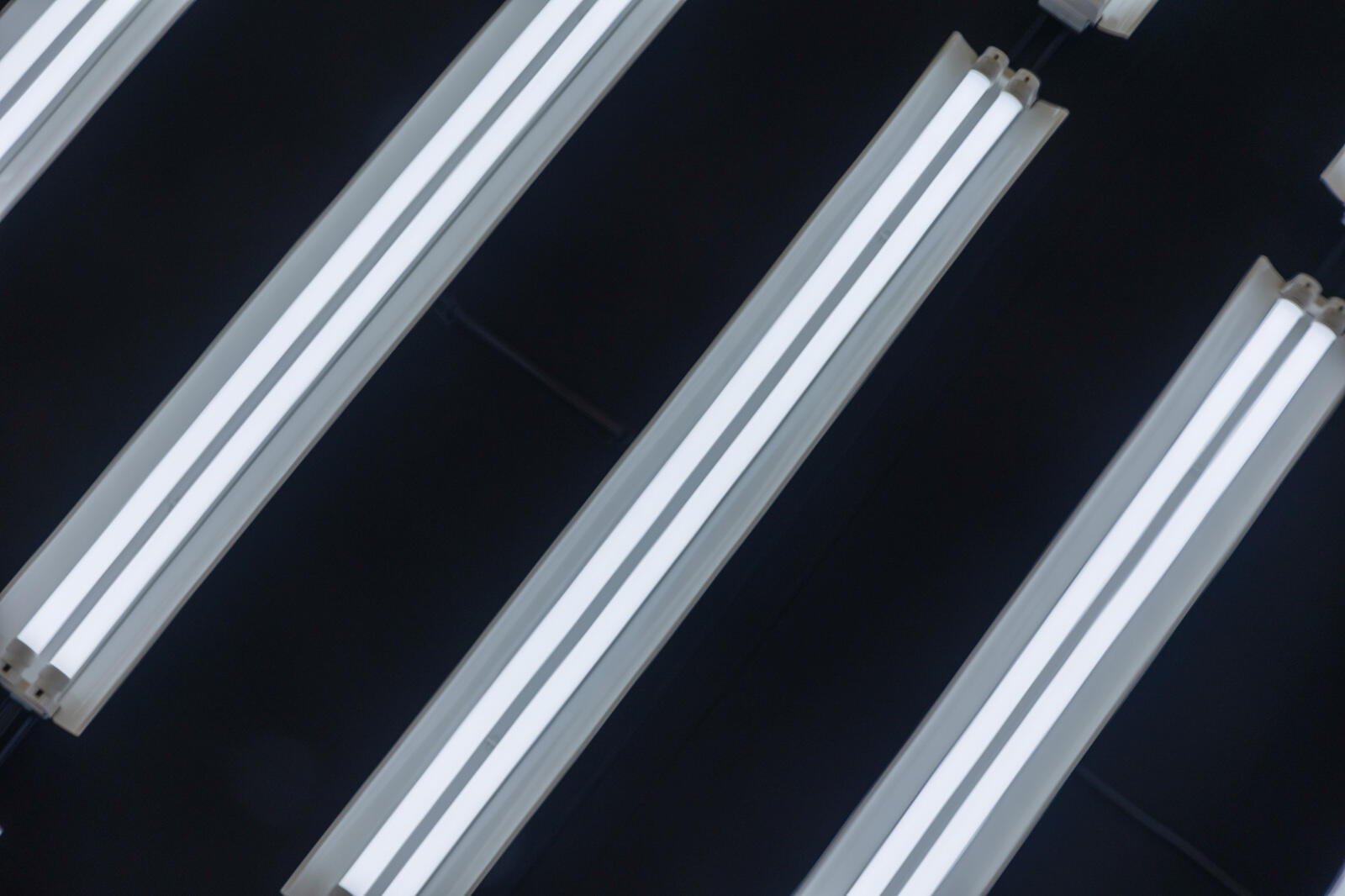
To achieve this, the Century's painting process consists of seven steps (i.e. seven layers), compared to four steps/layers for ordinary vehicles.
The only step performed on the mass-production line before the car arrives at the workshop is electrodeposition coating, to prevent rusting. After the middle coat is applied, the entire body is wet sanded under running water.
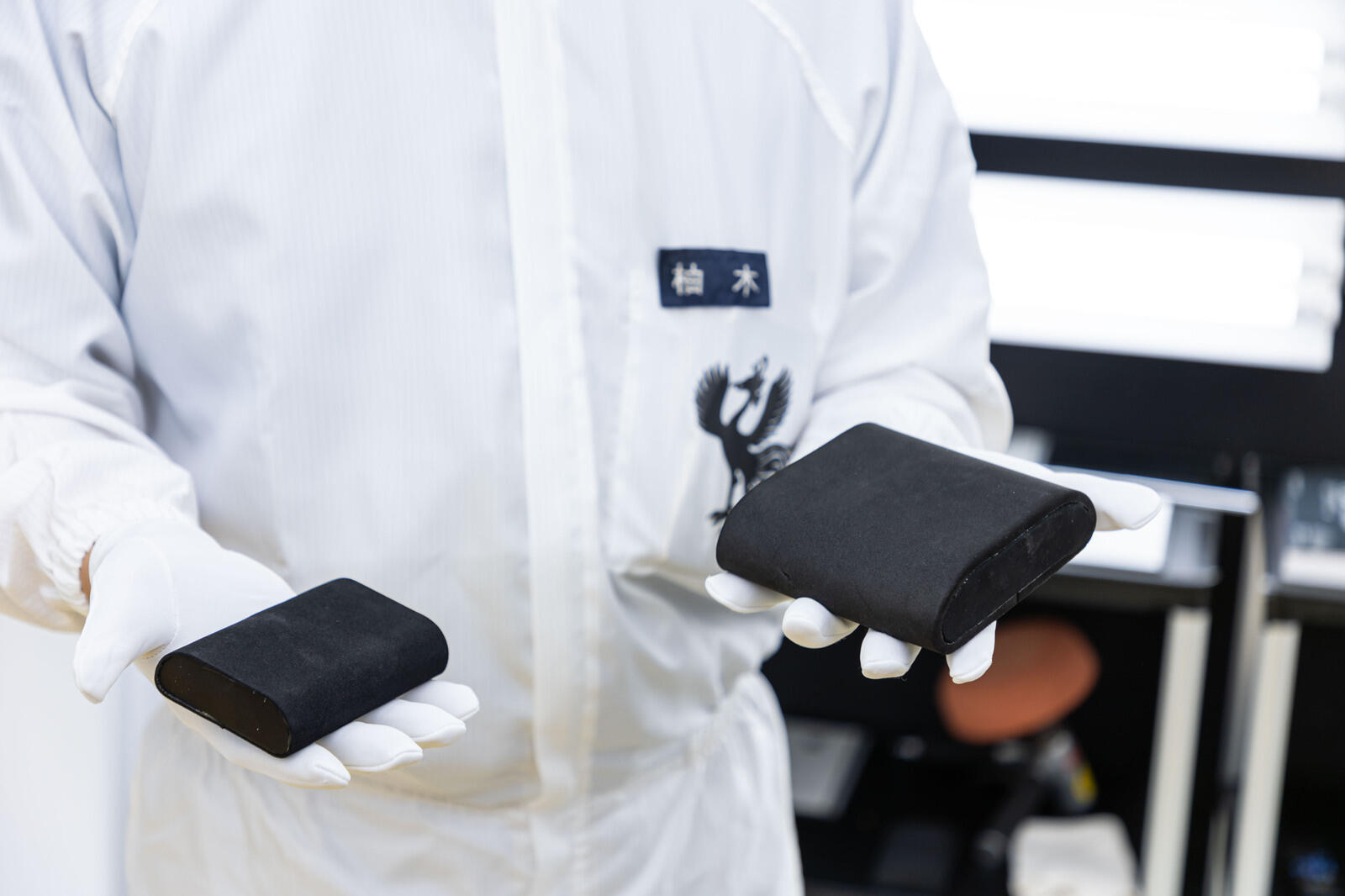
Once all of the painting is complete, the entire surface undergoes another three hours of wet sanding.
Yunoki recalls how, during his time at TMEJ, one of the plant’s takumi could tell that he wasn’t polishing properly simply by hearing him work.
Apparently, the sound reveals whether someone is firmly putting their weight into the polishing.
A sign in the workshop lists four guidelines, including “Deliver beauty, even in parts not visible to the customer” and “Do not base decisions on specifications.” They lay out the Century mindset as inherited from TMEJ, reflecting the skills and spirit of monozukuri.
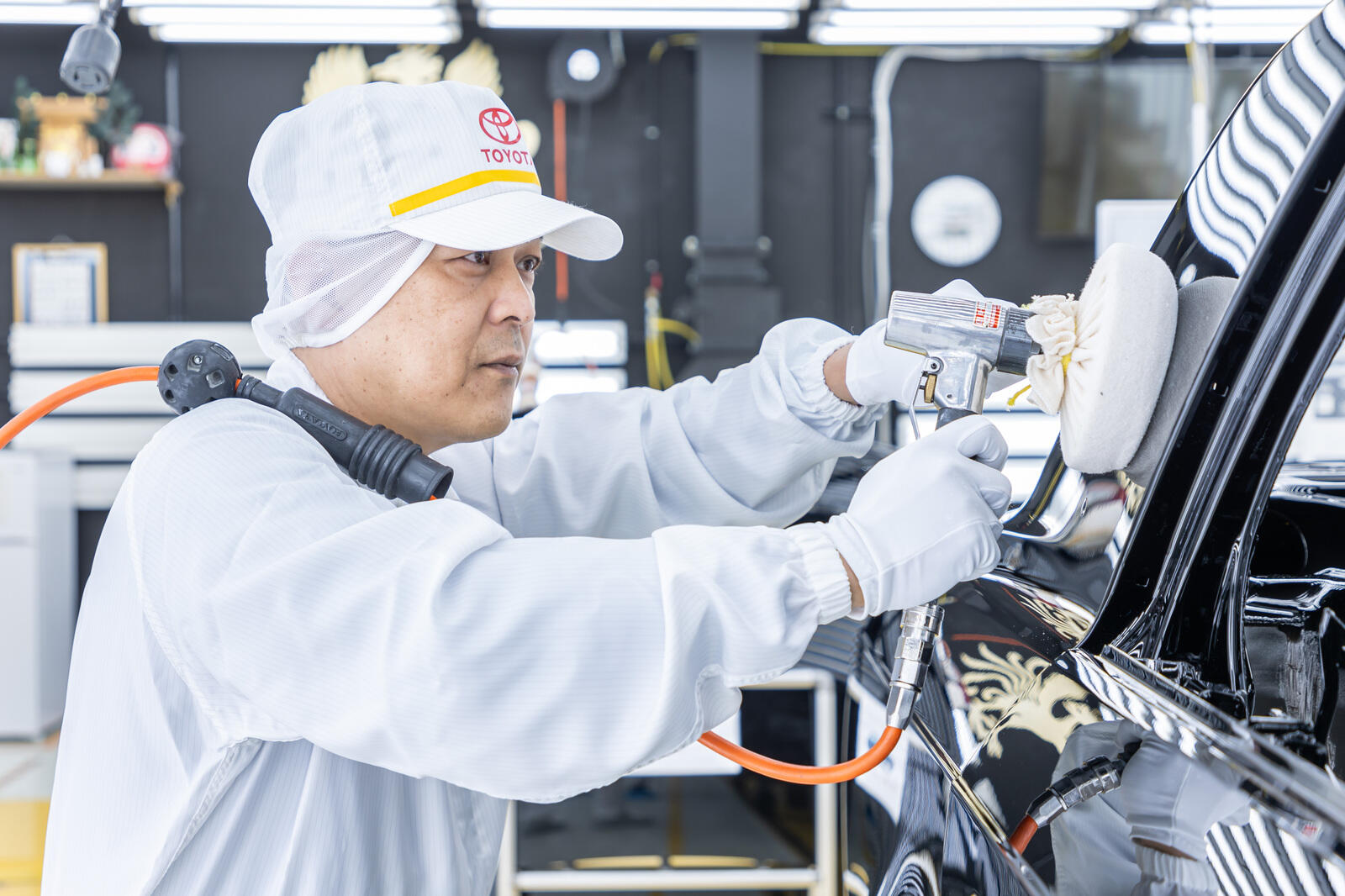