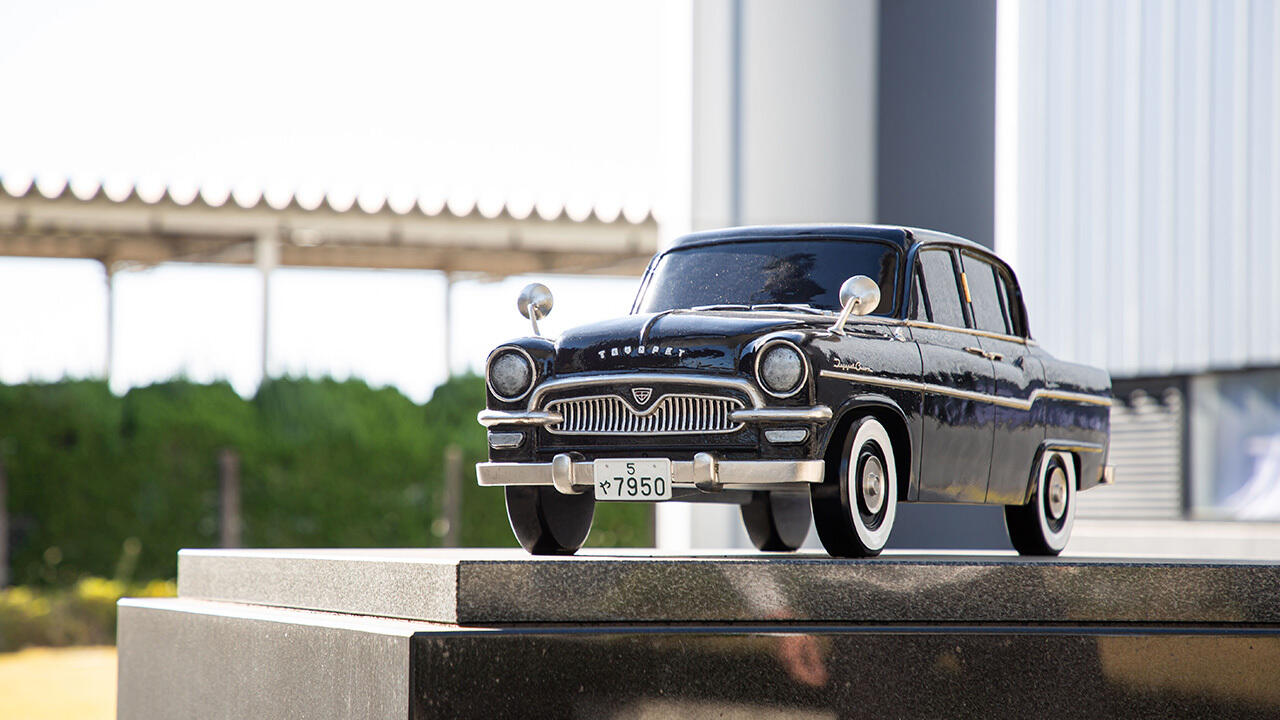
In the five years since 2020, Toyota's Motomachi Plant has launched 15 different car models. We unravel the plant's history to see how its unique spirit and skills have been passed down to this day.
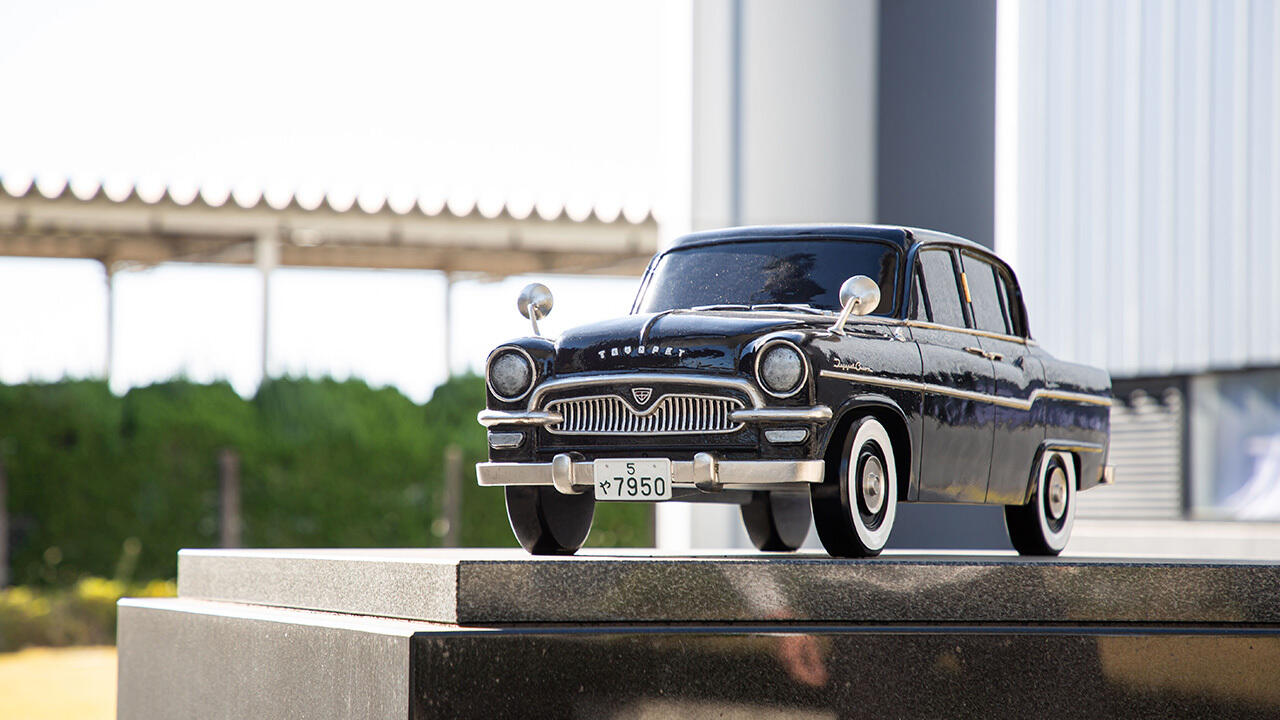
Cornerstone of the company
Do you know how the Motomachi Plant got its name? Yes, the facility’s address is 1 Motomachi, Toyota City, Aichi Prefecture. But that is not its origin story.
Machi kouba are the small factories and workshops found in towns around Japan, while the word “moto” can mean both “former” and “origin” or “source.” Hence, the name Motomachi honors the company’s starting point as a small-scale local operation, while also reflecting the plant’s role as the cornerstone of Toyota’s development.
In this article, we trace the Motomachi Plant’s unbroken trajectory to this day.
The “reckless” endeavor of Asia’s first dedicated passenger car plant
In January 1955, the Crown became Japan’s first truly homegrown passenger car.
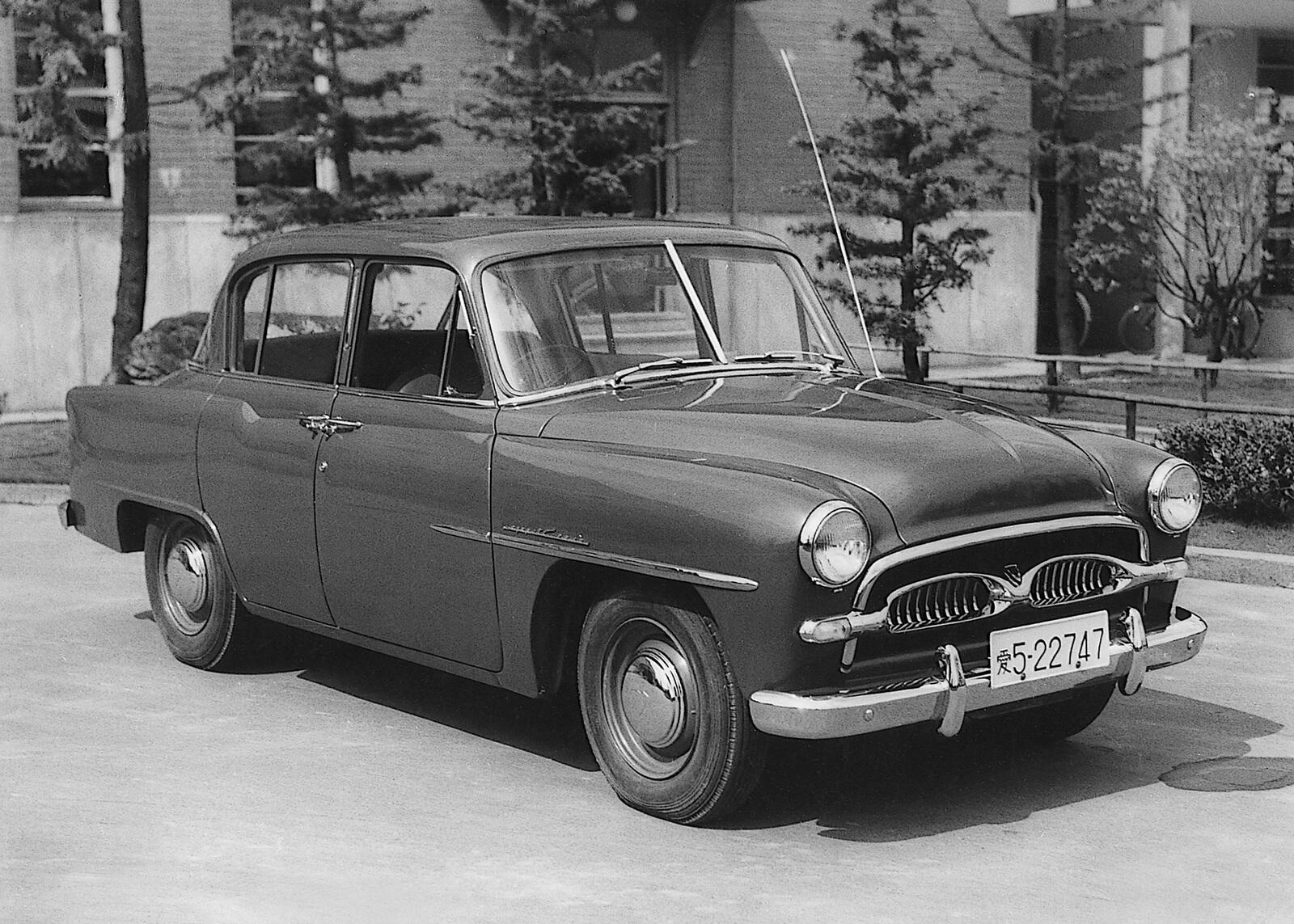
“With Japanese ideas and skills, we must create an automobile industry for Japan.” After discovering the potential of automobiles in America, Toyota founder Kiichiro Toyoda was determined to help his country grow through carmaking.
This car, the culmination of Toyoda’s long-held dream, cost around 12.5 times the average annual income at the time. Despite this, it proved so popular in Japan that supply sometimes could not keep up with demand amid the country’s need for taxis, hire cars, and other commercial vehicles.
Observing these developments, Toyota’s leaders set out to build the first dedicated passenger car plant in Asia. Eiji Toyoda, the company’s fifth president, later reflected on the decision.
“Construction of the plant was a big gamble that would either pay off handsomely or ruin us. Had we lost the gamble, we probably would have fallen on hard times again (note: as in the postwar period).”
From Toyota: Fifty Years in Motion, by Eiji Toyoda
In the late 1950s, Toyota was selling 2,000 Crowns a month. Meanwhile, initial plans for the plant would give it a monthly production capacity of 10,000 vehicles. Given how far this figure outstripped existing sales, however, the facility instead started off making 5,000 cars per month, while leaving room to expand capacity later.
Construction costs totaled 2.3 billion yen. Wagering such a vast sum of money on the country’s first dedicated passenger car plant could well be regarded as a reckless endeavor.
The chosen location was about 2.5 kilometers northwest of Toyota’s Koromo Plant (now the Honsha Plant), on the site of the former Tokai Hikoki Koromo Plant in Tsuchihashi.
During World War II, the Japanese government purchased some 660,000 square meters of land for Tokai, an aircraft maker, roughly half of which was secured by Toyota during the first phase of construction.
In July 1958, a construction committee was formed for the tentatively named Tsuchihashi Plant, headed by Shoichiro Toyoda, then a 33-year-old director. He noted the following in his autobiography:
“Building our first dedicated passenger car plant raised a succession of difficult problems, but we solved each in turn by drawing on the ingenuity of the Obayashi Corporation, Ito Koumuten, and the other companies that assisted with equipment and machinery … Although I received advice from Eiji and other colleagues, in the end they told me, ‘You are in charge, do it your way,’ which gave me the courage to get the job done on my own terms.”
From Mirai wo Shinji Ippo Zutsu [Step by Step, Believing in the Future], by Shoichiro Toyoda (published in Japanese only)
When the purchased government land proved insufficient, local authorities offered Toyota the adjoining persimmon groves.
Through the efforts of the young committee chairman, greatly assisted by building contractors and the local community, the first phase of construction was completed with remarkable speed in August 1959. Merely 11 months after work began, the plant commenced operations.
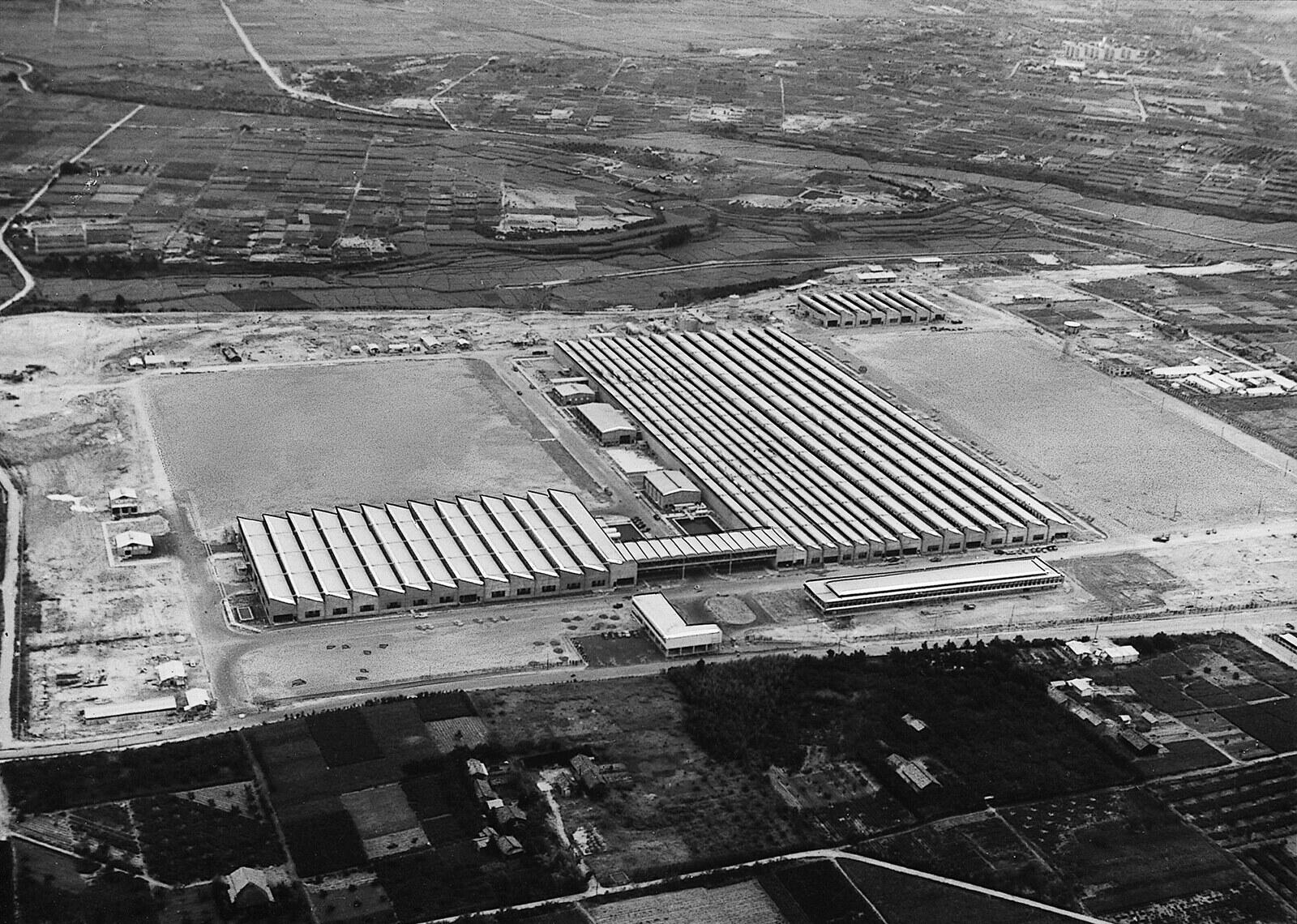
The opening of the Motomachi Plant was a major step, ensuring Toyota stood out from the pack among Japanese carmakers.
Frustrated ambitions
Starting with the Crown, the Motomachi Plant went on to produce the Corona, Publica, and Mark II, with annual volumes steadily increasing to a peak of 444,560 vehicles in 1990.
In its results for the fiscal year ending that June, Toyota posted record profits of 733.8 billion yen (non-consolidated).
In that same period, however, Japan’s economic bubble burst. Weighed down by fixed costs, Toyota’s outlays on materials and labor came to exceed sales growth, and profits began to decline the following year.
What’s more, whereas luxury models and large cars had previously flourished, with sedans accounting for 70% of the passenger car market, their popularity now plummeted amid an RV boom led by younger customers.
These changes dealt a heavy blow to the Motomachi Plant’s production figures.
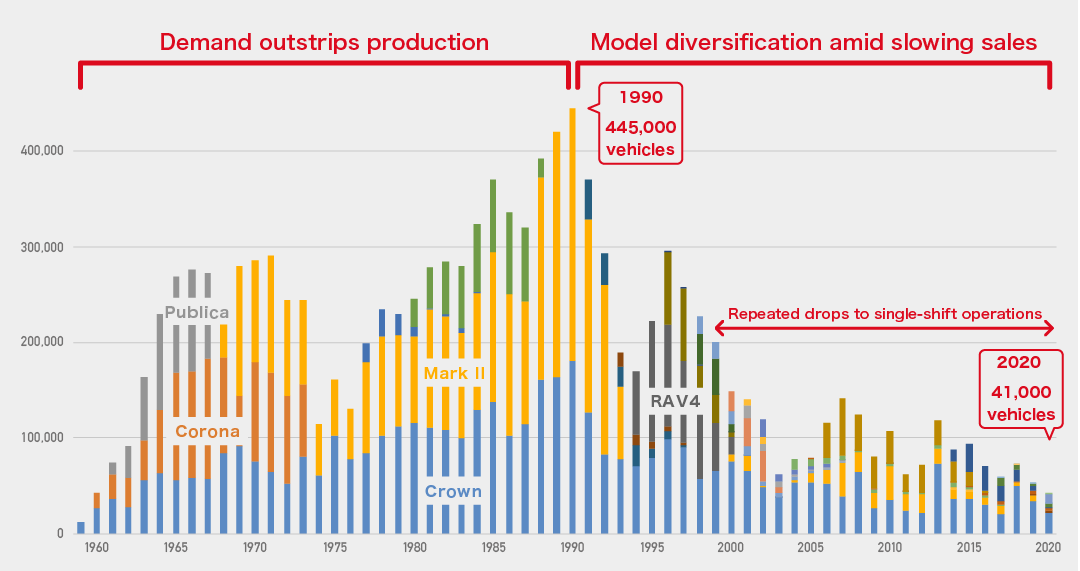
With no cars to make, there was no work to be done. Day by day, the plant’s team members were transferred to other plants making cars that sold well. Motomachi found itself with excess capacity, and for roughly two decades starting around 2000 the plant could not consistently sustain a two-shift roster, instead alternating between one- and two-shift operations.
Deputy Plant General Manager Masahiko Ishihashi was born and raised in Toyota City and has spent his entire 46-year career with Toyota at Motomachi. He remembers the plant during that period.
Masahiko Ishihashi, Deputy Plant General Manager
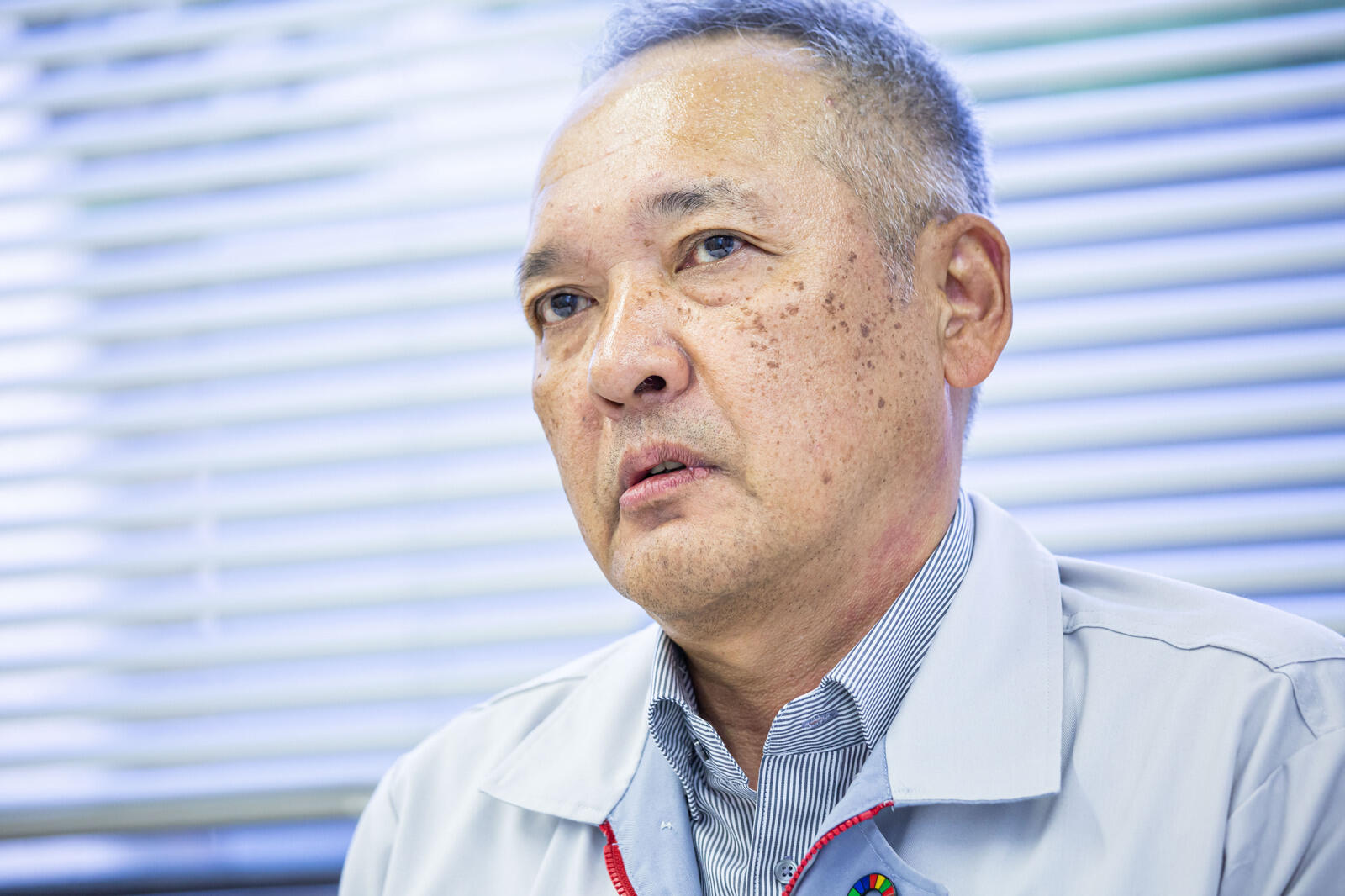
After peaking at 445,000 vehicles in 1990, our production volume fell to just 50,000 cars. With no work to do, our colleagues moved on to other plants.
We were determined to stay together and do whatever it took to maintain two shifts. We honed our skills, and said, “We will make anything, no matter how difficult the car.” This helped us gain vehicles to produce.
Today, the plant lineup includes FCEVs (fuel cell electric vehicles) and BEVs (electric vehicles), and our production volume is finally back up to around 150,000 cars. We’re also able to run two shifts.
Such is the history behind the high-mix, low-volume production that is a key feature of the Motomachi Plant. Between 2020 and 2024, it was able to launch 15 new models.
As Ishihashi explains, one important factor behind this endeavor is the presence of the manufacturing engineering team, which is concentrated in Motomachi.
Masahiko Ishihashi, Deputy Plant General Manager
Manufacturing engineering (which sets up new production lines) is nearby, and they help us to get the ball rolling on new things. While the numbers may be small, we start by getting products out into the world, and then other plants that are strong in mass production increase the volume. To begin, we don’t know whether something will sell, and Motomachi is the plant that takes this initial ‘wager.’ Perhaps we retain the spirit of earlier generations.
The efforts undertaken at Motomachi have spread to other facilities, becoming a cornerstone of growth for the whole company. The plant’s founding vision is still going strong.