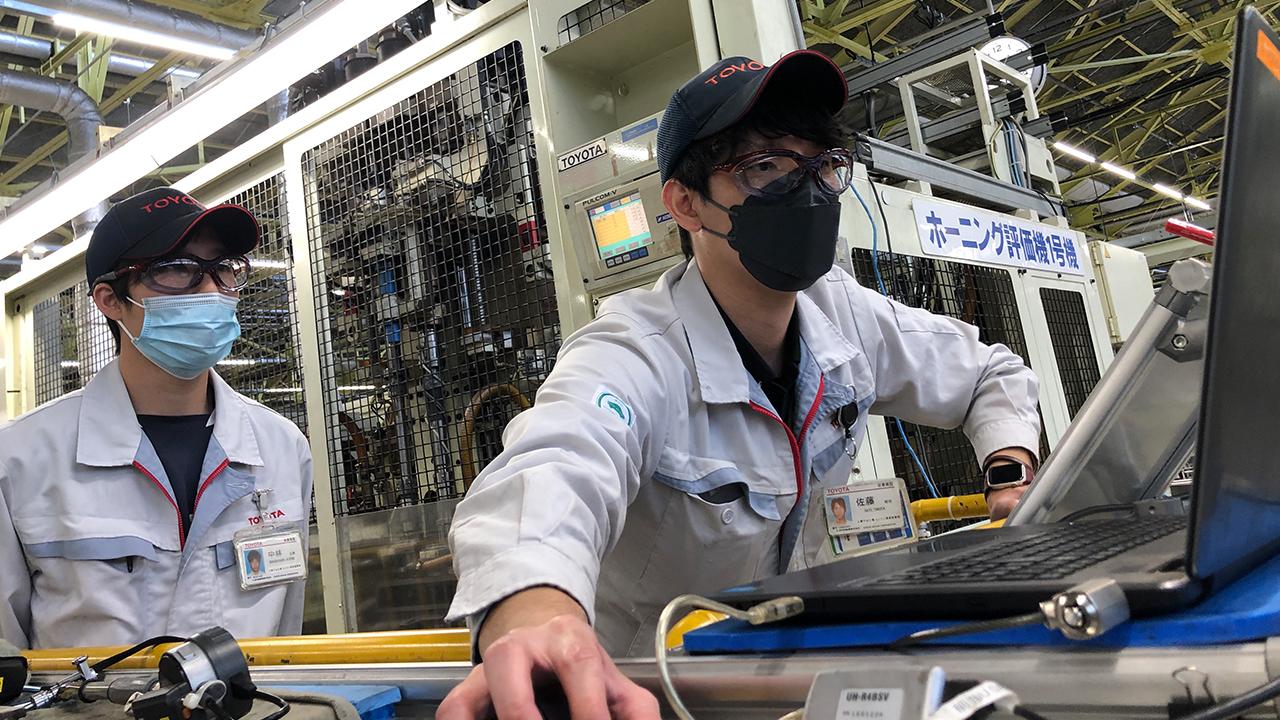
This series explores the project to restore a first-generation Crown, a car that embodies Toyota's origins. The second half of the eighth edition focuses on the team that harnessed cutting-edge fabrication technologies to give the restored engine more power than the original.
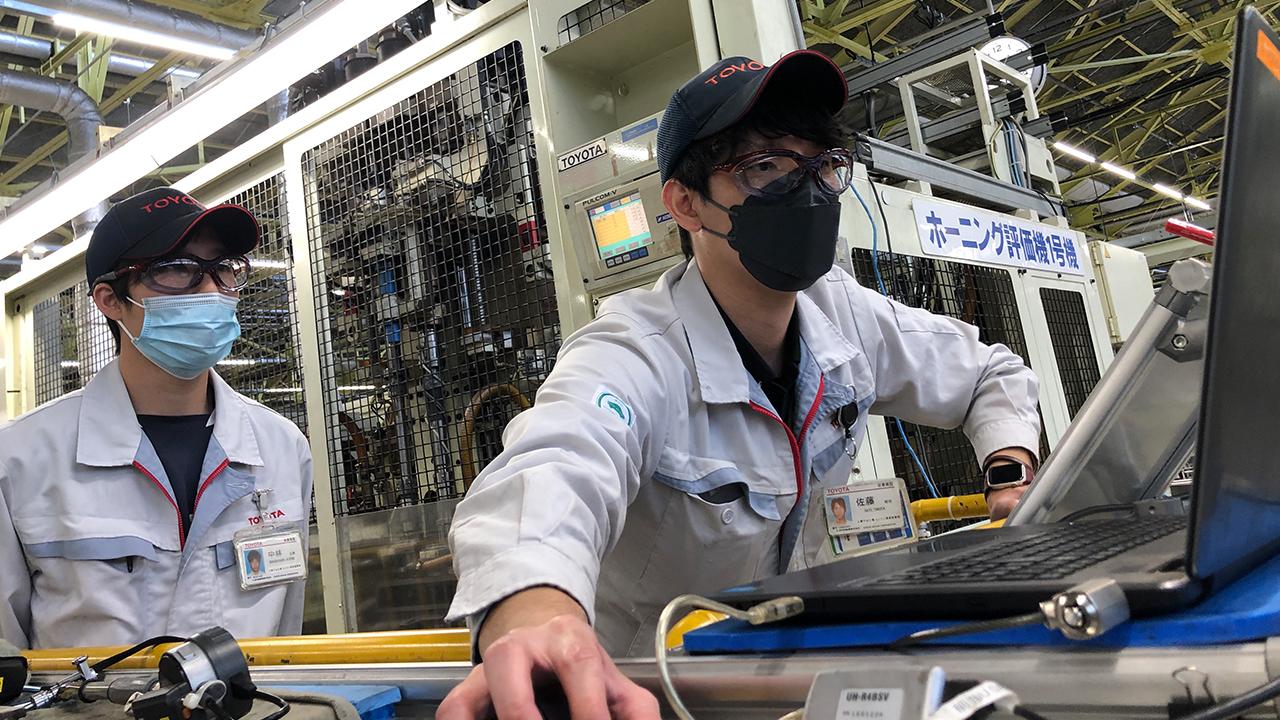
A project to restore a first-generation Crown started at the Motomachi Plant in the spring of 2022, bringing together a diverse group of skilled members.
This series closes in on their restoration efforts. In the second half of the eighth edition, we track the efforts of the Kamigo Plant/Shimoyama Plant Engine Manufacturing Engineering Division’s honing team, which harnessed state-of-the-art honing techniques to completely restore the engine, giving it a great sound and power to surpass the original.
“Abnormal wear” on cylinder bores
As mentioned in the first half, the engine team faced various problems, but abnormal cylinder wear presented the most difficult challenge.
After pulling the engine apart completely and closely inspecting the dismantled pistons, piston rings, and oil rings, the team found several surfaces covered with extensive scratches and carbon sludge (black soot).
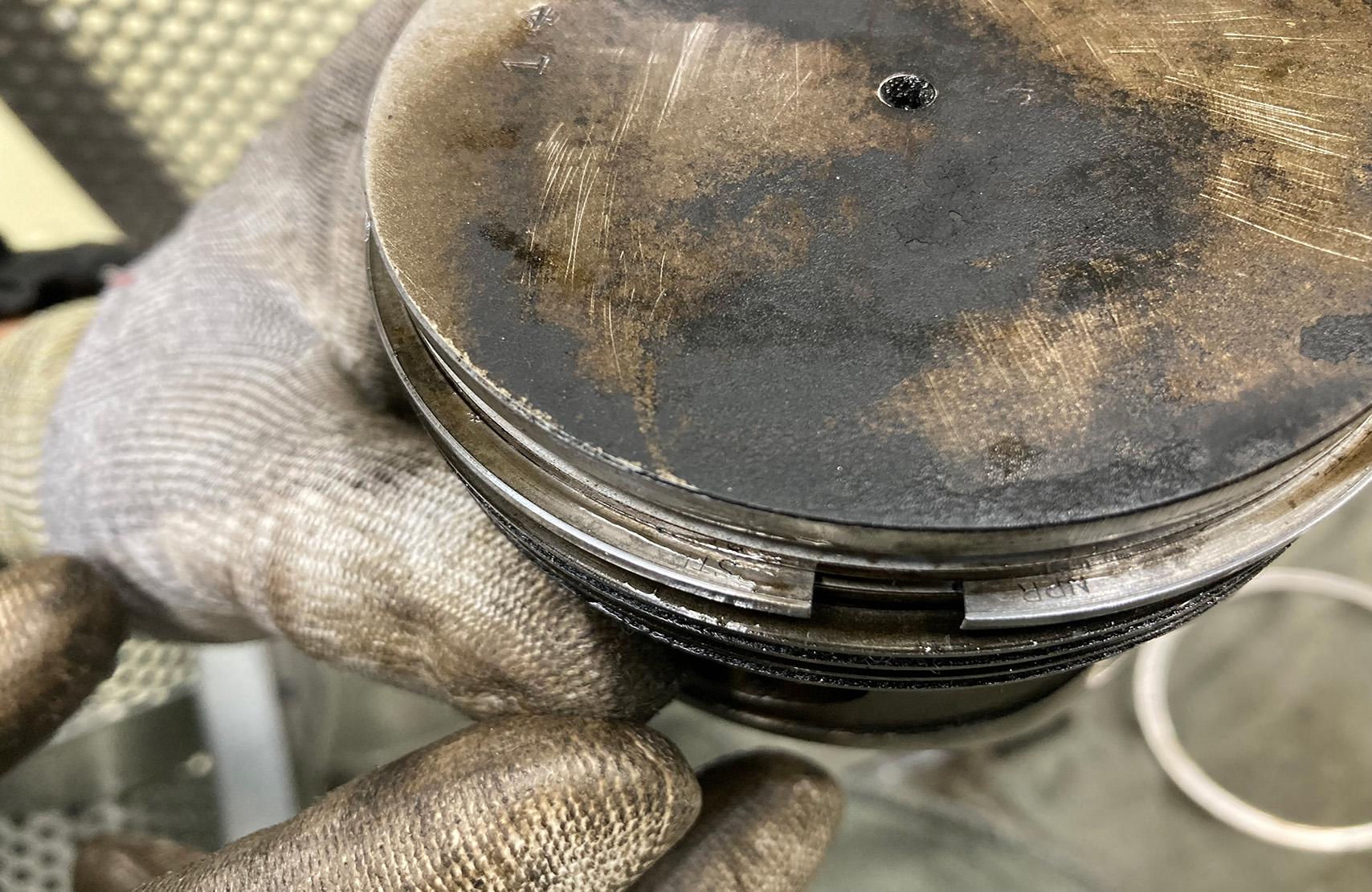
This is a symptom of poor engine cooling, leading to abnormal wear as the oil cannot properly lubricate the pistons and cylinders.
As things stood, the engine would not run correctly even with new pistons and piston rings.
The team members were left scratching their heads. As we explained in the first half, this engine showed signs of having overheated multiple times. Besides new pistons, piston rings, and oil rings, the abnormally worn cylinder inner walls would have to be reconditioned.
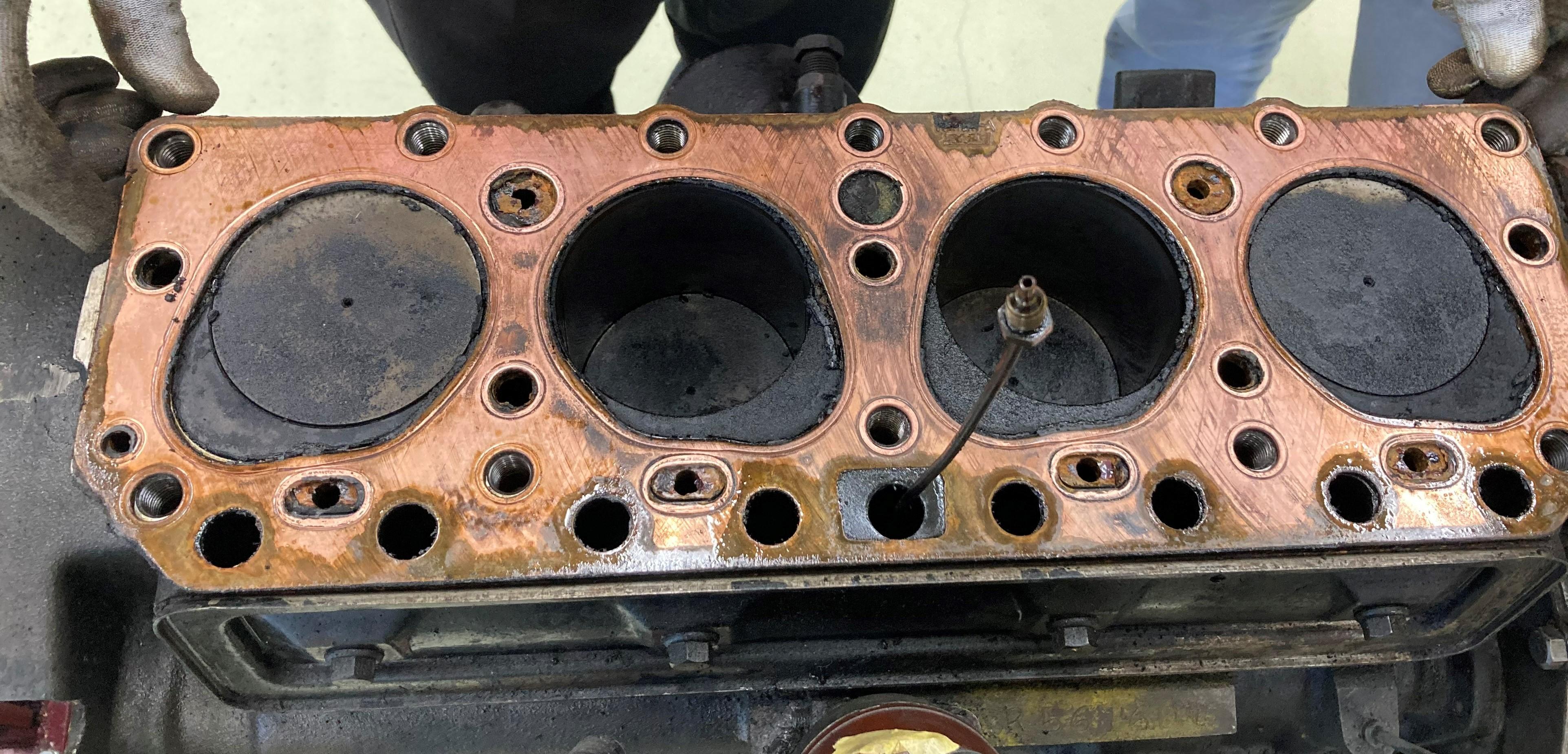
Incidentally, the standard solution for an engine that had overheated repeatedly would be to replace the whole thing. This is because overheating often causes engine blocks to deform, leading to coolant or oil leaks.
However, for this restoration, there were no spares—after all, these engines were built 70 years ago. The team had no choice but to somehow refurbish the cylinders to get the engine running normally again.
Honing the cylinder bores
In the end, to bring this old engine back to life, the team drew on the most up-to-date technology and expertise that Toyota has to offer—cylinder bore honing.
While honing generally refers to the process of sharpening a blade, in the case of an engine cylinder, it means using a honing machine to create a precision finish on the cylindrical inner surface
More specifically, with the engine block secured in the machine, various grinding stones are fitted to the honing head and rotated as they move in and out of the cylinders, polishing the inner walls to the required shape at a micron level. This delicate process determines an engine’s overall performance and can be regarded as the cornerstone of engine manufacturing technology.
Incidentally, engine bores can also be machined through a different process, known as “boring,” which involves more significant cutting of the cylinder’s wall surface to 0.1-mm precision. This is done when the cylinder walls are too heavily scarred for the engine block to be usable.
In some cases, cylinders are “overbored” to increase their diameter and volume as a way to increase engine displacement and thus boost power output. Honing, however, is a much more intricate process.
Honing a cylinder bore is about more than simply grinding the wall to eliminate unevenness and make it smooth.
As a piston travels up and down the cylinder at high speeds, it is aided by a layer of engine oil formed on the cylinder wall. This film serves as lubrication, ensuring the piston and piston rings can move smoothly without directly touching the cylinder bore.
To enable this, the cylinder bore should not have a perfectly slick surface but rather a degree of unevenness or roughness that enables it to sufficiently retain engine oil.
On the other hand, if the cylinder bore surface is too rough, the piston ring cannot achieve a close fit, leading to gaps between the ring and cylinder bore.
These gaps may cause a blow-by, where combustion gases flow into the crankcase and degrade the engine oil or allow the oil itself to enter the combustion chamber.
When this happens, any excess oil remaining on the cylinder bore surface will burn as it comes into contact with the high-temperature combustion gases. This, in turn, can lead to fatal engine problems, such as pistons seizing up due to burnt residue on the bore surface or white smoke from the burned engine oil mixing with exhaust gases. The resulting soot and smoke interfere with the function of various parts, including the catalysts that clean exhaust emissions.
In other words, cylinder bores must have an ideal roughness that enables the piston rings and oil rings to seal tightly, yet with enough unevenness to retain a micron-level film of oil on the surface. Achieving this allows the engine to reach peak performance and durability.
World-leading honing specialists
This delicate task fell to the honing team—EX (expert) Takuya Sato and Hiromu Nakabayashi, led by Assistant Manager Takayuki Miwa—working under Resident Engineering Consolidation Section Manager Takayuki Okada (Kamigo Plant/Shimoyama Plant Engine Manufacturing Engineering Division). As honing experts, they have visited engine plants around the world to share their knowledge.
Miwa
With honing, the bore surface finish depends entirely on a combination of two factors: the condition of the surface (i.e., the form, roughness, and hardness) prior to machining and the cutting ability of the selected grinding stone. This time we only got one shot at it, no test runs. It gave me the greatest pleasure to be involved in this project, using our technology and know-how to help restore the historic first-generation Crown.
In their state-of-the-art honing process, the team controls surface roughness at the micron level (1 micron = 1/1000 mm).
The engine block is set in a honing machine developed in-house at Toyota. A cylindrical tool fitted with the grindstone is inserted into the cylinder. With grinding coolant flowing, this rotating tool moves up and down while pressed against the cylinder bore surface, finely grinding the bore with micron-level precision.
Okada
The rotary tool that houses the grindstone also has a sensor that serves as a torque meter. Information from that sensor shows us the cutting load that is currently being applied to the cylinder bore surface during machining.
Led by Assistant Manager Miwa, the team verified the relationship between this cutting load and machining precision, ensuring we maintained both a quality finish and the grindstone’s cutting ability throughout. They constantly evolved their methods to handle all the changes in the engine block.
The team also uses three different types of grindstones on the rotary tools: diamond, CBN (cubic boron nitride), and WA (white aluminum oxide grit). All three types and their rotary tools were on display in the workshop, along with sample engine blocks both before and after machining, albeit from current vehicles.
Up close, the difference in cylinder bore surfaces before and after honing is clear to see.If you look carefully, the “before” surface is streaked with fine lines made by the cutting tools, while the “after” sample gleams and shines, almost mirror-like.
Miwa
Just as in the previous first-generation Publica restoration, because there are no spare engine blocks, we need to minimize the depth of surface machining. This time around, we again needed to achieve the ideal finish while keeping machining to a minimum.
As for the fruits of this honing process, those who gathered to see the Type R engine fired up for the first time post-restoration were given the full experience. The smooth purr sounded like no other Type R engine the team members had heard before. What’s more, the engine also exceeded expectations in terms of power.
Given the history of gasoline engines, this comes as no surprise. The engines of 70 years ago—when the first-generation Crown arrived—used different materials and designs than today, and the precision machining technologies for cylinder bores paled in comparison to what we have now.
By harnessing these modern technologies, the team was able to make the Crown’s Type R engine run with an entirely new level of smoothness and power. This “ultimate restoration,” surpassing the original, could only be achieved by the car’s actual manufacturer, Toyota.
Amid the global push to electrify vehicles, unfortunately, engines tend to be disregarded as a technology of the past.
At the same time, these internal combustion engines have undergone more than a century of evolution, accompanied by dramatic advances in manufacturing technology. And honing technology is both the heart and the cutting edge of engine manufacturing.
If these technologies can be used on older engines to achieve previously unimaginable levels of performance, reliability, and durability, they will allow beloved vintage cars to remain on the road. By doing so, the technology opens a new chapter in the world of vehicle restoration.
(Text: Yasuhito Shibuya)