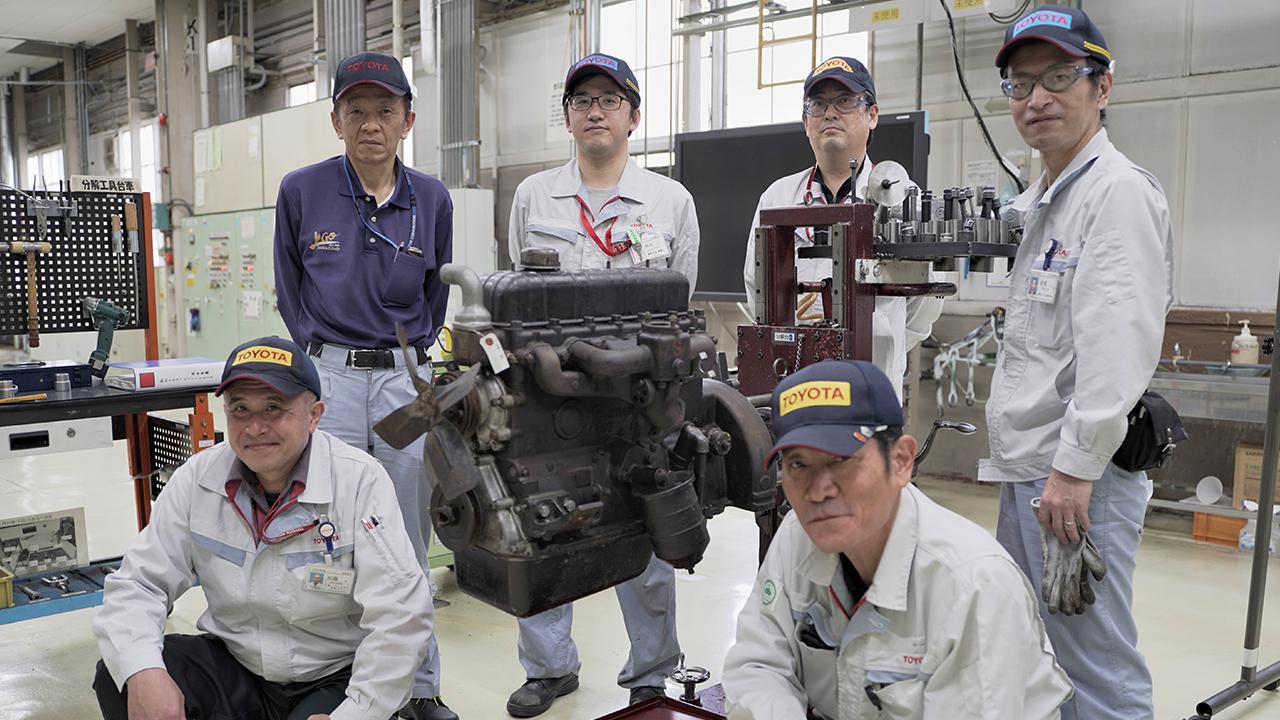
This series explores the project to restore a first-generation Crown, a car that embodies Toyota's origins. In the first half of the eighth edition, we showcase the team that pulled apart and rebuilt the engine down to the last screw.
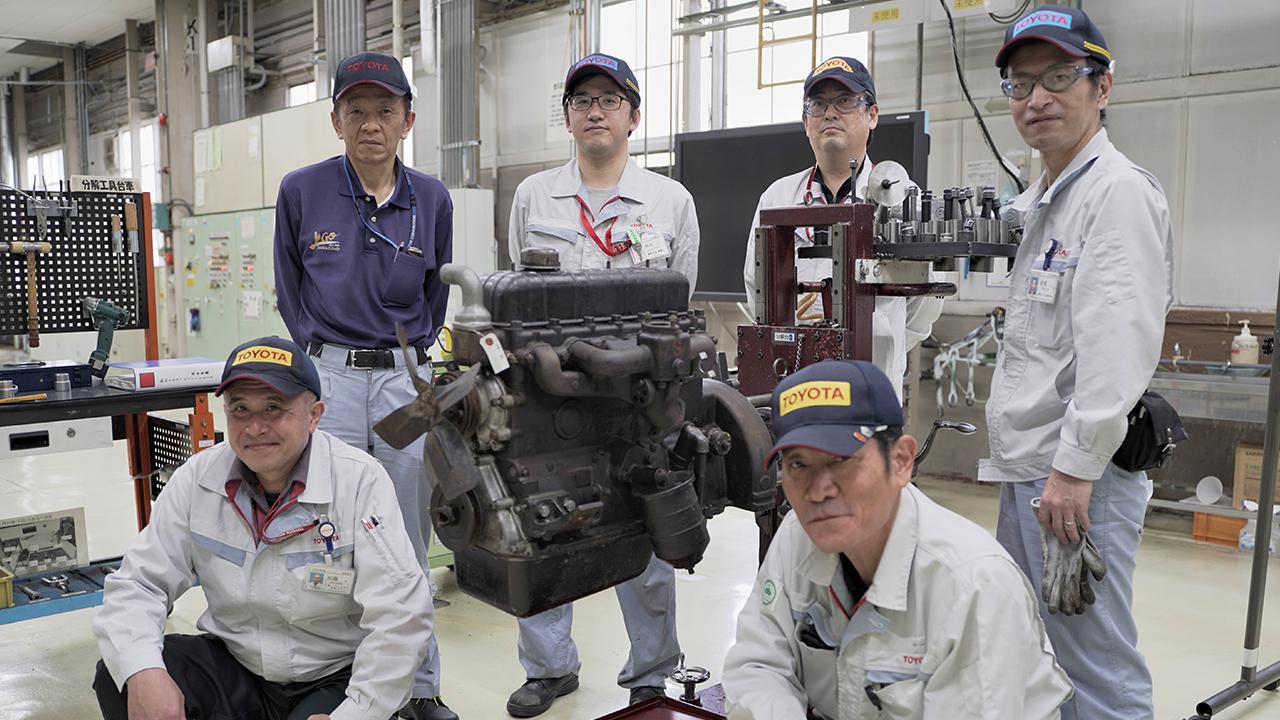
A project to restore a first-generation Crown started at the Motomachi Plant in the spring of 2022, bringing together a diverse group of skilled members.
This series closes in on their restoration efforts. In the first half of the eighth edition, we catch up with the team responsible for the engine. We bring you the struggles they faced in disassembling the engine, checking its condition, and figuring out how to approach the restoration.
A mixture of model years
After the first-generation Crown’s engine was removed from the chassis, the task of restoring it fell to Toru Iwaki (Kamigo Plant/Shimoyama Plant, Quality Control Div.), Hiroshi Ito, Yasushi Kato (both of the Kamigo Plant/Shimoyama Plant, Technical Training Group), Masatake Makita (Tahara Plant, Engine Manufacturing Div.), and Shigeo Sonoda (Shimoyama Plant).
First, they set about completely stripping and cleaning the engine, down to the last screw.
This work also involved numbering and cataloging each part, then checking their specs and condition to pinpoint which could be used again and which would need to be made anew.
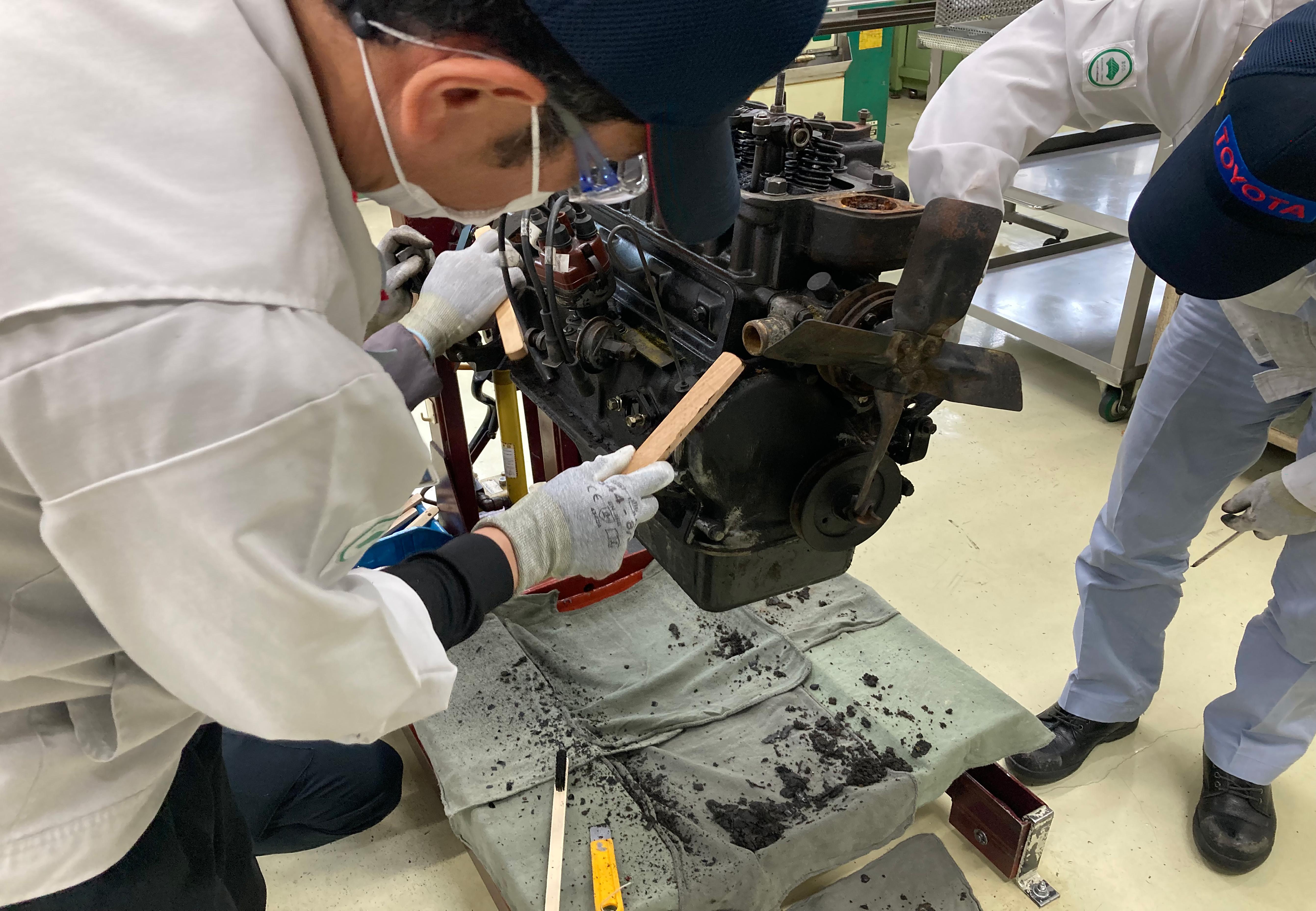

The first-generation Crown sported a Type R engine, which followed on from the Type S used in the Model SB truck in 1947. Development was completed in August 1952.
The Type R was a water-cooled inline four-cylinder 1453cc engine with an overhead valve (OHV) design in the tradition of the Type A, Toyota’s first mass-produced engine rolled out in 1935.
Initially, engineers had prototyped the Type P with the same side valve (SV) configuration as the Type S. In the pursuit of superior performance, however, they switched to an OHV engine, and the Type R was born.
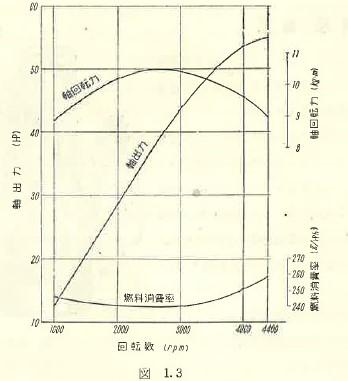
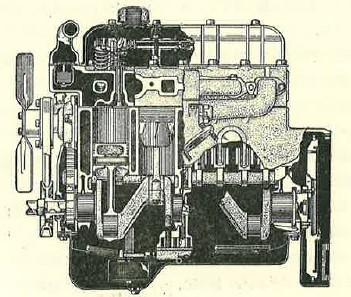
The Type R was nearly square, with a bore and stroke of 77 x 78 mm and a compression ratio of 6.8. It generated 48 horsepower at 4,000 rpm.
Delivering a 20-hp improvement on the Type S without impacting fuel economy, the new engine earned a great reputation in the Toyopet Super Model RH series of passenger cars. A production line completed in July 1953 could turn out 500 Type Rs per month.
The Crown was the car created specifically to carry this engine. Even after the first-generation Crown launched, engineers continued working on improvements to boost power. With a higher compression ratio and other refinements, the engine’s final version produced in 1962 reached a maximum output of 62 hp.
When the team dismantled this particular engine, they found signs that it had overheated several times over the past 70 or so years. Overheating is a serious problem that causes damage throughout the engine. As such, the team had to thoroughly check the condition of every component. In doing so, they instantly found an assortment of model years among the parts.
Iwaki
When we pulled the engine apart, we could see how hard the people who maintained it had worked to keep this Crown going.
From the design drawings, we knew that the engine had received frequent improvements to boost power output in its time. But the differences in specs exceeded our expectations.
Comparing the disassembled engine parts against the original drawings, we discovered a mix of components from different versions, including the cylinder block, crankshaft, cylinder head, camshafts, connecting rods, and intake manifold.
Sorting the usable from the unusable
The cylinder block, cylinder head, and camshafts were from 1956, and the crankshaft was from 1958. The connecting rods dated back to 1953, while the intake manifold was a 1955 model.
When this Crown was still on the road, the mechanics who looked after it had likely done whatever they could to procure the necessary parts and keep the engine in working order. That would have been the only way to keep it running for 70 years.
Team members individually labeled every dismantled part, identifying where it appeared on which year’s drawings. They then carefully checked which components could still be usable with some maintenance and which were beyond salvage.
Cars contain various parts that wear out and must be replaced during servicing. In the case of engines, this includes the gaskets, chiefly the head gasket, which seals the gap between the metal cylinder block and cylinder head, preventing cylinder pressure from releasing and coolants or oils from seeping in. Another example is rubber parts such as the hoses, which enable coolant to circulate.
Certain parts must be exchanged for new ones if there are issues with how they function. Among them are the pistons, which constantly bear the explosive force of high-temperature, high-pressure combustion gases; the piston rings, which encircle each piston to seal the gap between the cylinder’s inner wall and prevent those gases from escaping; and the oil rings, which sit outside the piston rings and serve to contain the oil to reduce friction losses between pistons and cylinders.
Fortunately, specialized manufacturers can often make such consumable parts to order, even for older engines such as the Type R.
The first step was to swiftly finish checking each component, refurbish those that could still be used, and source new parts for those that could not.
The Type R’s astonishing construction
As they tackled this task, the engine restoration team members were amazed at the structure of this 70-year-old engine, unlike anything found today, and the skill of its original creators.
Their astonishment centered on the connecting rods (or con rods) that support the pistons as they absorb the force of explosive combustion in the engine’s cylinders, transmitting their up-and-down movement to the crankshaft.
In today’s cars, con rods are fitted with two main bearings—thin, semicircular metal plates that sandwich the crankshaft from above and below, holding the rod in place and ensuring smooth rotation.
Typically made from copper alloys or an alloy known as white metal, these bearings can contain ample engine oil across their surface, forming a lubricating layer where the parts come into contact.
This oil film keeps parts in place while preventing them from touching directly, reducing surface friction.
In other words, the con rods and crankshaft are designed to rotate smoothly by sliding on the oil film formed atop the metal bearings.
In the engine being restored, however, the con rods were not fitted with any such metal bearings. Instead, the metal-bearing material was applied to the surface of the part itself.
Iwaki
My first thought was, “What’s going on? There are no bearings.” But when I searched around, I learned that applying the metal bearing material in this way was a technique called thermal spraying.
Checking the bearing surfaces revealed damage that made them unusable as they were. This presented another big problem. We found a supplier that still manufactures bearings using this method, but we didn’t know whether they would be able to repair them in the same way.
However, when we investigated further, it turned out that in 1958, the con rods were changed to a separate bearing style. We were able to complete the restoration by obtaining these 1958 con rods and fabricating new bearings. We also made new camshaft bearings, con rod small end holes, and rocker arm bushes.
As it turned out, another major problem awaited the engine team—the wear on cylinder bores (inner walls).
We shine the spotlight on this issue in the second half.
(Text: Yasuhito Shibuya)