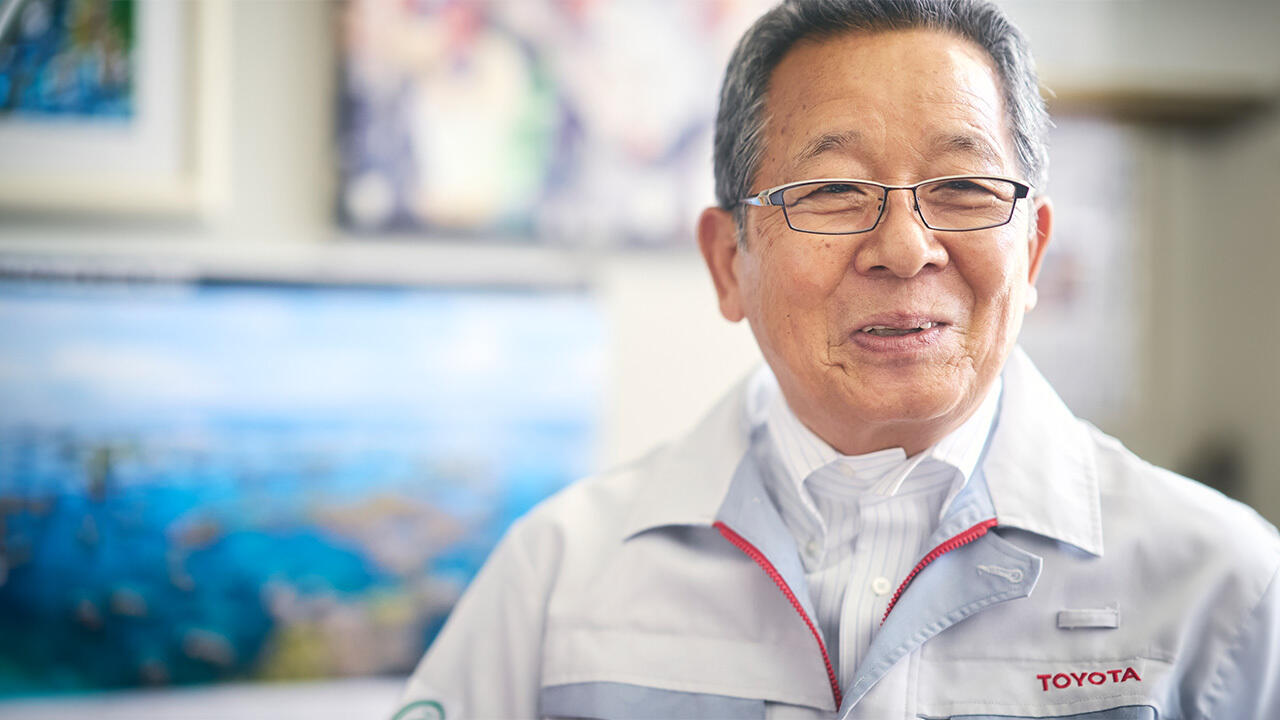
The kaizen spirit is part of Toyota's DNA and has its roots in the Creative Idea Suggestion System. We look at the history and intentions behind the long-running initiative, which also serves as a tool for fostering kaizen talent.
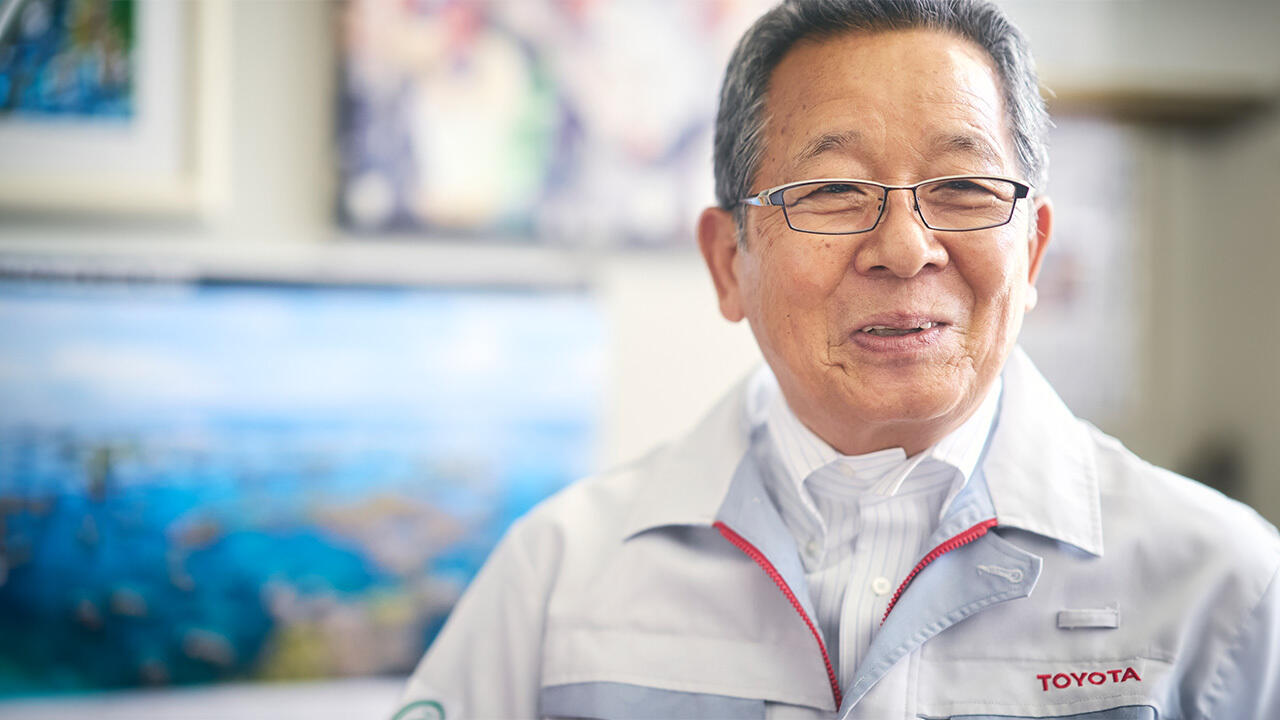
When one of our rookie Toyota Times reporters was told that making a work improvement could earn them 500 yen, they looked baffled. What on earth was this about?
In this new series, we’re showcasing something familiar to every Toyota insider: the Creative Idea Suggestion System, a quintessentially Toyota tradition passed down through generations.
“How can I get this job done more quickly and easily?”
No doubt everyone has had such thoughts in the workplace. When it comes to boosting productivity and quality, the Toyota Production System (TPS) and kaizen (continuous improvement) have become familiar concepts.
Though these terms are now part of the everyday lingo at Toyota and related companies, from the outside, they are often misunderstood as being very difficult to put into practice.
Some even conjure up frightening images of supervisors, stopwatch in hand, scrutinizing every task in minute detail to raise productivity.
The reality, however, could not be further from this picture.
Executive Fellow Mitsuru Kawai, known affectionately as Oyaji Kawai, has spent 61 years in the genba, earning immense trust among production floor workers. “It’s not about increasing productivity—we do it to make our jobs easier,” he says. “When a task is easier, it gets done more quickly, and the result is greater productivity.”
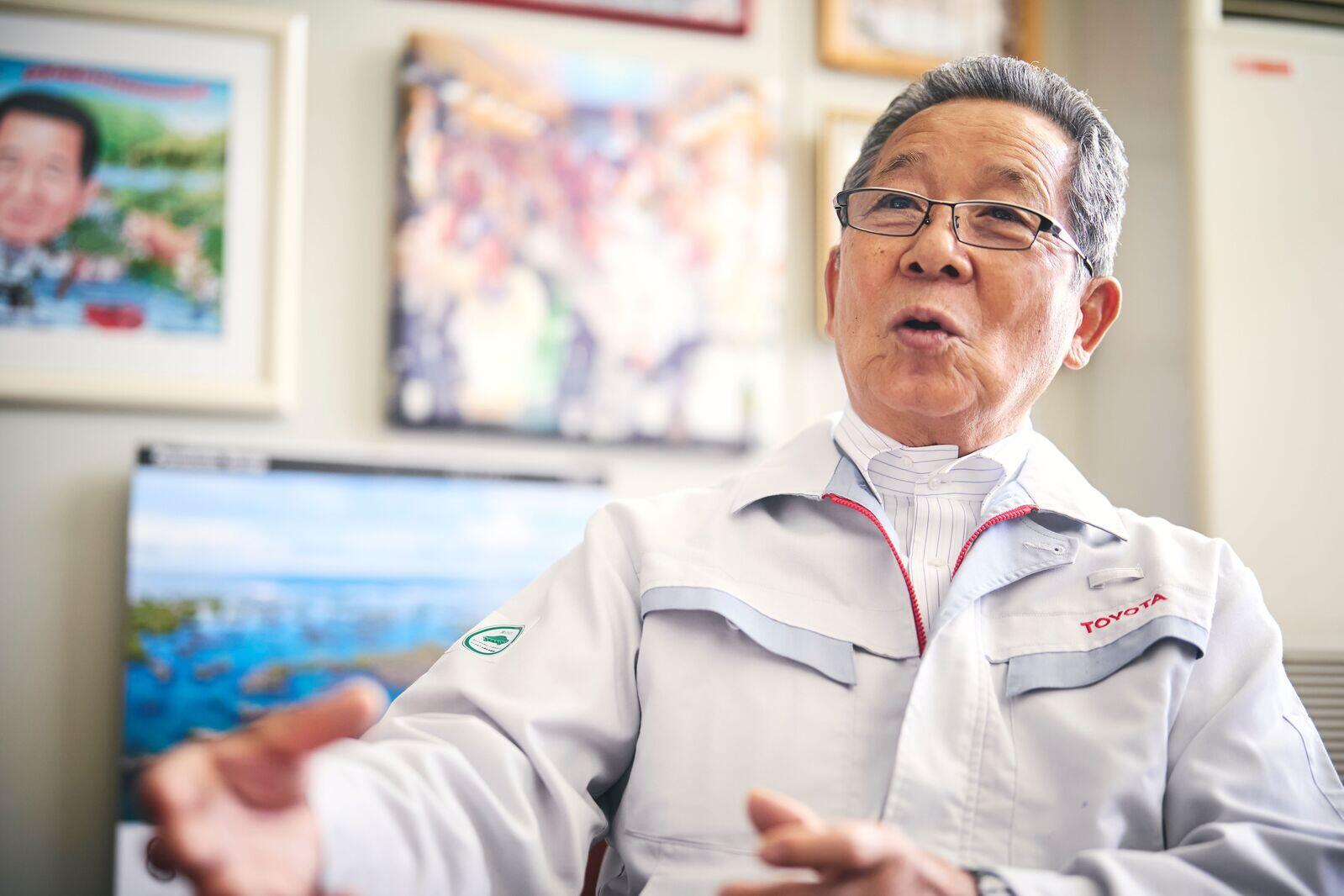
Keeping ideas flowing on the verge of bankruptcy
The path to major reforms starts with small improvements.
Launched in 1951, the Creative Idea Suggestion System has played a part in fostering this aspect of Toyota’s corporate culture for more than 70 years.
Sadayuki Yuzawa, Professional Partner, TQM Promotion Div.
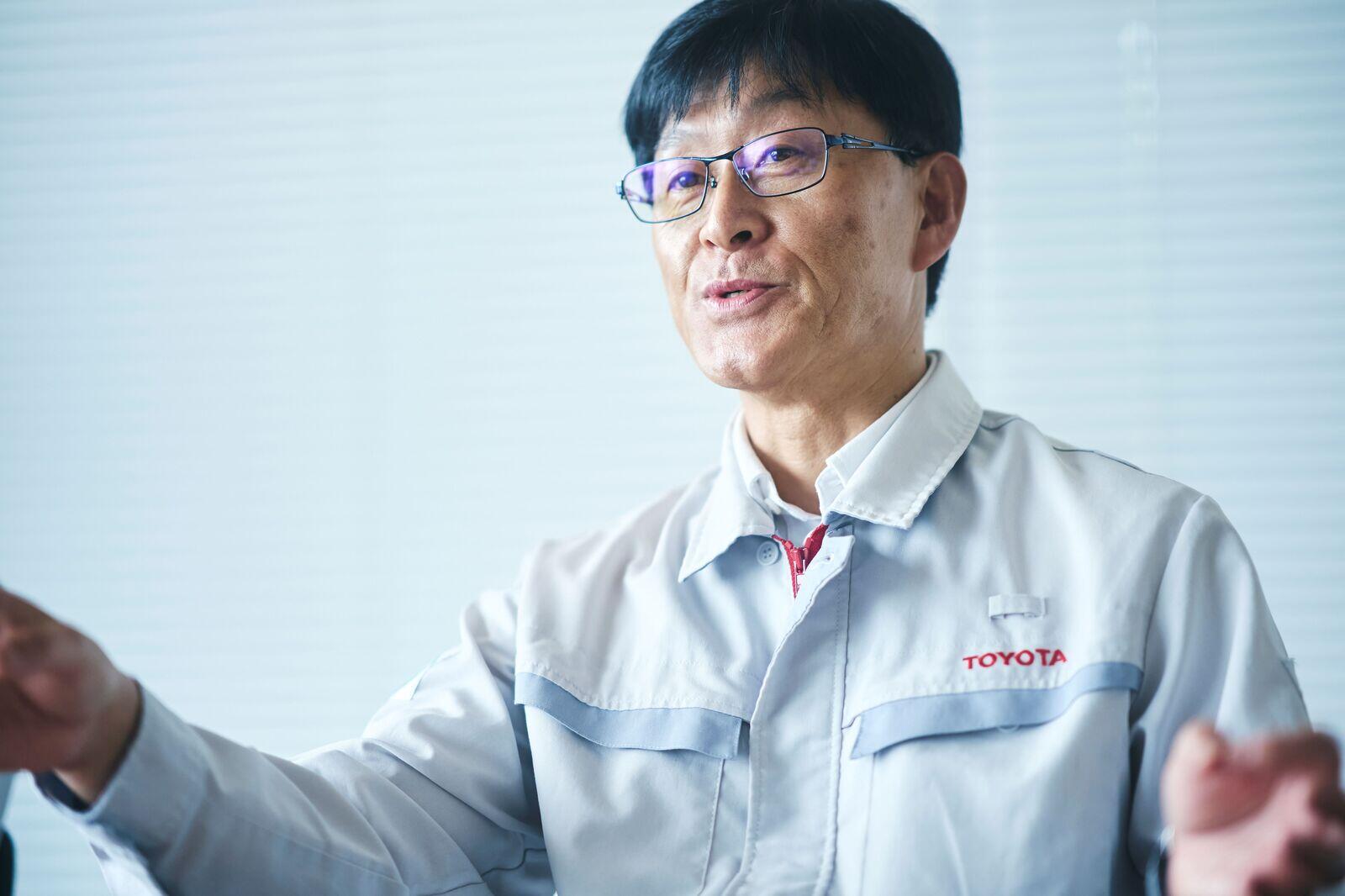
1951 was a time when Japan’s auto industry was taking on America’s Big Three carmakers in a battle for survival. It was also at this time that Eiji Toyoda, while visiting a Ford plant, came across a suggestion system that rewarded creative solutions in the production genba. This became the benchmark for Toyota’s own Creative Idea Suggestion System.
The Dodge Line, a 1949 policy aimed at curbing rampant postwar inflation, caused many bankruptcies across Japan. In 1950, Toyota also faced a major labor dispute that resulted in a quarter of its workers leaving the company. Short on money, equipment, and goods, the only way forward was through human ingenuity.
Masahiko Suzuki, Chief Expert, Genba Kaizen Dept, TQM Promotion Div.
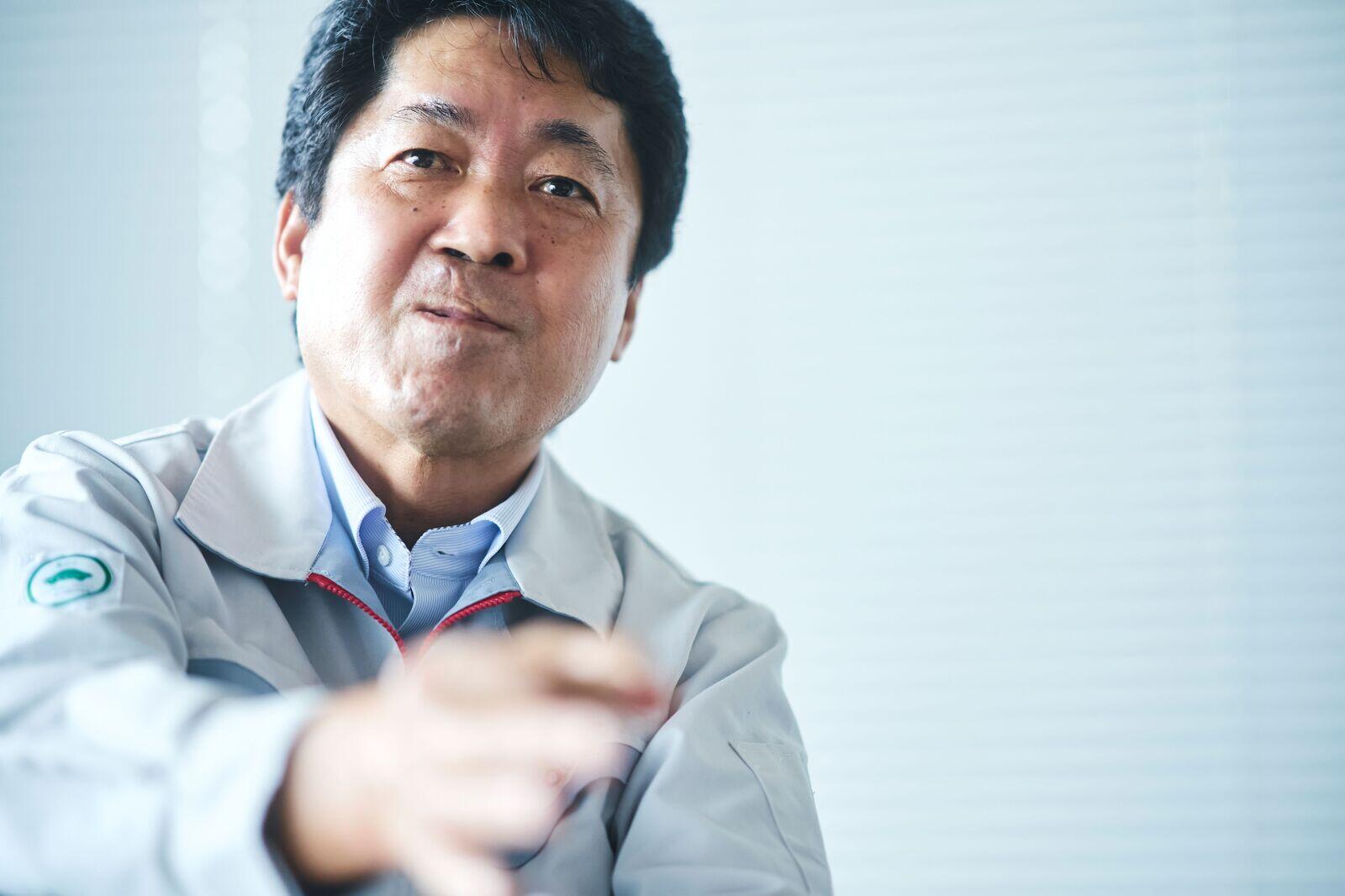
“The original handbook says that ideas could even be submitted verbally or by someone writing on your behalf—it didn’t matter how small, just keep them coming.”
“In 1953, the initiative’s aim was summed up in a new slogan, ‘Good Thinking, Good Products.’ To this day, it is displayed at each plant and widely known as a cornerstone of kaizen.”
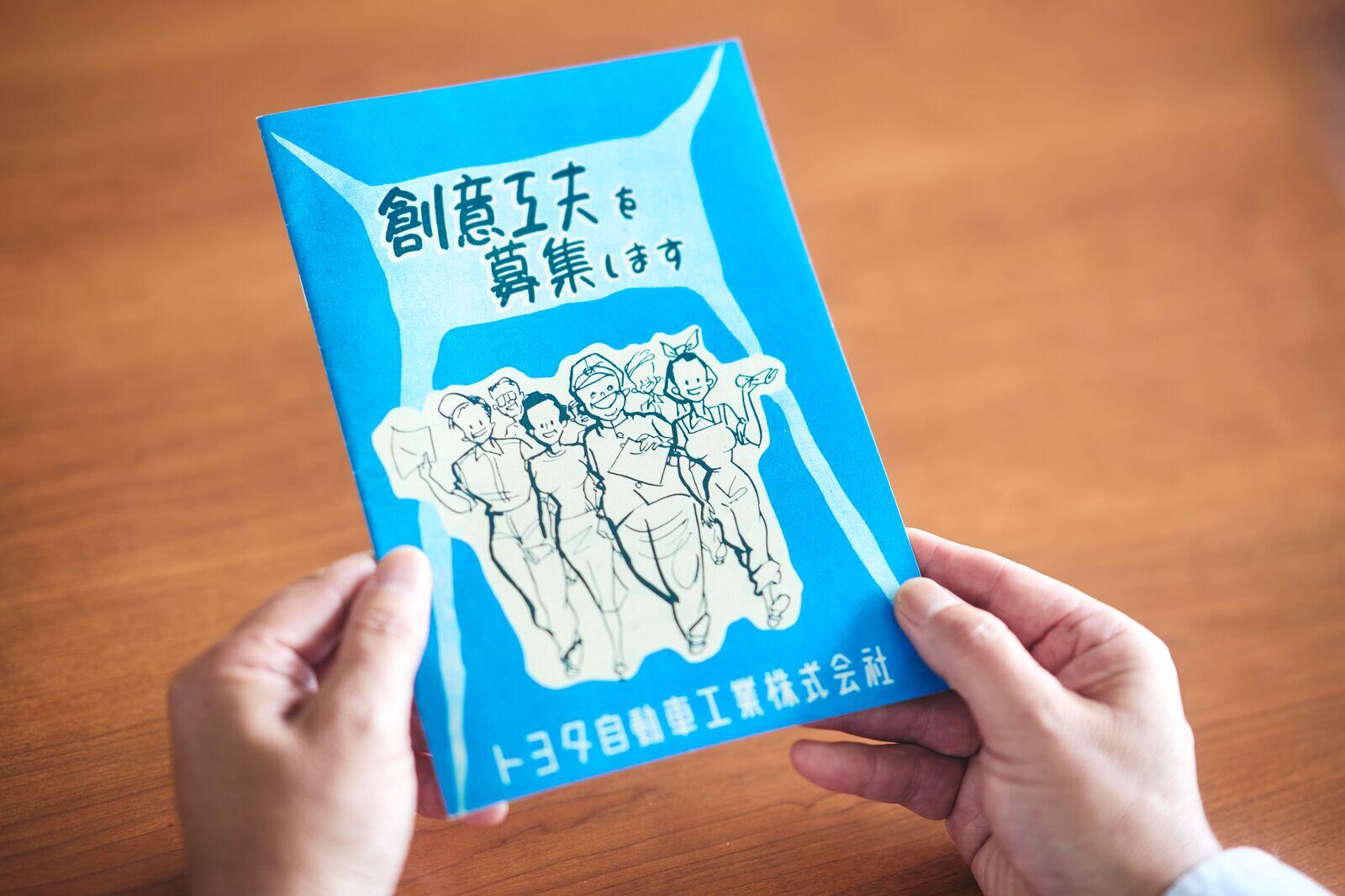
Oyaji Kawai also recalls his own experience: “When I entered the Toyota Technical Skills Academy out of junior high school, the first thing we learned in the classroom during training was how to submit creative ideas.”
Since then, the system has become an indispensable part of Toyota’s personnel development.