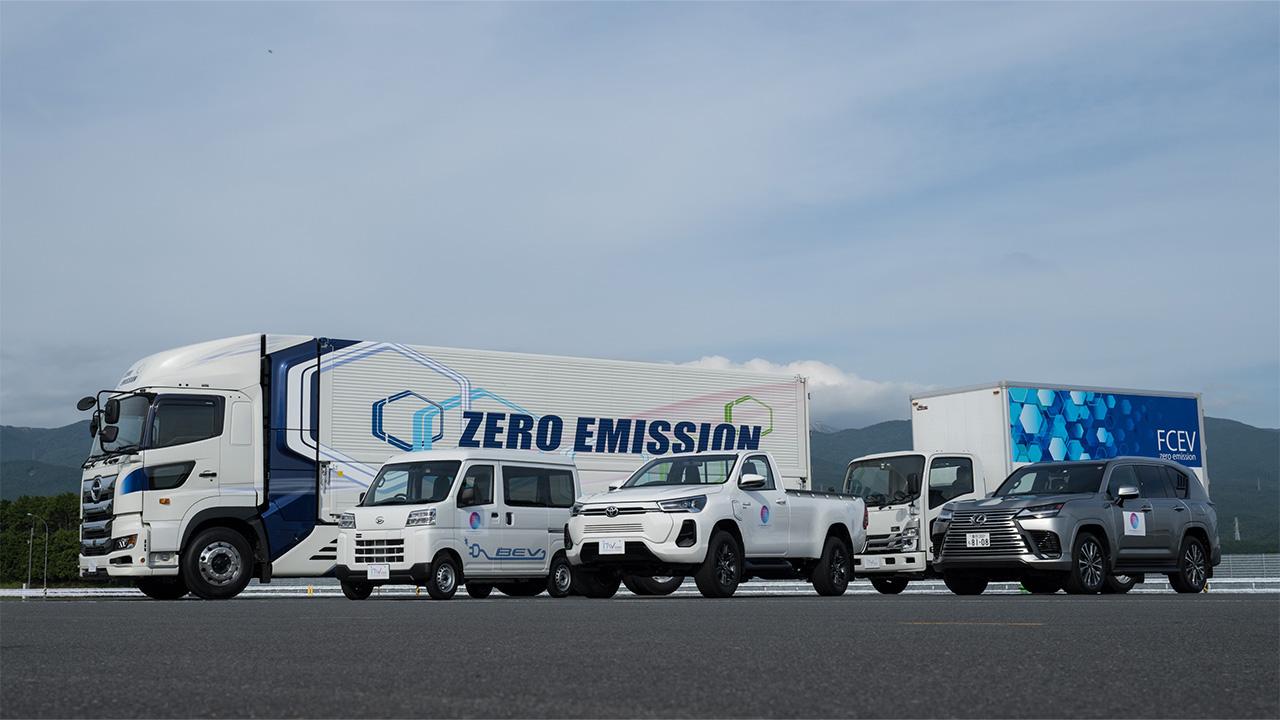
As part of efforts to advance CASE technologies, Toyota is stepping up collaboration in the commercial sector, where a growing circle of like-minded partners is leveraging economies of scale to create a prosperous mobility society.
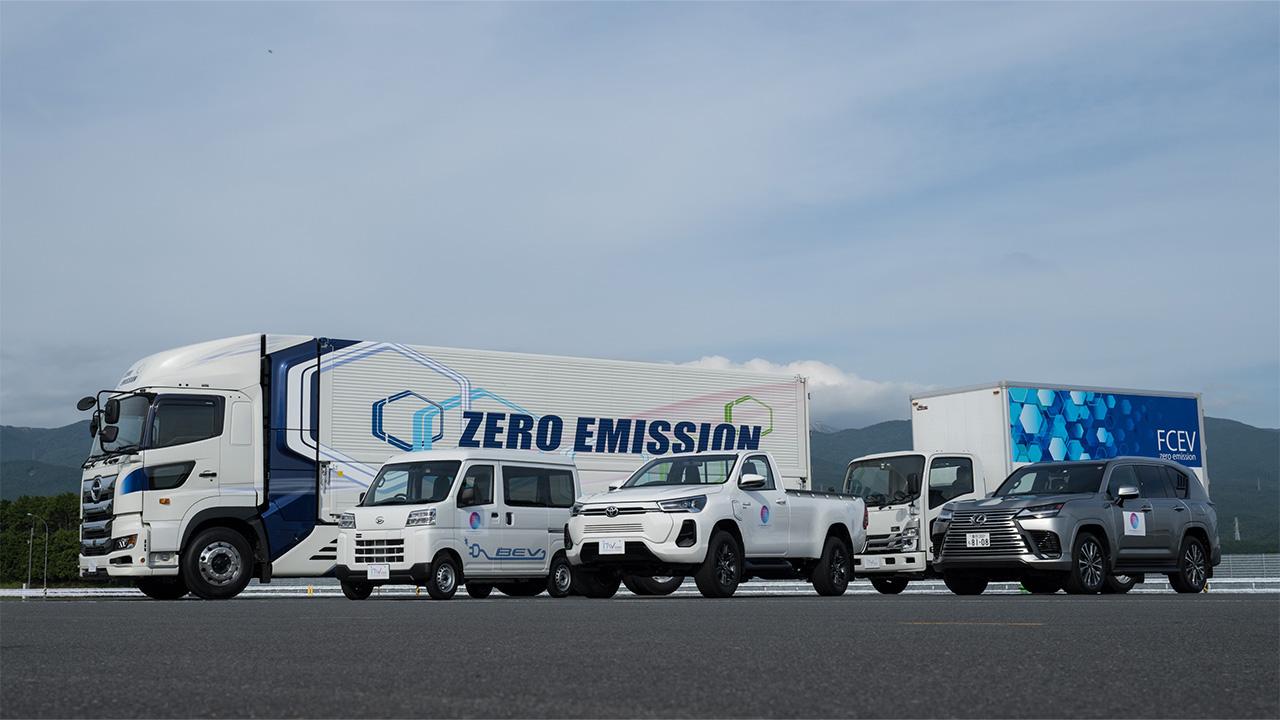
“We want to combine data on trucks and Toyota’s passenger cars and use the resulting big data to solve the problems faced by our customers.”
These were the words of Executive Vice President Hiroki Nakajima, Toyota’s Chief Technical Officer (CTO) and the man behind June’s Technical Workshop, speaking at a press conference to mark the launch of CJPT* in 2021.
*Commercial Japan Partnership Technologies. Established by Toyota Motor Corporation, Hino Motors, and Isuzu Motors in April 2021, with Suzuki and Daihatsu joining that July (Hino was expelled in 2022). The partnership aims to accelerate the rollout and adoption of CASE technologies, helping to solve the issues faced by the transportation industry and contributing to the creation of a carbon-neutral society.
Trucks account for around 90% of logistics in Japan; with bus and taxi transport included, the sector employs roughly half of the country’s 5.5 million auto industry workers, or 2.7 million people.
Although these commercial fleets make up only 20% of vehicles on the road, they account for 40% of total mileage and half of overall CO2 emissions.
For CASE technologies to improve and become more widely used, they must be deployed in tandem with infrastructure, with commercial vehicles playing a key role. This shared understanding of the industry’s challenges is what led to the formation of CJPT.
The member companies joined forces because they recognized the importance of scale in solving logistics issues.
This need for economies of scale was also highlighted in the merger between Mitsubishi Fuso and Hino announced in May, a four-way collaboration that also involves Daimler Truck and Toyota.
So how will the benefits of size contribute to the growth of technologies, products, and services?
This third and final article in our Technical Workshop series looks at how Toyota is harnessing scale to enrich lives.
We explain how technological development is being driven by growing partnerships and the use of big data obtained from truck manufacturers and the Toyota cars on our roads.
Tackling logistics challenges with connected technologies
When CJPT was unveiled in 2021, three main challenges were identified within the logistics industry: driver shortages, transport efficiency, and carbon neutrality.
To tackle these problems, Toyota has been planning and developing the Efficient Transport Operation Support System (E-TOSS), combining the company’s connected technology, which wirelessly links cars to the outside world, with the logistics expertise of retailer AEON.
This system looks to boost the efficiency of transport from warehouses to retail stores and has roots in the TPS (Toyota Production System) mindset. It can prepare efficient transportation plans by bringing together Toyota’s real-time information processing capabilities, big data, and information specific to commercial vehicles like truck driving data and traffic restrictions.
E-TOSS also utilizes the traffic condition forecasting technology developed through Toyota’s in-car navigation business, enabling the system to accurately gauge daily fluctuations in cargo volumes and optimize consolidation, or loading goods bound for multiple destinations in the same truck.
These capabilities improve the truck load factor—thought to be less than 50% across the industry—and identify efficient transport routes, helping reduce the distances traveled and the number of journeys*.
*Estimated 10-15% reduction in CO2 emissions and logistics costs, based on the decrease in total mileage during trials at AEON distribution centers.
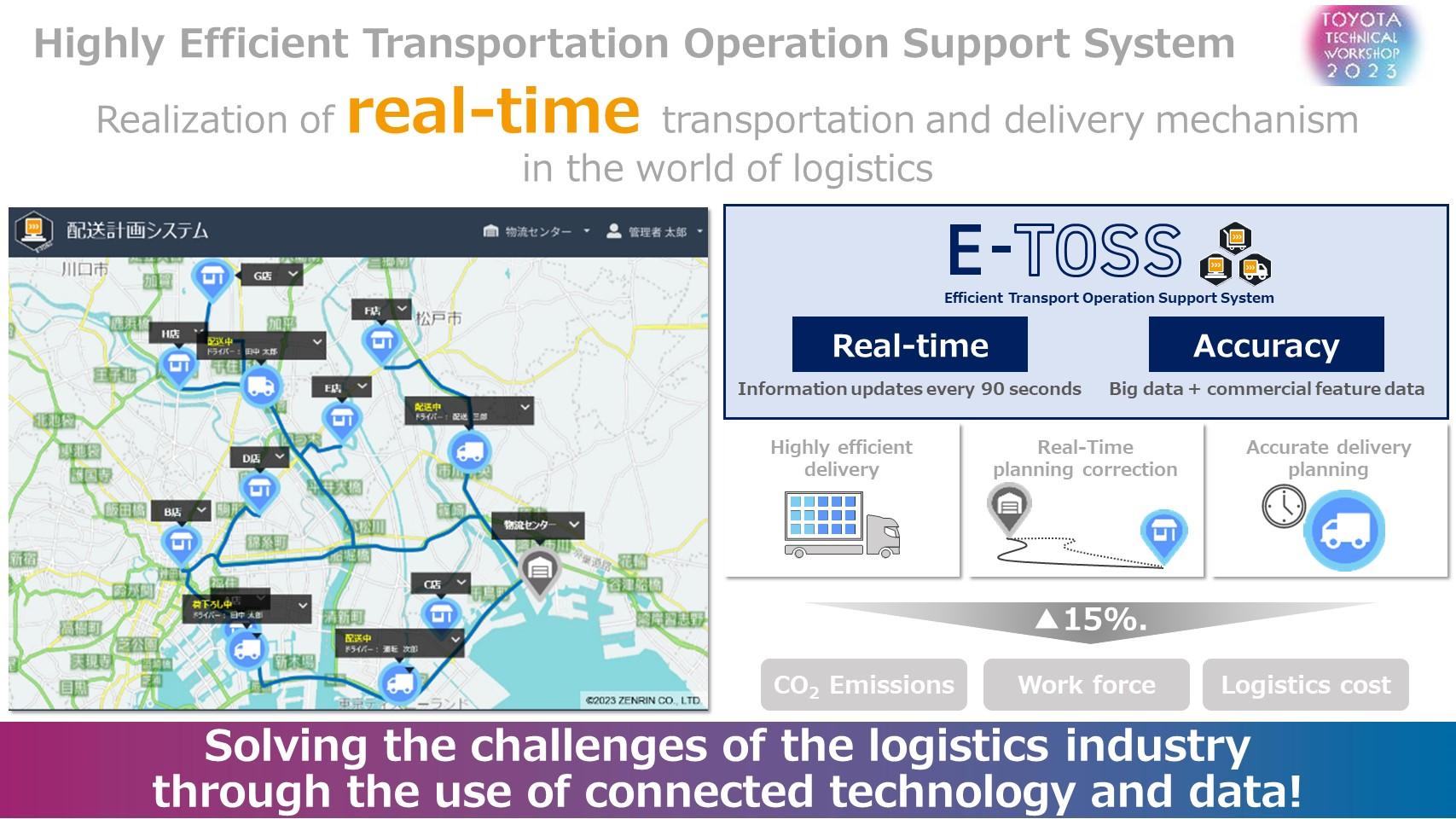
At the workshop, Toyota’s engineers explained the system, while monitors displayed footage of real-time deliveries.
E-TOSS is already in use at AEON’s Minami-Osaka distribution center, with plans to expand the service to Kyushu. Toyota hopes to see it widely adopted across the logistics industry.
Test driving carbon neutrality
At the start of the workshop Mitsumasa Yamagata, president of the Hydrogen Factory launched in July, outlined his 2030 vision for rapid expansion in the fuel cell market, centered on commercial vehicles.
He also revealed that Toyota received outside offers for 100,000 vehicles in that year, most of which are also commercial vehicles.
Yamagata gave several reasons for this outlook. For one, trunk line logistics connecting major cities over large distances consumes vast quantities of fuel, so enabling heavy-duty trucks to run on hydrogen would spur uptake.
Since these vehicles drive fixed routes each day, their utilization rate can also be improved by, for example, placing hydrogen stations near expressway interchange onramps/offramps.
This approach would help the station business achieve profitability, which is regarded as a major hurdle.
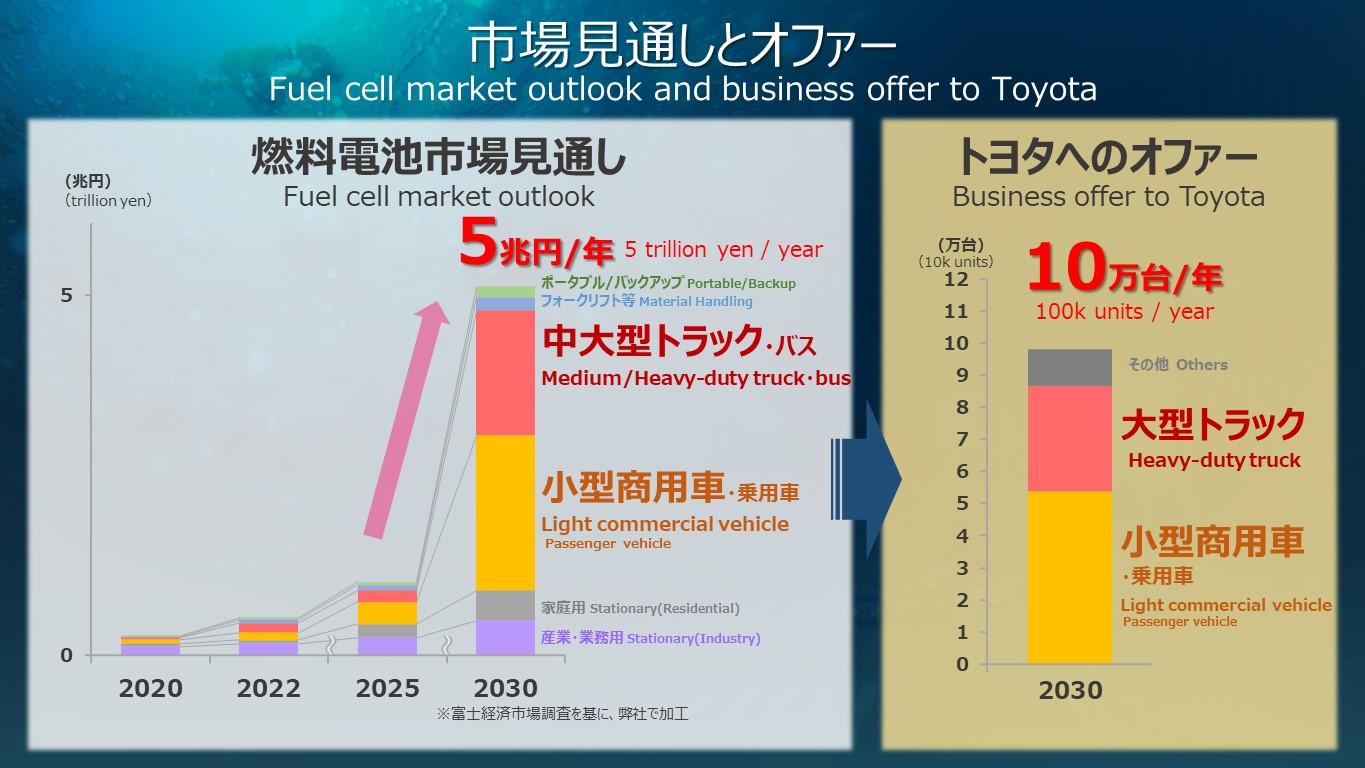
The workshop also featured displays and test drives of FCEV trucks currently being trialed and BEV commercial minivans.
Heavy-duty trucks based on the Hino Profia are equipped with two sets of FC stacks from the Mirai, modified for commercial use. The hydrogen tanks developed for these heavy-duty trucks provide a range of over 600 km from 50 kg of gaseous hydrogen.
In May, these trucks entered on-road trials conducted by Asahi Group Japan, Seino Transportation, NEXT Logistics Japan, and Yamato Transport, running between delivery hubs on trunk line routes. Ongoing development is tackling issues such as loading volume/capacity and vehicle cost.
Similarly, light trucks based on the Isuzu Elf use a single set of modified Mirai FC stacks. These vehicles use tanks from heavy-duty trucks to carry a total of 10.5 kg of gaseous hydrogen for a range of 260 km.
Since February, they have begun to take the road in Fukushima and Tokyo as an option for regional logistics centered on delivery hubs.
As with heavy-duty trucks, Toyota is working to address issues such as price, while eyeing a future B-to-G expansion at the municipal level, where FCEVs can serve as garbage trucks or meal delivery vehicles.
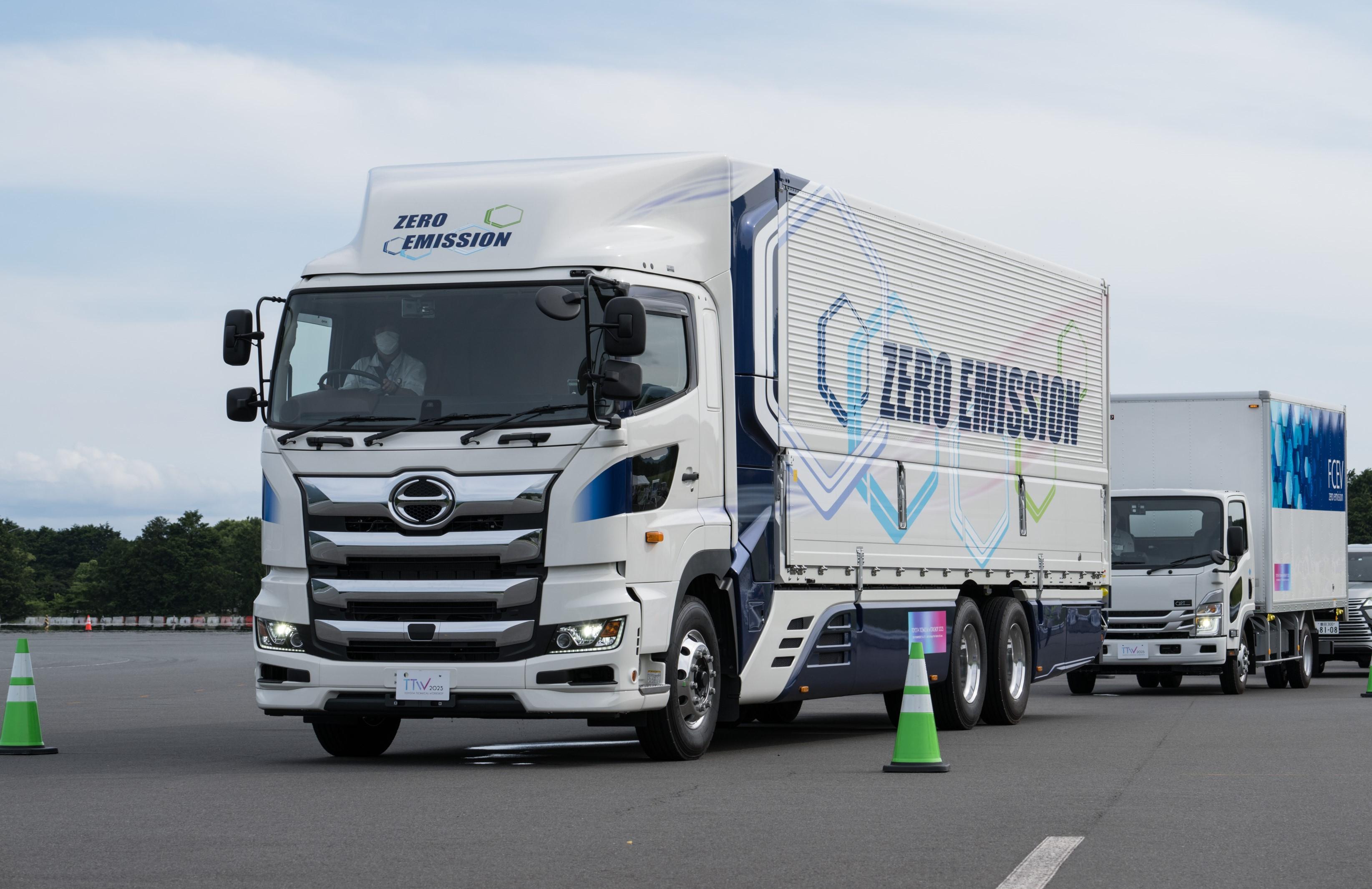
And for last mile logistics there are BEV commercial minivans, which were also exhibited at the G7 Hiroshima Summit.
Combining the expertise of Suzuki and Daihatsu—leaders in minivehicle development—with Toyota’s electrification technology, the three companies have jointly developed a BEV system optimized for light commercials. These vans have a range of 200 km, with a maximum load of 350 kg and a carrying capacity to equal gasoline-powered vehicles.
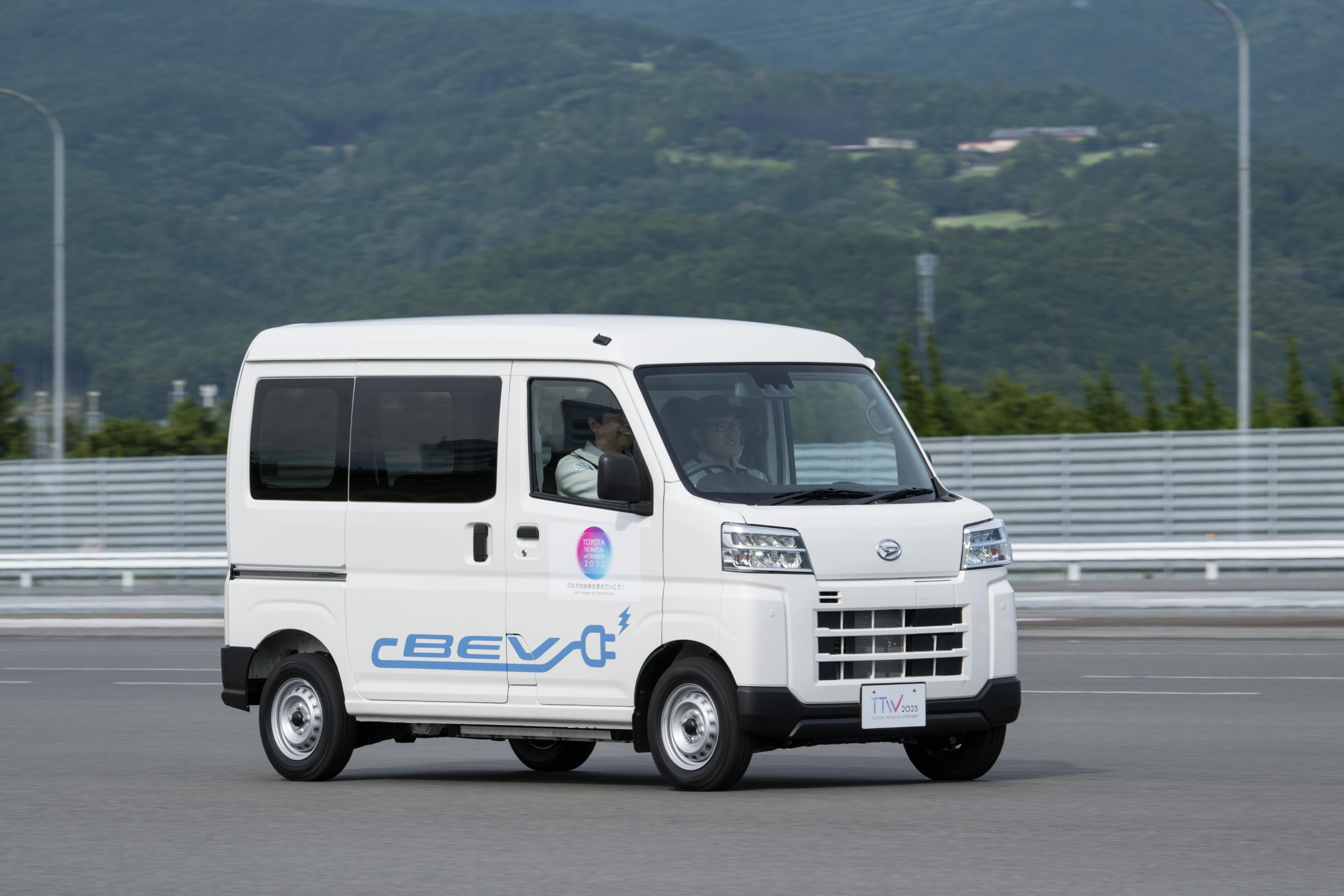
All three manufacturers plan to release their models by the end of this fiscal year.
Such teamwork spans the entire transportation network, from major arteries to capillaries, spurring cooperation to achieve a carbon-neutral logistics industry.
Scale improves safety
Toyota is upgrading the safety performance of its Advanced Driver-Assistance Systems (ADAS) by drawing on a wealth of data that could only be amassed by a company shipping 10 million cars each year.
The next-generation ADAS currently in development uses data collected from vehicles equipped with third-generation Toyota Safety Sense (TSS). Situations involving emergency braking or steering are identified and used to train the AI.
With this process, a greater pool of similar cases leads to higher recognition rates and accuracy. Here Toyota’s large vehicle volumes provide an advantage, making it possible to acquire a usable degree of information even for rare near-miss scenarios.
At the event, real examples were used to demonstrate these data-driven improvements in recognition.
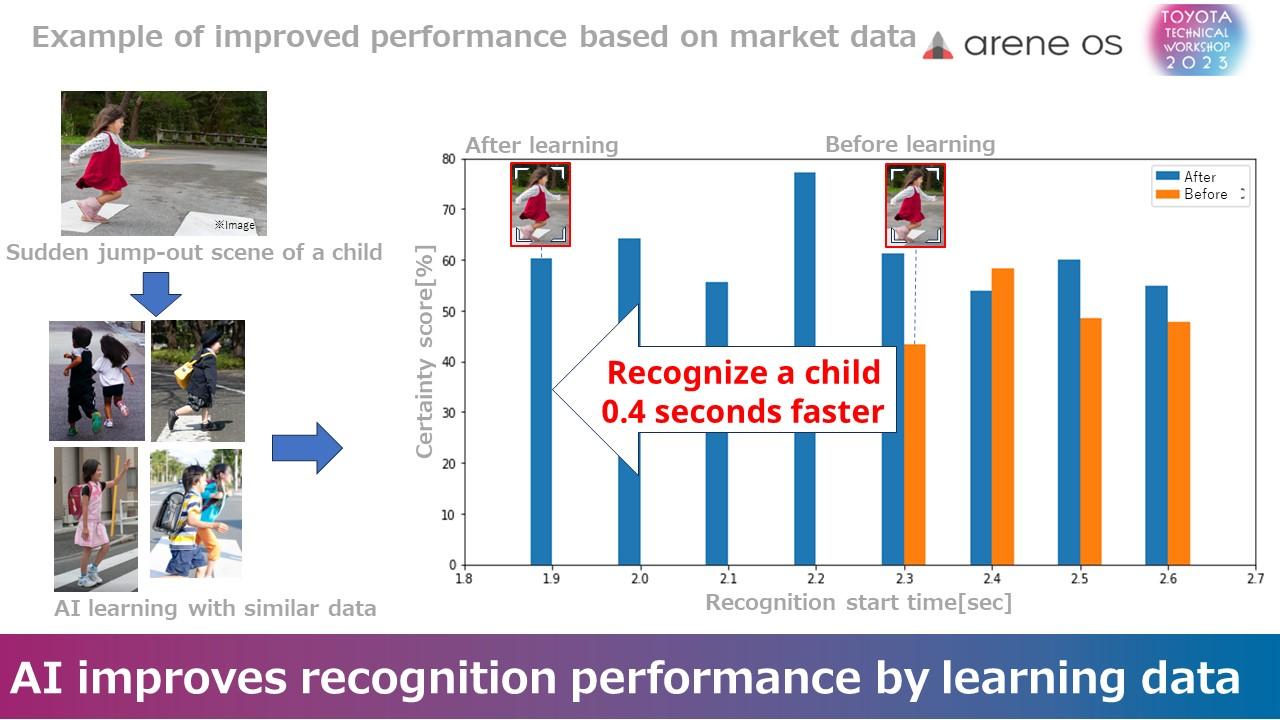
Prior to being trained, the AI took 2.3 seconds to recognize a child about to run onto the road. Performance was improved by gathering a large amount of data on similar situations, including children running or using a pedestrian crossing. After training, recognition time was down to 1.9 seconds, 0.4 seconds faster.
The data trove also fuels automatic map generation (Geo). Ordinarily, updates require survey vehicles to hit the streets, taking anywhere from six months to a year.
Toyota’s access to large quantities of data enables it to track three-dimensional vehicle paths in real time, reducing the frequency of map updates down to a single day.
Road gradient information can also be obtained with far greater definition, helping make driving not only more comfortable and safer but also more fuel- or energy-efficient.
Engineers continue striving to change the future of cars
Toyota’s recent workshop showcased many technologies driven by the new leadership’s focus on electrification, intelligence, and diversification.
They ranged widely, some relating to car performance, others offering a taste of the future of mobility. And yet all these items stemmed from Toyota’s accumulated expertise in making ever-better cars.
The company’s new management team is intent on changing the future of cars. Despite being set a monumental task with no clear solution, at the workshop, Toyota’s engineers somehow seemed to be reveling in the challenge.
At the event, Vice President Nakajima wrapped up his opening remarks with the following:
“As forward-looking engineers, we are excited—let’s change the future of cars! I want this to be the common cause towards which we all strive.”