
Batteries with a 1,000 km cruising range and FC systems that combine fuel efficiency with longevity and lower costs were among the next-generation technologies unveiled by Toyota for future release.
[BEV] Next-generation batteries to underpin 3.5 million vehicles in 2030
Speaking publicly for the first time since the BEV Factory’s launch in May, President Kato vowed to “change the future through BEVs by transforming our cars, manufacturing, and the way we work, thereby contributing to Toyota’s future success.”

At the workshop, Kato indicated that his unit’s next-generation BEVs * will first hit the market in 2026 and that 1.7 million of the 3.5 million BEVs Toyota expects to sell in 2030 will be next-generation models.
*Vehicles with all aspects optimized for BEVs, from batteries and platforms to production methods. Maximizing battery use and improving efficiency will increase the cruising range to 1,000 km. Models that combine thrilling performance and design will also be released under the Lexus brand.
Toyota also unveiled two next-generation lithium-ion batteries that the company plans to use in its next-generation BEVs: a performance version, and a popularization version.

The performance version will double the cruising range of conventional batteries to 1,000 km by increasing energy density and improving vehicle efficiency through aerodynamics and other factors. At the same time, Toyota also aims to reduce costs by 20% and offer rapid charge times of 20 minutes or less.
Meanwhile, the popularization version adapts the bipolar structure used in hybrid (HEV) nickel-metal hydride batteries.
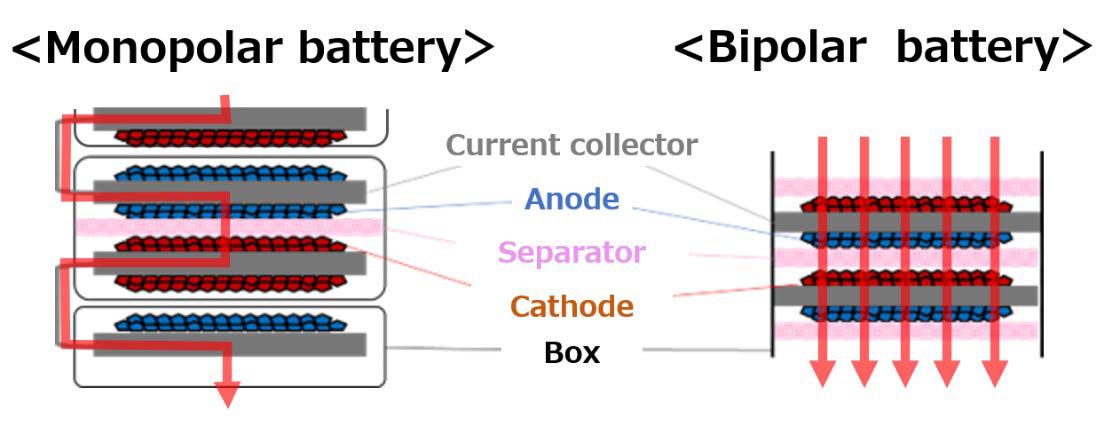
Even as it boosts cruising range by 20% over conventional batteries and similarly keeps rapid charging times under 30 minutes, this version is expected to cut costs by 40% thanks to fewer parts (one-fourth to one-fifth of the current number).
The high-performance version will then take the best aspects from both next-generation batteries, combining a bipolar structure with a high-nickel cathode.
Doing so is anticipated to give a further 10% boost to the performance version’s cruising range and reduce costs by 10% while keeping rapid recharging within 20 minutes or less.

Befitting a full lineup manufacturer like Toyota, the company is developing a range of battery options that can respond flexibly to customer needs.
[BEV] Discovering new all-solid-state battery technologies
Toyota also used this opportunity to provide an update on its all-solid-state batteries, said to be a game changer for BEVs.

All-solid-state batteries have a solid electrolyte, allowing faster movement of ions and greater tolerance of high voltages and temperatures. It is hoped that this technology will result in increased power output, longer range, and shorter charging times.
The tradeoff, meanwhile, is thought to be shorter battery life. Solid electrolytes repeatedly expand and contract as the battery charges and discharges, which can create cracks that inhibit the movement of ions between the cathode and anode.
At the workshop, Toyota announced a newly discovered technology to overcome this challenge. The company will now focus on developing mass production methods to address the issue of cost.
Toyota also revealed that it has revised earlier plans set forth in 2021 to begin introducing all-solid-state batteries through HEVs, and will now strive for commercialization in 2027-2028.
The performance version battery is being developed with Prime Planet Energy & Solutions, while the popularization, high-performance, and all-solid-state batteries are a joint undertaking with Toyota Industries Corporation. These efforts bring together expertise from across the Toyota Group in the push toward commercialization.
[BEV] Aerodynamics based on rocket technology
Battery development alone does not dictate the performance of BEVs. Vehicle design considerations such as minimizing drag, improving energy regeneration, and overall energy and heat management must also be addressed at the same time.
One such aspect of vehicle design introduced by President Kato was aerodynamic technology. Toyota is working jointly with the Space Systems Division of Mitsubishi Heavy Industries to apply hypersonic rocketry technology to cars.

Toyota is studying the technologies that protect rockets from the heat caused by air friction and compression and is looking for ways to transfer that knowledge to the speed range of a car.
Drag can be lowered by controlling points of contact with the airflow, for example, through body surface treatment.
Toyota hopes to reduce the drag coefficient (Cd) to around a tenth of that for existing car bodies (0.20).
Remarkably, this reduction is not restricted by the shape of a car or whether the material is steel or aluminum, enabling designs that are both stylish and aerodynamic. Such is the potential of this technology.
Development is underway, with the goal of commercial release in three years.
[BEV] Monozukuri advances to halve investment costs and processes
As President Kato explained, the product advances embodied by next-generation BEVs will be underpinned by advances in monozukuri (manufacturing).
“The future of monozukuri is about halving—halving BEVs, so to speak. Modular structures and self-driving assembly lines will halve production processes and plant investment. In addition, we can halve production preparation lead times through the potential of digital twins.”

Toyota’s next-generation BEVs will be built upon a new modular structure in which car bodies are divided into three sections: front, center, and rear.
Of these, only the center section will house batteries. With the front and rear unaffected, battery advances can be rapidly incorporated into vehicles.
One of the production technologies that will make these modular structures possible is known as giga casting.
At present, the rear section of a bZ4X is made with 86 sheet metal parts and 33 press processes. Using integrated molding with aluminum die-casting can reduce this to a single part made by a single process.
This approach seeks to reduce both cost and weight below conventional models as well as boost productivity, leveraging one of the company’s strengths, the Toyota Production System (TPS).
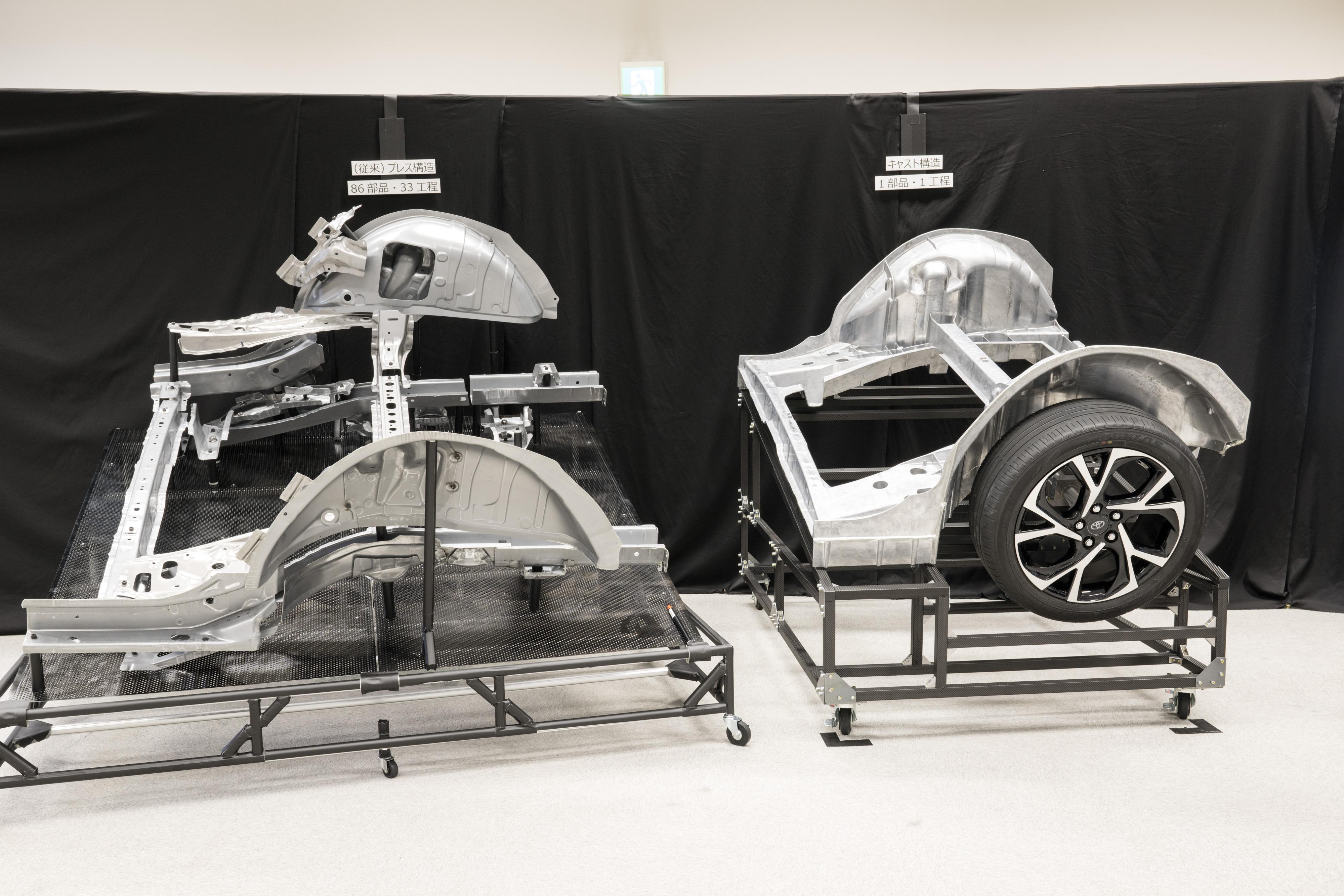
Another of the presented technologies was a “self-driving assembly line,” in which the cars being assembled move between processes on their own.
At a minimum, a vehicle needs only the three modular components (front, center, rear) and a battery, motor, tires, and wireless terminal to drive independently.
Such a setup eliminates conveyors from the assembly line, allowing for more flexible factory layouts. This will help shorten the years-long lead times needed to prepare for mass production and reduce the required plant investment, which runs into the billions of yen.
Development is being hastened toward deployment within three years.