
The liquid hydrogen Corolla took on its second Fuji 24 Hours Race. Despite a long stint in the pits, the car showed remarkable advances. We sum up three key areas of progress.

“What’s frustrating is that we did so much test driving, eliminating the problems one by one ahead of the race. Just last week, we tested without any trouble, and both Masahiko Kondo and Morizo were pleased with how the car ran. Then we get to the main event… It goes to show how tough things are in the world of racing.”
These were the words of driver Hiroaki Ishiura, who heads the squad of the #32 liquid hydrogen-fueled Corolla, revealing his disappointment during a post-race interview.
Round 2 of the 2024 ENEOS Super Taikyu Series Empowered by BRIDGESTONE was the Fuji SUPER TEC 24 Hours Race, held on May 27-28.
The liquid hydrogen Corolla spent nine hours in the pits due to brake system problems, finishing with 332 laps (approx. 1,515 km). Despite officially completing the race, the team fell short of last year’s 358 laps (approx. 1,634 km).
Anything can happen in the world of racing. Although the team had hoped for a better result, this year’s liquid hydrogen car demonstrated remarkable progress.
We break down the vehicle’s evolution into three key points.
Upgrade 1: Improved pump durability
“Among the liquid hydrogen technologies, the pump is our biggest challenge, our weak point,” says GR Vehicle Development Division Project General Manager Naoaki Ito, who oversees the hydrogen engine project.
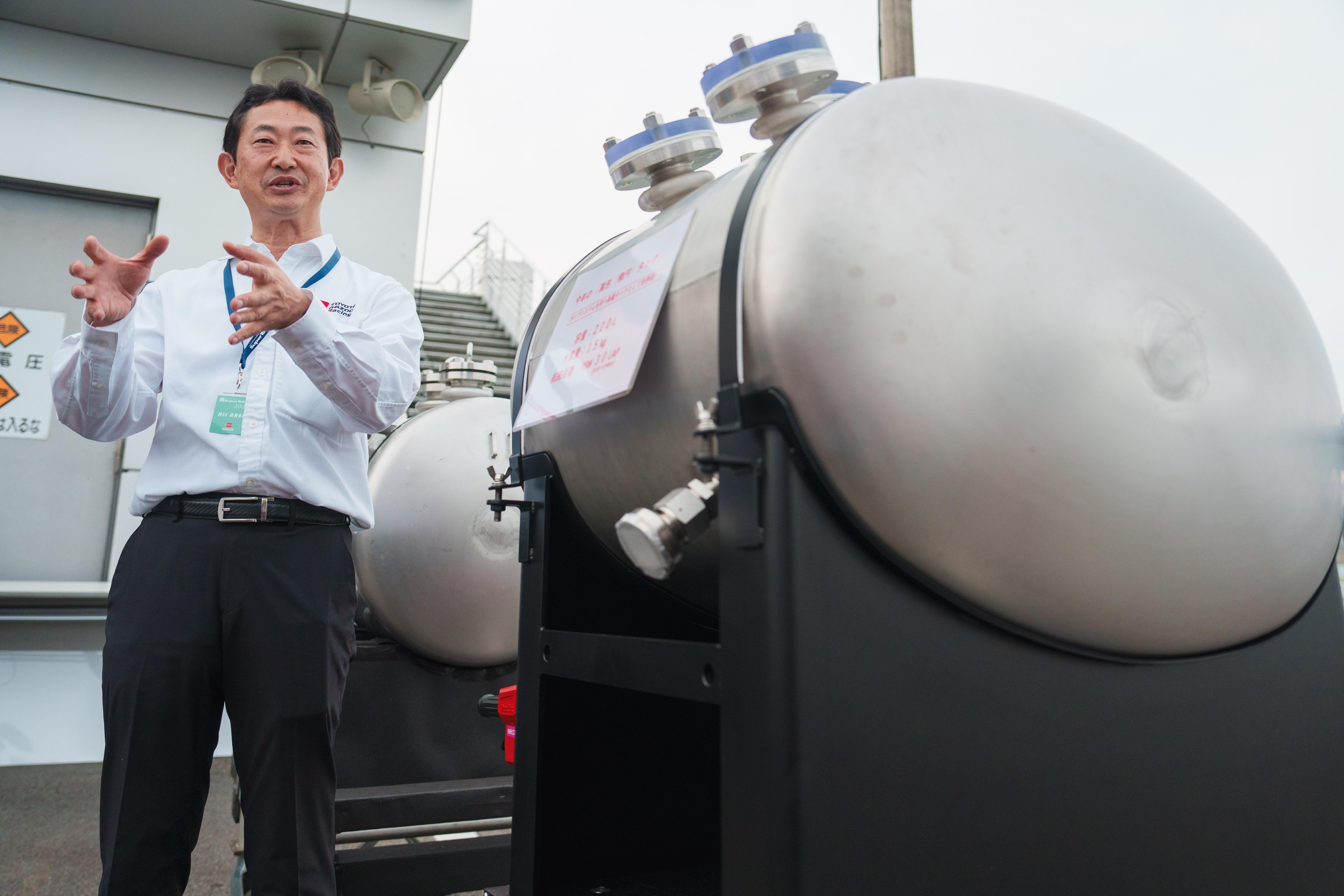
At last year’s Fuji 24 Hours Race, the liquid hydrogen Corolla had two scheduled stops of four and three hours, respectively.
That time was spent replacing the pump that delivers liquid hydrogen from the fuel tank.
The motor’s rotational movement is converted into the piston’s up-down motion by a mechanism known as a crank, enabling it to pump liquid hydrogen at a pressure of roughly 10 MPa.
The issue last year was that, in the process, the motor's torque and the opposing pressure wore down the crank gears and other parts, reducing durability.
The problem was that the motor only applied force to one side of the crank. To overcome this, engineers left the motor as it was and added a dual-drive gear set (the blue and red parts in the photo below).
With this setup, the driving force is transmitted to both sides of the crank, alleviating torsion in the components and boosting durability.
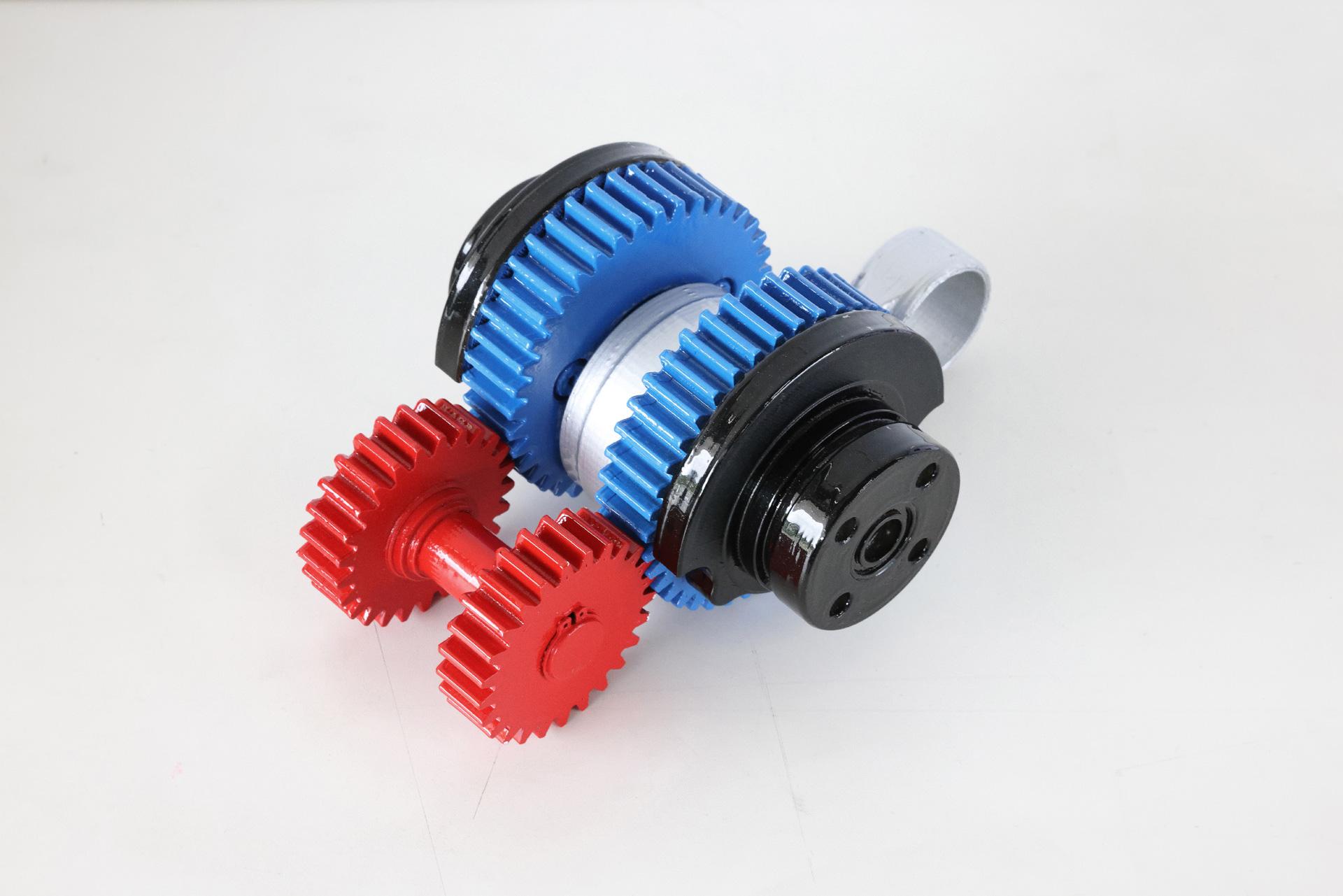
The solution is extremely simple: add only a gear set. But in the weight reduction-obsessed world of racing, “keeping it simple is crucial,” says Ito.
Still, the modifications had a big effect, completely eliminating pump failures in follow-up testing. Although the car had a lengthy pitstop during the race, this had nothing to do with pump durability.