
Hydrogen engines are two-thirds of the way to production, continuing to evolve through both racing and public road trials.
Upgrade 2: Extended range
The second area of improvement is range. In addition to hosting the season’s final round, Fuji Speedway was also the location for May’s 24-hour race, where the liquid hydrogen Corolla made its debut.
At that outing, the car managed a maximum of 16 laps per refuel; six months later, that number has jumped 25% to 20 laps.
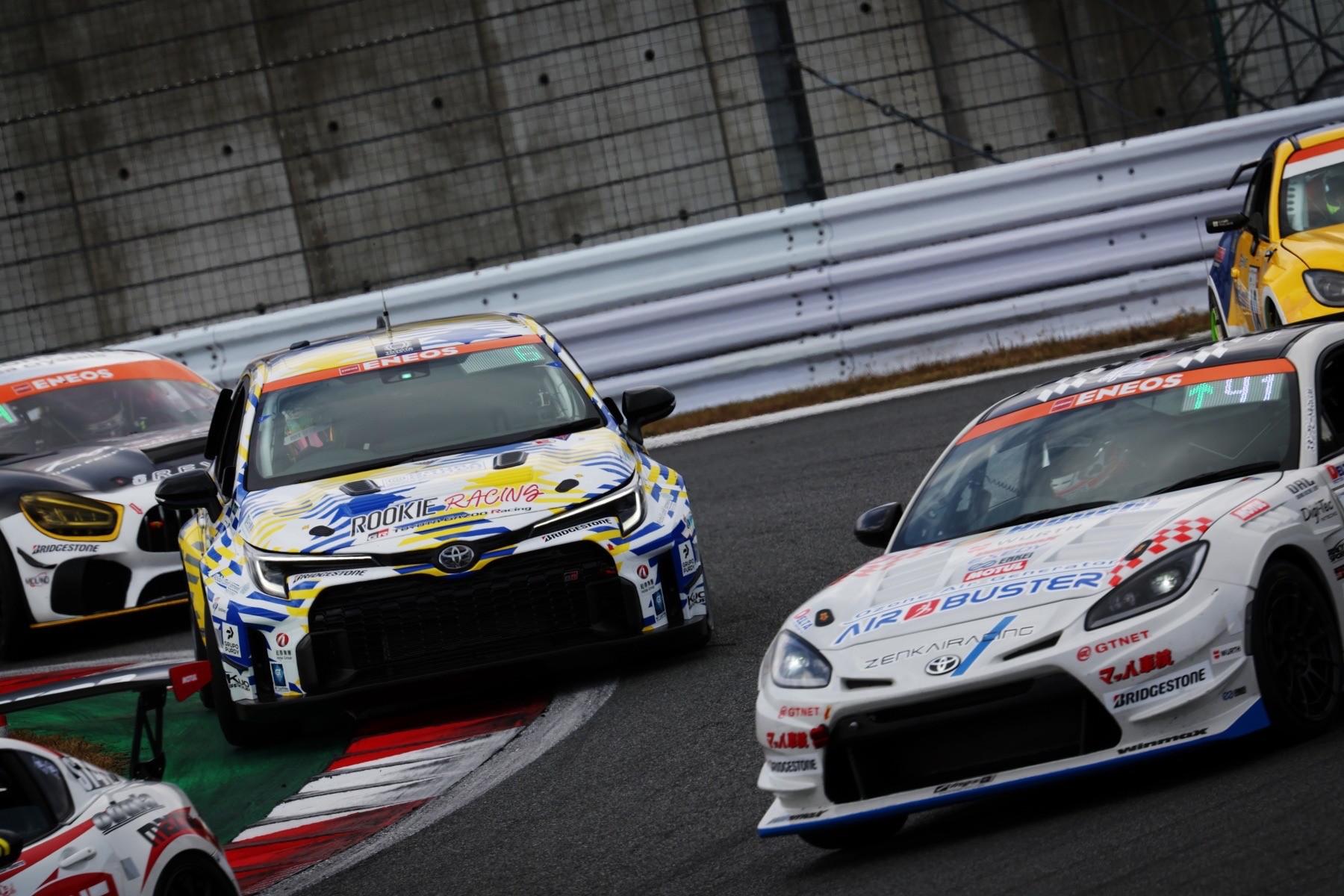
On the technical side, this comes down to three aspects. First is greater accuracy in measuring the amount of fuel in the tank.
The liquid level sensors found in regular fuel tanks do not work with liquid hydrogen kept at an ultracold -253℃.
Instead, the level is measured by gauging the electrical charge difference between liquid and gas. However, since the boundary layer tends to be indistinct, the tank often ended up less full than expected.
Although the technology is still being improved, it is gradually providing a clearer picture of that vague boundary, enabling tanks to carry more liquid hydrogen.
The second factor is reduced heat transfer into the tank. Liquid hydrogen tanks are maintained at -253℃. Unfortunately, connections to the pump and other parts that interrupt the vacuum layer inevitably bring in heat, causing a certain amount of boil-off hydrogen vapor that must be vented from the tank.
Even when vaporized, however, the hydrogen remains at an extremely low -200℃. The team devised a way to harness this gas by arranging its outlet path to pass around the points where heat enters the tank. This dampens the boil-off process, securing more liquid hydrogen for driving.
The third aspect is optimizing fuel injection during driving. This task has carried over from the days of gaseous hydrogen, with the team working to improve the amount of fuel injected when the gas pedal is not at full throttle.
Upgrade 3: Weight reductions
Third, the hydrogen-engine car also received a weight reduction, shedding 50 kg since the Autopolis race in Hita, Oita Prefecture in July.
This is partly thanks to a redesign of the liquid hydrogen tanks, which have a double-shell vacuum-insulation structure to keep out heat. After confirming that safety would not be affected, the team was able to make the outer plates thinner.
Toyota also worked with suppliers to make various other weight reductions. These included the tank’s primary safety and boil-off gas valves, developed by Aisin.
Boil-off gas valves operate constantly to vent hydrogen as it naturally vaporizes.
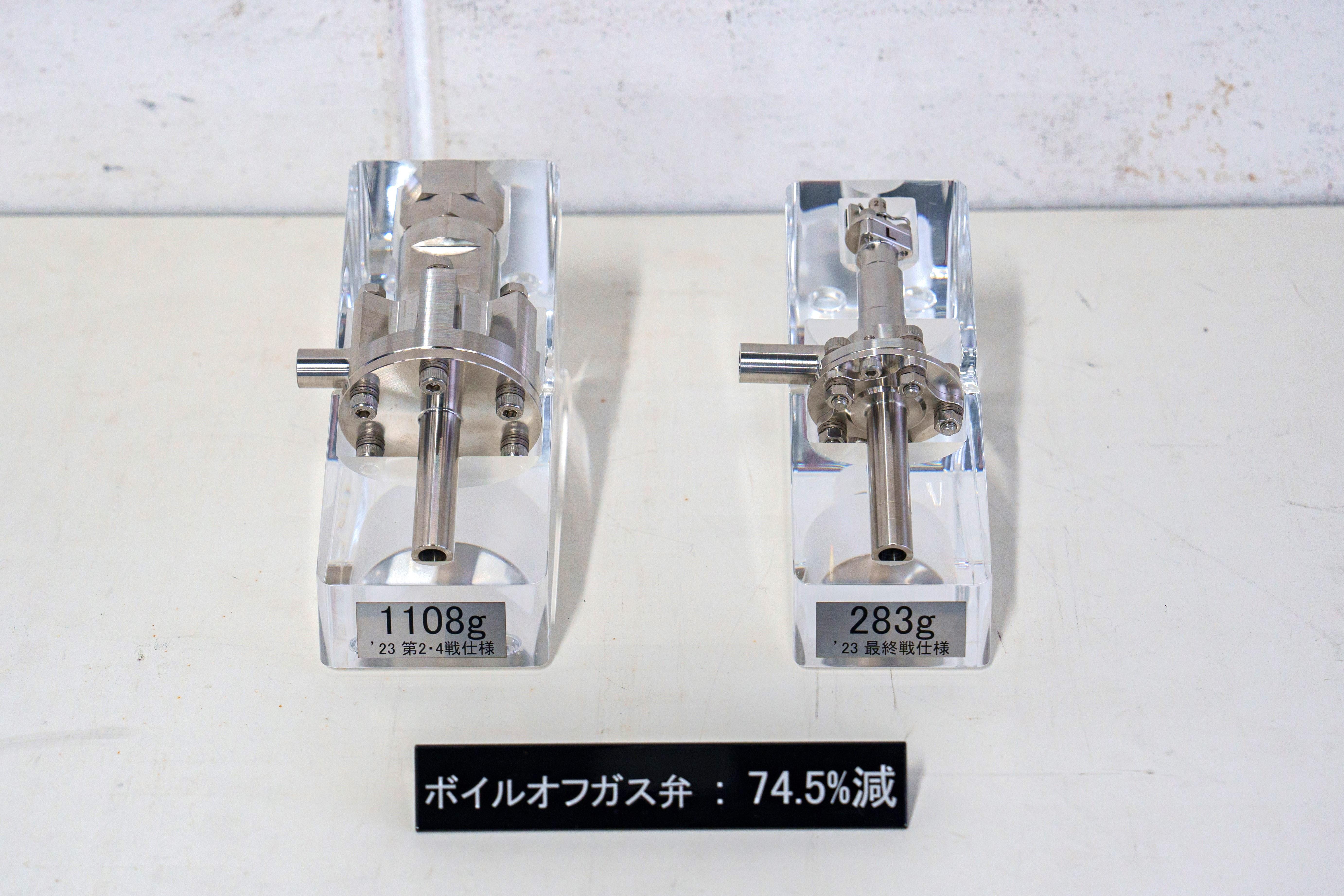
On the other hand, the primary safety valve is designed to release if the tank’s internal pressure rises abnormally, meaning it is not activated under normal conditions.
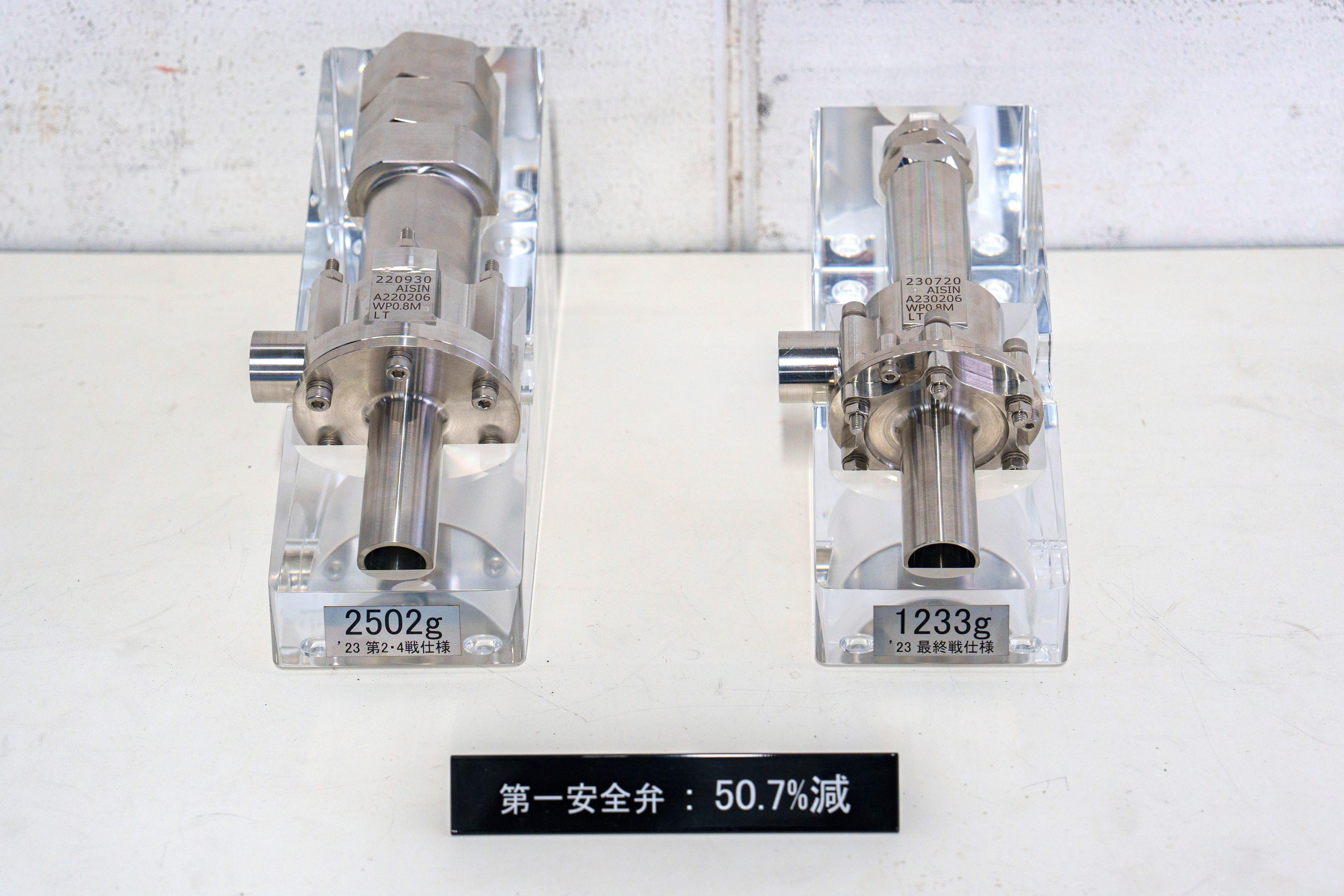
Given the liquid hydrogen system’s agile development, parts initially had to be designed before the tank’s shape and operating pressures were finalized, so safety margins were set to cover the worst-case scenarios.
As development progressed, however, engineers found that component structures and thicknesses could be slimmed down while still guaranteeing safety. They trimmed 74.5% from the boil-off gas valve and 50.7% from the primary safety valve.
Similar improvements with other suppliers continued to shave off the grams, resulting in a car that is some 100 kg lighter than in the season opener.
Upgrade 4: Improved engine performance
The engine also received a performance upgrade. In the case of liquid hydrogen, engine performance is directly linked to the efficiency of the fuel pump.
Continued improvements have enabled the pump to deliver fuel at consistently high pressures. By the final race, the engine’s output had caught up to that of gaseous hydrogen.
This progress puts it on par with the performance of gasoline engines.
After driving the newly upgraded H2 Corolla, Chairman Akio Toyoda (aka Morizo) described the extent of these improvements: “Compared with this year’s Fuji 24-hour race, my recent qualifying time was two seconds quicker [per lap]. While my skills have also progressed, it shows how much the car has evolved.”