
What does "improvements in the production process" that Toyota can contribute to mean? This is a story of a personal protective equipment manufacturer that produces protective gowns for the frontlines of healthcare, where improvements were being implemented.

On April 10, Akio Toyoda, speaking as Chairman of the Japan Automobile Manufacturers Association, delivered the following message at a press conference:
What exactly does “improvements in the production process” mean? The Toyota Times editorial team visited a personal protective equipment manufacturer, where improvements were being implemented, to learn more about the various efforts being undertaken by this company to produce personal protective gear for medical workers.
1. A rain wear manufacturer in Aichi Prefecture, Japan
Situated in Aichi Prefecture is a company called Funahashi Co., Ltd. According to the company’s website, it is a long-established manufacturer of rain wear, founded in 1921.

The website goes on to explain:
Current president and grandson of the founder, Akihiko Funahashi, inherited this “stubborn commitment to manufacturing easy-to-use products.” When COVID-19 started to spread, he had been making occasional trips to a regular hospital, and on one such visit, he learned from hospital staff that they did not have enough personal protective equipment (PPE), or protective gowns. Through further discussion, he learned that their existing gowns were unable to offer sufficient protection from droplets of saliva from the many patients who were coughing violently.
He had a hunch that his company would “be able to help using its production equipment and know-how,” and decided to rise to the challenge of producing protective gowns.
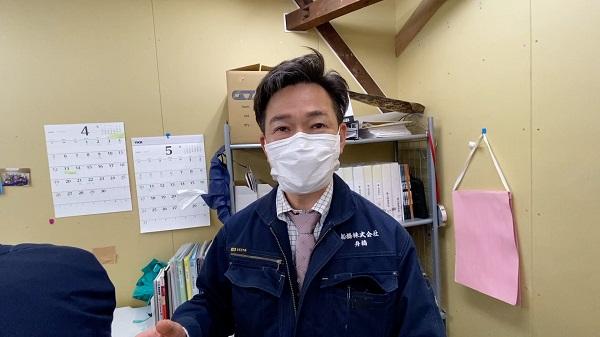
2. Monozukuri (manufacturing) that puts the frontlines of the medical sector first
The Funahashi protective gowns are already in use on the frontlines of the healthcare industry, and have a solid reputation among healthcare professionals. But what’s so great about the gown? In part, it is the company’s desire to be “faithful to customers” as expressed by founder Katsuji Funahashi. When developing the product, members of the Funahashi team got as close to the healthcare frontlines as they could.
Funahashi's protective gowns are narrow around the neck and cuffs to mitigate invasive risk of droplets.
On the other hand, they have a reputation for ease of wearing and removing. The gown has a cut at the back, which is easier to tear apart when removing it. Funahashi sticks to the thinness and softness of the material that makes less distinctive rustling sound of plastic. They also focused on the transparency of the material. This makes name tags of the doctors and nurses visible from the patients to ease the anxiety from them even a little.
Funahashi always maintains a customer-first policy, so it applied a “healthcare worker-first” thinking to its development of protective gowns.
Which brings us next to the efforts of a young Funahashi employee, Suzuka Ohnishi, when he tackled the challenge of incorporating numerous requests from the hospital as communicated to President Funahashi.
Looking back on the difficulties he experienced then, Ms. Ohnishi said:
President Funahashi also commented happily on the moment when they reached “the final check” after going through many trials:
3. As many and as swiftly as possible to help save lives
The manufacturing of protective gowns required “mass production,” which had not been required with the production of rain wear. “We had aimed to deliver as many good-quality products, as soon as possible, to the medical frontlines. However, the best we could do was 500 products a day.”
On the other hand, as the needs of medical frontlines increased day by day, the passion and action of President Funahashi began to be taken up by media.
A number of people saw the advertisement and announced that they would join in the efforts.
One of those respondents was Toyota. They offered to utilize their process improvement capabilities, already employed in automobile production workplaces, to help in production.
In the words of President Akio Toyoda, process improvement is “any improvement that can increase production by even one unit.”
Manufacturing processes, including those for both vehicles and rain wear, are made up of unique and individual “operations”, “movements” and “bridging between the processes.” If a slight modification enables you to reduce time spent on each of these actions, then time spent creating a product can be reduced and production volume can be increased.
At Toyota, this modification is called kaizen (improvement). Toyota employees, who routinely implement kaizen in their daily work, were invited to visit Funahashi.
4. Collaboration between like-minded individuals
In their efforts to achieve manufacturing operations that put healthcare workers first, the Funahashi team had another concern. They wanted to source materials that would reduce the rustling sound of plastic. They had their eyes on a plastic used for agricultural products as the optimal material, but without a supply route in place, they found procurement difficult.
There were other members who offered to collaborate after seeing the newspaper advertisements. The president of SanTerra Co., Ltd. Jinshou Nambu, a Sumitomo Chemical Group company, made a call to President Funahashi.
President Nambu of SanTerra was offering “to run its machines specially on weekends to ensure Funahashi could meet production volumes.” President Funahashi was astonished by this generous offer, but President Nambu simply replied, “But you want to deliver the protective gowns quickly, don’t you?”
As partners appeared, production of PPE became a reality.