
What does "improvements in the production process" that Toyota can contribute to mean? This is a story of a personal protective equipment manufacturer that produces protective gowns for the frontlines of healthcare, where improvements were being implemented.
9. Gathering of an alliance of seven volunteers
It wasn’t only SanTerra and Toyota that raised their hands in response to the advertisement that President Funahashi put in the newspaper.
Companies that believed “we can also produce these gowns,” also raised their hands. And this is how it came to be that seven companies, including Funahashi, would be producing protective gowns.
HOUWA CHEMICAL and Hekikai Giken produce vehicle seat covers. Futaba sansyo produces hoods for tents and trucks. SUIKOU and Okagawahousei are apparel companies, while TOYOKNIT is a competition swimwear company.
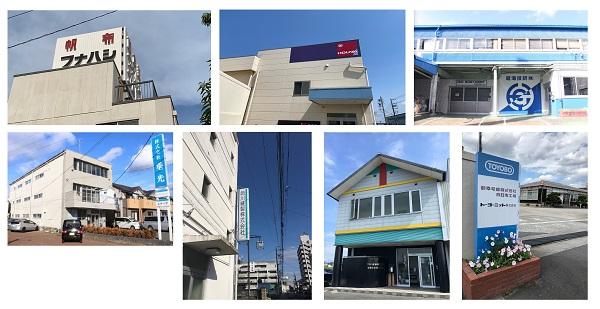
Although these are manufacturing companies, their products are different and had no prior connections with each other.
The seven companies, including Funahashi, had a few things in common, that is, “the facilities to cut (products)” as well as “people who had a light hand.” Above all, these companies, even when operations were slowing, “had management with the belief that they wanted to do something for others.”
Know-hows created at Funahashi such as “material and product shape” and “how to produce” was shared with each company, and it made the 400,000 units per month become a reality.
10. The Avengers nurture the Avengers
There are numerous Toyota staff onsite at the Funahashi plant. They are not there to help out with manpower, but to identify points of improvement by immersing themselves into the work. Their presence at the Funahashi plant is not long-term.
After reaching a decision on efficient ways to work, they traded roles with Funahashi’s workers.
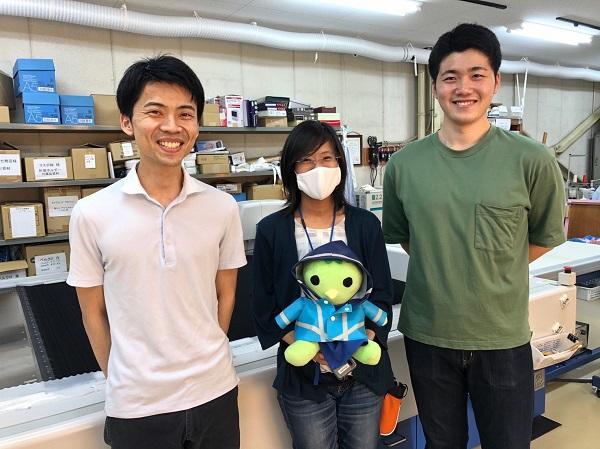
They were the experts for each process at Funahashi. For example, Suzuka Ohnishi, who initially had difficulty making the trial products, is now an expert in the process of attaching the sleeves.
Hirotaka Tatematsu is a young ace in the process of folding, and Yu Nakagawa is also a young ace of the material cutting process. These employees support each process.
Additionally, Manami Outani, who is assigned the role of external negotiations, and Takayuki Kawano, a leader of the younger members, were working on their roles to share the contents of improvement and production management under the Avengers from Toyota.
In this way, Funahashi’s younger employees worked as a core of the company while working on the production as well. Sometimes, they visited the other six companies to share the know-how.
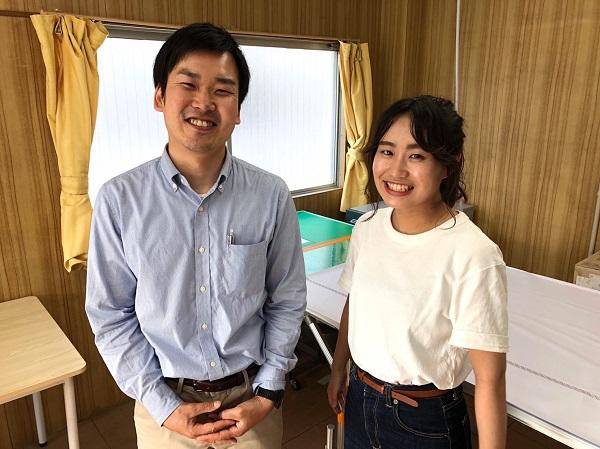
This passing on of know-how is called “yokoten” at Toyota. It is an abbreviation for “yoko ni tenkai suru,” and the same method of improvement is conducted on other processes and at other plants, and helps improve production efficiency.
An Avenger of the folding process, Mr. Tatematsu, talked about his experience as follows:
We learned that he was a new employee who started working in April. When asked, “Do you enjoy you work?” Mr. Tatematsu smilingly replied without hesitation, “I enjoy it!”
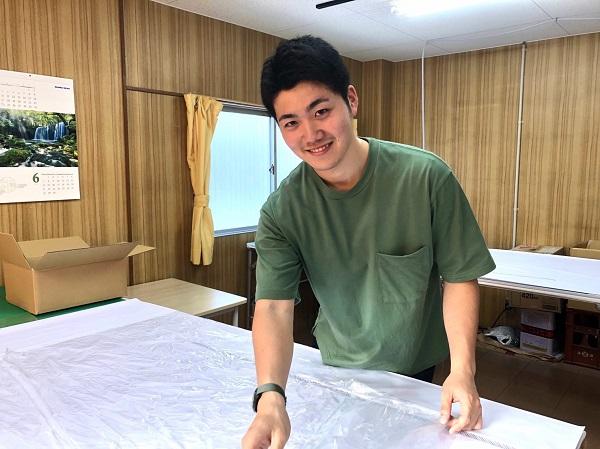
While many new employees joining the workforce this year have been faced with a tough situation, such as not being able to participate in entrance ceremonies, or having to work from home even when starting a new job, we were happy to learn that there were new employees who were able to embark on such a fresh new start to their work life.
11. Yokoten is not a one-way procedure
We would like to introduce the six remarkable companies that responded to Funahashi’s plea.
If you look at each company’s genba (worksite), there were threads of commonalities, namely, improving quality and production efficiency, including work procedures, facilities, and materials. So much so that if observing operations, you might even think, “Is this the same company?” This is proof that the passing on (yokoten) of know-how from Funahashi has occurred in an effective, timely manner.
However, this yokoten is not a one-way procedure. Each company stands out on their own for their unique characteristics and specialties, and this, too, is often passed on.
[HOUWA CHEMICAL]
HOUWA CHEMICAL conducts cutting and sewing of bedding and leather covers for car seats. This company had utilized its experience in car seats to suggest methods of cutting multiple sheets in one go.
Although they had been used to cutting thick fabric with the cutting machine, and it was their first time using the machine to cut thin plastic sheets, they were able to find a way to cut as many as 70 sheets without causing wrinkling at once, by adjusting the speed of the cutting
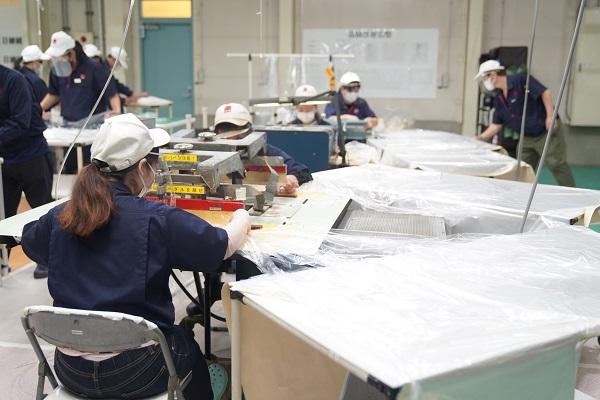
[Futaba sansyo]
Futaba sansyo is a company that handles thick plastic materials used for tents and sheets used by trucks.
The company possesses various techniques, including techniques that utilize high frequency, ultrasonic waves, and electricity, for welding plastic materials together. The thin vinyl welding used this time did not require as much heat and energy, so the most suitable and inexpensive machine for production was found. As a result, these machines were installed at all seven companies.
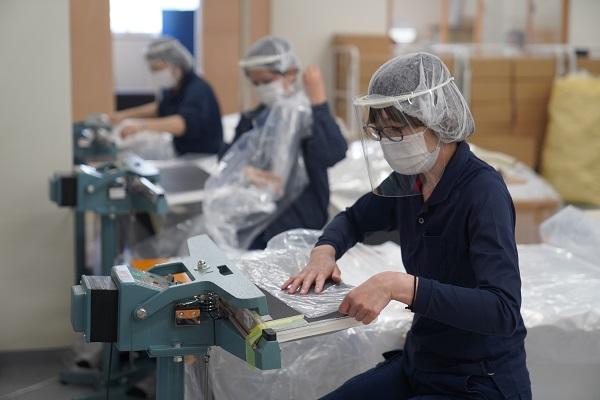
[SUIKOU]
SUIKOU produces clothing sold in department stores and is known for its exceptional handiwork expertise.
The cutting and folding of protective gear requires a high level of precision and teamwork, but what we observed at SUIKOU was a level of precision in cutting that could not be viewed as handiwork.
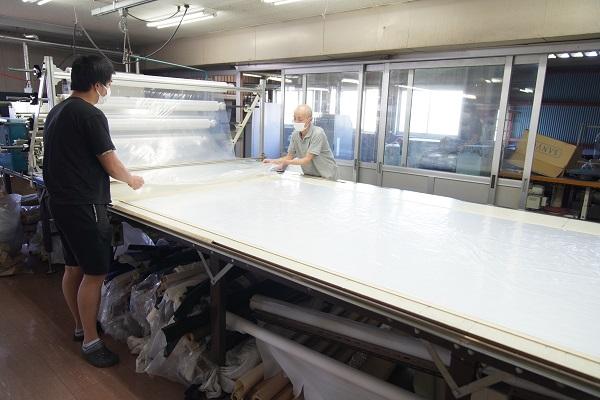
[Okagawahousei]
Okagawahousei, a company that works with women’s skirts, specializes in operation processes without any waste. They understand how an improvement can reduce time by a mere second, and implement highly detailed improvements, such as thoroughly preparing material to be used in the next step, to ensure that the overall production process is not delayed by a single minute. Through these efforts, Okagawahousei has achieved the highest production volume of 6,000 units per day among the seven companies.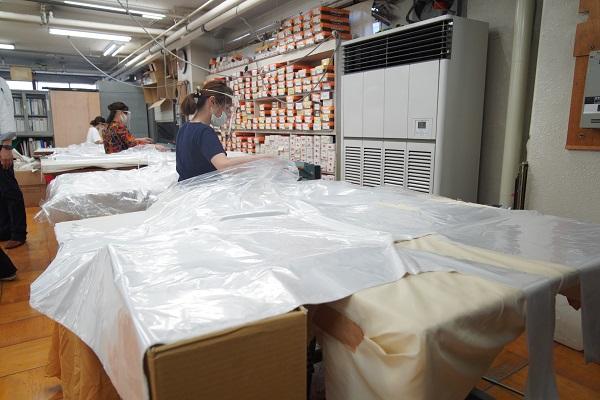
[Hekikai Giken]
The talent of Hekikai Giken lies in a production management method that utilizes their experience in auto parts manufacturing. In this method, they compare a one-hour production plan with the results, and when a difference is identified between the actual plan and the results, they try to identify the reason and then work to resolve it. This production management method played a key role in the production of protective gear.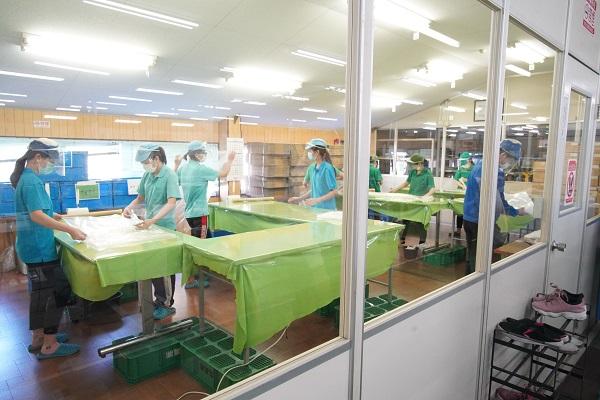
[TOYOKNIT]
TOYOKNIT is a manufacturer of swimsuits and sports uniforms.
Their level of commitment to quality left a lasting impression on us. If there’s a quality defect at one company, the information is shared with each company shortly. When a problem with a cuff on one of the completed products was identified, they opened all boxes so that all completed products that had already been packaged could be checked. Their commitments to quality has been shared by each company going forward.
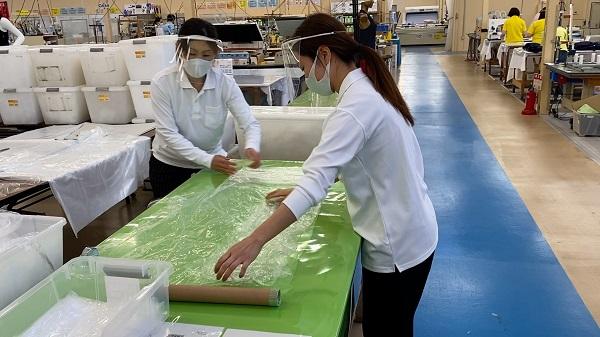
We can see, then, how the expertise of each company is passed on, and that the production volume actually increased.
Currently, as of May 20, the production volume of all seven companies is 25,000 units per day, and 500,000 units per month, and have already exceeded our goal of 400,000 units per month.
12. What we already had in common (that wasn’t passed on)
Separate to the know-how that was passed on, there are two aspects the seven companies of the alliance of volunteers have in common.
One was the drive to produce as many protective gowns as swiftly as possible.
Of course, each company has faced various challenges in light of the COVID-19 pandemic, for example, waning demand for products and slowing operations. They have gone to get other work to secure employment for their employees and somehow continue their operations.
However, before it reached that point, there emerged a strong desire to do whatever they could to help others experiencing difficulties, and this desire is expressed by the words, “producing as many protective gowns as swiftly as possible” from each company.
Another commonality could be seen in the lively demeanor of the employees, in the way that they were smiling and communicating.
Each company employs quite a few people from overseas. While the current situation makes it difficult to know when they can return to their countries, they can work with pride knowing that their efforts are contributing to the medical frontlines, and can share this with their families back home.
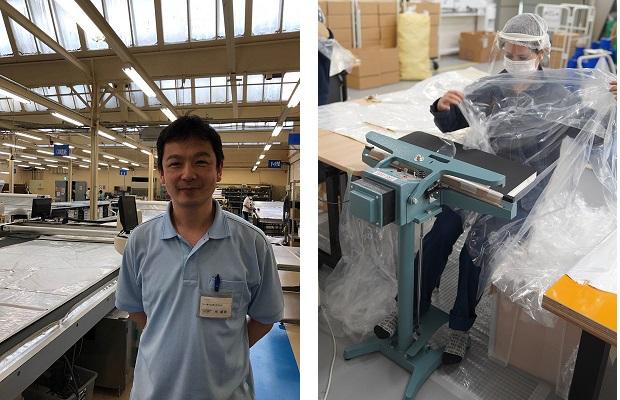
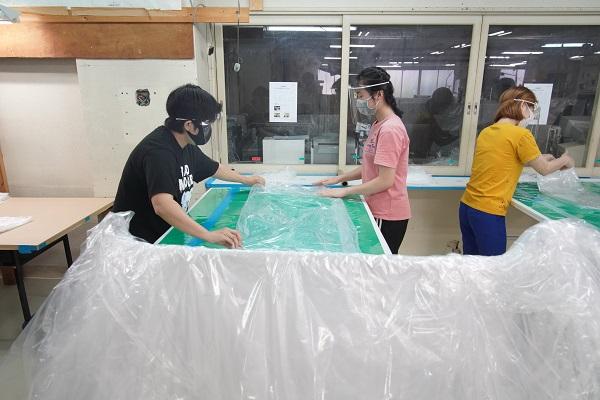
Takashi Mori, Funahashi’s plant chief, spoke about the experience of being involved with the production of protective gear:
Honestly, I have hardly rested this month. Every day I wake up early and work until late. Sometimes I catch the last train at night. My body is okay, and every day I enjoy being able to see the production numbers continue to steadily rise.
I did not think we could produce this many products. I can’t believe we were able to do this ourselves. My biggest take away from this is that I am left with more confidence and motivation. I’m sure what we experienced and learned through these efforts will be utilized for improvements in our production and operation going forward.
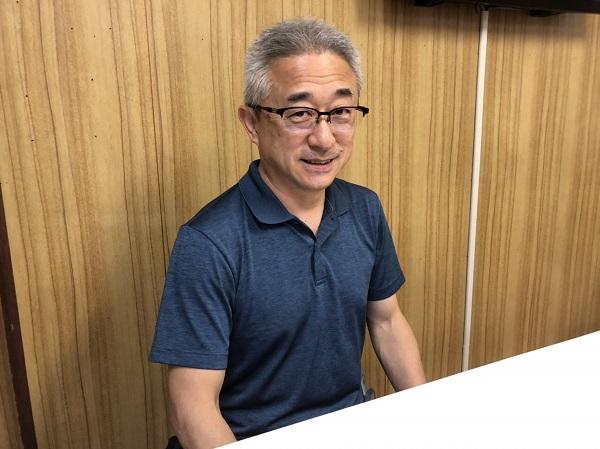
13. Continuing to protect monozukuri
President Akio Toyoda made the following remarks at Toyota’s financial results press conference:
We have continued to protect people with skills and expertise, who can make things that are needed when help is needed.
I want to create a place where such people can grow and be protected, here in Japan. Even now, as we are facing the COVID-19 pandemic, this desire within me is unwavering.
Irrespective of the size of the company, no matter how difficult the situation you find yourself in, or rather, because you are now experiencing a time of extreme difficulty, there are many companies in Japan that have grit, and protected people with skills and expertise. I believe, now, more than ever, we need a society that supports such companies. Through monozukuri, please lend your support to the companies that have supported the Japanese economy and this country.
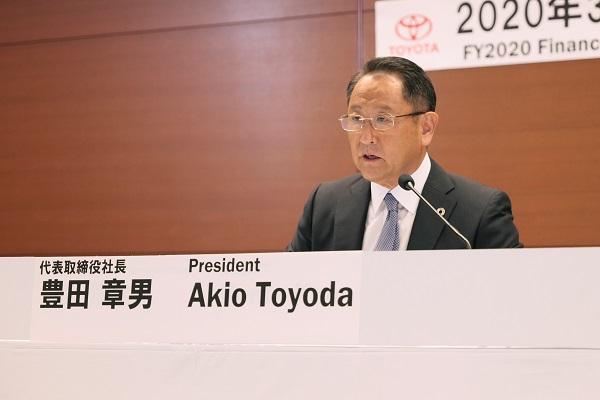
Protecting the people, skill and expertise involved in monozukuri in Japan made it possible to produce such medical protective gears this time.
Even under these difficult circumstances during COVID-19, the skills and expertise behind monozukuri continue to advance.
We must pursue a higher step in our endeavors, while continuing to protect monozukuri even further with a tough mind and strong will, moving forward.14. A tale of two “Funahashis”
Japanese readers would have noticed that “Funahashi” is written in two different ways in this article. This is not an error. The company name is written one way, and the president’s name is written using a different Chinese character, or kanji.
The family name Funahashi means “boat bridge,” but when founder Katsuji Funahashi started his company, he named it using a different character, which translates as “ship bridge.” The reason behind this change is that he wanted his company to become a large ship rather than a small boat. That way, the company could help carry others in times of trouble. Likewise, if the company found itself in trouble, others could climb aboard to help. From this perspective, the choice of this name perfectly suits the company.