
What does "improvements in the production process" that Toyota can contribute to mean? This is a story of a personal protective equipment manufacturer that produces protective gowns for the frontlines of healthcare, where improvements were being implemented.
5. Toyota members join Funahashi to improve operations
Manufacturing of protective gowns consists of largely four separate processes:
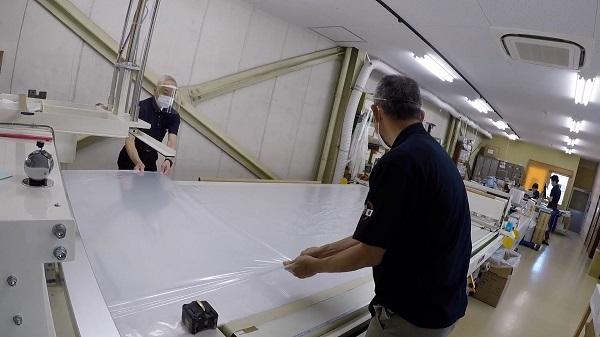
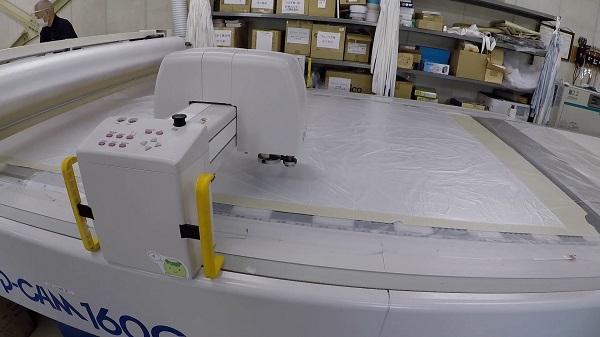
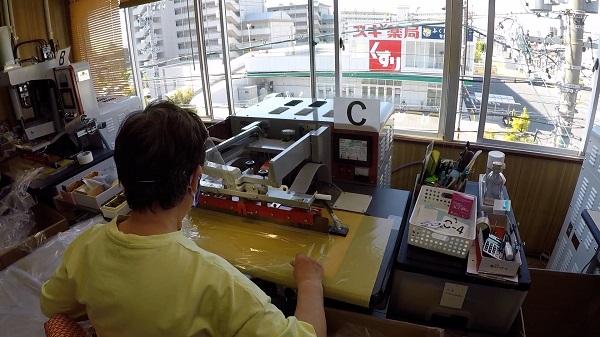
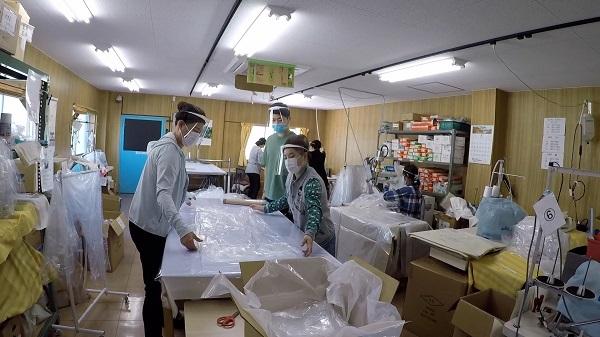
The first thing the team from Toyota did when they arrived at Funahashi was to help with manufacturing operations. On the fourth day the Toyota Times editorial team also joined the site to gather information for reporting. Everyone worked together harmoniously, as if they had always been colleagues. In fact, it was hard to distinguish between the Toyota employees and Funahashi employees.
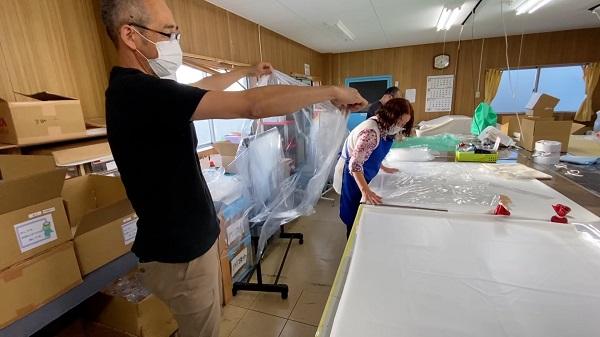
Incidentally, when Funahashi employees first heard that Toyota members were coming to help, their expectations were not that high. On the day of arrival, they were expecting to see only a single, younger worker from Toyota.
As President Funahashi went to welcome Toyota members, he was surprised to see eight experienced-looking older people approaching him. With each one looking unexpectedly dependable, he laughed while remarking, “I thought they were the Avengers!”
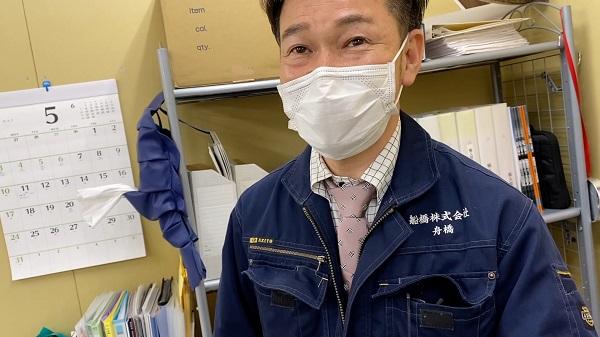
The first step for “the Avengers” in their efforts to implement improvements was to actually start working there. Alongside the Funahashi team, they tried to identify where the difficulties were and the obstacles that led to delays.
The first major obstacle identified was the “imbalance in capacity between processes.”
The equipment used in the “protective gown pattern cutting process” (No. 2 above) could cut out as many as 30 sheets at once. However, the equipment used in the material length cutting process (No. 1 above) could only cut 10 sheets at once.
This meant that the 20-sheet capacity of the pattern cutting process (No. 2) was put to waste. Then, they moved on to consider “how we can operate process No. 1 three times faster.”
6. Correcting the capacity difference
New machinery was not installed for process No. 1. Instead, while working together, they were able to identify small changes that made manufacturing easier.
There are two main operations to complete in process No. 1.
This is like using plastic wrap in the kitchen, only a bigger version.
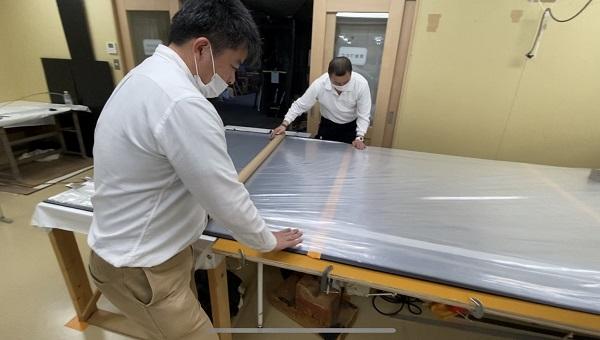
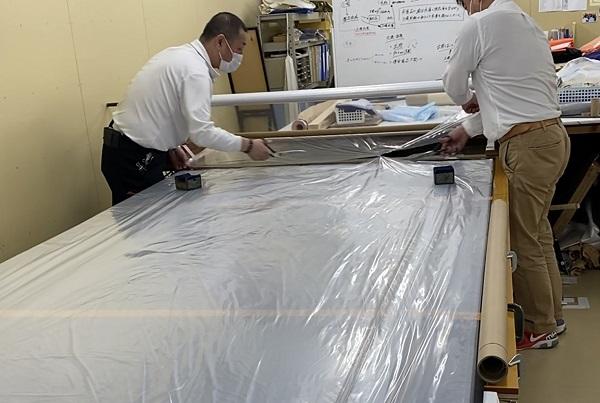
The Avengers looked for the difficulties in completing these operations.
When drawing the plastic from the roll at process No. 1, it is necessary to draw it out to a certain position. Their workbench was white. However, the more sheets of clear plastic they collected on the bench, the more the plastic became a milky white color and obscured the borders of the white workbench. They made the decision to change the bench color to black, and as a result of this simple change, they improved the ease of working to a surprising extent.
In addition, they prepared the clips and weights to stabilize the drawn materials. Then, they made the original scissors box to get them easily. The efficiency of work improved surprisingly through these efforts.
While actually doing the work, they noticed other issues as well and made improvements. While they could originally only cut 10 sheets in this process, after four days, they were able to cut 30 sheets.
During the process of attaching arm sleeves, they noticed there was a machine that hadn’t been used for fifty years. Although the machine was old, it worked correctly after the maintenance.
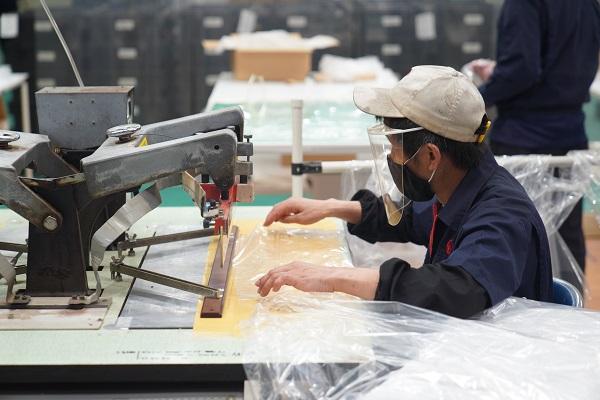
They worked on not only increasing the tools and equipment, but also on reducing the work time.
Initially, it had taken 90 seconds for beginners and 70 seconds even for
veteran workers to attach an arm sleeve. However, they shared the know-how and summarized them in a video. By sharing these know-how, currently, fast workers can cut it out in just 30 seconds, and even the beginners can do it within 60 seconds.
7. Value created by a one-minute improvement
In addition to improvements in operations, improvements can also be made to the “flow of items between processes.”
After process No. 3, the finished products are folded and packed in process No. 4.
Previously, in process No. 3, after the sleeves were attached, products – still wrinkled – were placed (practically dropped) in the adjacent box.
Then, during process No. 4, the worker would “remove the wrinkled product from the box → unfold → check the front and back, then the inside and outside → unwrinkle → fold → put into package.”
Obviously, writing it all down like this, you might wonder why the products needed to be packed into boxes. We learned that, “If they are put in the box in a wrinkled state, we would obviously have to unwrinkle them.” And kaizen (improvement) measures can be implemented to target this example of “waste,” or wasted activity.
In this way, the improvement itself seemed so simple. “If we go to the trouble of smoothing out the wrinkles, then why don’t we make them wrinkle-free in the first place?”
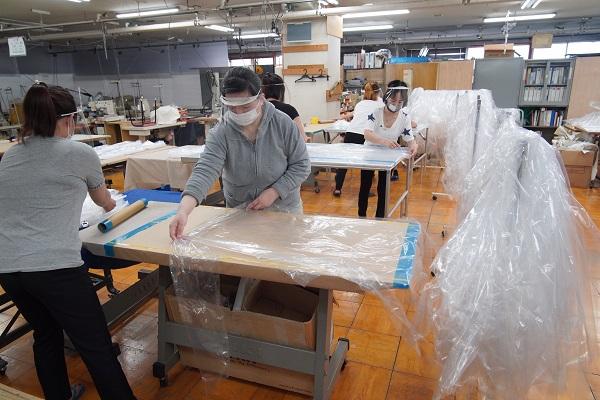
Instead, they decided to use commercially available clothing racks, and just hang the gowns there ready for transfer to the next process. In this way, the products didn’t get wrinkled. And no one had to go out of their way to check
the front and back, nor the inside-out. Time for this operation was reduced by “one minute.”
Now, a one-minute reduction might seem insignificant, but Funahashi’s agreement with the government was to deliver 400,000 gowns.
By saving one minute per gown, they could save a total of 400,000 minutes, which is a total of 6,666 hours, or 277 days. This accumulation of one-minute savings is what led to the achievement of “as many and as swiftly as possible.”
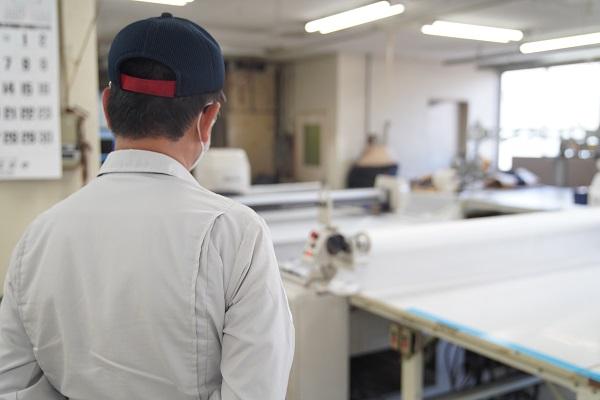
In addition, every kaizen solution applied was the result of wisdom and the implementation of slight modifications. Difficulties will become the seeds of improvement. By facing these difficulties one by one, we think of ideas on how to improve them, and don’t rely on automation easily. These improvements did not involve a large investment. At some point in the future, with such large quantities of protective gowns no longer being required, Funahashi will be thankful that they did not invest in equipment that is only needed for a limited time to meet temporary needs.
The Avengers also stated:
8. Agreement to deliver 400,000 protective gowns
Funahashi’s protective gowns are to be supplied to government agencies first. From there, they will be distributed to healthcare institutions, and will not be officially sold.
One day, a teleconference was held to discuss delivery methods and quantities to supply, attended by representatives of the ministries and agencies, President Funahashi, and one member of Toyota’s Avengers.
The government official asked how many gowns Funahashi was able to manufacture. And the Avenger answered this question as well.
He said:
For a moment, President Funahashi could not believe his own ears. Originally, the company’s production capacity was just over 10,000 units per month. Productivity improvements are one thing, but this would be a 40-fold increase.
President Funahashi was looking back on the passion of the day that inspired him to achieve the challenging target with surprise.
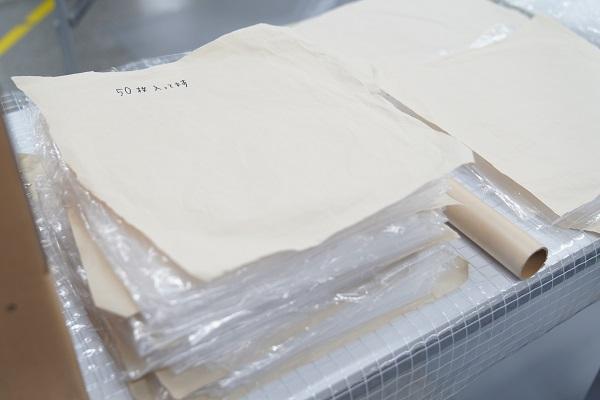
When Toyota Times first reported on Funahashi, the Avengers were already four days into their visit. At the time, production capacity was 2,000 units a day (40,000 units a month), which was four times greater than before.
Then, when we reported two weeks later - after Golden Week - Mr. Mori, head of the Funahashi plant, reported on the production achievements of the previous day at the morning meeting.
He said:
4,101 units cut, 4,262 units processed, and 4,199 units folded.
We managed to accomplish 4,000 units amongst all the divisions. Especially in the folding division, we have accomplished more than the previous day, each day. So everyone, let’s continue cooperating with each other, striving toward achieving this big goal.The production capacity grew to 4,000 units a day, which was eight times greater than the original amount. Or in monthly terms, 80,000 units. Improvements in productivity were obvious. Even so, with only a single company – Funahashi – the promised 40,000 units per month could not have been achieved.
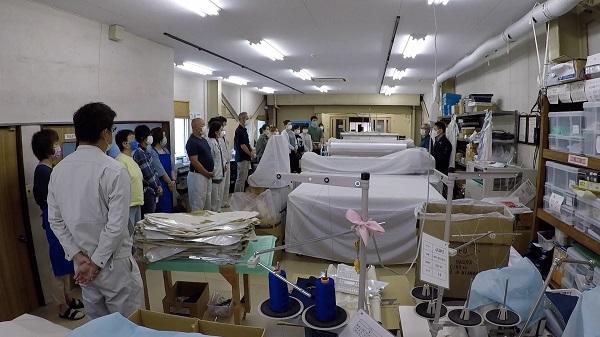