
「新しいカタチのスポーツSUV」として登場したクラウン スポーツ。同車における「もっといいクルマづくり」のためのさまざまな挑戦について、開発メンバーに話を聞いた。
700回の失敗を乗り越えて……
「見て」“WOW”と感じてもらえるようこだわったのが、“リヤフェンダーの意匠”だ。
クラウン スポーツの外形デザインのリーダーを務めた小出幸弘は、同車ならではの俊敏な走りをボディ形状で表現すべく、エモーショナルなデザインにこだわったと語る。
小出
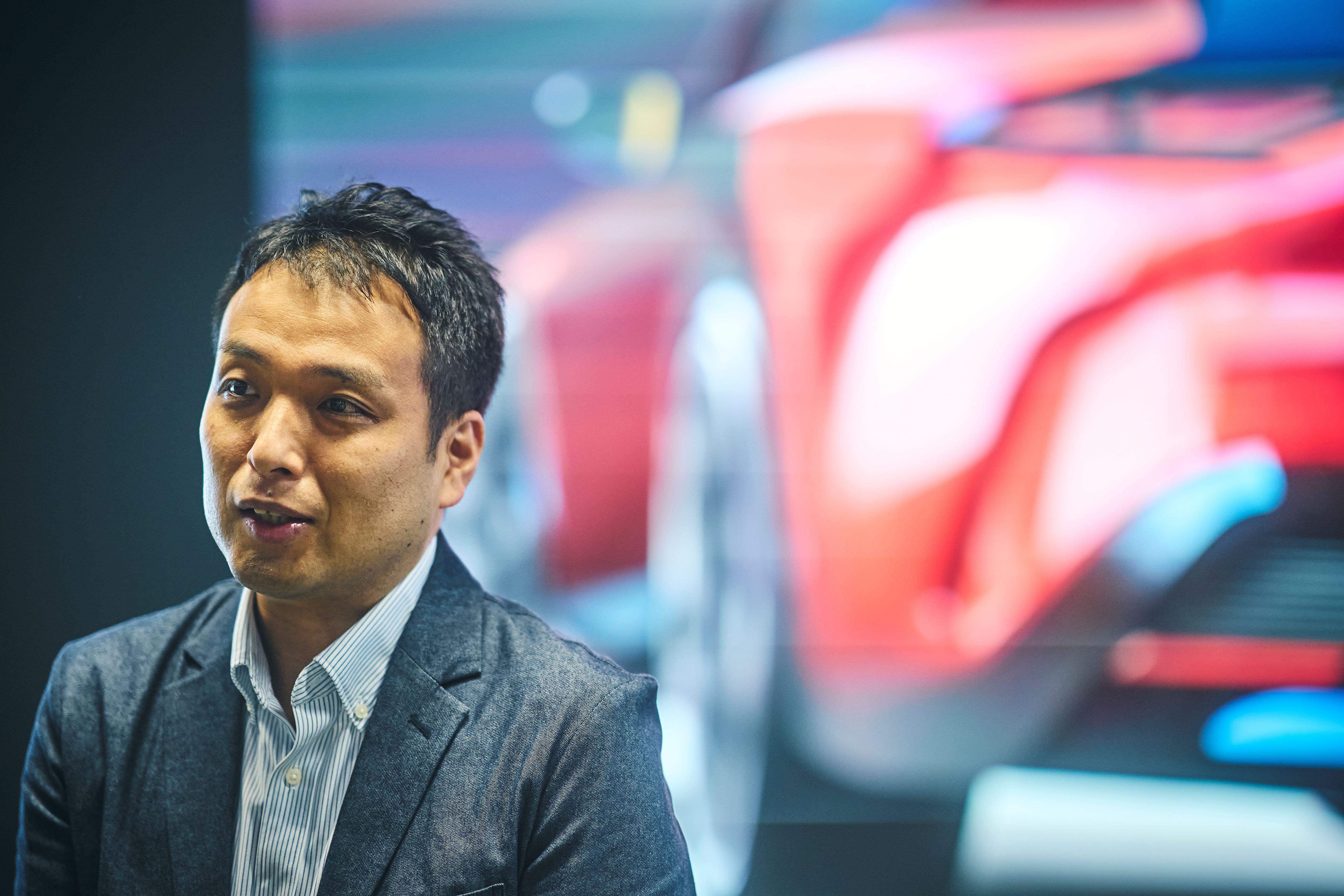
クラウン スポーツの21インチという大径サイズのタイヤに加え、足まわりの力強さをリヤフェンダーで表現したいと考えました。
また、クルマのデザインではボディ側面にキャラクターラインを入れるのが一般的ですが、クラウン スポーツではあえて入れず、ボディ面の抑揚だけで人々の感情に訴えるようなダイナミックさを表現することにこだわりました。
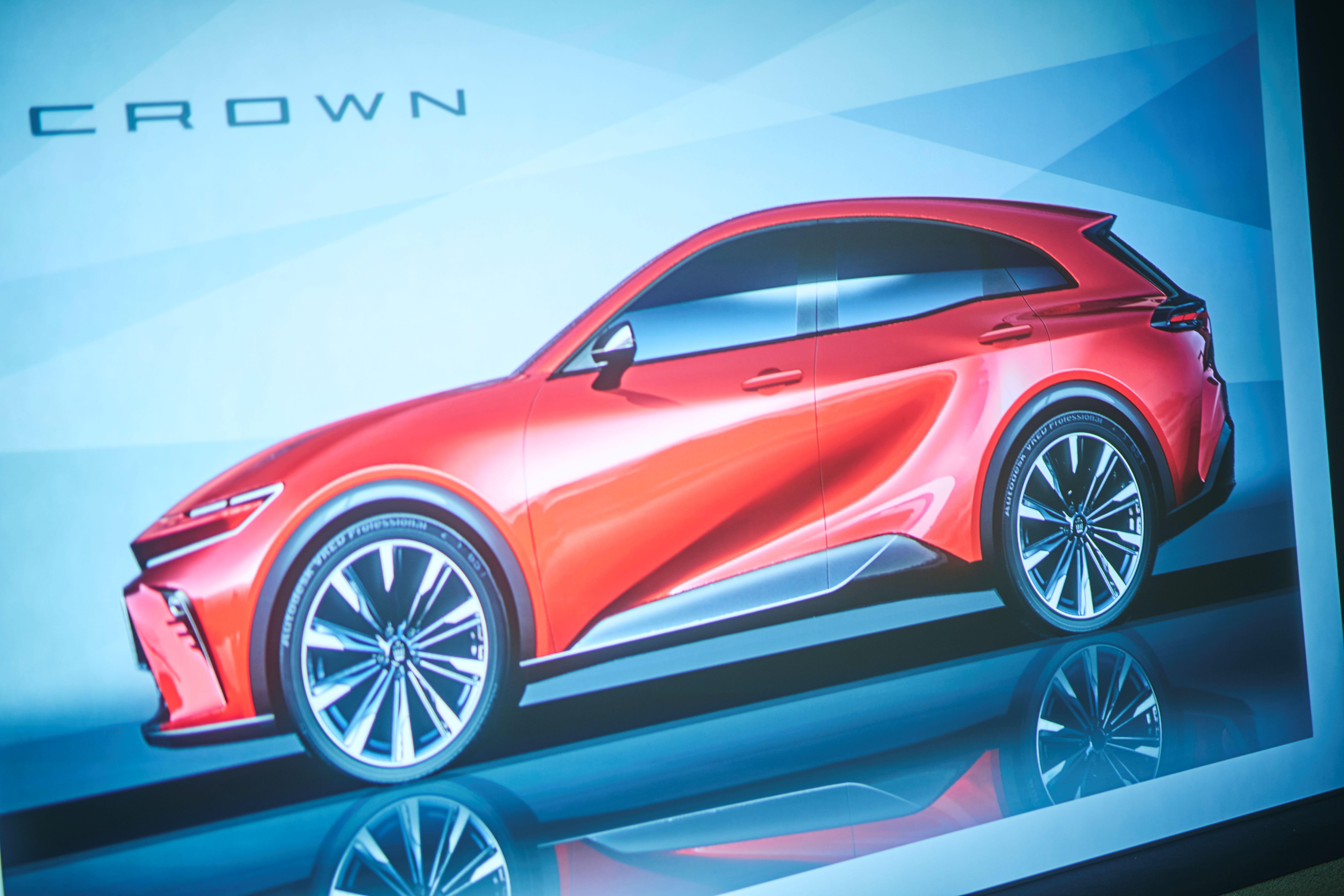
従来のトヨタ車にはない、大きく張り出したリヤフェンダー。小出は、キャビン後方(リヤフェンダー上部のサイドウィンドウ部分)やボディ側面(リヤドアの辺り)を絞り込むことで、実際の張り出し以上に力強さが感じられるようデザインをつくり込んだという。
小出
ボディ面の抑揚が大きいので、走っていると写り込みによってさまざまな表情を見せるのですが、それが本当に奇麗で……クラウン スポーツならではのエモーショナルさや艶やかさを表現しました。
この意匠が実現できたのは、生産技術メンバーのおかげです。
生産技術のエンジニアとして新型クラウンのプロジェクトに参加した福田幸介は、2016年に入社して以来、プレス生技(現 製品化製造技術部)という部署に籍を置き、一貫してリヤフェンダーをプレスするための生産技術や金型の設計に携わってきた。
福田
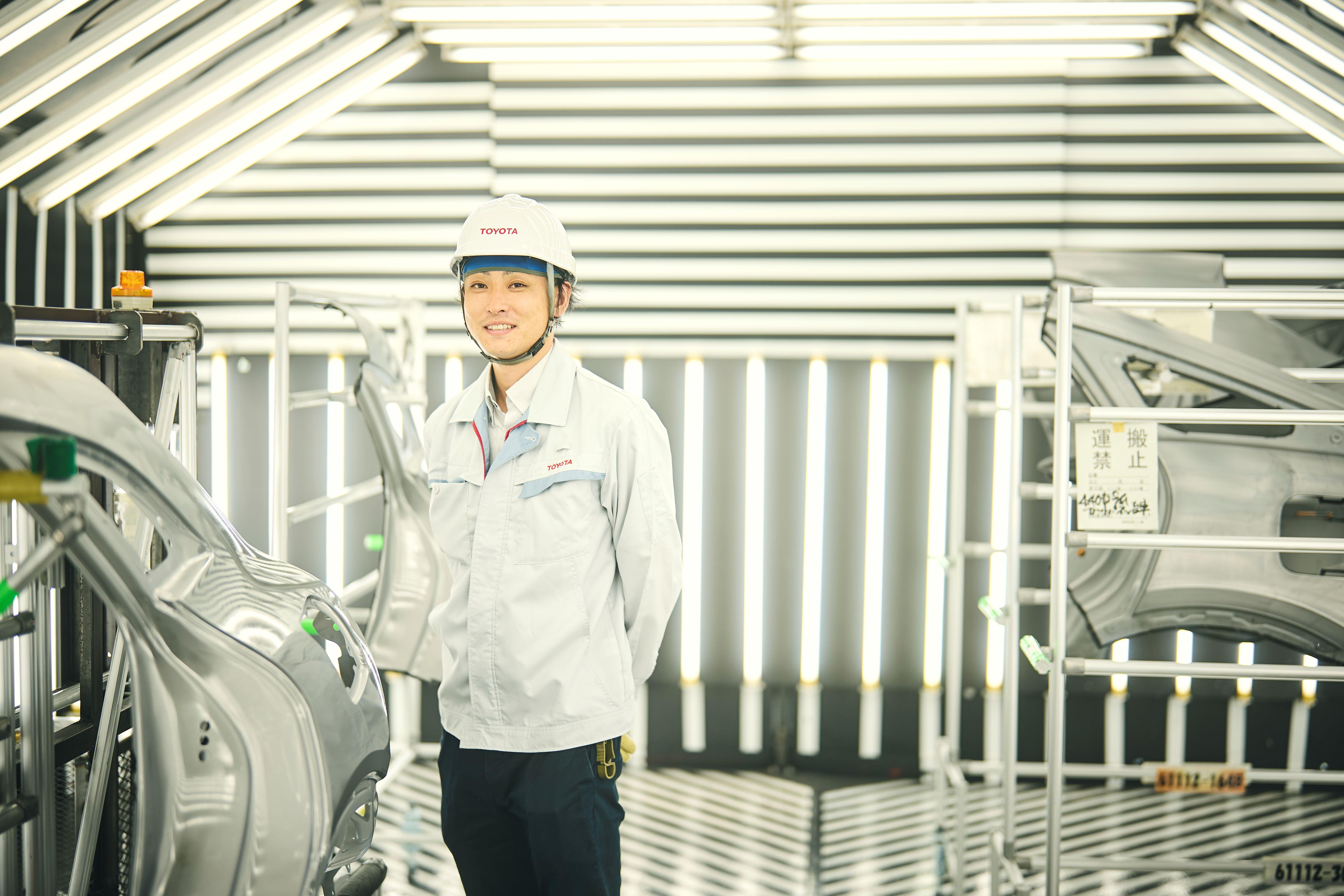
私の仕事は、開発中の車両について、デザイナーたちと一緒になって「こういうデザインならば、こういう方法でつくれる」といったように生産方法を検討し、プレス金型を設計することです。
通常はプレス金型の設計までを手掛けるのですが、クラウン スポーツはかなりチャレンジの多いクルマでしたので、金型の設計・製作後も量産評価から生産開始まで一貫して担当しました。
そんな福田が絶大なる信頼を置くのが曽場充士だ。
リヤフェンダーの美しい面を実現するには非常に高い精度が求められ、設計データと寸分たがわぬ金型を作りこむ必要があった。そのため、金型を工具で削ったり、溶接で肉盛りしたりして調整することでボディのひずみを消すなど、ボディパネルの精度を高める作業が必要になる。
曽場は、そんな作業を手がける金型のスペシャリストだ。
2007年に入社し、2年間は技能五輪の選手としてヤスリを使って金型を仕上げる技を磨いた曽場。2009年に金型を製作する部署(モビリティツーリング部)に異動して以来、金型の調整を担当してきた。
曽場
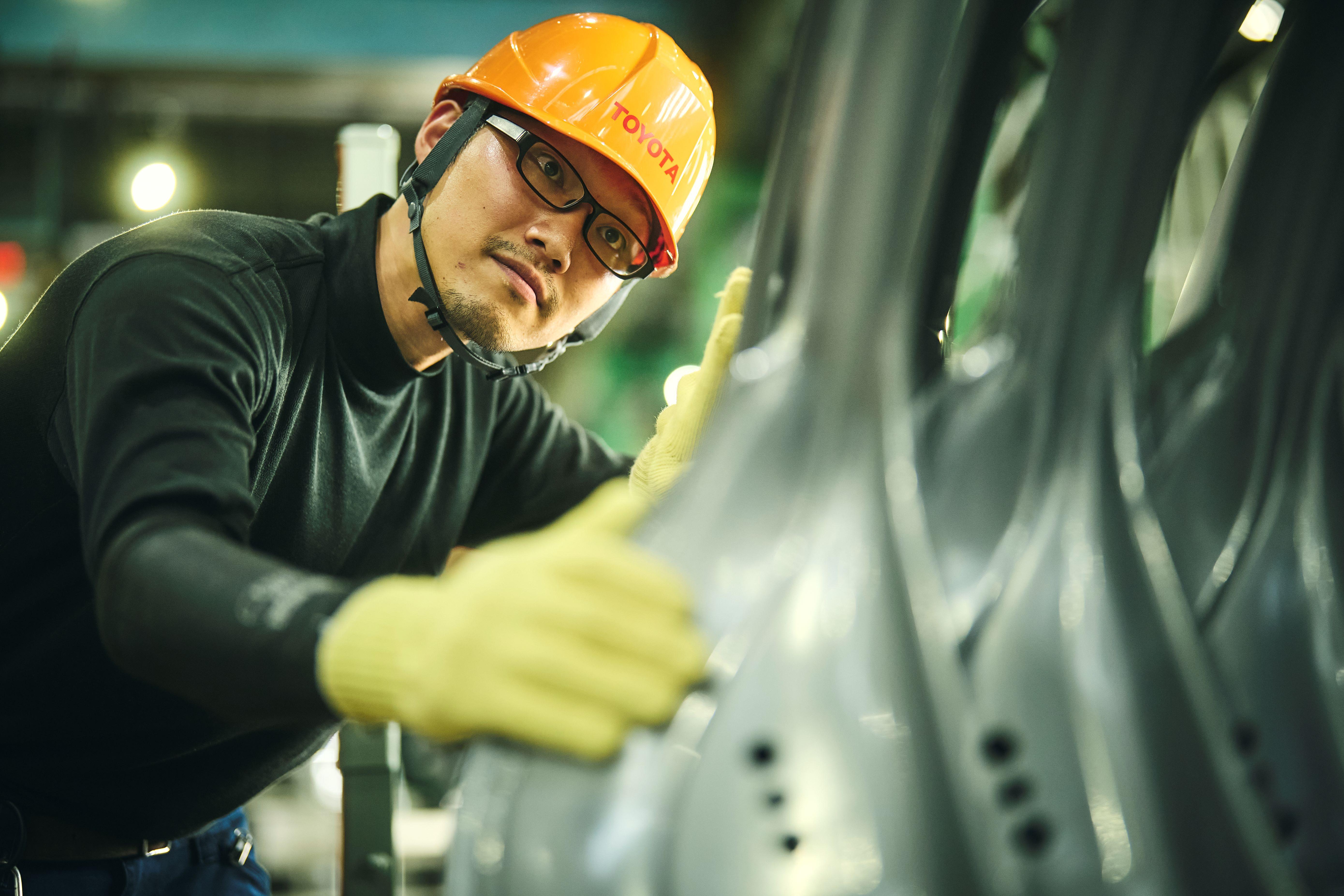
クラウン スポーツのリヤフェンダーは、金型一筋でやってきた私から見ても「とても深いな」というのが第一印象でした。
通常、福田のような生産技術担当者がプロジェクトに参加するのは、外形デザインがある程度かたまったタイミングが一般的だ。しかし、このチャレンジングな意匠を実現するため、小出は少しでも早くデザイナーの想いや意匠の方向性を共有したいと思い、通常より早い段階で、まだ造形途中だった1/1スケールのクレイモデルを福田に確認してもらったという。
福田
初めてクレイモデルを見たときは本当にかっこ良くて、何とかこのままの形で世に出したいと思いました。実現させるのはかなり難しいだろうな、というのが正直なところでしたが……。

ボディの張り出しが大きいとパネルを成形する量が増える。それによってパネルの一部に応力が集中、もしくは分散することで、ひずみが生じたり、割れやすくなったりする。そもそも、成形量が増えることで、奇麗な面の品質を担保するのも難しくなるという。
福田
3次元のCAD(Computer Aided Design)システムを用いて、コンピューター上で金型を設計し、シミュレーションにかけてテストするのですが、どうしてもうまくいかないんです。
4カ月かけて700回ほどトライ&エラーを繰り返しましたが、失敗の連続で、さすがに心が折れそうになりました。
そんな状況を打開するきっかけとなったのが、上司からの「無茶してもいいぞ」という言葉だった。
福田
私たちエンジニアには「設備はこう使うべき」とか「金型はこうあるべき」といった、ある種の固定概念があります。
それらをいったん取り払って、もっと柔軟に、今まで使ったことないのような設備の使い方や、金型の動かし方にチャレンジしてもいいと上司から言われて、気持ちが楽になりました。
新しい挑戦を繰り返す過程で、福田は今までにないつくり方を思いついた。
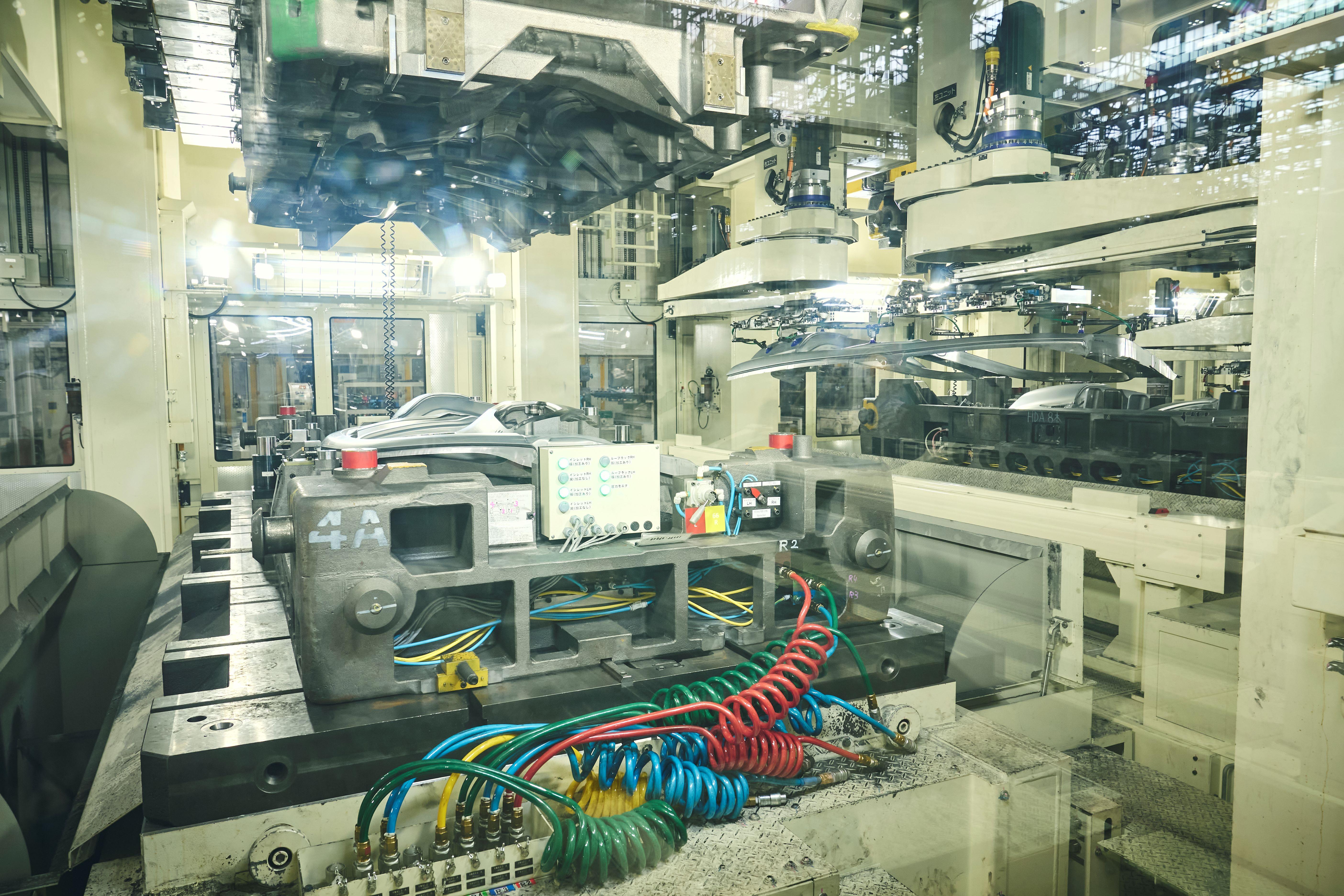
一般的にプレス加工では、固定された金型に材料となるパネルを押し付けて成形するが、プレス中の材料が理想的に成形されるよう、本来固定される金型を少し動かすようシミュレーションしたところ、うまくいくケースがあったという。
ただ、0.7秒の工程で金型の動きを調整しなければならない、非常に難易度の高い作業。福田たちはテスト用の金型を製作し、開発した新工法がシミュレーション通りになるか、実際にプレス試験を行った。
福田
テスト打ちをしてみたところ、案の定、不具合がたくさん発生しました。解決のためには、金型を1000分の1ミリ単位で調整する必要があるのですが、そこで重要になるのが曽場さんのような匠による技能です。
不具合が出るたびに、エンジニアによる技術的なアプローチと、匠による技能的なアプローチを繰り返しながら、仕上げていきました。
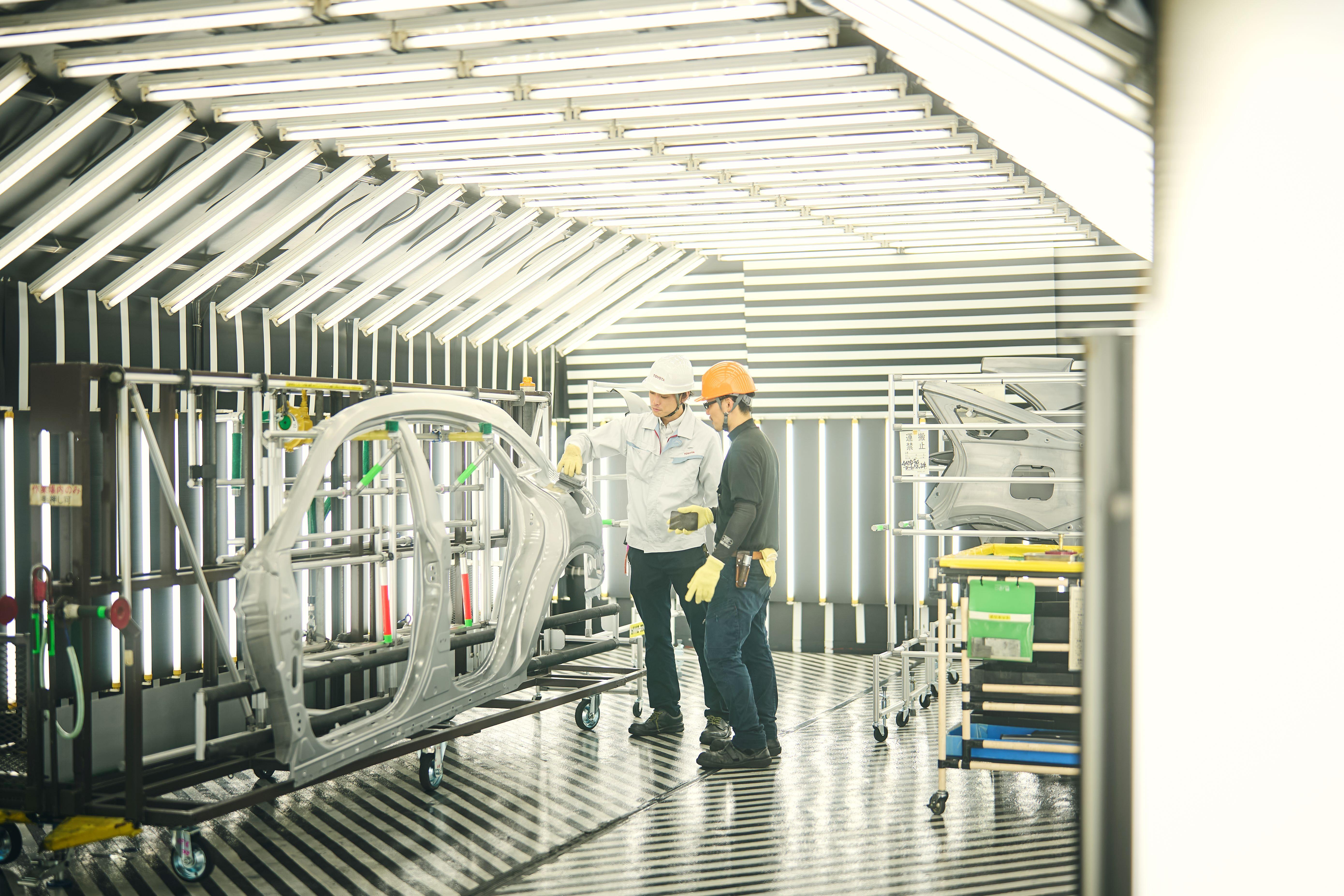
曽場
クラウン スポーツのプロジェクトに携わった同じ部署のメンバーでは、僕が一番金型をいじくり倒したと思っています(笑)。1週間、同じ箇所を調整し続けたこともありました。
個人的には、この金型の調整を担当させていただいて、鍛えられましたし、すごくいい経験をさせてもらいました。
こうして大きく張り出したリヤフェンダーの実現が可能となり、最初の試作車を目にした小出は、「本当に感動した」と感慨深げに振り返る。
小出
試作車が私たちデザイナーが目指した通りの意匠に仕上がっていて非常にうれしかったです。
この意匠が実現できたのは、ワンチームとして力を合わせて困難に挑戦していこうという想いが、部署を越えて一致した結果だと感じています。
福田
難しいから妥協するのではなく、技術で実現させるのはエンジニア冥利に尽きます。今回の経験を活かして、別のプロジェクトでも挑戦を続けていきたいと思っています。
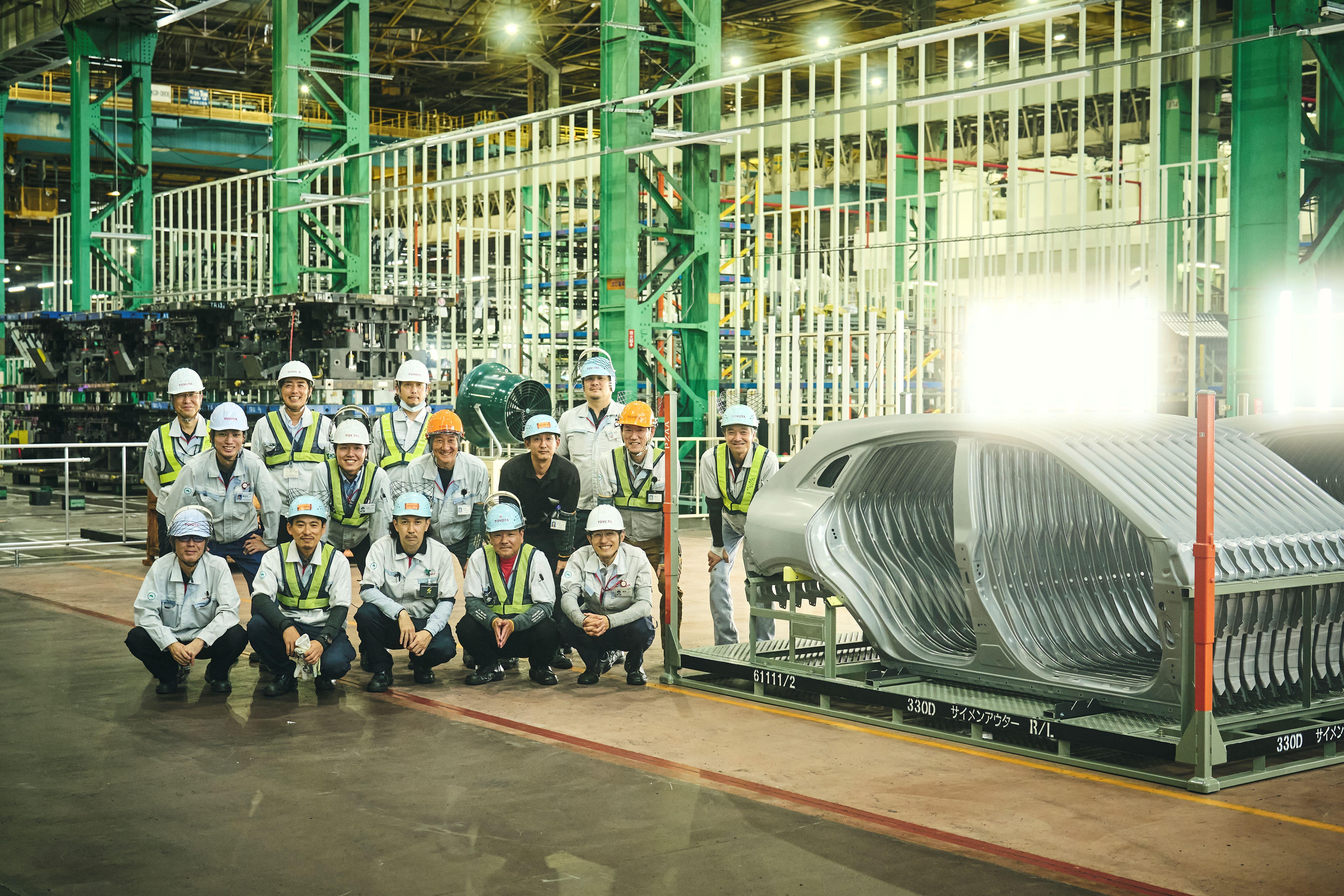