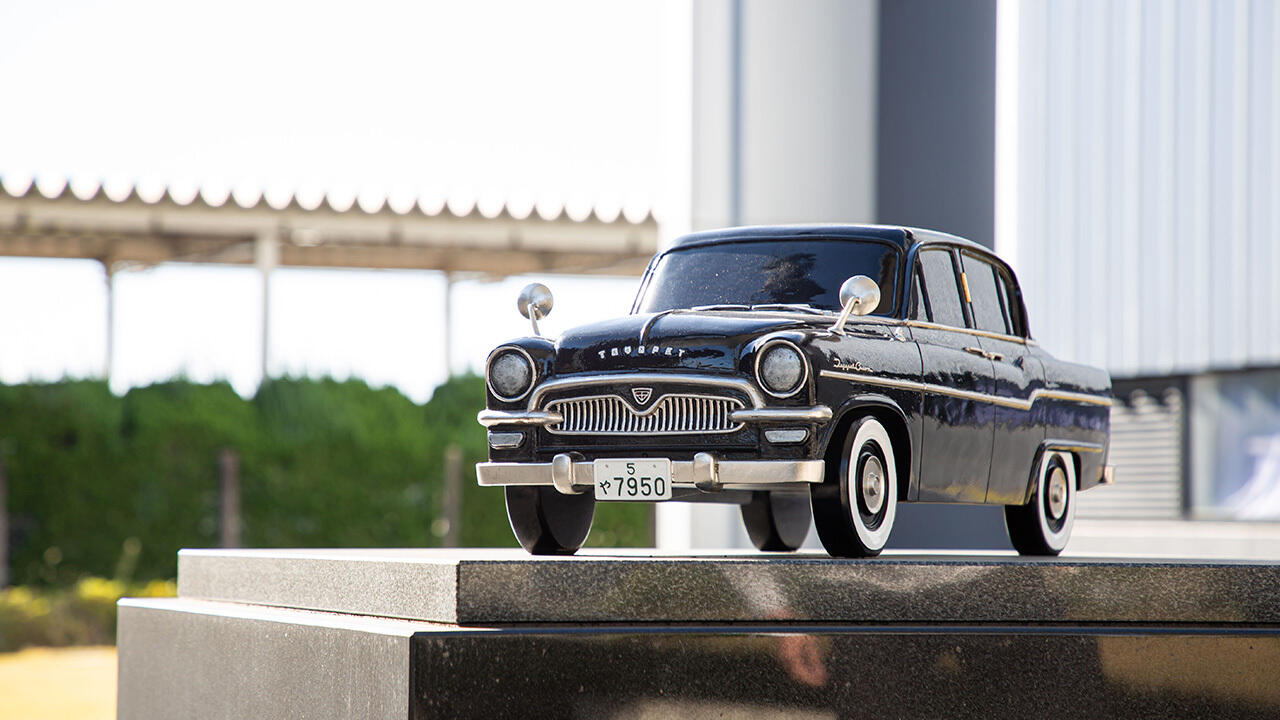
2020年から5年で15のクルマを立ち上げた元町工場。「何でもつくる」「どんなクルマでもつくる」と立ち上がった先人が築き上げたのが「多品種少量生産」だった。歴史を紐解きながら、今も脈々と受け継がれる精神、技能に迫った。
「やるしかない」切り開いてきたチャレンジ集団
決して順風満帆ではなかった歩みの中で芽生えた多品種少量生産。その実現に必須なのが、形もパワートレインも異なるクルマを同じラインで流す「混流生産」だ。
組立部 第1組立課 北井和広副課長は次のように語る。
組立部 第1組立課 北井和広副課長
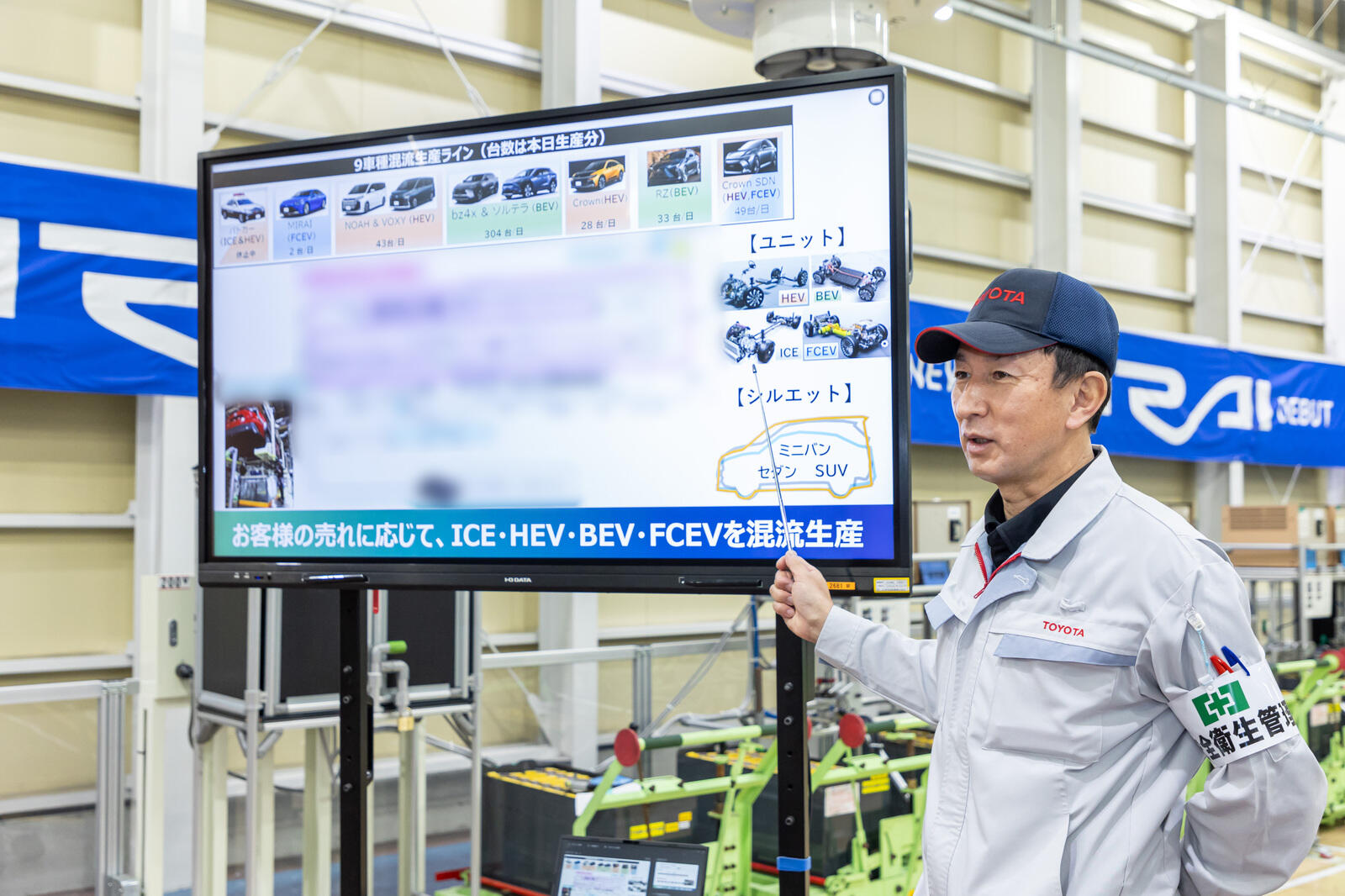
ここで働く我々はマルチパスウェイを実現するためにさまざまな改善をしています。多様性の時代、人に優しい工程をつくるとともに、働いていてやりがいを感じられる取り組みも進めていかないと、マルチパスウェイは実現しないと思います。
バックドアのワイヤーハーネスの取り付け1つを見ても、セダン系は通常の立ち姿勢で作業ができるが、高さのあるミニバン系では、踏み台に上って作業しなければならない。
さらに、SUV系ではバックドアに奥行きがあるため、車内に乗り込んでの作業となる。前かがみの姿勢で身体に負担がかかっていたため、作業用のからくり台車に、腰掛けられる椅子を付設した。
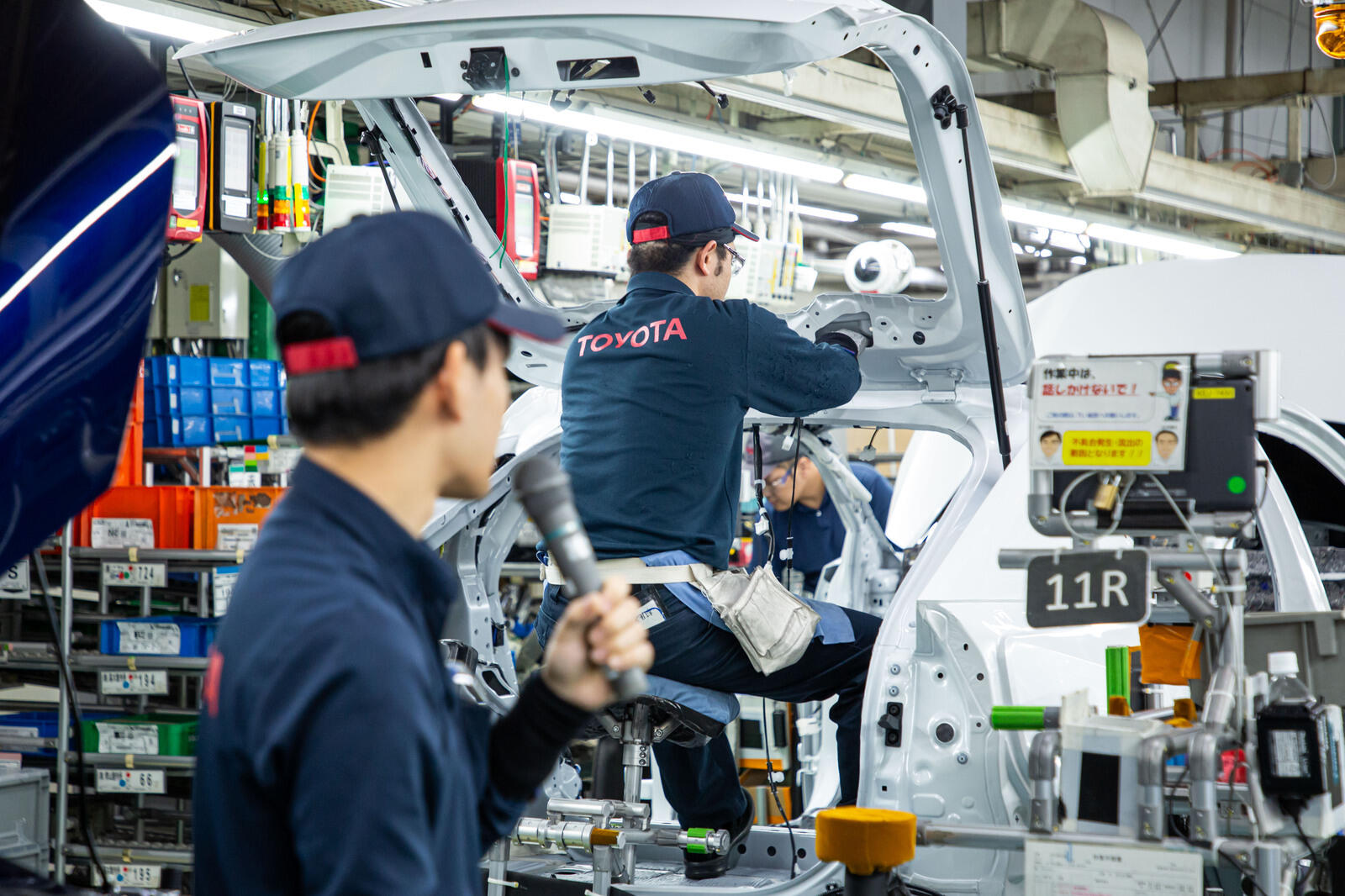
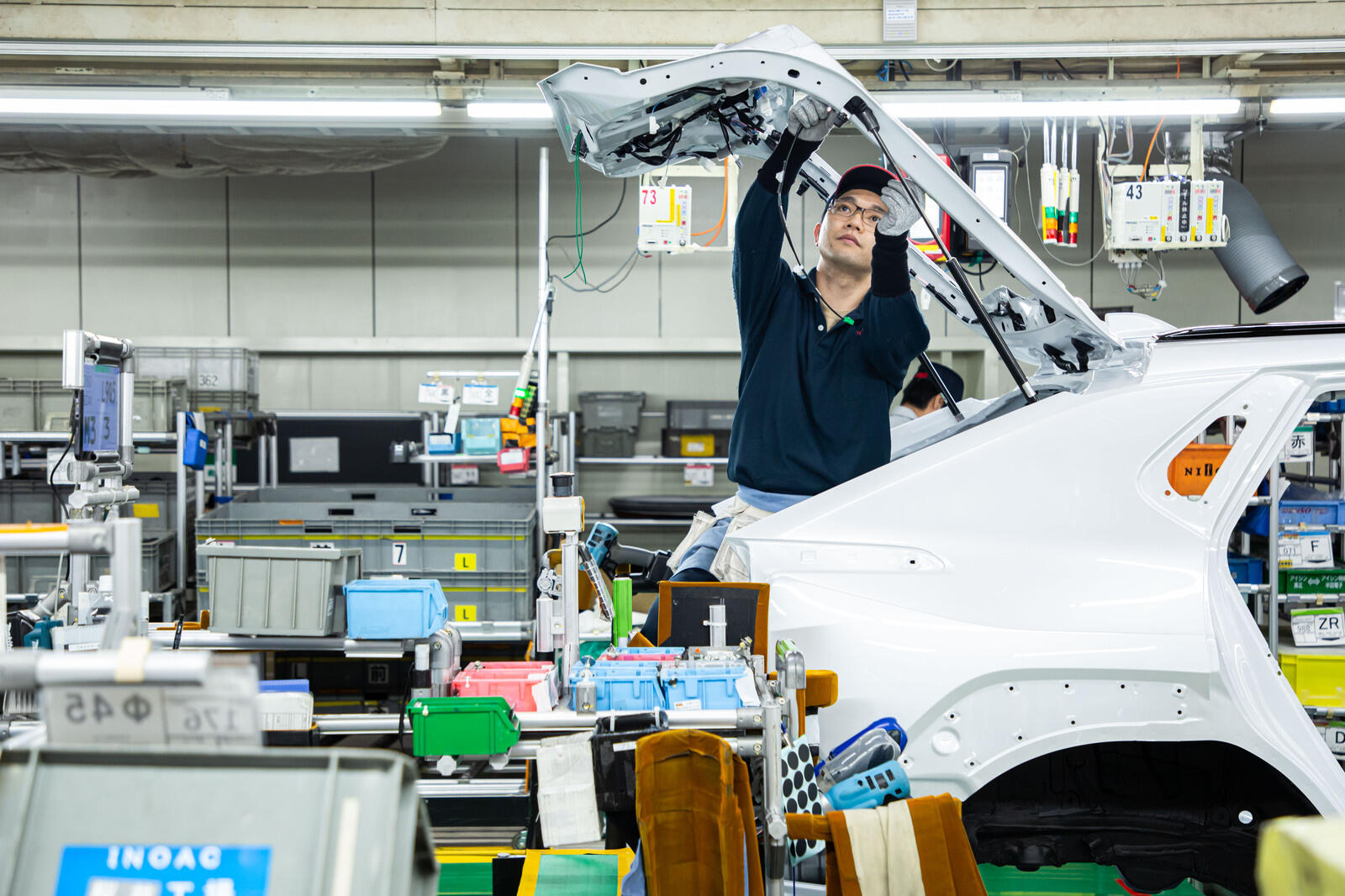
ただ座れるだけではなく、乗った重さでバネが沈み込み、椅子が安定するよう工夫。また、座面が回転するようにして、常に体の正面でワイヤーハーネスを組付けられるようにするなど、働く人に寄り添った改善を施した。
「なんでもやる」という精神は、“少量特殊生産”にもつながった。
GRヤリスやGRカローラに加え、最近ではLEXUS LBX MORIZO RRの生産も行う「GRファクトリー」。
「モータースポーツを起点としたもっといいクルマづくり」で得られた知見を、アジャイルに生産工程に反映するこのラインも、元町工場の中にある。
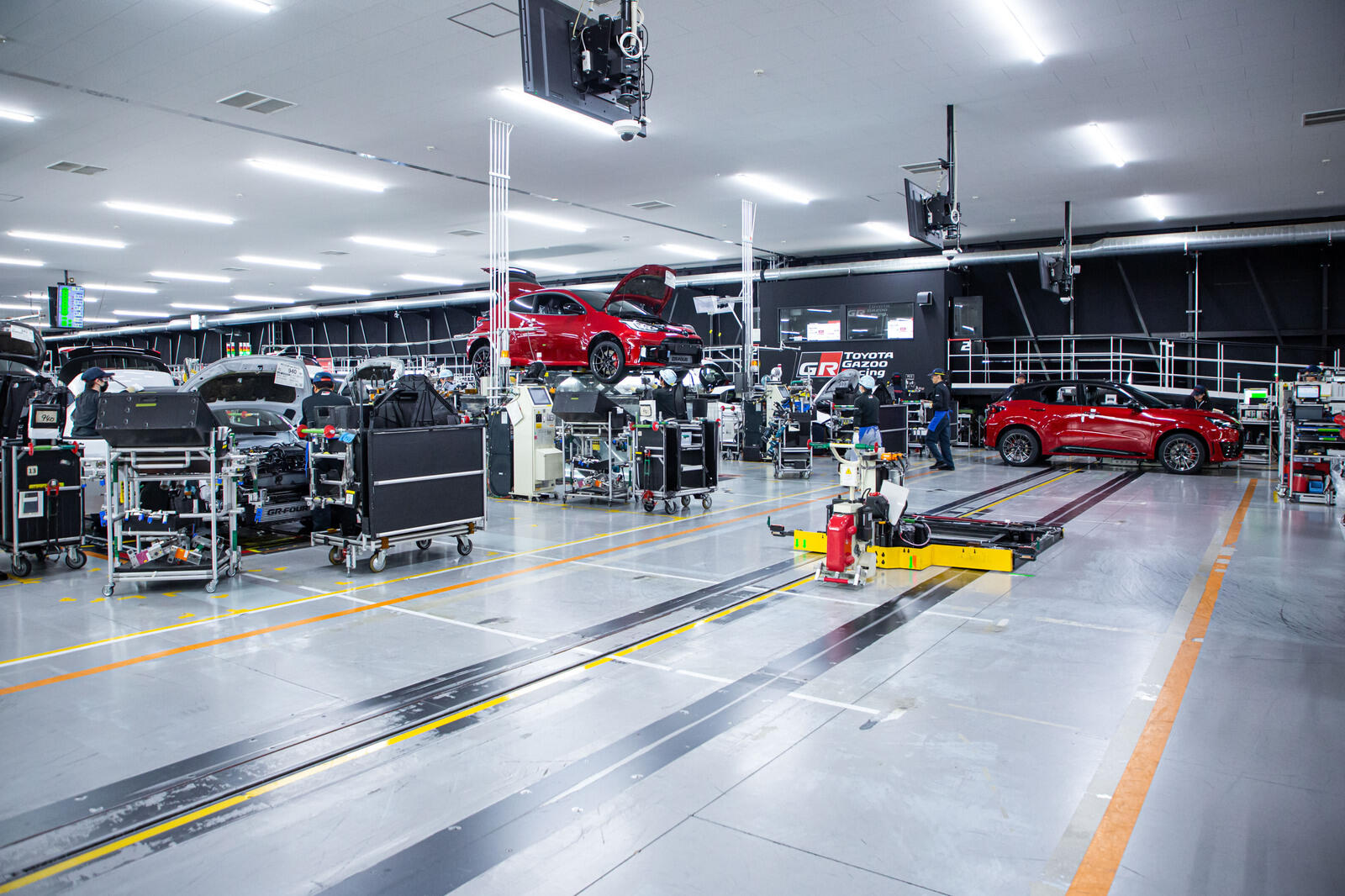
ここが他と大きく違うのは、「そのままサーキットに持ち込んで全開走行できる」モノづくりのクオリティを量産ラインに落とし込んでいるということだ。
どんな工業製品も、一定の基準値内でばらつきが出る。市販車ではまったく問題ないわずかなばらつきも、クルマの限界性能で戦うレースでは大きな差となって結果に表れる。
GRファクトリーでは、プロのレーシングドライバーの監修も仰ぎながら、このばらつきを極限まで抑える挑戦を行う。
例えば、足回り部品をボディに結合するボルトの穴の位置を三次元計測し、基準値からのわずかなズレを補完できるよう、足回り部品をマッチングさせるシステムを使用。
取り付ける際にも、個体差を踏まえて、目視では気付けない1mm以下のレベルで治具の位置調整を行い、徹底的にばらつきを排除していく。
さらに、驚かされるのは、アライメント(タイヤの向きの)調整までは、決してハンドルを切らないようラインがつくられているということだ。組立でつくり込んだ高精度・高バランスを崩さないようにクルマは徹底して、直進方向に流されている。
組立が完了した後の最終検査に移る際も、検査員がハンドルを切らなくて済むよう、ターンテーブルに載せて、クルマの向きを変える。
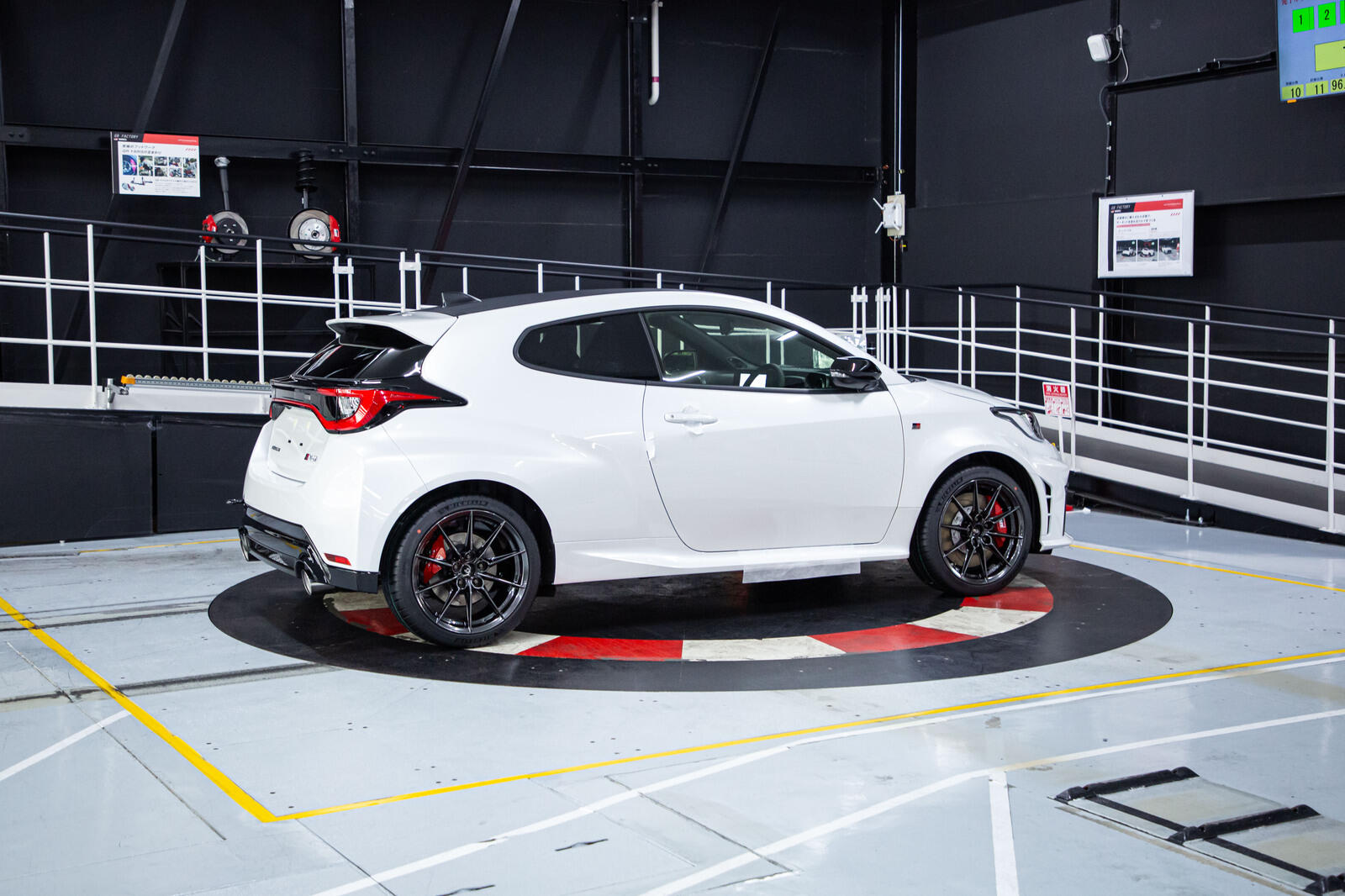
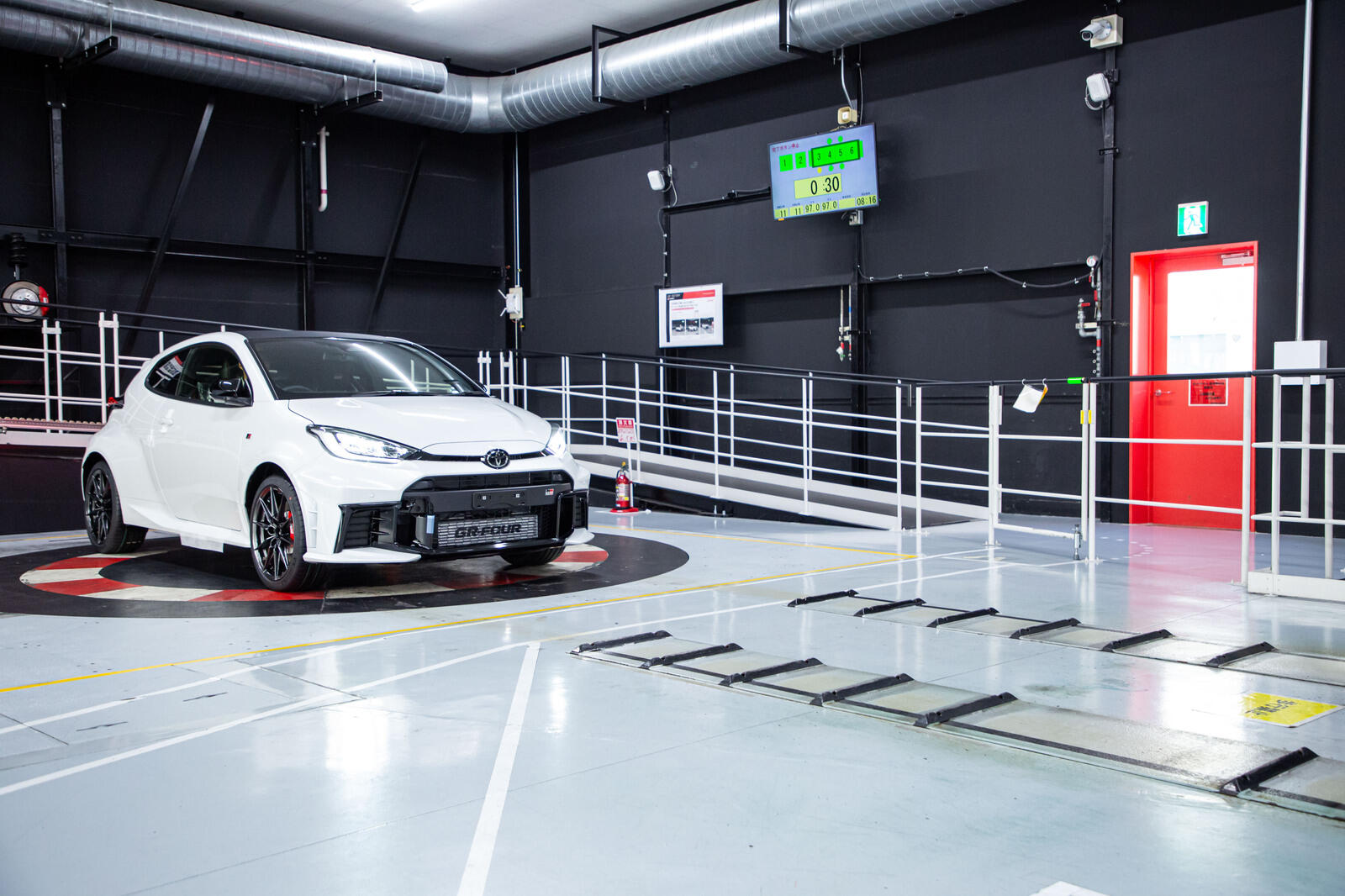
アライメント調整の直前では、波状路を通らせてクルマを揺らし、足回りのひずみを排除。
徹底的に一台一台に向き合ったモノづくりを量産ラインに落とし込む、前例のない挑戦。組立部第3組立課の杉浦健太課長はモータースポーツを起点に、絶えず進化が求められるラインを受け持つ現場の覚悟を語った。
組立部 第3組立課 杉浦健太課長
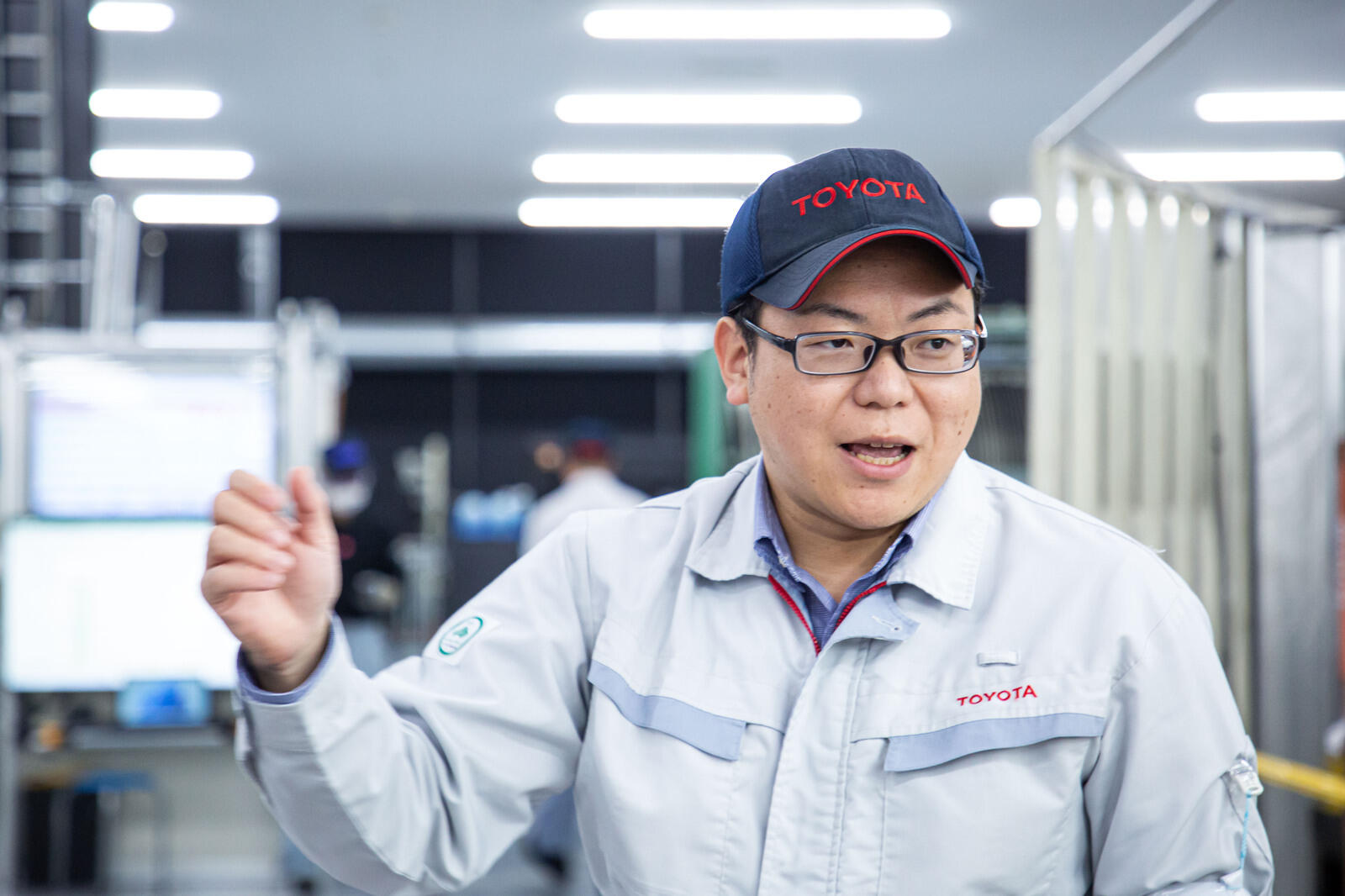
モリゾウさんやレーシングドライバーの皆さんから難題と思えるようなフィードバックを受けることもあります。だけど、できないのではなくて、みんなでどう実現させるかを考えてやっていることも、GRの1つのこだわりです。ラインが一度完成したら終わりではなく、クルマと同じようにどんどん進化していくことを、我々は求められていると思います。
意志をもって残す「手工程」
「下手な字を教えたらロボットは下手な字を書く。ロボットに上手な字を書かせたいと思ったら、上手な字を教えなければならない。そのために、もっとうまい字が書ける人を育てることが大事」
現場一筋61年、モノづくりの現場に身を置き続けてきた河合満おやじ(エグゼクティブフェロー)は「技能」と「技術」の関係をこんな言葉で説明する。
この“技”のスパイラルアップについて、元町工場・宮部義久工場長は次のように語る。
宮部義久工場長
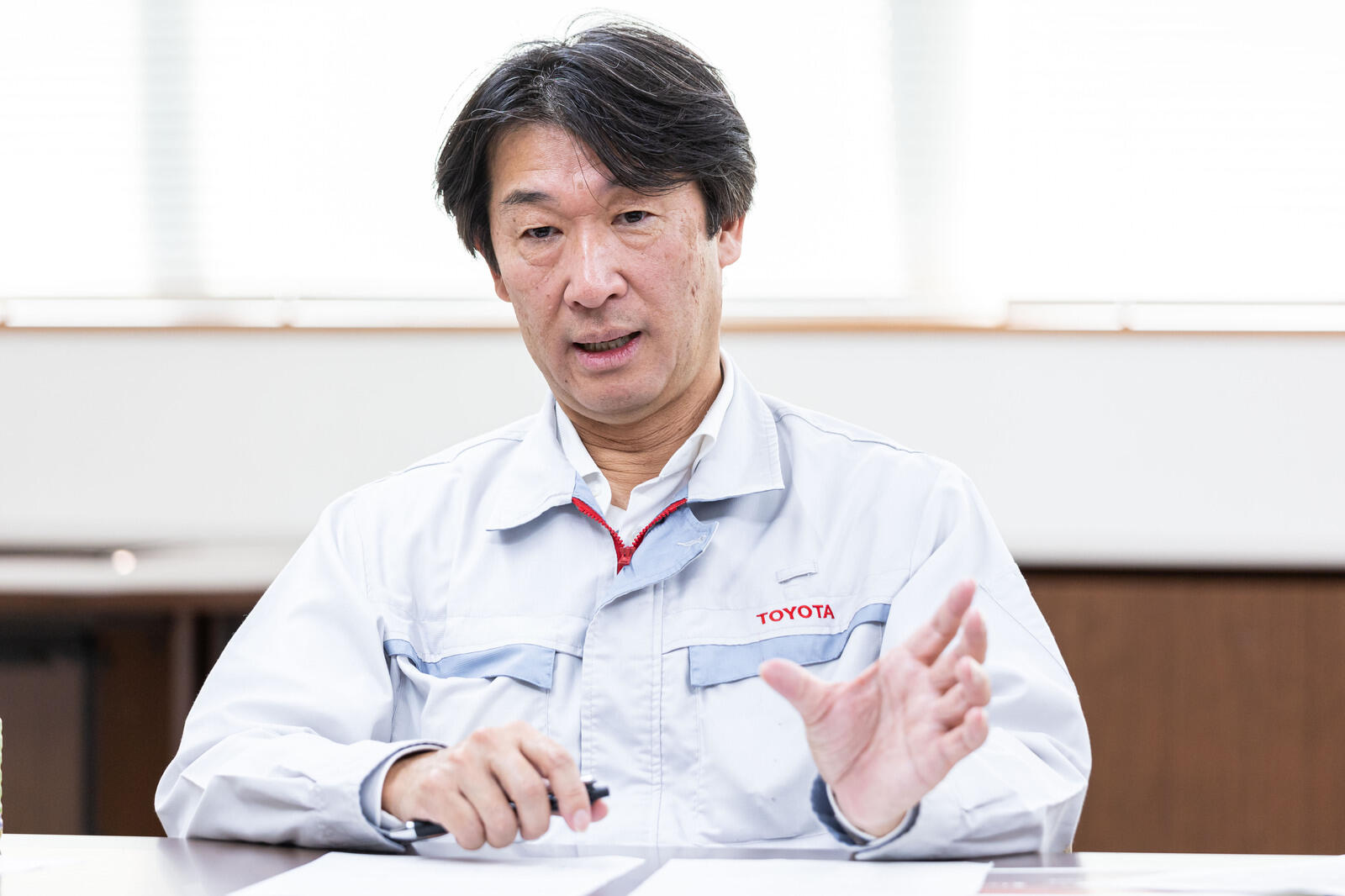
今はまだ、手作業でモノづくりをやってきた世代の人たちが現場にたくさんいるので、ロボットに教えるプログラムがつくれます。でも、何十年かたったときに、一度も自分で作業をしたことがない人たちばかりだったらつくれない。そのクルマ、その工程を一番よく知っている人たちがAI化や自動化を進めていくことが大事だと思います。
GRなどの量を求めないブランドを扱う個性があるからこそ、意志をもって手工程を残しているという元町工場。
ここからは、こうした考えのもとで継承される職人技を見ていこう。
「少量多品種」に向き合う元町では、取り扱うプレスの型も多い。現状985型。これを日々メンテナンスし、生産を維持するのが型保全の役割だ。
例えば、鋼板を裁断する刃が欠けたり、摩耗したりした際には、溶接し、削って、復元する。特に溶接は作業者のカンコツが求められる作業だ。修理の速さや型の壊れにくさにも技能が及ぼす影響は大きい。
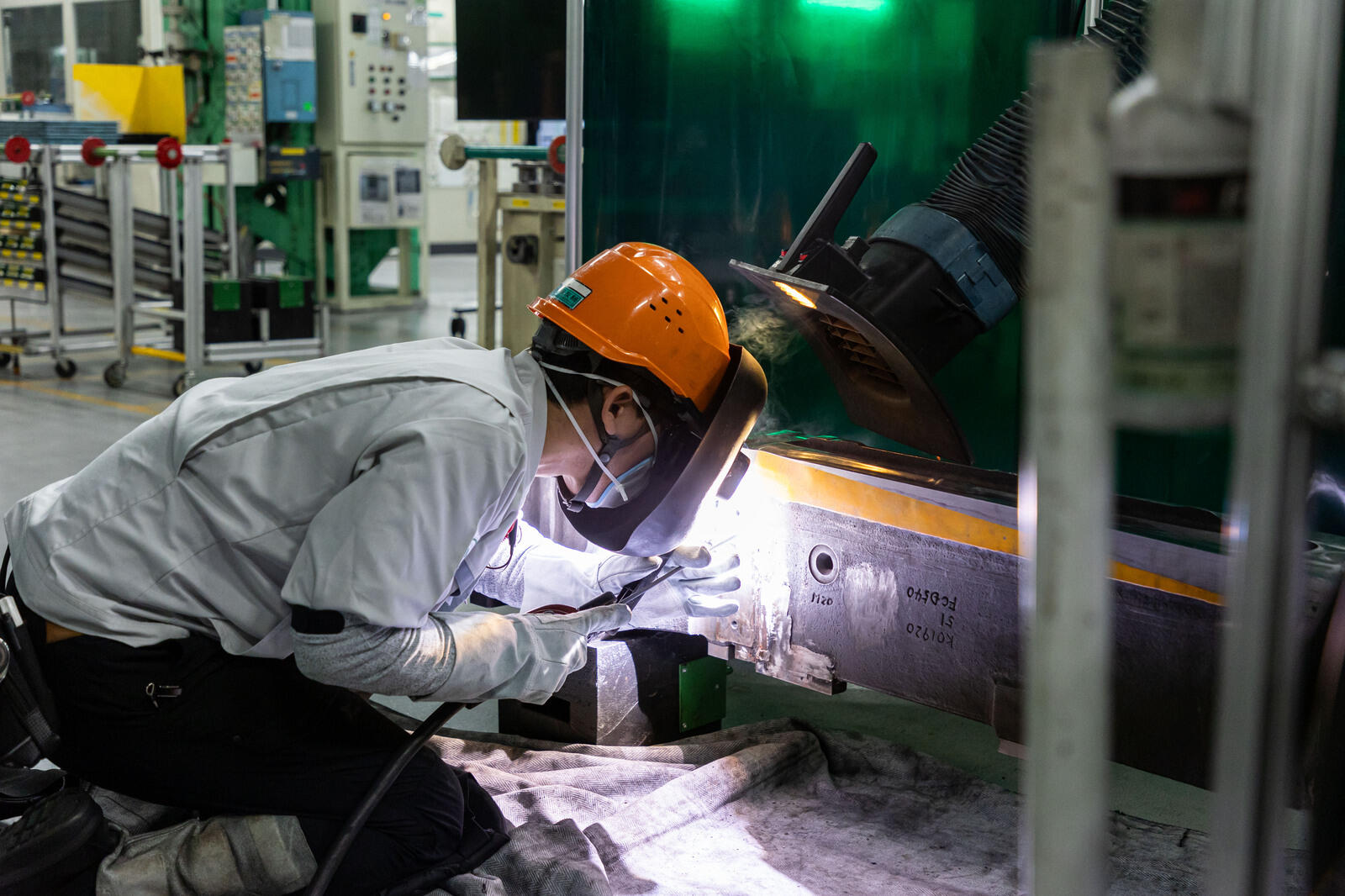
溶接競技会の全国大会出場経験もある車体部プレス課の児崎友輔さん。先輩から受け継いだのは、技術だけではないという。
車体部プレス課 児崎友輔さん
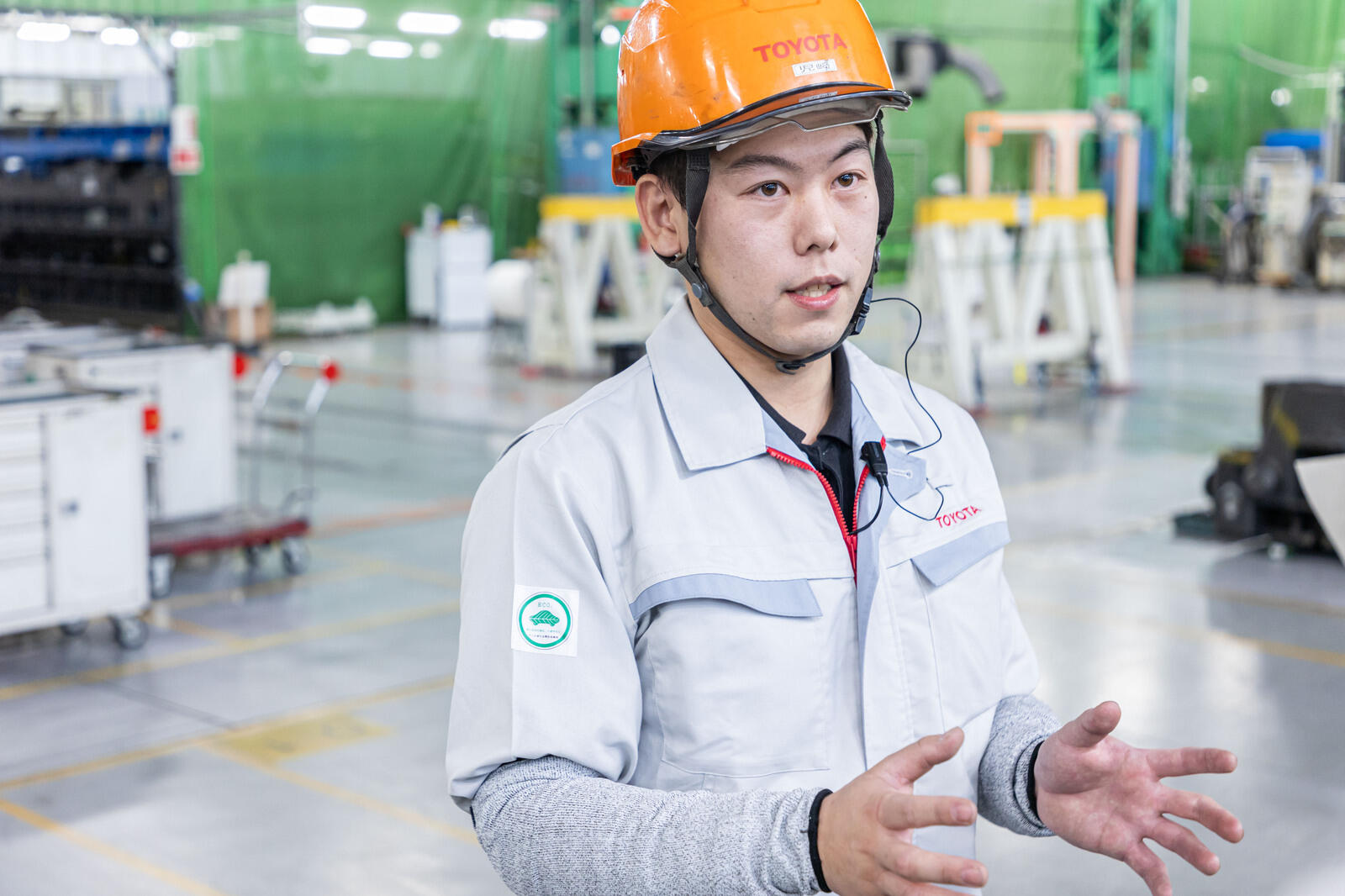
先輩方の作業現場や溶接競技会のOBの方々の作品を見せてもらうと、ただ上手につくっているだけでなく、「こういうものをつくりたい」というこだわりが見えるんです。技能の上達にはこだわりが大事だと気付かせてもらってからは、道具や環境、さらには心や身体の状態にも気を遣うようになりました。そうするとつくるものが洗礼されていく。それが楽しいです。後輩たちにもこだわりをもって溶接に取り組んでほしい。そんなメッセージを伝えていきたいです。
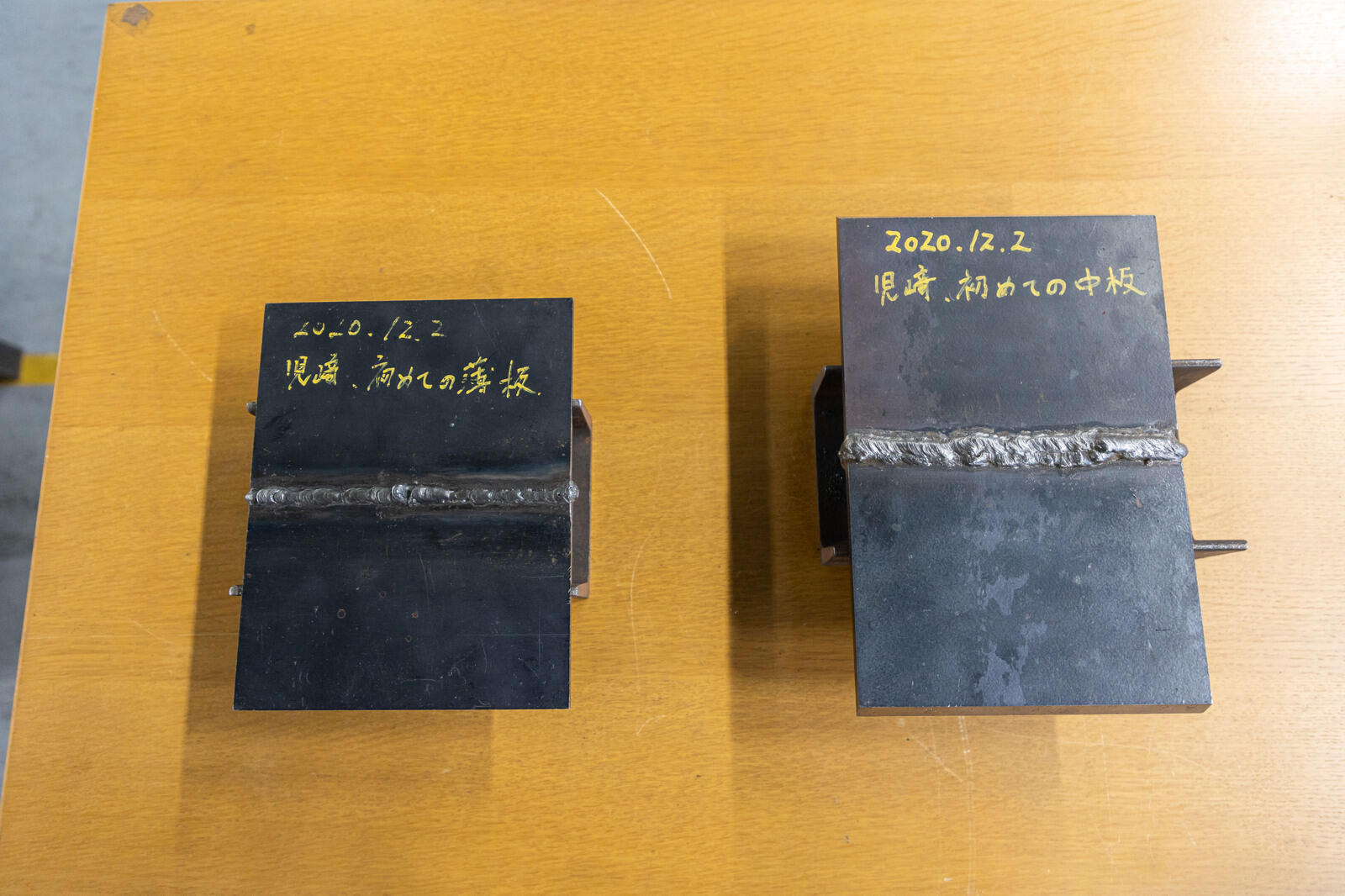
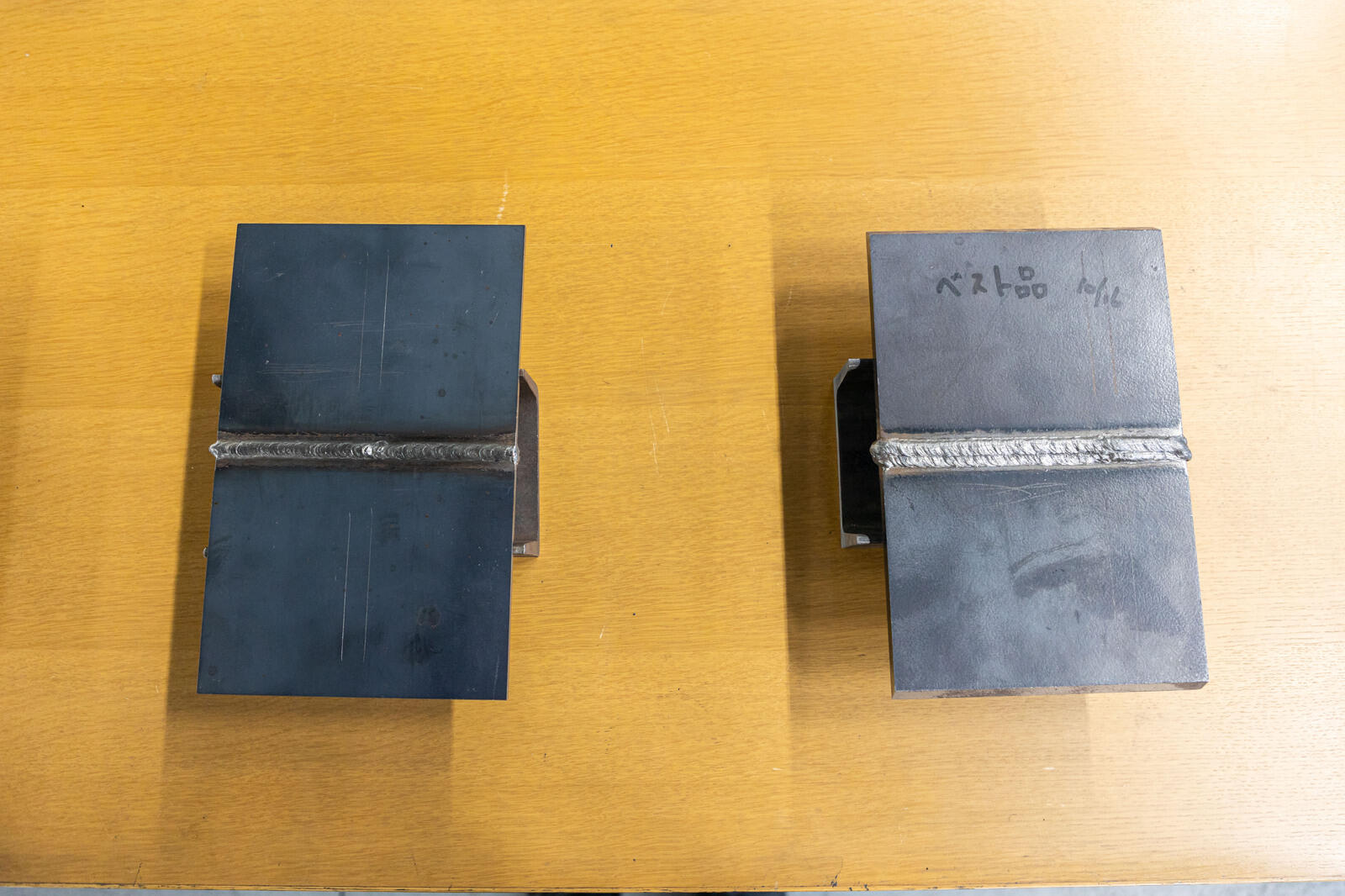
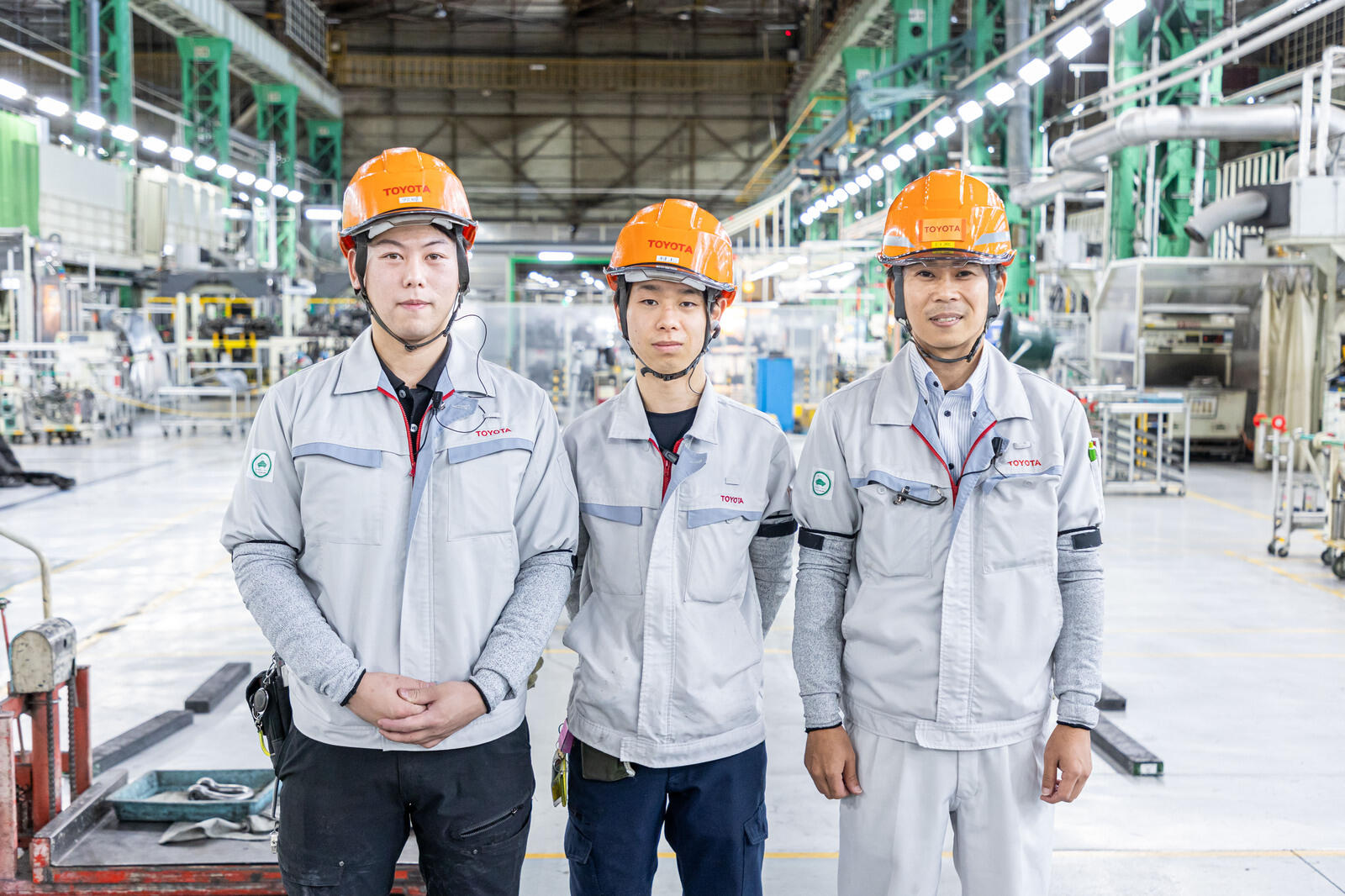
元町工場にあるひときわ小さな工房。量産ラインと比べて圧倒的に静かな空間に見え隠れする人影。
トヨタの最高級車センチュリー。選抜された匠の手仕事でつくられていくこのクルマの生産拠点も元町工場の中にある。
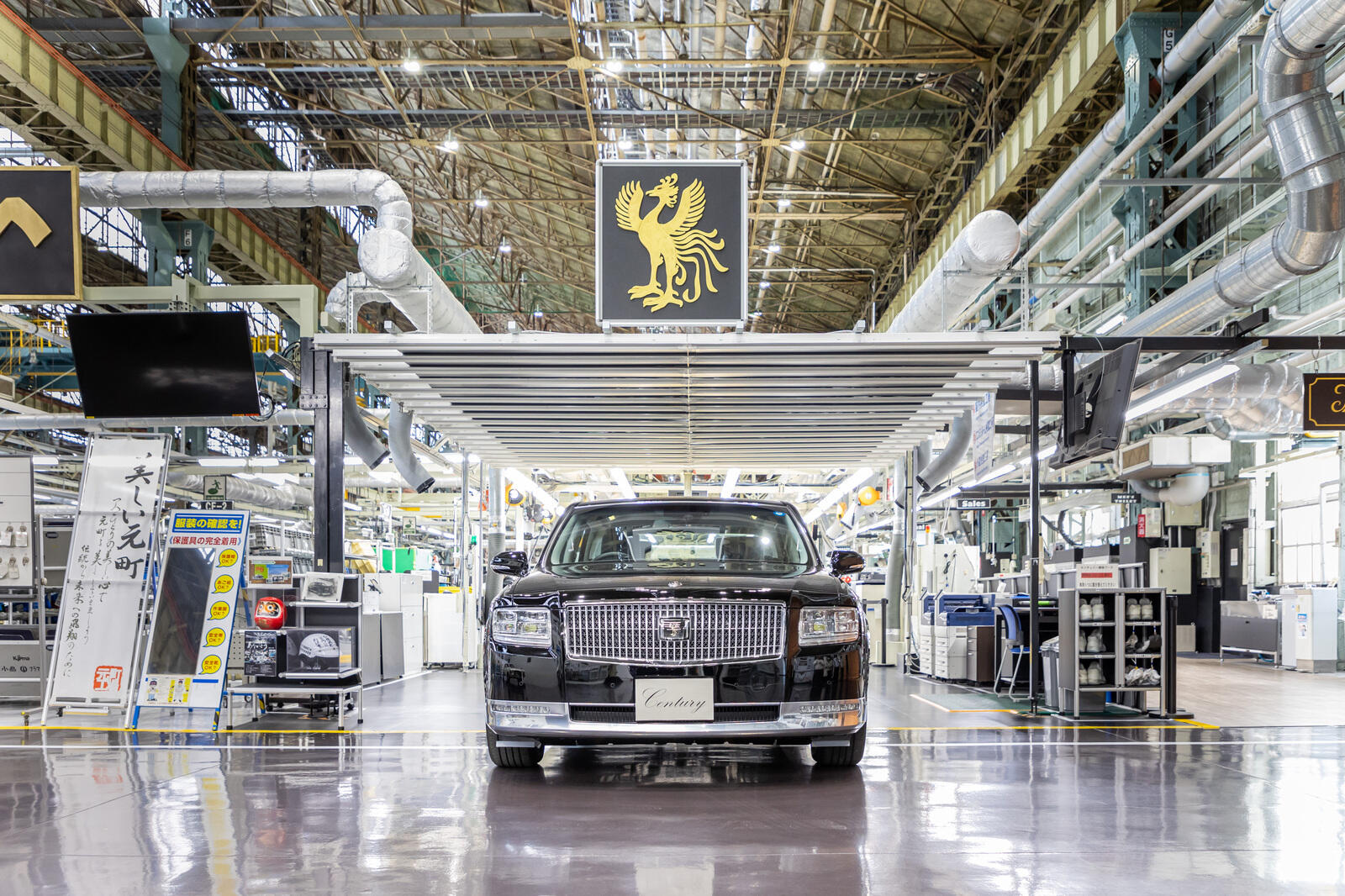
鳳凰のエンブレムが存在感を放つ組立ラインでは、4人の職人が3日間をかけて1台をつくり上げる。品質も、職人が一つひとつ自らの目で確認し、チェックシートにサインする。
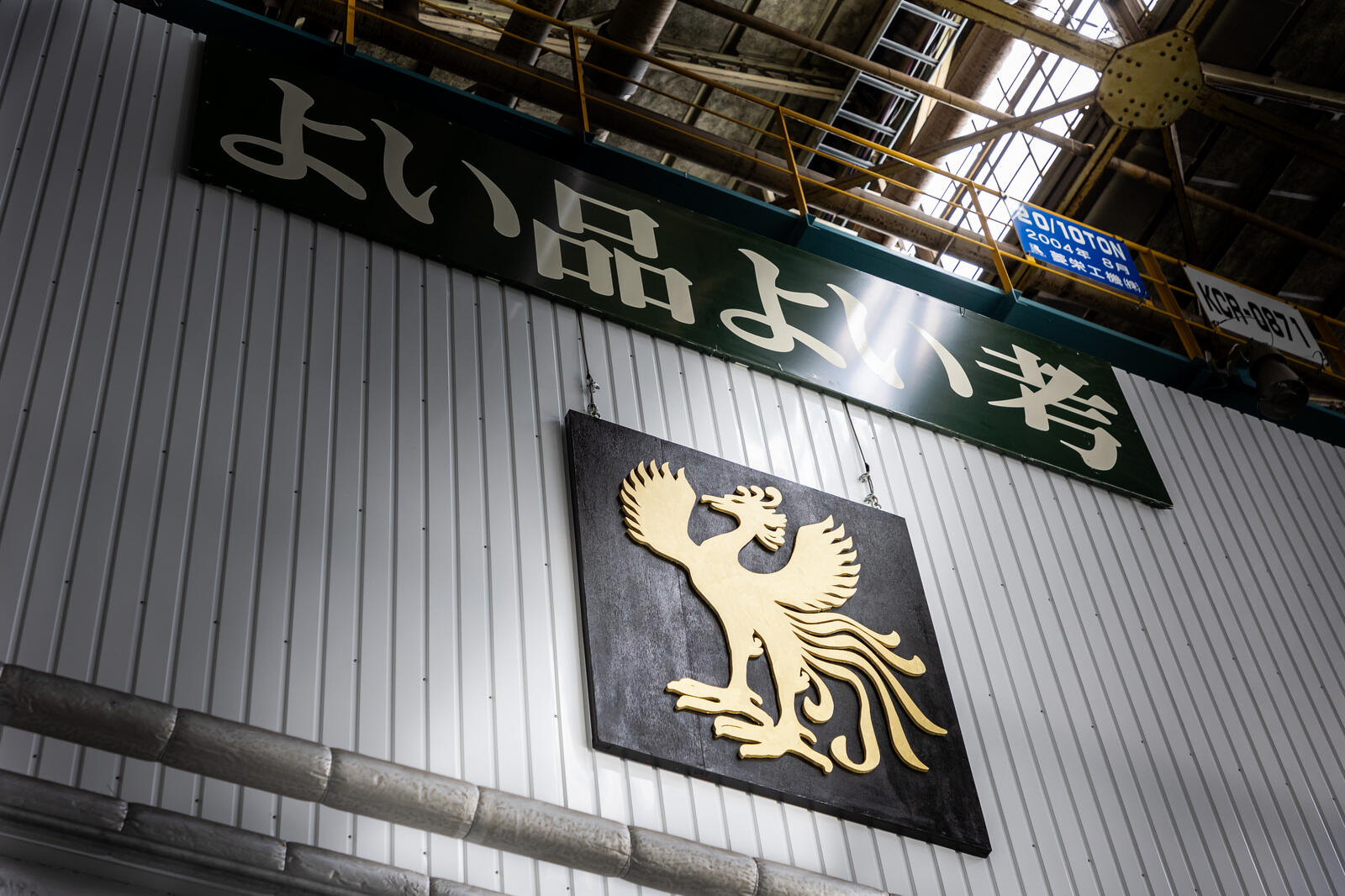
今回編集部が訪れたのは、センチュリーの塗装工房。明るい空間にどっしりと佇むセンチュリーと、胸元の鳳凰が目を引くクリーン服に身を包んだ作業員が出迎えてくれた。
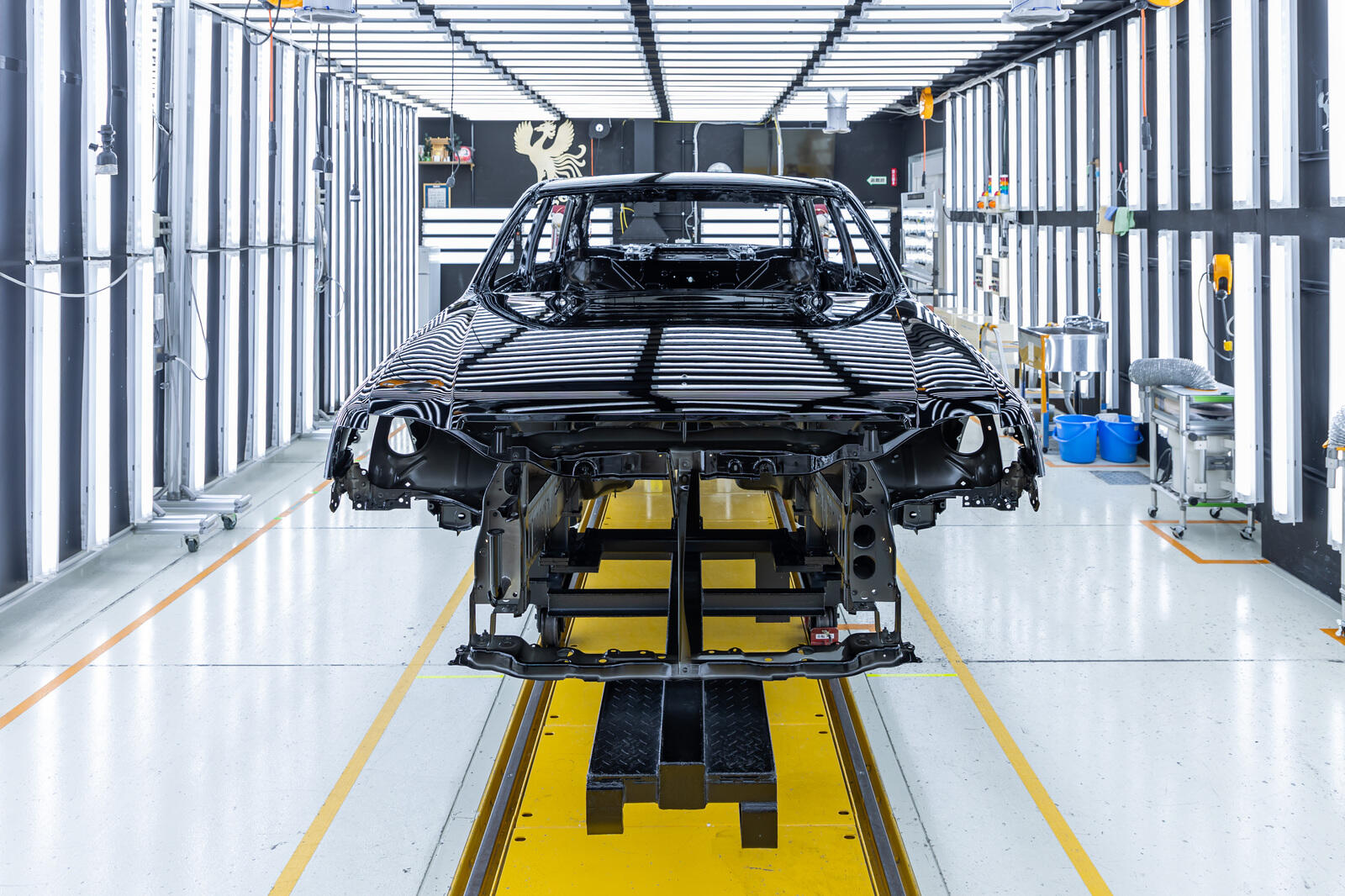
元々、センチュリーを生産していたトヨタ自動車東日本(以下TMEJ)東富士工場に、塗装成形部 塗装課の柚木正美組長はじめ数名が出向し、その技能と魂を継承した。
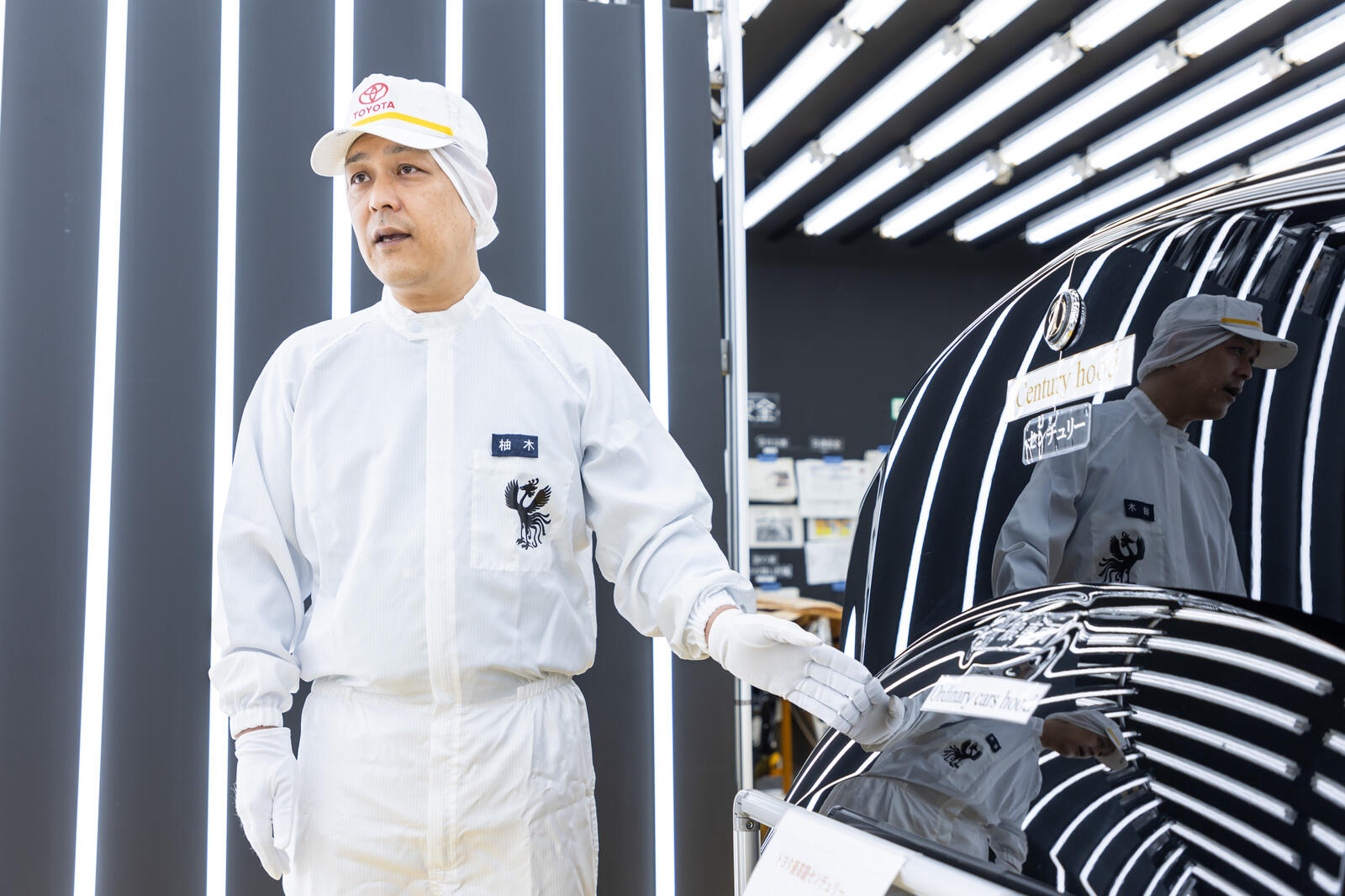
センチュリーがほかのクルマと一線を画すクオリティの1つに「肌ランク」がある。つまるところ車体の塗装面の仕上がりの美しさであり、センチュリーが基準とする肌ランク5は、車体を鏡のように扱えるほど、ゆがみなく光を反射することが条件となっている。
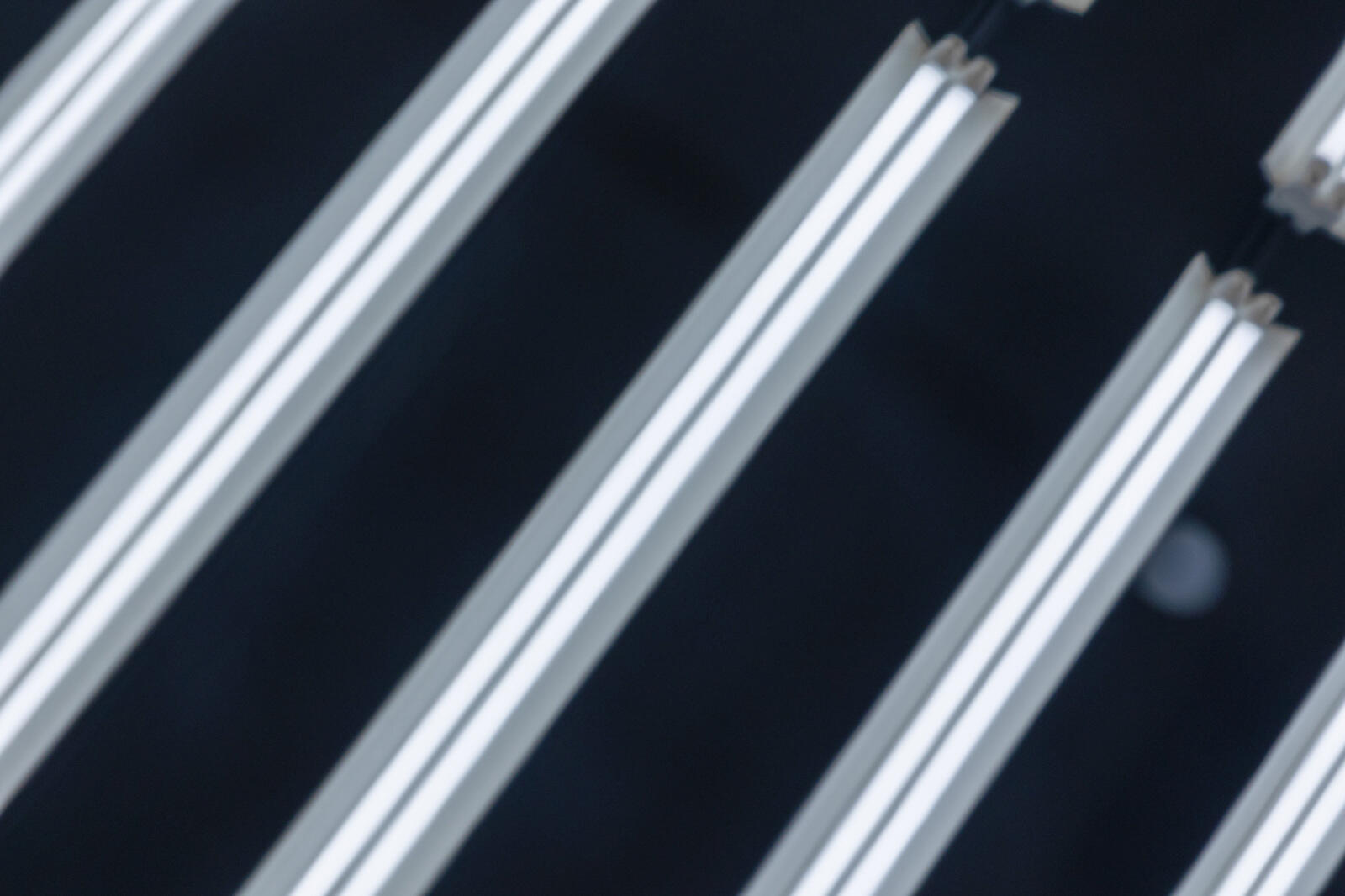
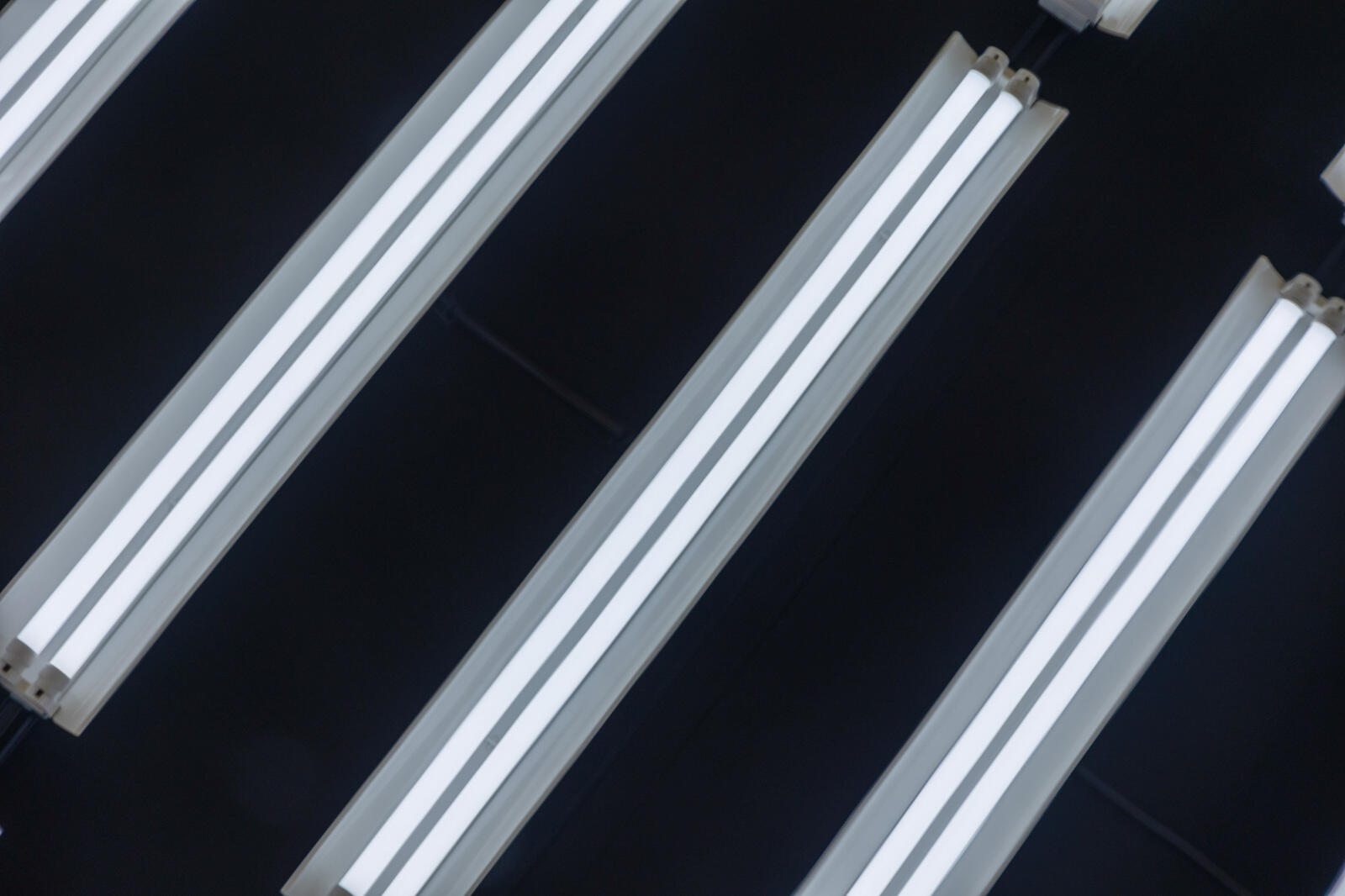
これを実現するため、センチュリーの塗装行程は、一般車両の4工程(=4層)に対して7工程(=7層)としている。
量産ラインの塗装工程で、錆びにくくするための電着塗装のみ行い、この工房へ。中塗りを行った後は、ボディのすべてで水をかけながら磨き上げる“水研”を行う。
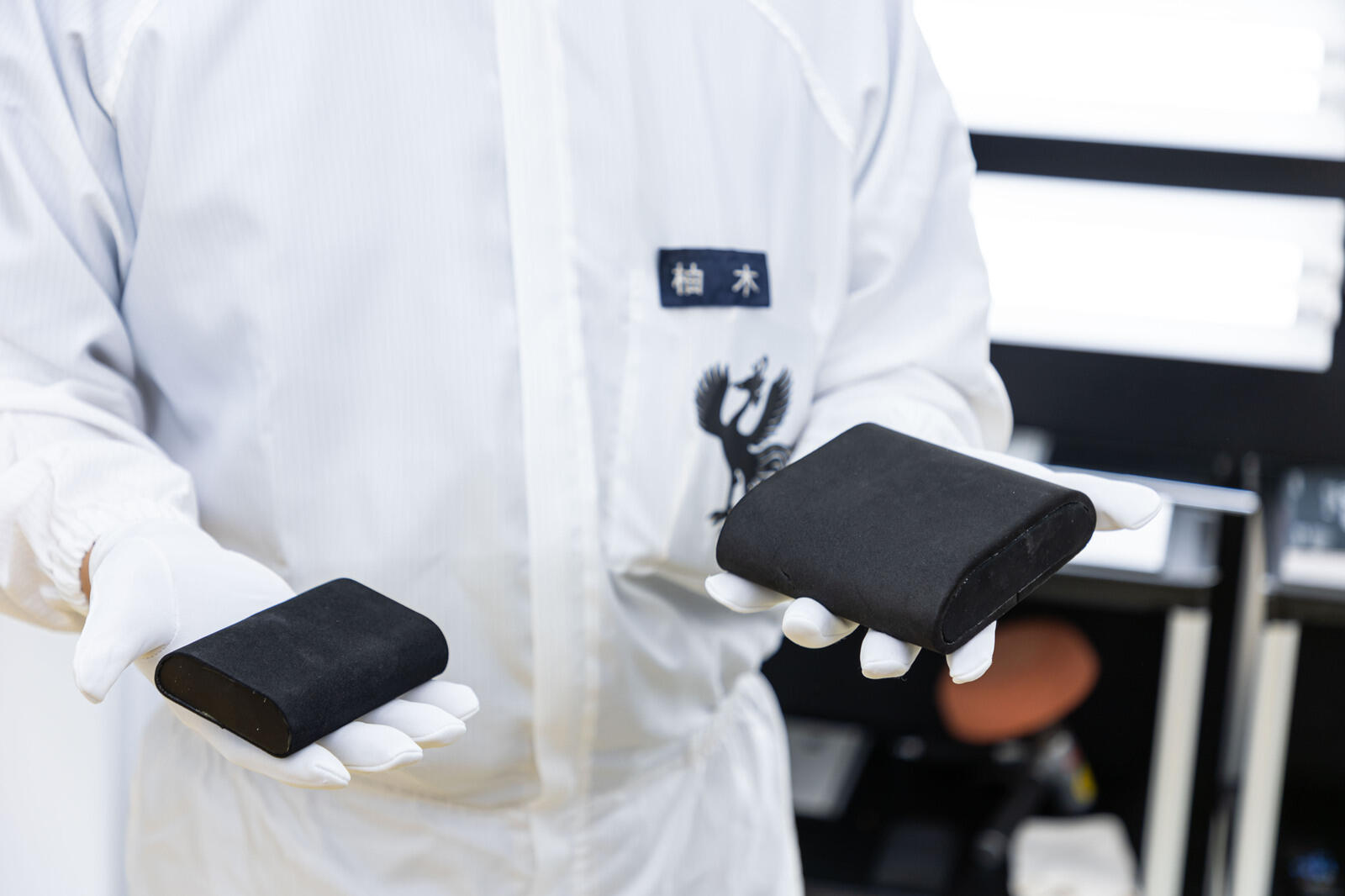
すべての塗装を終えた後も、再度3時間かけて全面水研を施す。
柚木組長がTMEJに出向していたときのこと。同社の匠が、柚木組長の磨きの音を聞いただけで、うまく磨けていないことを言い当てたことがあったという。
しっかり体重をかけて磨けているかどうかは、磨きの音に表れるそうだ。
工房には「見えない部分まで綺麗にしてお客様に提供」「規格で判断しない」といった4箇条が掲げてある。TMEJから受け継いだセンチュリーマインドだ。ここにも、モノづくりの技と心が受け継がれている。
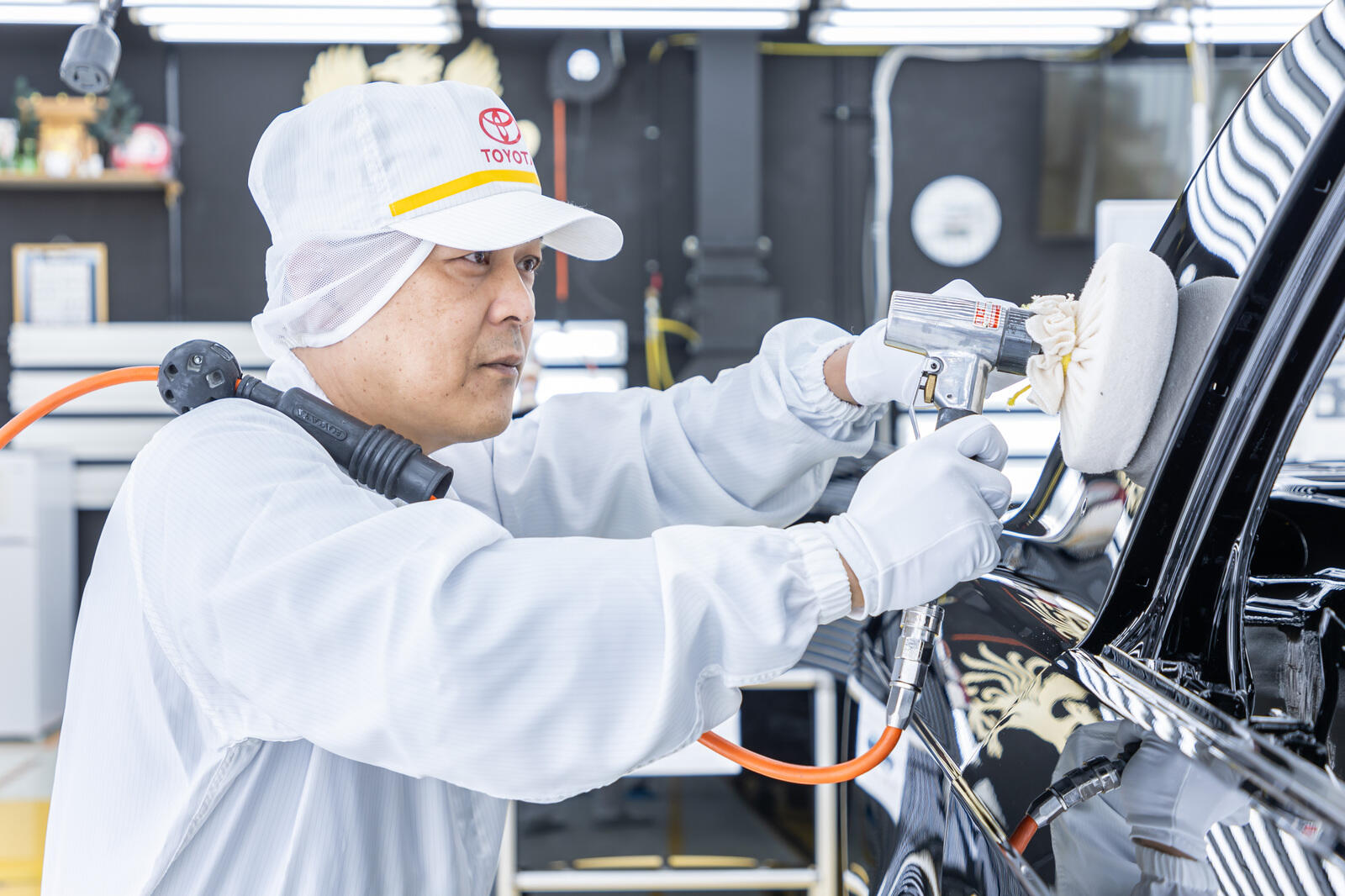