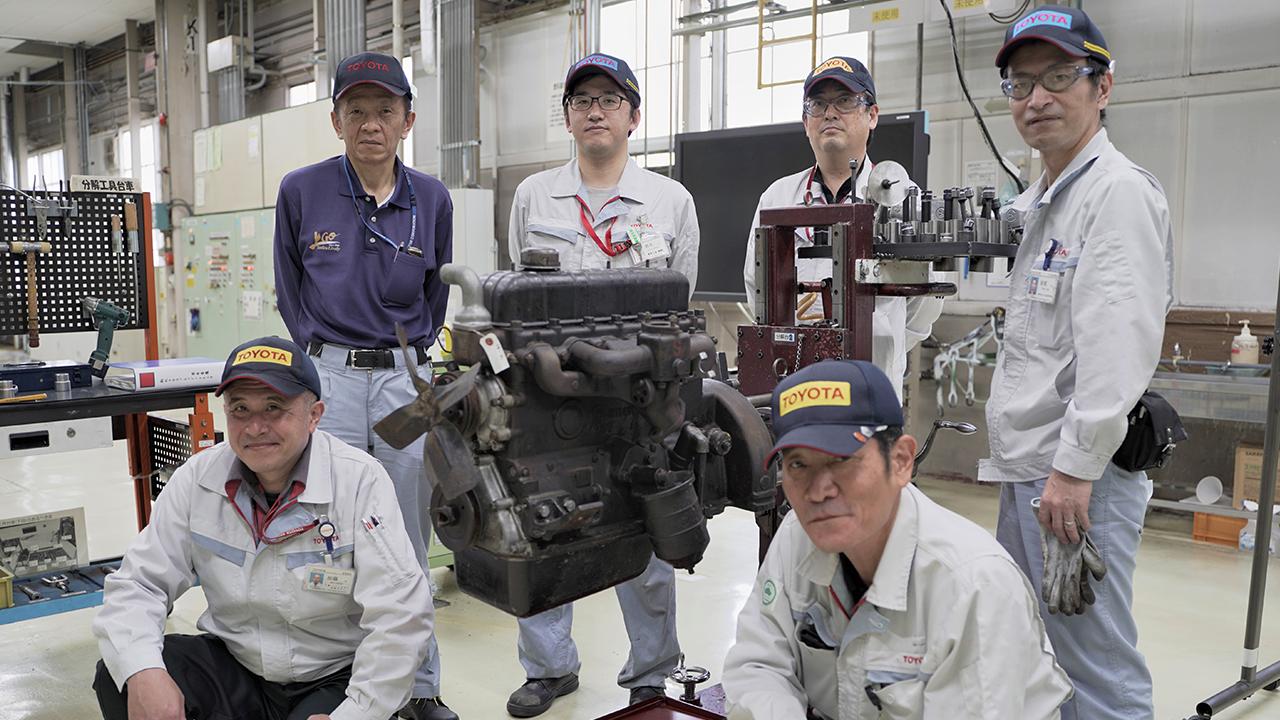
自動車業界が大変革期にある今、トヨタの原点に立ち返るべく始まった「初代クラウン・レストア・プロジェクト」。第8回前編では、エンジンをネジ1本に至るまで分解して再生させたチームの奮闘についてリポートする。
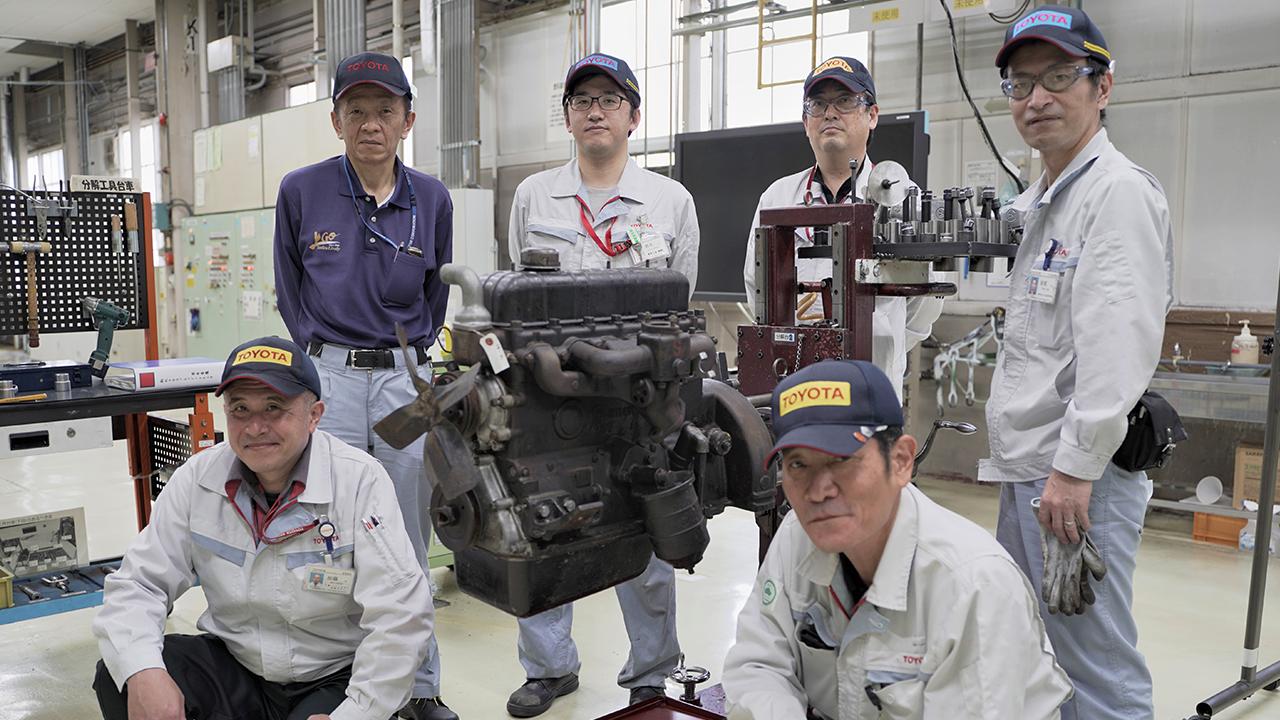
100年に一度の大変革期を迎えた自動車業界。トヨタ自動車ではあらゆる部門で前例のない画期的な取り組みがスタートしている。
そのひとつが2022年の春、社内の各生産工場から多彩な人材を集めて元町工場でスタートした「初代クラウン・レストア・プロジェクト」である。
トヨタイムズでは、その意義とレストアの現場をリポートしていく。第8回の前編では、エンジンのレストアを担当したチームを取材。エンジンを分解してその状態をチェックし、レストアの方針を確立するまでの奮闘をお届けする。
さまざまな年式の部品が混在
シャシーから降ろされた初代クラウンのエンジンのレストアを担当したのは、上郷・下山工場 品質管理部の岩城徹、同工場 技能育成グループの伊藤裕、加藤靖、田原工場エンジン製造部 牧田真武、そして下山工場 園田茂雄たち。
彼らがまず取り組んだのは、エンジンをネジ1本に至るまで完全に分解して清掃することだった。
さらに、それらに番号を付けて整理し、仕様や各部品の状態を調べ、使える部品か、新たにつくらなければならない部品かをハッキリさせることだった。
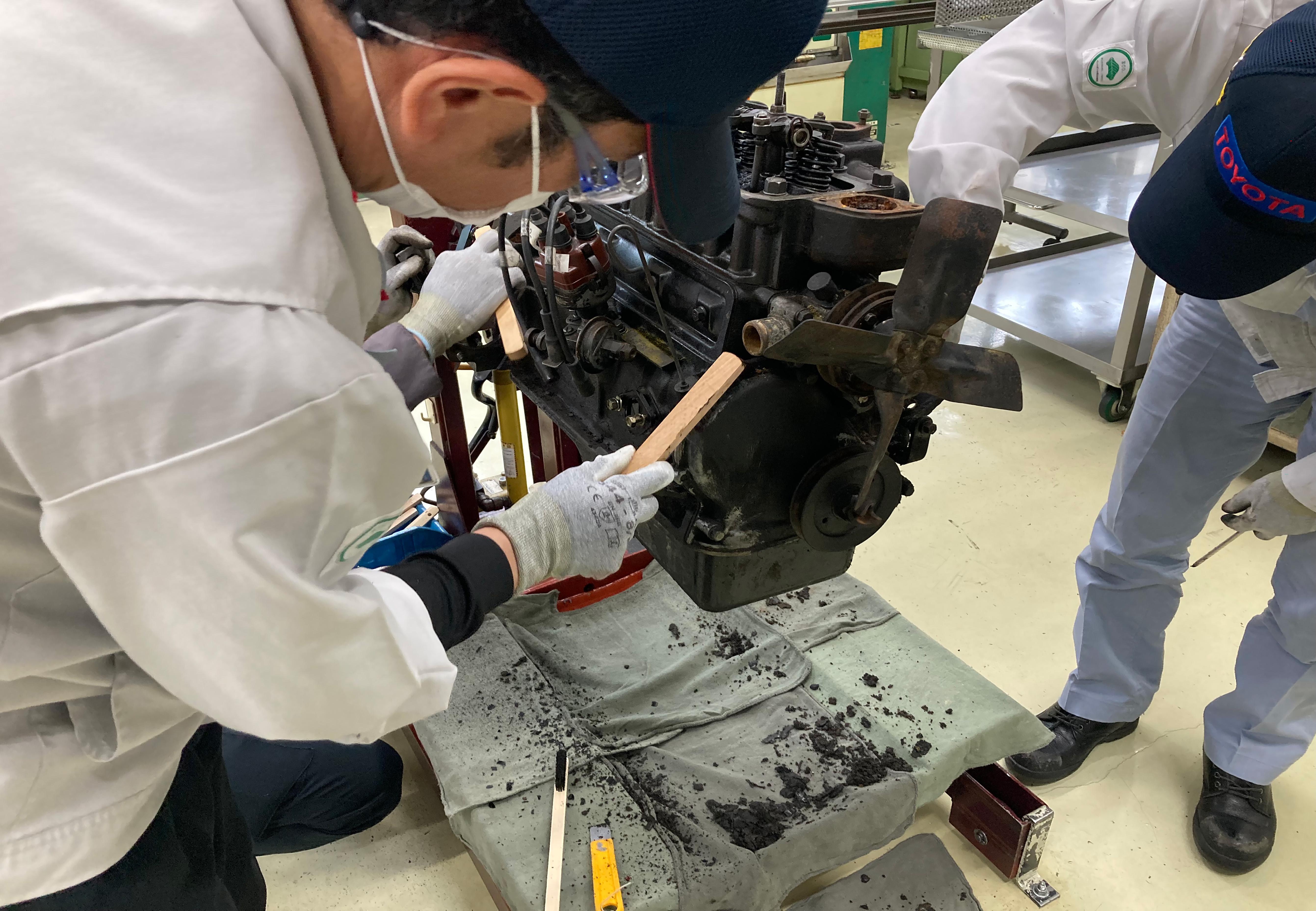
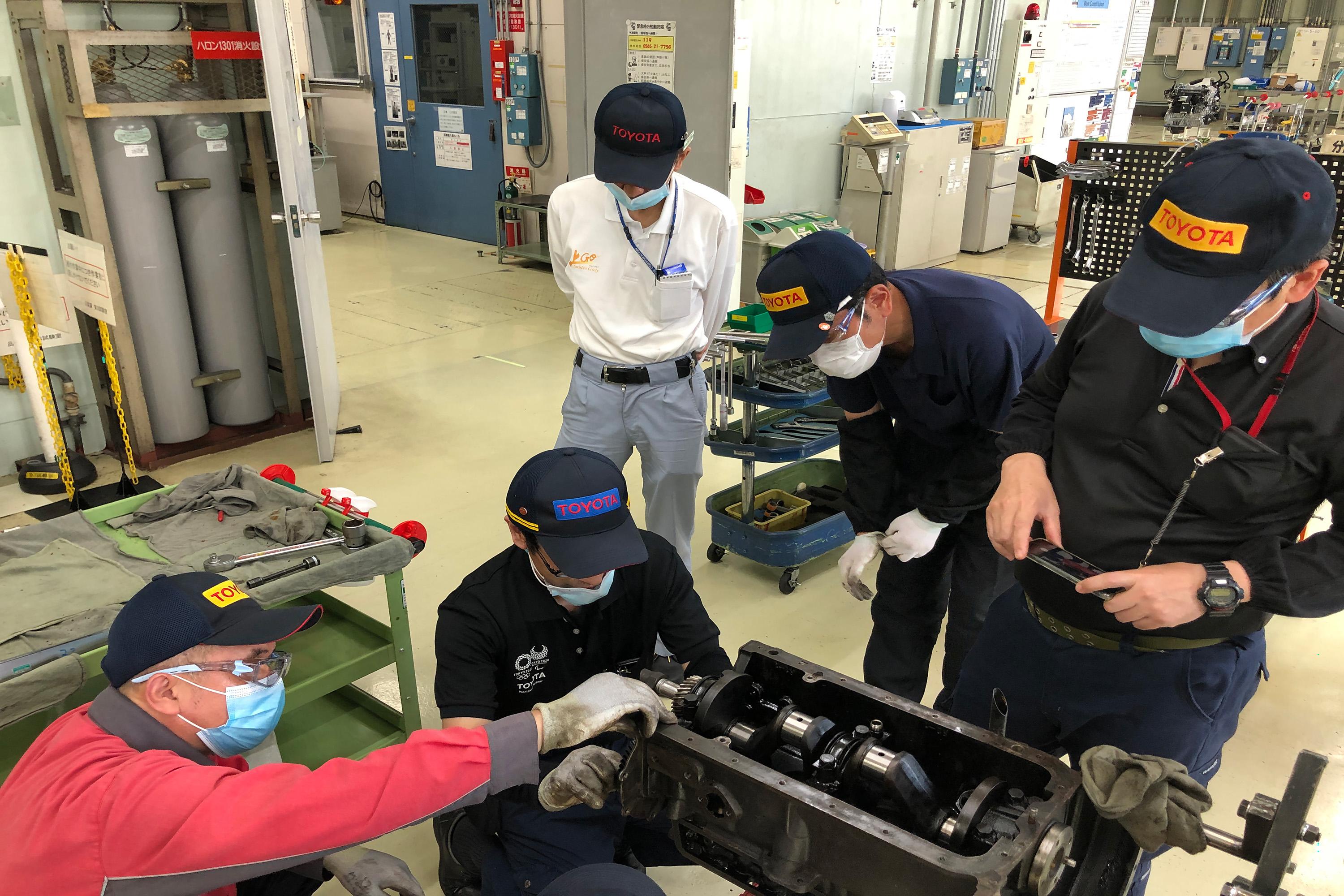
初代クラウンに搭載されたR型エンジンは、1947年にトヨペットSB型トラックに搭載されたS型エンジンに続いて開発され、1952年8月に設計が完了した。
トヨタ最初の量産エンジンであるA型(1935年生産開始)の伝統を引き継ぐOHV(オーバーヘッドバルブ)式、1453ccの水冷直列4気筒エンジンだ。
当初はS型と同じSV(サイドバルブ)式のP型が試作されたが、より優れた性能を追求するためにSV式からOHV式に変更されて誕生したという経緯がある。
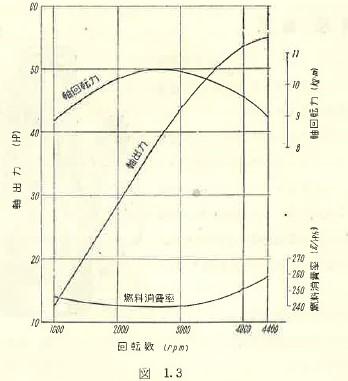
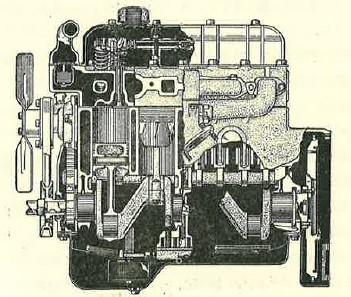
R型エンジンはボア×ストロークが77×78㎜というほぼスクエア型で、圧縮比は6.8。毎分4000回転で48馬力を発生した。
S型エンジンの28馬力に対して20馬力もアップしながら燃費に差はなく、トヨペット・スーパーRH型系乗用車に搭載されて高い評価を得た。1953年7月にはこのエンジンの月産500台の生産ラインが完成している。
初代クラウンはこのエンジンを搭載すべく生まれたクルマだった。そして初代クラウンに搭載されてからも出力アップのための改良は続き、圧縮比を高めるなどの工夫で最高出力は1962年生産の最終型では62馬力にまで向上している。
今回分解したこのエンジンは、約70年の間に何度かオーバーヒートを起こした痕跡が見つかった。オーバーヒートは重大なトラブルであり、エンジンのあらゆるところにダメージを与える。だから徹底的に部品をチェックして、状態を確認する必要がある。その際にまず判明したのが、年式の違う部品が混在していることだった。
岩城
エンジンをバラしてみると、このクラウンが走り続けられるようにエンジンを整備してきた人たちの苦労が見えてきました。
設計図から当時はエンジンの改良による出力アップが短い間隔で行われていたことは分かっていました。でも、仕様違いは予想を超えていましたね。
分解したエンジン部品を当時の設計図と照らし合わせて整理してみると、シリンダーブロック、クランクシャフト、シリンダーヘッド、カムシャフト、コンロッド、インテークマニホールドなどに、さまざまなバージョンの部品が混在していることが判明したのです。
まずは“使える部品”と“使えない部品”に分類
シリンダーブロック、シリンダーヘッドとカムシャフトは1956年式。クランクシャフトは1958年式。コンロッドは1953年式。インテークマニホールドは1955年式。
このクラウンが現役だった当時、整備を担当したエンジニアたちは、必要な部品を何とか調達して、エンジンが動く状態をキープしようと努力してきたのだろう。70年という年月を考えれば当然のことだ。
チームメンバーはバラしたそれぞれの部品について「何年の設計図の、どの部品か」を確認してラベリング。そして、メンテナンスすれば使える部品か、メンテナンスをしても使えない部品かどうかをていねいに確認していった。
クルマには整備の際に交換しなければならない消耗部品がいくつもある。エンジンについては、シリンダーブロックとシリンダーヘッドの間にはさんで金属同士の隙間を埋め、シリンダーの内圧を逃がさず、冷却水やエンジンオイルのシリンダーへの流入を防ぐヘッドガスケットに代表されるガスケット類があげられる。また、冷却水を循環させるホース類のようなゴム系の部品もそうだ。
常に高温・高圧の燃焼ガスにさらされ、その爆発力を受け止めるピストンや、ピストンの外周部にセットしてシリンダー内壁との隙間を埋め、燃焼ガスがシリンダーの外に逃げることを防ぐピストンリング、ピストンリングの外側にあってオイルを保持してシリンダーとピストンの間の摩擦損失を減らすオイルリングのように、機能に問題があれば新品に交換しなければならない部品もある。
幸いなことに、こうした消耗部品は、専門メーカーに依頼すれば、R型エンジンのような古いエンジンのものでも、製造してもらえることが多い。
まずは各部品の確認作業を早く終わらせて、使える部品は再利用できるようにし、使えないものは、新しい部品を調達しなければならない。
R型エンジンの驚きの構造とは?
エンジン・レストアチームはこの作業の中で、70年前に生産されたこのエンジンの、今からは考えられない構造と、その製造を担当した当時の人々の技術に驚いた。
それが、シリンダー内で爆発的に燃焼したガスの力を受けるピストンを支え、その上下運動をクランクシャフトに伝えるコネクティングロッド(コンロッド)だ。
今のクルマの軸受部分には、上下2枚のメインベアリング、つまり薄い板状で半円形のメタル軸受がはめ込まれている。この2つでクランクシャフトをはさんで保持し、スムースに回転させる役割を果たす。
この軸受は銅合金やホワイトメタルと呼ばれる合金からできていて、表面にエンジンオイルをたっぷり含むことができるため、部品が接触する部分に油膜ができる。
この油膜が、部品同士が直に接触するのを防ぎながら部品を支えつつ、部品の表面の摩擦を減らしてくれる。
つまりコンロッドやクランクシャフトはメタル軸受の表面にできた油膜の上をすべりながらスムースに回転する仕組みになっている。
ところがレストアするエンジンのコンロッドの軸受部分には、このメタル軸受がはめ込まれていなかった。なんとその代わりに、部品の表面にこの軸受の金属素材が盛られていたのだ。
岩城
最初は「あれ?ベアリングがない」と思いました。でも調べてみると、軸受けの金属素材を盛るのは、溶射ベアリングという技術であることが分かりました。
軸受の表面をチェックすると、傷があってそのままでは使えない。これも大きな問題でした。現在もベアリングをこの方法でつくっている業者さんも見つかりましたが、この方法によるベアリングの修理を引き受けていただけるものなのか、分かりません。
しかし、さらに調査を行った結果、コンロッドは1958年にはベアリング別体式に変更されていることが判明しました。1958年式のコンロッドを入手しベアリングは新規製作することで復元することができました。その他 カムシャフトベアリングや、コンロッド小端穴とロッカーアームのブッシュも新規製作をしました。