
自動車業界が大変革期にある今、トヨタの原点に立ち返るべく始まった「初代クラウン・レストア・プロジェクト」。第4回では、愛車として何十年も乗り続けられる品質を追求したボデーの修復と特殊な塗装についてお届けする。
予想をはるかに超えたボデーや部品のサビ
元町工場の一角にある塗装作業に使われていたエリアで分解を終えた初代クラウンは、いよいよボデーのレストアがスタートした。作業を担当するボデーチームは、堤工場の車体部 第一ボデー課で最終ラインの工長を務める石橋港人を筆頭に、田原工場、高岡工場、堤工場、元町工場の生産現場をはじめ、普段は試作車づくりで溶接を担当している開発試作部など、社内の各部署から結集した9名のエキスパートからなる。
そのときのボデーの状態について、リーダーである石橋工長は語る。
石橋工長
シャシーはとてもしっかりしていましたし、塗装された状態では、ボデーのコンディションも良好のように見えました。
当初、私たちは「これなら1カ月もあればボデーのレストア作業は完了するのでは」と思っていたくらいです。ところが、内装部品や基幹部品を取り外してみると、そう簡単ではないことが分かったのです。
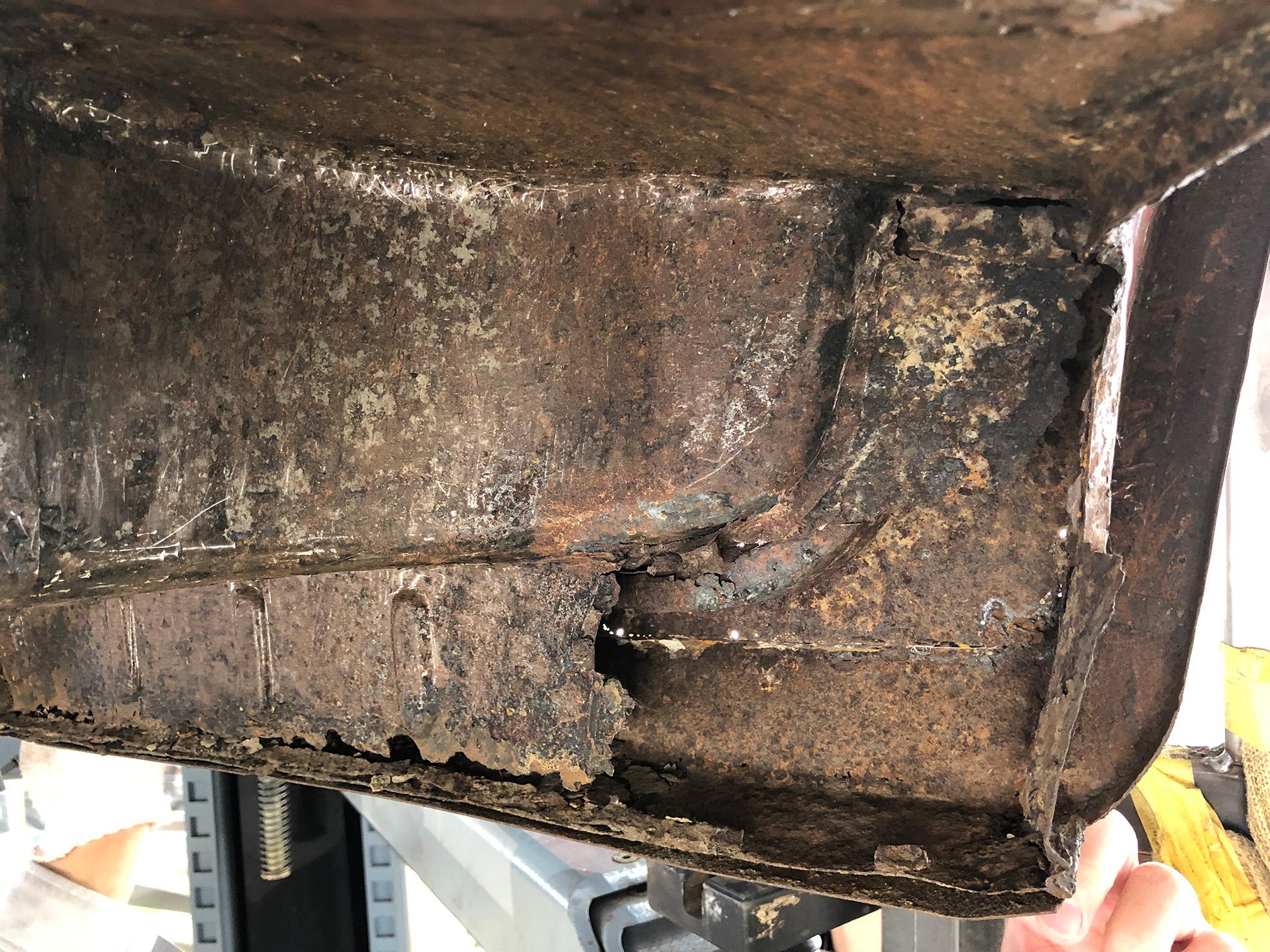
メンバーがまず取り組んだのは、はくり剤などを使ってボデーに施されていた塗装を完全に取り除き、ボデーパネルをシルバーの鋼板の状態に戻すこと。すると塗装の下から、それまで隠されていた真っ赤なサビや細かなボデーのへこみが次々に現れた。
60年を超える長い年月から生まれたサビとへこみは深刻だった。なかでも外からは見えない、アンダーボデーと呼ばれるボデー下側、それもドアの下部やホイールハウスなど、どうしても雨水が溜まる部分の腐食は予想をはるかに超えていた。
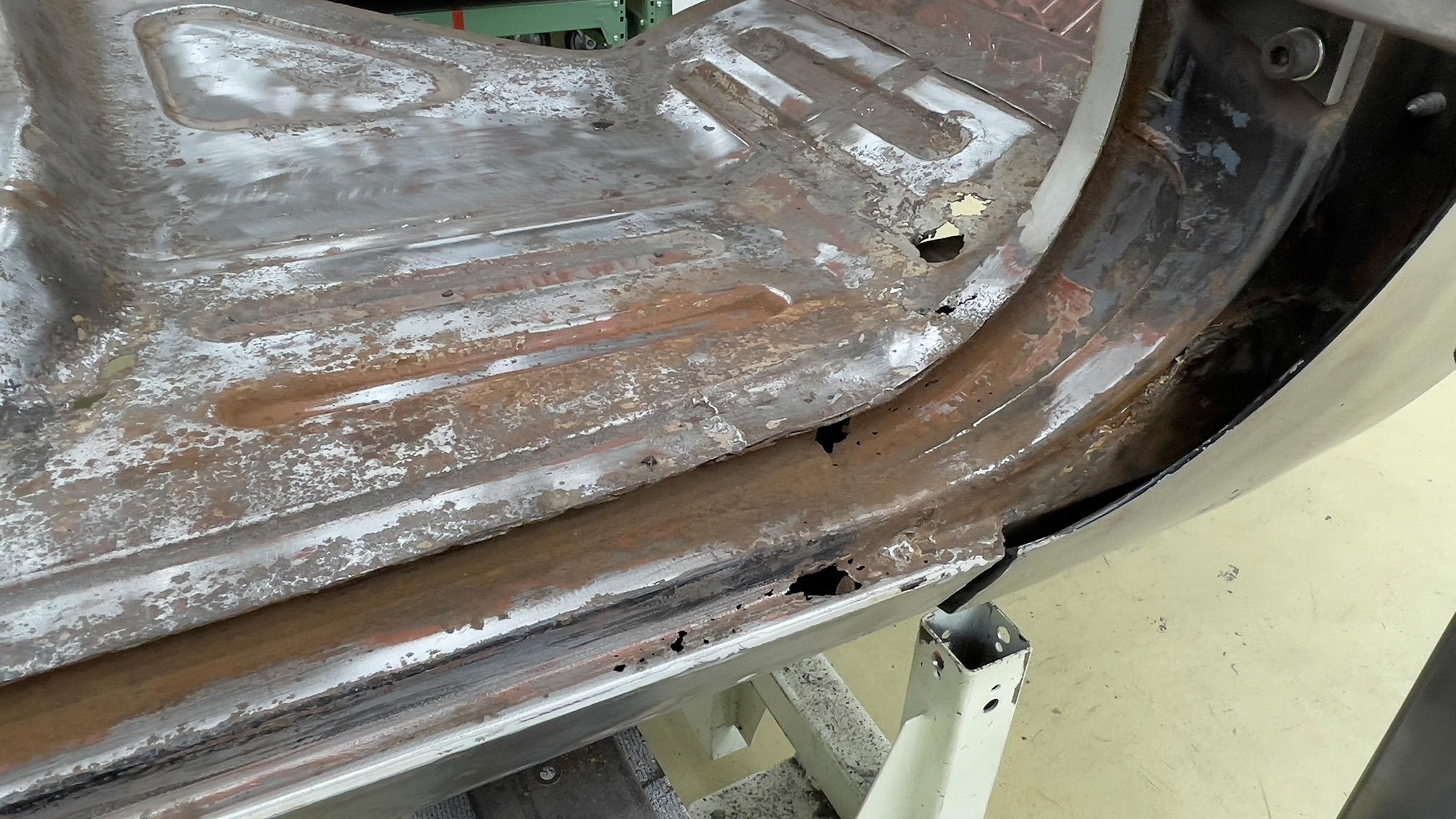
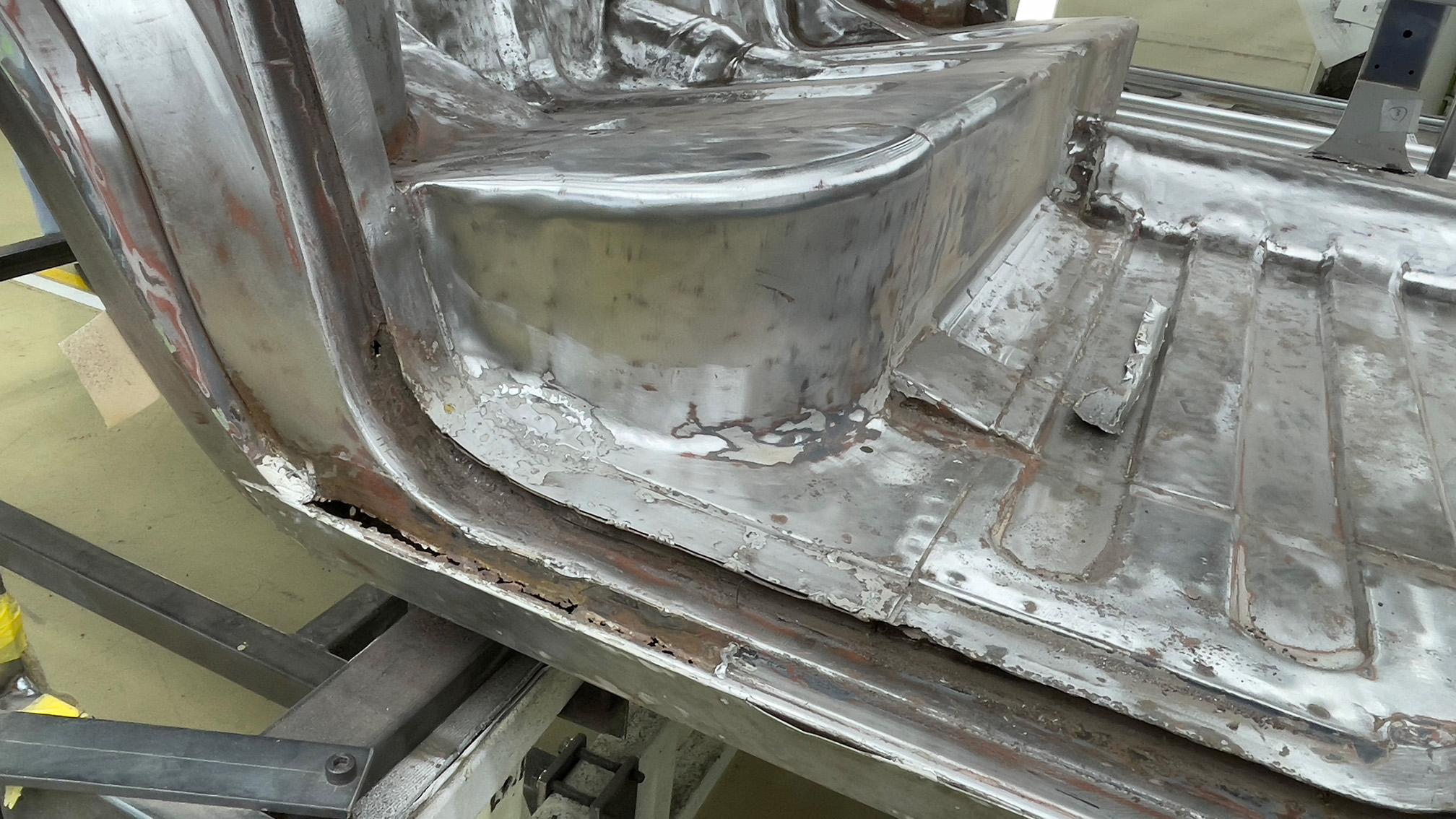
ボデーパネルを型からつくり直し
こうした状況からボデーのレストアは、高技能者ぞろいのメンバーの当初の予想をはるかに超える膨大で難しい作業になった。それは今回のレストアが自動車メーカーだから実現できる、内部まで完璧なレストア、オリジナルを超える品質を目指しているからでもある。
最初のサビ落としから作業は困難を極めた。ヤスリやペーストを使い、手作業でサビを徹底的に落としていく。ボデーの表面に少しでもサビが残ってしまうと、その部分に塗料が乗らない。そのまま塗装をすると、塗装表面はサビ部分が凸凹になって美しく仕上がらないし、再びそこから腐食が起きてしまう。だから作業に一切妥協はできない。
チームメンバーのひとり、田原工場車体部レクサスボデー課の佐藤隆明SXは語る。
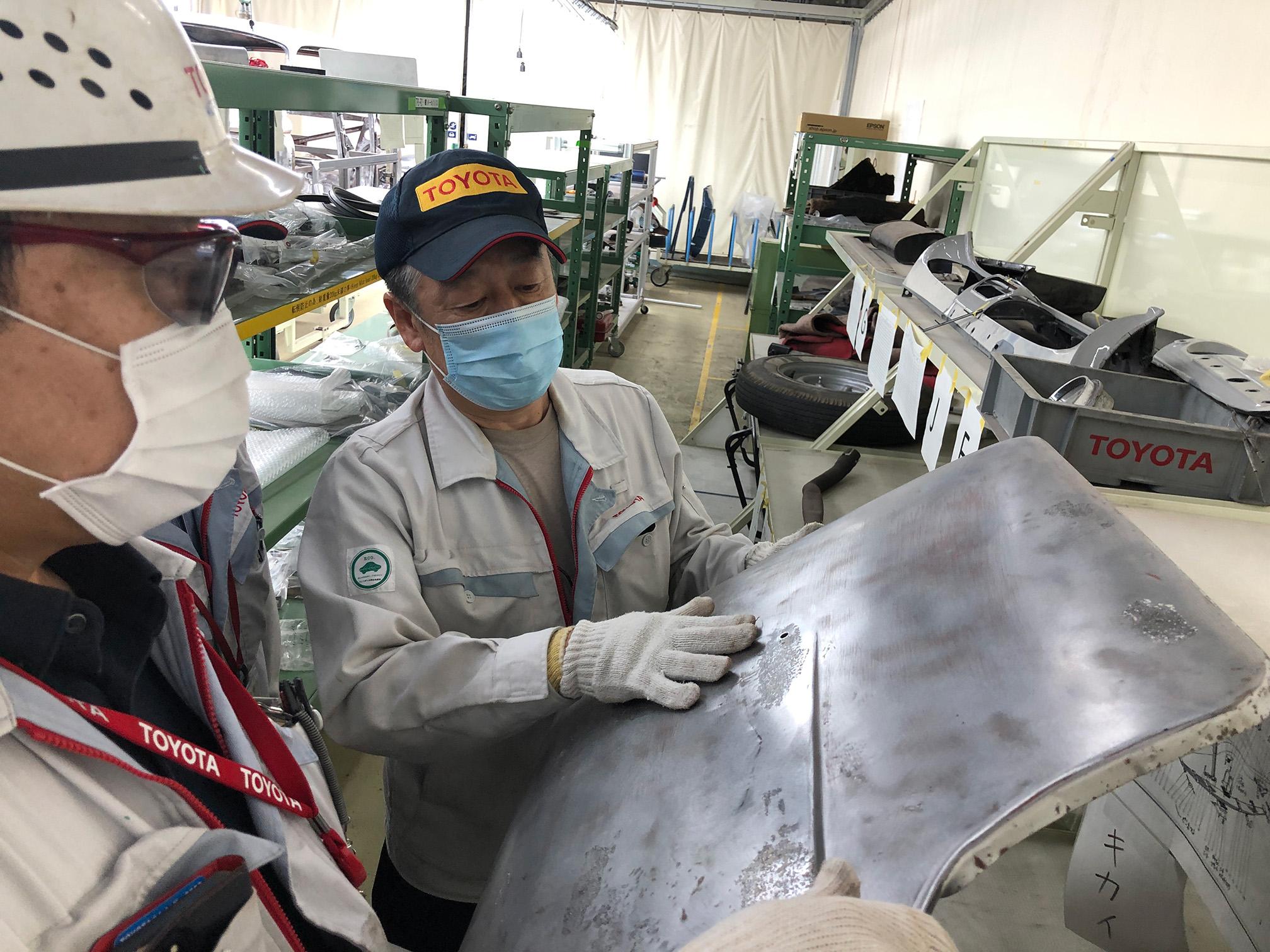
佐藤SX
初代クラウンのボデーは、現代のクルマのように部品の合わせ目にシーリングが施されていません。そのためサビが発生しているのは、長い年月を考えれば仕方がないことだと思います。
でもボデーの腐食状態をみて、改めてサビの恐ろしさを実感しました。また、ボデーのへこんだ部分にパテを盛って応急的な修理がしてある部分も見つかりました。これもそのままにはできません。

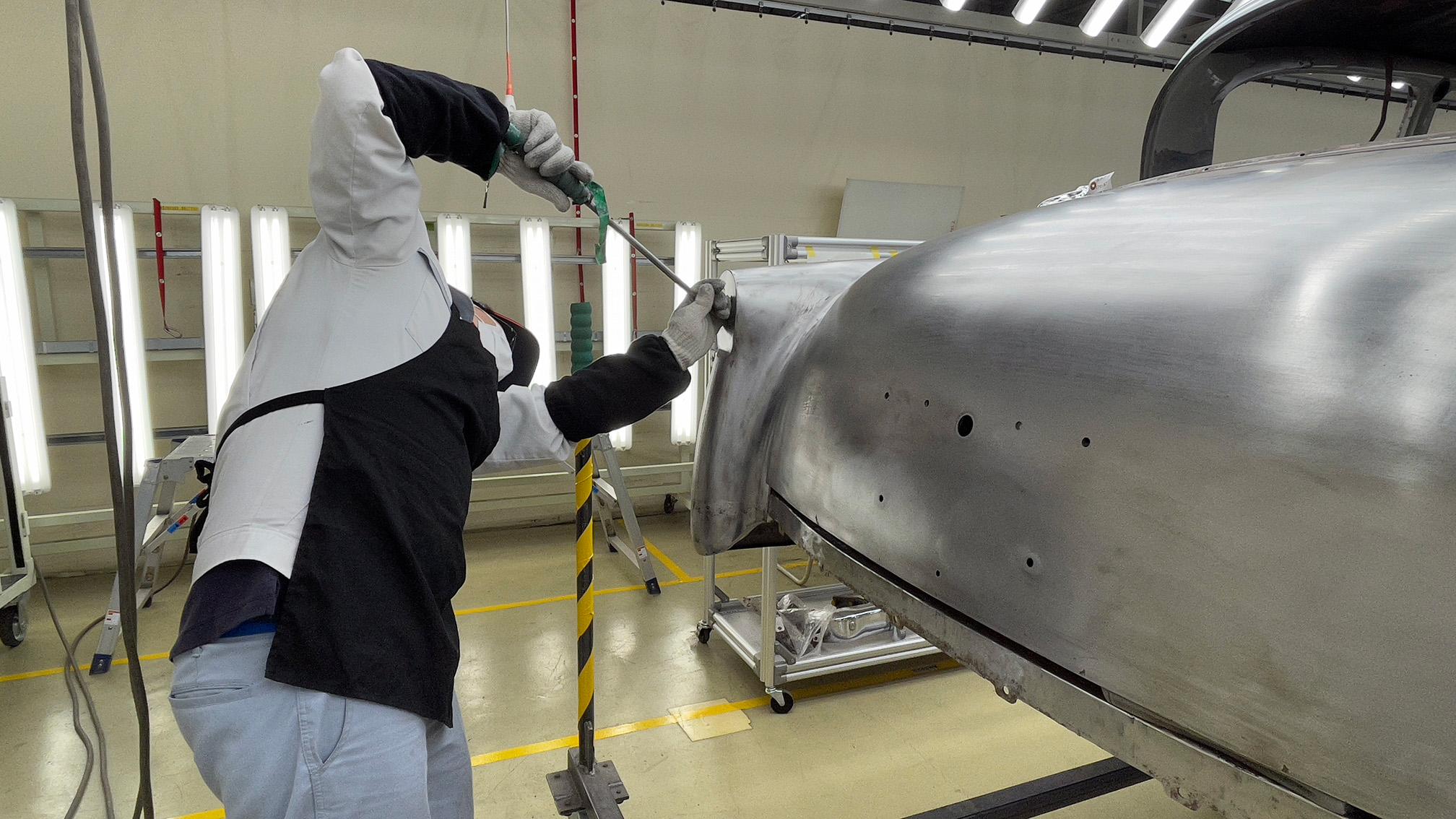
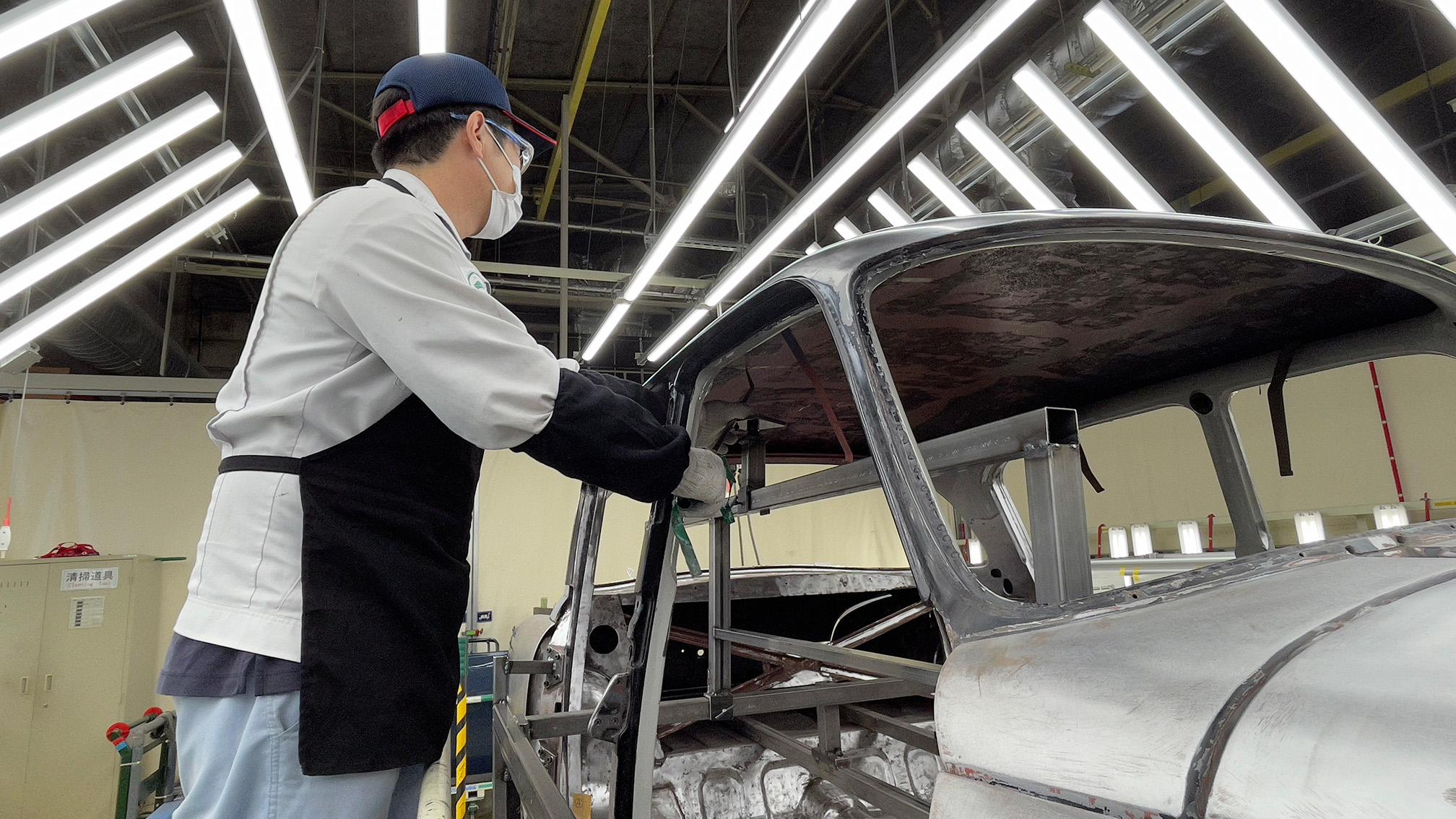
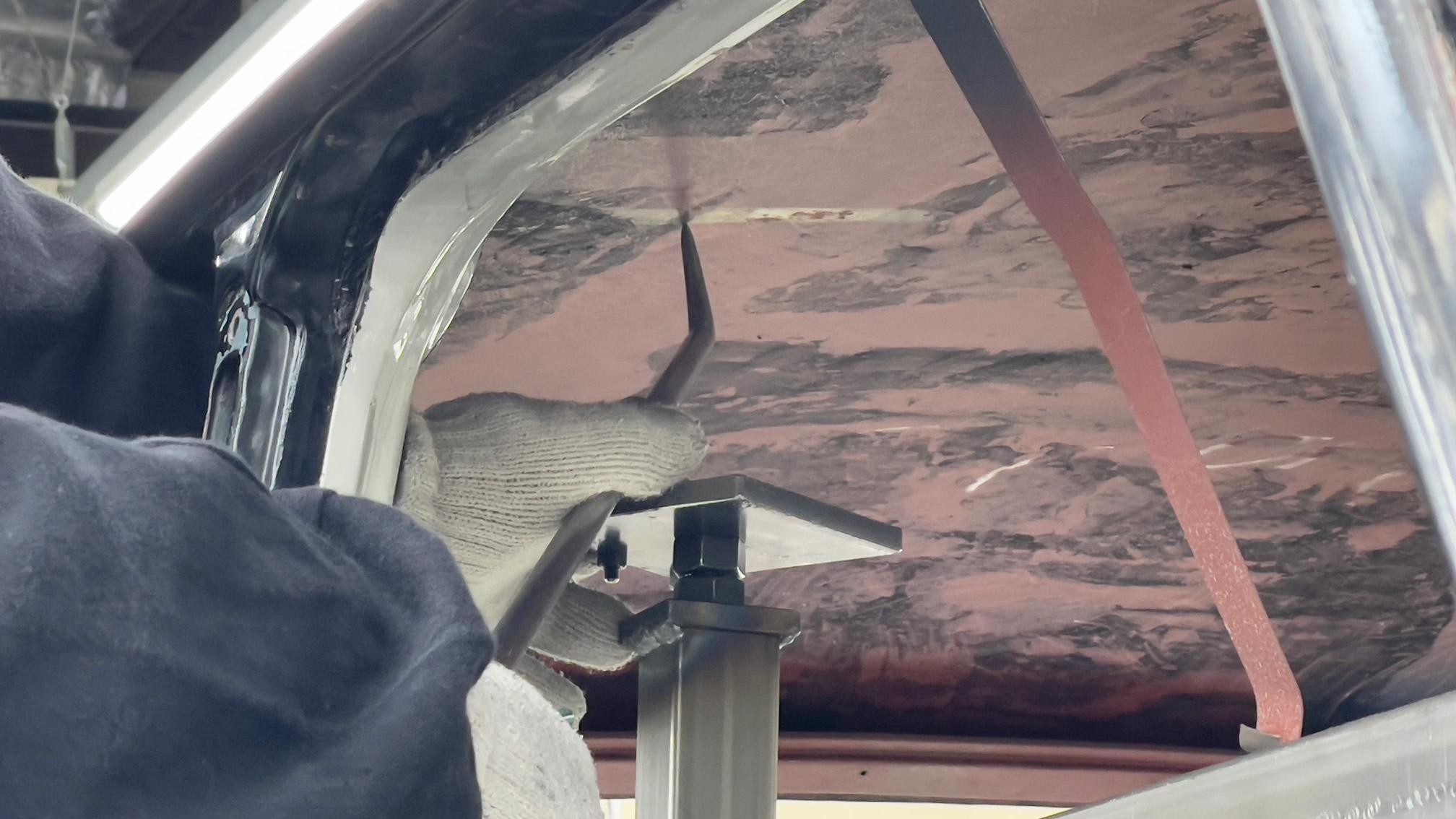
数週間をかけて、手作業によるサビ落としが終わると、いよいよ板金作業だ。見つかったボデーのへこみは、一つひとつハンマーなどの工具を使い、手作業で叩き出して元通りの姿に戻していく。
また、へこみにパテを盛って修理した部分は、パテを取り除いてから、叩き出しの作業を行う。さらに小さなへこみは一つひとつ、へこんだ鋼板の表面に銅線をいったん電気溶接して、その鋼板を引っ張ることでへこんだ部分を引っ張り出す「スタッド溶接」という方法で修理していく。
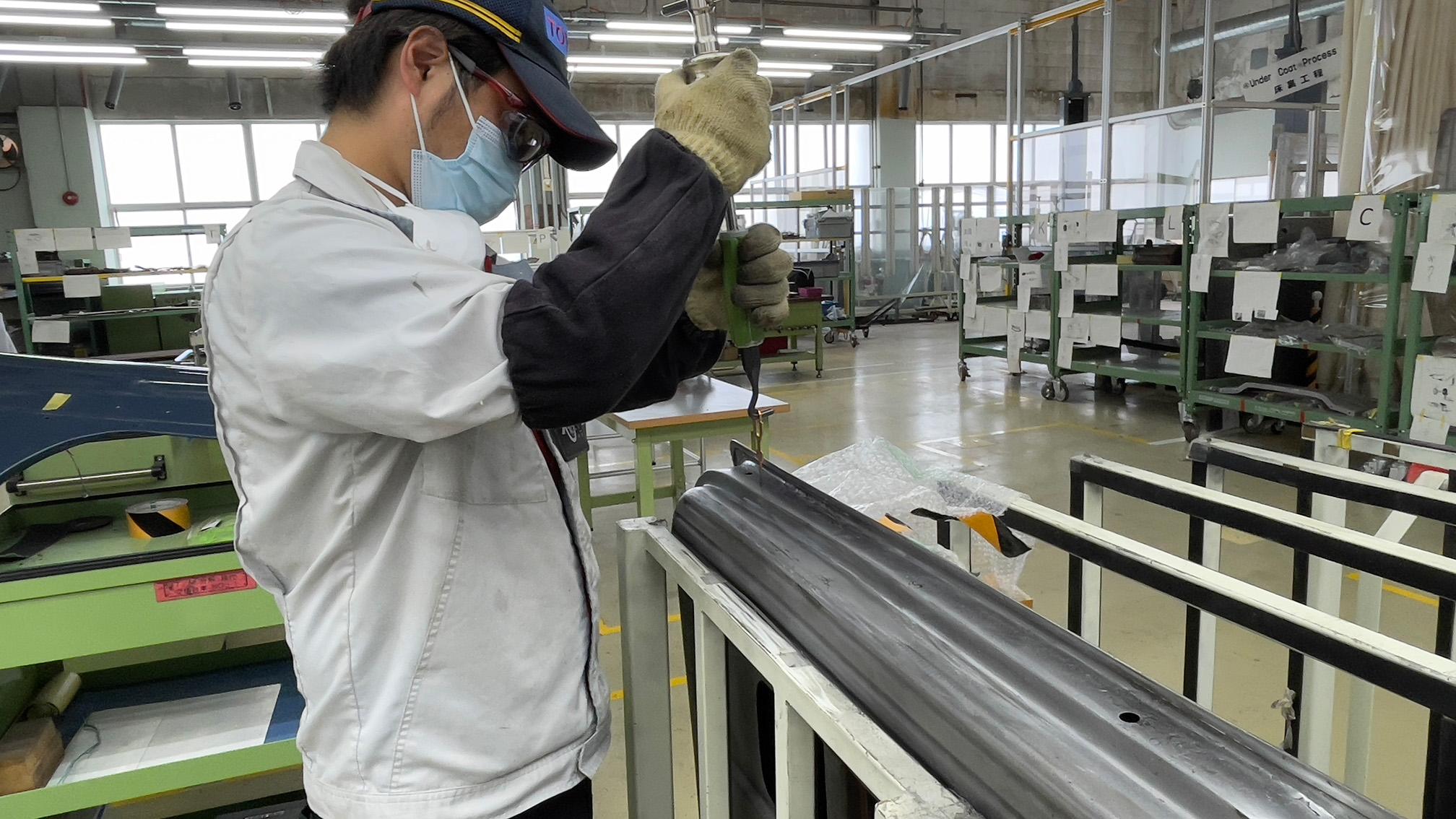

しかし、サビ落とし作業で鋼板が薄くなったり、腐食して穴が開いてしまったりした部分は、もはやどうしようもない。初代クラウンのボデーは鋼板でつくられたパネルを何枚も溶接することで構成されている。
小さなダメージの場合にはその部分に鋼板を当てて溶接して修復する。だがパネルのダメージが大きければ、パネルの型をつくり、その型に合わせて鋼板をハンマーで叩いて成形するという板金加工で、パネル自体をゼロからまるごとつくるしかない。
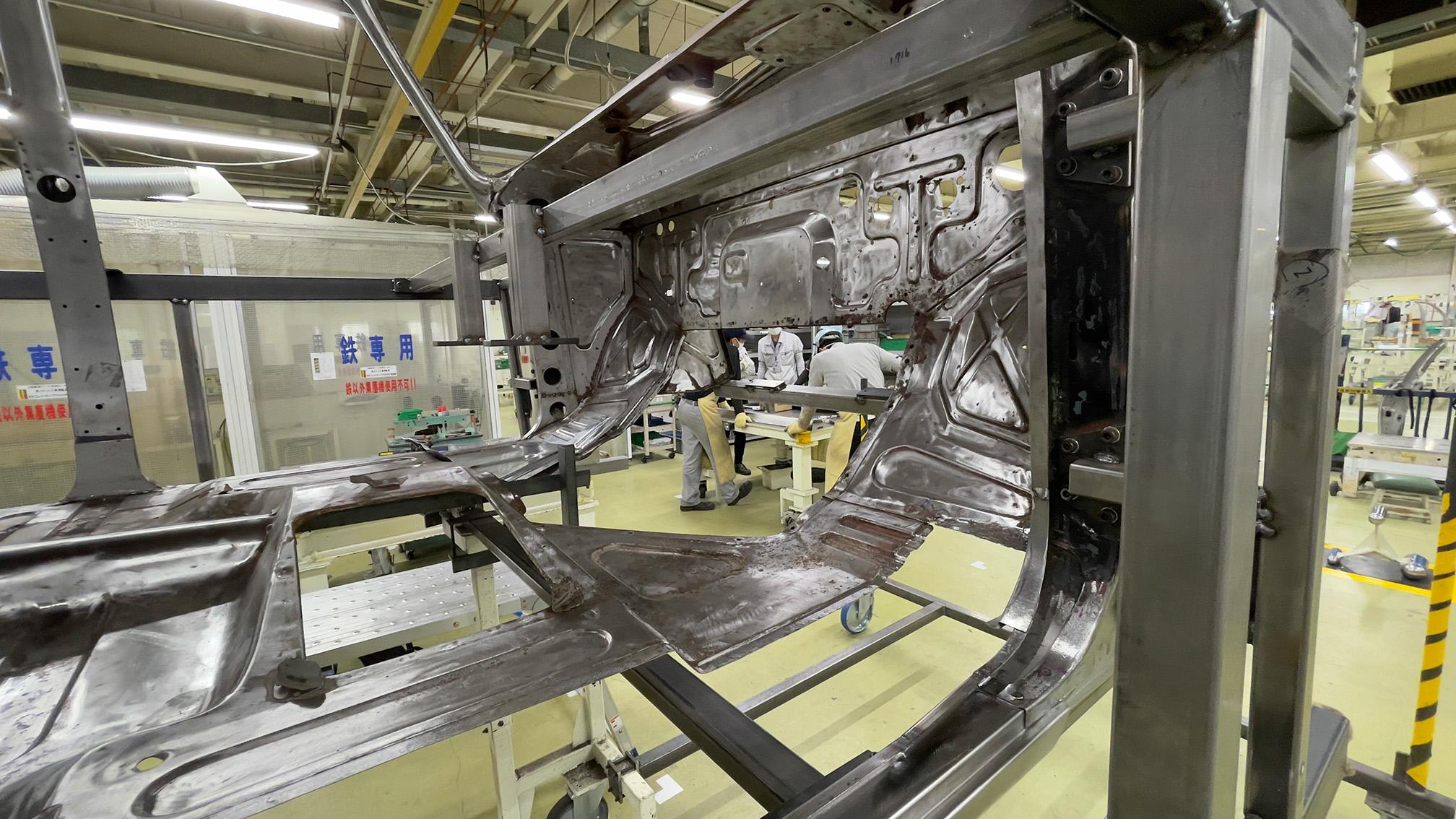
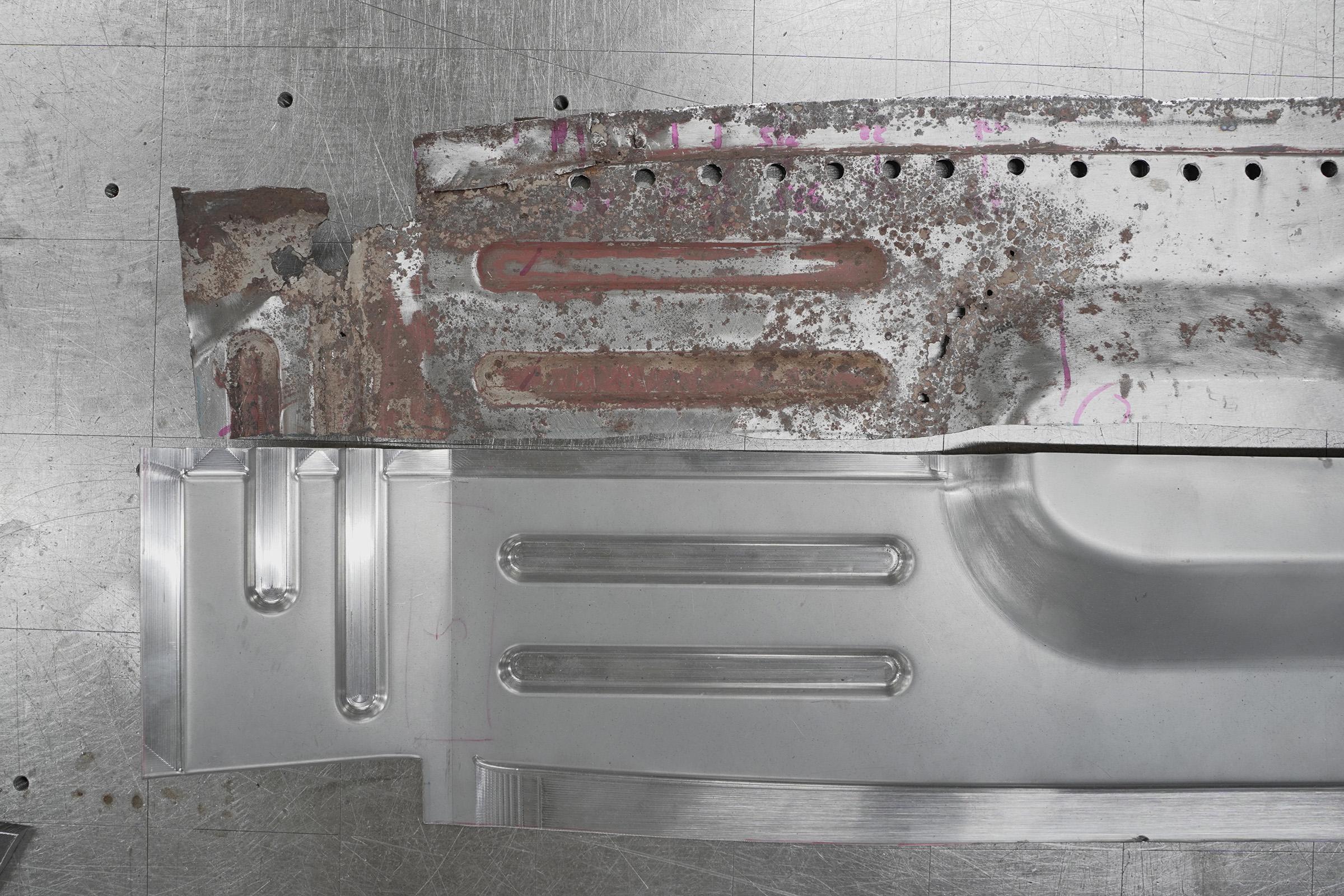
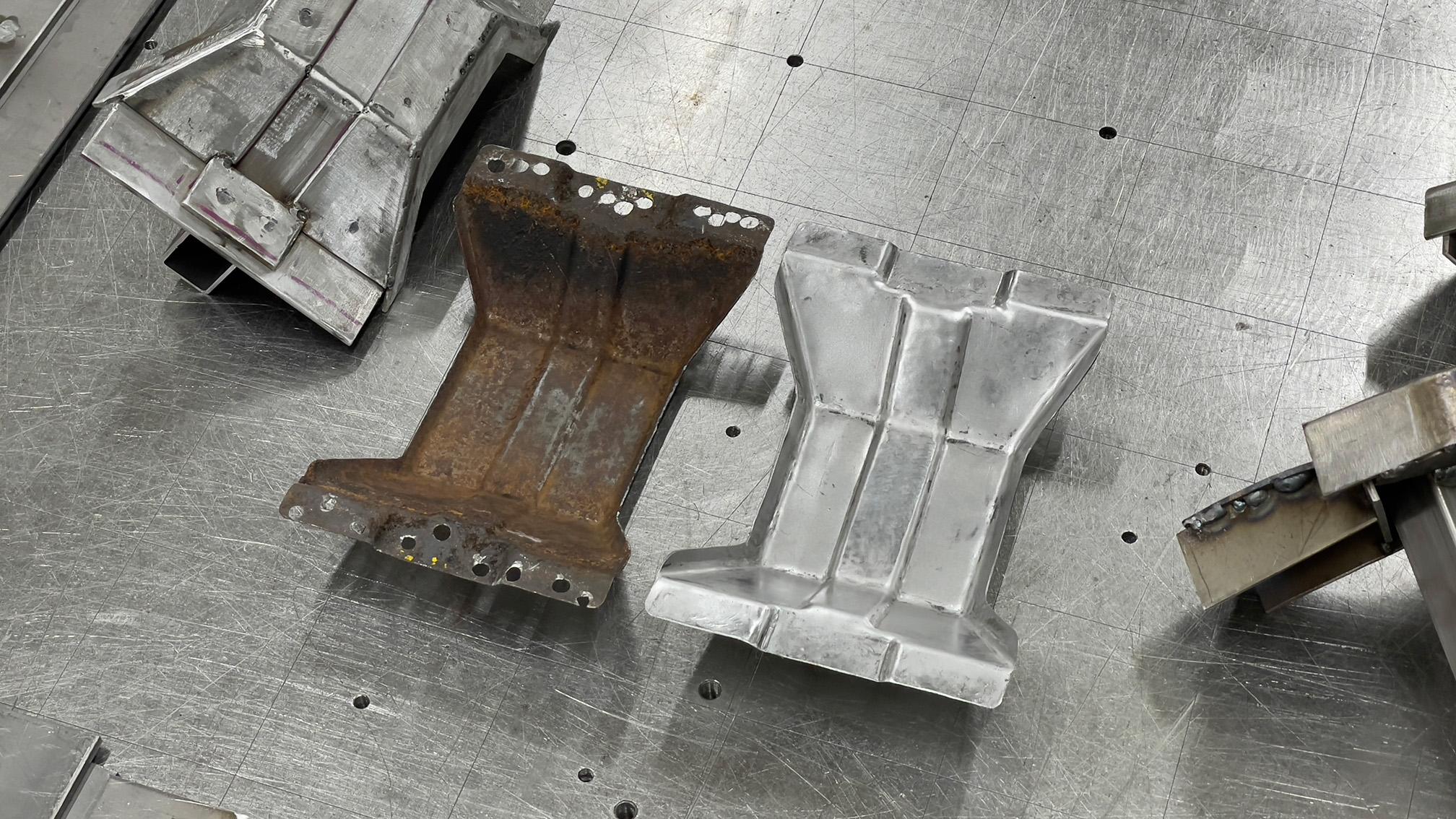
この難題続きの板金、溶接、そしてパネルづくりの作業を、ボデーチームの9名のエキスパートたちは着々と進めていった。ちなみに石橋工長は、国内はもちろん、世界中の工場立ち上げを指導してきた溶接の達人だ。
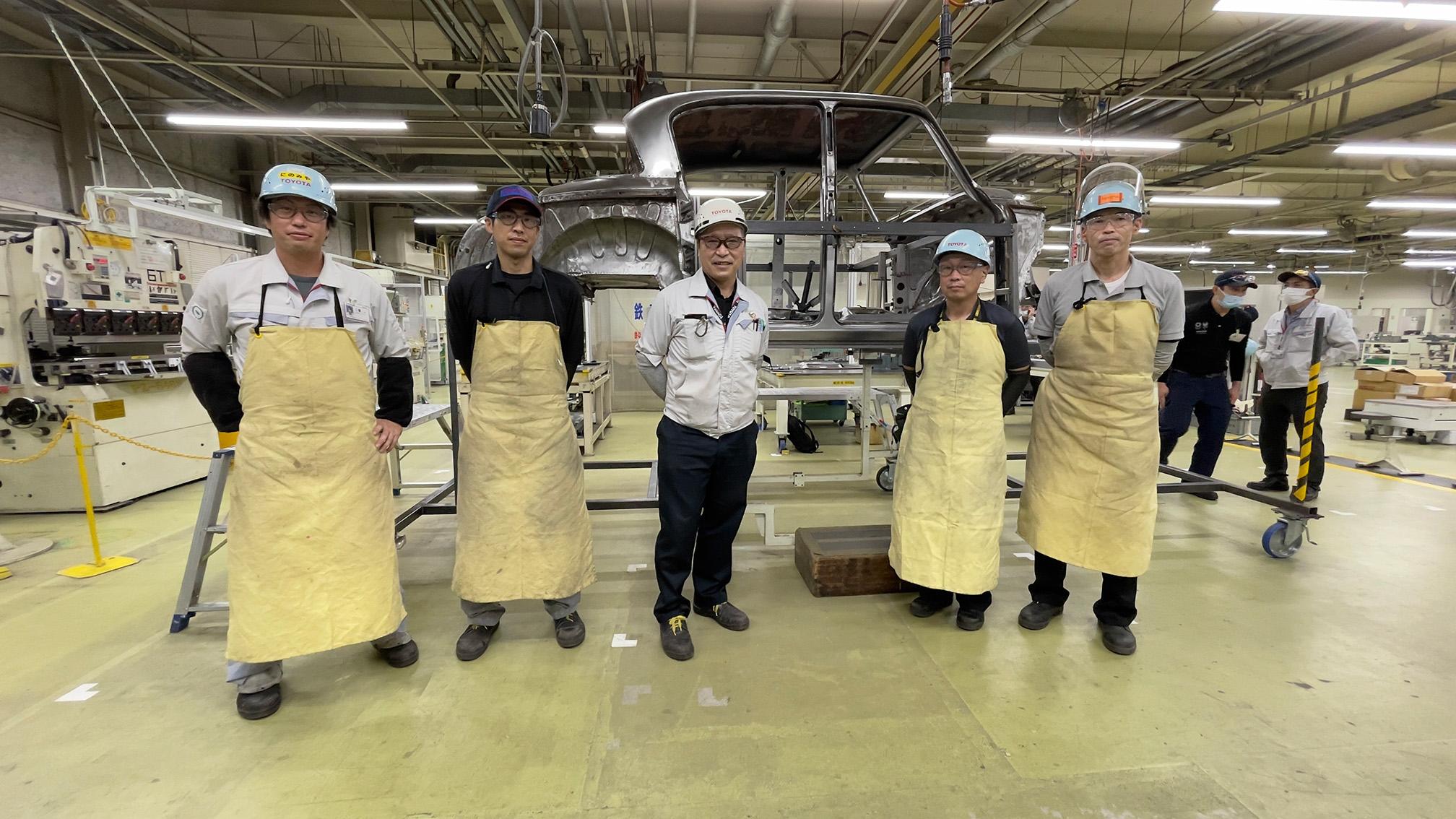
石橋工長
長らく生産現場の仕事に携わってきましたが、今回のレストア作業は経験のないことばかりでした。たとえば型からボデーのパネルからつくるのは自分のキャリアでは初めて。生産現場の高技能者と試作開発部門から集まったメンバーが協力して取り組むことで、この作業を進めることができました。
そのうえ、作業を進めれば進めるほど、もっと良くしたい部分が出てくる。結局、各メンバーの職場に何度もお願いして、復帰時期を延ばしてもらうことになりました。
高岡工場からメンバーとして加わった若手、36歳の二宮貴仁も、ボデーのレストア作業は毎日がトライ&エラーの連続だったと語る。
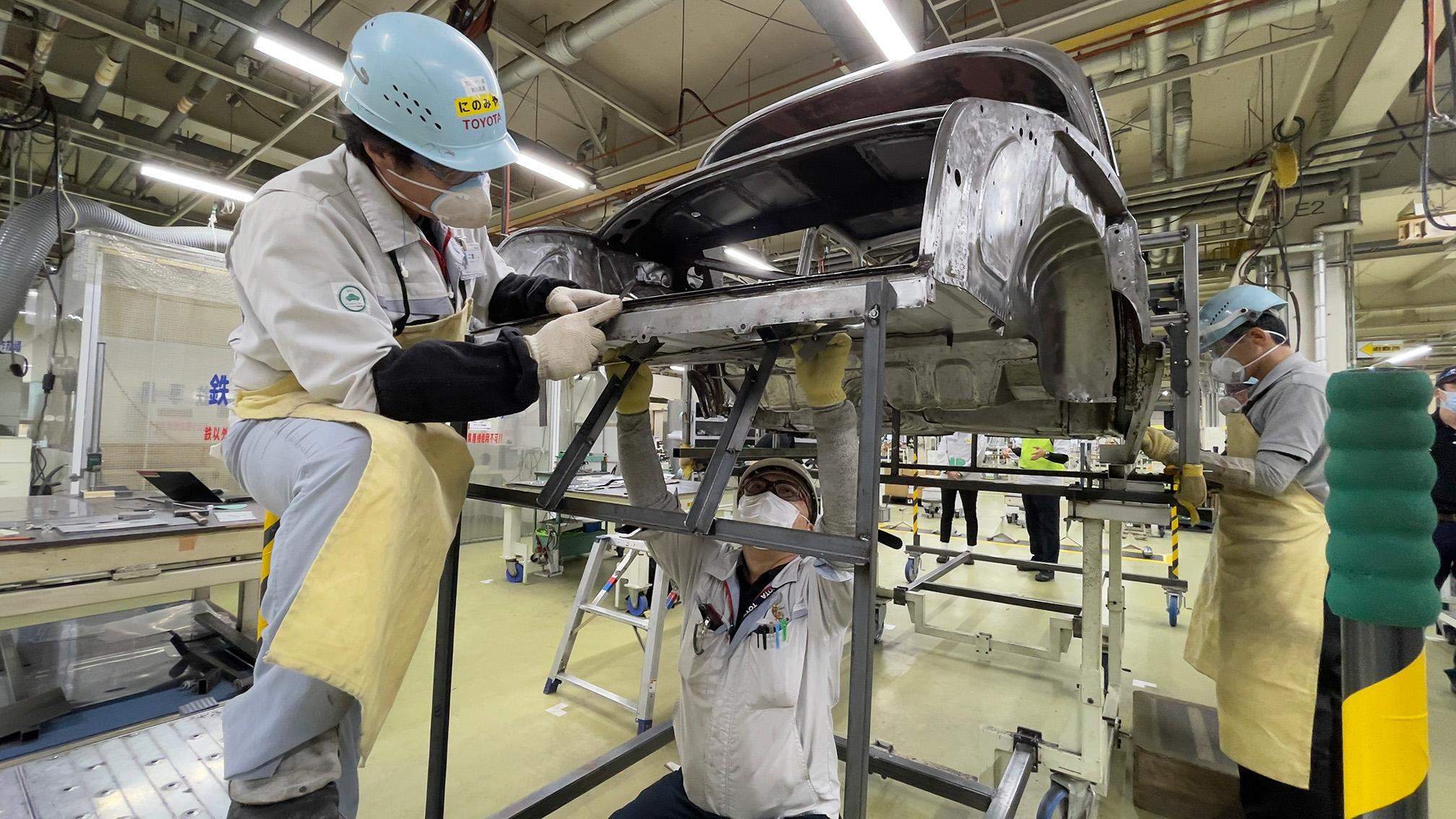
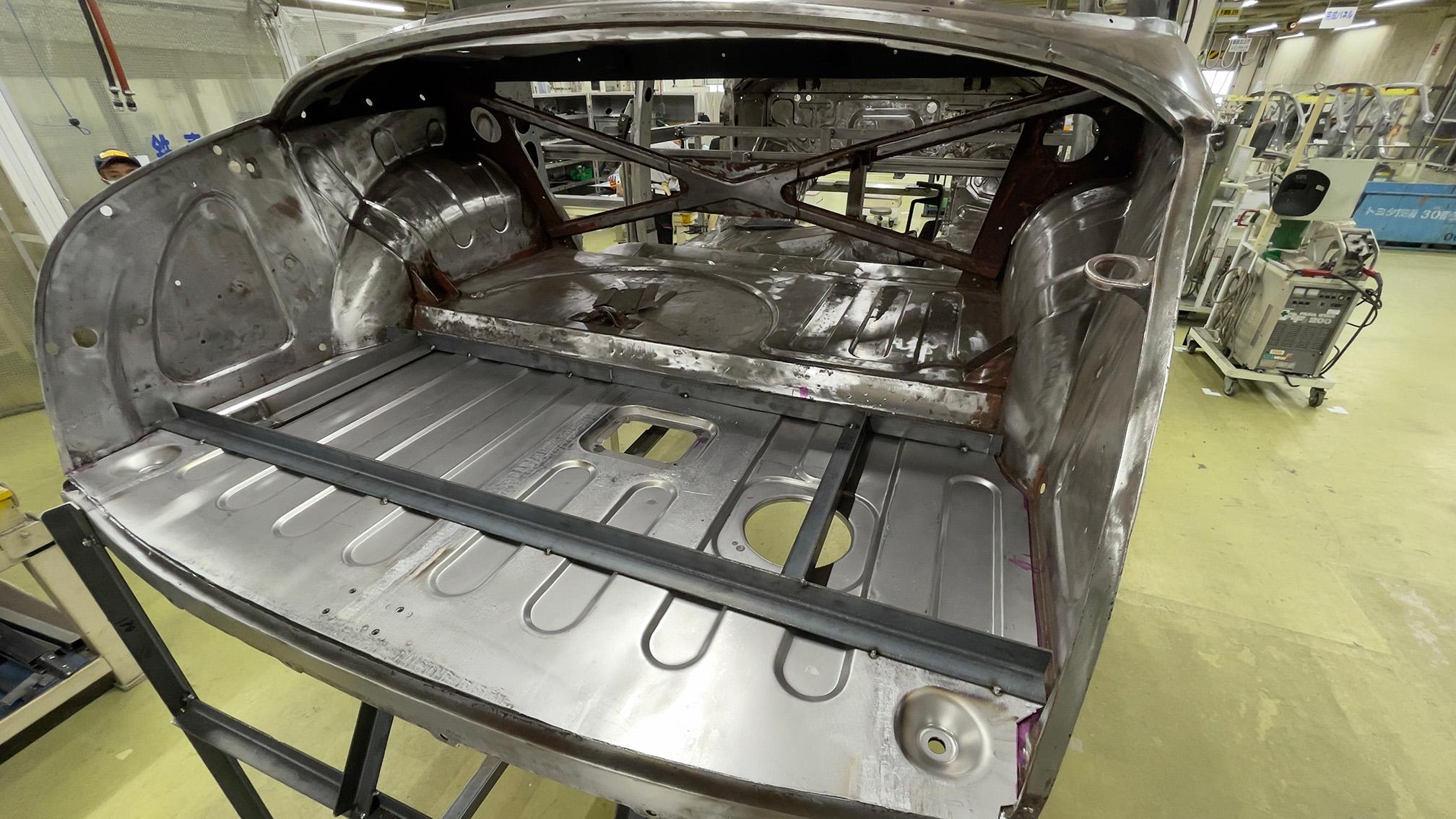
二宮TL
作業の基本はいつもの仕事と同じ。ところがうまくいかない。初代クラウンのボデーは、薄いところでも現行車よりはるかに厚く1㎜以上もある。ハンマーで叩いてボデーを元通りの形状にしようとしても、思い通りにならない。すべての作業がチャレンジで、とにかくやってみるしかないんです。
作業が難しければ難しいほど、メンバーたちのモチベーションは高まった。そして作業の過程で、65年前にこのクルマをつくった人々の技能の素晴らしさを実感したという。
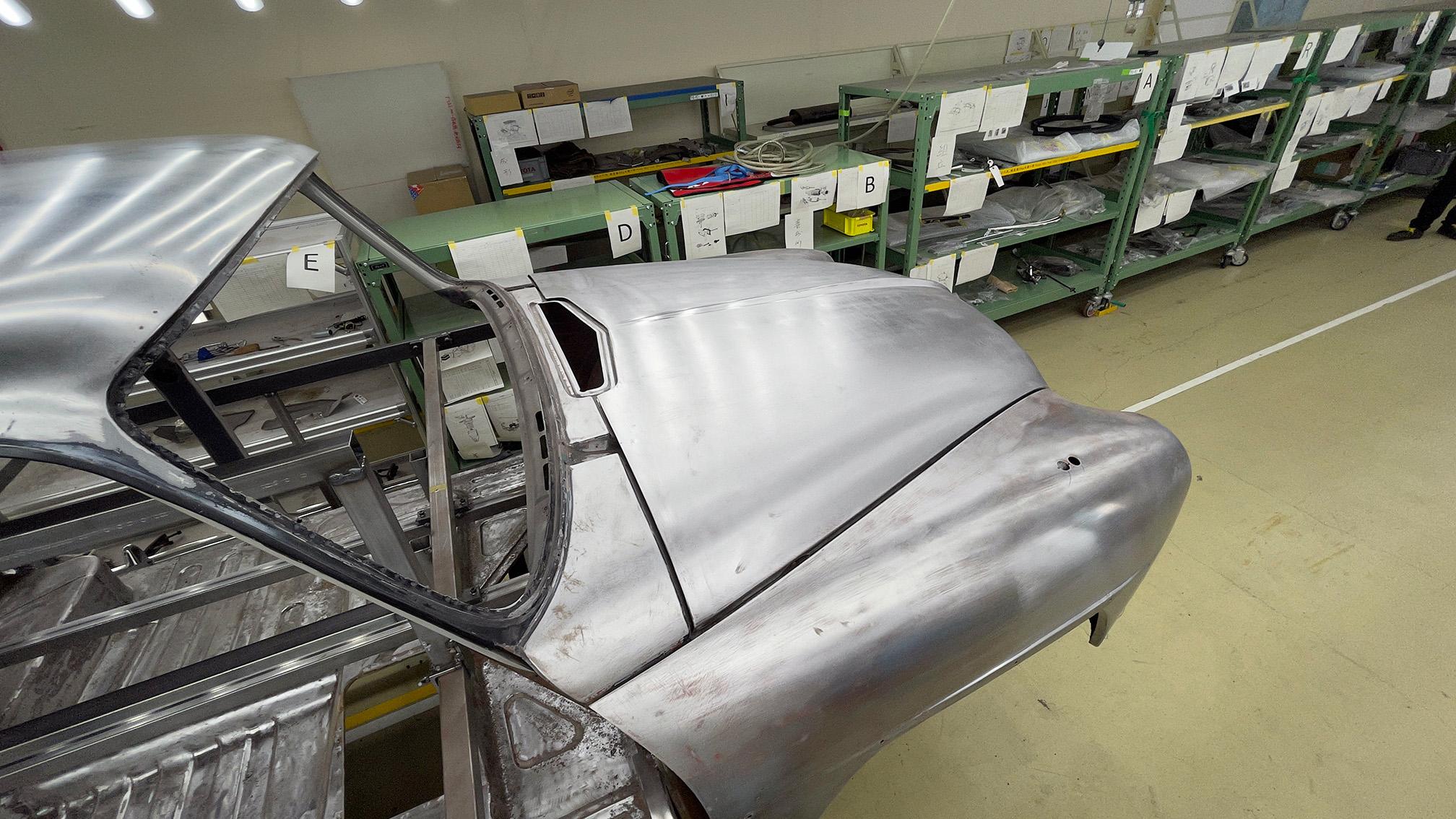
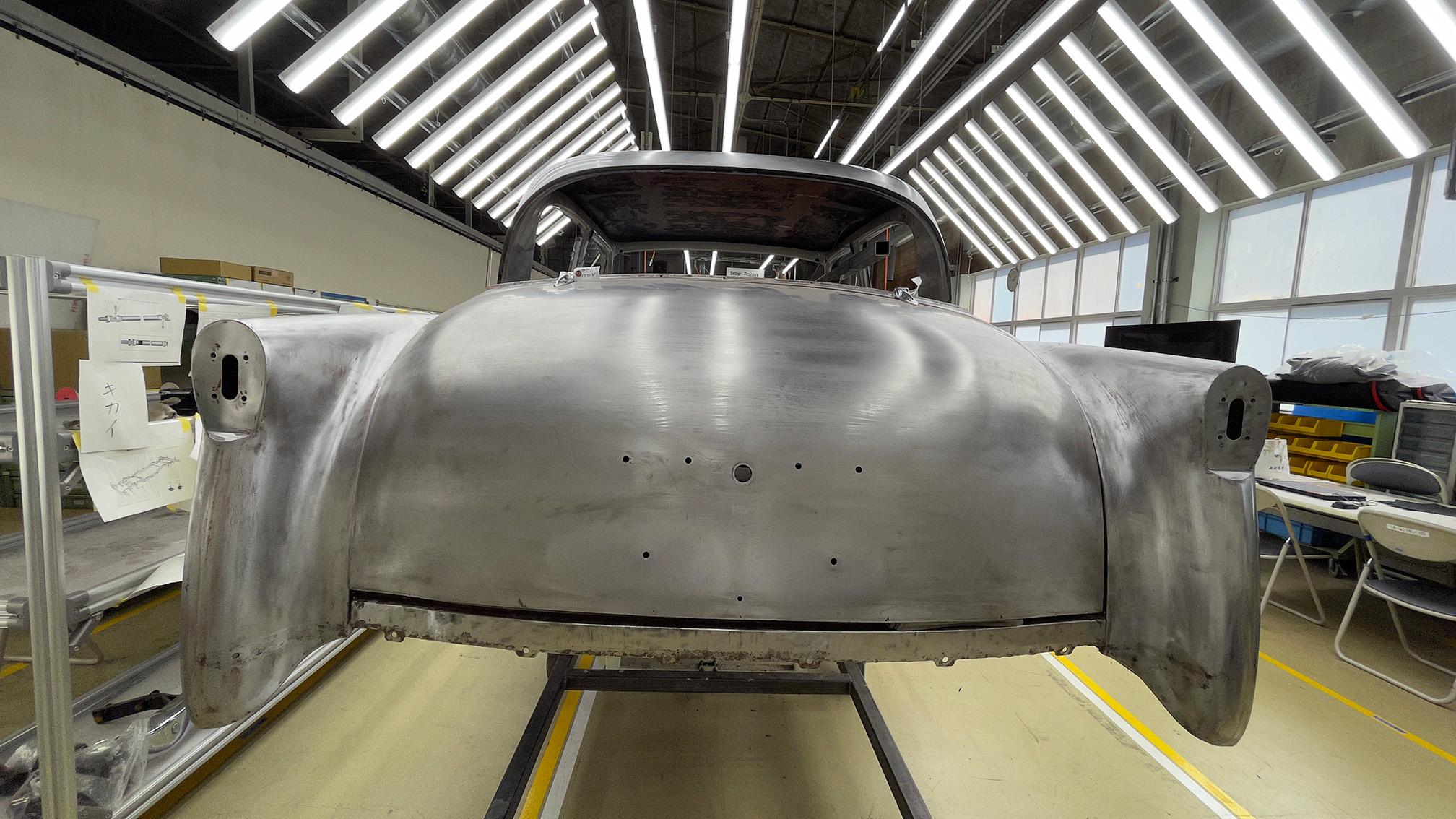
石橋工長
たとえば流線型のボデーのハイライトのひとつである絶妙な丸みのフェンダー部分ですが、ここは3枚のパネルを溶接することで構成されています。現在のように設備が整っていないなかで、このような高度な溶接作業ができたのは、当時の匠たちが非常に優れた技術を持っていたからでしょう。
ちなみにこのボデーを構成するパネルの製作では、従来の板金溶接の方法に加えて、「インクリメンタル成形」と呼ばれる量産ボデー製造ラインではあまり見かけない製造方法も採用された。こうしたレストアへの新工法導入の挑戦については、次回以降で改めてリポートしたい。
トヨタが誇る高技能者にとっても「すべてが挑戦」だったというボデーのレストア作業は、スタートから数カ月を経て2022年10月末に完了。次の塗装工程へと移った。
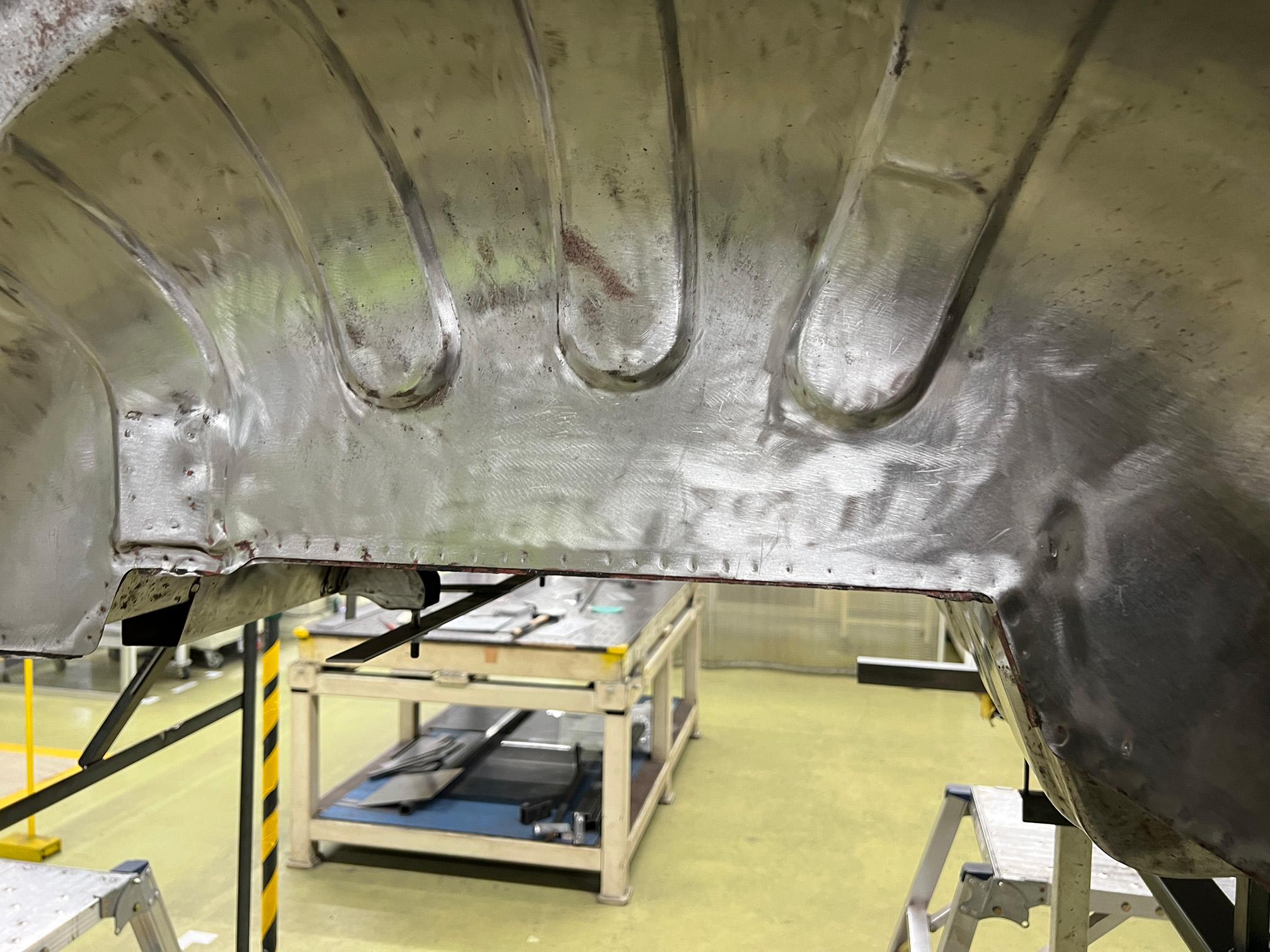
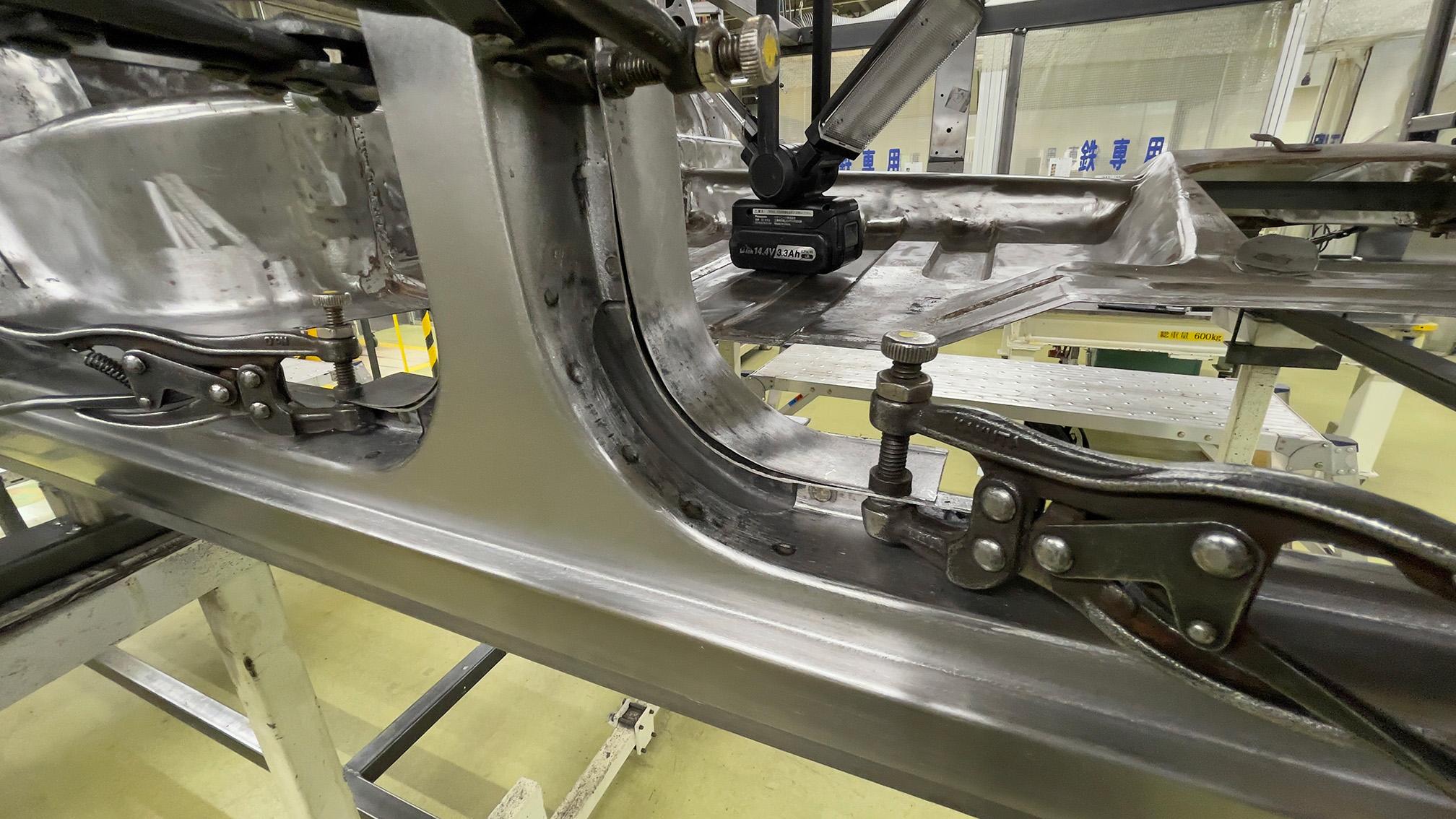
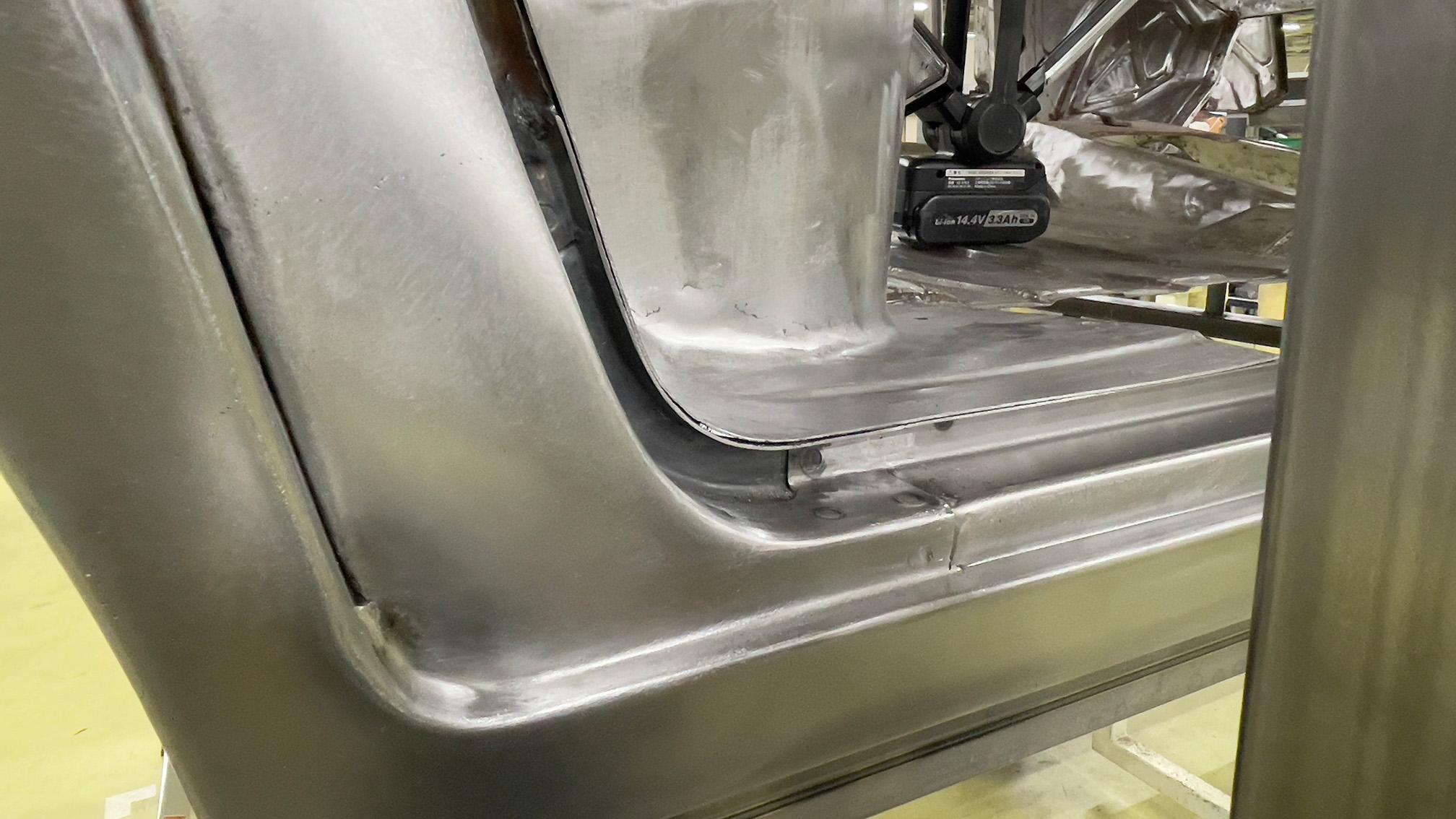