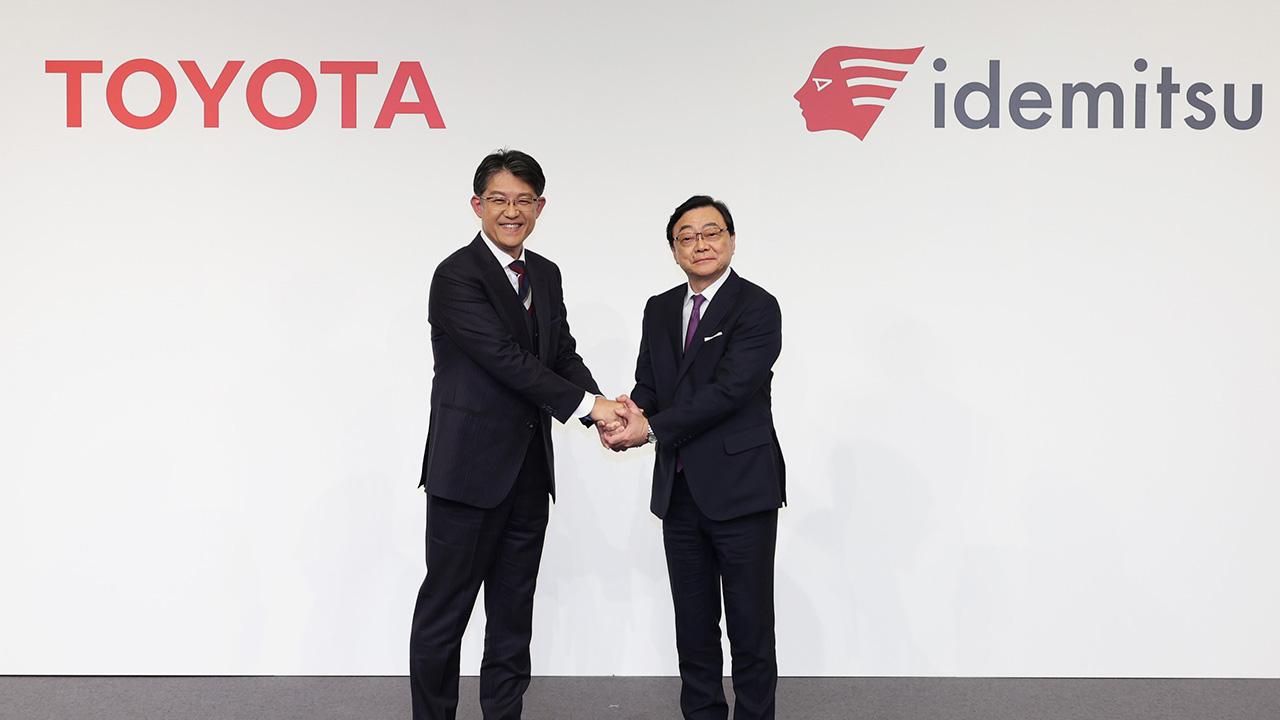
All-solid-state batteries have been touted as the future of batteries and a game-changer for BEVs. Two companies have joined forces to make the Japanese industry more globally competitive.
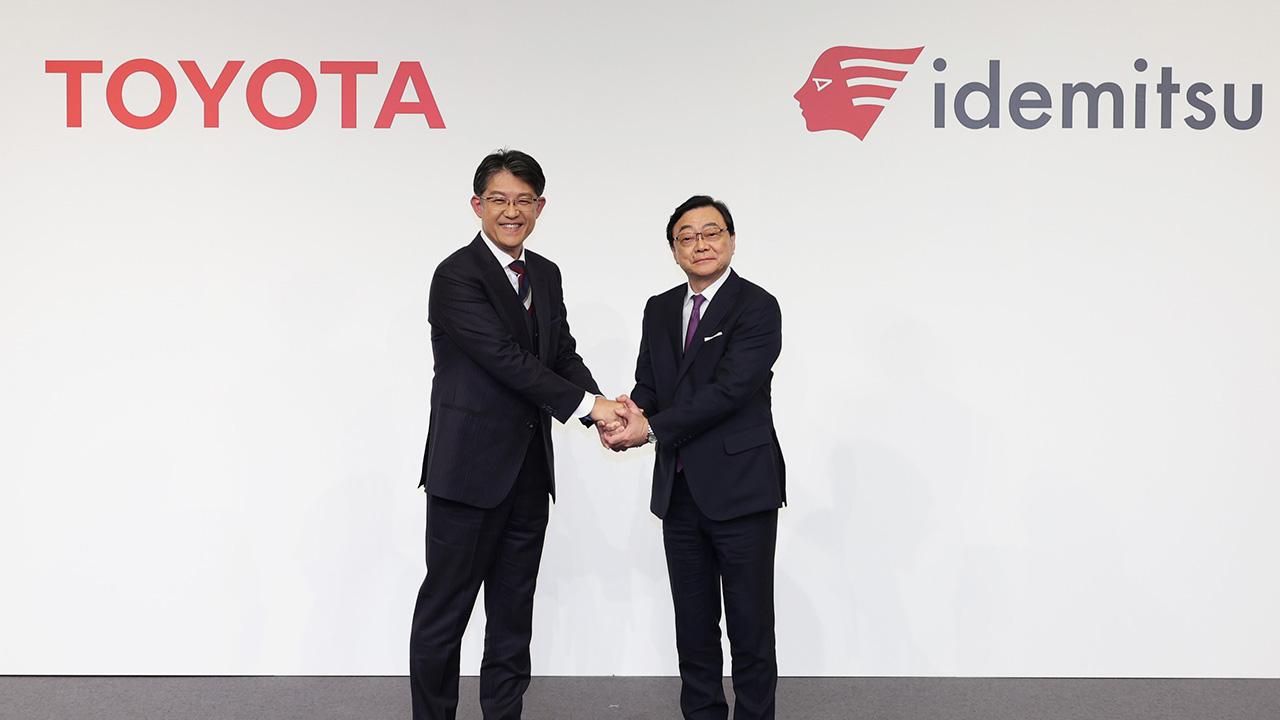
On October 12, Idemitsu Kosan and Toyota announced that they will work together toward the mass production of all-solid-state batteries.
The two companies will seek to develop mass production technologies for solid electrolytes—the pathway for ions moving between the cathode (+) and anode (-)—to improve productivity and establish a supply chain.
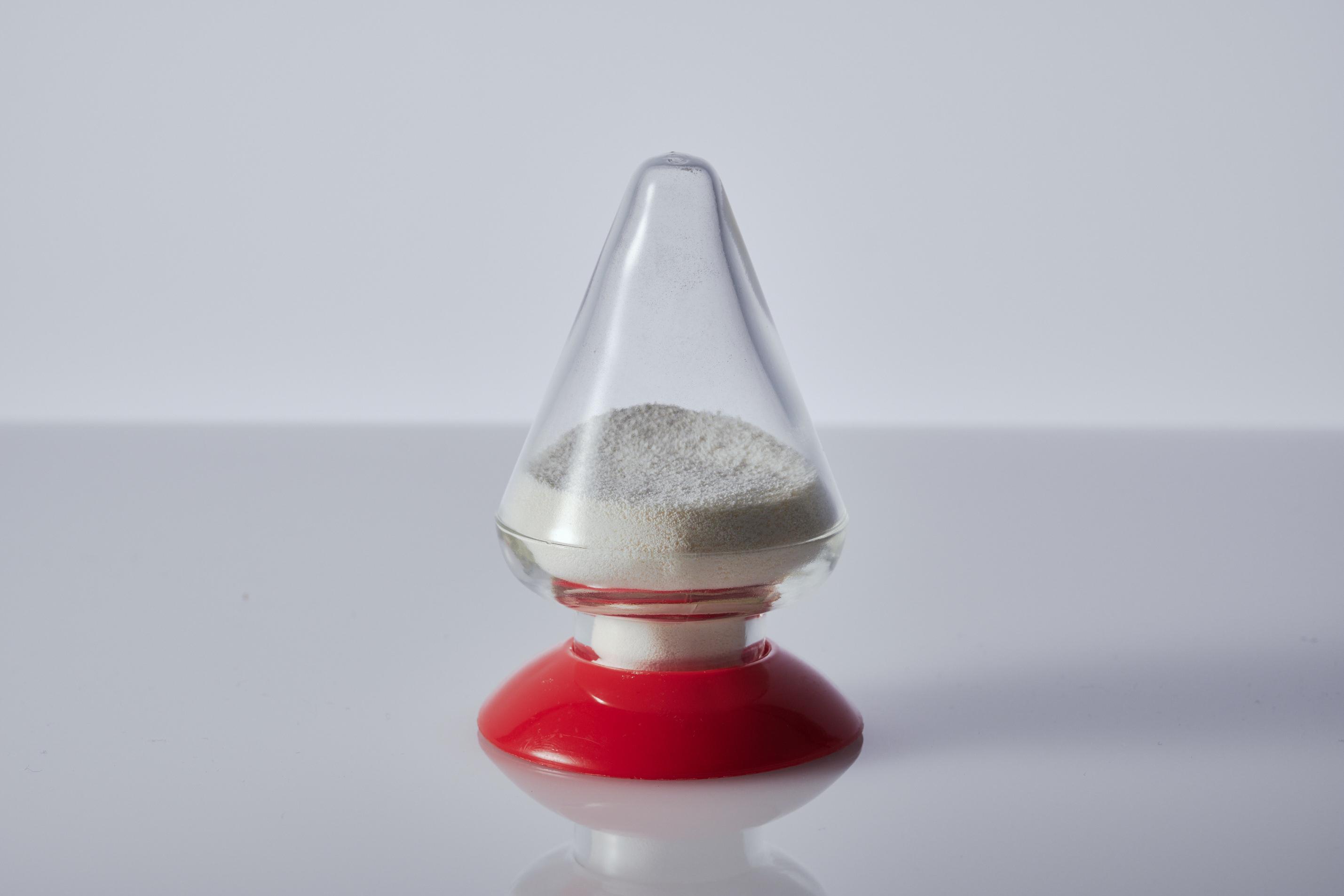
Toyota aims to commercialize the technology with battery electric vehicles (BEVs) slated for release in 2027-28.
The two companies lead the world in patents related to all-solid-state batteries and the sulfide solid electrolytes used to make them. Through closer collaboration, they will aim to establish the global standard.
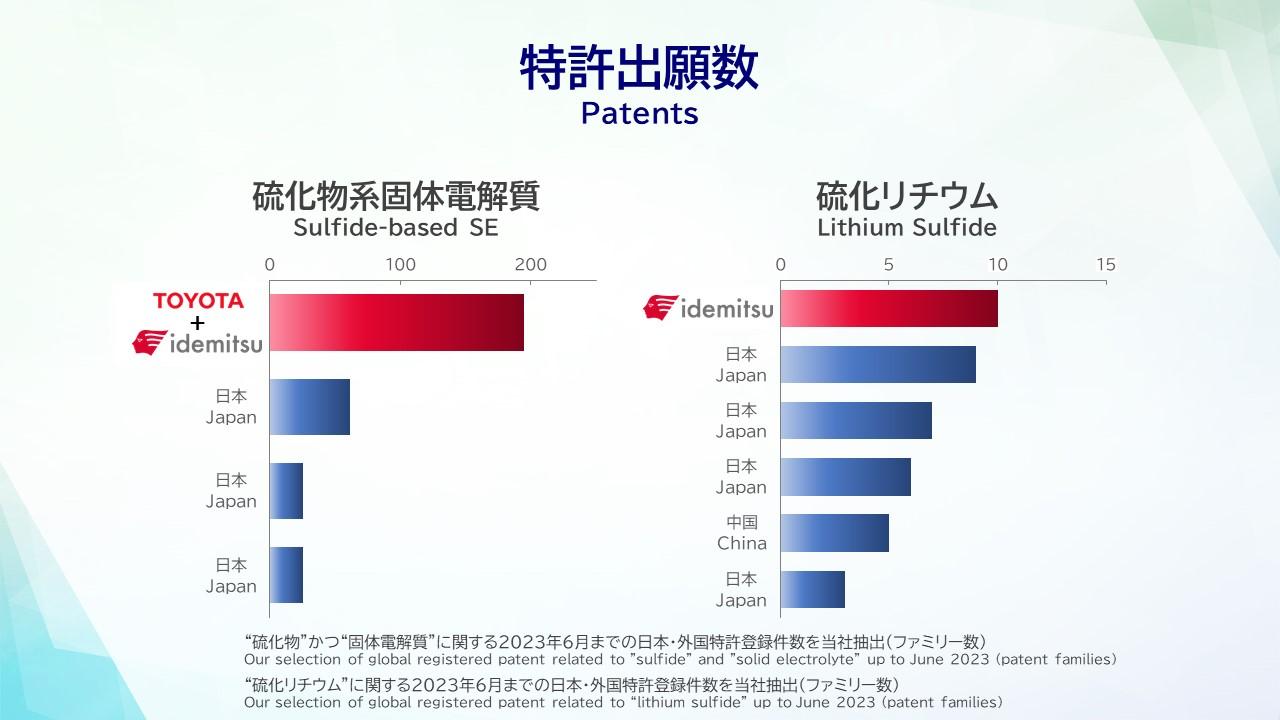
“For the beginning of the manufacturing phase, the important thing is the power of realization,” Toyota President Koji Sato emphasized at the press conference. “Working together will multiply our power of realization many times over.”
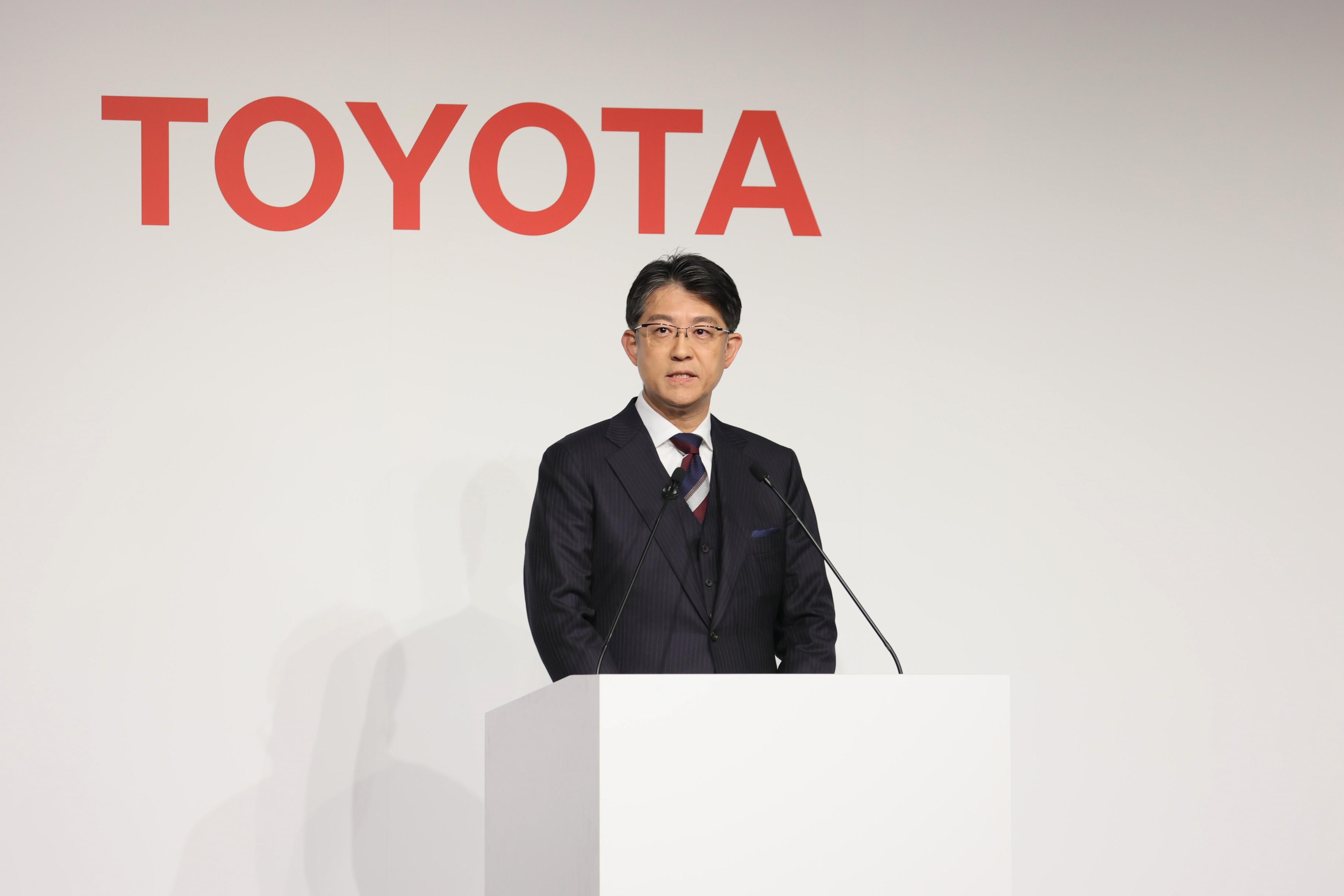
The three-way advantages of all-solid-state
Batteries charge and discharge as ions move between the cathode and anode. In most cases, the electrolyte that serves as their pathway is liquid. By providing a solid pathway, all-solid-state batteries allow ions to move faster.

This shortens BEV charging times, extends cruising range, and boosts output.
President Sato pointed out that the higher energy density can help enhance a vehicle’s basic performance.
“Instead of vehicle development revolving entirely around aerodynamics, for example, we will have greater freedom to create attractive designs and spaces that allow for better cabin packaging.”
Idemitsu technologies overcome drawbacks
Meanwhile, the chief drawback is battery durability. The constant cycle of expansion and contraction during charging and discharging may cause cracks between the solid electrolyte and the cathode/anode, degrading performance.

Idemitsu has worked on solving this issue with Toyota since 2013.
Through a decade of trial and error, the two companies combined their technologies to develop a flexible, highly adhesive, and crack-resistant solid electrolyte material.
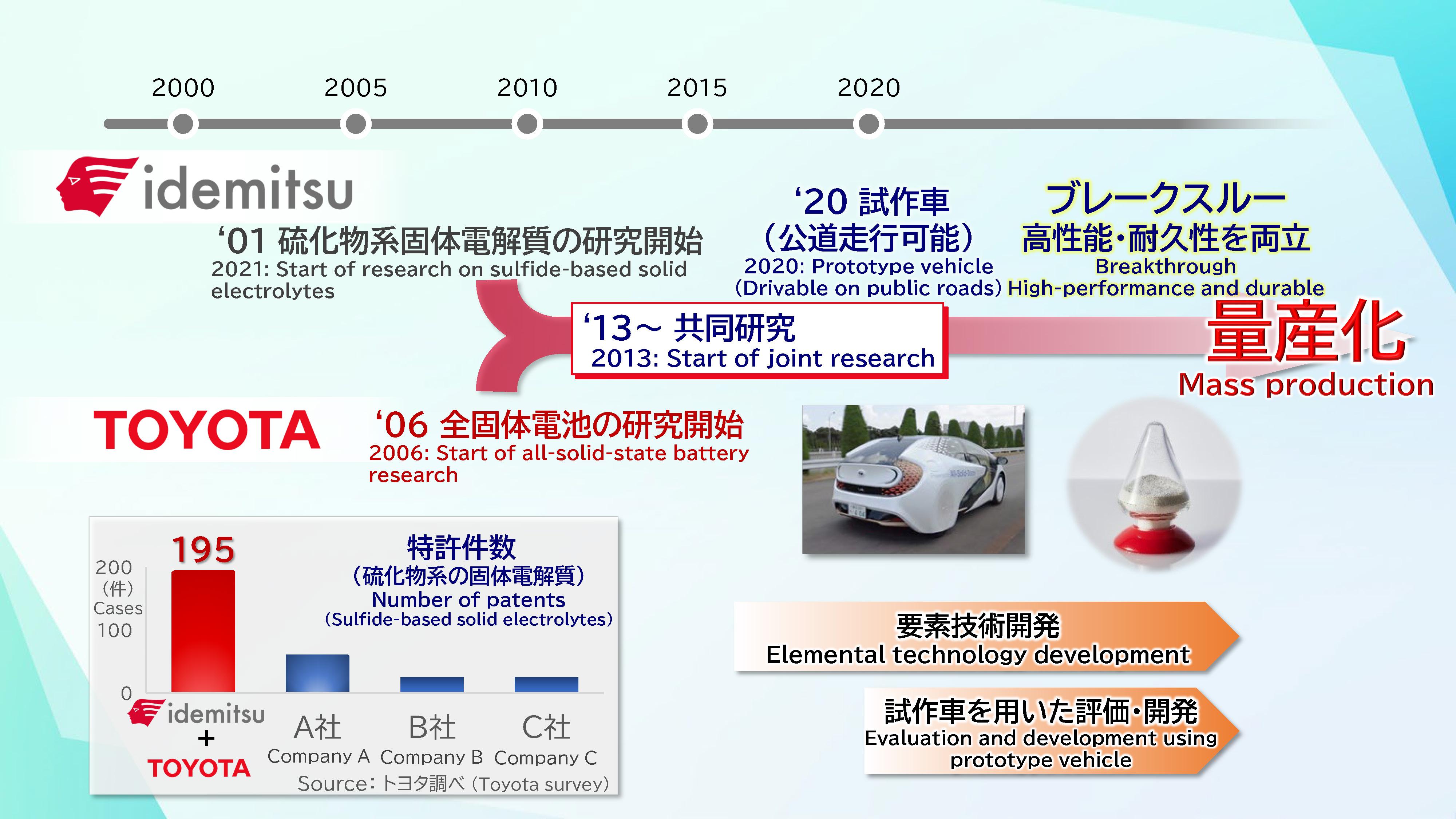
Pairing this new electrolyte with the Toyota Group's cathode/anode materials and battery technologies has put the partnership on a path toward achieving both performance and durability.
Why has Idemitsu, a company better known for its gas stations, been developing battery technologies?
President Shunichi Kito explained.

“During the oil crisis in the 1970s, oil came to be seen as a finite resource that would one day be exhausted. Some said it would run out within 40 years, so we set about developing alternative energies and materials.”
“We conducted research across a rather broad range of fields, seeking ways to add greater value and use oil effectively. The results can be seen in several businesses today.”
This most recent collaboration is focused on sulfide solid electrolytes, which hold the potential for high battery capacity and output.
The sulfur components are byproducts of the petroleum production process. Their usefulness was discovered in the mid-1990s, spurring the research that led to this partnership.
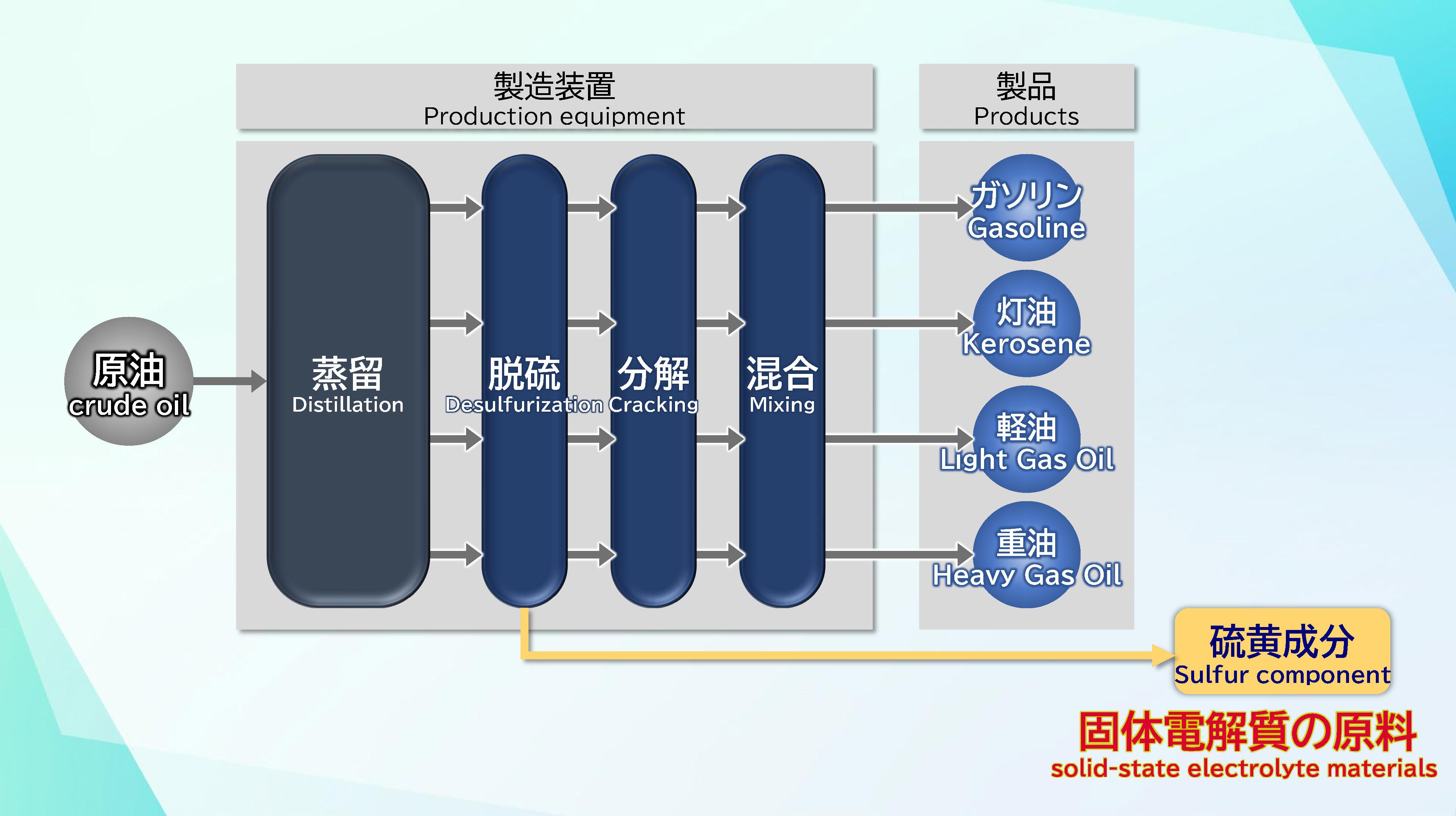
To delve a little further, Toyota holds the patent for the material's components. At the same time, Idemitsu's strength lies in its technological capabilities for producing materials with high water resistance, ion conductivity, and flexibility.
This collaboration enables the companies to integrate their materials development technologies, Idemitsu's materials manufacturing technology, and Toyota's battery mass production technology—in other words, it will bring together all aspects of the process, from materials to finished batteries.
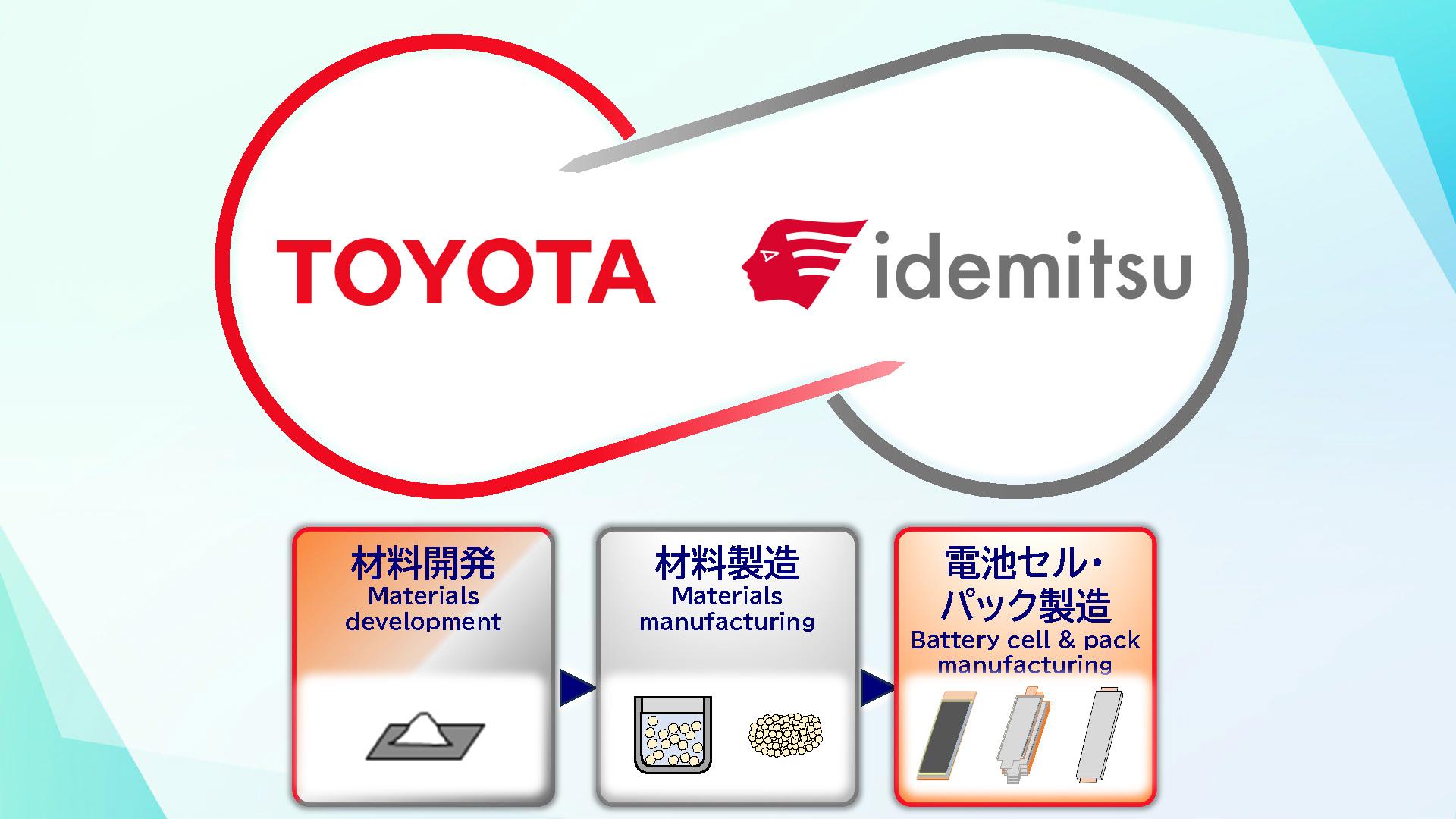
President Sato spoke about the synergies this move will create.
“I believe this framework is crucial for boosting the international competitiveness of Japan’s industry. Rather than seeing other companies as rivals, we need to become more globally competitive. To that end, we are pursuing continued improvement, speeding up collaboration to deliver results as quickly as possible.”
“Integrating the entire process down to materials is partly about increasing speed, but it also enables us to return to the starting point for improvement. Eliminating rework ultimately speeds up development.”