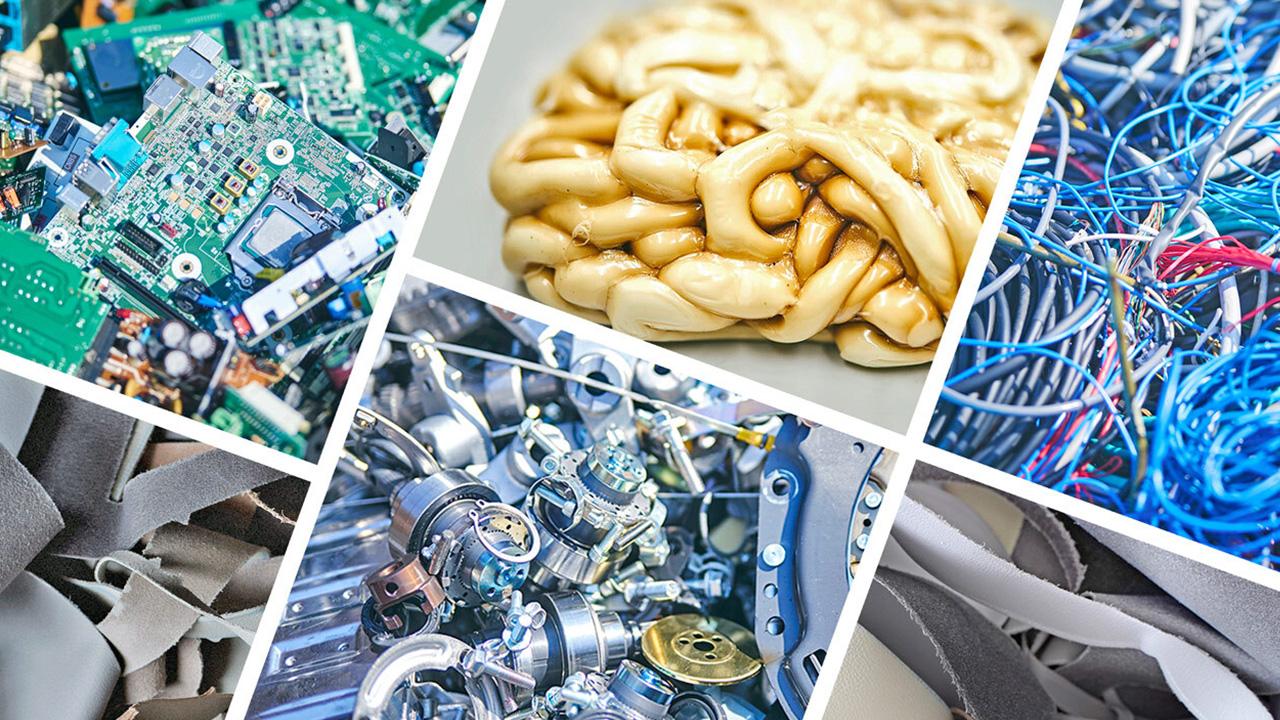
Reduce, reuse, recycle. Under those watchwords, materials that slip through the cracks can still get a new lease on life--even when they look a little odd!
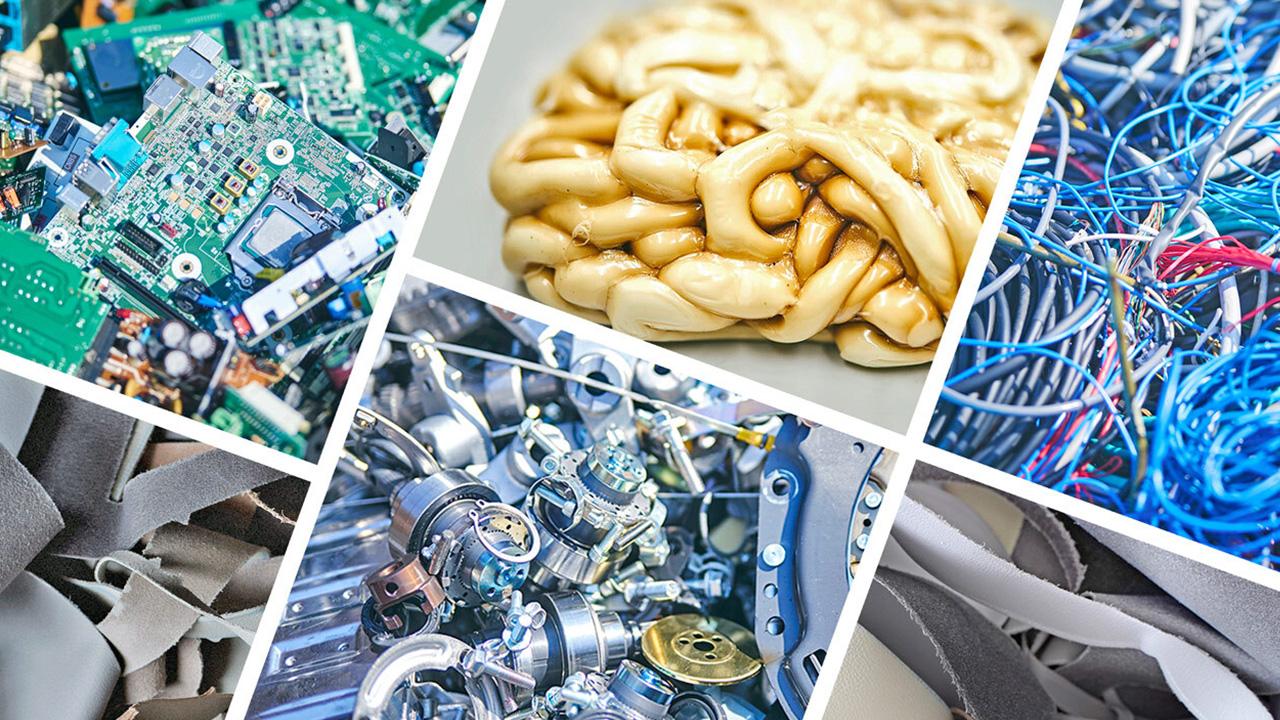
Let’s begin with a question: What do these pencil cases, cardholders, and tags have in common?
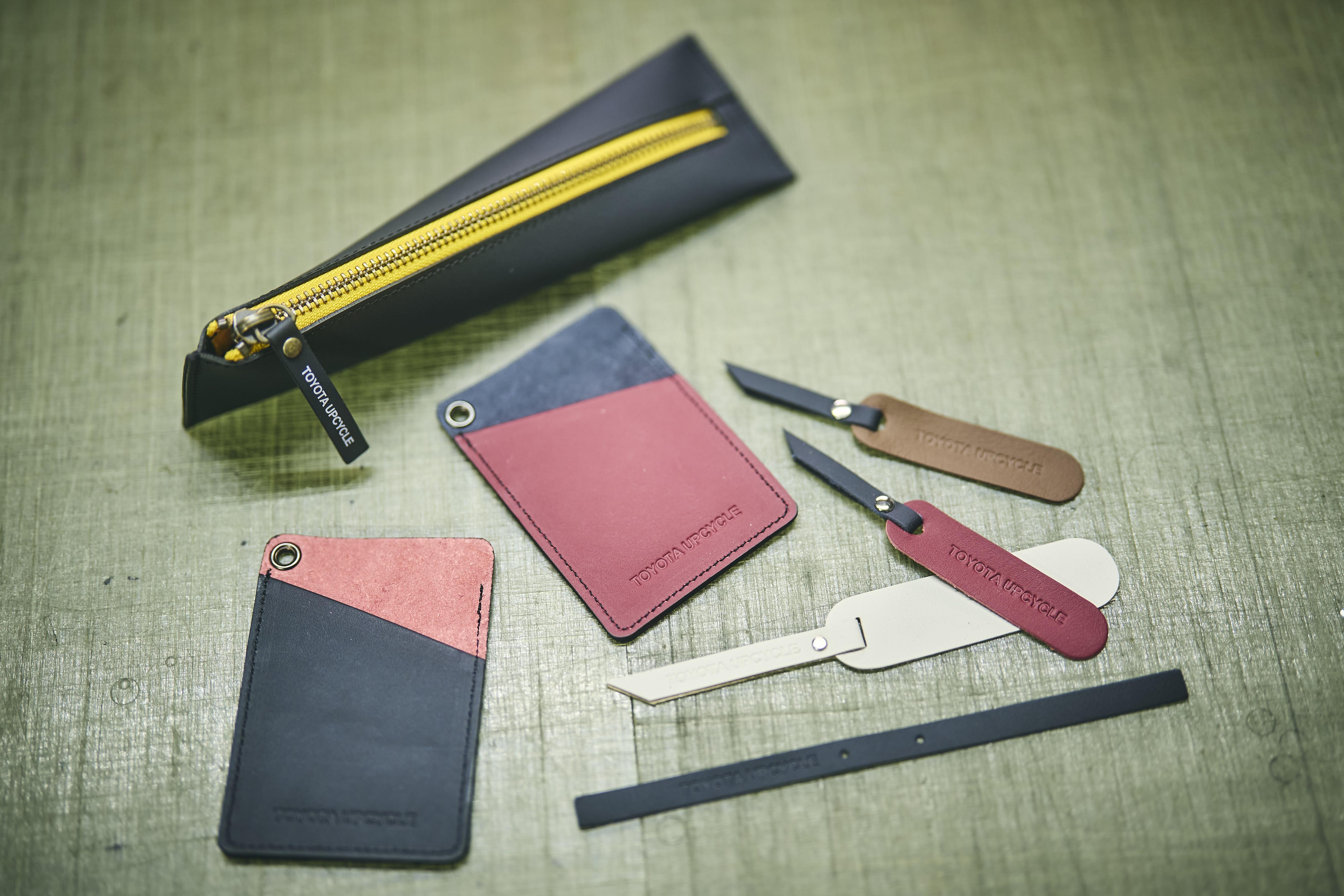
As it happens, they are all upcycled products made from car seat leather that would otherwise have been discarded. These items, which even contain Lexus seat materials, can be purchased online (only available in Japan).
The bags and other accessories below were also upcycled using offcuts of a certain material. Can you guess what part it came from?
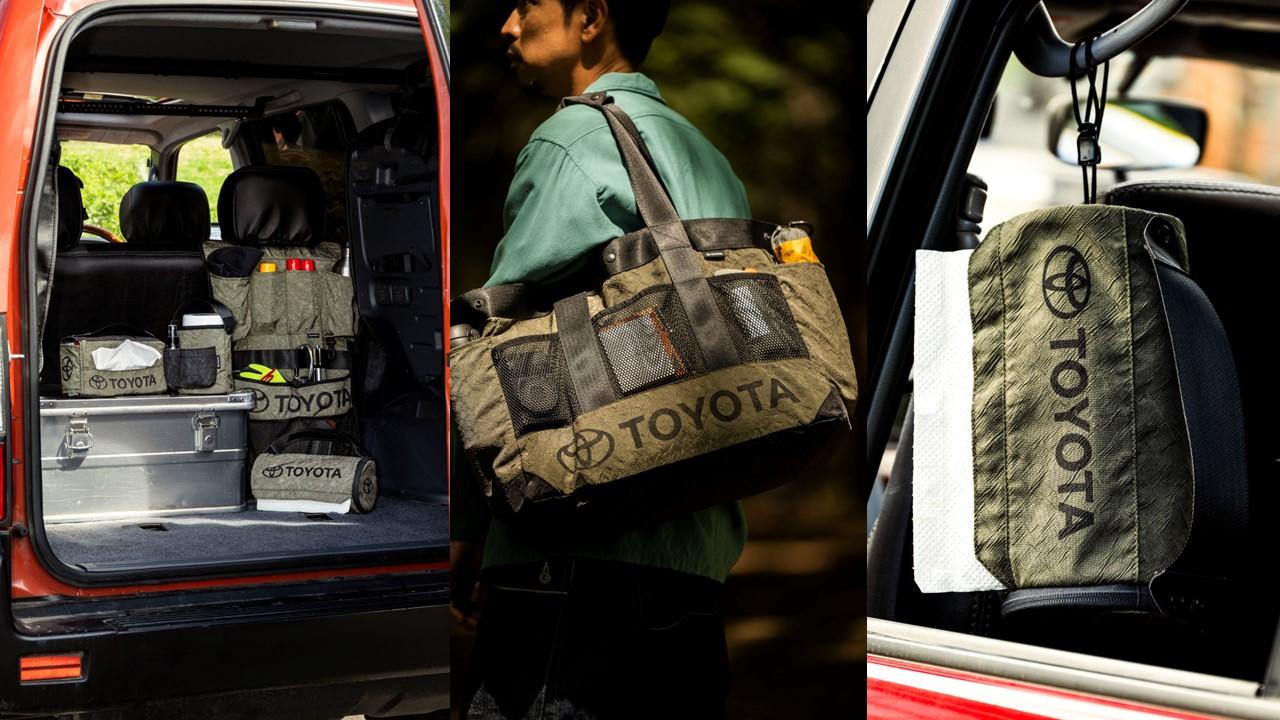
The answer is airbags. Meanwhile, the straps are leftover pieces of seatbelt material. Next, we have a business card case and key fob sporting a carbon fiber weave design.
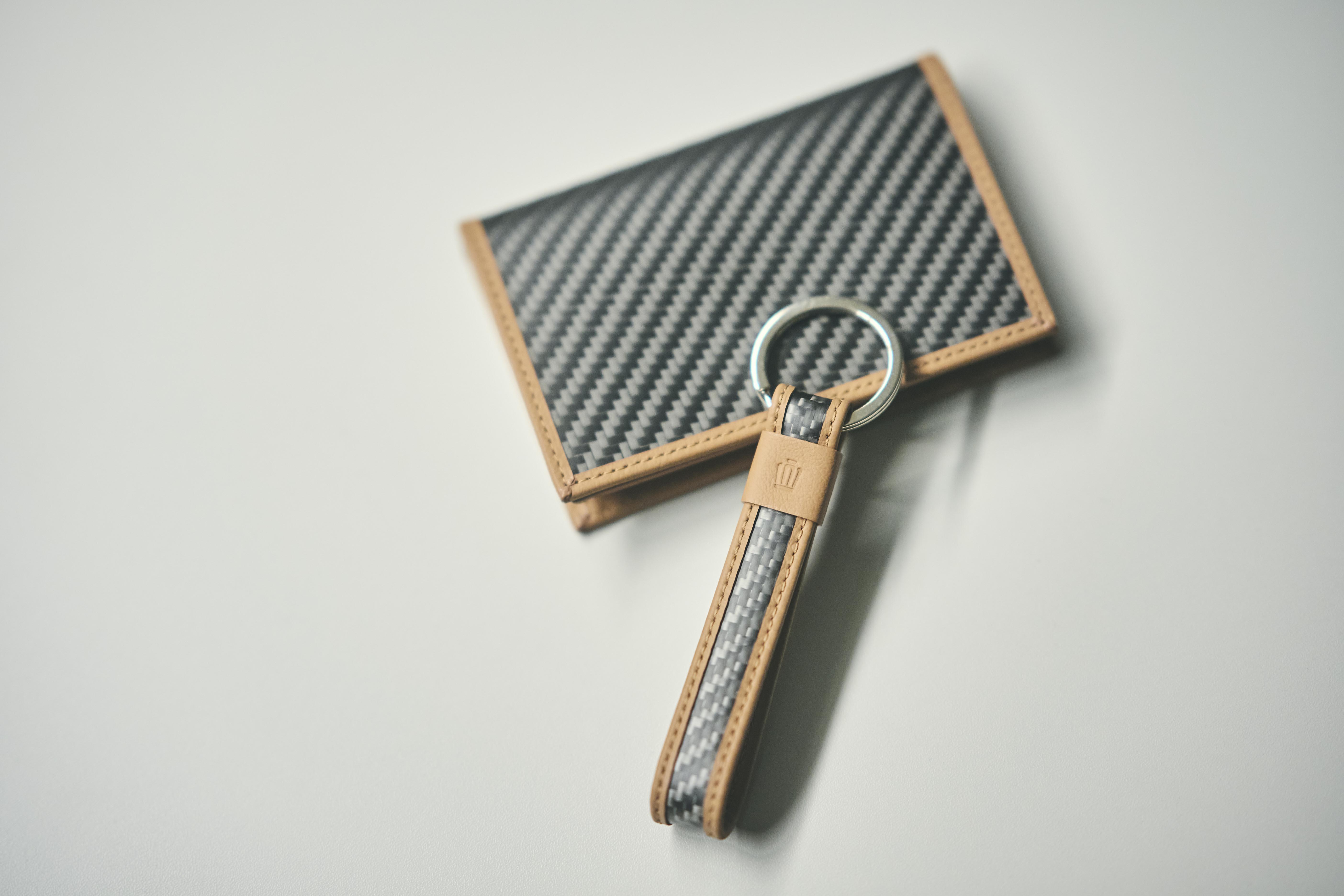
These are made from a recyclable carbon fiber and resin composite, along with offcuts from Crown leather seats. That’s right—real carbon fiber.
A grotesque, brain-like substance
Now then, any idea what this might be?
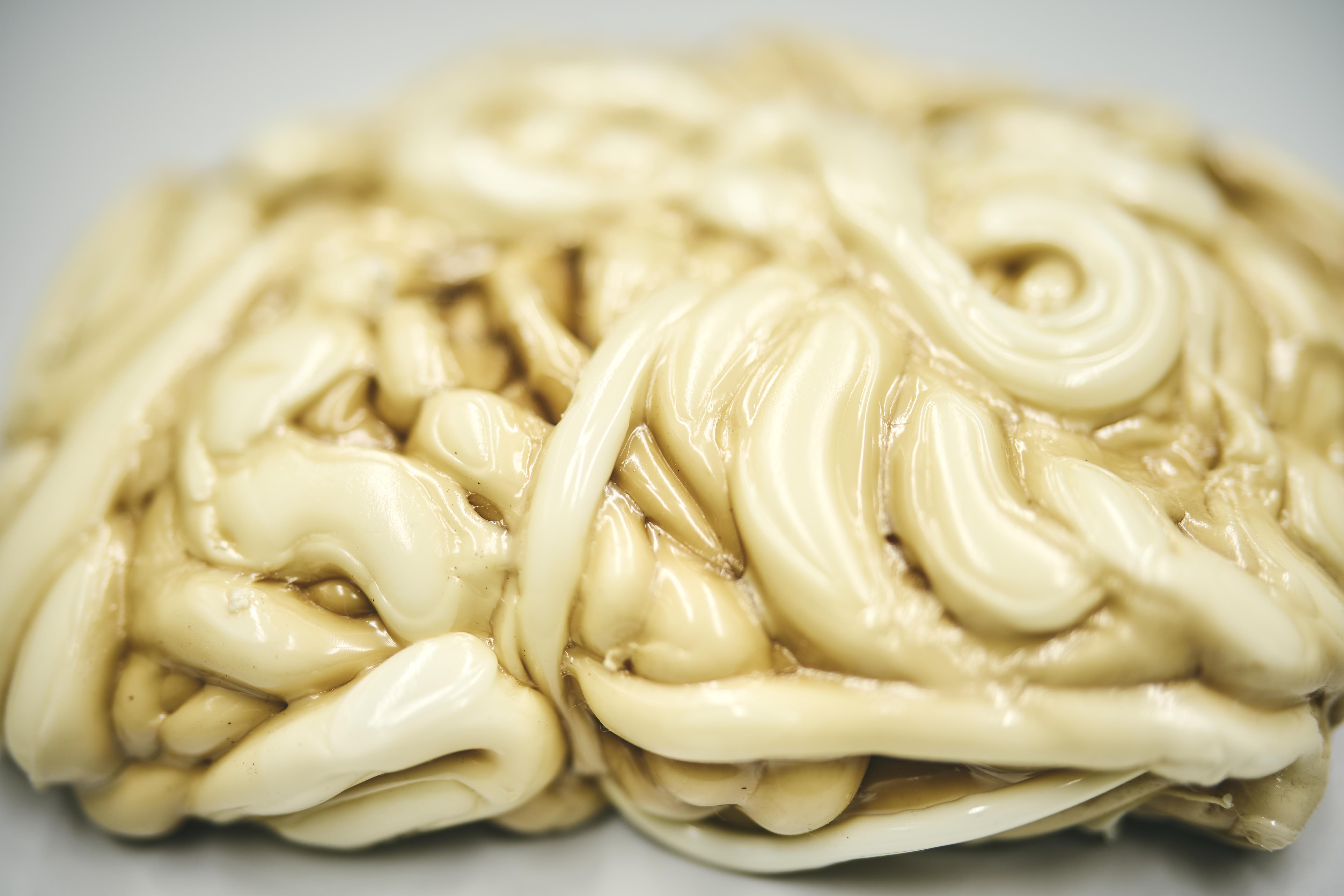
This rather grotesque-looking substance is the purging compound discharged during the injection molding of resin parts for FCEV hydrogen tanks. Not that this will mean much to most people...
Allow us to explain. Resin parts for FCEV hydrogen tanks are made by filling molds with molten resin.
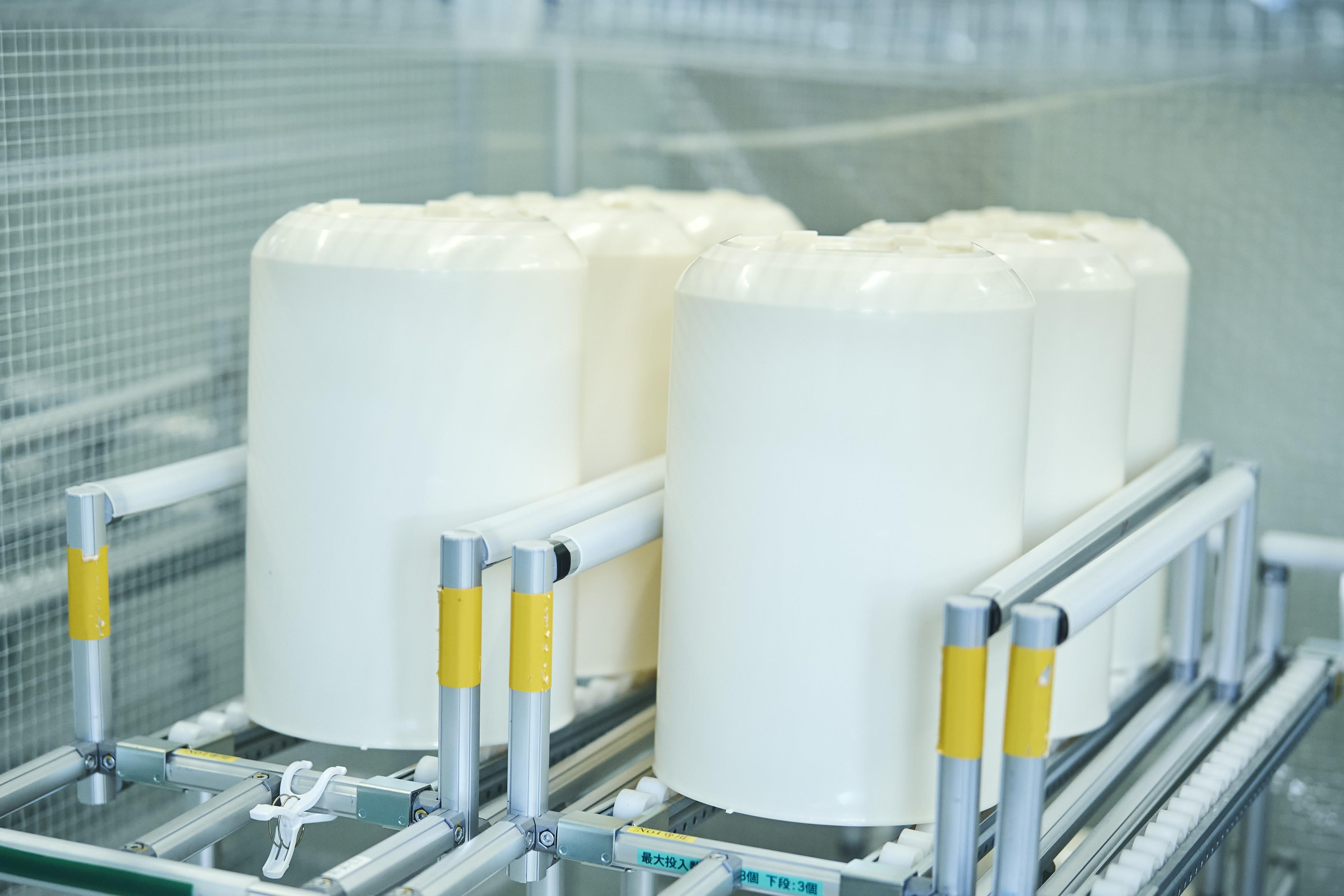
Resin that collects in equipment piping will oxidize and cause defective products, so it must be purged at the start of each day’s operations.
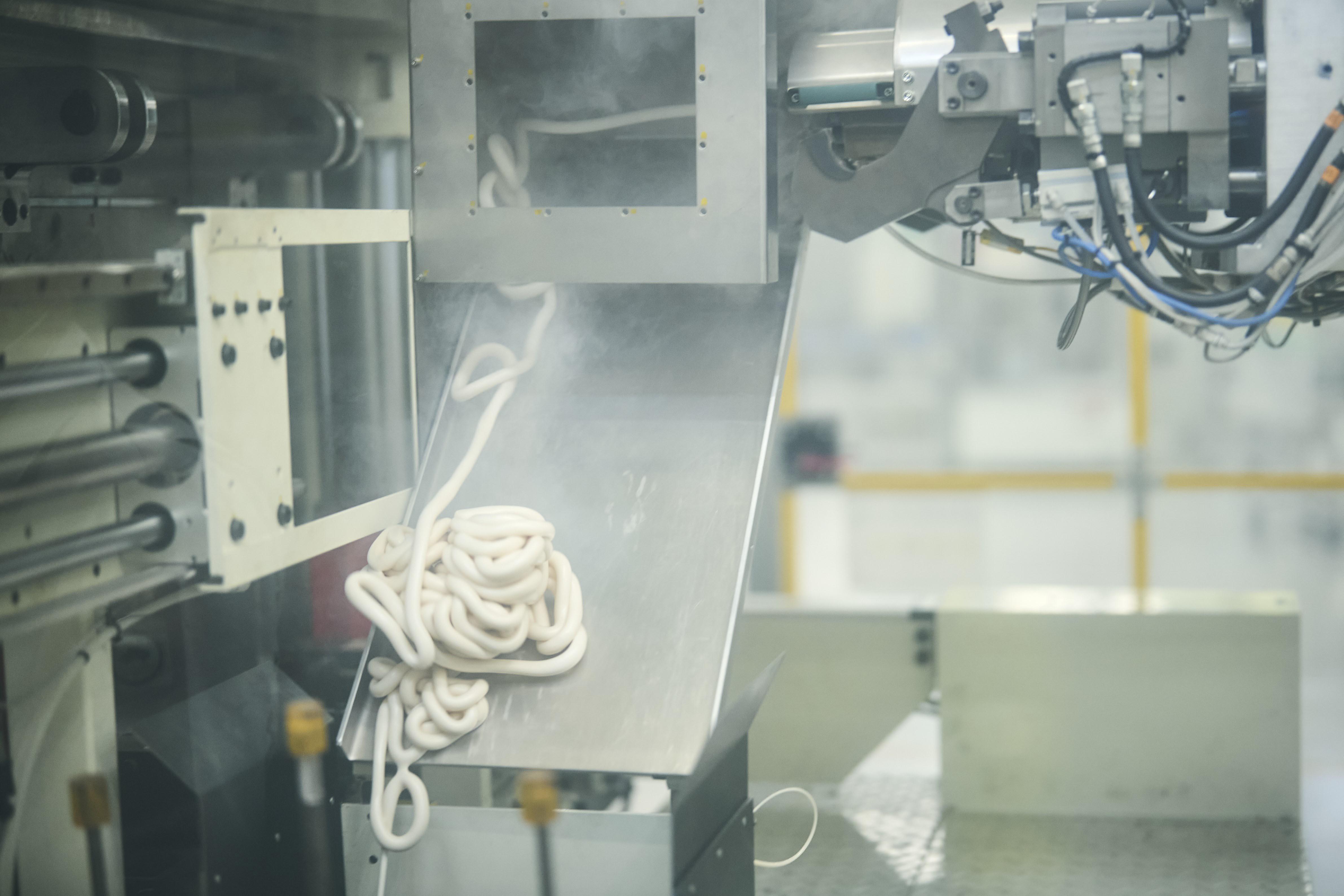
The expelled substance cools and hardens into the brain-like mass we saw earlier. So, how is this creepy-looking material given a second life?
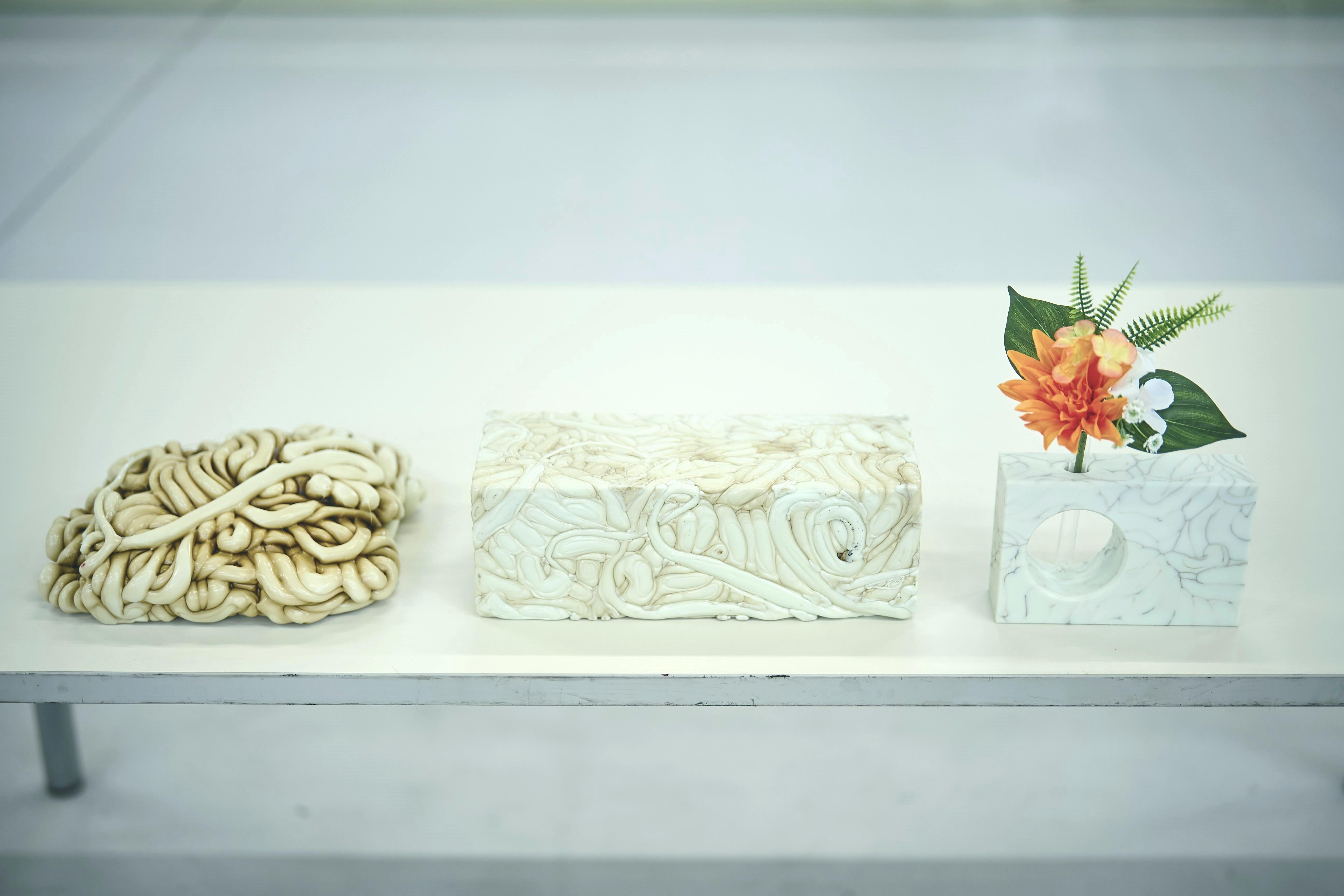
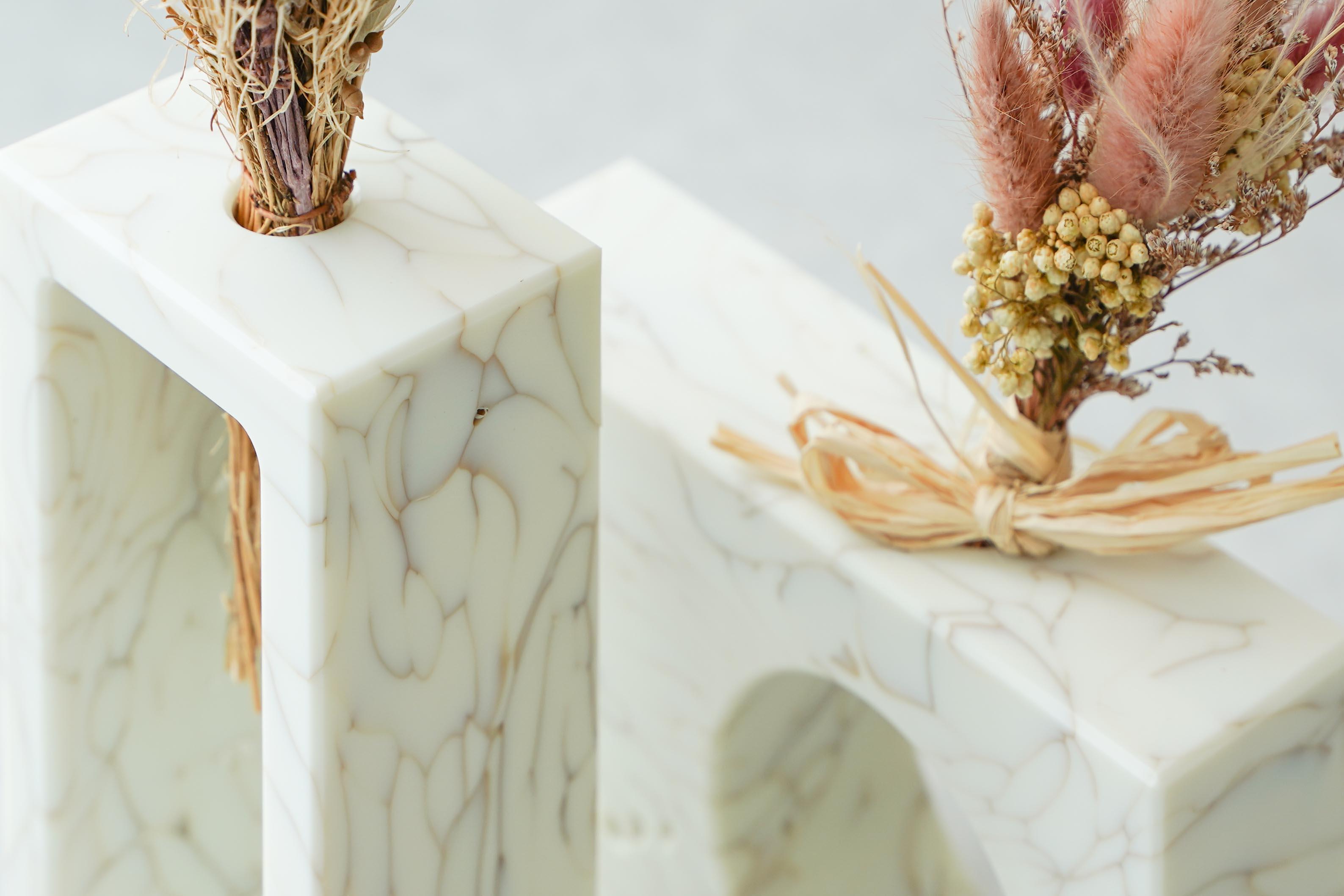
Amazingly, those tangles of resin are transformed into marble-like interior accessories. Toyota is currently exploring the potential of releasing them as products.
Why is Toyota tackling this now?
Many companies are already working to create products from what would otherwise be waste materials. Why is a latecomer like Toyota trying to catch up? We posed this candid question to one of the staff involved.
Noriyuki Nakamura, Project Manager, Business Development Dept., New Business Planning Div.
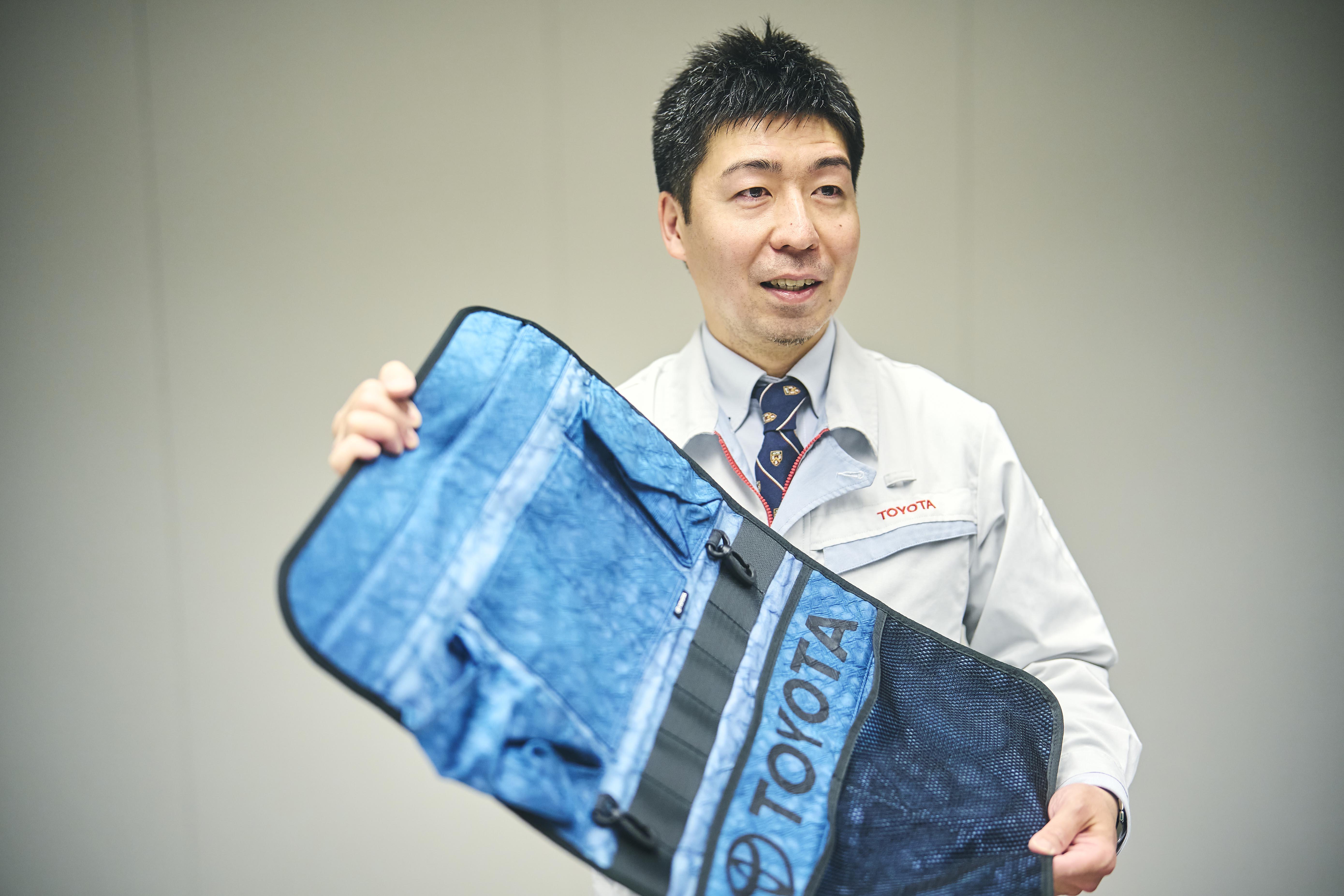
We inevitably have pieces that don’t make it into the car and are discarded—for instance, the cowhide that can’t be used for seats simply because of small scratches or wrinkles or the bits left over when it is cut to shape.
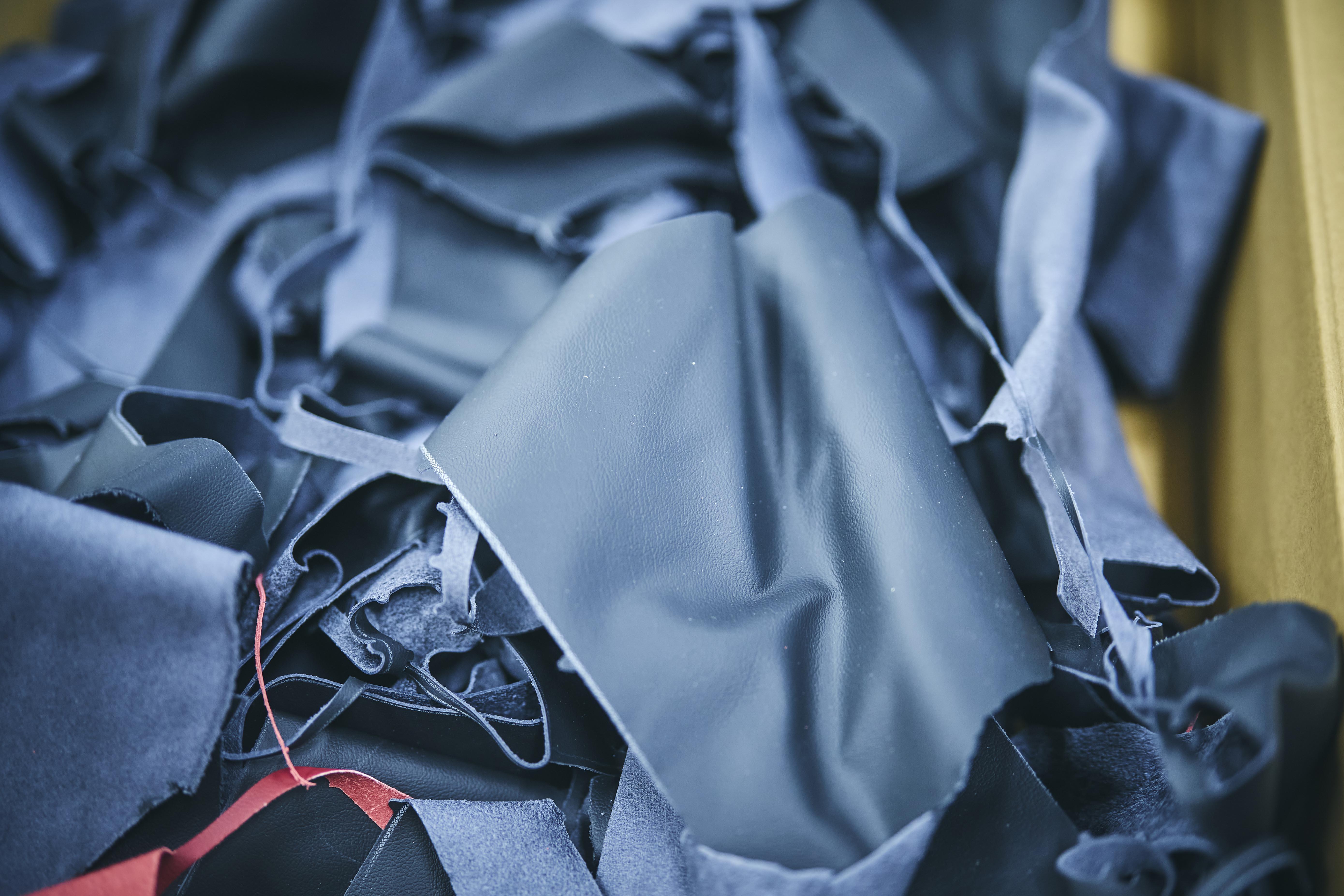
These materials were created to exceed strict carmaking standards, which means they are exceptionally lightweight and durable. To think of them being incinerated, emitting more CO₂... we had to do something! That’s why we launched this project.
A car consists of some 30,000 parts. For the automakers handling this vast array of components, upcycling becomes all the more important.
Waste from the car production process is greatly cut down by recycling raw materials, reducing how much is used and discarded, and reusing whenever possible.
Upcycling is about breathing new life into materials that don’t fit these categories and end up destined for disposal. Basically, it is the final safety net keeping them from the scrap pile.
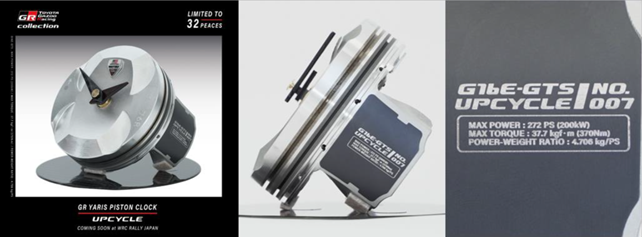
Instead of refusing to follow in the footsteps of other manufacturers, Toyota has seized the chance to reduce waste. We visited the production genba and found that the reasons extend beyond the environmental.