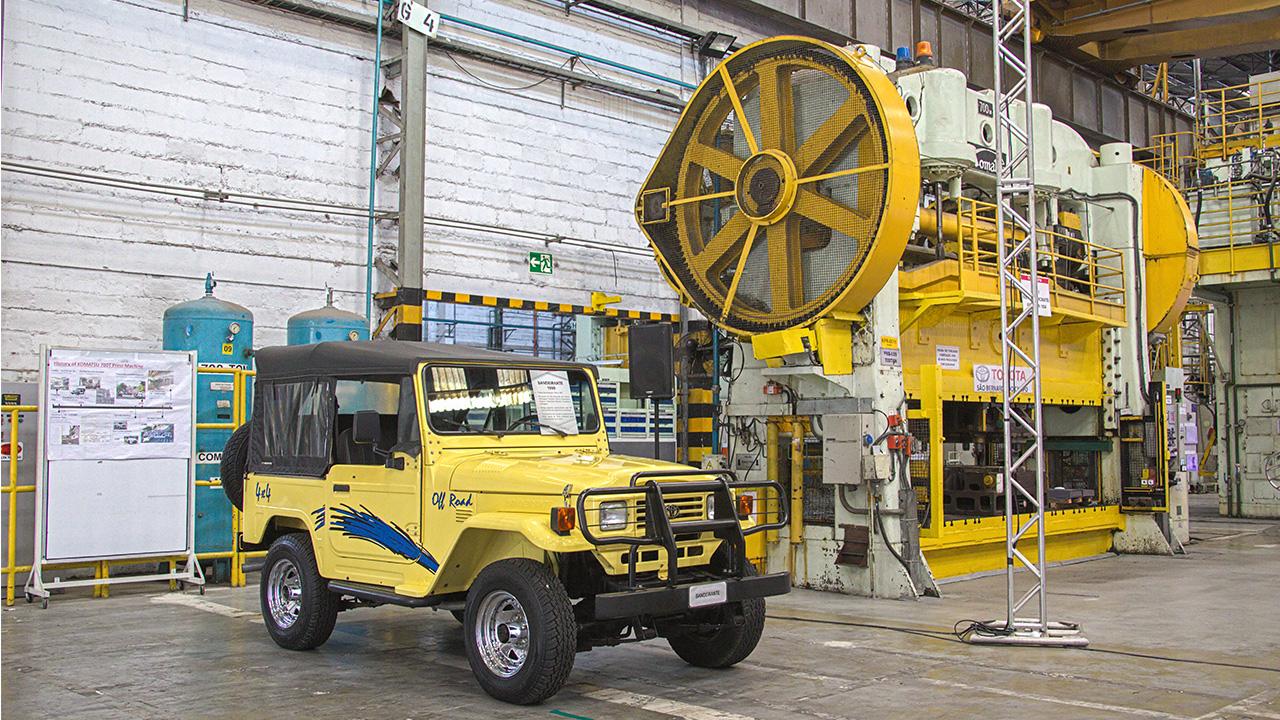
"Have you ever considered why we are manufacturing in South America?" This was the question Akio Toyoda, then-President of Toyota, posed to the Toyota Latin America Chief Executive Officer, who had come to discuss the plant's closure.
The plant linked to Taiichi Ohno, the architect of TPS
Another indispensable aspect of the Sao Bernardo Plant’s history is its connection to Taiichi Ohno, who developed the Toyota Production System (TPS) and served as Vice President of Toyota Motor Co., Ltd. (now Toyota Motor Corporation).
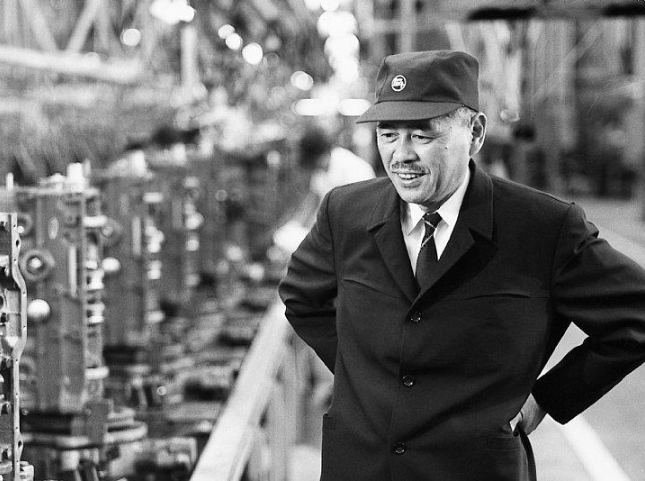
In the 1970s, Brazil’s automotive market experienced rapid growth, surpassing 500,000 vehicles produced in 1971 and reaching 1 million in 1978.
However, Toyota do Brazil’s production hovered below 1,000 units annually, leading to poor performance. Ohno, then an executive, was entrusted with the task of revitalizing the company.
Hisashi Noguchi, who interviewed Ohno multiple times, shares a comment in his book The Man Who Created the Toyota Production System: The Fight of Taiichi Ohno (1988):
“In 1950, Toyota was on the brink of bankruptcy due to labor disputes and financial collapse. To rebuild the company, the goal was set to have 5,000 employees produce 5,000 vehicles per month. Based on that experience, I set the reconstruction target for Toyota do Brazil at 400 employees to produce 400 vehicles per month. However, it was believed that achieving this goal would be manageable only if the Toyota Production System (TPS) was implemented.”
However, as Toyota’s first overseas plant, there was a language barrier between Japanese instructors and local workers.
This is where Japanese immigrants fluent in Japanese and their descendants working at the plant played a crucial role.
Ohno and the team who arrived from Japan trained these employees on TPS principles and techniques, establishing a system where they took the lead.
The implementation of TPS locally far exceeded expectations. A forging line setup change that took an hour in Japanese plants, which involved adjustments to processing machines and jigs (auxiliary tools) according to the products on the line, was reduced to 15 minutes in Brazil. The progress was significant enough that employees from Japan started coming to Brazil to learn.
“At that time, Toyota do Brazil probably had a more advanced production system than Japan. In this regard, Toyota do Brazil was indeed a model case or a test plant for small-scale diversified production, where TPS was most effectively implemented,” Ohno said in the book.
TPS, deeply rooted in Toyota do Brazil, is now expanding outside the company as part of social contribution activities.
“Now, various leading Brazilian companies and hospitals are adopting TPS. There is even a case at a Japanese festival where TPS doubled the productivity of yakisoba (stir-fried noodle) making. It’s more ingrained in Brazil than people realize, and this is also thanks to Mr. Ohno,” explains Inoue.
Employees devoted their lives to this plant
“An important aspect to understand is that it’s not about closing but relocating equipment. We aren’t reducing production volumes; it’s about consolidating and restructuring plants for future development,” emphasizes Inoue.
With the restructuring, Sao Bernardo Plant employees were offered reassignments to other plants within the state.
However, these plants are about 150km away, and for some employees with family commitments, relocation isn’t feasible, necessitating their departure from Toyota.
The company has committed to thoroughly communicating with each individual about their transition, including career assistance, to ensure a stable post-retirement life.
Marcelo Perin, a welding supervisor who contributed to the equipment transfer until the end, said, “Initially, it was shocking, but with the company’s support, everyone understood and felt reassured in their work.”
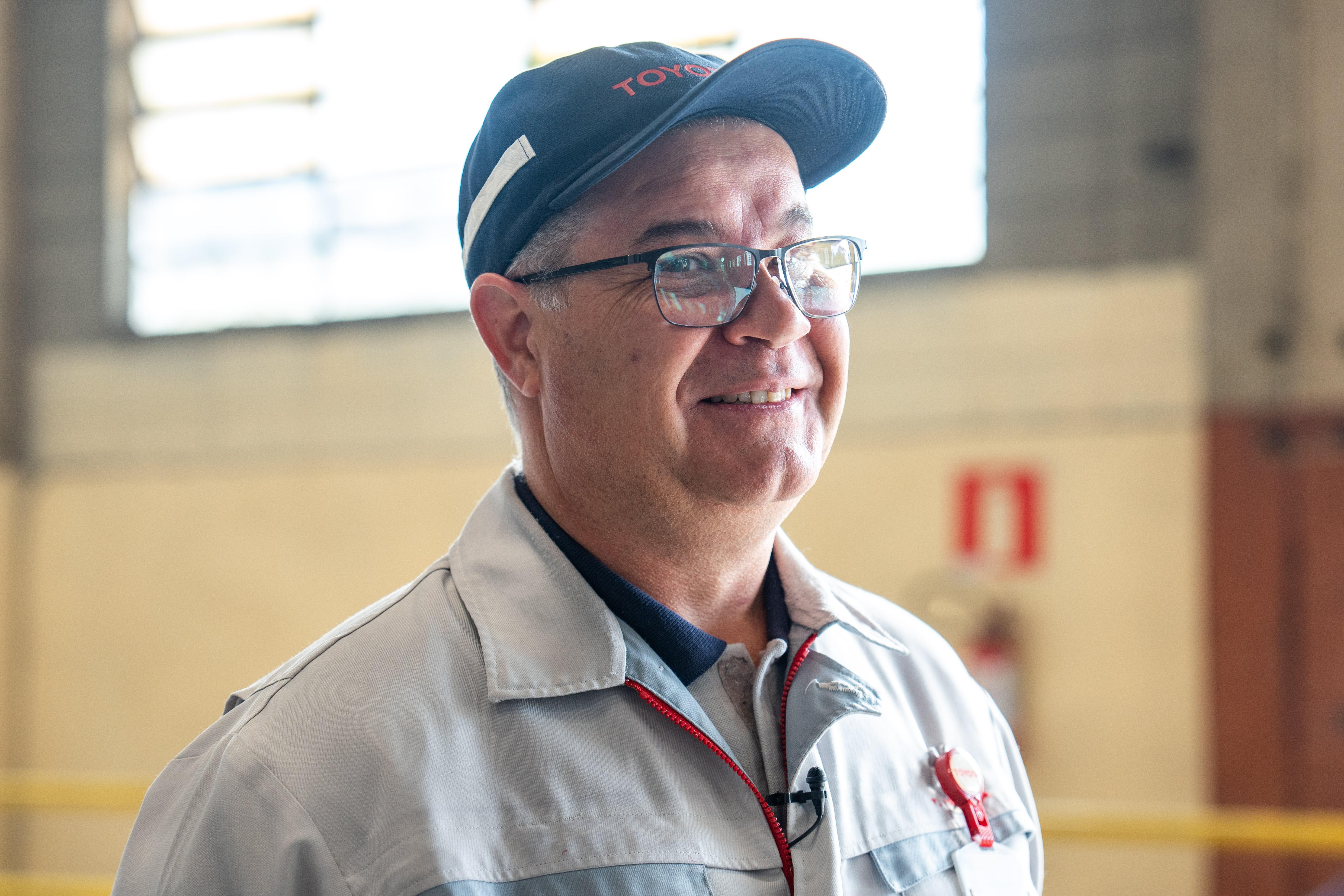
In the plant, even minor lapses in attention can lead to significant accidents.
He sees his role as resolving various concerns of employees and ensuring they can work with peace of mind, focusing on clear communication and training for those involved in new processes.
He plans to retire and start a new business venture. “I’m ready for a new challenge in a different field, but I’ll always be available to support Toyota if needed,” he says with a smile.
Cristiano de Lima Santos, a machining group leader, will transfer to the Porto Feliz Plant, which produces engines.
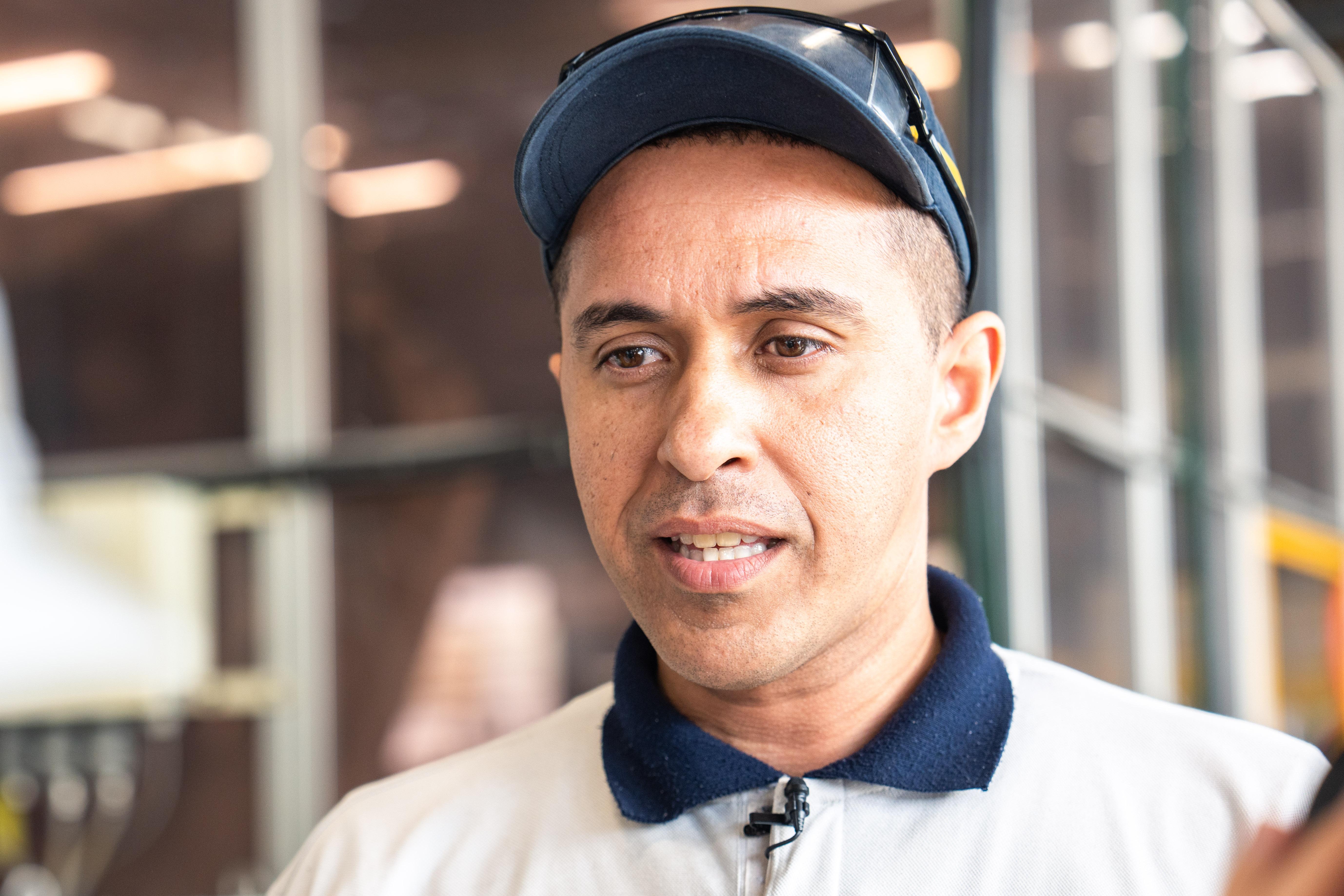
“The news of the plant’s closure was shocking, as I’ve been here for 18 years. My wife and two young daughters were initially surprised, too.”
What alleviated their anxiety was the welcoming messages from staff at the new plant, like “Welcome, everyone from Sao Bernardo!” which appeared on the internal network when the transfer was decided.
“Everyone I talked to described the area as comfortable to live in, and as I researched more, I became optimistic. I’m not worried. I believe the schools there will offer a better environment for my children.”
In the new plant, he will be responsible for tasks different from his current ones.
“I’m excited about this new learning opportunity. I hope to spend the rest of my career here and retire from this company.”
It’s not just current employees who hold special feelings for the closing plant. Yoshiharu Haraguchi, who joined in 1962 when the plant started and worked until his retirement in 1995, reflects on his time there.
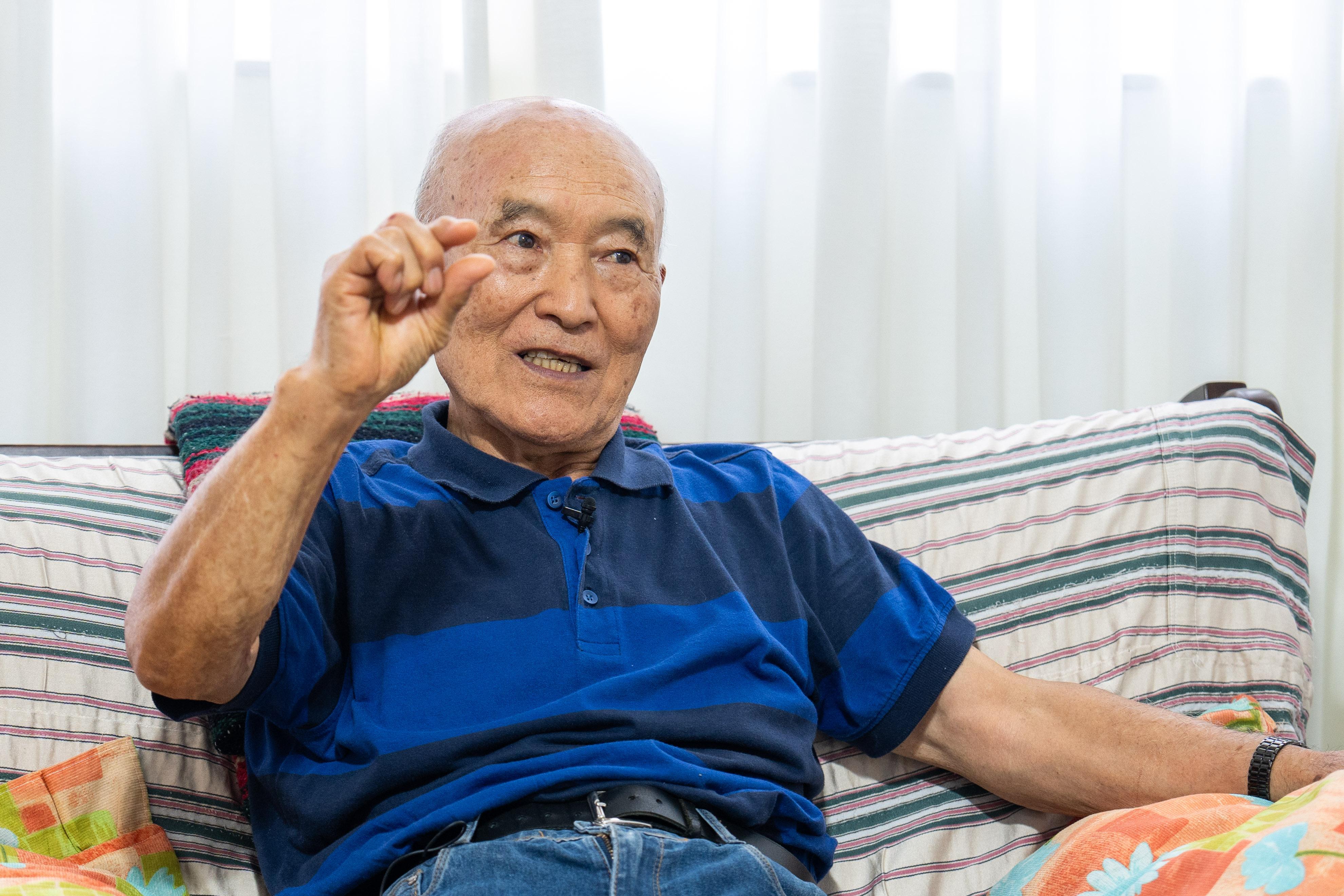
“When I set out to drive to the bank in Sao Bernardo, I naturally find myself heading towards the plant,” Yoshiharu Haraguchi reflects on the significance of the place in his life.
Haraguchi, who supported Toyota do Brazil since its challenging early days, shares the following:
“Back then, we believed in earning our wages ourselves. When times were tough, we even manufactured in-house the parts that were outsourced. We learned to do everything possible. That’s how we protected our jobs.”
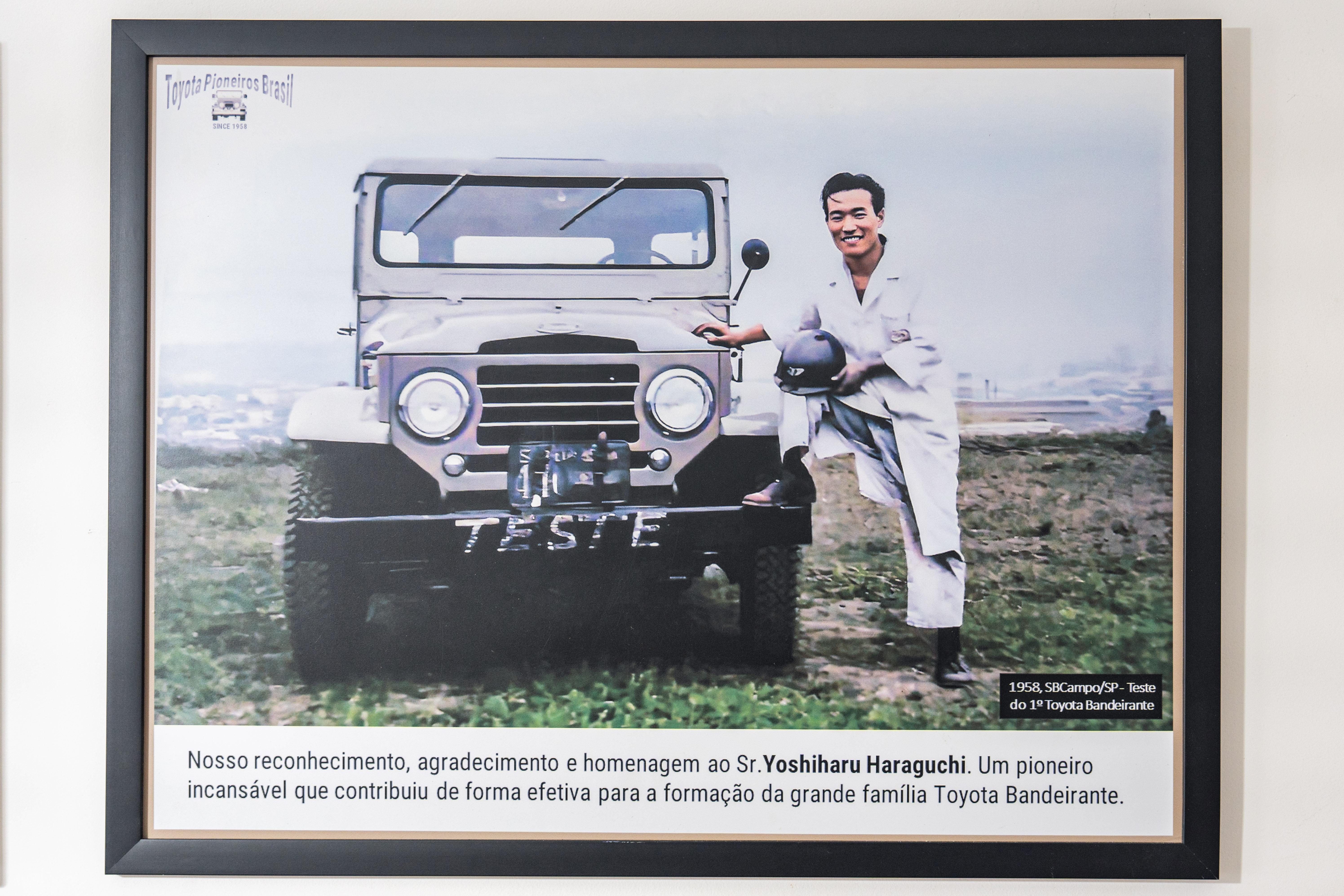
“I believe I am who I am today thanks to the Sao Bernardo Plant. So, even after retiring, when someone asked, ‘Haraguchi, can you help us?’ I always said, ‘yes.’ I kept coming to help for 15 years.”
Those who supported the plant during its start-up phase, those who contributed until the last moment, and those inheriting the legacy each hold a special connection to the plant, to which they dedicated much of their lives.