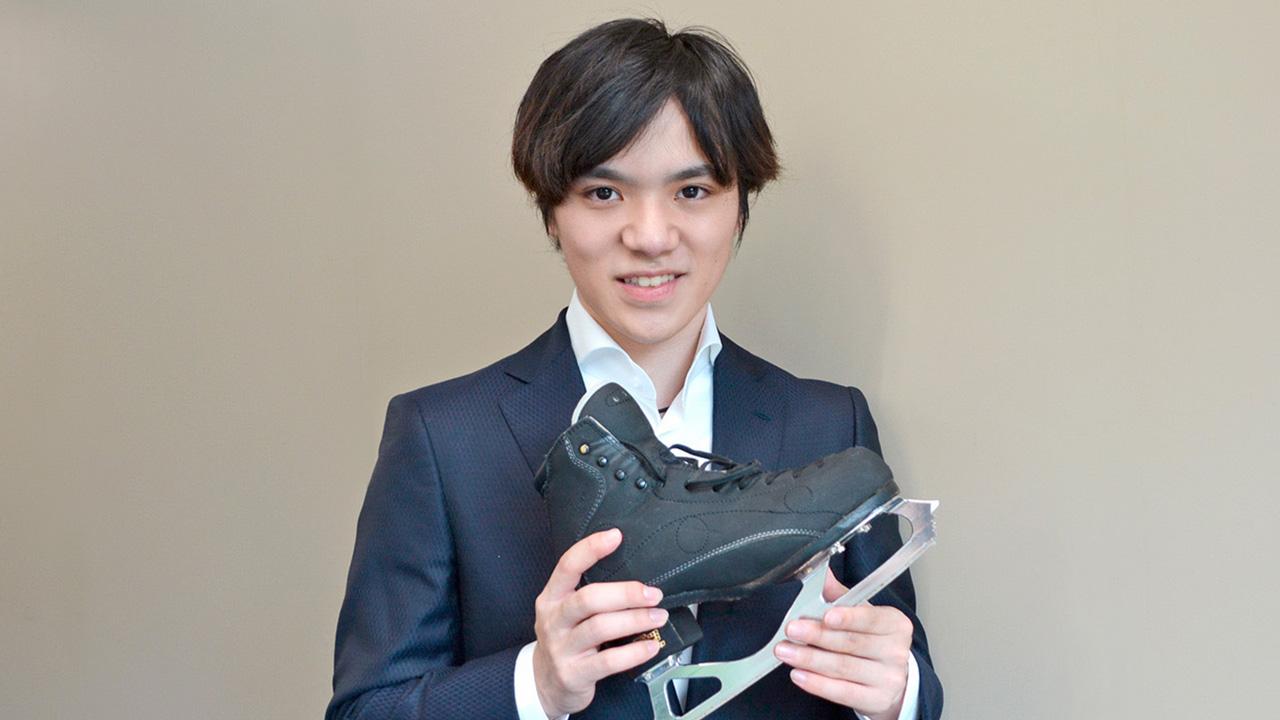
Figure skater Shoma Uno has a special relationship with a certain Nagoya-based manufacturer.
Impressions of Toyota staff
Do Toyota employees really work hand in hand with suppliers? We tentatively posed the question to CEO Teranishi…
CEO Teranishi

We first met for a lecture on using the software. I was impressed by how courteous and attentive they were with our staff.
Since we were taking on a new area of manufacturing, there were countless obstacles, and we tackled them together. Today our partnership has gone beyond metals to include more plastics work as well.
At the same time, the technical level they’re aiming for is extremely high. For instance, I remember we were asked to prototype fuel cell molds to very exacting specs.
This being a Toyota Times interview, the CEO was no doubt choosing his words carefully. And yet Yuta Kobayashi, who served as a contact person for the project, also told us that his initial doubts proved to be off the mark.
Yuta Kobayashi, Manager, Yamaichi Special Steel

To be honest, I imagined the people at Toyota would be hard to deal with. (laughs)
But everyone was really friendly and open, working with us to find solutions for technical challenges. They made the effort to visit our facilities and get their hands dirty alongside us, which helped a lot.
Toyota founder Kiichiro Toyoda laid out a “Co-existence and Co-prosperity” procurement policy for working with suppliers, which includes the following line:
“Our suppliers are like branch plants for which we must strive to improve performance.”
Rather than pursuing the lowest prices, Toyota offers up its expertise and works with suppliers to raise their productivity. This is the spirit that guides Toyota’s procurement.

We can’t make cars on our own
In that case, how do Toyota’s engineers feel about joining forces with suppliers to make cars? We asked three Toyota Engineering Society members who accompanied us for this report.
Hirofumi Fujita, Project Manager, Toyota Engineering Society

In all honesty, we simply can’t build cars by ourselves. The company also encourages us to go out and learn. I believe carmaking is only possible if we have suppliers with advanced technical capabilities.
Toyoyuki Sato, Group Manager, Toyota Engineering Society

We develop products in tandem with materials manufacturers. Ultimately, they produce the materials that become parts, which we use to make cars. In other words, they are indispensable partners in carmaking.
Tomoyuki Tsuji, Assistant Manager, Toyota Engineering Society

It is incredibly powerful when many people move together in the same direction. Time and again in my daily work, I’m helped out by suppliers, and I often feel that they are the company’s real strength.
All three surprisingly emphasized that carmaking is a team effort. As it happens, teamwork is also a core part of the Toyota Engineering Society (TES) to which the trio belongs.
Fujita explained that the volunteer organization was set up in 1947 with a view to “creating the future through the power of people and technology.” The society’s activities aim to improve members’ technical skills and contribute to local communities.
TES is organized by a committee of more than 100, including full-time staff, and has more than 20,000 members.
Fujita
Members come from all corners of the company, sparking connections—and friendly rivalries—between people who wouldn’t otherwise meet in the course of regular work.
All three members agree that one of TES’s main roles is creating horizontal ties across department lines.
Peers, not hierarchies
Every August, the Toyota Engineering Society holds “Engineers Day,” a technology exhibition for fellow employees.

The two-day event draws some 20,000 visitors each time, and this year Yamaichi Special Steel is among the scheduled outside exhibitors. Their display will feature invaluable footage of Uno in conversation with the Yamaichi team.
CEO Teranishi

With the Japanese economy facing a downturn, the importance of small and medium-sized companies will only grow.
Thanks to the challenges we have taken in 3D printing and blade manufacturing, we can contribute new value to the world. Doing so helps our company to survive and our employees to be happy.
If someone asks whether Yamaichi is needed in the world, I want to be able to say “Yes.” That’s the kind of company I’ve tried to create, so I was thrilled that we were invited.
Toyota’s monozukuri is sustained by 5.5 million peers working in Japan’s auto industry. At the end of our interview, Uno also touched on the importance of such partners.
Uno
Figure skating is the same—you cannot succeed without others. Even when you feel all alone, there are many people around you.
People nowadays tend to focus on what’s in the spotlight, but I am grateful for all the people who support me behind the scenes.
Toyota’s relationship with its suppliers is a bond between equals. The company’s manufacturing continues to be driven by diverse partnerships.