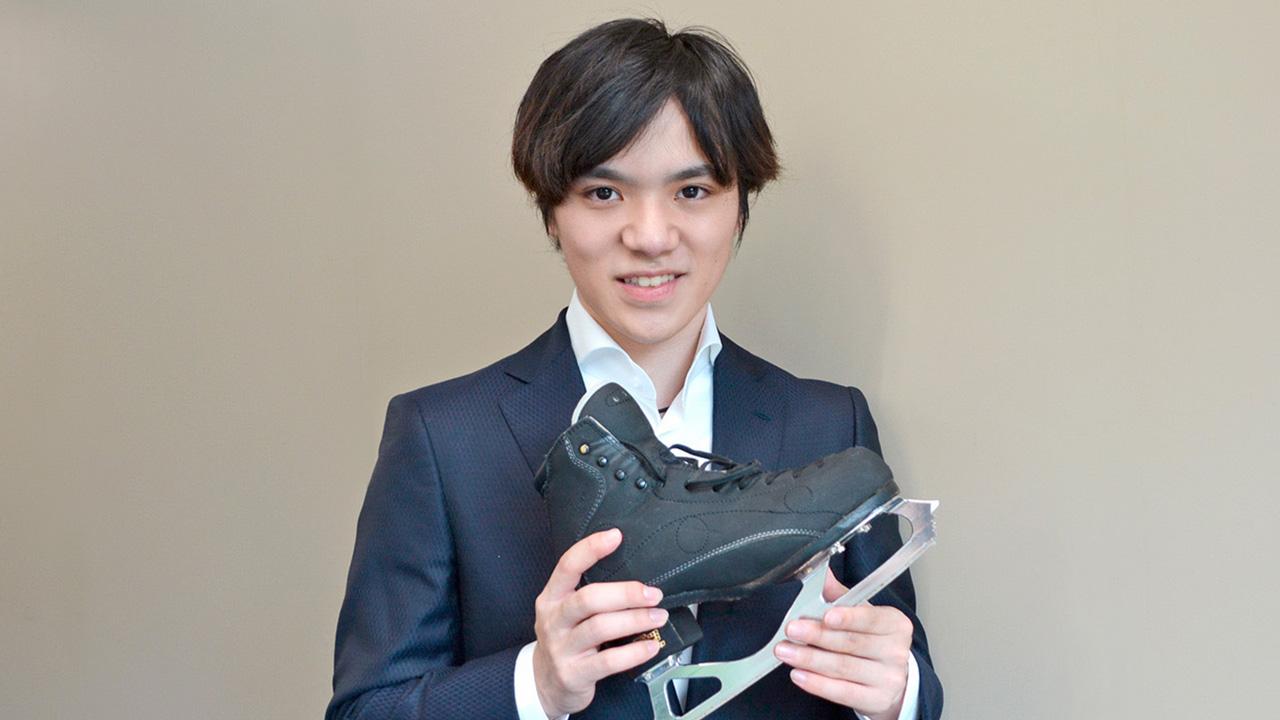
Figure skater Shoma Uno has a special relationship with a certain Nagoya-based manufacturer.
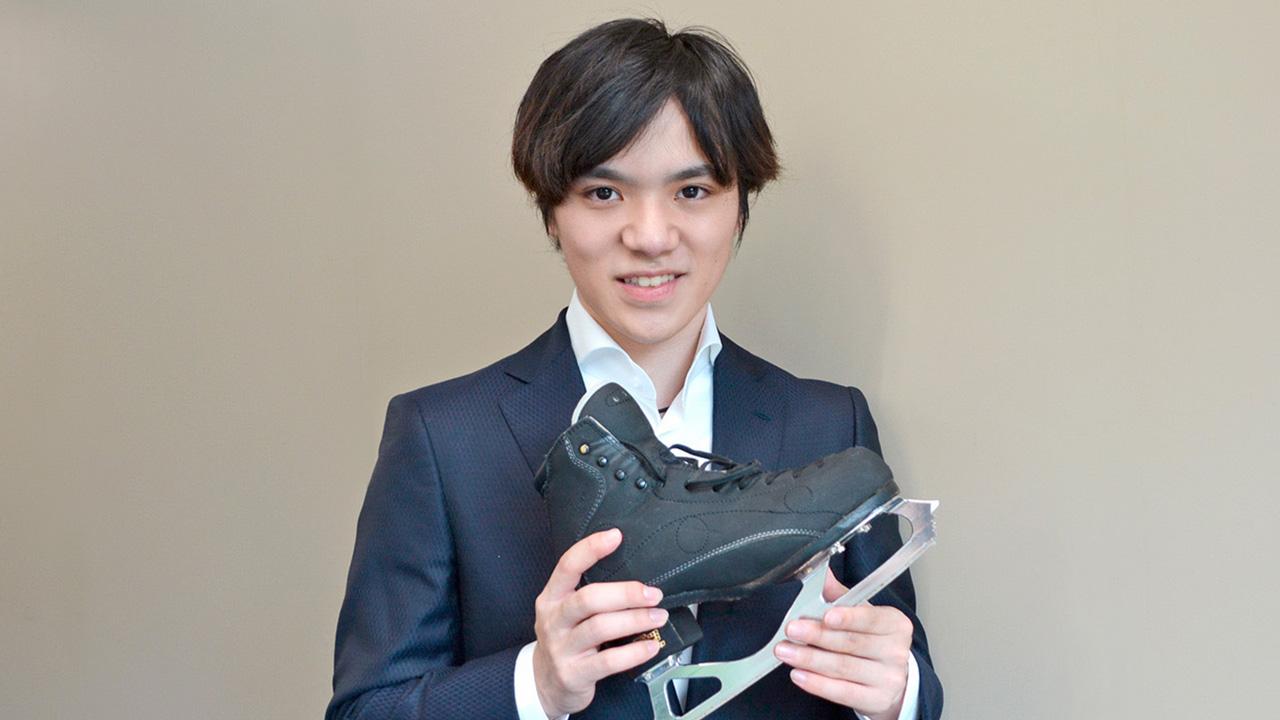
Shoma Uno is a globally renowned figure skater. He is the country’s first male competitor to win back-to-back World Championships, in 2022 and 2023, making him one of Japan’s top athletes.
As it happens, Uno also has a special relationship with one of Toyota’s carmaking partners.
The company helping Uno put his best foot forward
In the fall of 2020, Uno switched from using Western-made skate blades to Japanese ones. He was astonished at the difference.
Uno
The new blades offered high quality and durability, with the reassuring consistency of always feeling the same.
Figure skating requires a lot of finesse, so equipment issues can keep many competitors from performing at their peak. Having gear you can trust is crucial, and I believe these blades have gotten me to where I am today.
The blades that Uno praises so highly are the work of Yamaichi Special Steel, a Nagoya-based manufacturer that also assists Toyota with advanced carmaking technologies.
Yamaichi can precisely machine metals down to thousandths of a millimeter. CEO Motoharu Teranishi explained the secret behind the company’s blades.
CEO Teranishi
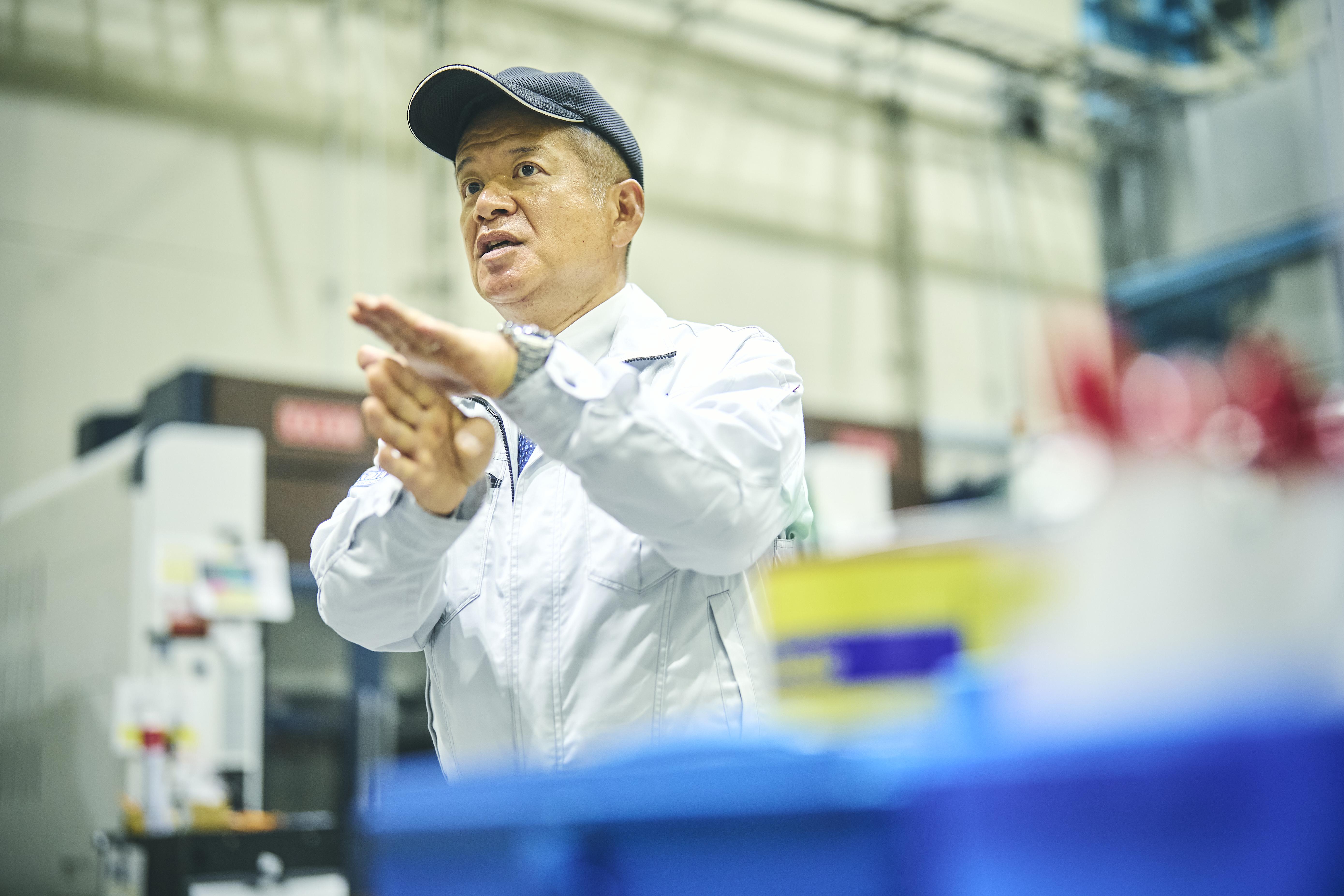
Ours are the only blades in the world to be machined from a single piece.
Typical blades are welded together in a three-piece structure, but since the welds lack strength, they may bend or break under the load of jumps.
With quad jumps now the norm, the impact of landing can also cause blades to bend or break. In the past, Uno would replace his every few weeks.
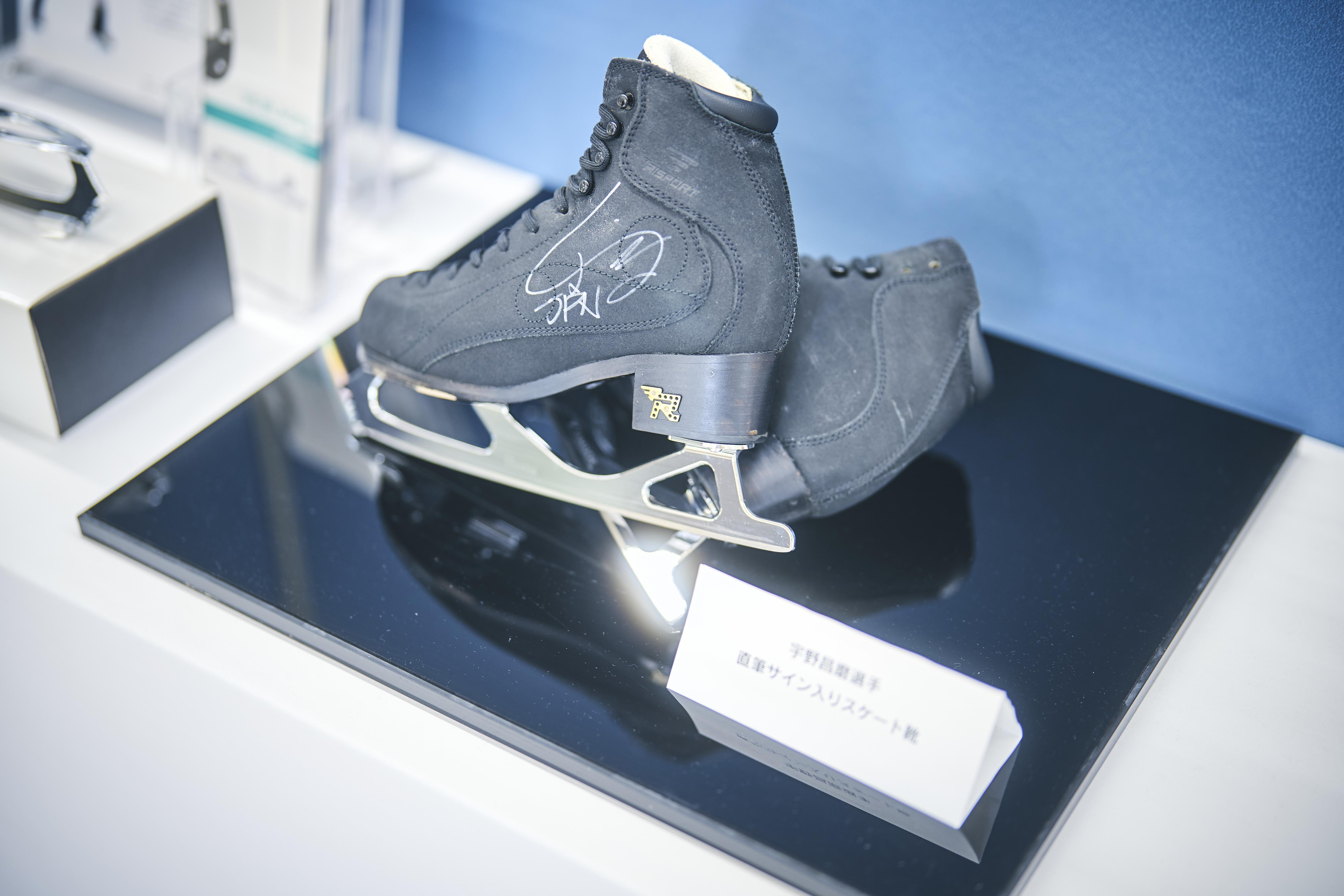
If this blade breaks, it might be time to hang up the skates...
Yamaichi’s one-piece blades are made by machining a 10-kilogram block of special steel down to around 280 grams.
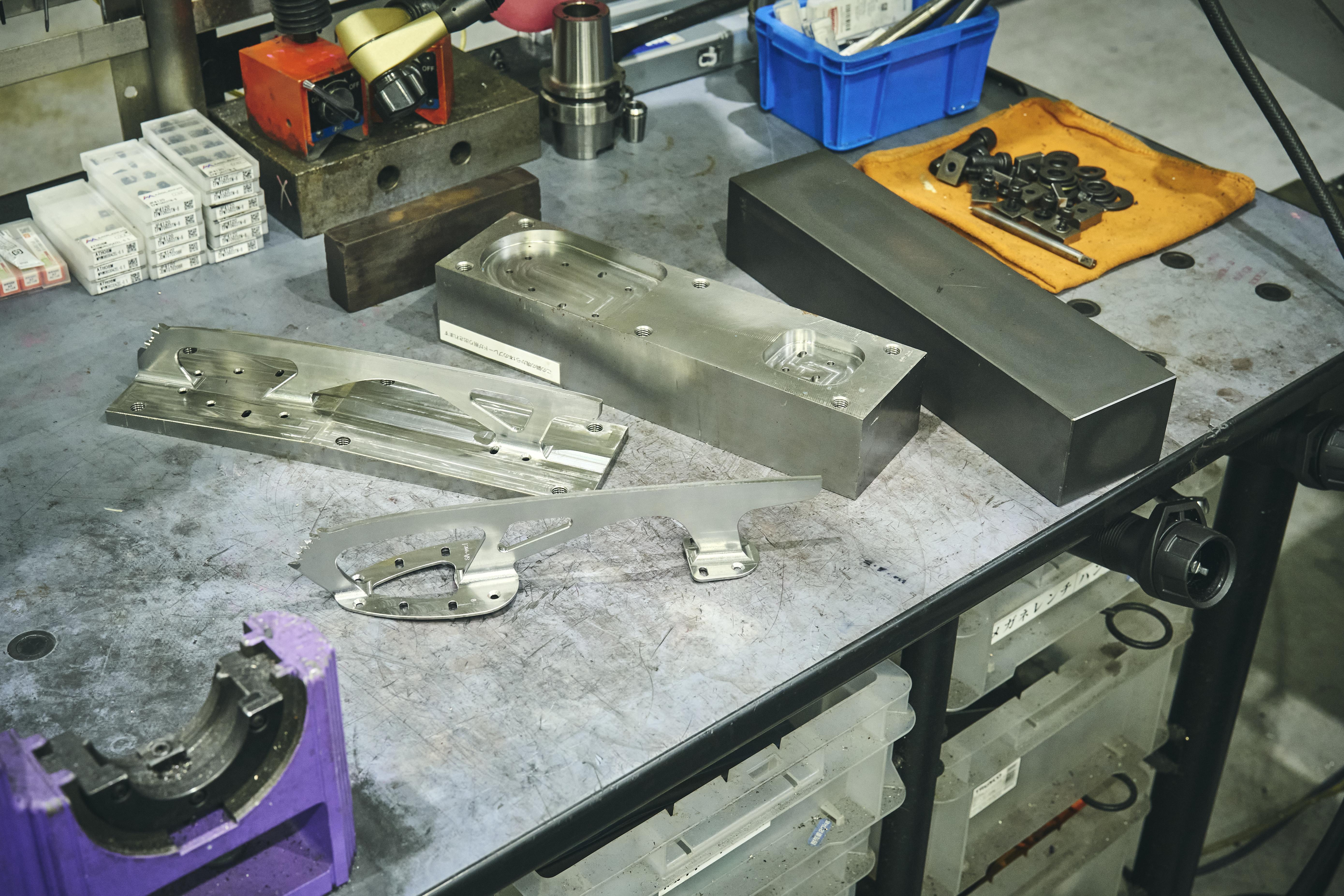
The process takes roughly half a day on the cutting machines, but in the beginning, it was all trial and error.
CEO Teranishi
Working with various special steels is what we do, so we have a wealth of expertise in this area. Learning about the troubles that skaters have with their blades, I felt that we could make something better.
The material must balance hardness and toughness. We prototyped more than 100 sets with different materials and processing methods.
Here’s what Uno had to say about the blades born from these efforts.
Uno
Because you get so much from each push, it’s less physically taxing, which ultimately has a positive effect on your jumps.
For blades, hardness is key. I’ve been using these for two years without sharpening them once. When these blades break, it might be time for me to retire. (laughs)
Steel is to Yamaichi what cars are to Toyota.
CEO Teranishi radiates confidence in the company’s craftsmanship, cultivated through years of sweat and toil. “You can strap these on and use them forever, which doesn’t make for good business,” he says with a rueful grin.
Where carmaking meets blade-making
Takaki Ishikawa, who oversees Yamaichi’s manufacturing operations, explained how the company’s carmaking expertise was put to good use.
Takaki Ishikawa, Group Manager, Yamaichi Special Steel
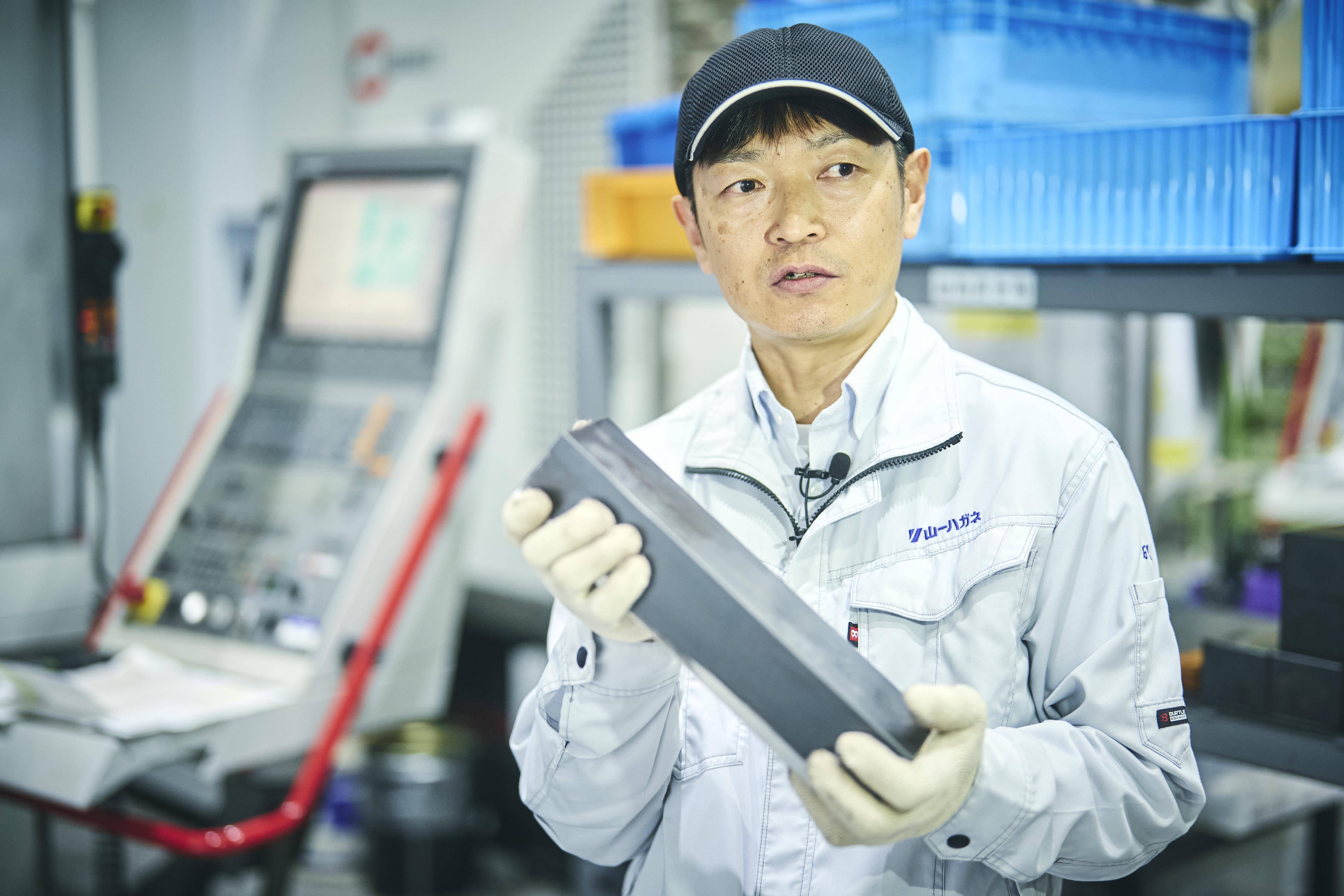
Cutting hard special steels involves applying immense force, which unfortunately can cause the material to warp.
The key lies in minimizing that deformation to ensure precision. We cultivated this know-how while working with Toyota to produce molds for motor cores.
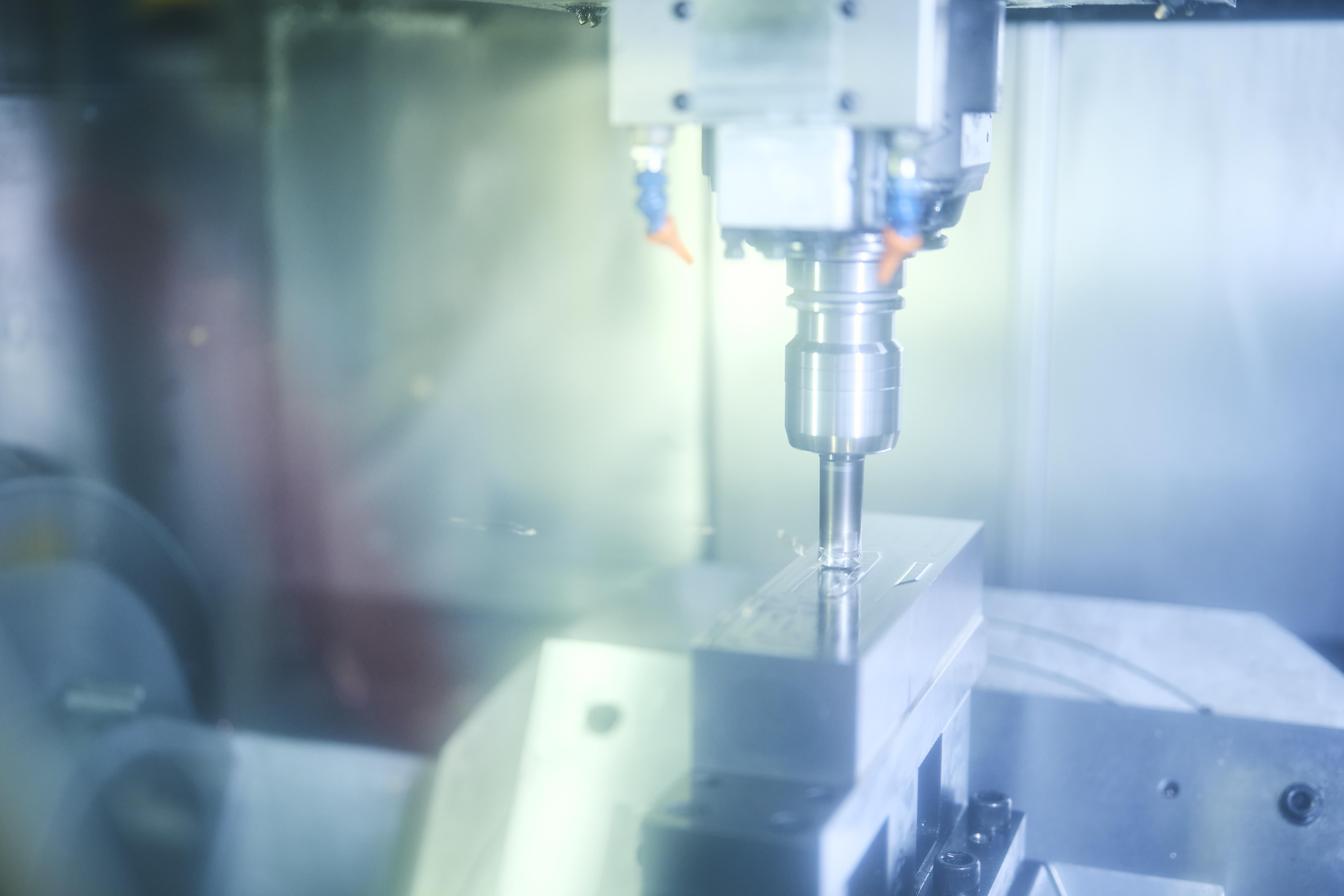
Yamaichi first became one of Toyota’s carmaking partners back in 2016.
CEO Teranishi
We started working together when our company launched a new cutting-edge joint venture with a French firm, 3D-printing plastic and metal parts for aircraft.
We contacted Toyota and began by delivering design software and 3D-printed pieces.
The mobility of the future will rely on technologies not yet in use today. We look forward to seeing the role that Yamaichi’s technologies come to play.
Incidentally, Toyota sometimes faces claims of “subcontractor bullying” in its relationship with suppliers. We asked CEO Teranishi for his honest opinion.