
How do you recycle 99% of a car that contains around 30,000 parts? Here we offer a peek into the world that awaits vehicles once their driving days are over.

Like paper going through a shredder, a one-tonne steel car meets its end at the hands of a giant machine. Not many car owners know what fate awaits their cherished cars once they’re no longer fit for the road.
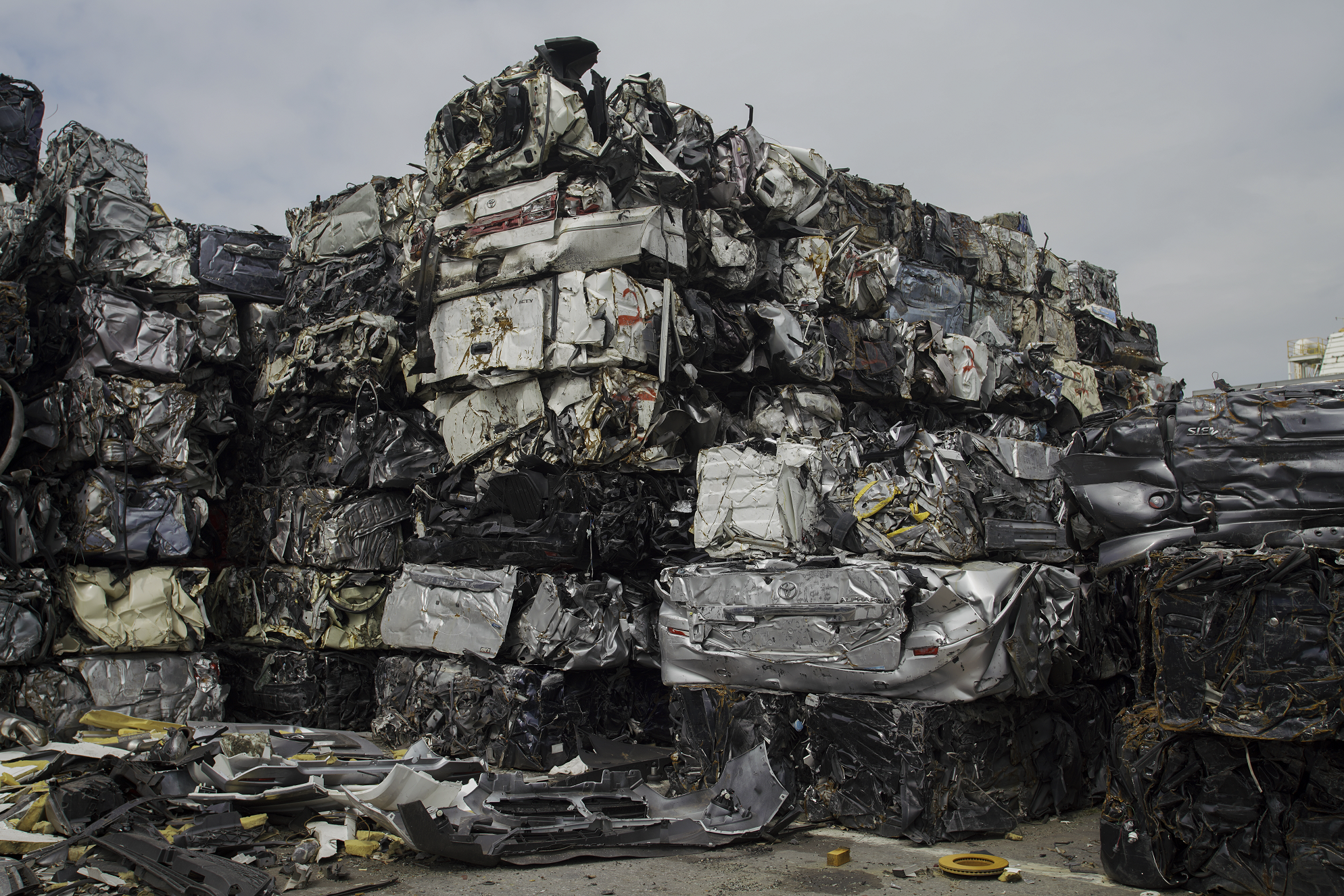
For this article, Toyota Times delved into the rarely seen world of end-of-life vehicle recycling.
99% recycled
In March 2022, Toyota’s Japanese social media account featured a GIF animation in the style of a retro game.

It depicted a big car made up of some 30,000 parts being 99% recycled. How is something as complex as a car pulled apart and turned back into usable resources?
The secret, according to Toyota’s Environment Affairs and Engineering Management Division, lies in the way cars are put together.
Built to be taken apart
Toyota builds its cars with easy-to-dismantle designs. But what does easy mean, exactly?
Masahiro Egawa, Environment Affairs and Engineering Management Div.
Toyota vehicles are made to be taken apart. By building this into designs, we can simplify disassembly work and boost recycling efficiency. Starting with the 2003 Toyota Raum (a Japanese domestic model), we’ve been adopting designs that streamline disassembly and sorting to promote the recycling of resources such as copper and rare metals from end-of-life vehicles.
At every stage, Toyota’s production genba emphasizes the need to make work easier for those handling the next parts of the process. Even so, most people would not be aware that this even extends to the end of the car’s life a few decades into the future.
Egawa speaks of one particularly satisfying sight during a vehicle’s disassembly. He refers to the moment when the electrical wiring harness threaded through a car’s interior is stripped “as smoothly as pulling the bones from a grilled fish.” Egawa revealed the secrets that make this possible.
First, the wiring terminals are designed to be easily removed when the harness is pulled, like the lid of a can.

The wiring harness also has a point that, when pulled, allows it to be removed in one motion without coming apart. This spot is wound with yellow-green tape, making it easy to recognize, even when working with heavy machinery.
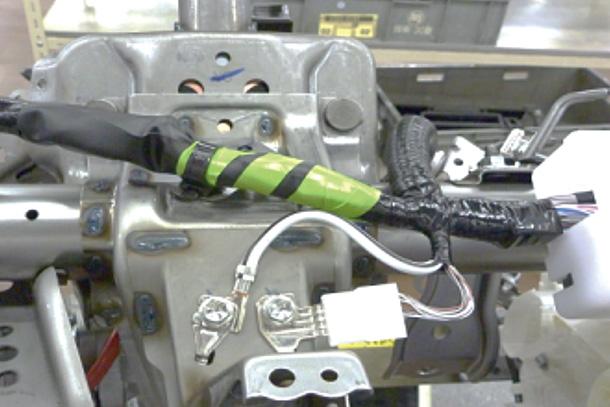
Toyota has also brought the heavy machinery used by dismantlers into its plants. This assists research into easier dismantling, with the results reflected in vehicle designs.
Risa Oya
A car that is easy to dismantle is easier to assemble during production and also easier to repair or replace parts at dealerships. It makes work easier for many people.
With the number of electrified vehicles set to increase, the team is already thinking ahead about how they will be taken apart.
Hideto Mitsuhashi
Battery electric vehicles carry large batteries that weigh over 500kg. We’re working with manufacturing sections to consider how to remove and transport these batteries more easily.
Having been designed for easy recovery of resources, how are the scrapped vehicles recycled?
Cubes of vehicles
Vehicles arriving at the dismantlers are first drained of waste oils and other fluids. Bumpers, doors, engines, and other parts fit for use as second-hand spares are then removed. The leftovers are flattened in a press and taken to a recycling company.

Toyota Times visited Toyota Metal, the world’s only recycling company jointly managed by a carmaker.
There, each car is pressed into a cube weighing around 600kg. Several such blocks are hoisted together, crane game-style, into a shredding machine to be pulverized.
From there, a conveyor carries them into a building where scrap steel is sorted away from non-ferrous metals such as aluminum and copper. This even includes small quantities of gold and silver.
The steel thus recovered is taken to steel manufacturers, where it may again find its way into vehicle bodies—cars made from cars.

Sorting makes everything a resource
After the metals have been recovered, what remains is a mixture known as “shredder residue,” which includes materials such as resin, urethane, and glass.
To the untrained eye, shredder residue looks like nothing more than garbage. And yet, this too yields resources, as resins and other intermingled materials are also recyclable. The key to turning trash into resources lies in sorting.
Another day, another 400 tonnes of resources from end-of-life cars
Toyota Metal President Tadashi Matsumoto came to the company in 2019 after working in the field of environmental recycling at Toyota Tsusho, a Toyota Group trading company. “Twenty years ago, we were seen as a scrap dealer,” he says before explaining the company’s vision.
Tadashi Matsumoto, Toyota Metal President
Toyota Metal began in 1970, back when recycling was far from most people’s minds, with a dedication to the mission of reusing resources.
We’re proud that we give disused cars a new lease on life as resources. Our modern society has vast reserves of resources waiting to be recycled and reused, and we want to unearth them to help create a circular economy.
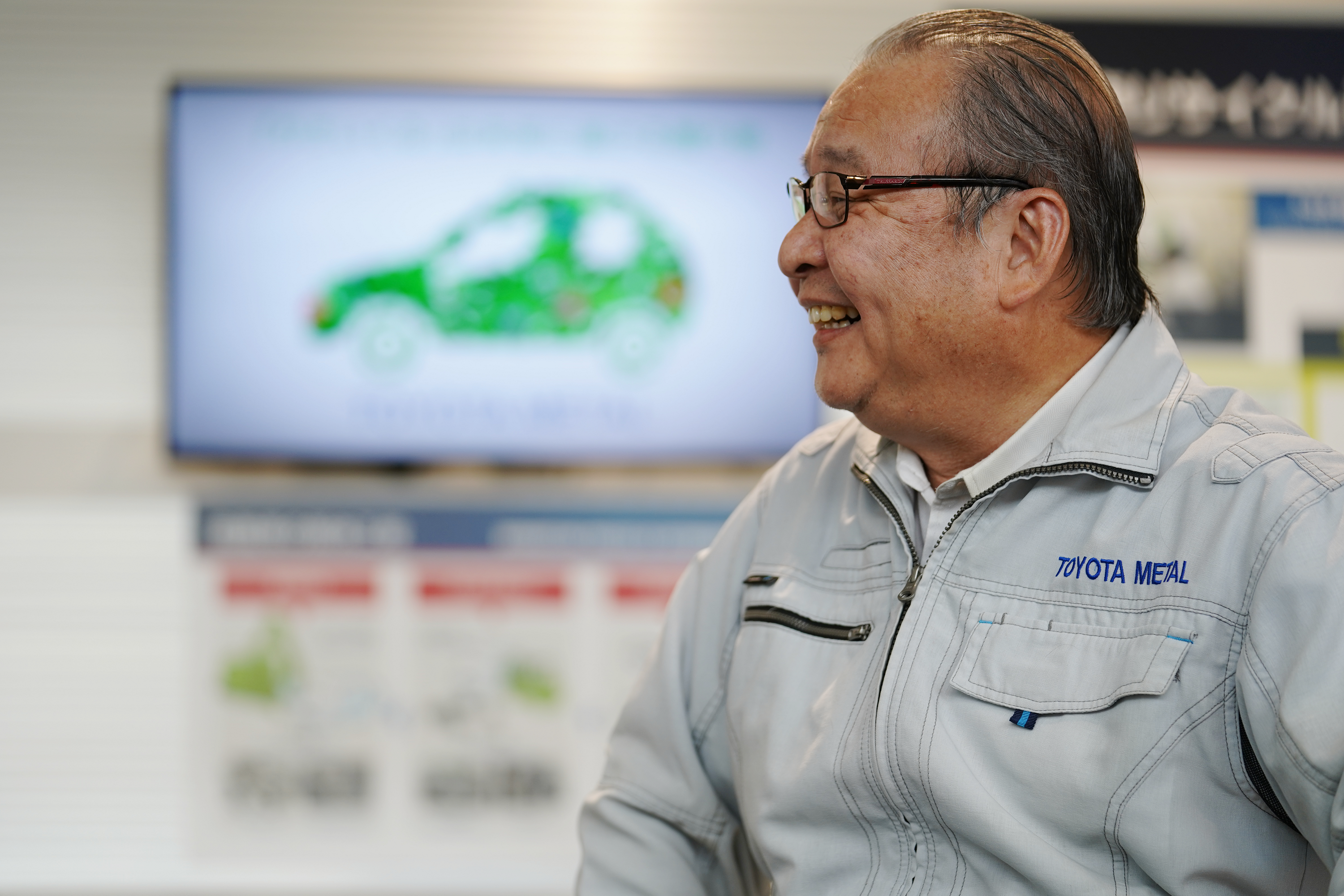
Making cars carbon neutral is not just about production and use—figuring out what to do with them afterward is also crucial. In Europe, proposed regulations prohibit the sale of new vehicles unless they meet certain standards for recycled materials. Carmakers’ involvement in recycling companies will only grow more relevant.
Hirotaka Natsume, who made a career change to join Toyota Metal, shared his motivation.
Hirotaka Natsume, Toyota Metal Accounting & General Administration Department
My last job was in sales at a Toyota dealership, selling Corollas. I moved here because I was curious about what happens to the battered old trade-ins. At Toyota Metal, we extract up to 400 tonnes of resources daily from as many as 1,000 cars.
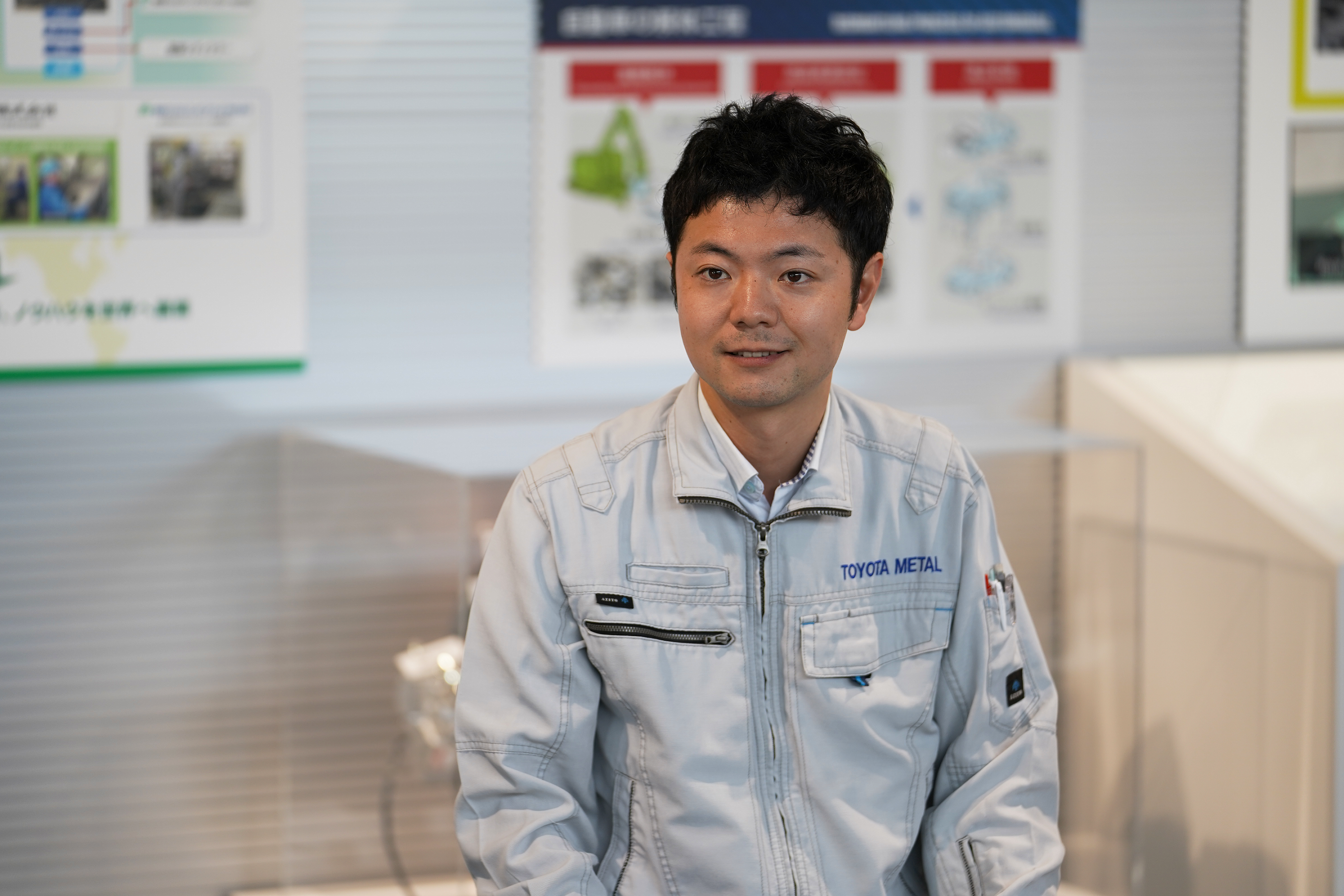
Four hundred tonnes per day. There is a world of difference between this becoming garbage or useful resources. “No other job is as good for our planet,” remarked another employee on that significance.
The mystery of the last 1%
So when 99% is recycled, what happens to the remaining 1%?
Tadashi Matsumoto, Toyota Metal President
The remaining 1%, consisting of things like mixed rubber after the metals are recovered, is used as fuel. The resulting ash-like substance is often used as a hardening base material when building roads.
As it turns out, even that 1% has found its way to serving society. These days, all kinds of manufacturers beyond the car industry come to observe Toyota Metal. What takes place there is not dismantling but rather cutting-edge resource creation.
As Toyota President Akio Toyoda says, “Cars are one of the few industrial products that are affectionately called ‘beloved.’” It is moving to think that, even at this moment, all those cars beloved by owners for many years continue to live on somewhere, only in a different form.
