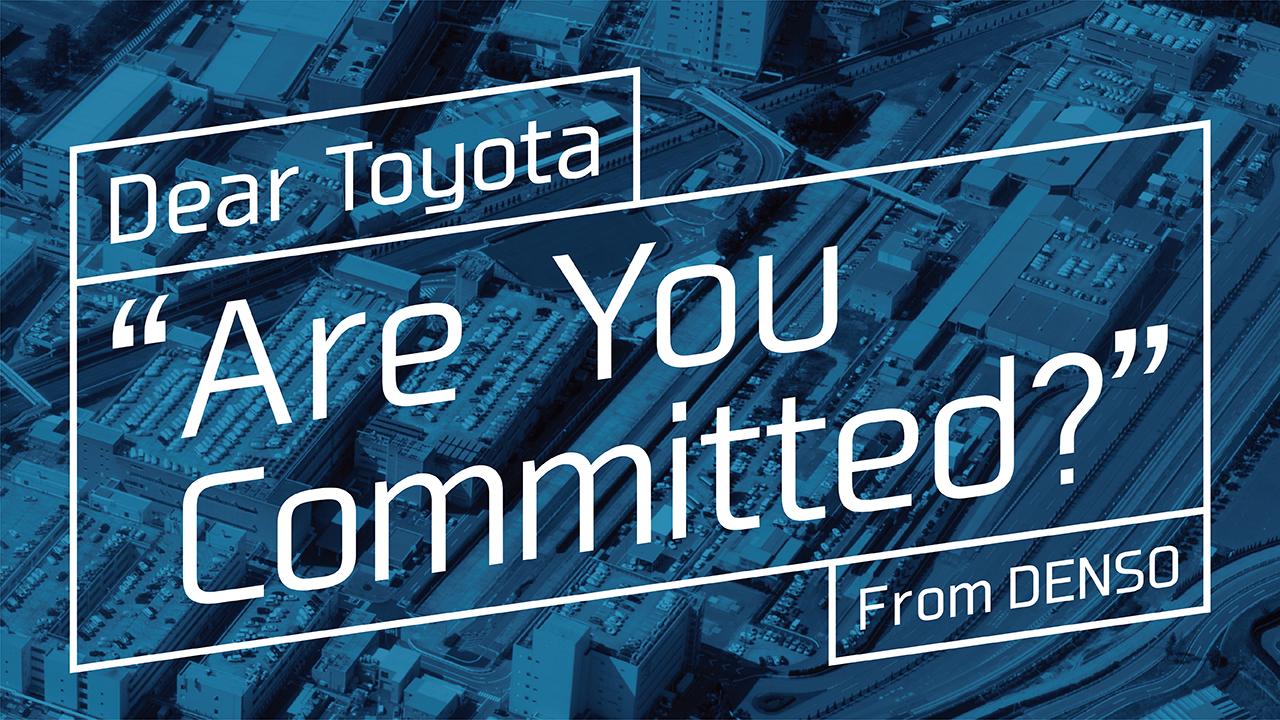
As part of the company-wide TPS training program that started in 2020, Toyota's R&D group, Vehicle Development Center has conducted various kaizen activities on "meter development" together with its partner DENSO. How did they solve issues and what is their progress?
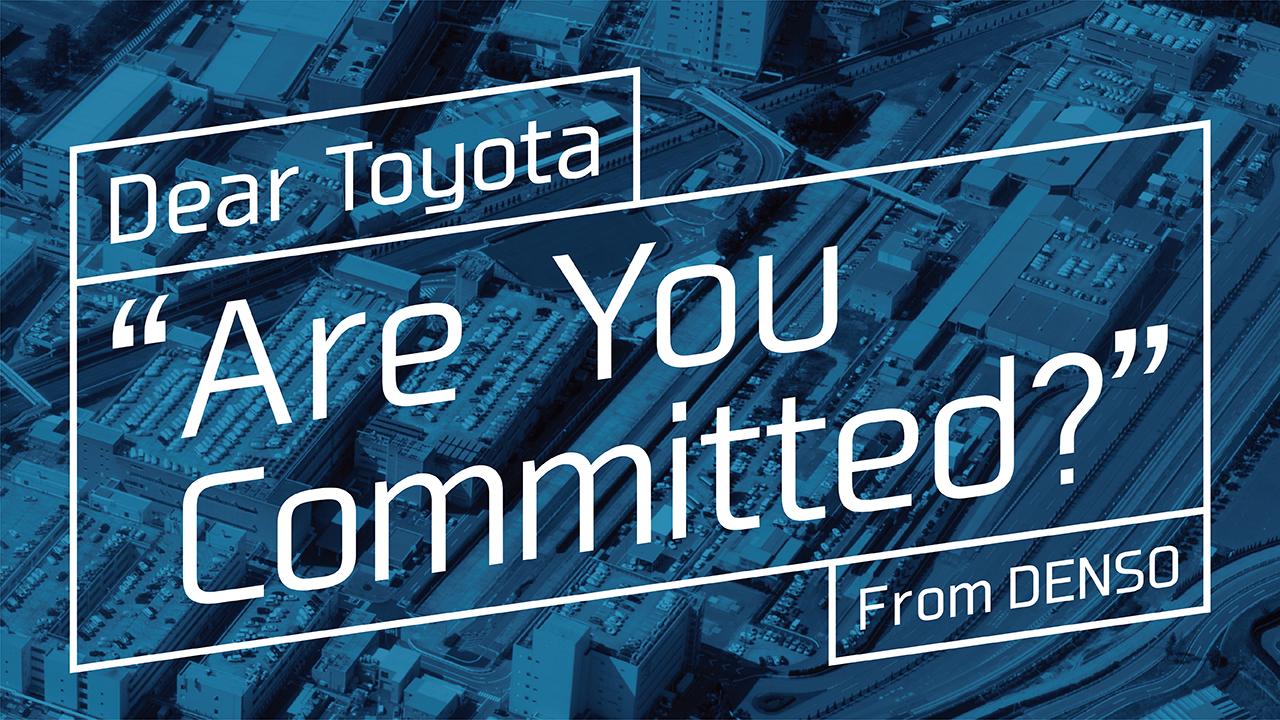
Toyota’s company-wide TPS training program for office staff was launched in August 2020. In the previous article, Reporter Kyonosuke Morita of Toyota Times joined the joint presentation in this initiative, and interviewed two key persons who promotes TPS, Executive Fellow Shigeki Tomoyama and Chief Officer of the TPS Group Kyogo Onoue.
On a later day, Morita came down to Toyota City, where Toyota has its headquarters, to report on the specific efforts by one R&D group, the Vehicle Development Center. Toyota Times was given exclusive access to the “TPS Room” of the group where they discussed and conducted actual kaizen measures in the last several months.
Furthermore, an interview with engineers from DENSO, one of the major business partners of the Vehicle Development Center, revealed what the real TPS genba was like between Toyota and Denso, in which they exchanged honest feedback to seriously improve their work process and continue it for many more years to come.

What kaizen activities have been implemented in the production of increasingly complex digital meters?
Hiroki Kawakami of the BR Electronics Control Renovation Dept., and Masayoshi Hattori of the TNGA Management Div.-they are the leader and sub-leader in the Vehicle Development Center’s TPS project with around a dozen members in the team. To kick off the project, they have set up the TPS Room and have been involved in kaizen activities since then.
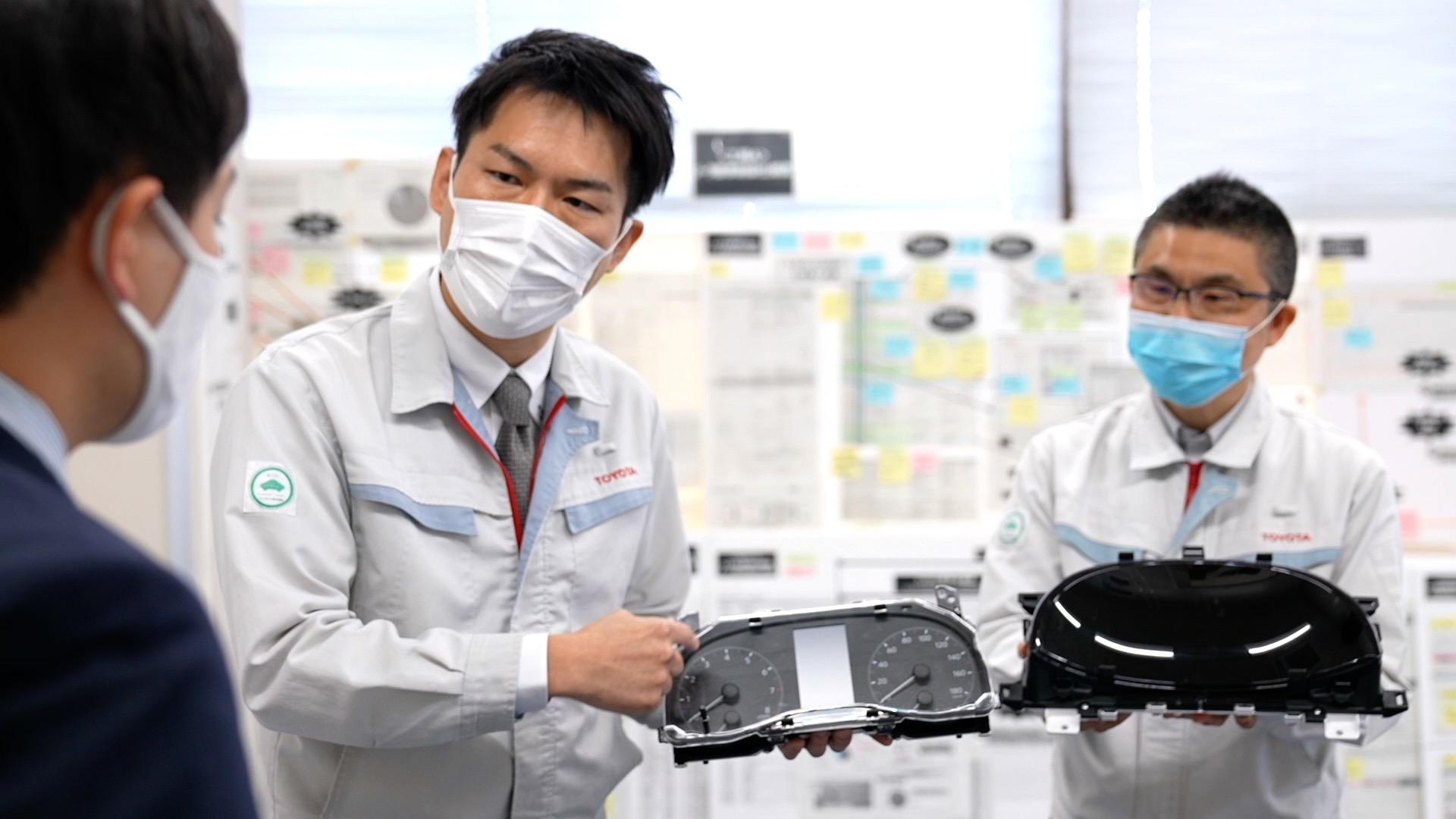
The Vehicle Development Center oversees everything from the advanced planning of vehicles to the development of mass production vehicles, and it is one of the organizations that promote software-first initiatives in developing vehicles. In this kaizen project, the members worked on improving the process of developing meters inside vehicle cockpits.
Kawakami
Toyota is aiming to place software first, and in the future, we will be required to further bolster the added-value of software and speed up development. Software is particularly important in meters, so kaizen in this area is unavoidable. We plan to implement kaizen in meters, then apply them to other parts.
In recent years in particular, the digital instrument panel has become larger and more multifunctional with the increasing need to show warnings and guidance to users. The information and content displayed there have increased rapidly, making the development work more complicated and difficult. That’s why we decided to focus on this part to implement kaizen.
Analog meters for showing speed and engine revolutions are now being replaced by digital displays. This has enabled the displaying of all kinds of information, but has resulted in a need for cooperation among a variety of fields and departments during the developmental stage, increasing the amount of time and number of people required. The development had to be streamlined so that software-first development Toyota has shifted to will become advanced as pursued.
There are four main stages involved in the development of meters.
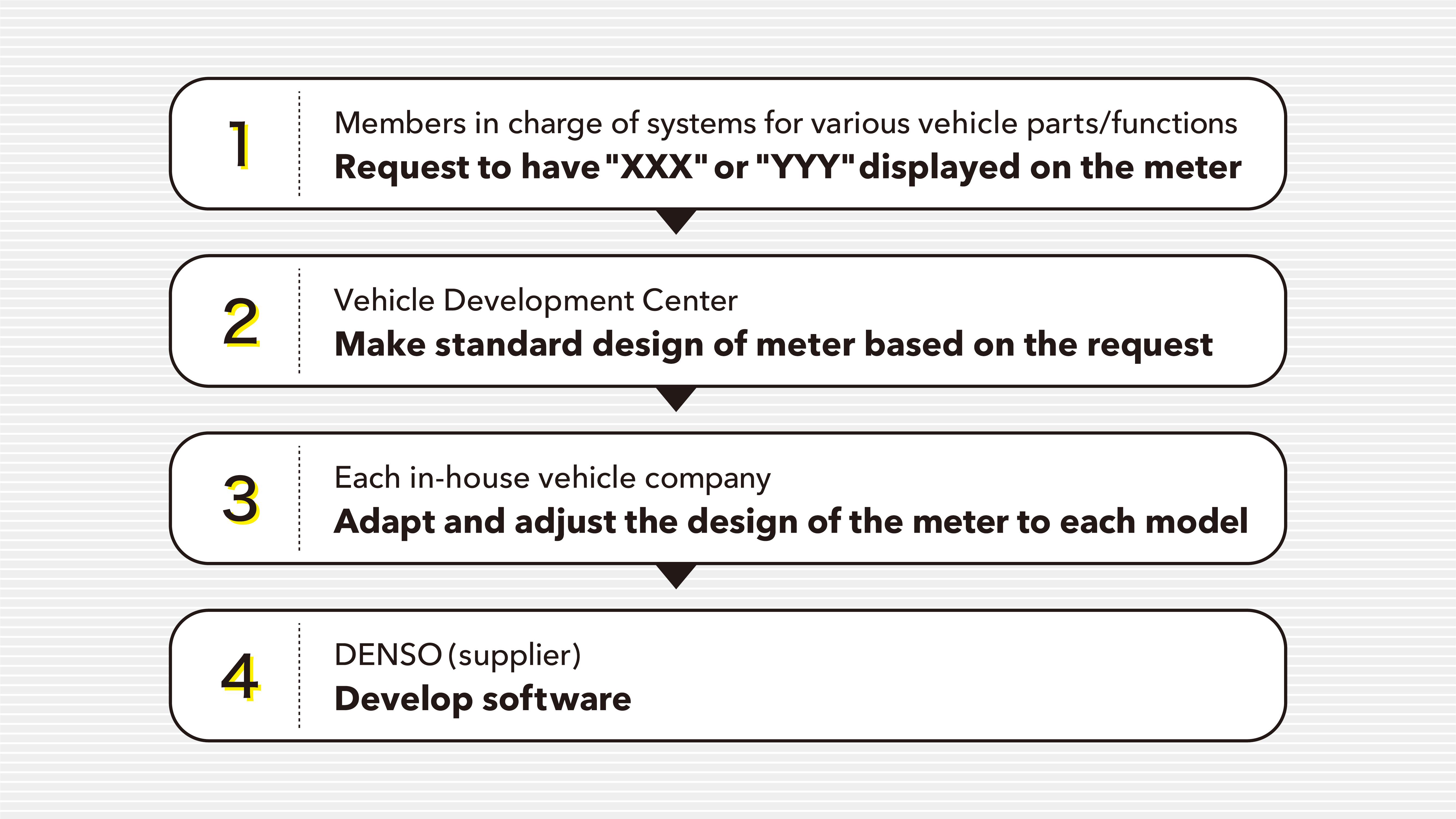
Training program members worked on kaizen in procedures (2) and (3), and the downstream procedure was handled by their supplier, DENSO. As it was explained in the previous article, the philosophy of TPS is based on the idea of “making someone else’s work easier.” In their case, that someone else means DENSO. Has their work become easier? This will be explained by the DENSO engineers in the later part of this story.
Material and information flow diagram; the starting point for TPS
The first thing that catches attention in the TPS Room is the walls covered in paper. There, diagrams with numerous labels are joined together by arrows.

Morita
These material and information flow diagrams really stand out inside the room.
Kawakami
It’s a vital tool for putting TPS into practice. The material and information flow diagram is created upon ascertaining the actual work flow. It’s an excellent tool whose purpose is not only to enable visualization of the work, but to identify procedural problems, such as delays and rework, while also allowing others to discuss the issues with the people involved based on a shared perspective.
Called “monojo” in short in Japanese, the diagram allows visualization of the flow of procedures, identifies delays in the flow of materials and information, and shortens overall lead time. Specifically, it encloses a certain set of operations in a box and shows the flow of materials and information there. Where the flow cannot be drawn up, there is a high possibility of operations being vague. The diagram allows identification of potential kaizen issues.
Kawakami
Along the x-axis are the days, and this diagram shows the procedures implemented from summer 2019 until summer 2020. Specifically, it enables visualization of the entire flow of materials and information on determining the control specifications of meters, in addition to the actual flow of specifications forms sent out to the supplier (DENSO).
On the y-axis are the members in charge. The divisions in charge of meters in the Vehicle Development Center receives information from the divisions developing systems, and the actual vehicles are planned and developed by Toyota’s in-house vehicle companies where there are people in charge of meters for each model. Then the supplier comes in at the end.
Morita
There are so many labels, but what are they?
Kawakami
Different office staff have different styles of drawing up a diagram, and people rack their brains over how to do this in order to identify the issues. In this example, the yellow labels indicate what the members in charge are actually doing. Pink labels indicate the issues and delays that have come to light.
What’s important here is not to indicate “what work there usually is,” but to indicate “what work the person in charge actually did.” This should be clarified by hearing from the members who actually carry out the work on a genchi-genbutsu basis, not on one’s image or guess. Writing down the procedures based on facts allows identification of the real issues.
The Vehicle Development Center receives a request (requirement specifications document) from the people in charge of upstream processes to “display XXX or YYY information on the meter.” A control specifications document indicating how the meter works is issued to DENSO in charge of downstream processes, and then the meter is developed and manufactured. That summarizes the main procedures.
So, how are issues and delays identified?
Morita
How do you identify delays?
Kawakami
It’s not just the number of days taken. Time may be wasted while waiting for the requirement specifications document, or while making adjustments. We checked if there was such a situation as we updated the diagram. Where it says “temachi” or waiting time, it indicates that time is being wasted while waiting for materials or information.
Morita
So it means that drawing up this diagram a little at a time resulted in the identification of potential issues in the areas indicated by the pink paper labels.
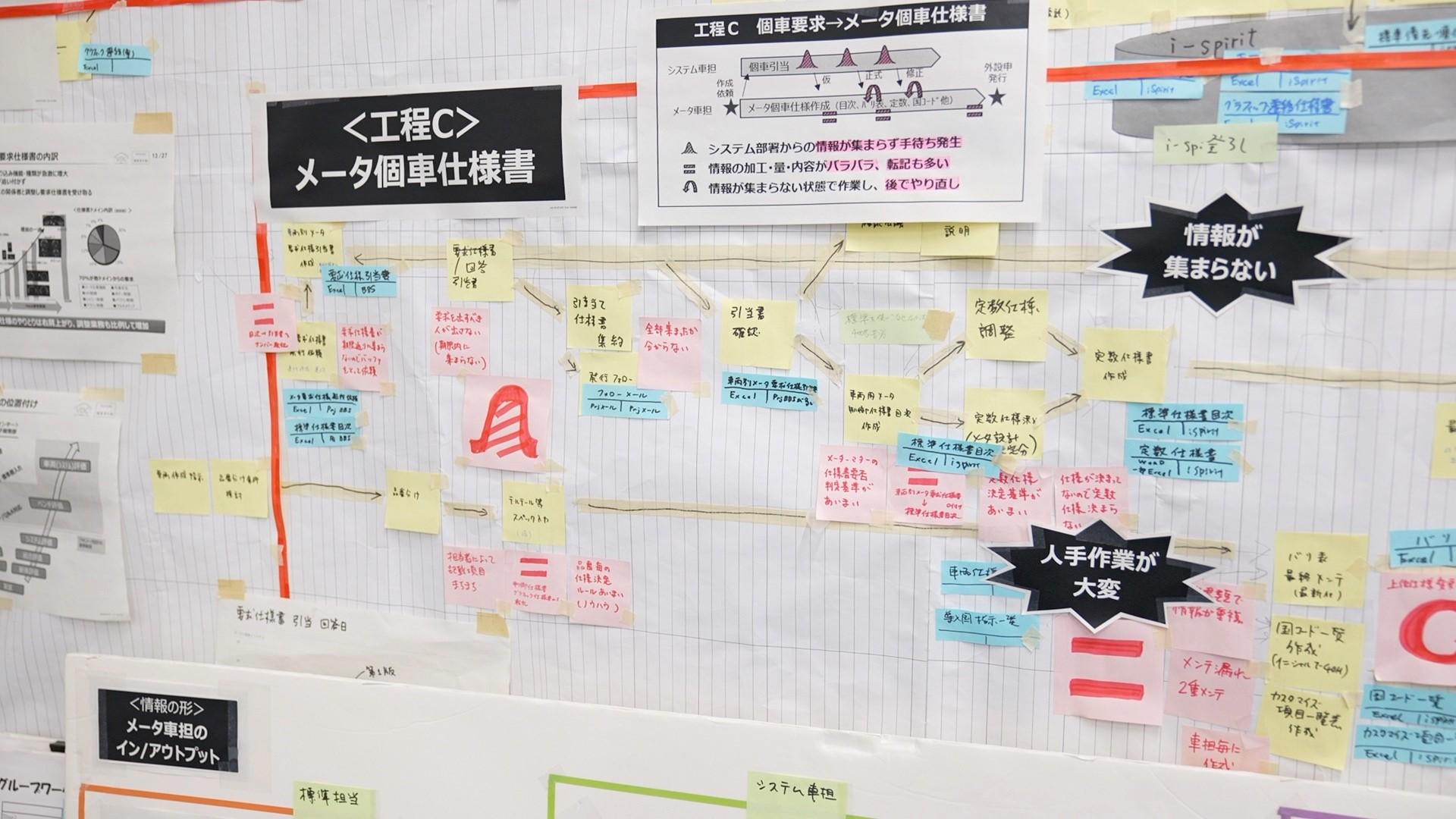
Simply drawing up a material and information flow diagram leads naturally to the identification of issues.
Shortening the work time while also decreasing the burden
In this kaizen project, the procedures indicated in the diagram were divided into three parts in order to learn of the issues. First is the procedure to issue a requirement specifications document after discussions between the divisions developing systems and designing meter standards, before completing the process when the meter control specifications document is issued.
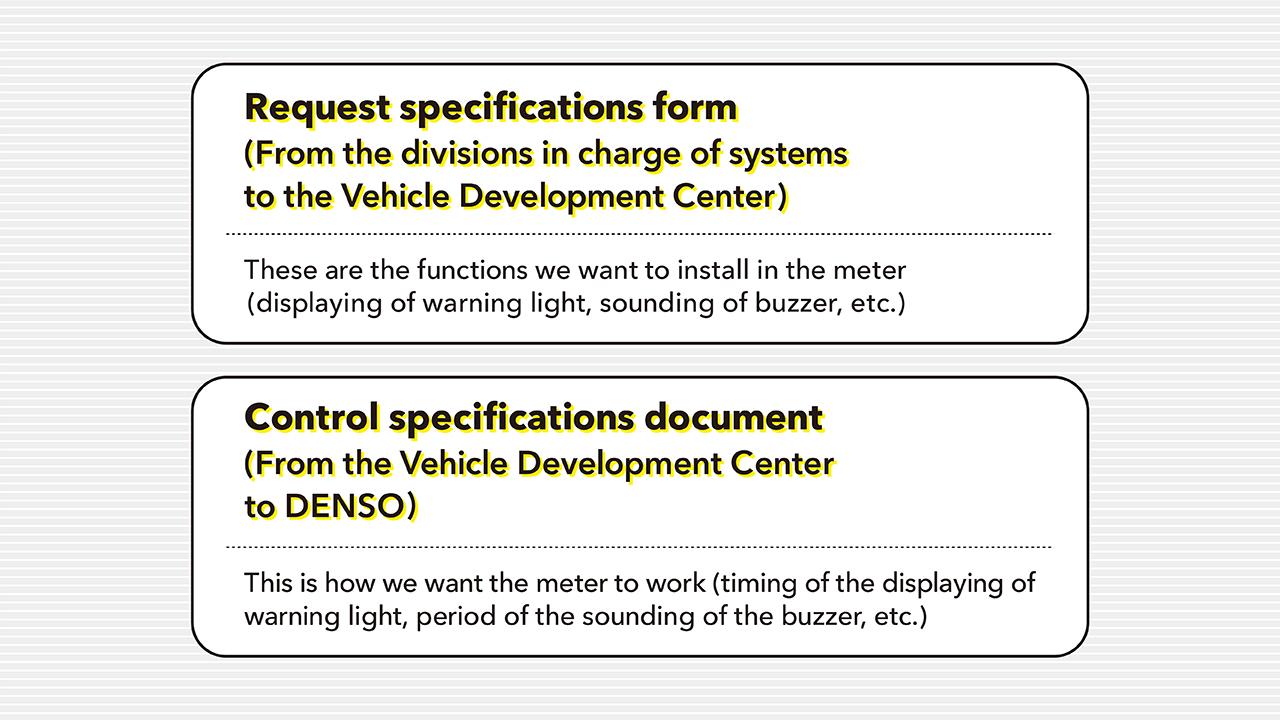
The lead time required for this process was 120 days. It took four months from the time the person in charge at the Vehicle Development Center asked divisions developing various systems for their request, until an order was placed with DENSO.
What took a particularly long time was the exchanging of opinions leading up to the completion of the requirement specifications document. The Vehicle Development Center would convey the delivery deadline, then ask the various departments in charge of systems to submit their requirements as soon as possible. It would be easy if all the requirements could be compiled in the document, but not all the requirements were submitted as early.
Kawakami
The people involved in upstream processes would think, “We still have time” or “We don’t have to submit the requirements yet.” Therefore, many of them would submit their specifications documents just prior to the deadline. This led to the members involved in development on our end having to face great difficulty. Similarly, they received few requirements at the beginning, so they just waited for nothing.
As a result, if the documents are submitted to us at an insufficient level just before the deadline, we would have to delay the timing of issuing the specifications documents, or we would have to go back to the upstream process when we are proceeding with our control specifications documents because some mistakes are discovered.
This led to the identification of two types of waste; waste from waiting and waste stemming from defects and having to make corrections.
Waste from waiting sometimes lasted up to two months after asking for submission of requests. While time was wasted in having to wait, they would be inundated with work around the time of the deadline. This would result in deterioration of precision and a need to make corrections. It was also time-consuming, and placed a burden on the members working on-site as the deadline approached.
So, a decision was made to implement kaizen to eliminate these two types of waste. First, the work was beginning too early. But delaying the start of work could not be a solution. As Kawakami says, dealing with a huge number of requests in a short period of time placed a huge burden on the members in charge on-site. In other words, there was a need to delay the start, while reducing the amount of rework just prior to the deadline.
So, work began by examining what kind of work was being repeatedly done.
Hattori
We analyzed everything one at a time, and it was revealed that around 80% was due to clerical mistakes and failure to adhere to the rules. It came to light that people were not sticking to the guidelines.
Kawakami
Most of the mistakes stemmed from typographical errors. Other than that, time was wasted on numerous inquiries regarding the format of the requirement specifications documents and how to write them.
For example, some people mistakenly use the word “cancel” although the designated English translation for the term was “deactivate,” which led to a request to correct the mistake.
But instead of saying, “Please beware of typographical errors” or “Please adhere to the designated format,” the aim of TPS was to focus on “why such mistakes occur.”
At Toyota’s R&D divisions, they often use check sheets for verifying information after entering it into the system. They include questions like, “Did you check A, B, and C?” which you check off. But the answers for what had to be verified on the check sheets varied from person to person. They resulted in discrepancies in the answers depending on who was carrying out the checks, leading to inconsistencies in the identification of errors.
This meant that the end product differed depending on who was carrying out the work. What is useful in kaizen here is standardized work. The quality standards of the finished product have to be clarified, and the work has to be standardized to eliminate inconsistencies. This is the concept of ensuring quality during the production process as was described in the previous article.
Simply shortening the work time only places a burden on on-site workers. That’s why identifying and eliminating the causes of waste is important to lighten their burden. The result was that the 120-day lead time was shortened to 35 days.
Listening to the opinions of people working downstream
Apart from what was described above, two more issues were targeted for kaizen.
One was a problem with the huge number of inquiries that were being received from the supplier, DENSO, regarding the control specifications documents issued by the Vehicle Development Center. Many of the inquiries were the result of inaccuracies and mistakes in the specifications forms. Simple errors were being conveyed to DENSO, disrupting their work.
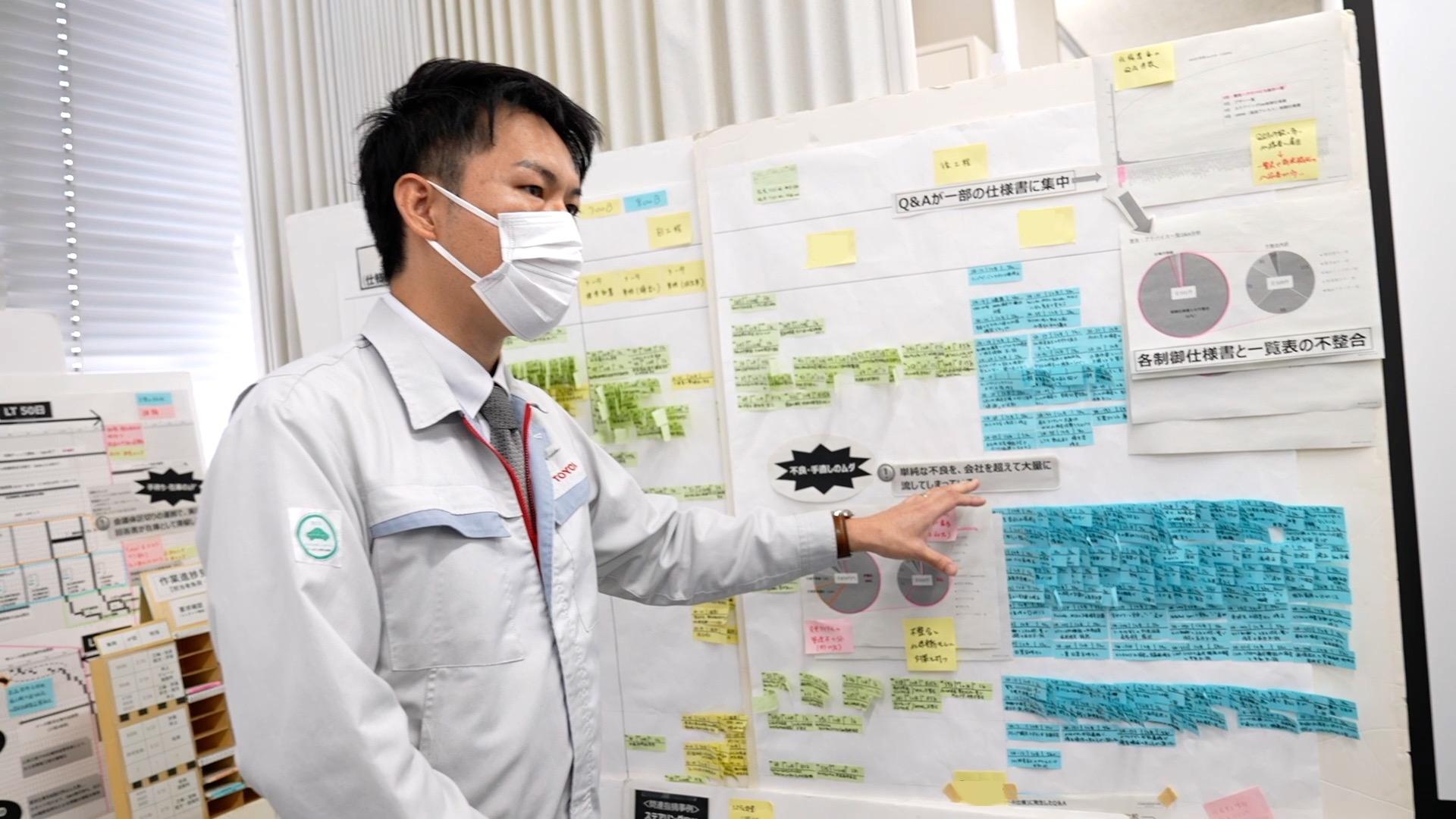
The other issue was in the process of deciding the specifications for the meters of different vehicle models. The meters are bound for different destinations depending on the model, and detailed decisions had to be made, for example, on whether to display the speed in kilometers per hour or miles per hour.
The detailed specifications per stock numbers of meters are compiled on what is known as a “variation chart.” In the process of preparing these variation charts, there were no standard rules on the types of information to be gathered, and a lot of the work involved manual copying of information onto the charts leading to inconsistencies in the details.
Moreover, the variation charts themselves were sometimes different depending on where the vehicles are made. In other words, DENSO would receive these charts, and had to iron out the inconsistencies.
Kawakami
The amount and type of materials and information differed from vehicle to vehicle, making it extremely hard for DENSO to deal with, so they had to reorganize the information they received every time. We realized we had been forcing them to waste their time.
Here too, kaizen efforts were made to standardize the work to eliminate inconsistencies. In doing so, they focused on standardizing downstream procedures based on “the amount and type of materials and information needed by DENSO.”
Kawakami
We discussed how the variation charts were actually being used by DENSO and what kind of charts they wanted in deciding the standards.
Information may be of convenience to Toyota, or Lexus, but such information was difficult for the recipient, DENSO, to use, resulting in them having to carry out (extra) work. So, discussions were focused on the type of information that DENSO would appreciate in receiving.
How the variation charts were being used was verified through genchi genbutsu by actually visiting DENSO. Work is apparently being carried out even now to try and standardize the variation charts.
The true opinions of the supplier
What were the objective opinions toward this initiative to implement TPS for office staff? And what effects were actually felt? Toyota Times was able to talk to the people in charge of processes at DENSO, outside Toyota and downstream of the Vehicle Development Center. Product General Manager Wada and Manager Yoshida were not only involved in downstream processes, but they also cooperated in the kaizen project.

Morita
As a supplier, two of you from DENSO took part in the TPS training program for office staff this time, but how did you honestly feel when you heard about this initiative?
Wada
We were told about it in September last year, and the first thing I said was, “Are you committed?” because I wanted to know from the start how deeply we were to get involved in it. I wanted to know this, because we had worked on the same initiative with Toyota in the past on several other occasions.
Morita
Why did you want to know how serious they were about it?
Wada
This isn’t easy to say, but in the past, I feel that Toyota has given up in the middle of some projects. Based on such past experience, I wanted to know from them how committed they are this time and how they plan to make changes.
He shared his honest feelings using such impactful phrases as, “Are you committed?” and “Toyota has given up in the middle.” So, why did they decide to cooperate this time?
He apparently realized how serious Toyota was about the initiative this time, because the whole company was behind it, and they even established a dedicated team to implement TPS measures. He saw that a team had been set up for the training program to assist the Vehicle Development Center, and thought that “things may go well” this time.
Yoshida
I was quite frank in asserting my views this time. I was quite harsh in telling Toyota where they needed to make improvements, but in response to my views, Mr. Kawakami said, “Thank you for pointing these things out. Please don’t hesitate to tell us more.” So, I haven’t been holding back on expressing my opinions (laughs), which has made things very smooth.
In implementing TPS together, the key to success has been building a relationship that has allowed them to air their concerns without hesitation. The immediate assertion of these candid views testifies to the mutual relationship that has been built up over the past several months.
More than a year ago in April 2020, there was an opening ceremony at “Denso Hirose Plant”. As part of the “Home & Away” strategy, Toyota and Denso announced consolidation of their core electronic component operations, including then Toyota’s Hirose Plant within Denso. That’s how the plant was reborn.
At the ceremony, President Akio Toyoda shared his thoughts on the decision as follows:
Akio in April 2020
‘Home & Away’ does not mean simply cutting off or consolidating business operations.
It means solidifying our group-wide efforts so we can survive in this era of profound transformation together. Then, we will be able to help create the future of Japan and the future of mobility.
‘Home & Away’ is a Toyota Group strategy to that end.
Therefore, it is not necessary to look at things as one leading and the other following or vice versa.
All we need is a shared ‘willingness’ to make ever-better cars.
Toyota and Denso will develop an equal relationship, and present it to the entire Toyota Group.
The TPS team this time built exactly such relationships in which there was no hierarchy of one leading and the other following.
The discussions on actually implementing the kaizen activities were as follows:
Yoshida
We were receiving specifications documents that were not of good quality. We would say, “These specifications documents are probably not right,” leading to the issuing of numerous forms to notify Toyota of the problems. To prevent this, we provided them with information on what checks to carry out in order to boost the quality of the documents.
Morita
You could tell them about the trouble just as you were struggling with it, right?
Yoshida
That’s right. We would point out specific examples to say, “We did this and that to discover these problems,” or “You can do this to ensure the prior detection of defects.”
So, how do they feel about the results of the project to date?
Yoshida
Once again, I’d like to be frank in expressing my opinions, and I feel that the next step is to continue this initiative as an organization. Kaizen is currently underway. We now have an idea of how it’s done, and we’ve achieved results through it. But we mustn’t end here. I think our next step is to make sure it is incorporated into our operations and organization so that it is implemented in a sustained manner.
Wada
Other than the Vehicle Development Center, there are many others at Toyota who use the meter specifications forms, and I think our issue going forward is to try and promote kaizen among all those involved.
The expansion of TPS to 5.5 million people in the industry
As reported in two articles, the TPS training program was launched with the aim of spreading TPS beyond production sites and among office staff within Toyota, but it is also spreading steadily outside the company. The interview with DENSO testified to the potential of how TPS can be applied more widely in the supply chain.
The two engineers from DENSO stressed that what these activities achieved as its first step was the fostering of an attitude of listening to the issues of downstream workers.
Wada
In the past, I don’t think Toyota ever came down to our level to listen to our opinions. They had asked us our opinions, but we had been skeptical about how they were making use of them. That was the reason why I asked at the start, “Are you committed?” But these activities have really fostered solidarity. I also think we were able to achieve so much because the whole company became involved with the implementing of TPS for office staff, and we strived to set an example.
In doing so, he views the TPS training program for office staff as follows:
Wada
The concept of TPS has become firmly established in all parts of Toyota, so I think everyone is striving to implement kaizen in their respective processes. This has now spread to us, asking us what we do on our part. They turned their attention to us, which I think is how they have managed to take the initiative one step further in this TPS for office staff.
The idea behind TPS stressed by Akio was “to make someone else’s work easier,” and this has been firmly embodied in the efforts made. Furthermore, the idea is spreading outside the company through DENSO.
Wada
We too feel the need to promote this further within DENSO, and I think our efforts will spread even further to other suppliers. So, the idea should not be applied to DENSO’s products or to meters only.
It would be ideal for it to spread extensively throughout every aspect of our relationship with Toyota as a supplier. I think President Toyoda’s message is that he also wants to address structural issues in the automotive industry, including the 5.5 million people involved in the industry, whom he has recently been cheering for.
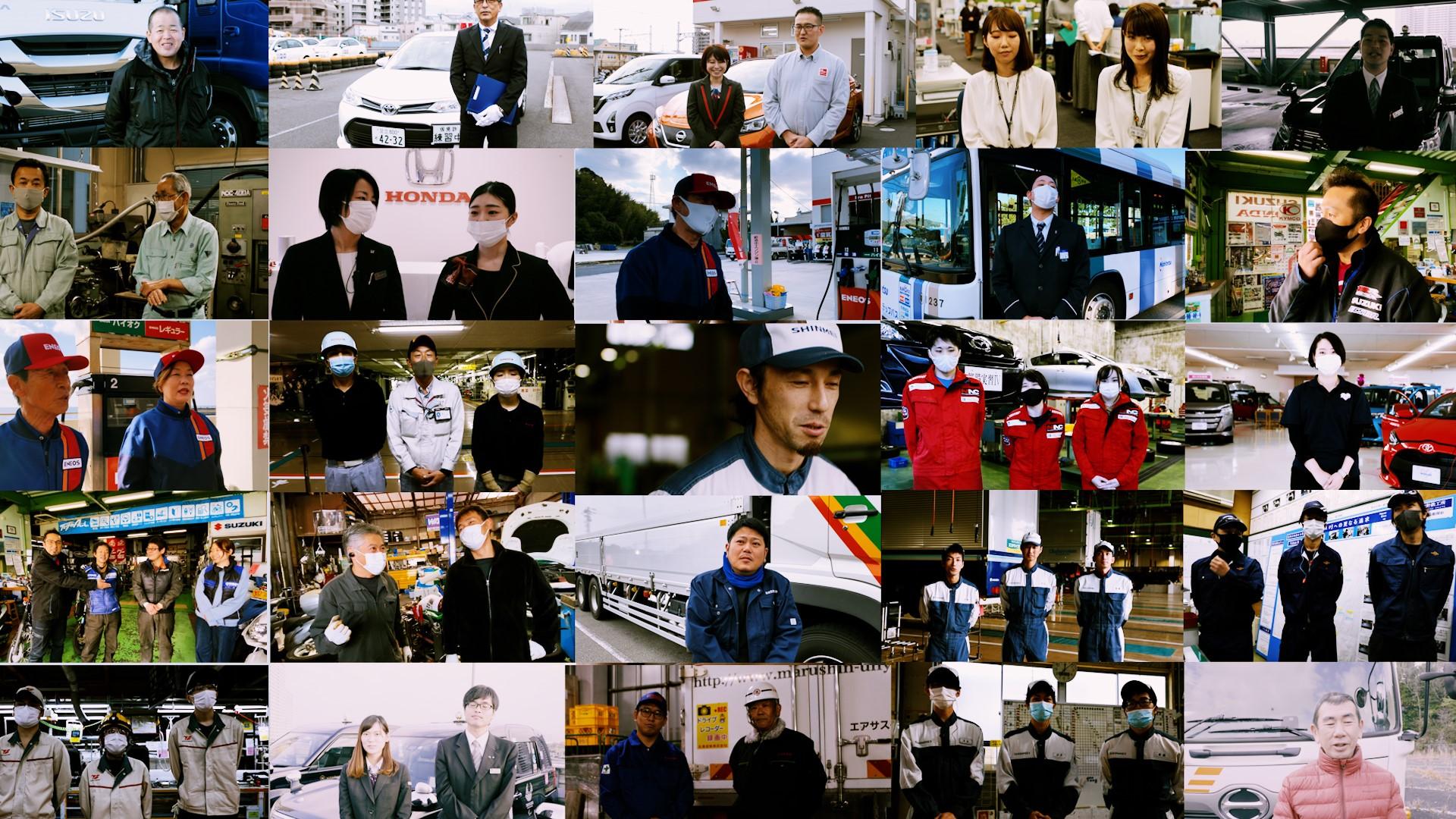
In January this year, JAMA Chairman Toyoda had a message for the 5.5 million people involved in the automotive industry. It was a powerful message in which he said that to survive this once-in-a-century era of profound transformation, now was the time to bring together the power of 5.5 million people, and the steps taken by every individual would make a big difference.
Much heard at JAMA or Toyota, but it was a very impressive moment hearing Mr. Wada of DENSO mention the 5.5 million people.
Wada
First, President Toyoda’s comment that the purpose of TPS was to “make someone else’s work easier” made it easier for us to make a start on this project. We have other business partners, so I think we have to promote these activities based on the same idea in order to spread the initiative. If we can do that, I think we’ll be able to realize true “Just-in-Time systems” for all procedures. Implementing TPS for someone else, as President Toyoda says, is an idea that all our members, including myself, can relate to, and we want to promote this far and wide from now on.
In reporting on the Vehicle Development Center this time, there were specific kaizen activities in great detail. It is needless to say that the shortening of lead time, and the decrease in the number of defects achieved through the activities are of great importance.
However, a major effect that TPS brings is perhaps the attitude of the people involved and how they further influence others around them. The two people in the downstream operations at DENSO are already beginning to think about operations further downstream. Perhaps this is what testifies to the ongoing success of the initiative. There is no end to TPS, as after kaizen is the state of before kaizen.
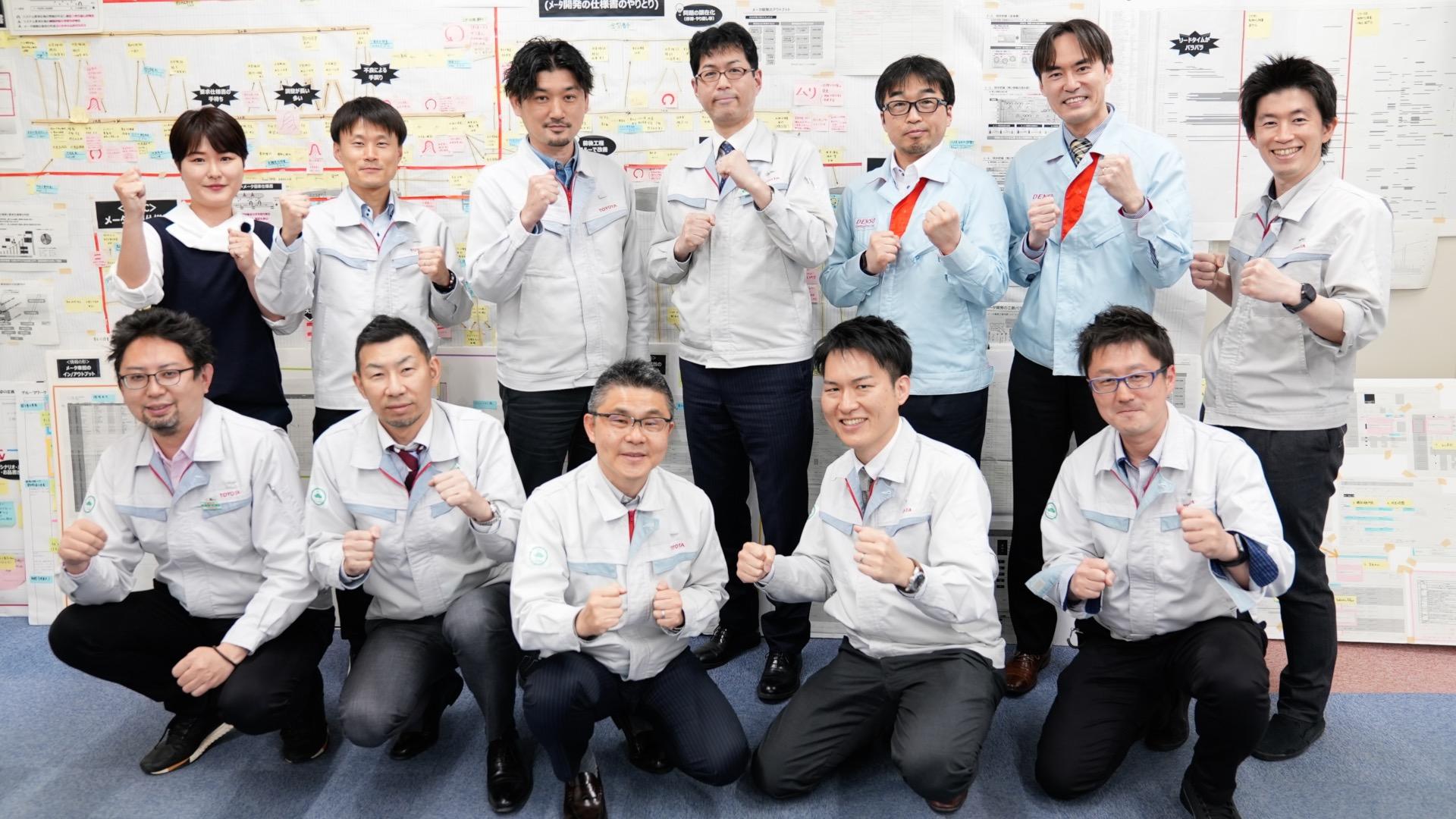
(Original Japanese edited by Mami Shoji)