
A project team worked on reviving Toyota's first racing car, the Toyopet Racer from over 70 years ago. This third part describes the challenge of rebuilding its transmission.

This series features Toyota’s project to revive a legendary racing car by reporting on the project members’ efforts as well as the history and meaning behind this vehicle. This article highlights the transmission team’s monozukuri (manufacturing) efforts.
Skipping first and second gears to honor the original
The transmission team finally reached the real monozukuri phase. The biggest challenge for Asuka, Honda, and Ishida was designing and building the Racer’s four-speed manual transmission. They pieced together 70-year-old blueprints to try and design the components.
The original Model SD transmission had four forward speeds and one reverse. However, for the Toyopet Racer, the specifications indicated third and fourth as forward gears, no reverse. The car effectively only had two speeds with the four-speed transmission. The first and second high gear ratios were designed for trucks and rarely used in the Model SD.
Asuka
I believe all four gears had been functional in the original transmission, but the shift linkage setup didn’t allow you to put it into first or second gear. We honored that design by also making a shift linkage that skips first and second.
The team carefully verified such details to ensure a faithful reconstruction with such limited information.
A joint monozukuri effort by young and old alike
One of the project’s aims was to nurture young people who will lead Toyota’s future car-making. As such, the trio turned to car production veterans for advice when manufacturing the transmission.
Lending them hands were Kenji Koumaru and Hiroyuki Tamesue of the Powertrain Manufacturing Fundamental Engineering Div., veteran engineers with over 30 years of experience in the field each.
Koumaru
I’ve been at Toyota for over 30 years. A young project member approached us in March 2021, saying that they want to make around 200 transmission and suspension parts. That’s how I learned of the Toyopet Racer revival. I had no idea such a machine existed 70 years ago. I thought, I have to lend a hand to such an amazing project.

Tamesue
That was also my first encounter with the Toyopet Racer. I was happy for the chance to work on an FR manual transmission again. I’ve been at Toyota for 30 years, 24 of which have been spent working on transmission prototyping. There have only been a few FR manual transmission prototypes in that time, including one for use in taxis. Even so, the mechanism is a foundational part of car manufacturing.
The cast-metal transmission case is the largest component in the transmission rebuild. Outsourcing this piece alone would cost several million yen. Making the mold in-house using the original methods would also be expensive and time-consuming.
The team instead used a 3D printer to create the mold, which will be featured in a future article.
Unexpected good fortune
The team had an unexpected stroke of luck after three months of work rebuilding the transmission parts; an original transmission had been discovered.
Asuka
Someone found another Toyopet Model SD engine and transmission. We decided to restore them, thinking they would serve as a textbook for the revival work. We weren’t sure if we had enough time to rebuild the transmission from scratch for vehicle testing, given the tight schedule. We can find certain things only through getting a car up and running, so we decided to proceed with the rebuilding and restoration in tandem to get the Racer test run-ready at an early stage.
The restoration work would also require specialized skills and expertise. Tamesue and the other Powertrain Manufacturing Fundamental Engineering Div. members gave a huge help to the team.
First, they had to dismantle the assembled transmission into individual parts. However, the interior was severely rusted, and a gear shaft refused to budge.
Ishida
You need expertise in which substances and techniques to use in removing rust. Tamesue not only taught us how to do it but also did much of the work himself.
Tamesue
The shaft had been press-fitted into the gears, so you can dislodge it with the right impact, but the three were too worried about damaging the part. I think they did a good job under the circumstances. We started out working by hand, but the shaft was so badly rusted that we ended up using machines.
It is a daunting task even to imagine. And yet, all the parts were cleaned and the original transmission completely restored, with extensive support from the Powertrain Manufacturing Fundamental Engineering Div.
Manual transmission rebuild, a first even for veterans
The rebuilt 70-year-old manual transmission was completely different from those of today both in structure and the shape of its components. Such manufacturing work was a first even for veterans like Koumaru and Tamesue.
Tamesue
I was involved in restoring the original, along with fabrication and assembly for the newly built transmission. To be honest, building the new one was the harder task.
Koumaru
What kind of metals should we use to fabricate the new gears and other parts? What kind of heat treatment would be needed to ensure strength? These were our first challenges. The old blueprints mentioned materials that are no longer in use. On top of that, the drawings didn’t include dimension tolerances. We needed to figure out alternative materials and dimension values.
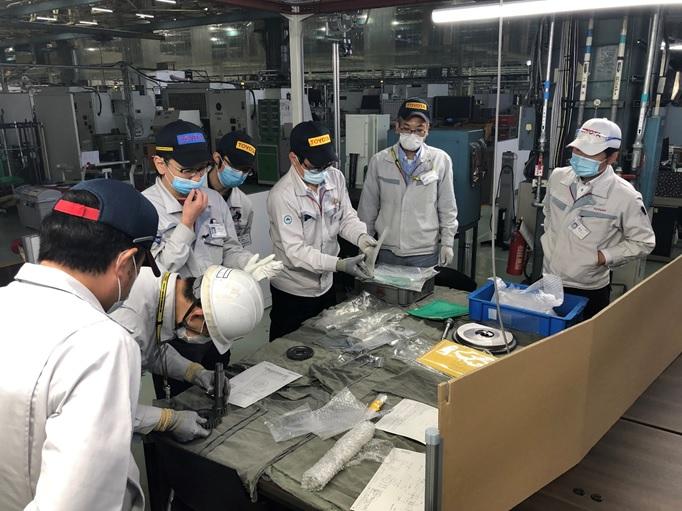
An unusual approach to making parts fit
Asuka, Honda, and Ishida worked hard in making the key components like gears and shafts with the help of other engineers. Only one Toyopet Racer was being rebuilt, which meant producing only one set of 200 different parts. None of the three had ever done anything like this before, and even for the two veterans it was a special experience far outside their usual work.
The trio decided to stick with generic parts for things like bearings, bushings, and oil seals as originally planned, undertaking a meticulous selection process.
They first had to verify the performance requirements of every part based on limited information from cross-sectional drawings. The team examined each one to determine whether generic parts could fit while considering the clearance between surrounding components. Such efforts allowed the team to procure generic parts for the components.
Finally, the three began assembling the transmission components they had designed and fabricated under Tamesue’s expert guidance.
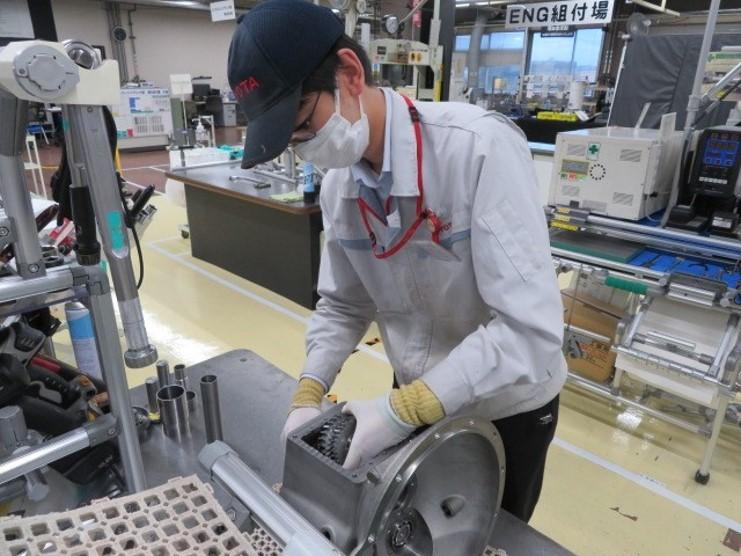
Tamesue
All sorts of things happened once we started the assembly work. We ran out of parts and had to quickly design and make them. Then, when we put the rotating parts together, we found they lacked clearance and couldn’t turn, so we had to grind certain sections down. We would never do this kind of adjusting process in our regular work.
Honda
We prepare parts drawings with dimensions and geometric tolerances for every component in normal design work, checking the clearance between parts and determining their positions in the assembly beforehand. When fabricating parts, we determine the dimensions of materials and molds in advance based on design drawings.
However, we took a trial-and-error approach on the production floor to get the dimensions right. You need to understand the part’s function and carefully check on details, by using skill and ingenuity to make necessary adjustments. I had an invaluable hands-on experience through that process.
The transmission team completed both the original restoration and the new construction.
Koumaru
The three seemed to be struggling a little when I first met them. I think they did a great job getting this far. I look forward to seeing what they do in the future.
Tamesue
I’m sure at times they wanted to give up with the many issues they faced. Now, they deserve a lot of praise for all their great work in creating something of this caliber.
To build is to learn
The trio reflected on their experiences and the lessons.
Asuka
We were each able to think through the situation ourselves and act, share knowledge, and help each other beyond our respective roles. This is because we were dealing with 70-year-old cars and drawings that even the veterans knew nothing about. I realized that this is how we work when creating something completely new.
The project also helped me connect with new people. Now I know who to call on next time I want to embark on a similar venture.
We could not have accomplished this work without all those people who assisted with the transmission fabrication and restoration. I’m truly grateful to all of them. And as I had hoped, I learned so much from thinking through every part of car development.
Honda
This revival project allowed me to learn the basics of monozukuri and gain valuable experience in designing vehicles from a holistic perspective. In particular, I realized anew the importance of manufacturing genba (worksite). Now I can imagine more the monozukuri process on the production floor.
I want to be a genba-oriented engineer who can think out of the box and design competitive products both in terms of performance and manufacturing.
I also learned the importance of designing each part with total vehicle development in mind. I will work hard to make ever-better cars with the same passion as our predecessors.
Ishida
I used to think that you could build anything if you had the blueprints. But now I realize it’s not that easy. You need to consider fabrication methods and understand details beyond the drawings.
Other involved divisions contacted me saying that they couldn’t make the design I’d drawn using the given materials and methods, so I had to research materials and production methods to answer their questions, and I learned a lot from that experience.
I was also struck by how people back then used simple mechanisms to achieve things that are now done with electronics. Their ingenuity amazed me. I now see the fundamentals of monozukuri.
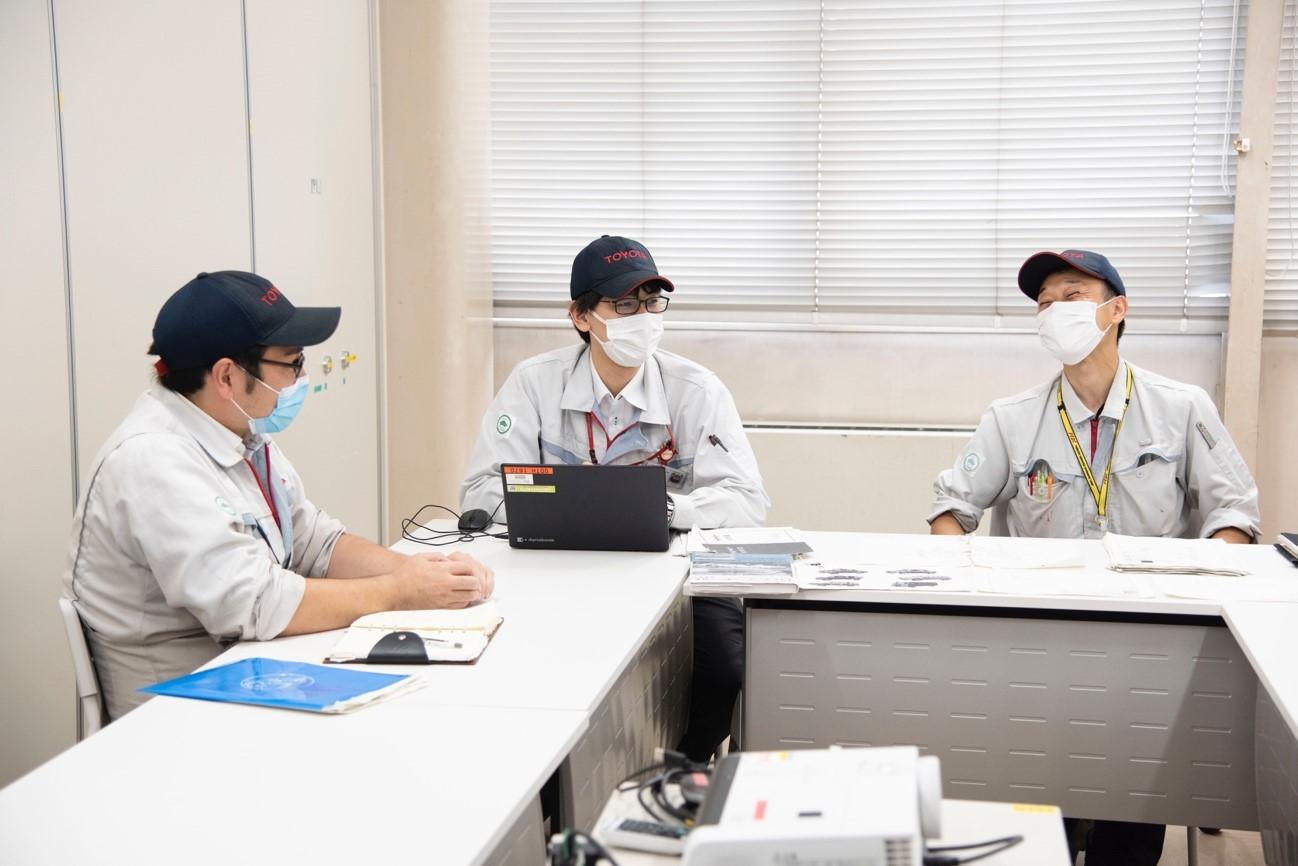
Stay tuned for the next story, which will focus on the engine restoration team.
(Text: Yasuhito Shibuya)