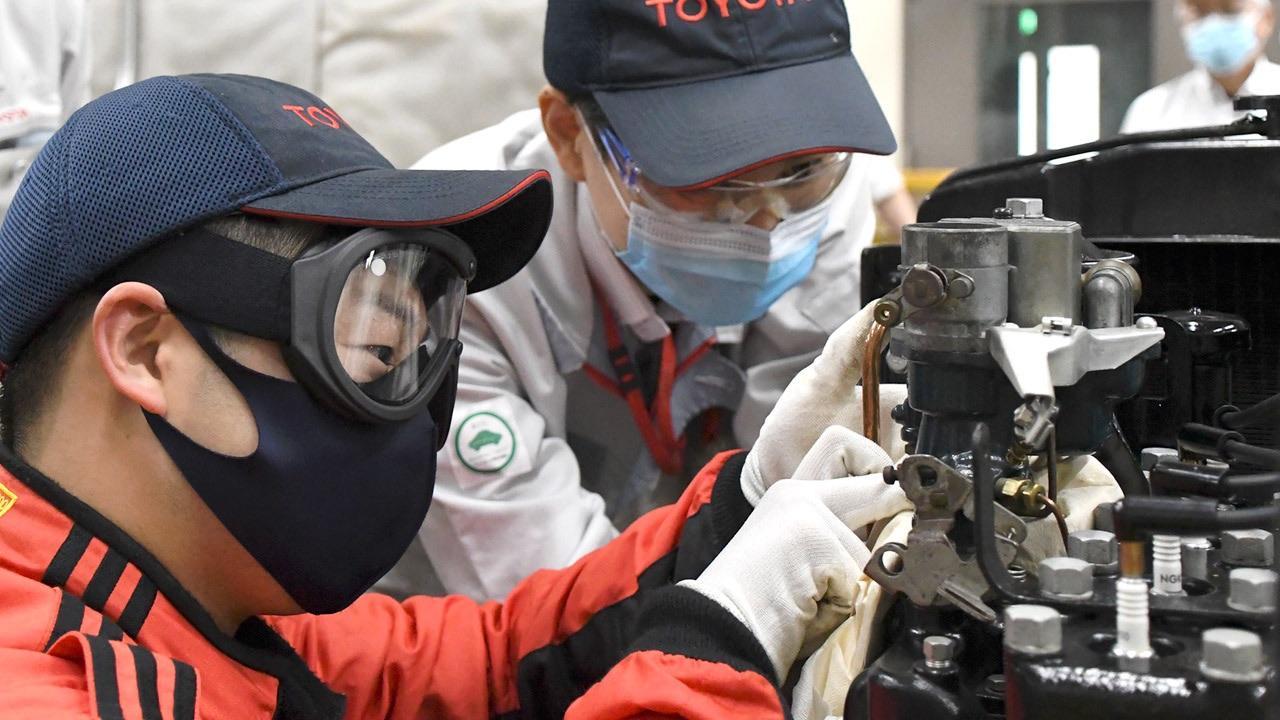
Toyota Times provides a series of articles featuring the project to revive Toyota's first racing car "Toyopet Racer", developed 70 years ago. This second part describes how the project team was formed inside the company.
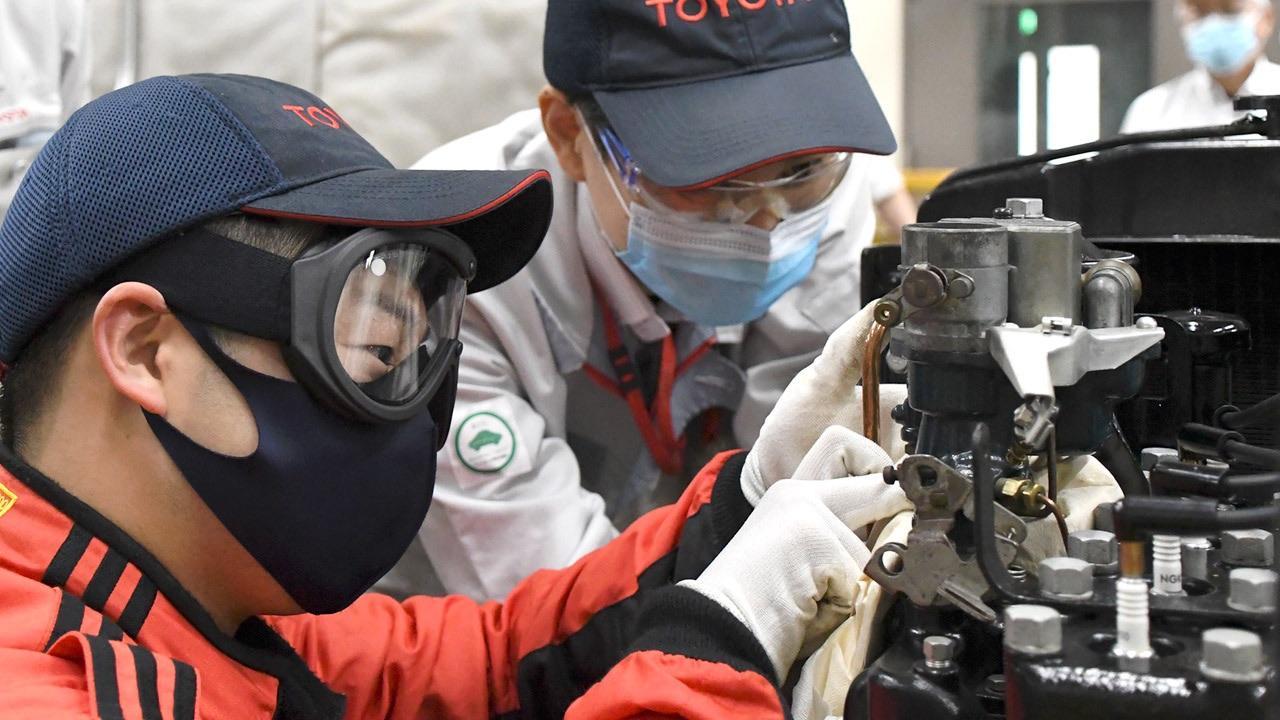
This series features Toyota’s project to revive a legendary racing car by reporting on the project members’ efforts as well as the history and meaning behind this vehicle.
Keiji Kojima, General Manager of Technical Development & Prototype Division, who together with project overseer Naoaki Nunogaki determined the basic parameters for the project and gathered together its members, was interviewed for this second article. He talked about the specific project policies, the reasons behind them, and the process leading to the formation of the project team.

Origins of “making ever-better cars based on motorsports”
The Toyopet Racer represents the origins of President Akio Toyoda’s vision to “make ever-better cars based on motorsports.” Starting the planning in the autumn of 1950, the car was completed in spring 1951. The idea of bringing back to life this legendary racing car, not just as a show car but a car that runs as it originally did-this project was officially launched in May 2020 after Akio approved the plan.
Nunogaki approached Kojima about how to select members and the specifics of moving the project forward.
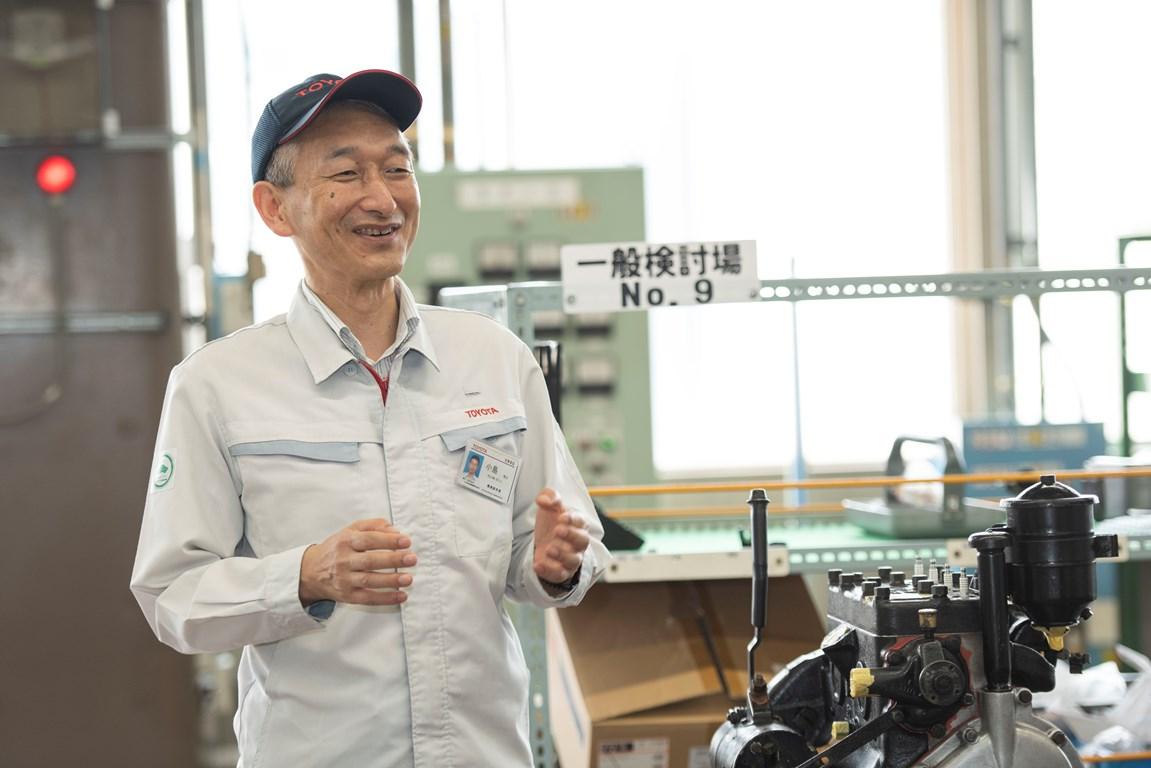
The main job of the Technical Development & Prototype Division that Kojima oversees is to manufacture prototype vehicles from base materials like steel sheets, so that they can be used in the various tests necessary to commercialize vehicles. The technical skills, experience, and cooperation of this team of prototype professionals would be absolutely essential when seeking to revive the racing car.
Nunogaki and Kojima are friends of 20 years. However, they hadn’t met each other in a long time.
Kojima recalls: “When Nunogaki came to me saying, ‘I want to revive the Toyopet Racer, will you help?’ I had never even heard of such a vehicle. It wasn’t until I read Toyota Motorsports Zenshi – Toyopet Racer, Goshu Isshu Rally-wo Chushin-toshite (Early History of Toyota Motorsports – About Toyopet Racer Centered on the Round Australia Rally) published by Miki Press in 2018, that I realized with surprise that it had existed, and that our team could play a role in bringing it back to life.”

Hearing from Nunogaki that, “There are hardly any materials about the mechanics of the vehicle, other than photos and internal magazines,” Kojima says that he thought then that this would be an unprecedented monozukuri (manufacturing) and car making project, and something even the veterans of Technical Development & Prototype Division had never experienced before.
“We would be creating something from scratch, which makes it incredibly difficult. Even so, it was a really interesting challenge. I was absolutely convinced that we could do it, because all the technicians in our division can make almost anything. They’re particularly skilled at bending and beating steel sheets to form shapes. However, what posed the biggest challenge was the engine. It’s difficult to create an engine from nothing. I also thought that it would be a tough challenge to manufacture parts other than the body, like the chassis,” says Kojima.
Fortunately, the Toyota Automobile Museum had an S-type engine in its collection, but after disassembly and inspection, it was found that the internal engine components would not work without restoration. Other major components such as the suspension, front axle, transmission, body, and seats, would all have to be built from scratch.
“Even so, I absolutely believed that we could get it done if we brought the right people together. I wasn’t too worried.”
An opportunity to develop human resources to support the Toyota of tomorrow
Needless to say, the main mission of the project was to bring back to life the Toyopet Racer in its original form.
However, another aim of the project revolved around Toyota’s future. This was to nurture the young people who would perpetuate the spirit of the people who had created this machine, and take Toyota’s monozukuri (manufacturing) and car making into the future.
“At Toyota today, in pursuit of efficiency, all processes are thoroughly divided up. That’s why every division is only involved in a small part of each vehicle, which means there are hardly any opportunities to get involved in every process of car making from start to finish. It is difficult these days to develop all-round car engineers who understand the entire vehicle, and who can look at the vehicle as a whole, before thinking about and deciding what to do with the individual parts and functions,” Kojima explains.
Due to the scale of production, a generation ago monozukuri (manufacturing) and car making became segmentalized, with processes becoming detached from one another. If such a situation were to be left unchecked and most engineers eventually only understand the specific part of the car that they are in charge of, it will become difficult to develop a good car. A collection of good components created with only those individual components in mind will never result in a good car. Only with good components that are designed based on an image of the overall vehicle is it possible to create a truly good car. That is why Akio introduced an in-house company system, shifting the company’s organization to a product-based one, and changing the way the company makes cars.

In this project, although the manufacturing of components would still be done based on division of labor, from the point where those components are assembled through to driving tests, all members would be able to be involved in every aspect of car making from beginning to end. It was expected to provide a perfect opportunity to develop “car engineers.”
It was from this perspective that Nunogaki and Kojima decided to assemble a team of mainly younger members.
“Hand-crafted” monozukuri without over-reliance on machinery
The two also set out the major guiding principles of the project from the perspective of nurturing car engineers.
Firstly, the work of making and adjusting components would be done mainly by hand, using only tools that were available at the time as much as possible, and without relying on machines. Also, the team members would basically take charge of jobs that they had never before experienced.
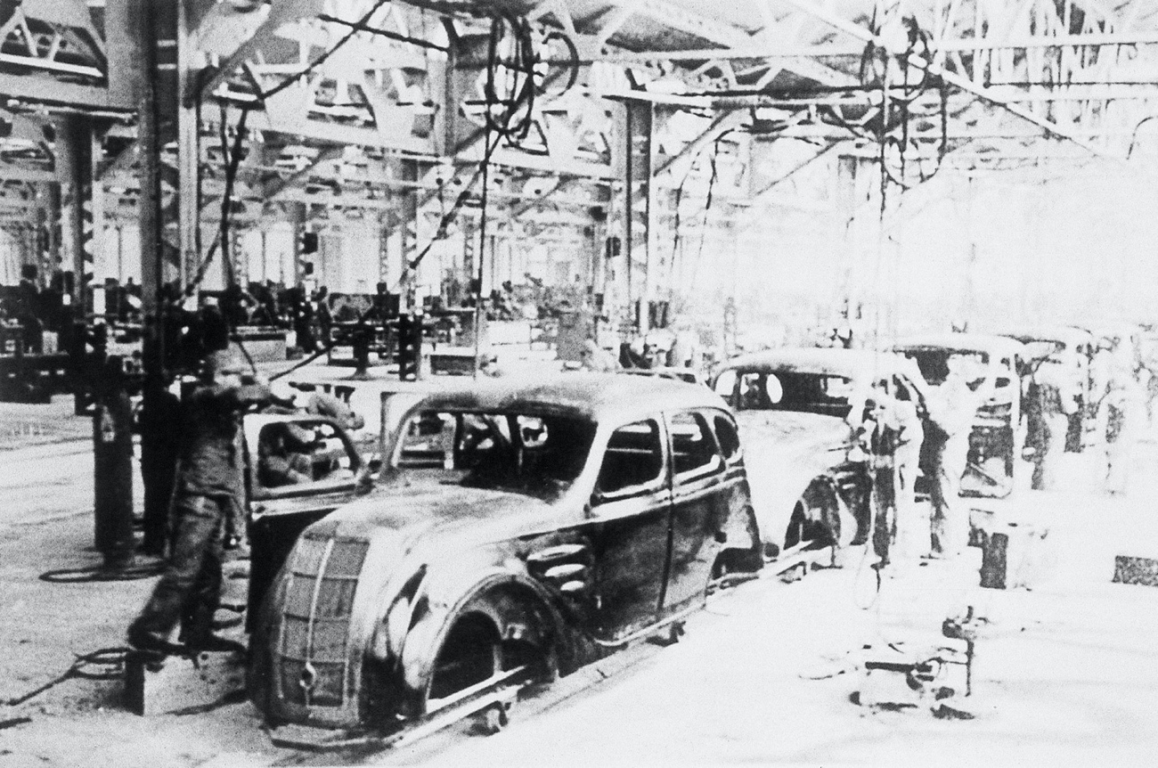
“Using the latest computer-controlled machine tools makes it easy to produce components quickly and accurately. But making something in that way wouldn’t bring us any closer to the ideas and difficulties experienced by people back then, who were making things mainly by hand. What I wanted to do was to produce something using tools and methods from that time as much as possible, and in so doing rediscover what we have forgotten because of the useful tools that are available today, and retrieve these forgotten skills to pass down to future generations,” says Kojima.
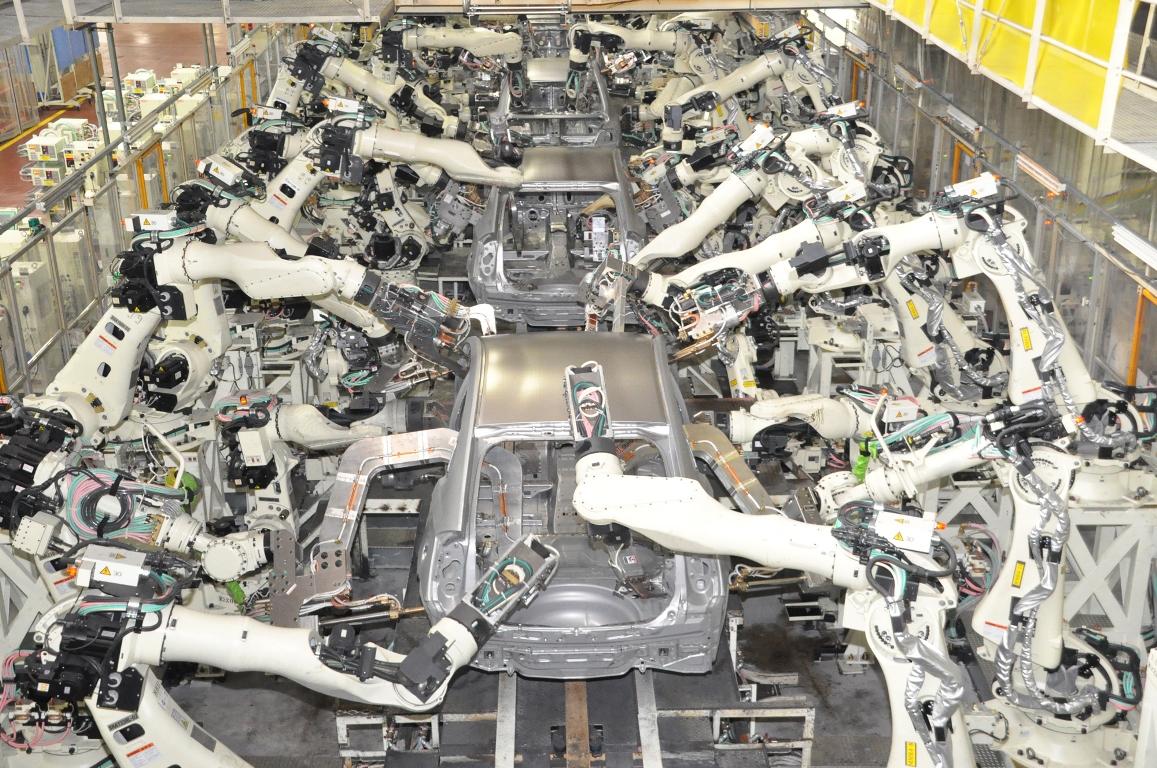
Executive Fellow Mitsuru Kawai is someone who worked his way up through the company to the position of Executive Vice President, never losing sight of the genba workplace, and who now has the title of “Oyaji,” or “Old Man” within the company. It was Kawai who had previously sounded the alarm, noting that “manufacturing is over-reliant on mechanization.”
“Today’s car making that relies on machines is heading in the opposite direction to the principles of monozukuri. If you don’t have any kind of feeling for hand-crafted monozukuri, you won’t know what’s going on inside a machine when something goes wrong, nor will you know how to solve the problem. It was out of just such a sense of crisis that when he was Executive Vice President, Mr. Kawai launched the initiative of ‘passing on defining skills’ to young employees. Nunogaki and I thought that this project would be a fantastic opportunity for young employees to go beyond division-based boundaries and experience and inherit various defining skills themselves,” explains Kojima.
The people who originally made the Toyopet Racer utilized materials and tools at hand to the maximum extent, creating something from zero out of sheer ingenuity. The idea behind this project is to recreate the monozukuri of that time and regain the lost feel for monozukuri.

Kojima says, “I wondered how it would turn out when today’s young team members tried to reproduce the original monozukuri techniques. It was a challenge that truly piqued my personal interest. I imagined that we would have a difficult time, but I was sure that the experience would be useful for the future of monozukuri.”
Motivated young employees assemble from around the company
So, with the project’s aims and goals duly set out, Kojima started gathering team members. He sent out an open recruitment call to all divisions for motivated young employees in their 20s and 30s. He also requested understanding and cooperation from management, asking managers to recommend young employees who would benefit from participating in the project.
On this project, a team was formed with a mix of members from the development side, involved in design and testing, and from the production side, who were responsible for production technologies and manufacturing. Usually work is divided into up- and downstream processes, and there are not many opportunities to work together on a project in the same capacity.
“Regardless of whether they are from development or production, each team will do their assigned task. Everyone has the same role, and by working together they should be able to learn from each other too.”
After a selection process in each division, 15 young employees were picked for the project team, mainly from the Production Engineering Development Center, Vehicle Development Center, and Powertrain Company.
“Oyaji” and “big brothers” take on support roles
In addition to selecting young team members, Kojima also set up a thorough back-up system to provide them with the necessary support. He first called on the veteran members of his own Technical Development & Prototype Division, asking them to provide guidance and support to the young team members.
“When I thought about the hand-made nature of this monozukuri project, I realized that we would need the cooperation of a genba veteran like Assistant Manager of Prototype Body Production Section, Eisuke Yoshino (introduced in “Masters who support car making in Japan” #4), so he was the first person I turned to.”
Ultimately, including Yoshino, with his expert skills in sheet-metal working and welding, a total of five “oyaji” were called upon to help, including professionals in chassis design, testing and evaluation, and casting, as well as the chief engineer who oversees all aspects of production car manufacturing.
In addition, Akira Ichikawa and Yuki Fujiwara, also from the Technical Development & Prototype Division, acted as support members, working in the project office as “big brothers” to the team.

Advisors and “big brothers” to team members. From left, Akira Ichikawa, Yasushi Kato (of Production Engineering Development Management Division in charge of launching the project), and Yuki Fujiwara.
There was also the reassuring presence of collaborators from outside the company, including Minoru Ishikawa, a legendary automobile mechanic from Shinmei Industry Co., Ltd., known for his restoration work on Toyota vehicles and considered to be a “walking encyclopedia on old Toyota vehicles.”
A last chance for everyone
“If we had started this project 10 years from now, I don’t think we could have done it. Today there are still dependable supporters both inside and outside of the company. We successfully grasped this last chance to do it while we still can.”
These are Kojima’s thoughts as he looks back on the project.
Then, on November 19, 2020, all 15 team members, the “big brothers” and “oyaji”, met together for the first time in a meeting room at the company. It was the first time for most members to meet each other, and initially they didn’t even talk to each other.

The members were formed into five teams, including engine, and body and frame teams. Finally, the revival project was ready for lift off.
Look out for the third part of this series, which reports from the revival project worksite on the various struggles faced by team members.
(Text: Yasuhito Shibuya)