
Toyota Times uncovers the essence and core strength of the traditional Japanese monozukuri, which is woven from the past into the future. The third interviewee is a master of forging.

While many people pay attention to advanced technologies such as 3D printers and AI when it comes to making something new, there is a lot of manual handiwork remaining in the front lines of car manufacturing.
In this series, by interviewing some of the masters supporting Toyota’s manufacturing with their craftsmanship, Toyota Times uncovers the essence and core strength of the traditional Japanese monozukuri (making things).
The third interviewee is Toshio Ando, a master of forging.
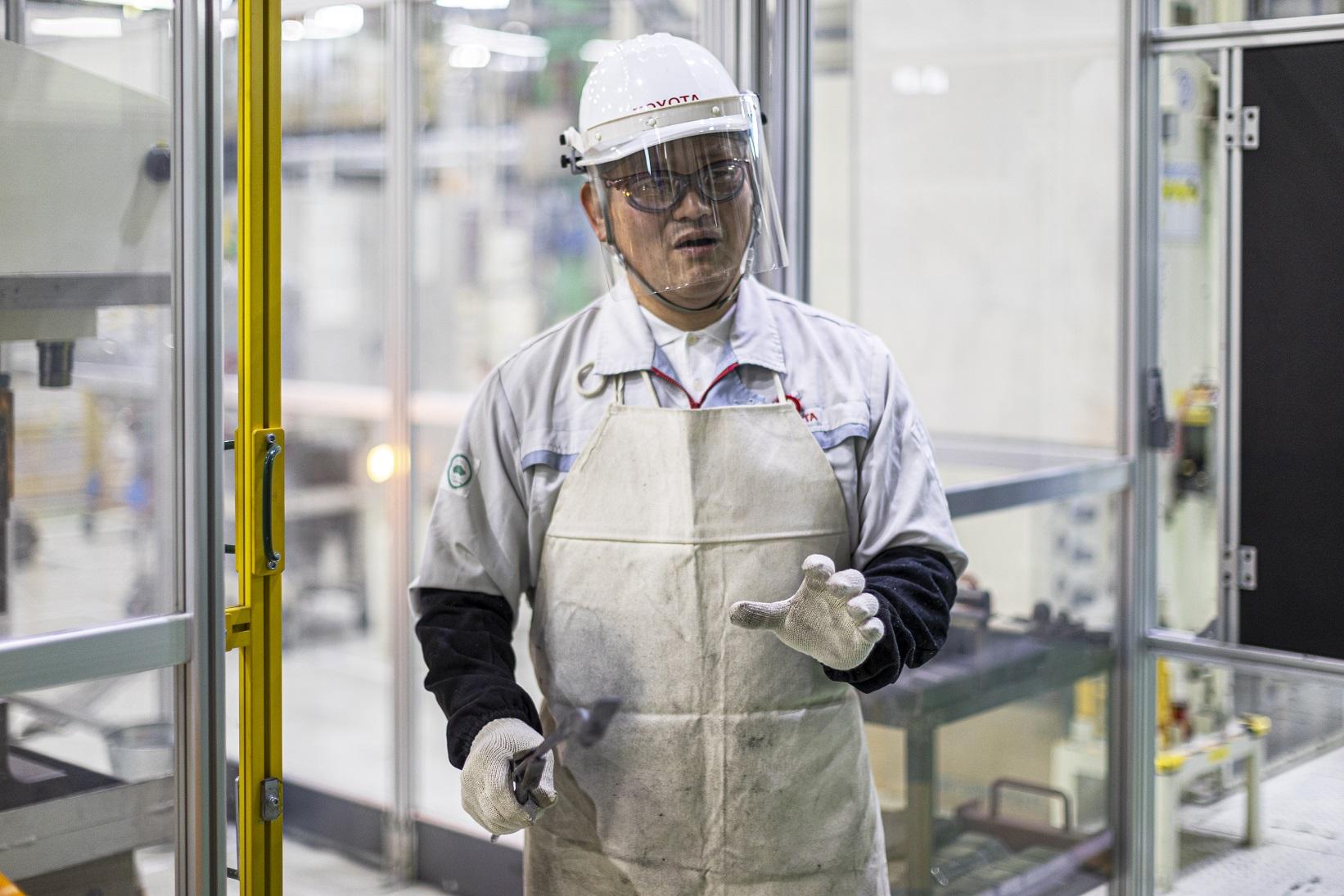
Series #3 Toshio Ando, a master of forging who understands the “feelings” of iron
Senior Expert (SX) at Powertrain Administration Dept., Powertrain Management Div., Myochi Plant, Toyota Motor Corporation.
Toyota’s blacksmith
Toshio Ando was born on in 1968 in Toyota City, the hometown of Toyota. After graduating from high school and joining the company in April 1987, he has mainly worked as an expert in prototyping and production preparation since being assigned to the 5th Production Engineering Division, which handles parts manufacturing by forging.
Along with casting, forging is one of the oldest metalworking techniques. Metal is heated until it becomes red-hot, and then molded to the desired shape with a one-handed hammer. It’s basically the work of a blacksmith. Until about half a century ago, there were blacksmiths in every town and village, who sold handmade iron tools, such as kitchen knives, scissors, sickles and plows. However, blacksmiths are rarely seen nowadays, and not many people know what a blacksmith is anymore.
According to one theory, the history of iron forging dates back to the Hittite people who invented ironware in Asia Minor in around 1700 BC. Heating and hammering vastly transforms the structure of metal. Metal crystals are compressed and density increases as the crystals become tightly packed. The direction of the scattered crystals is also transformed as they fall into regular alignment like the grain in wood. This line is called a metal flow (forging line), and the strength of the metal increases significantly along this direction. Impurities and carbon trapped inside the metal are released by hammering while also transforming the metal’s properties. Forging is also a method of making metal harder, more impact resistant and durable. There is also a method called cold forging that affords high precision by hammering the material without heat.
“I am the blacksmith of Toyota. Most people may not know this, but there are parts of a car that can only be made by forging. Therefore, the work of a blacksmith is indispensable.”
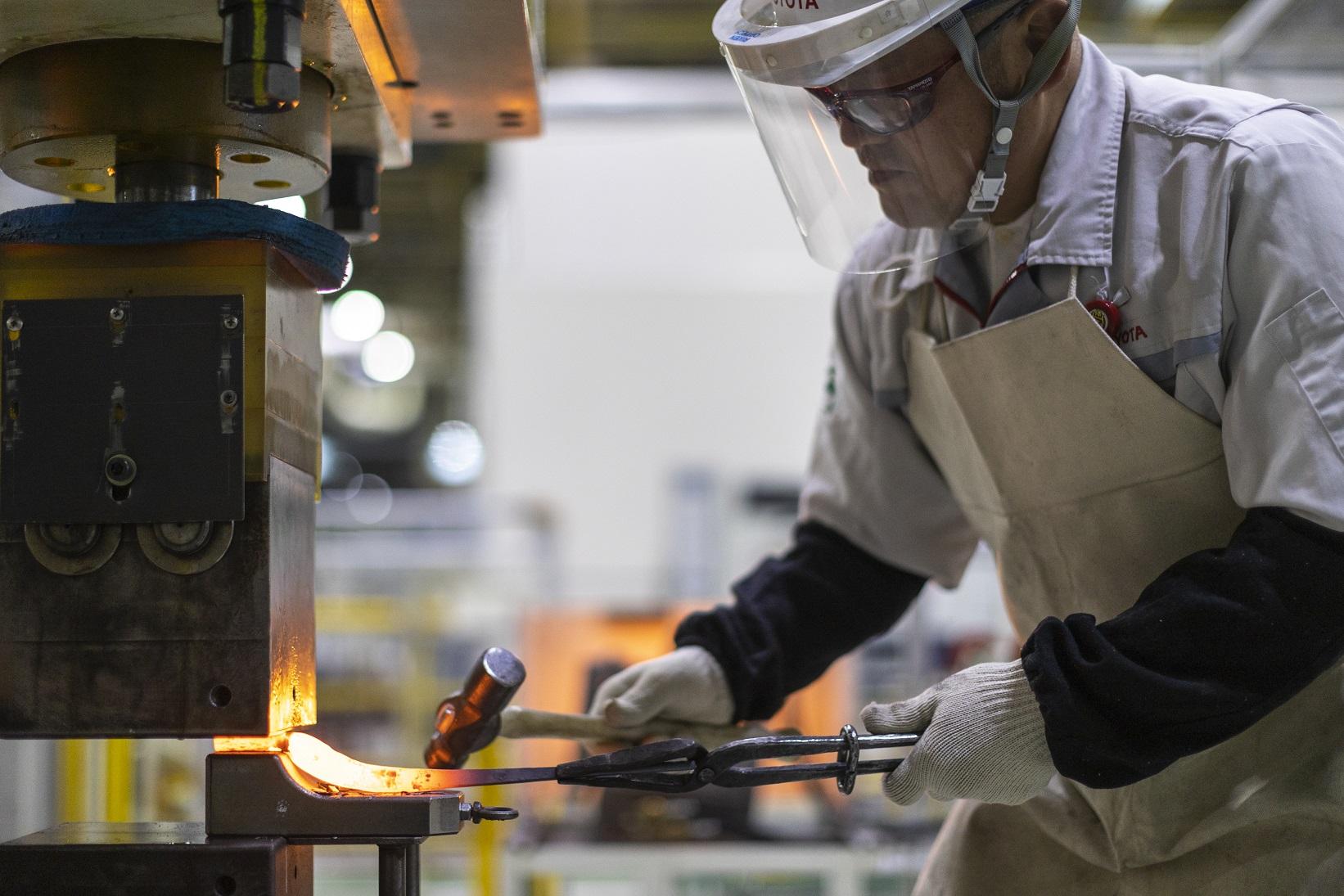

As a master of forging, Ando is currently leading the forging training program at the training center in the Myochi Plant, which begins with making things from metal materials using only a hand-held hammer. He is passing down the splendor, difficulty and depth of forging to his juniors.
Forging that is indispensable for car making
Cars run on the energy generated by the explosive combustion of gasoline and air in the cylinder of an engine. Great force is constantly applied to engine parts, including the connecting rods and crankshaft, which receive this force and converts it into rotational motion. The same applies to parts of the transmission, such as the transmission gears that transmit this force to the tires, and the suspension parts that support the tires and absorb the force from the road surface. Additionally, these parts must never break. If they do, it immediately results in the inability to drive or a traffic accident. Therefore, they need to be built sturdily.
Forging technology is indispensable when manufacturing such important parts. As part of car making, Toyota has been engaged in research and development of this technology, and training engineers since the company was founded more than 80 years ago.
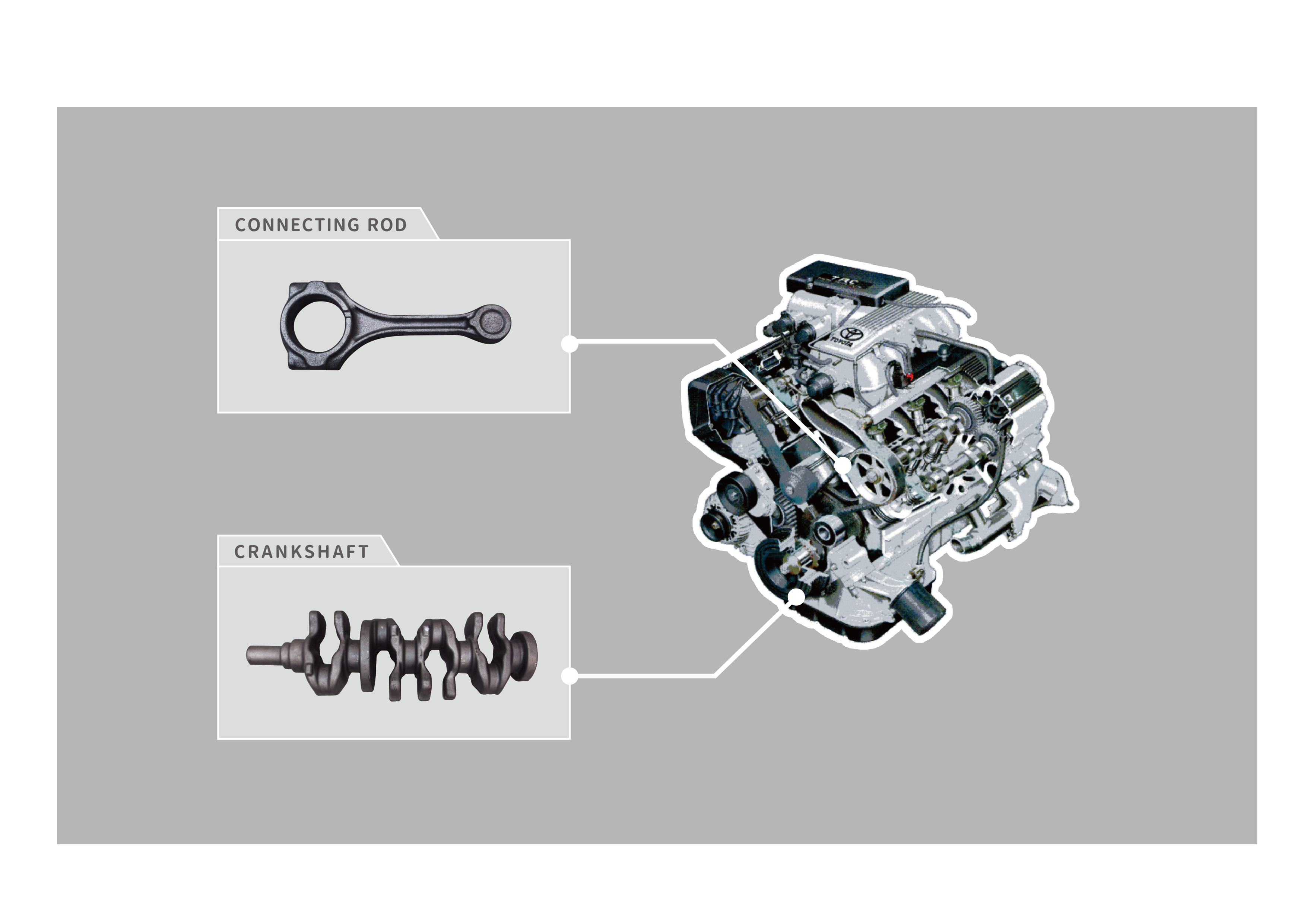
The forging division of Toyota was established in January 1934 as part of the Steel Production Department of Toyota Industries Corporation, which was responsible for R&D of steel products for automobiles. Records show that a steam-powered forging machine imported from the U.S. was installed here. Also, in November 1938, production of forged parts began at the Koromo Plant that was established at that time. According to the materials of the Toyota Commemorative Museum of Industry and Technology, the Koromo Plant had three steam-powered free hammers (press machines) of 1/2 ton, 1 ton and 2 tons. It is said that four people were involved in making parts by free forging without any molds.
Toyota is a pioneer of modern industrial production by forging, and Ando is one of the few who inherited its history and defining skills.
The path from judo to forging
Ando loved disassembling things when he was a kid. He also loved cars. However, his love of cars wasn’t the reason why he joined Toyota.
“I'm from an ordinary high school. I became the Aichi Prefecture judo champion and entered the company on a sports recommendation. However, I was seriously injured during practice just before joining the company. Because of this, I was told that it would be impossible for me to continue my career in judo.”

For Ando, who dreamed of a future in judo, this must have been a devastating setback. However, if it couldn’t be judo, Ando decided to master forging.
“While other new employees who had joined the company at the same time had acquired practical training experience in forging at technical high schools, I knew nothing about forging. It was actually unheard of for someone from the general course to be assigned to this division.”
There was no point in being there if you couldn’t do the job, and Ando wanted to be able to do the work. This is when Ando realized that he first needed to learn how to do the job.
“I hate to lose. Being told that I was not good at it actually fueled my ambition to do better. I wanted to prove them wrong by overtaking my seniors with my skills. With that in mind, I worked hard on acquiring my skills.”
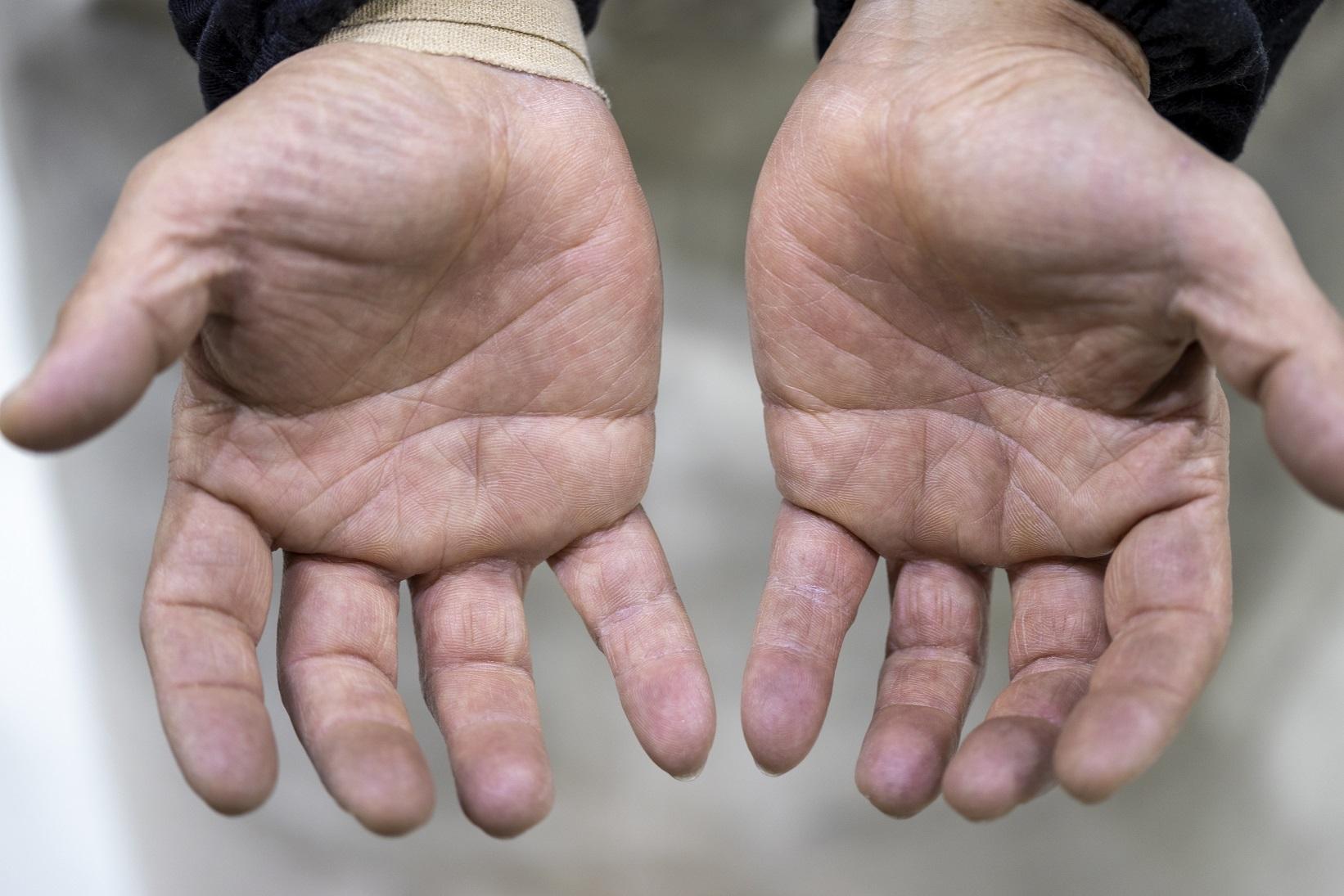
How Ando became fascinated with forging
Of all the Toyota manufacturing sites, the forging division was once said to be the toughest place to work. People called it the “3K workplace,” where 3K stands for kitsui, kitanai, kiken in Japanese, meaning “grueling, dirty and dangerous.” Metal was heated to the point of being bright red-hot, and hammered loudly many times with tons of force by a press machine or a hand-held hammer. This inevitably created a harsh work environment.
Mitsuru Kawai joined Toyota after graduating from junior high school, started at the forging site, climbed his way to become Vice President and currently holds the position of Toyota Executive Fellow. He stated in an interview for a business magazine, “The forging division was the only one I didn't like when I joined the company because it was so grueling. When I got assigned there I seriously thought about quitting.”
Meanwhile, Ando was fascinated by the wonders, joys and depth of forging as he spent his days receiving guidance from his seniors, who handcrafted various prototype parts using their experience and intuition.
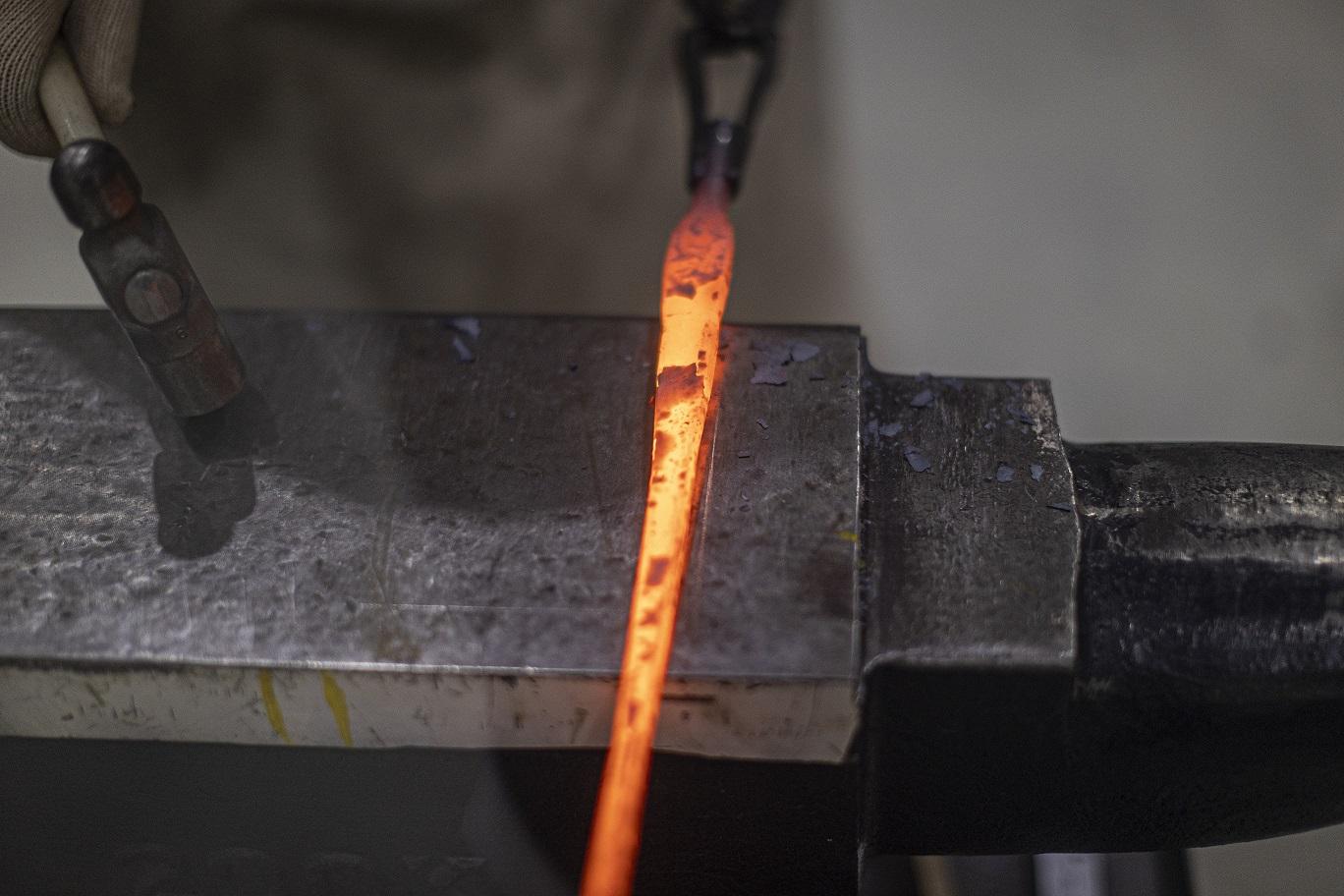
“Heat enables hard metal to be molded into any desired shape. Hammering also strengthens the metal. This is impossible with other technologies, such as cutting and casting, so many parts can only be made by forging. When I was building a new car and forging was selected as the method for making parts, I felt very proud.”
It was also Ando's job to prepare for production in cooperation with the design division to manufacture low-cost, high-quality parts by forging. Could this structure be made by forging? What kind of shapes or procedures should be used to make manufacturing easier? Ando's knowledge and ingenuity make Toyota cars better.
Especially now when everything is becoming automated...
Nonetheless, Toyota has been actively promoting mechanization and automation of forging work ahead of other companies. For example, in 1964, four years before Ando was born, Toyota introduced a U.S.-made automatic forging press for the first time to manufacture connecting rods, which are one of the main parts of an engine. Today, many forged parts including crankshafts are manufactured by integrating fully computerized automated machines handling everything from material input to finished products. Thus, the 3K workplace is a thing of the past. However, Ando talked passionately about the importance of passing on the defining skills of manual forging to the future, especially now that everything is becoming automated.
“The most ideal conditions for forging metal, including material temperature, mold temperature and film lubricant, are called in the forging process. These conditions are a sort of tacit knowledge that goes beyond words or manuals. In other words, something that can only be learned by actually intuiting and experiencing the process. The instincts for monozukuri work done by hand is essential for all craftspeople involved in monozukuri, especially now that so much of the work of forging is fully automated. How does the material change its shape in a machine? You must be able to visualize this to solve any issues that arise.”
These thoughts of Ando’s are based on the “spirit of monozukuri'' espoused by Mitsuru Kawai, who was the genba leader when Ando first started the job. The “forging dojo” of the Myochi Plant was established based on this spirit. This plant is also a place to educate and pass on manual skills and knowledge not only for forging, but also for other defining skills, including woodworking and casting introduced in the first and second parts of this series. Ando is passing on both the defining skills for forging and the philosophy behind it to the younger generation.
Understanding the “feelings” of iron
Ando demonstrated a training technique done only by forging experts called free hammering. One-hand hibashi, long metal chopsticks (for handling charcoal, especially in a brazier) are made out of round iron rod using only a one-handed hammer and an air drive free hammer without any kind of metal molds.

Dressed in working clothes, thick industrial leather gloves, a helmet and thick safety face shield, Ando beats the glowing red iron rod heated with a gas burner to over 1000℃ with a free hammer and a one-handed hammer while holding it in place with a metal tong. The iron rod then morphs into hibashi just like magic. All of this work was done freehanded.

Ando silently and constantly communicates with the material while he’s working. He can tell the temperature of the material just by looking at it, and only using his bare hands, he molds the material to his desired shape in the most efficient order and timing using the perfect amount of force.
“To achieve exceptional monozukuri by hand forging, you must sharpen your five senses to consistently feel the material’s temperature and amount of change, and think constantly about how to mold the material into the desired shape as you work on it. This is the only way to master the feel for the forging process.”
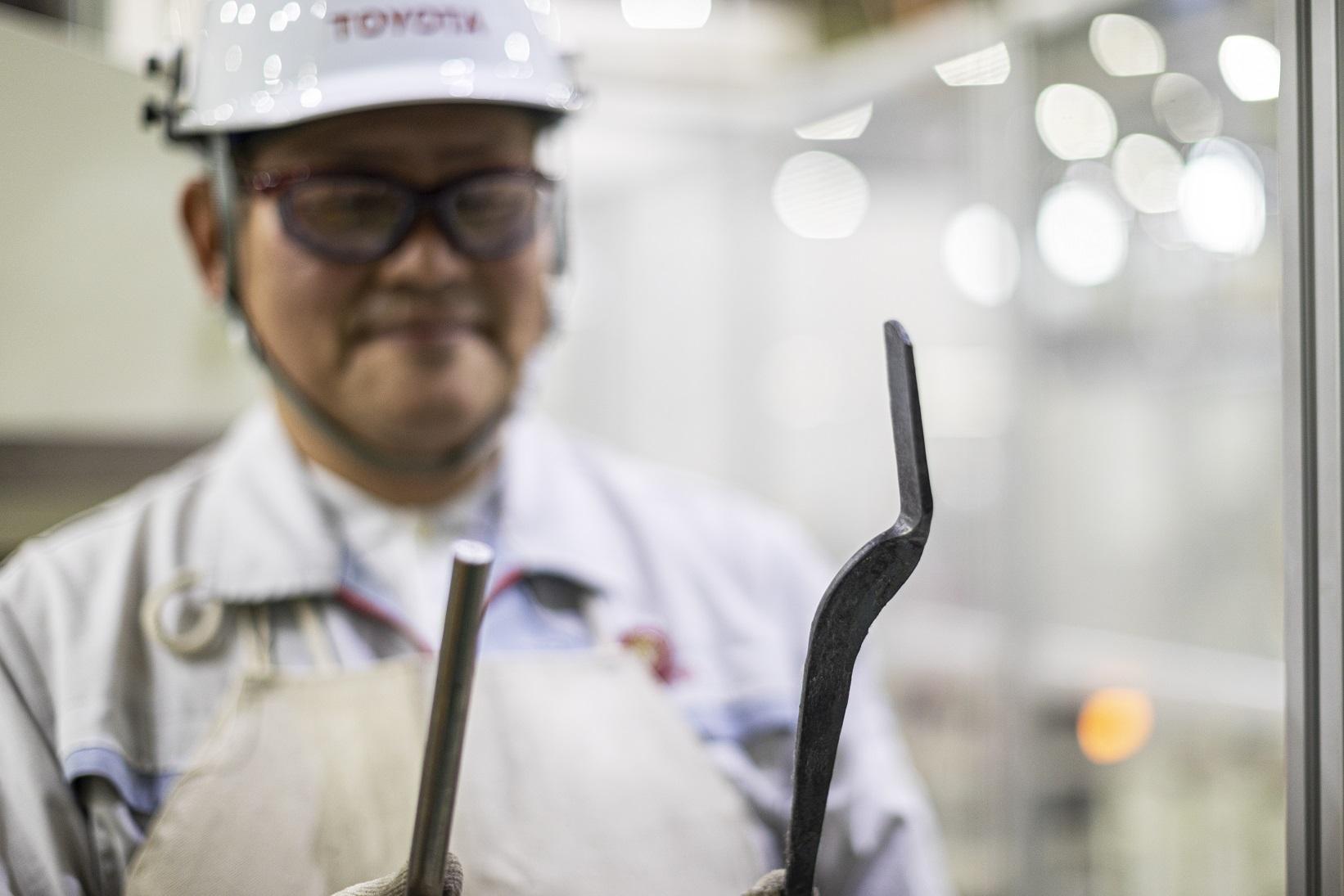
Ando calls this sensibility the “feelings” of iron. One cannot achieve the ideal monozukuri without understanding the feelings of the material. We can say that this is an important sensibility that is common not only for forging but to all skilled craftspeople.
“I often tell my students to understand the ‘feelings’ of iron. I am always thinking about the feelings of iron. That said, even after more than 10 years, I still don’t quite understand the feelings of aluminum. As cars become electrified and lighter, we’re definitely going to see more aluminum and other new materials. I’d like to learn and understand the feelings of aluminum and other new materials too.”
Ando passes on the tacit knowledge of forging that is crucial to car making and adapts to new materials. He also pushes to take the skills and production to the next level by making tacit knowledge more explicit. The forging master’s challenges continue today.
(Text: Yasuhito Shibuya, photo: Akira Maeda)