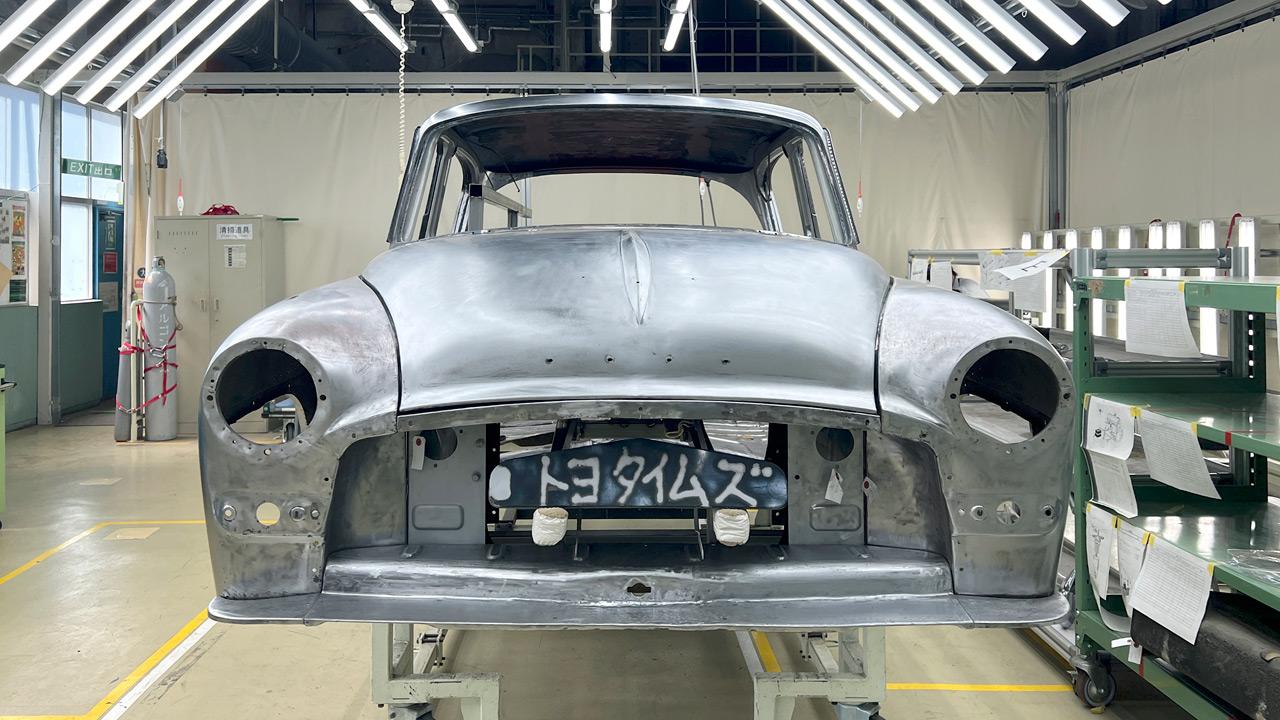
This series explores the project to restore a first-generation Crown, a car that embodies Toyota's origins. Part 4 covers the body restoration and special coating process designed to keep this cherished car on the road for decades to come.
65-year-old car meets modern electrodeposition coating
As mentioned at the outset, within the painting process, the team undertook a groundbreaking experiment that will play an important role in efforts to make existing cars carbon-neutral: the introduction of cationic electrodeposition coating for the body and chassis.
Cationic electrodeposition coating is a basecoat technique used on all current vehicles, not just Toyota cars. The technology involves submerging metal parts in a tank of dissolved water-soluble paint, then applying a direct current with the submerged part acting as the negative pole and the paint solution as the positive. Paint on the metal’s surface is transformed into an insoluble polymer, coating the part without the slightest gap.
This technique makes it possible to coat every nook and cranny, even in areas that are unreachable when painting by hand, such as rocker panels and the inside of chassis frames. What’s more, because the metal surface is completely covered at the molecular level, the risk of rusting can be eliminated so long as the coating is not damaged. However, applying the coating requires a paint-filled pool large enough for the entire body to be submerged.
Ideally, the team could make use of the production line for a current model, but the process is fully automated and not set up to handle odd jobs. And since the 65-year-old body was not designed with electrodeposition coating in mind, there was no guarantee that the attempt would not cause paint quality issues for the entire line of cars that came after.
As an added hurdle, a purpose-built jig would be needed to take the first-generation Crown down a production line for current models, costing upwards of ten million yen. For these reasons, no coating line could be found to perform the process in-house.
Regardless, the team was undeterred. They believed cationic electrodeposition coating for the body and chassis was absolutely essential to keep the Crown running in top shape for another 50 or 100 years, and to fulfill the wishes of car lovers eager to keep their beloved rides on the road.
One of those team members determined to make cationic electrodeposition coating work was SX Kinji Tomiyasu.
Tomiyasu
Like the Crown, the Publica we restored earlier was badly corroded, particularly on the underbody, and I experienced firsthand the difficulty of removing and refurbishing it completely. Frankly, there were areas where our knowledge and skills at the time fell short, which was frustrating.
On the other hand, for the Crown restoration we were able to assemble skilled technicians from across the company and really sink our teeth into the challenge of high-level restoration. Above all, the owner who entrusted us with his Crown had high expectations for the project, saying, “I’m sure the car will come out looking even better than new!” We didn’t want to simply restore it, but to create a Crown that can be driven for many years to come.
Toyota Housing helps make cationic electrodeposition coating a reality
The team members scoured every corner of Toyota, looking for someone who was doing cationic electrodeposition coating. Finally, they came upon a group company eager to take up the challenge: Toyota Housing, which develops and builds homes, offices, and commercial facilities.
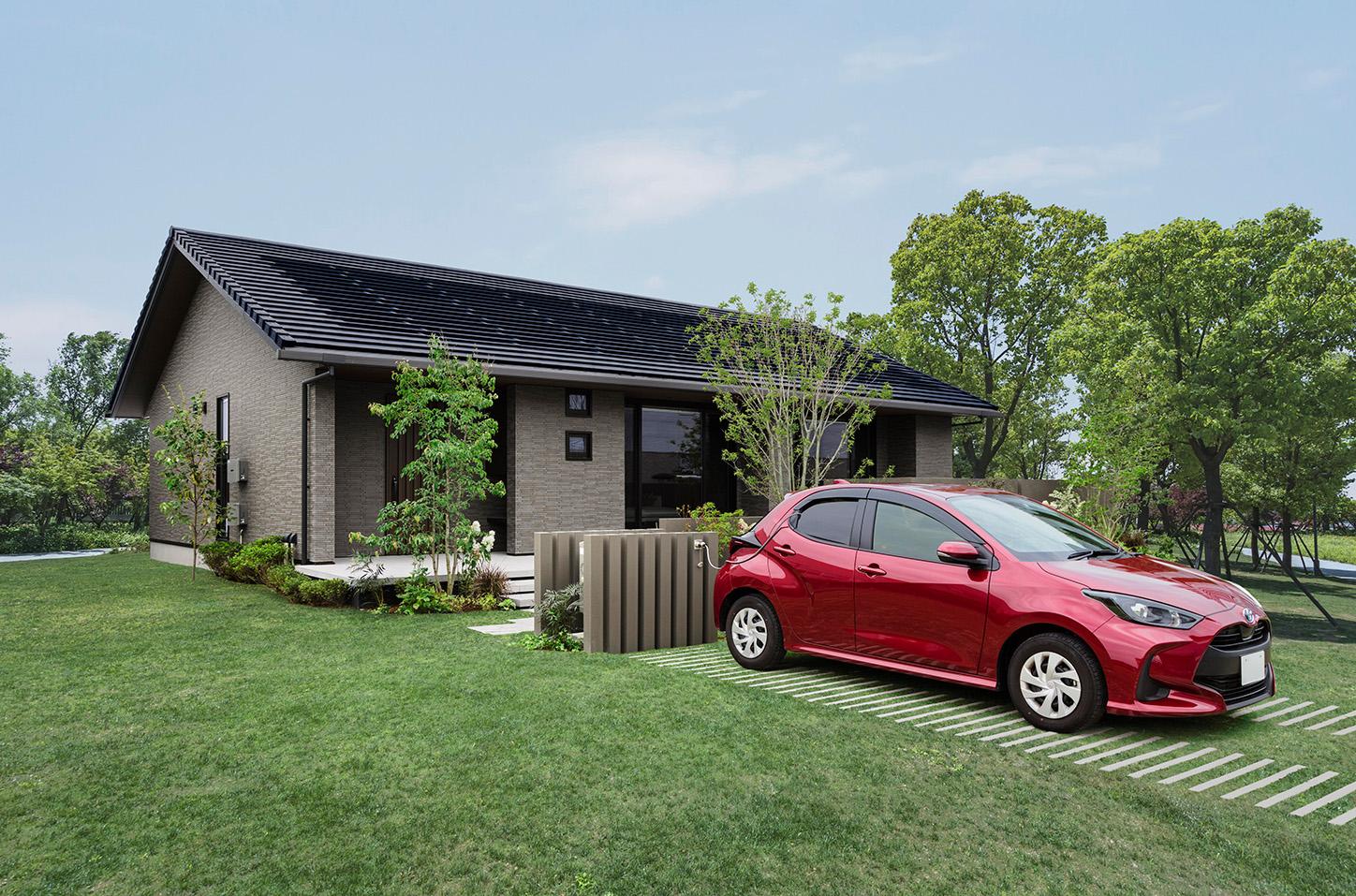
Toyota Housing started out in 1975 as the Housing Division of Toyota Motor Co. before being established as a Toyota Group company in 2003. The steel rigid frame units that serve as the company’s housing frames were originally born out of car-making technology. As it happens, these frames are also treated with cationic electrodeposition coating.
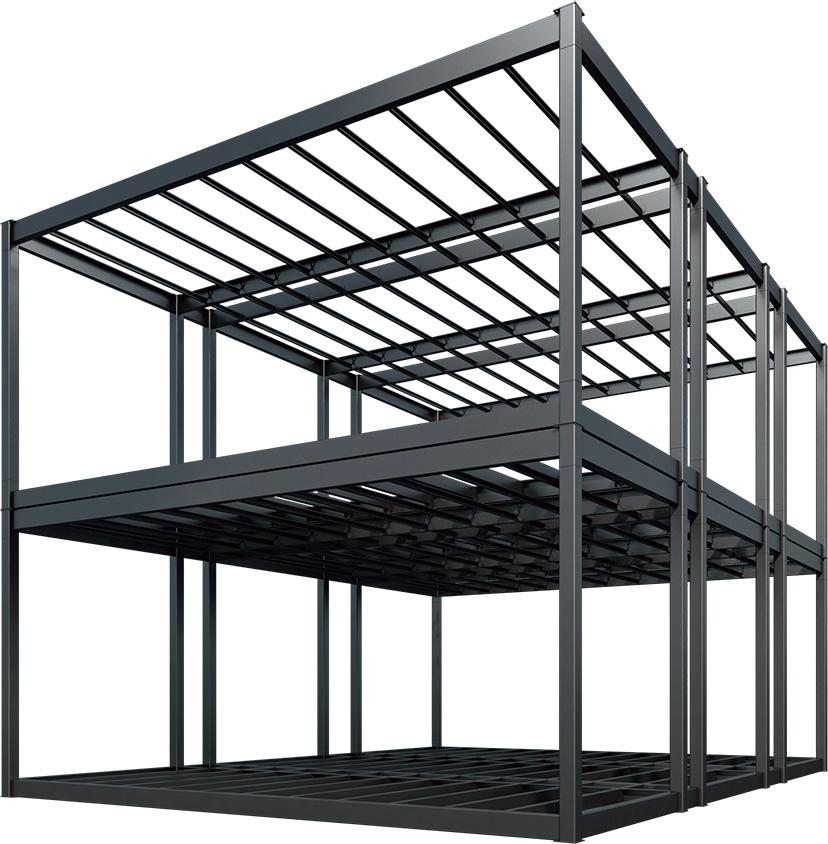
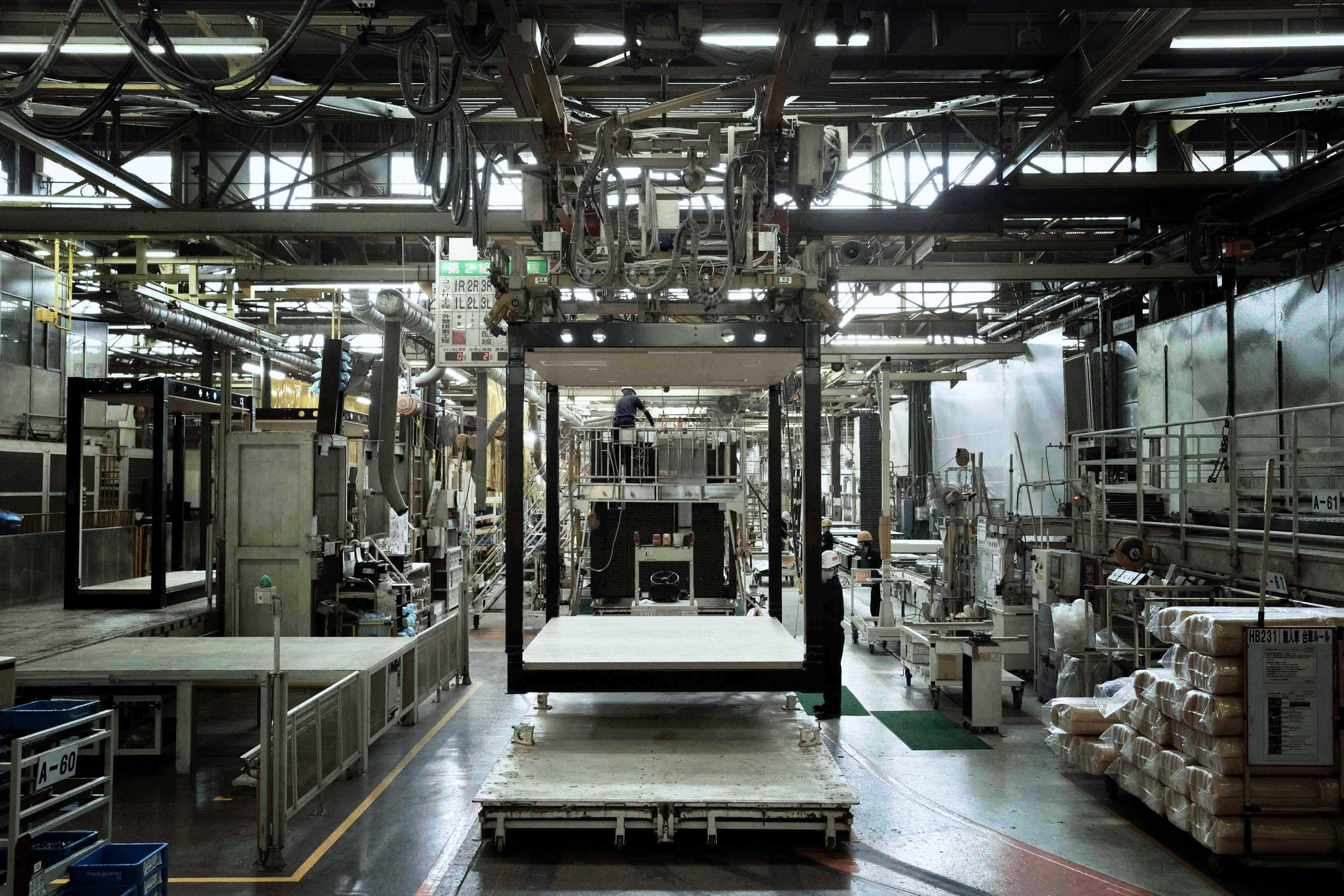
The Crown body team arranged to use the cationic electrodeposition coating facilities set up for Toyota Housing’s steel rigid frame units. Takashi Yamamoto of the company’s Manufacturing Department recalls receiving the request.
Yamamoto
When I heard about it from my supervisor, I was immediately interested. After all, the technology originated in Toyota’s car manufacturing. More than anything, I was struck by the team’s dedication to making the Crown even better than the original, a car that can safely remain on the road for another 50 or 100 years.
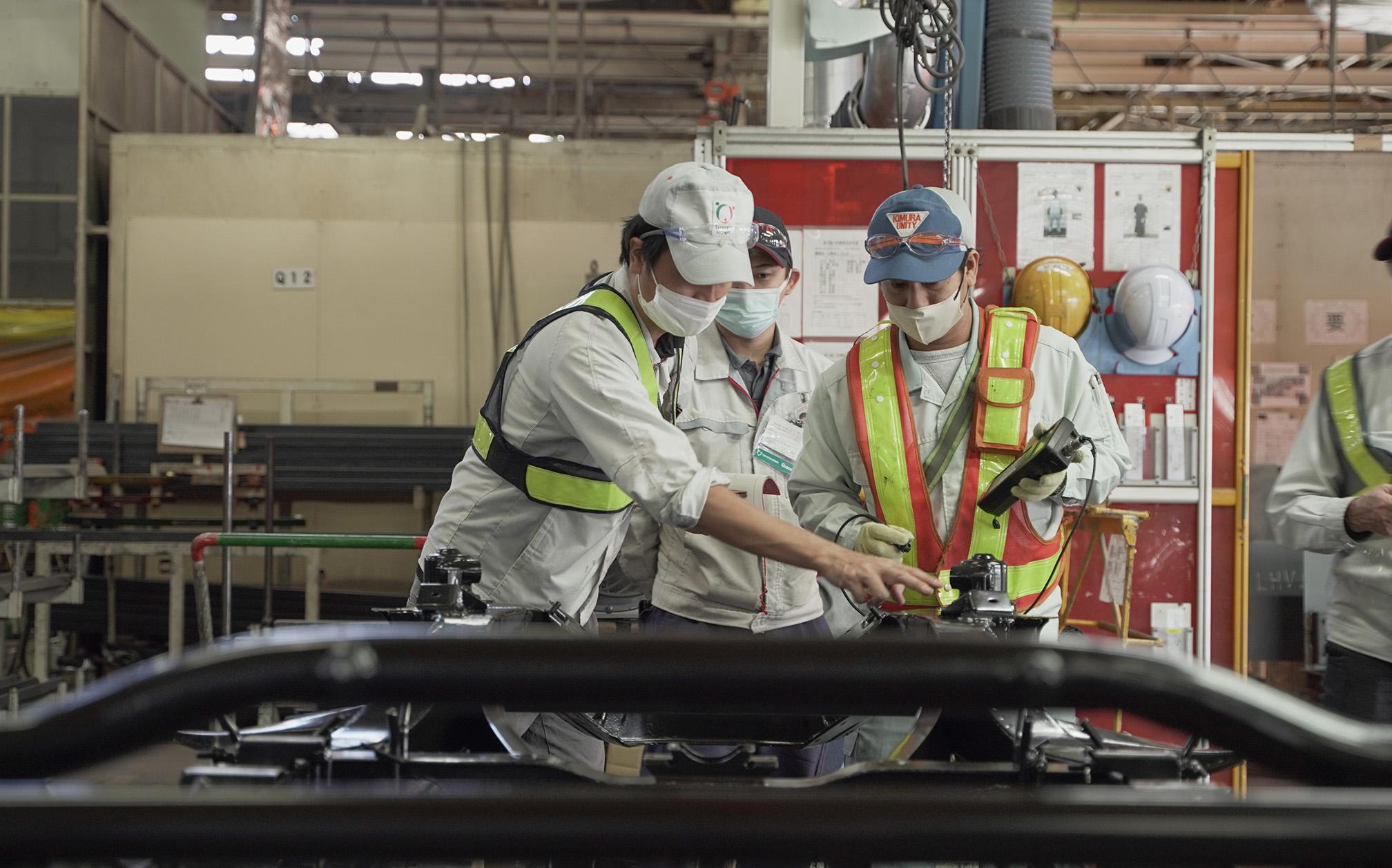
Even at Toyota Housing, the team faced two hurdles in pursuing cationic electrodeposition coating. First, the existing pallet and mounts would not allow the Crown’s body to be fully immersed in the paint, leaving some areas uncoated. The second obstacle was removing rust from internal sections of the body and chassis that could not be reached by hand.
Based on their previous discussions, the members cleared the first hurdle by building their own pallets and mounts to ensure sufficient immersion depth. The second problem was also solved by enlisting the help of Teikuro, surface treatment and coating specialists who chemically remove rust from large molds. Teikuro assisted the team with thorough rust removal and degreasing of metal surfaces to improve coating quality.
Thanks to these efforts, the team finally achieved the unprecedented step of applying cationic electrodeposition coating to the body and chassis of an old car as part of the restoration.
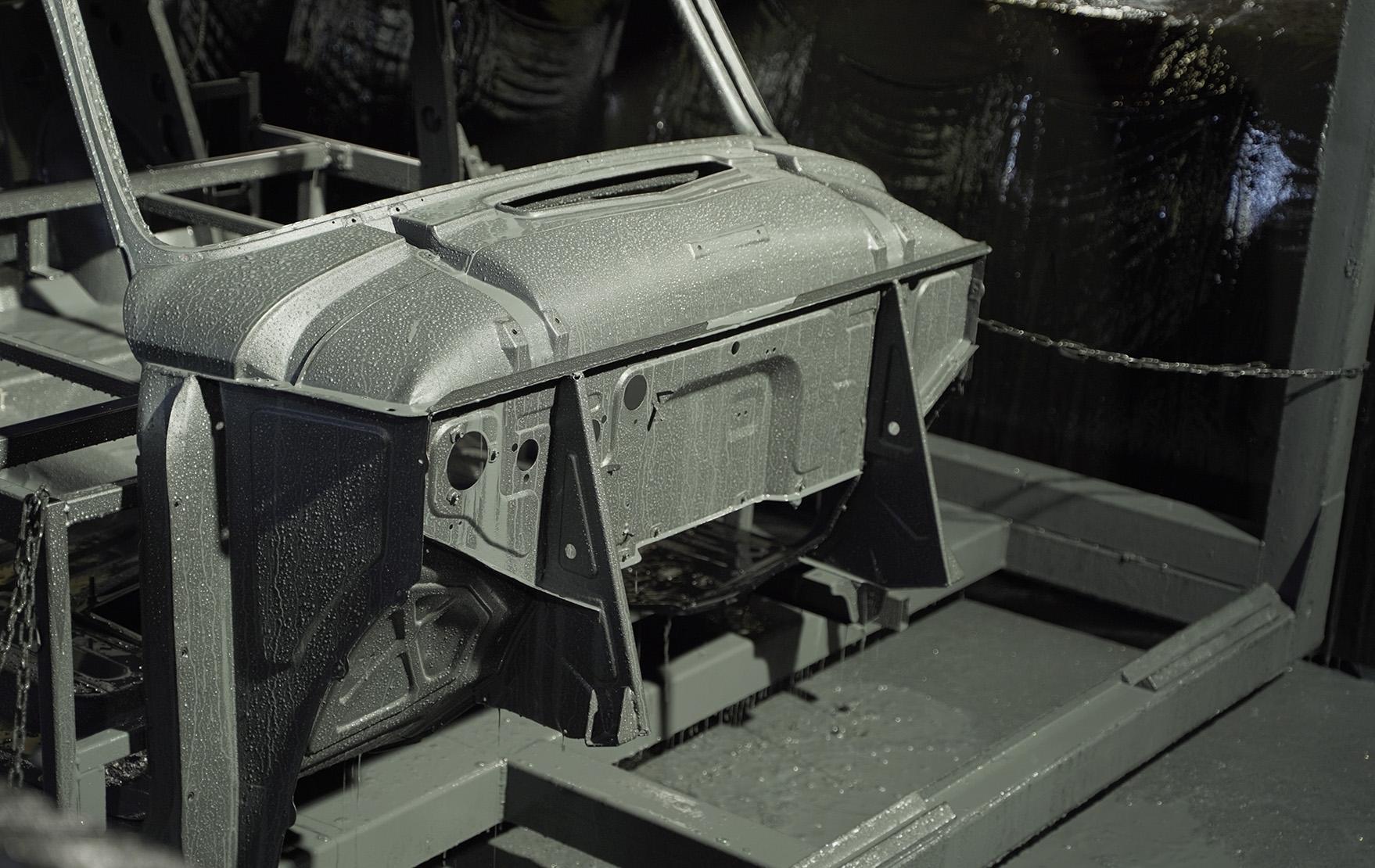
Tomiyasu
I have nothing but gratitude for Toyota Housing, who took on the job of electrodeposition coating the body and chassis of a vehicle that normally wouldn’t go through their regular production line.
In attempting the task, we consulted with the members to construct mounts and a jig to ensure that the body and chassis would be fully submerged in the electrodeposition tank. Although it seemed impossible at first, I think we were able to accomplish the cationic electrodeposition coating because of the team’s willingness to take on new challenges and cooperate, including with our partner companies.
Toyota’s highly skilled technicians managed a flawless body restoration that surpassed the original, complete with cationic electrodeposition coating thanks to the generous assistance of Toyota Housing. In doing so, they achieved more than the restoration’s aims of passing on skills and developing talent; the experience and results gained in the process will no doubt extend beyond the first-generation Crown restoration project, serving as an invaluable contribution to making existing cars carbon-neutral and helping to fulfill car lovers’ dreams of keeping their cherished rides on the road forever.
As this project has shown, restoring old cars is full of difficulties and amusing anecdotes that are not found in new car production. Part 5 of this series will focus on these hurdles and fascinating stories from the first-generation Crown restoration.
(Text: Yasuhito Shibuya)