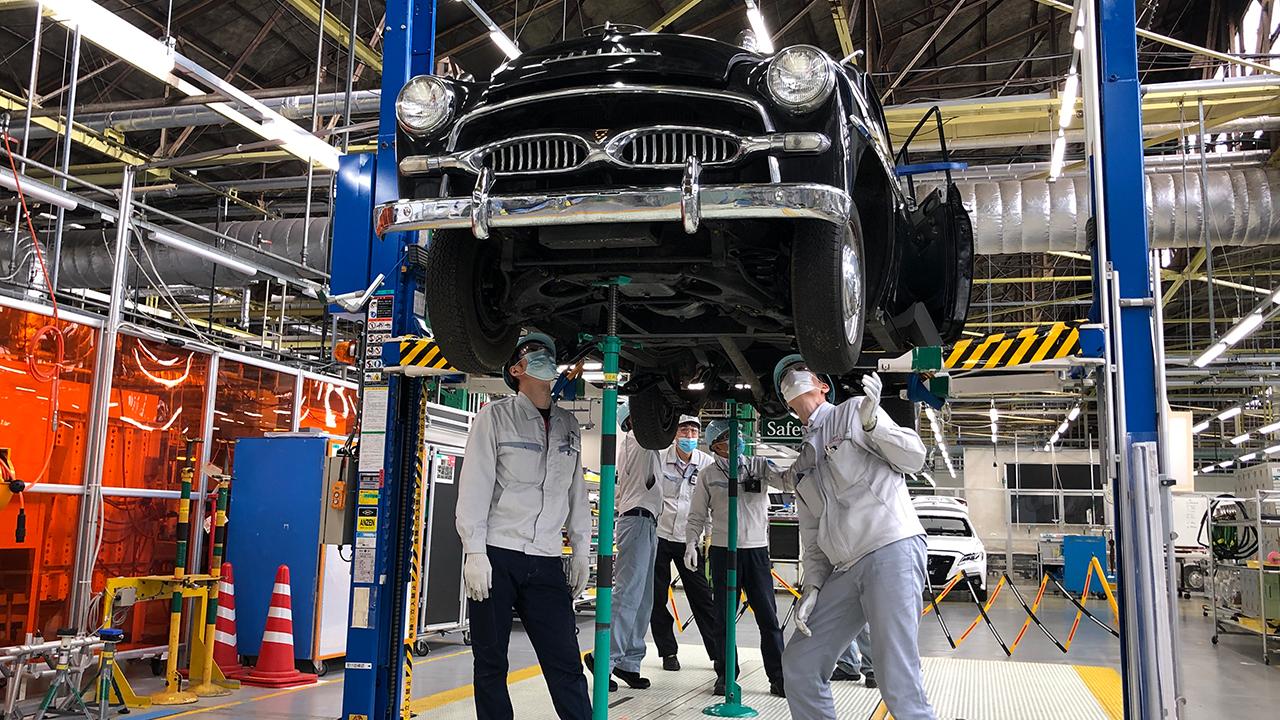
This series explores the project to restore a first-generation Crown, a car that embodies Toyota's origins. Part 3 covers the checking and disassembly work as the first stage of restoration.
The disassembly work begins
With these preparations complete, the task of disassembling the car could finally get underway. First, the team used a hoist to remove the transmission and Type R engine from the engine bay.
The Type R was a water-cooled, in-line four-cylinder engine with a displacement of 1453cc, producing 48hp at 4,000rpm. These engines had already been in use for over a year before the Crown’s release, including in the 1953 Toyopet Super and other passenger cars.
The Type R was the most technologically advanced Japanese engine of its time, with ongoing improvements continuing to boost power output for years after the Crown’s launch in 1955. This long-serving engine will remain part of Toyota’s history.
One of the big goals of this restoration was to make this engine capable of delivering the kind of power it did when the car first rolled off the production line.
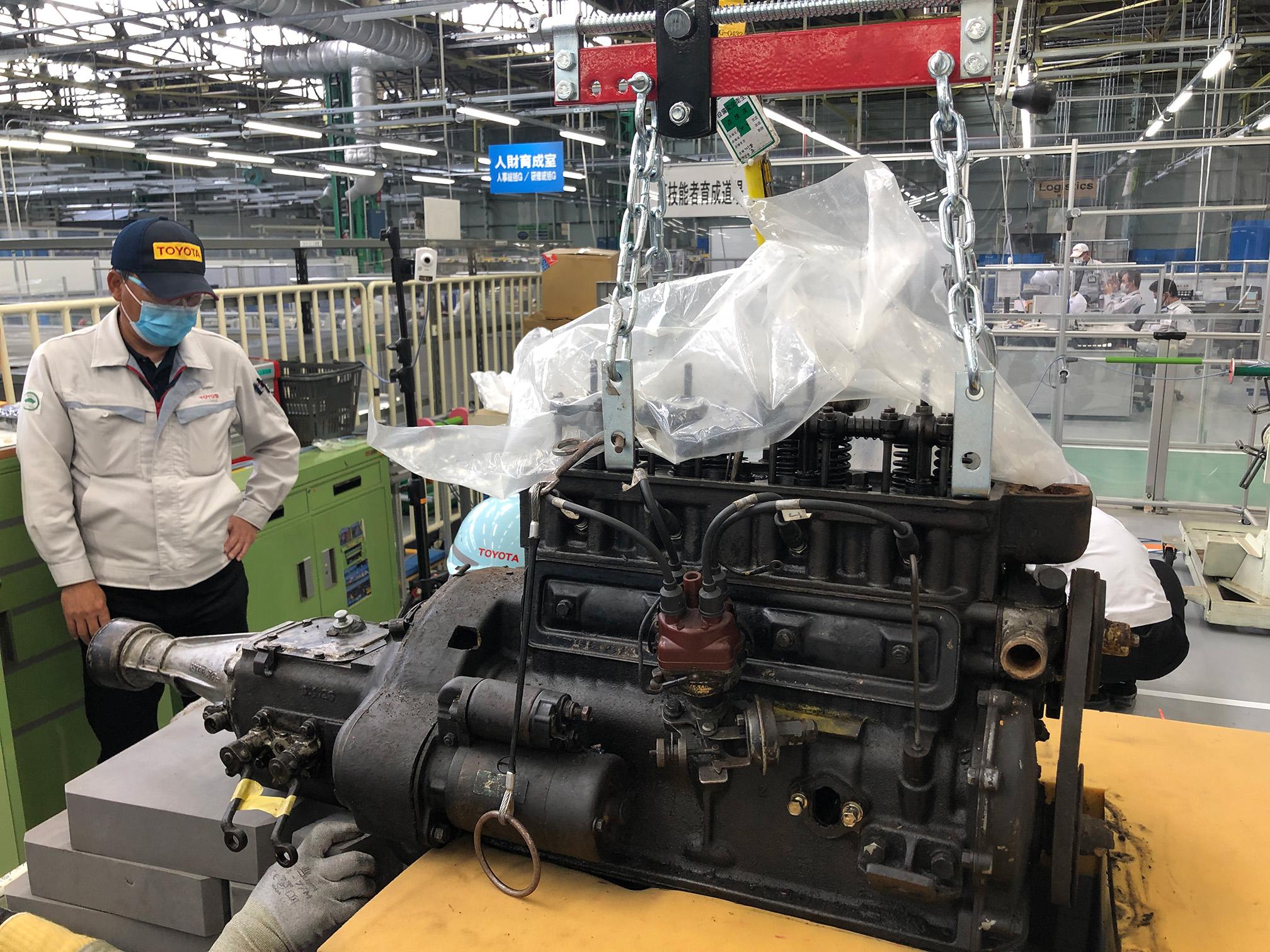
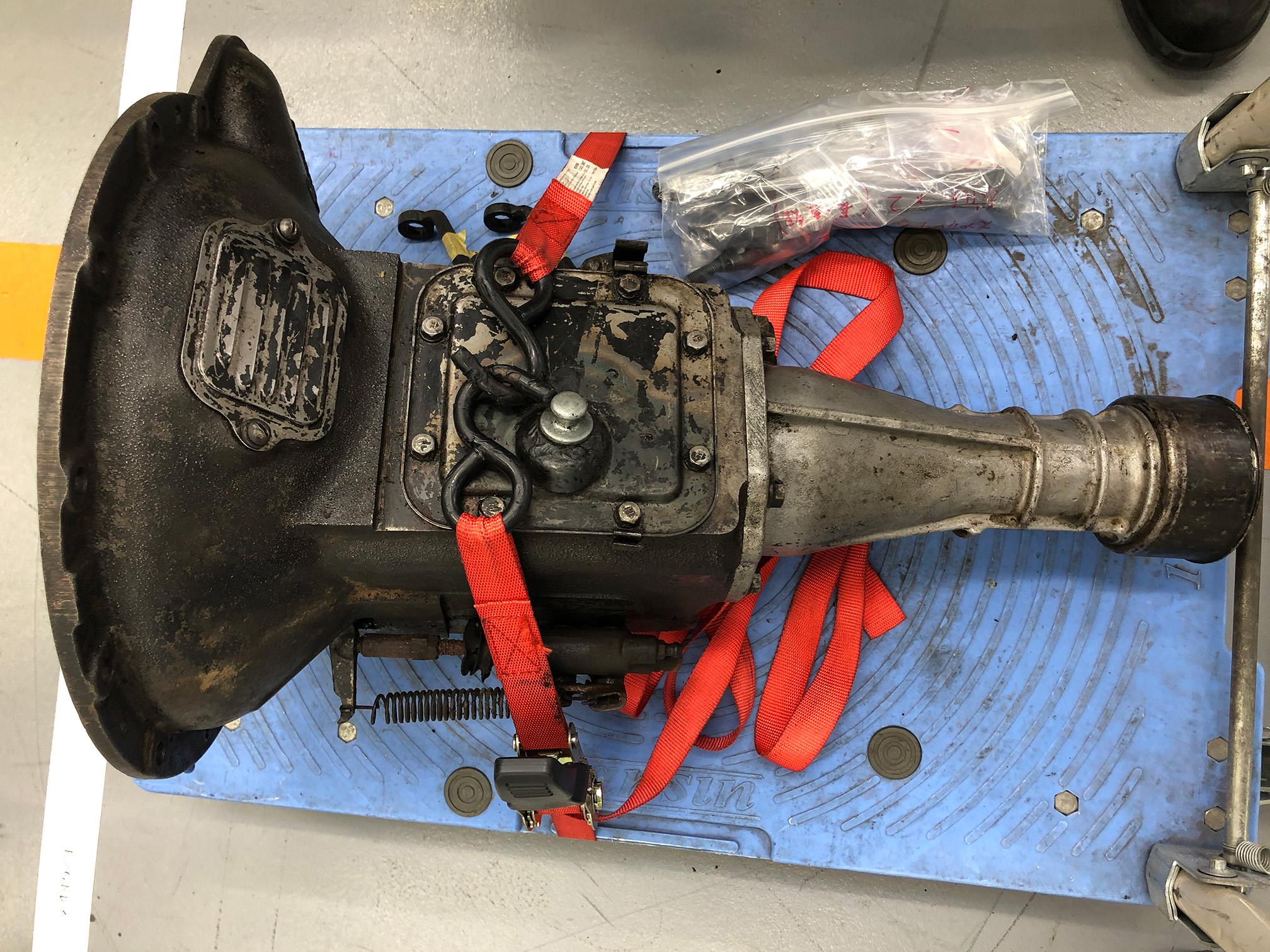
Next to come out was the equally ground-breaking four-speed transmission, featuring a synchromesh system for smooth shifting to the top and second gears. Later advances saw synchromesh used for all gears.
From there, the engine headed to Testing Room 3 at the Kamigo Plant to be prepped for disassembly. The transmission was taken to the Kinuura Plant’s Quality Control Division for a complete overhaul.
A car built with passion
At first, Nishida’s five assembly team members were at a loss as to how to approach the disassembly task, as it is the exact opposite of what is required to put a car together. Fortunately, many were technicians with experience in key production-floor roles. As the work progressed, the pace of disassembly picked up until it far outstripped the initial schedule.
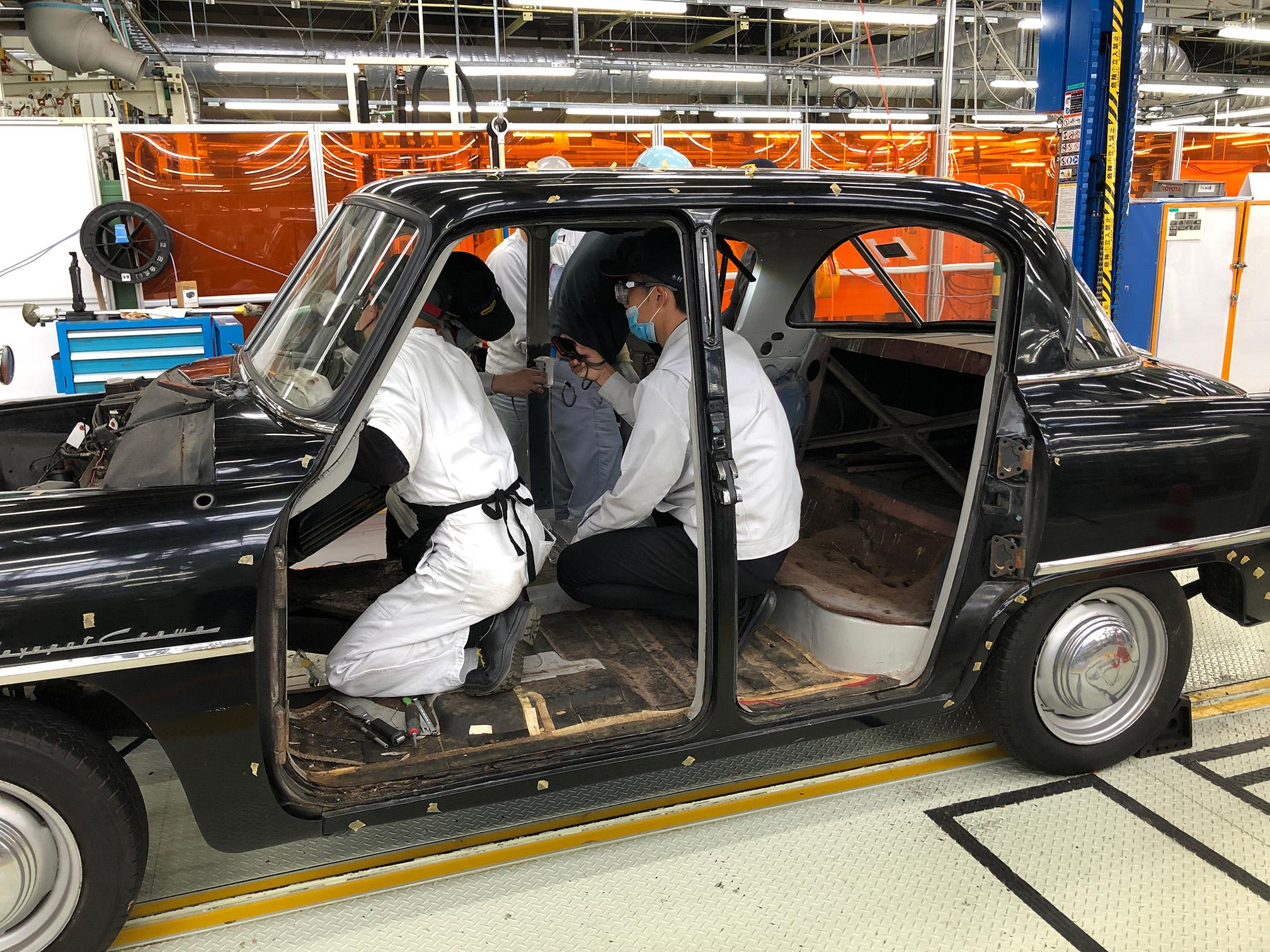
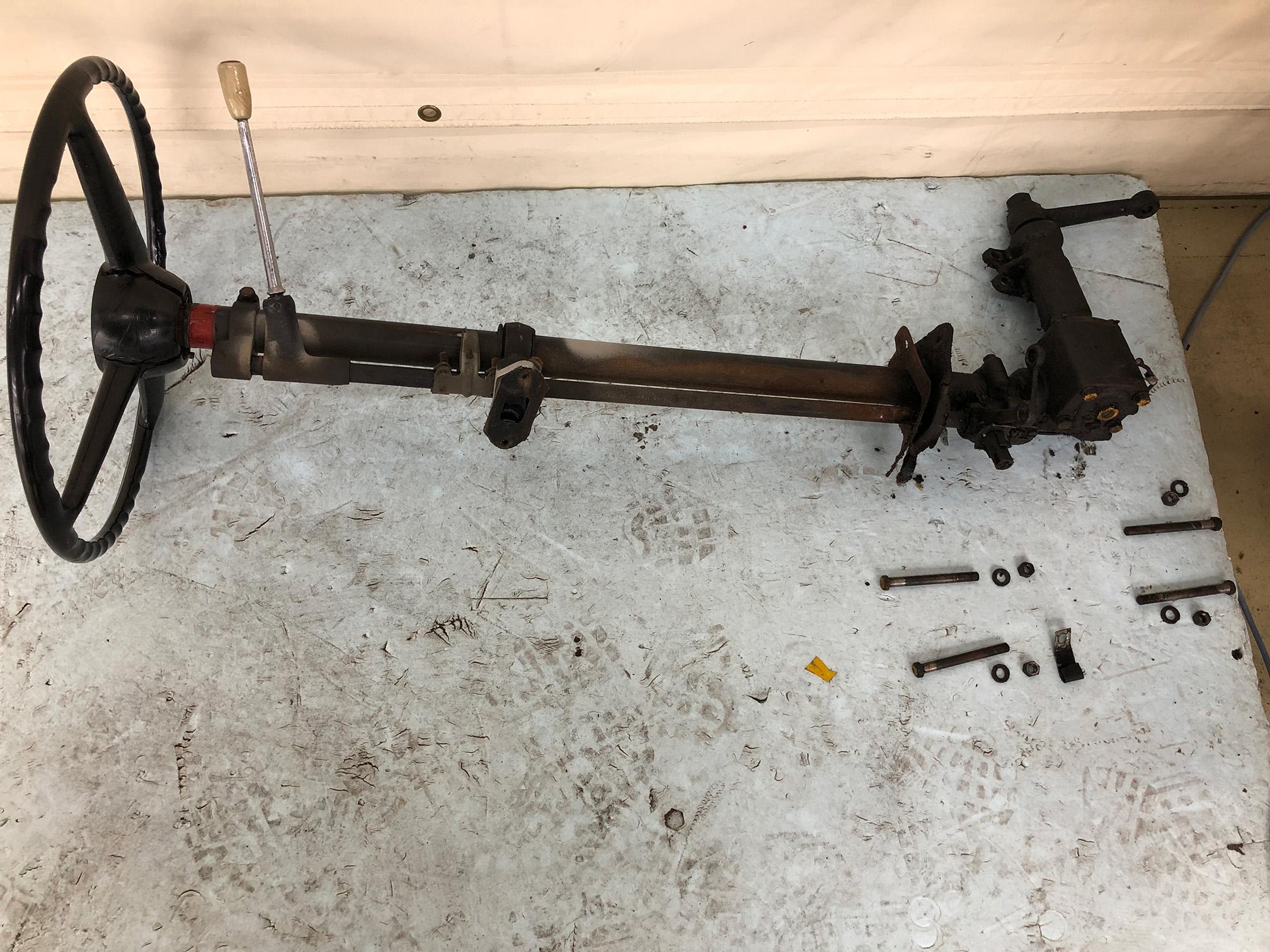
In the process of removing various parts from the body and chassis, pulling them apart, and checking their condition, the members came across numerous discoveries and surprises not found in their regular work of assembling new cars. Nishida spoke for his team.
Nishida
In general, the first-generation Crown has a simple design, but certain aspects are completely different from the cars of today. Much time and effort have gone into making many of these parts.
For instance, we were surprised to find that the front radiator grille was hammered out of sheet metal—that is, it was made by hand. The door locks weren’t electric as they are today, but rather a mechanism that combined springs and cams. When we disassembled such parts, at first I was worried that we might not be able to put them back together.
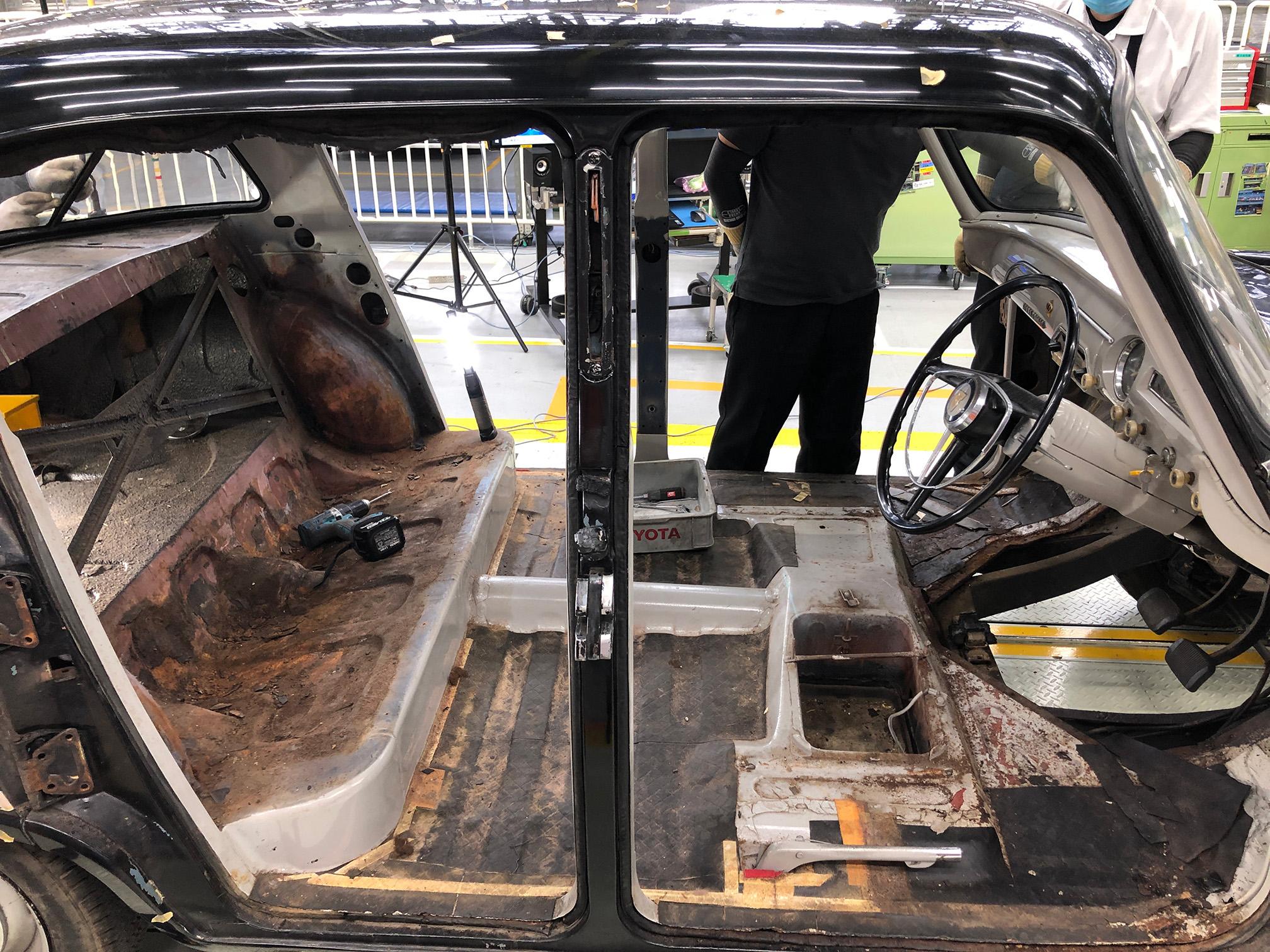
As he went about the disassembly work, however, these concerns vanished. In each part, Nishida could see the remarkable skills and dedication of the car’s original creators.
Nishida
Although I had expected it to a degree, the high level of craftsmanship that must have been the norm lived on in the details. I was struck by the incredible skills of the people back then.
What’s more, the parts were designed to be easily disassembled for repair, unlike today’s components which are made with replacement in mind. I think that’s why both owners and mechanics found joy in servicing and repairing these cars, something that you can’t expect in the cars of today.
These parts reflected the passion of the original makers, an intimate relationship between people and cars that is different from what we have now.
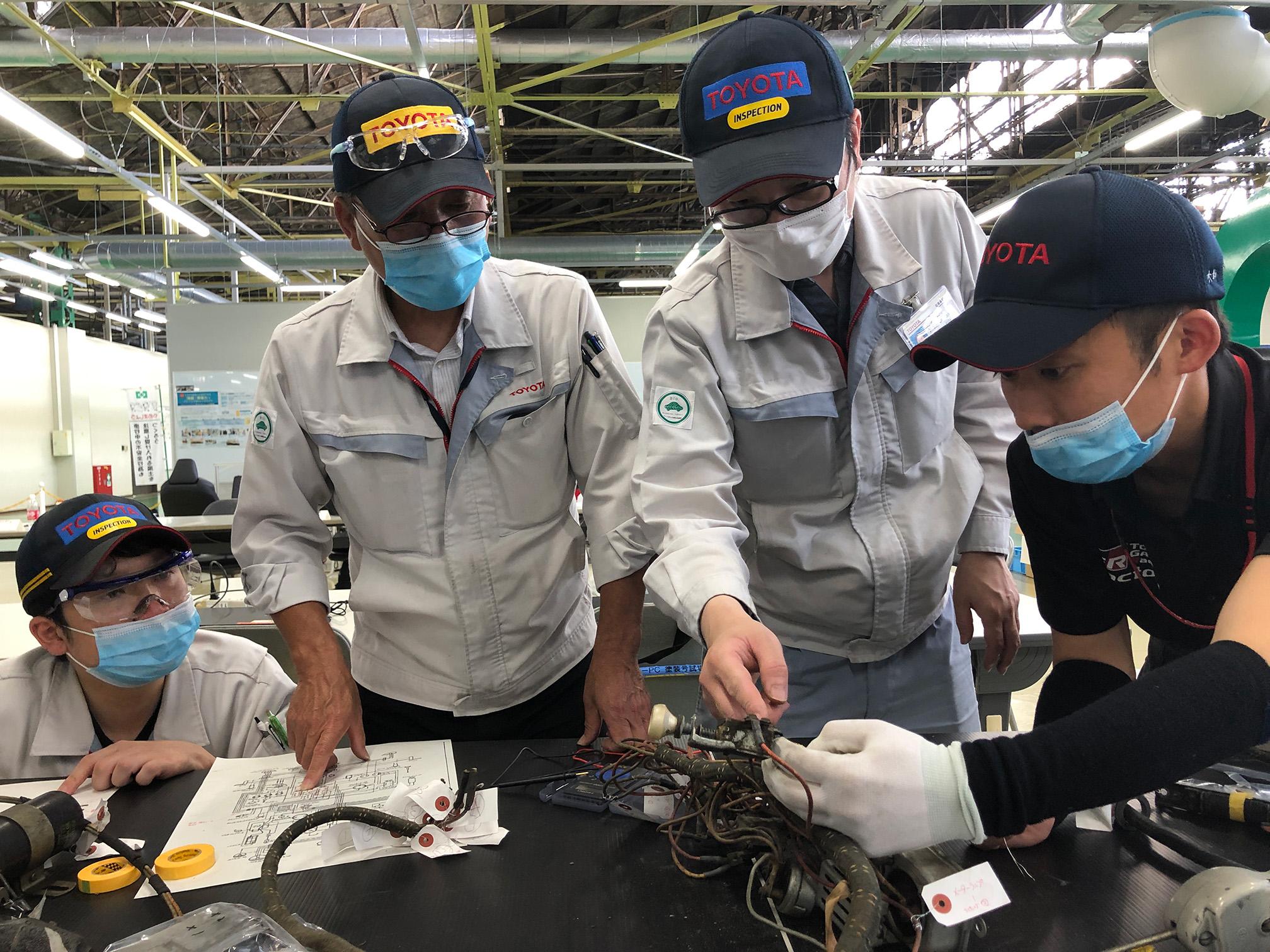
When the first-generation Crown was launched in the mid-1950s, and during the 1960s boom in car ownership, cars were a far greater status symbol than they are today. For an owner, reading the car’s manual was a special pleasure.
Many people also purchased service manuals and enjoyed learning how their cars were put together, along with carrying out repairs by themselves. This culture has been lost over the past few decades of rapid car evolution.
Even for veterans like Nishida, who has spent more than 30 years at the forefront of Toyota's car manufacturing, this was a new discovery.
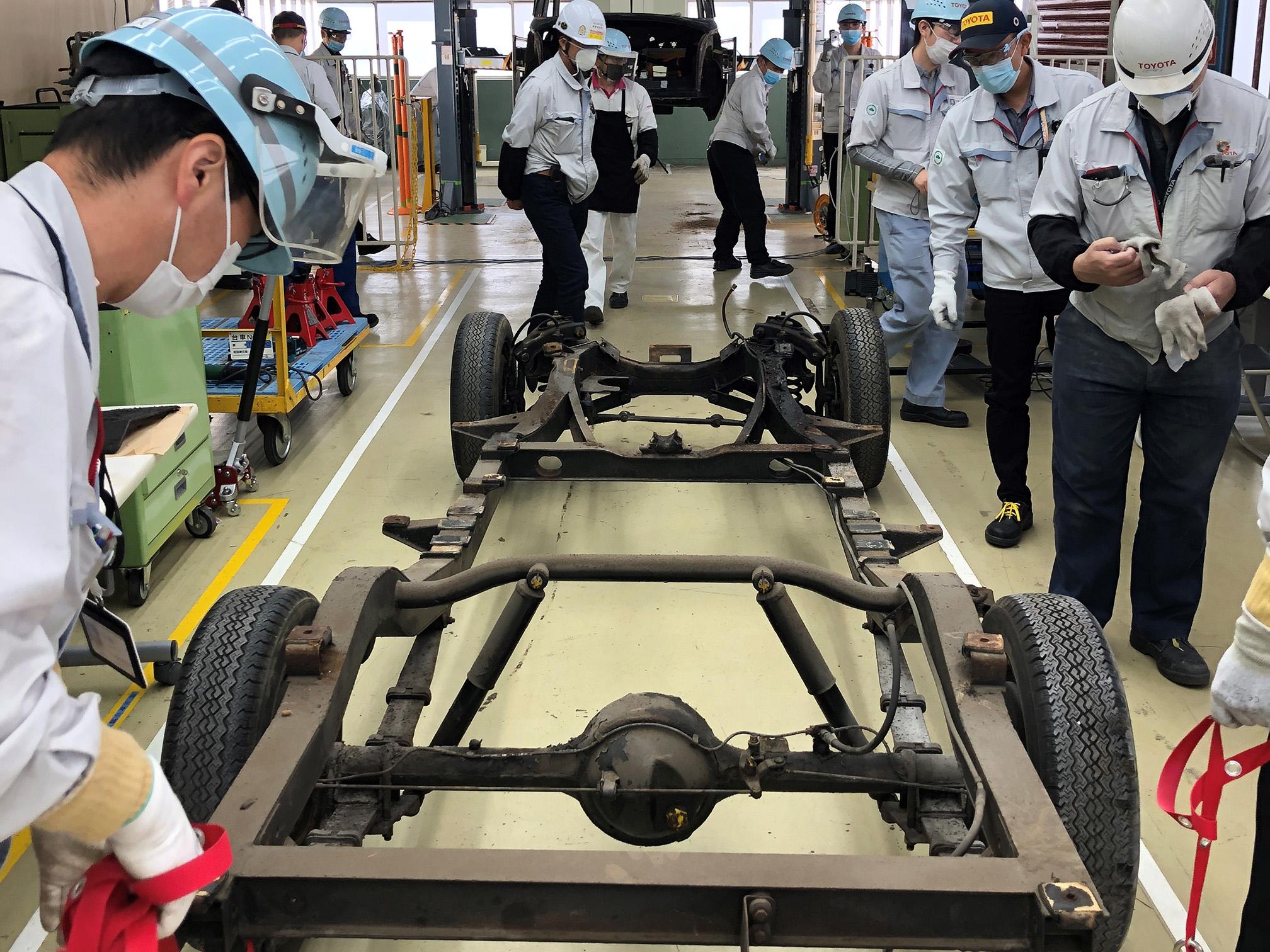
Working alongside the disassembly process, the four-man final inspection team, led by Utsunomiya in his 30s, diligently organized components as they were removed by the assembly crew, checking them against the parts catalog and blueprint data.
Interior parts such as the seats, windows, and wire harness were stripped from the body along with key components including the doors, muffler, and rear differential. The inspection team labeled each individual piece, checking them against PDF versions of the original blueprints and parts catalog.
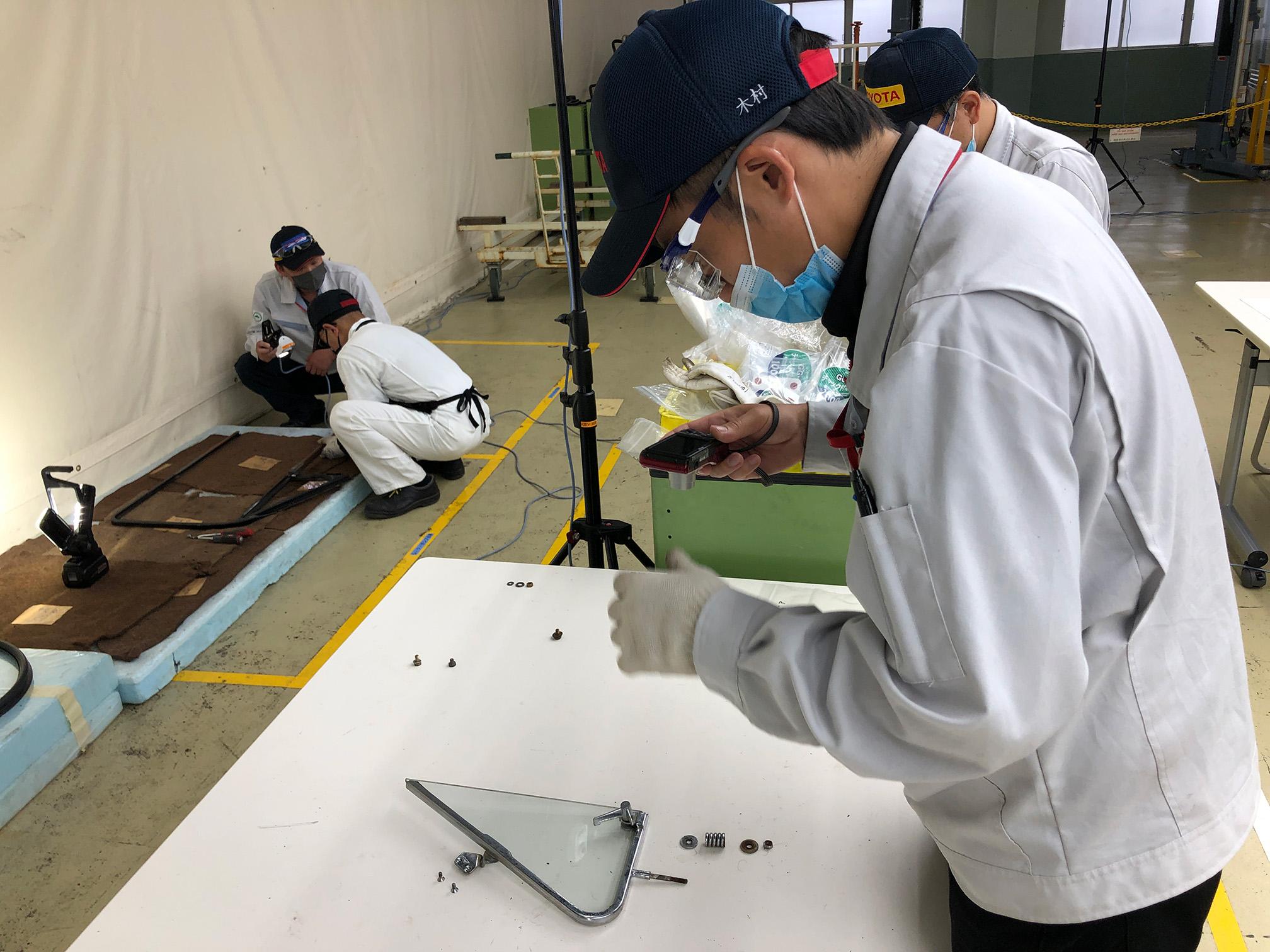
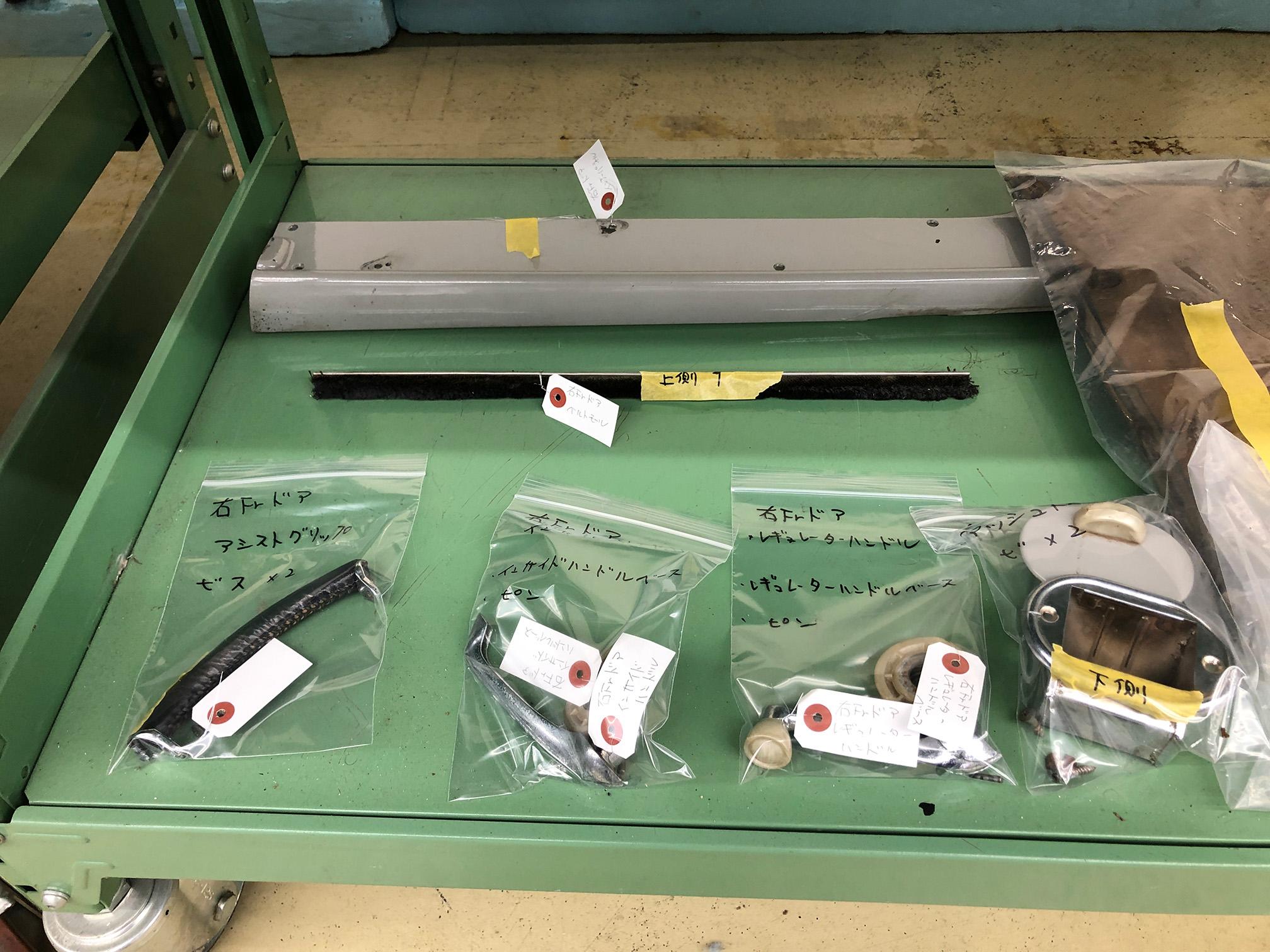
This process of checking each part and its construction can be regarded as “industrial archaeology” in practice, uncovering the ingenuity and effort of those who made the car and creating a record of past technologies and systems that are now being lost.
Just as the disassembly work was filled with discoveries for Nishida and his fellow assembly team veterans, for Utsunomiya’s crew the task of sorting and cross-checking brought much admiration and amazement.
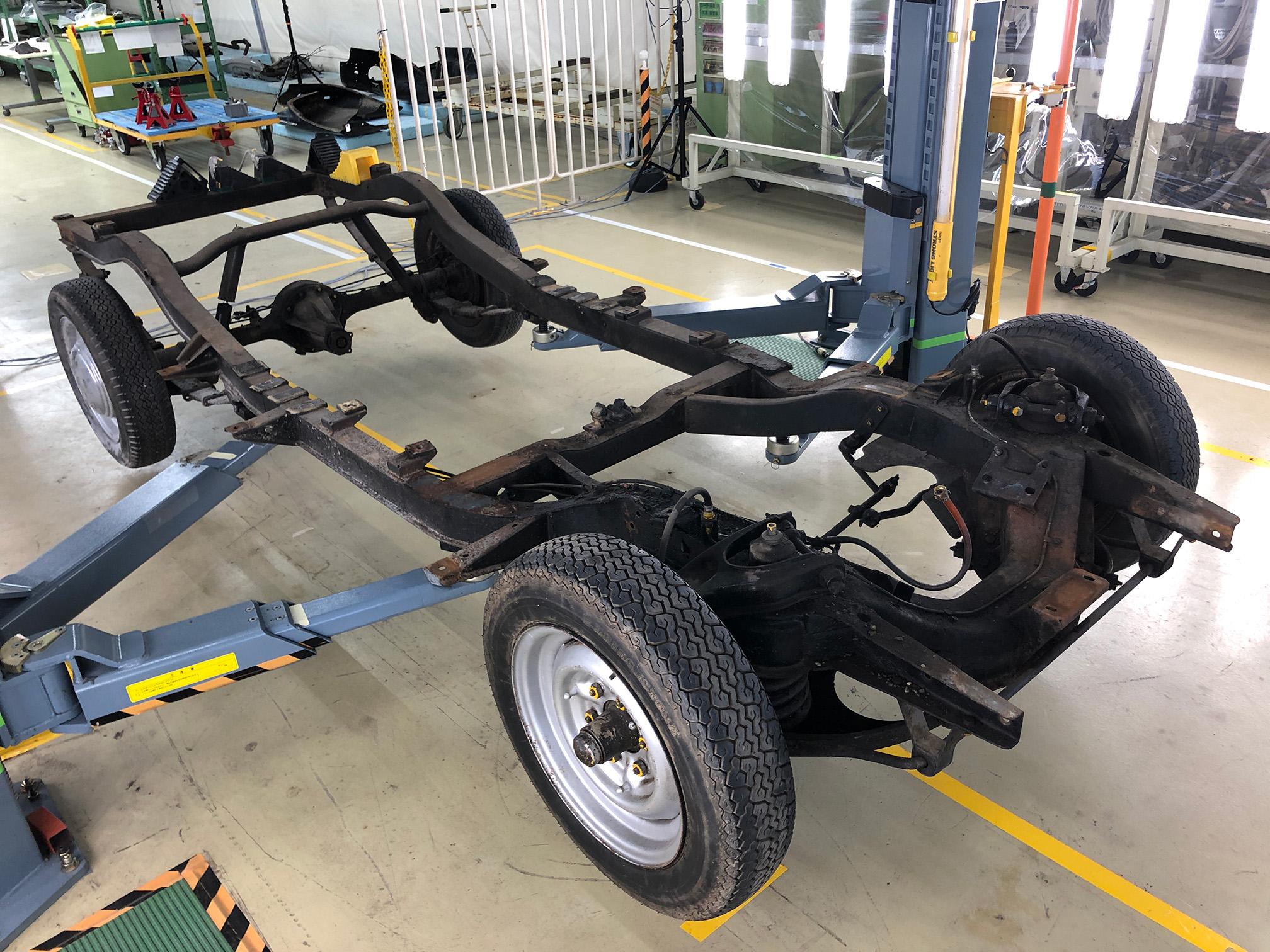
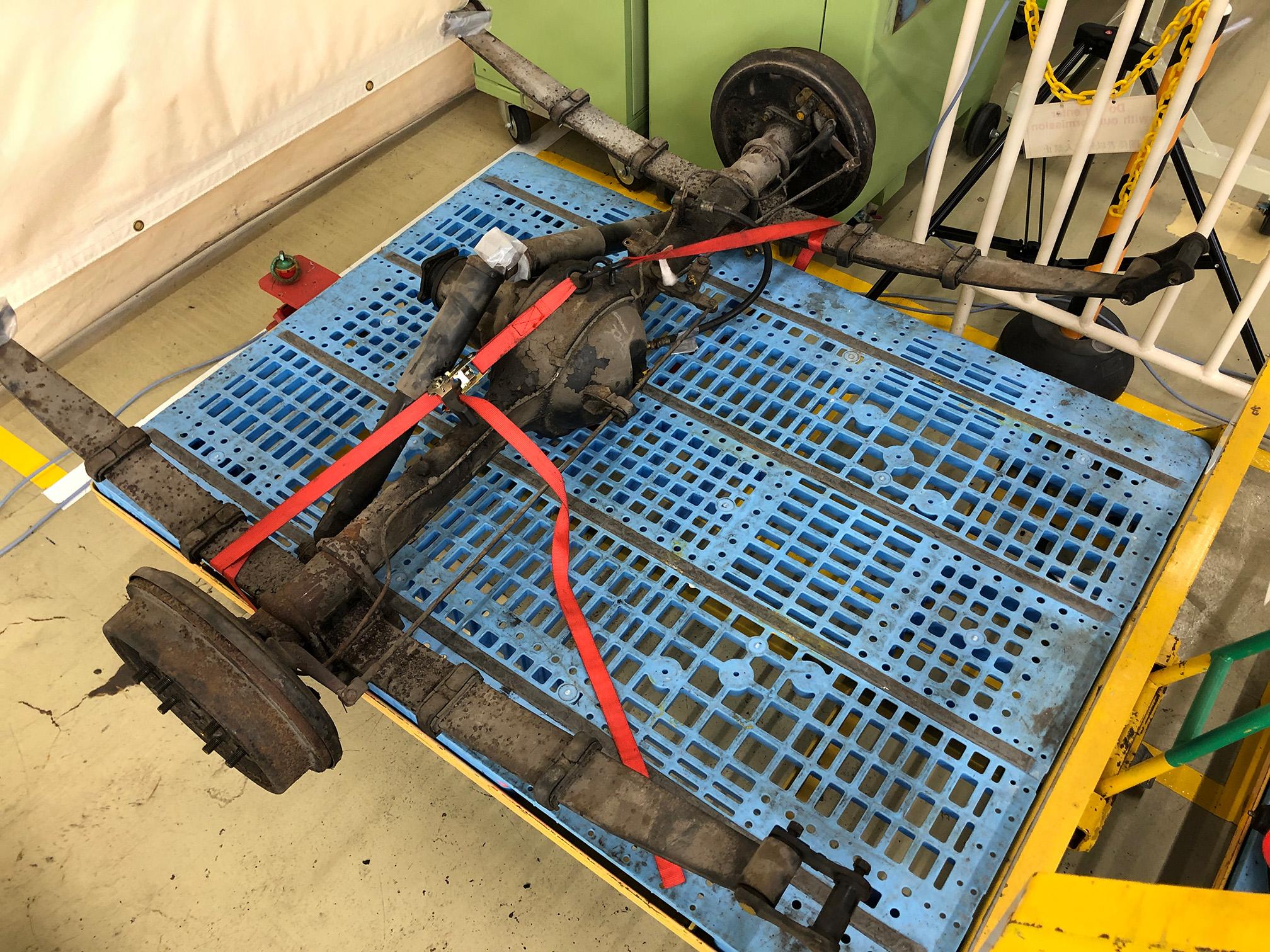
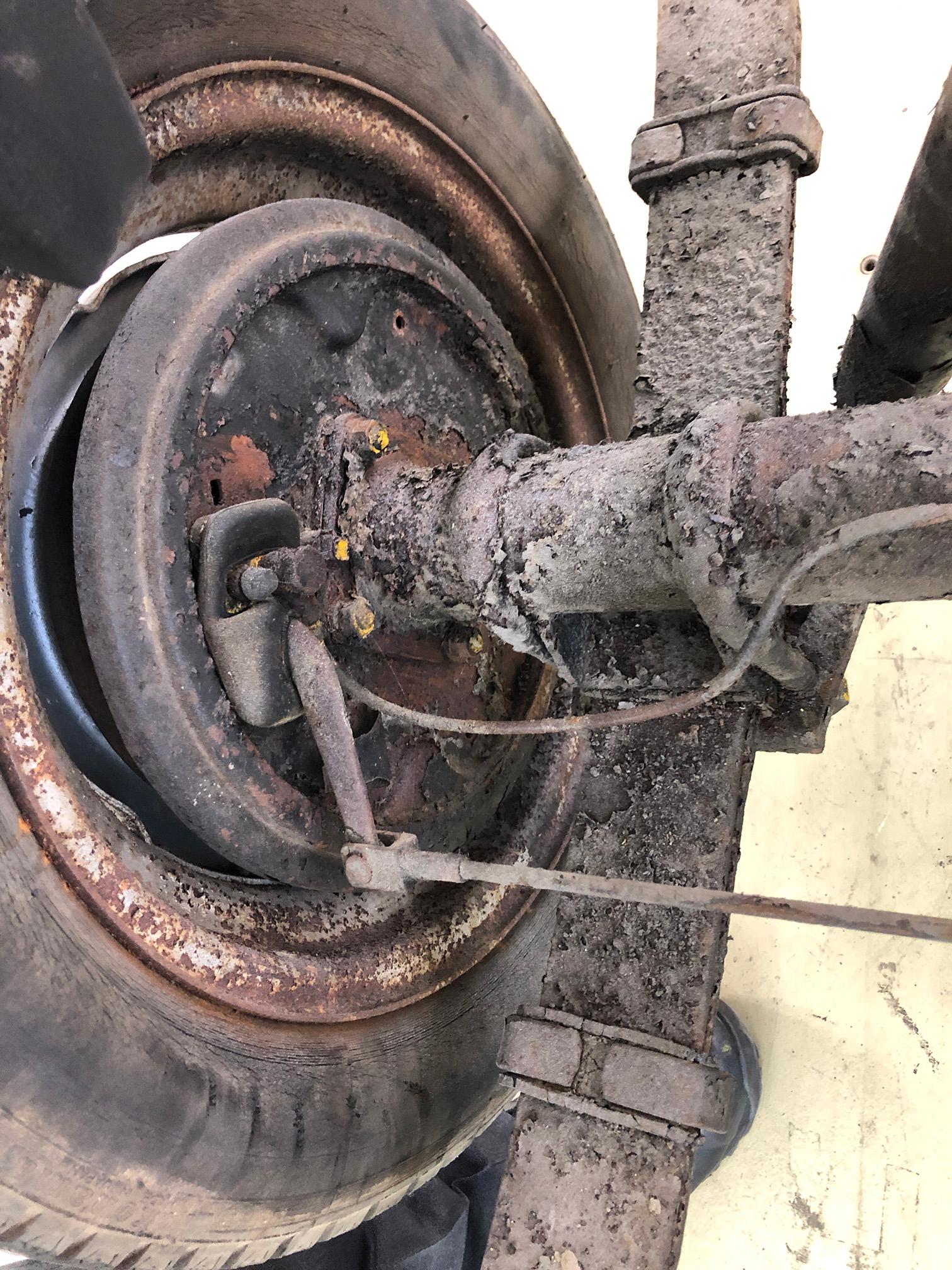
Utsunomiya
Nowadays, every part of a car is operated electronically by ECUs (electronic control units). But being there as the Crown was disassembled, sorting the parts and seeing how they were built, I realized that even this 70-year-old car was fundamentally the same as its modern counterparts. In place of ECUs, the same functions were performed by people and mechanisms.
I was also impressed that, with the technology they had available, even then the mindset was all about prioritizing the people onboard.
The inside locks and levers for opening the coach doors were designed to be pulled with minimal force, while the handles for winding the windows up and down were positioned such that the passengers could turn them easily from their seats. It was thrilling to see that they had pursued the same level of quality to ensure the car would be driven in comfort.
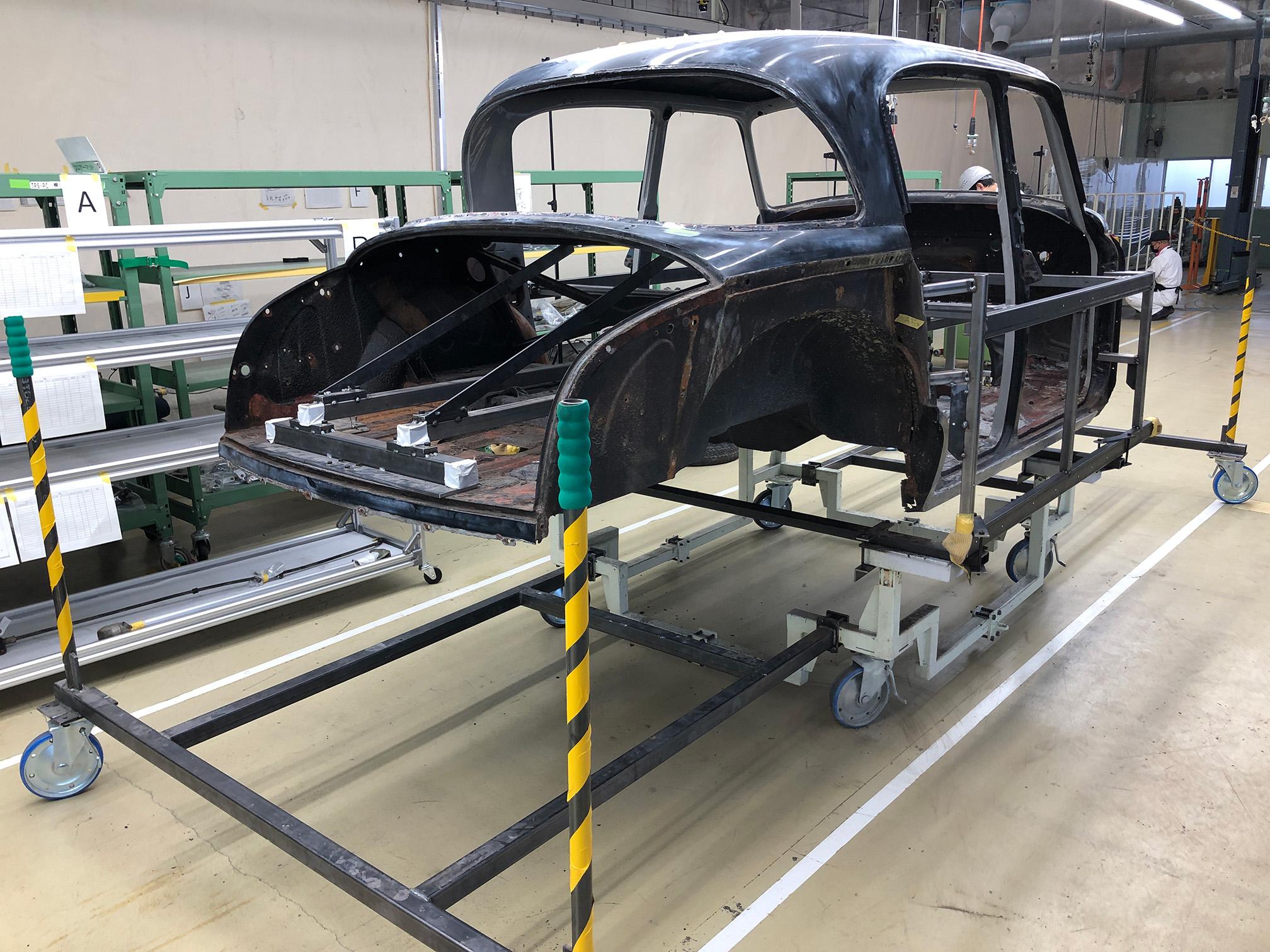
As they carried out the work, Utsunomiya and his young colleagues found that the first-generation Crown held a special allure missing from today’s cars.
Utsunomiya
The streamlined body has an attractive form that you don’t see nowadays, and the instrument panel is very stylishly designed. This first-generation Crown has many charms that automatically draw you in. It’s a car that makes you want one right away.
Our inspection team will be the final arbiter of the car’s quality. We want to do our job well to ensure that this first-generation Crown is restored with the quality of a modern Lexus.
“Selling things to people with conviction means creating something that feels good in one’s heart and has within it the true heart of the customer.”
As introduced earlier, these words from chief engineer Kenya Nakamura embody Toyota’s car-making philosophy, which began with this Crown. Despite coming from different generations, both the veteran Nishida and the younger Utsunomiya felt this concept firsthand while overseeing the disassembly work. Now, more than 60 years on, that philosophy has also been passed down to the latest Crown, the 16th generation.
The next article in this series will showcase body repairs by sheet metal welding and special coating, with every effort made to achieve the quality needed for another 10 or 20 years on the road.