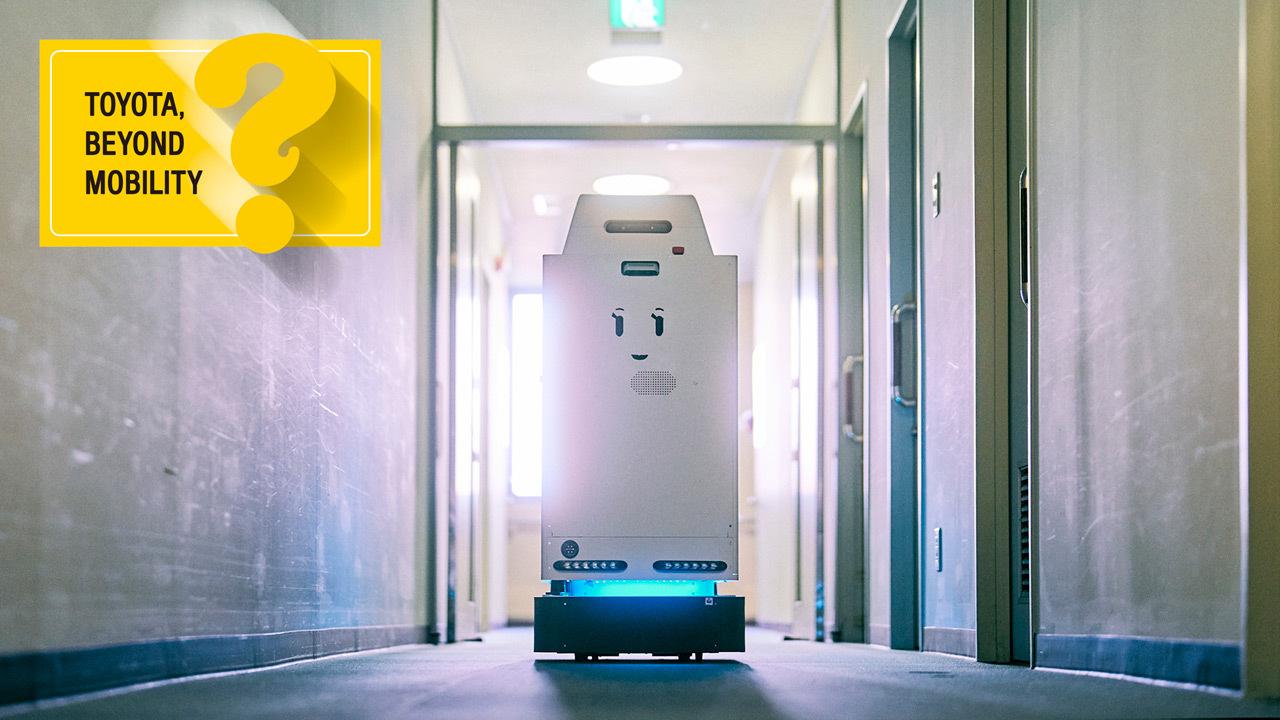
This is a series featuring Toyota's research in non-automotive fields, with the spotlight focusing this time on support for the work of hospital nurses.
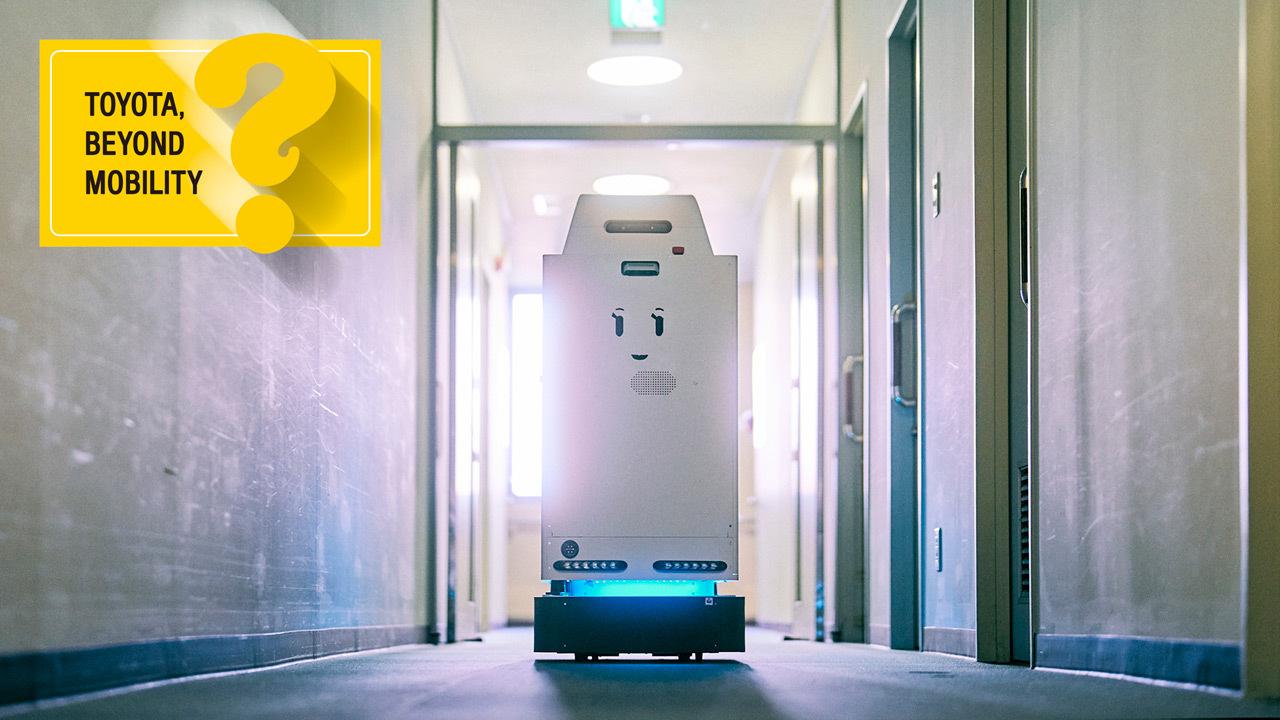
A team of Toyota employees spends their days observing nurses around the clock with stopwatches in hand. These and similar efforts have eliminated over 200 hours of night shift inefficiencies per year.
At Toyota Memorial Hospital in Toyota City, Aichi, autonomous delivery robots are in action and easing the workload of nurses so they can spend more time with patients.
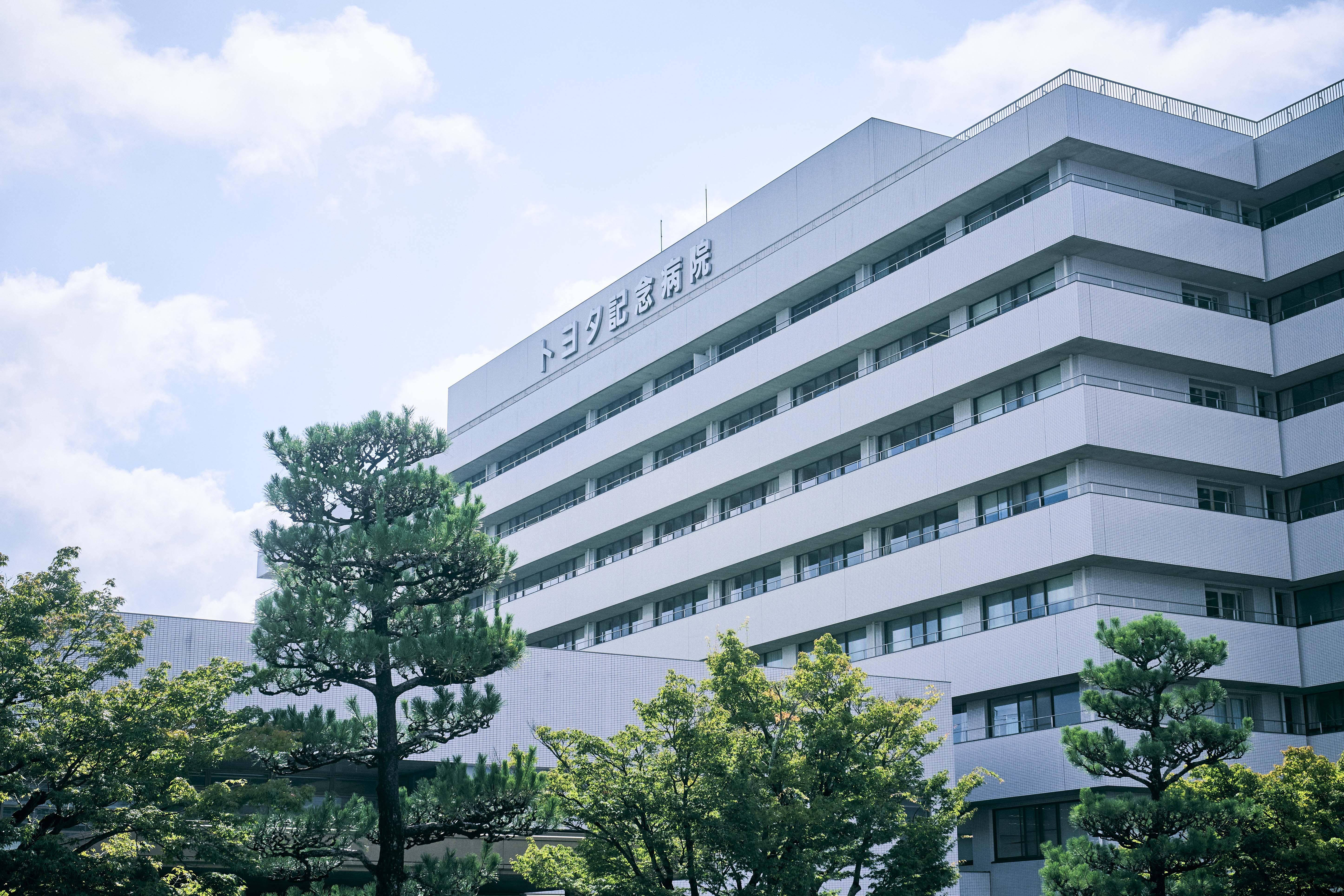
Nowadays, service robots are no longer a novelty, even popping up at family restaurants. In the tense environment of a medical facility, however, lives are at stake. This explains the robots’ tumultuous backstory, involving candid exchanges between equally dedicated nurses and Toyota developers.
Comments that annoyed nurses
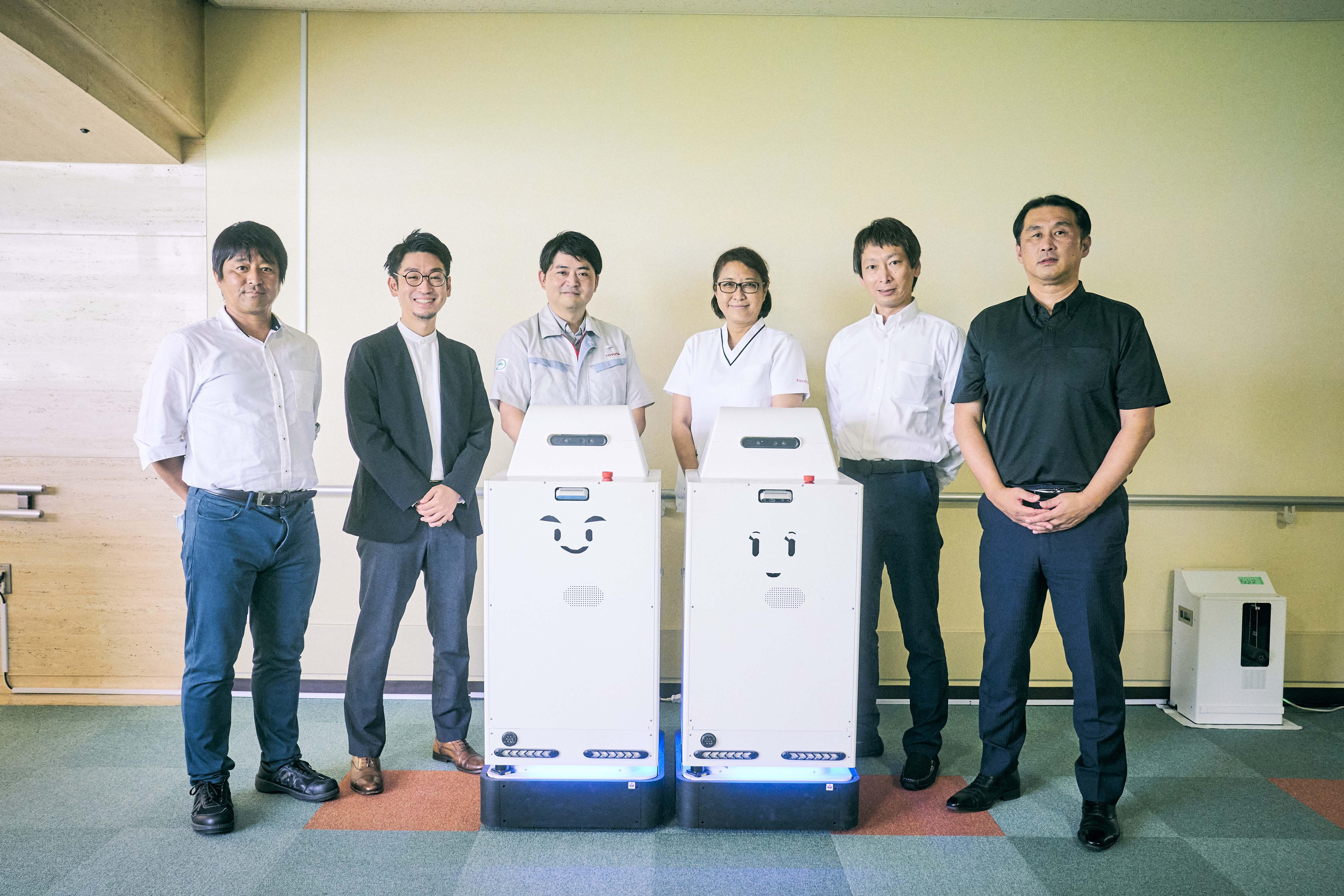
The delivery robot project began in 2019 when Toyota Memorial Hospital, operated by Toyota Motor Corporation, approached the company’s robot development unit. Toyota’s developers then spent two weeks at the hospital, around the clock, watching nurses at work to figure out what kind of support they needed.
Unfortunately, it didn’t all go to plan…
As kaizen professionals, the Toyota members observed how nurses worked and identified areas for improvement. They continually asked nurses: “Is this part of nursing work?” “Does this work add value?”
For their part, the nurses were clearly bewildered by this questioning.
Despite their practices being grounded in many years of experience, the nurses now felt as though their work was being called into question. This sparked a strong spirit of resistance. As Assistant Head Nurse Naomi Kuroda recalls, some nurses resented the outsiders who had suddenly invaded their workplace.
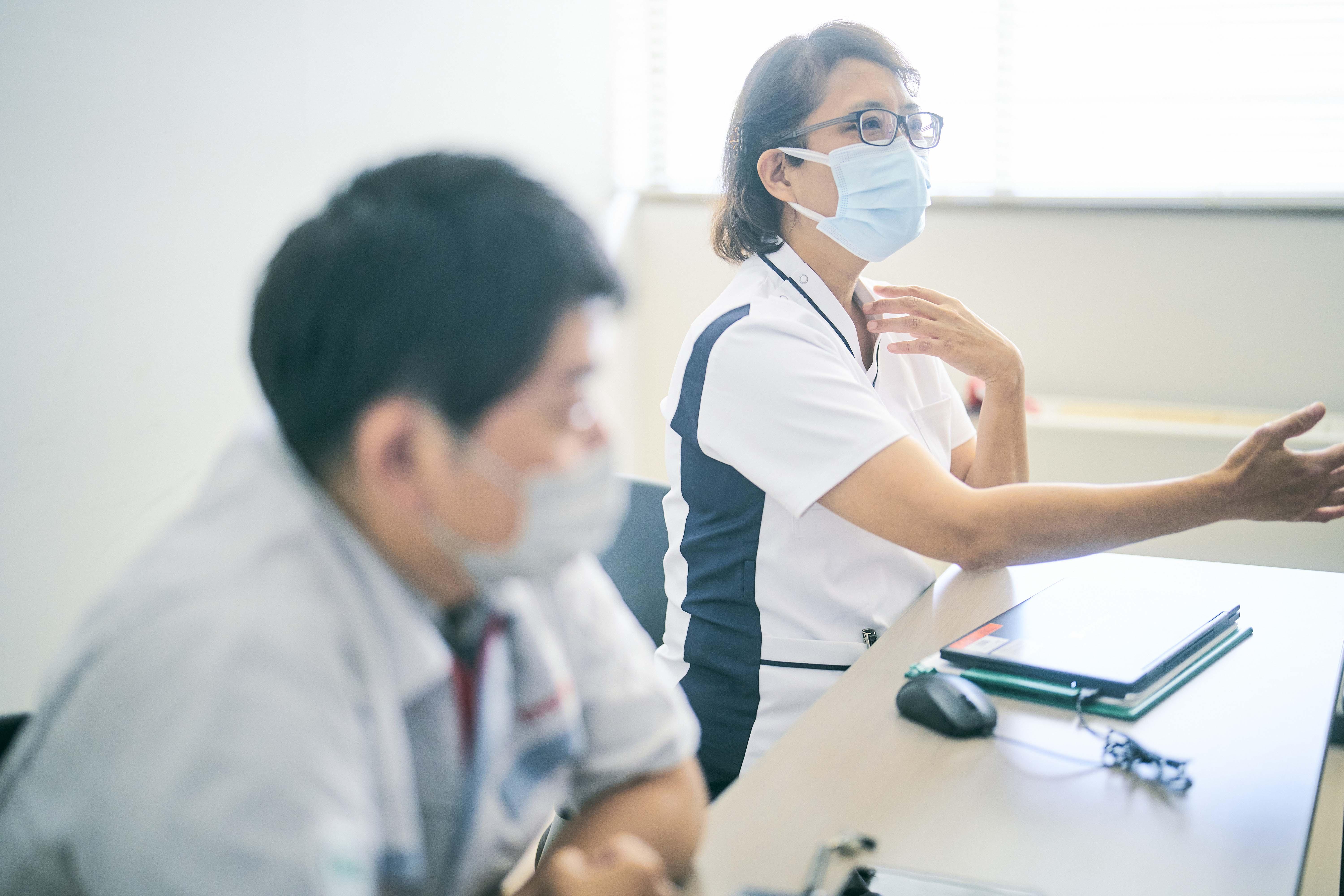
When people from different fields get together, some clashes of opinion are inevitable. Initially, such disagreements cropped up time and again, creating a somewhat volatile atmosphere.
This takes up 40% of a nurse’s work?!
To begin with, hospital staff felt that robot support was needed in the emergency ward.
The emergency ward lacks direct elevator access from the hospital’s pharmacy and runs on a skeleton staff at night. Regardless, “I was out getting medicine” is not a valid excuse when a patient is in need.
When Toyota’s team monitored the reality on the ground, they noticed that 40% of a nurse’s work time was taken up with tasks such as fetching items. “One day, they asked me if delivering things was part of nursing work,” says Kuroda. “I was taken aback. I finally realized that we didn’t have to be the ones doing that.”
This 40%—or 3 hours out of an 8-hour shift every day—could be used for more meaningful work. For a highly specialized profession like nursing, that would make a vast difference.
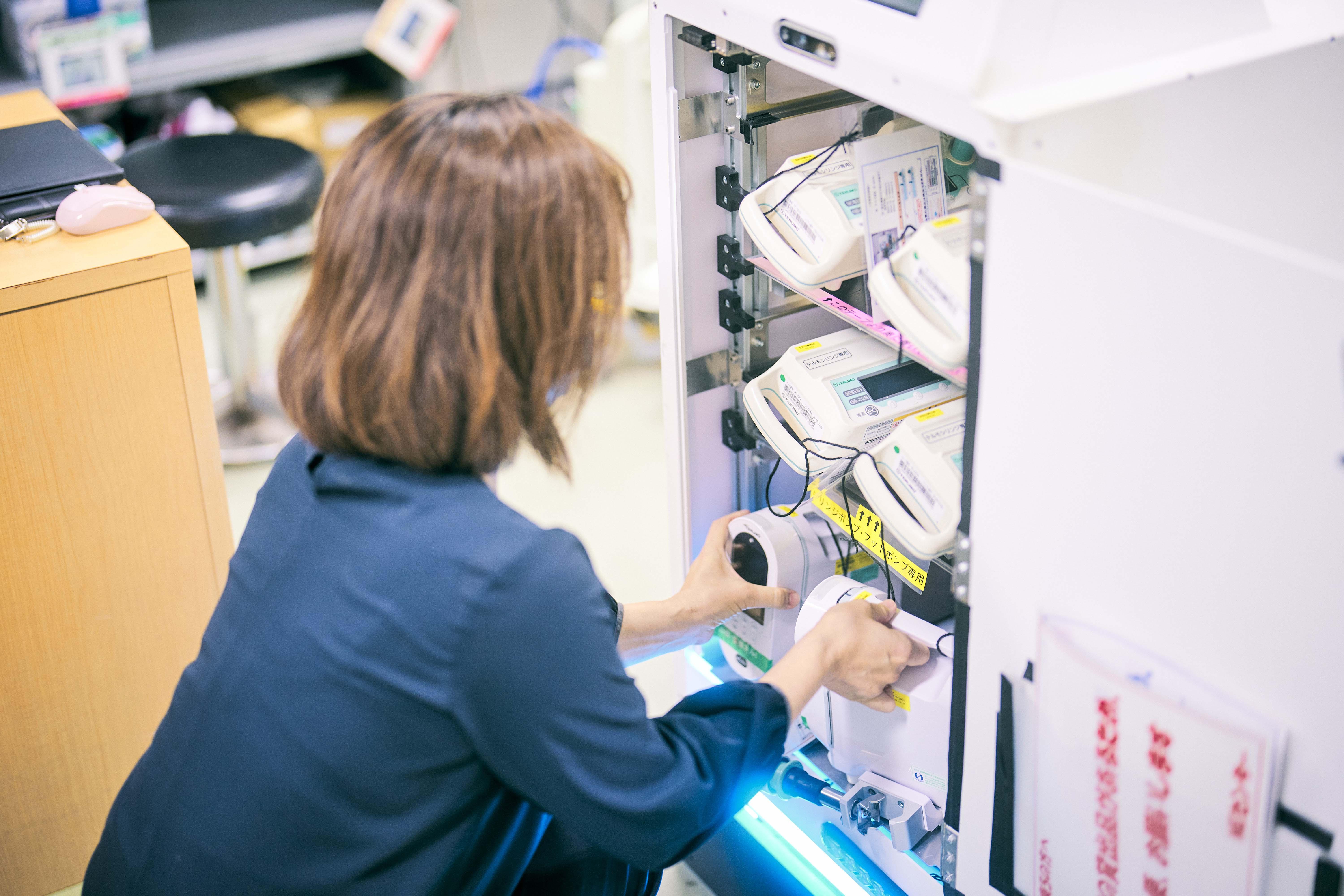
As they witnessed nurses doing their utmost for patients whose conditions had suddenly deteriorated, Toyota’s team members acknowledged that “nursing is hard work.” These sincere sentiments touched the nurses. Such interest and empathy gradually brought the two sides closer together, helping to bring kaizen into established medical care practices.
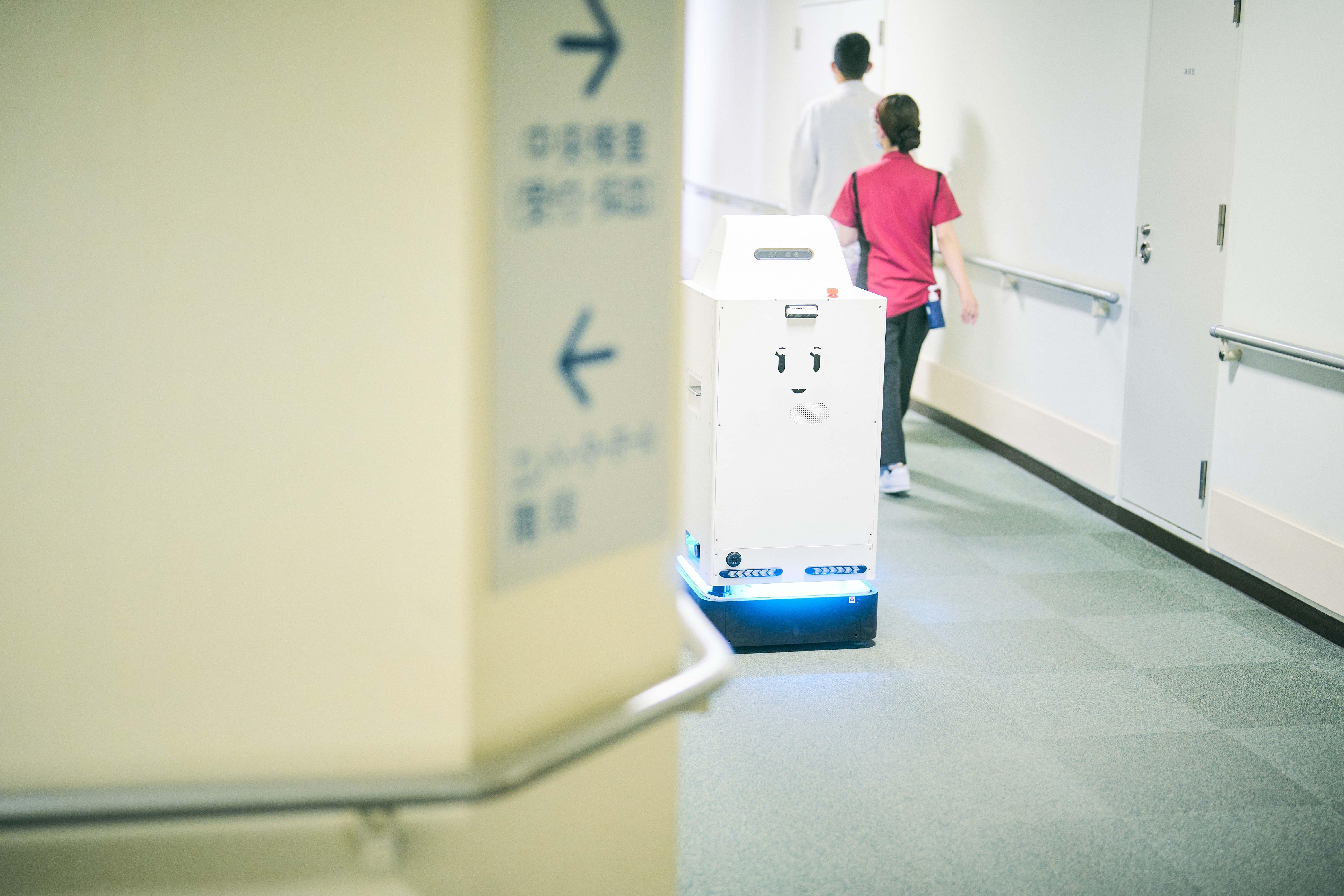
But in this day and age, why settle for a simple box-shaped robot?