
The new Yaris has earned Europe's highest accolade, the Car of the Year 2021 in Europe. Behind this success lies Akio's' commitment to post-disaster recovery, and the power of Tohoku manufacturing.

The Car of the Year 2021 in Europe is awarded to the year’s best car, as voted by 59 journalists from 22 European countries. Rising above a highly competitive field, this year’s crown was claimed by the Yaris.
Why was the Yaris selected in Europe? What had caught the eye of the jury? Following on from his interview with Chief Engineer Suezawa, Toyota Times reporter Kyonosuke Morita spoke with Masahiko Nagasaka, General Manager of the Toyota Motor East Japan (TMEJ) Iwate Plant that produces the Yaris in Japan.
News of win brings fist pumps all round
“We were absolutely thrilled about the win in Europe!” replied a beaming Nagasaka when asked how he felt upon learning of the Car of the Year result. On the day that the news arrived, the plant’s team, from section managers up, broke out into fist pumps at the morning meeting. This joyous scene was captured in a photo that was shared with Toyota’s another Yaris production plant in France.
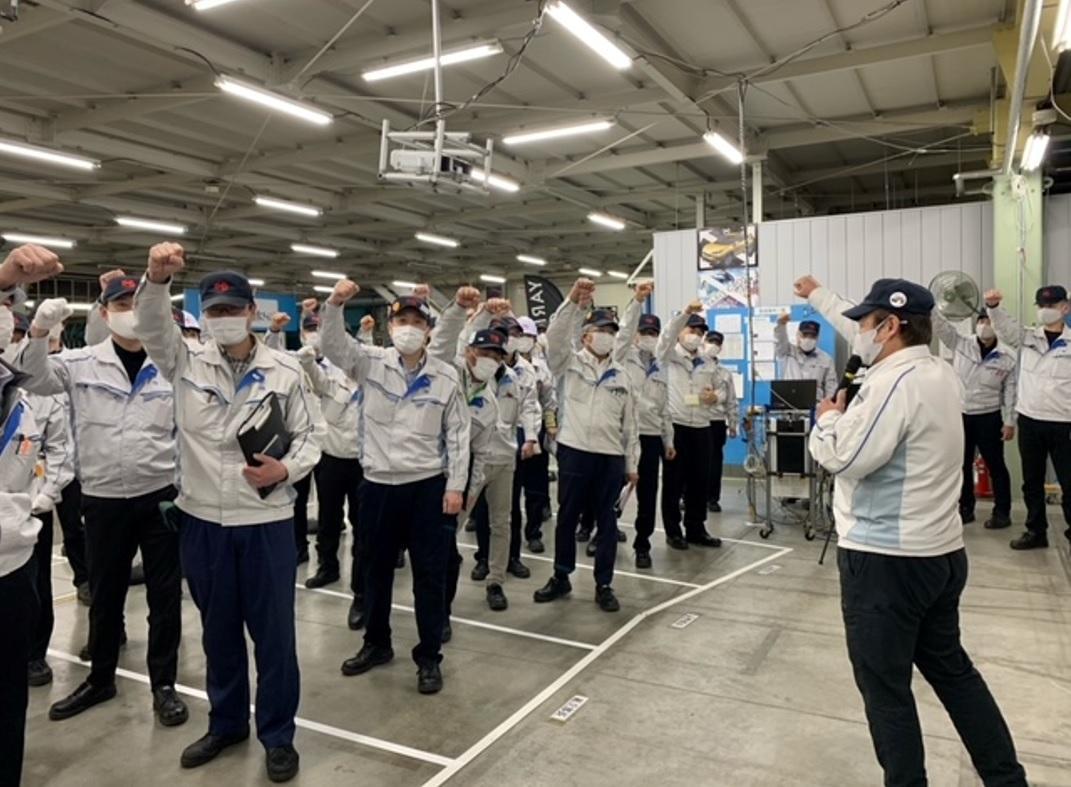
Nonetheless, winning Car of the Year 2021 in Europe did not come as a bolt out of the blue. Nagasaka felt confident about the result.
Nagasaka:
Of course, I had high hopes. I think the Yaris has a lot going for it as a product, and I was sure that genuine autobahn-driving (European) customers would recognize that quality.
Morita:
You mean that the Yaris’ true quality comes out in such demanding environments?
Nagasaka:
Yes. Despite being compact, it is powerful, with top-level safety features that scored five stars in the Euro NCAP (Europe’s safety assessment program). And being a hybrid, it is also environmentally friendly. I was sure that these aspects would be recognized.
At the same time, Nagasaka expressed disappointment about the Yaris’ third-place finish in Japan’s Car of the Year.
Nagasaka:
Given the extremely positive feedback from our customers about fuel efficiency and safety performance, I felt that we might take Japan’s Car of the Year as well, but the result was disappointing… And yet, we’ve stayed at number one in terms of sales, which shows that customers have embraced the car, not just in Europe but in Japan as well.
Having driven the Yaris and experienced its appeal first-hand, Nagasaka has complete confidence in the car.
Morita:
Reading comments from the Car of the Year jury, I get the sense that they ranked the Yaris highly in many areas, including fuel efficiency, noise, and driving pleasure.
Nagasaka:
There’s style as well. It’s compact but very powerful when you get behind the wheel. When the Yaris was launched, I was able to test it out on our track, which confirmed for me what a great car it is.
In Japan, the Yaris also became our first hybrid 4WD, which had been eagerly awaited in snowy parts of the country. We sent them out from the plant with confidence, knowing the cars will be loved by people in the region, here in Tohoku and Hokkaido.
Morita:
So from the perspective of the people making the car, everything has gone as hoped?
Nagasaka:
You could say that. We are producing large volumes, which comes with the challenges of operating the plant at high capacity, but we all take heart in the fact that we are able to deliver such good products to our customers.
Competitiveness gained through tireless effort
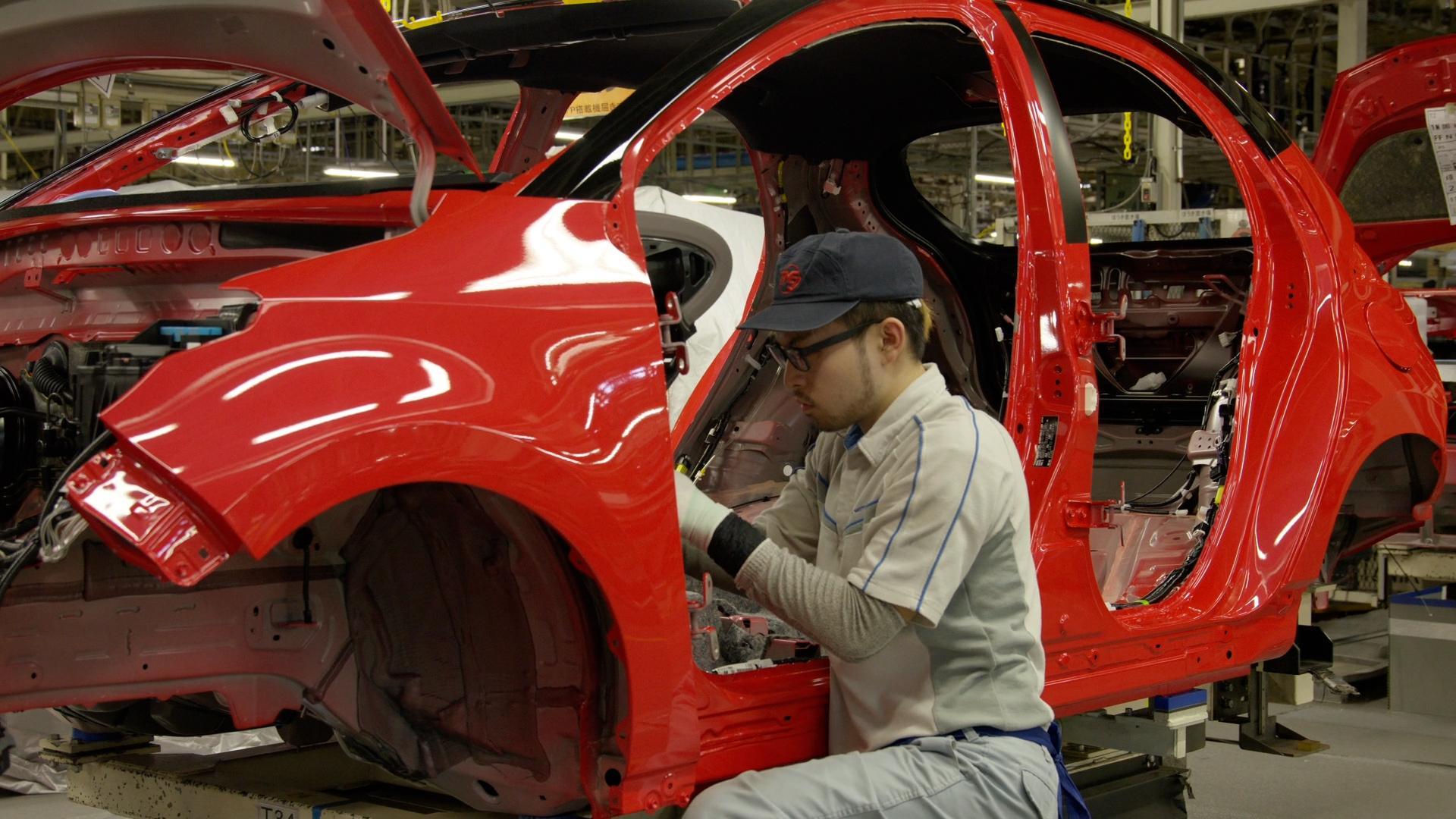
Currently, Toyota is the only company producing finished vehicles in Tohoku. Compared with areas like the Chubu region where Toyota has its headquarters and many car manufacturers and parts suppliers operate, Tohoku finds itself at a constant disadvantage. So why is the Yaris, an important model for Toyota, being produced at the Iwate Plant? Nagasaka believes this comes down to the plant being ‘highly competitive’.
Morita:
I’m sure it was not an easy road, getting to the point where you can produce something like this, but how do you look back on it?
Nagasaka:
I feel that producing the Yaris requires a competitive plant. Our Iwate Plant is located in one of the more remote areas in Japan, which puts us at a disadvantage in terms of logistics and cost. Despite this, we are competitive enough to be entrusted with producing the car.
This is partly due to the guidance of those who were here before us, who took various measures to increase competitiveness and ensure that cars would continue to be made in Iwate. We have gotten to where we are today by building on their efforts, for which I am very grateful.
Morita:
When you talk about building up competitiveness, what does that mean in practice?
Nagasaka:
There was the Great East Japan Earthquake, and before that the financial crisis. The Iwate Plant’s first line went into operation in 1993, followed by a second in 2005. When the financial crisis hit, global production was cut, including at Toyota, so for a time we couldn’t make cars no matter how badly we wanted to. To continue making cars amid such circumstances, our manager at the time was determined that the plant must offer the best in productivity and quality.
If we managed to be number one (within the Toyota Group), Toyota’s global stature would put us among the best plants in the world. This idea drove everyone on the team to work towards making the plant highly competitive. The plant includes stamping, body shop, painting, assembly, inspection and plastics – we aimed to be number one in productivity and quality across all these areas, and we actually achieved it.
Two ways to improve competitiveness
Saying that one will become ‘the best in the world’ or have ‘the world’s best technologies’ is easy enough, but actually doing so from Tohoku is another story. How did the Iwate Plant go about boosting its competitiveness? Nagasaka shared two of the plant’s initiatives.
The first was building their own equipment in the form of ‘karakuri’, hand-made mechanisms that improve work processes. Wherever possible, karakuri do not rely on electricity or other power sources; instead, they are ingenious solutions to small challenges, such as aligning parts or making tools easier to retrieve, all of which contribute to boosting efficiency.
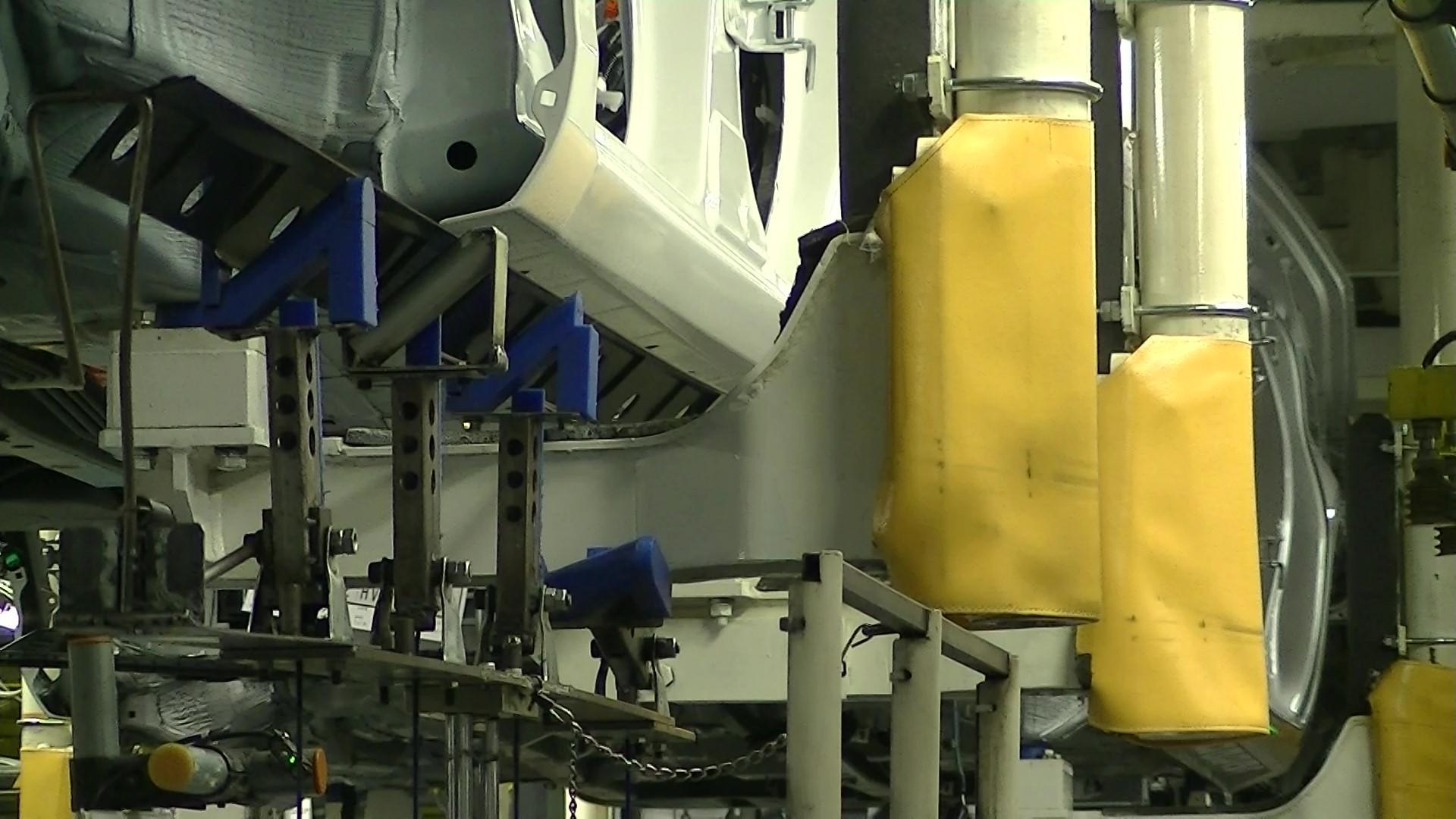
We are using karakuri to create our own equipment. Building the equipment ourselves means we can quickly repair anything that breaks down, and lets us recreate the exact motions we had in mind. Using karakuri to create equipment helps us to improve productivity.
Another of the plant’s initiatives is sequential production and delivery.
The color and specifications of cars to be made on the production lines are finalized a few days prior to assembly, and the parts suppliers are notified. In the past, this was determined just hours before, which forced suppliers to keep vast inventories to accommodate multiple vehicle models and specifications.
Setting the production sequence in advance, however, greatly reduces inventory space, as only the parts needed on a given day are delivered.
The cooperation of parts suppliers is crucial to running this sequential production and delivery system. This is where the plant’s Tohoku location comes into play. When a parts supplier serves multiple car manufacturers, tailoring deliveries to suit a single plant becomes difficult.
In Tohoku, however, Toyota is the only company producing finished vehicles. This means that many local parts suppliers deal only with Toyota’s plant, allowing for close coordination.
Nagasaka:
We work with suppliers to operate a ‘sequential production and delivery’ system, in which parts delivery is synchronized with vehicle production. This approach allows both ourselves and our suppliers to avoid surplus inventory during production. It is only possible here in Tohoku, and helps to make us more competitive.
I believe that both karakuri and ‘sequential production and delivery’ contribute greatly to our competitiveness.
Words of encouragement from local communities
Following the 2011 earthquake, President Akio Toyoda considered what Toyota could do to assist recovery. He decided to turn the Tohoku region into the company’s third-largest domestic production base, after Chubu and Kyushu.
Visiting the affected area just two weeks after the disaster, he realized that the recovery would take a long time, so the support needed to be sustainable in the long term. This led Toyota to construct a plant and set up an academy for developing talent and skills in Tohoku, as a way to establish manufacturing foundation in the region.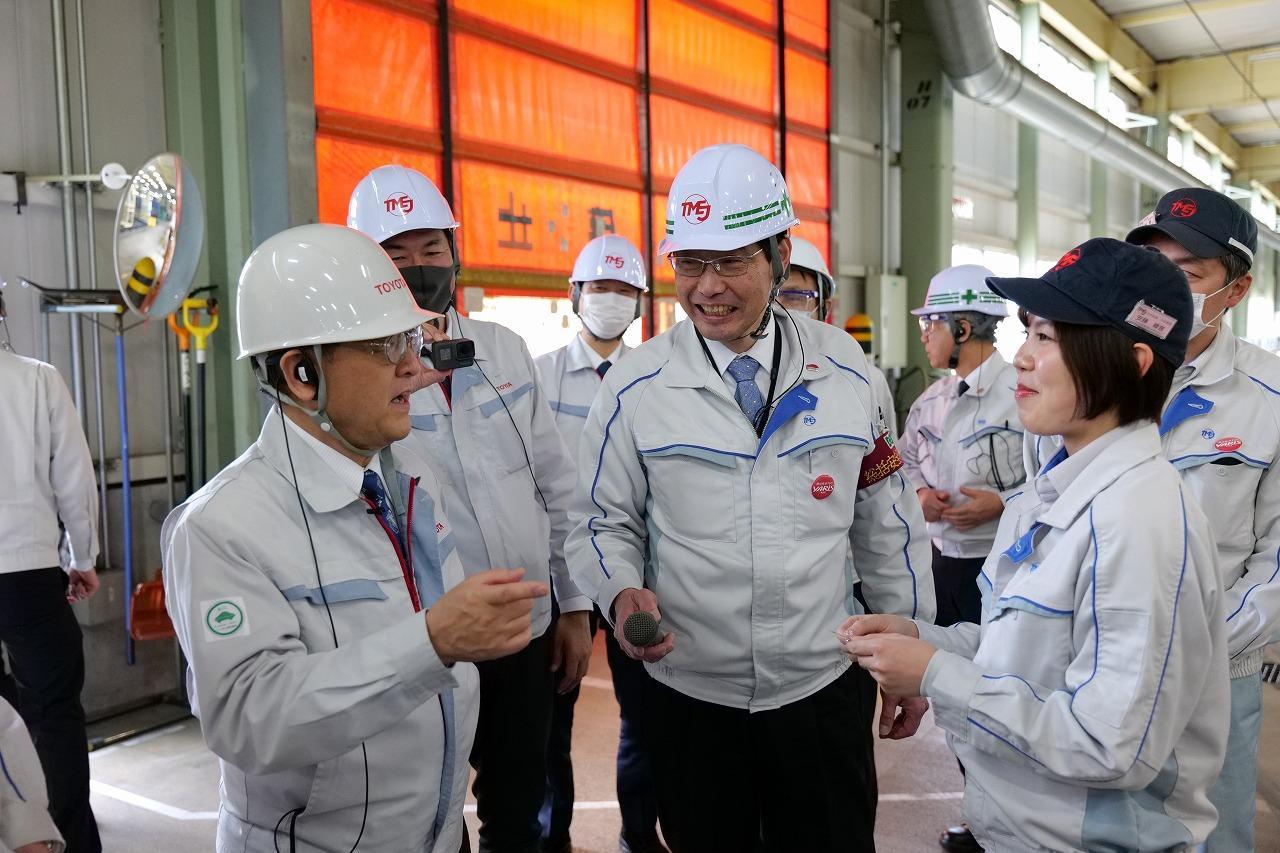
And now, in the milestone tenth year since the disaster, the Tohoku-built Yaris has won the Car of the Year 2021 in Europe and gained global acclaim. How does Nagasaka feel about this turn of events?
Nagasaka:
Winning the Car of the Year was a great confidence boost for us. Our plants here in Iwate and Miyagi are able to produce cars thanks to the support of local communities. We received encouragement from our suppliers and various other companies, governments, and even local residents, who congratulated us on the success. This made me really happy, and I believe it will spread throughout Tohoku to benefit the entire region.
Nagasaka himself comes from Tsugaru, Aomori, the region’s northernmost prefecture. His love of Toyota cars spurred him to join TMEJ (then Kanto Auto Works). He believes the Tohoku region is well suited to manufacturing cars.
Morita:
Being from Aomori yourself, do you have a strong attachment to the Tohoku region?
Nagasaka:
The people of Tohoku are very earnest. Many are also passionate and warm-natured, as can be seen in the many local festivals, from north to south – Nebuta in Aomori, Sansa in Iwate, Tanabata in Miyagi, and many others in Akita, Yamagata, and Fukushima. By bringing such people together to create cars in Tohoku, I hope to continue contributing to the area’s post-disaster recovery.
Morita:
How does this Tohoku culture tie into the production of compact cars?
Nagasaka:
Being earnest workers, the people of Tohoku tend to question how things are done and look for ways to improve, offering lots of suggestions. This attitude links in with the karakuri that I mentioned earlier. We have about 3,300 employees at the Iwate Plant, each one acting as a ‘karakuri-person’ responsible for creating the things they use. I think Tohoku people have an aptitude for these kinds of things.
Indeed, Tohoku is becoming a hub for producing compact cars, which Akio considers as the standard for ‘making ever-better cars’. Nagasaka shared his feelings about the idea of making these cars in Tohoku.
Nagasaka:
The first car I bought after getting my license was a Starlet, the predecessor of today’s Yaris. You begin with a compact car and enjoy what it has to offer before gradually saving up and buying bigger cars. But then, as you get older, you come back to something compact. That’s why I feel that compact cars will survive for a long time. I’m very pleased that we are able to build them here in Tohoku.
‘Tohoku manufacturing’ shines in France
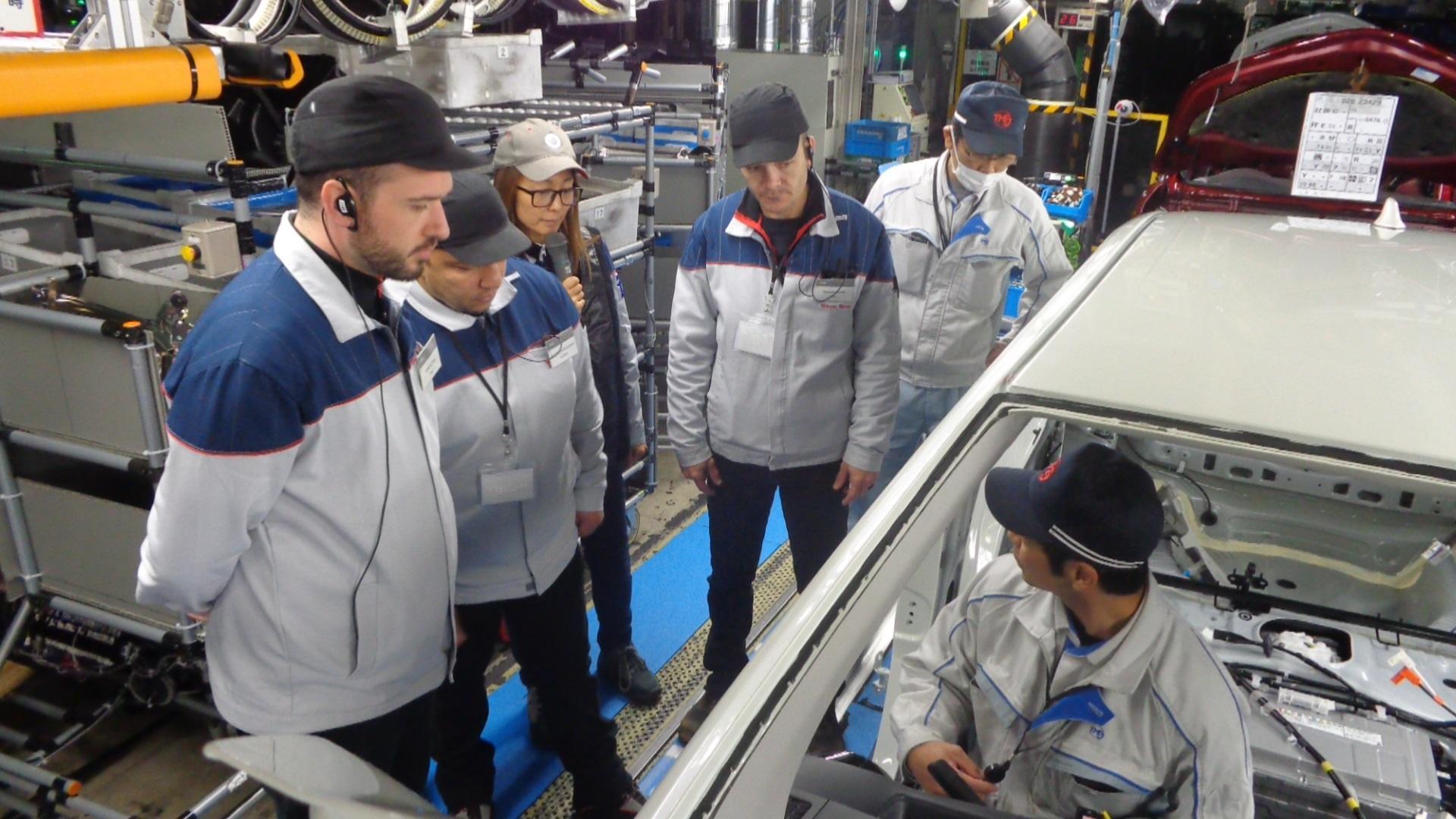
Along with the Iwate Plant, the Yaris is also being produced in France. How well has Tohoku’s manufacturing, underpinned by ‘earnest, passionate’ people, translated to France?
Nagasaka:
Actually, this Iwate Plant is the parent plant of our plant in France. Eleven members of our team were transferred there, with another fifteen visiting to provide support for production, quality, and operating improvements.
Even though we’re in different countries we are making the same cars, so there is also a kind of friendly rivalry. We spur each other on to build better cars.
Morita:
Did you also take the ‘karakuri’ idea across to the French plant?
Nagasaka:
We did. We also have staff visiting from France to see what we are doing here. Naturally, they were taught about karakuri and had a chance to create some as well. They returned home as certified karakuri-persons. As a result, karakuri can be found on equipment throughout the French plant.
Morita:
And they call them ‘karakuri’ in France as well?
Nagasaka:
Yes, they do.
It is the French plant that produces the Car of the Year-winning Yaris for the European market. And yet, tracing the car back to its origins, one will find the manufacturing expertise of Tohoku pulsing through its veins.
Delivering more Tohoku-built cars
Morita closed the interview by asking Nagasaka about his goals for the future.
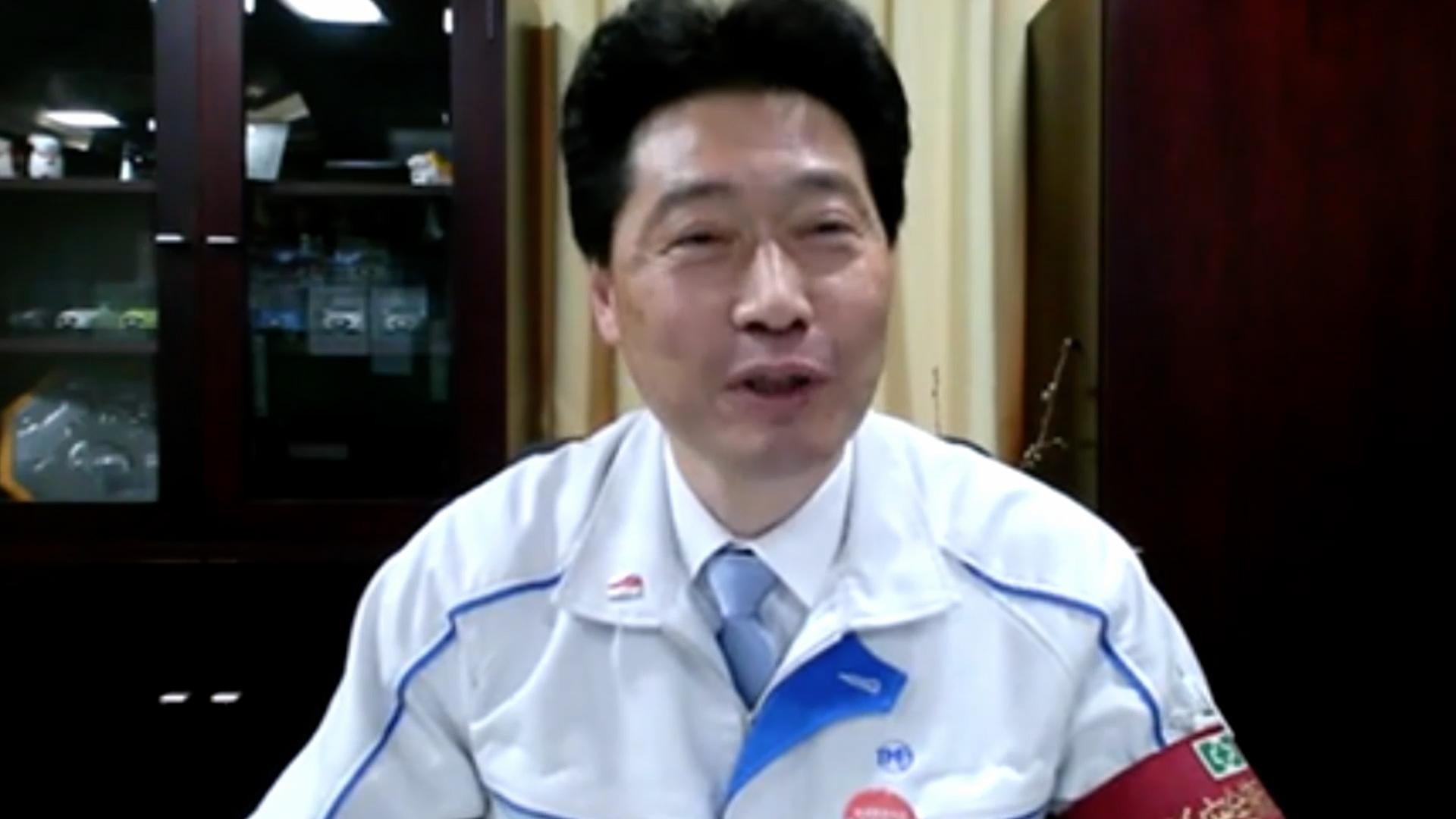
Morita:
What is your vision and goals for the future?
Nagasaka:
I’d like to see this Iwate Plant delivering more and more Toyota cars to customers, producing smiles for all. I want to create more Toyota fans.
Not only Iwate, but also Miyagi, Aichi, and Kyushu – I want to get more customers behind the wheels of all these Toyota cars, so that they can appreciate the quality of our products.
Morita:
You have already managed to build up the manufacturing capabilities this far, and received recognition from many directions. Do you think there is still room (for improvement)?
Nagasaka:
Yes, I think so. We have expanded our network throughout the region and are working to increase the number of local suppliers. I hope that Tohoku will become an even bigger player in car manufacturing. I believe the people of Tohoku will join us in making that happen, so we have to give more back to the community beyond car manufacturing as well.
Morita:
Once again, congratulations on winning the Car of the Year in Europe 2021.
Nagasaka:
Thank you very much.
Delving deeper into the Yaris’ production revealed that the car’s high quality is underpinned by Tohoku’s manufacturing prowess. In the wake of the Great East Japan Earthquake, Akio decided to turn Tohoku into a production hub for compact cars in an effort to help the region recover.
His vision was embraced by the people of Tohoku, whose hard work and ingenuity made the area more competitive. These efforts were in turn passed down to Toyota’s plant in France, culminating in the outstanding achievement of winning the Car of the Year 2021 in Europe. Morita’s interview brought home the fact that a single car can carry the hopes of innumerable people.