
The fuel may have changed from gas to liquid, but Toyota's development is as agile as ever. See how far the car and hydrogen stations have come in just two months.
Upgrade III: Faster refueling
Progress can also be seen beyond the car—the mobile liquid hydrogen stations used for refueling received three major upgrades.
Firstly, refueling times were shortened. In this race, the tank’s fuel port was equipped with a shutoff valve developed by Fujikin, a manufacturer of specialized precision valves.
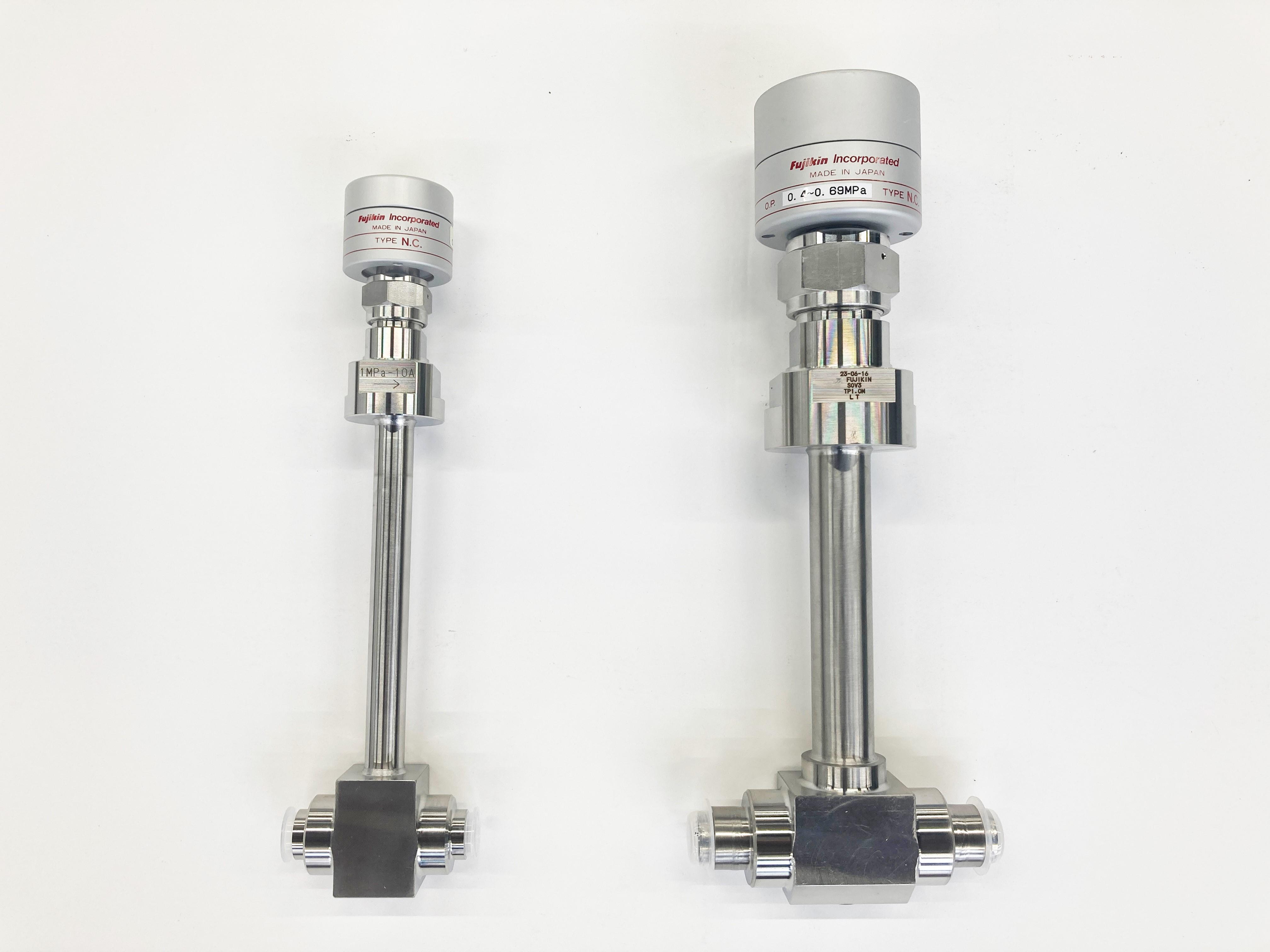
Faster refueling requires larger valves, but increased size typically creates difficulties with sealing.
By developing valve components that resolve these tradeoffs, Toyota cut the hydrogen filling time (i.e., the time when hydrogen is flowing) from 1 minute 40 seconds at Fuji to under one minute.
Upgrade IV: Refueling automation
All of the advances we’ve introduced so far help the team achieve better times and more laps in races.
Yet we must remember that this endeavor is about more than racing, as Toyota aims to commercialize hydrogen-engine cars and create a hydrogen society.
From that perspective, hydrogen refueling cannot always remain the preserve of specialized technicians trained in the unique environment of racing.
To that end, Toyota is working to automate the refueling operations of mobile hydrogen stations.
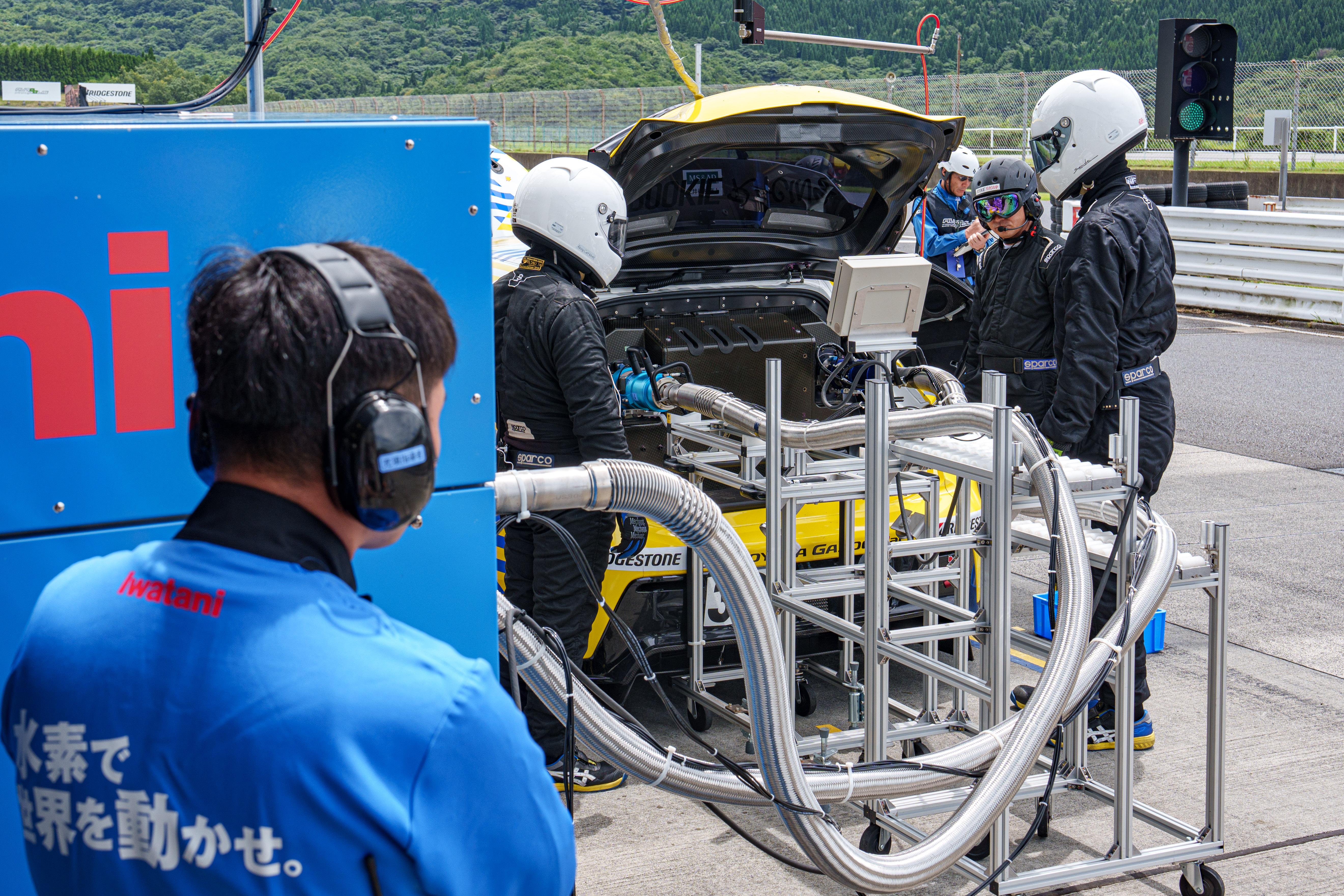
At the last Fuji race, mechanics handled every aspect, from opening and closing the refueling valve to stopping the flow when the tank was full.
This time around, nine of the 14 processes were controlled electronically based on information about the status, temperature, and pressure of the filling joint, as gathered by sensors during races and testing.
Now, mechanics only need to insert the joints and press a button to begin filling hydrogen; when the tank is full, a light will notify them that the joints can be removed.
Upgrade V: Lightweight refueling joints
Toyota also worked with Iwatani to reduce the weight of filling and return joints.
Until now, these were made of strong stainless steel that resists hydrogen embrittlement, but after confirming the design’s safety and reliability, engineers switched to using aluminum for parts that aren’t exposed to hydrogen.
Added to this, the hose itself was redesigned to eliminate potential dangers, doing away with the need for a safety cover that had been used to prevent finger injuries.
These efforts reduced the weight of filling joints from 8.4 kg to 6.0 kg and return joints from 16.0 kg to 12.5 kg.

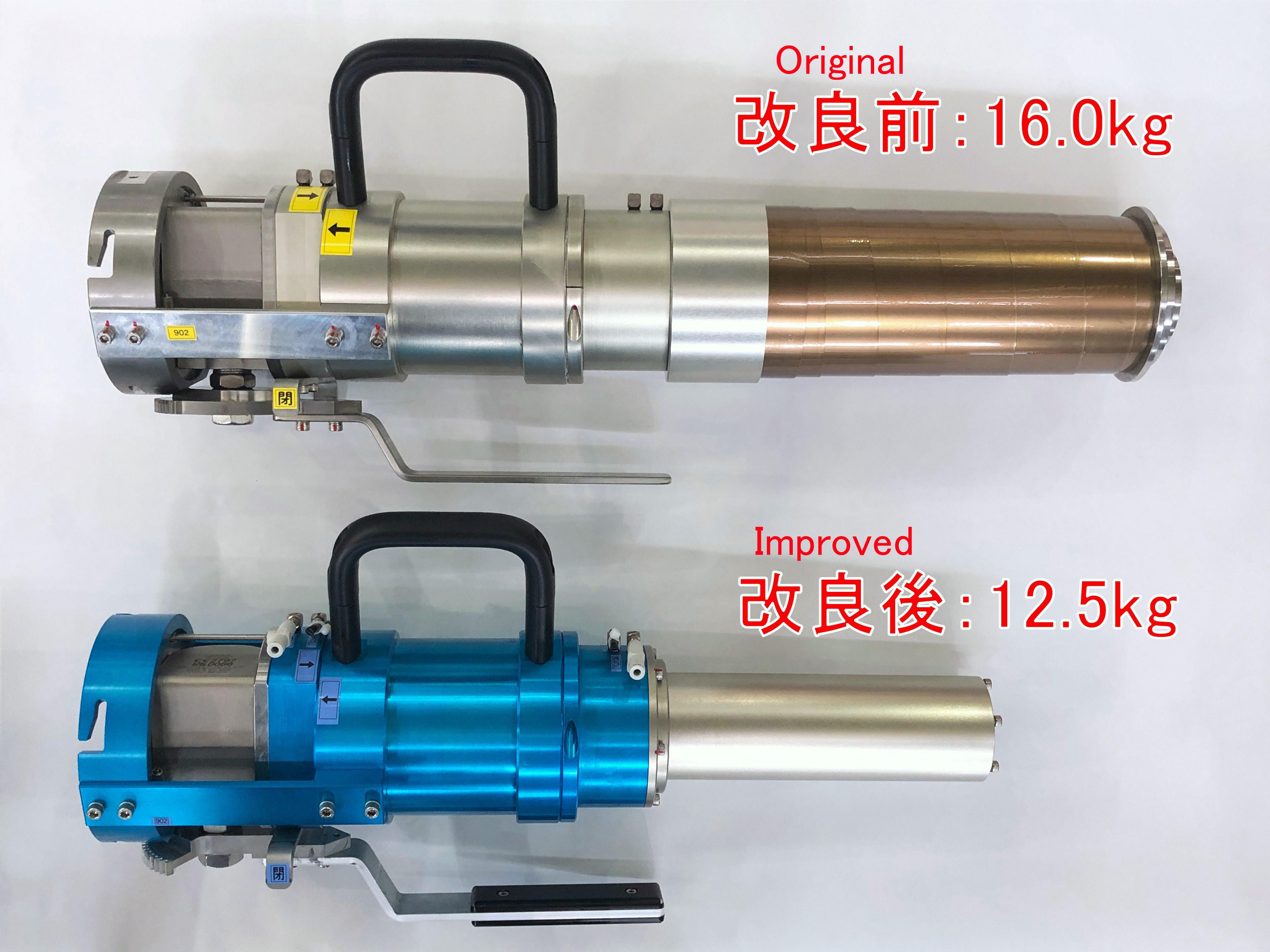
The plan is to eventually bring the weight of return joints in line with filling joints, which are currently half as heavy.