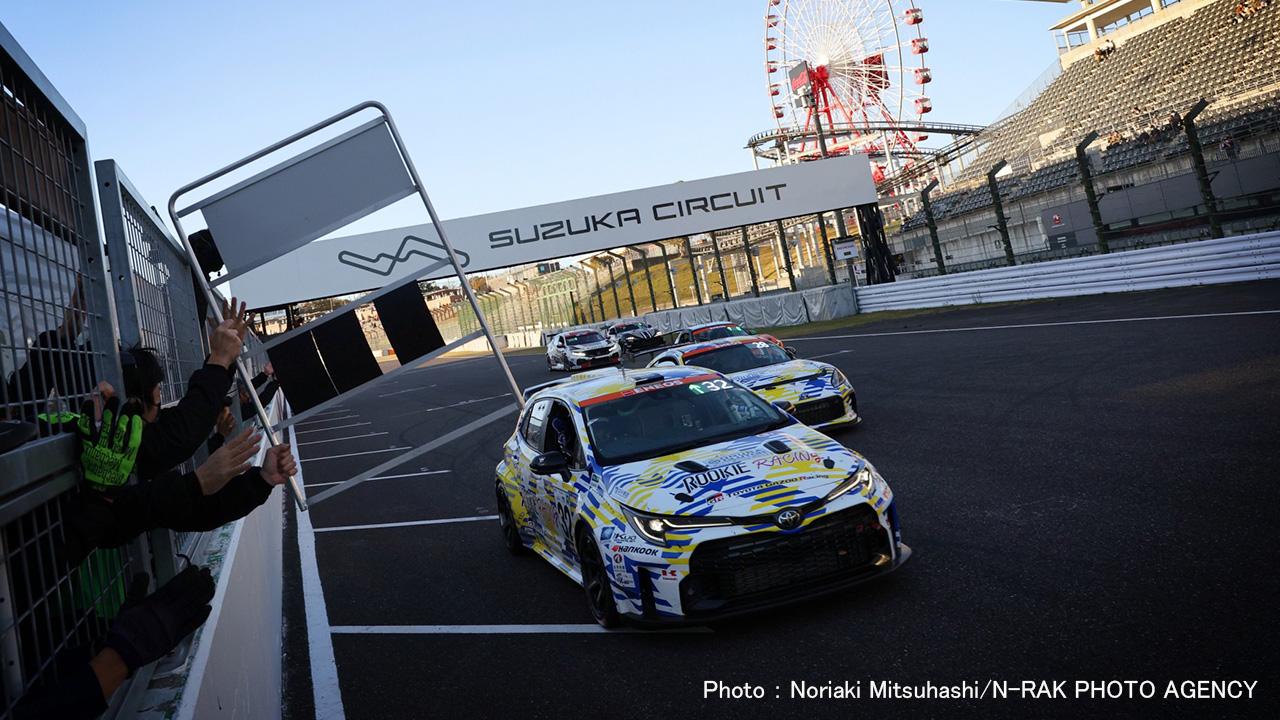
With the Super Taikyu Series, we are taking on the challenge of achieving carbon neutrality. This report summarizes the evolution of the hydrogen engine and the deepening of partnerships and teamwork during the second season of racing.
Current location of the hydrogen engine on its road to production
At the 24-hour race held at Fuji International Speedway in June, and using the example of climbing Mt. Fuji, the hydrogen engine was described as being at “station 4” on its way to commercial production. Six months have passed since then, so how much progress has been made?
Tomoya Takahashi, GR Vehicle Development Division’s General Manager, expressed the following.
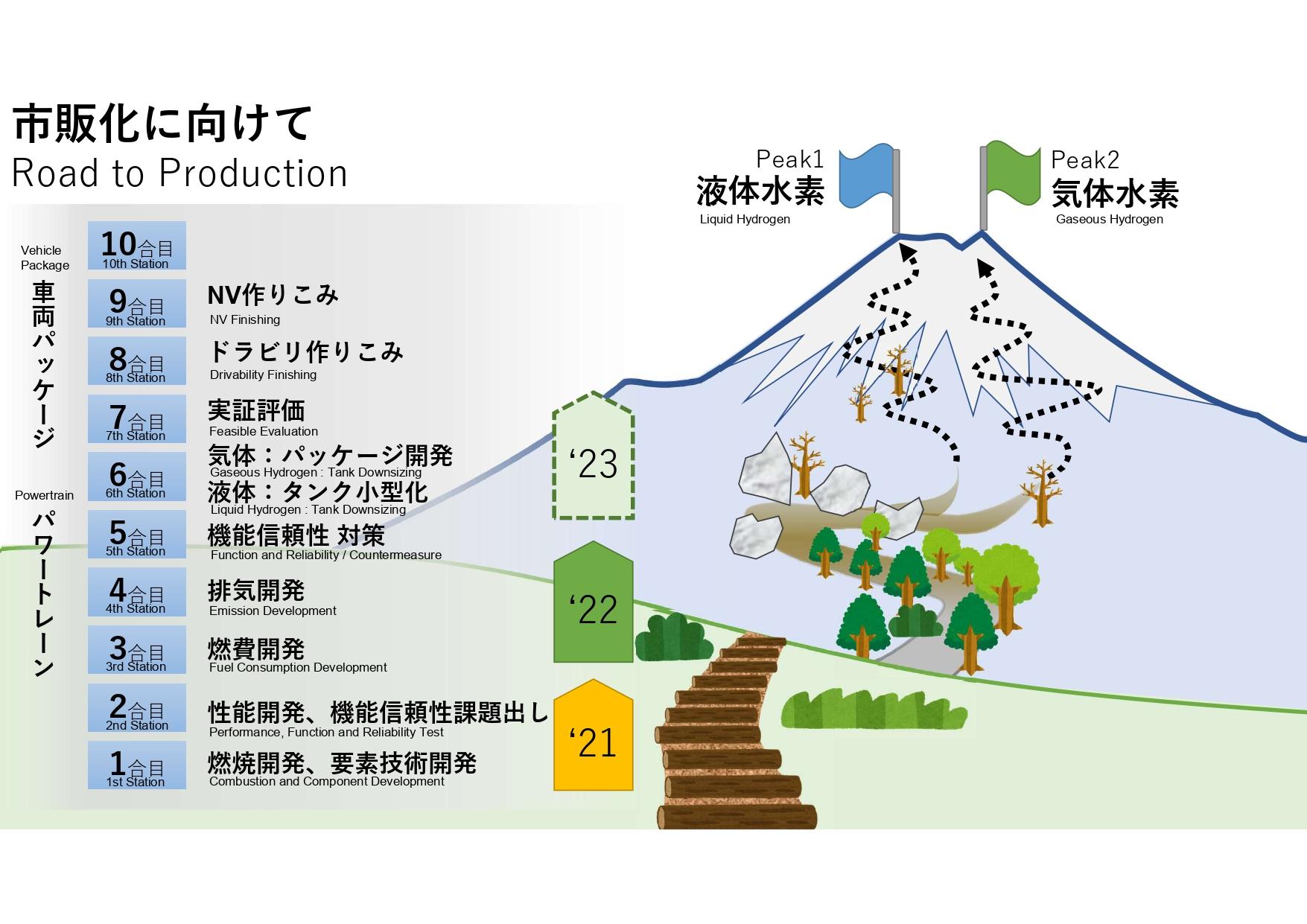
Takahashi
During the 24-hour race, we talked about being around the fourth station. However, since then, development has continued, and there is no doubt that we are now going from the fourth to the fifth station.
Teru Ogawa, Deputy General Manager of the GR Powertrain Development Div., continues.
Ogawa
Aiming for mass production, emission development at the fourth station has started in parallel with development for the race. A new dedicated team has been established to accelerate development.
The fifth station’s functionality and reliability measures are issues we found to be caused by the high-rpm, high-load environment used at Super Taikyu races. These issues are also being worked on via mass production development by the new team in parallel with the race.
At the sixth station, we have tank downsizing. This is an effort to increase the driving range with liquid hydrogen.
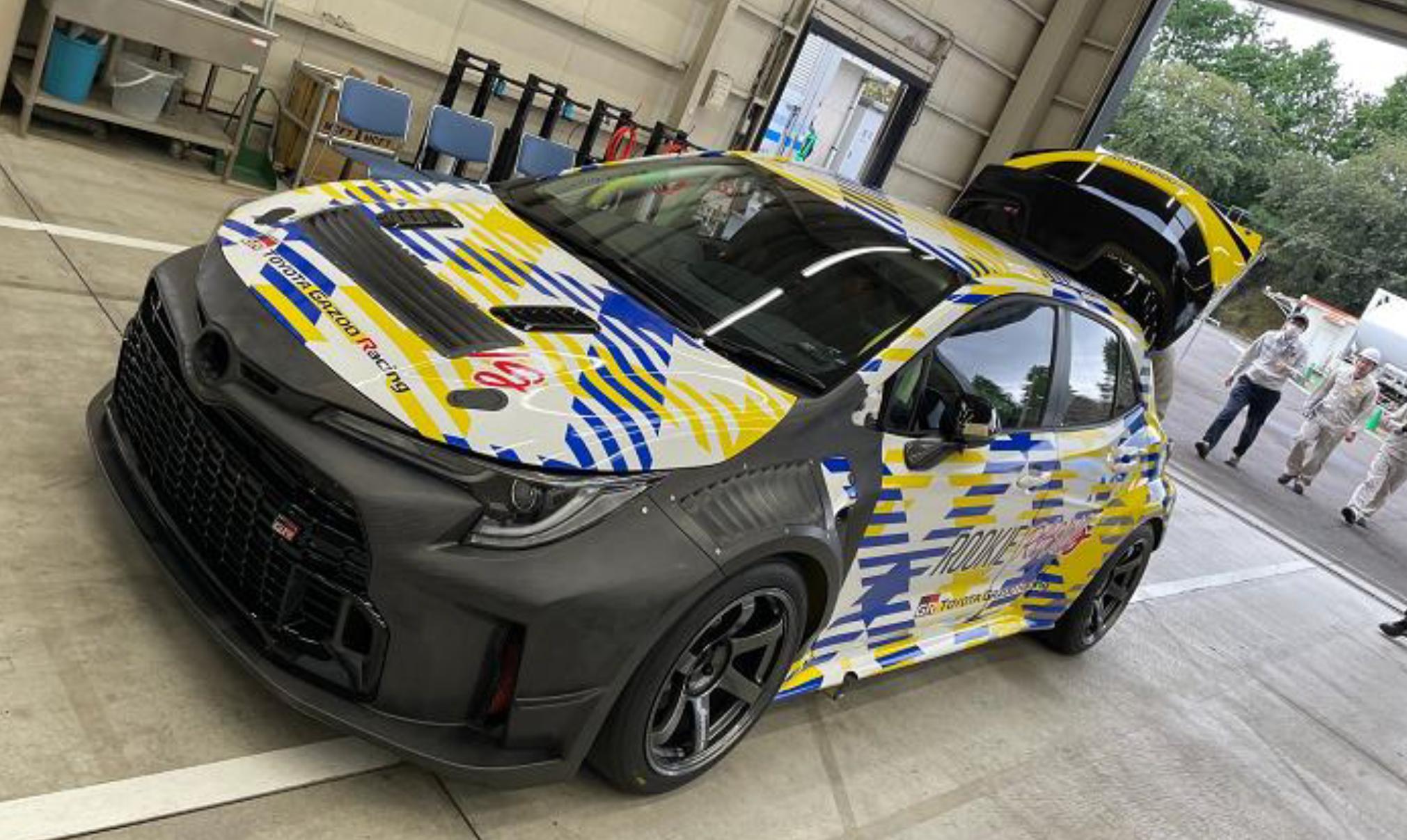
I think liquid hydrogen will be an even more difficult road to travel, so I would like to start by releasing a car that uses gaseous hydrogen.
We have started moving toward the fourth, fifth, and sixth stations in our climb up the mountain. Although it is now possible to safely run the engine in the next step after working on the first station’s problems, such as abnormal combustion, we have yet to reach the stage where we have fully mastered the underlying mechanics.
We would like to improve the road conditions so that our partners in the hydrogen-use area can climb the mountain with peace of mind.
In the 2023 season, we would like to continue to forge a path ahead while paving the road from station one to four, which is the section represented by log stairs in the previous illustration, to make that section passable for vehicles.
The team explained that the road to commercialization is just like climbing Mt. Fuji in that the closer you get to the summit, the steeper and harder the climb becomes.
A growing group of like-minded partners working to accelerate the move toward a hydrogen society
Through the Super Taikyu Series in 2022, the number of partners producing, transporting, and using hydrogen has increased.
First, let’s look at some partners who are producing hydrogen. In addition to those who participated until last year such as Iwatani Corporation, Taiyo Nippon Sanso, Namie Town in Fukushima Prefecture (FH2R), Toyota Motor Kyushu, Obayashi Corporation, HySTRA, in which Iwatani Corporation, Kawasaki Heavy Industries, and Electric Power Development Company all participate, and Fukuoka City, newly joining members this season are Yamanashi Prefecture, Yamanashi Hydrogen Company, and Kitakyushu City.
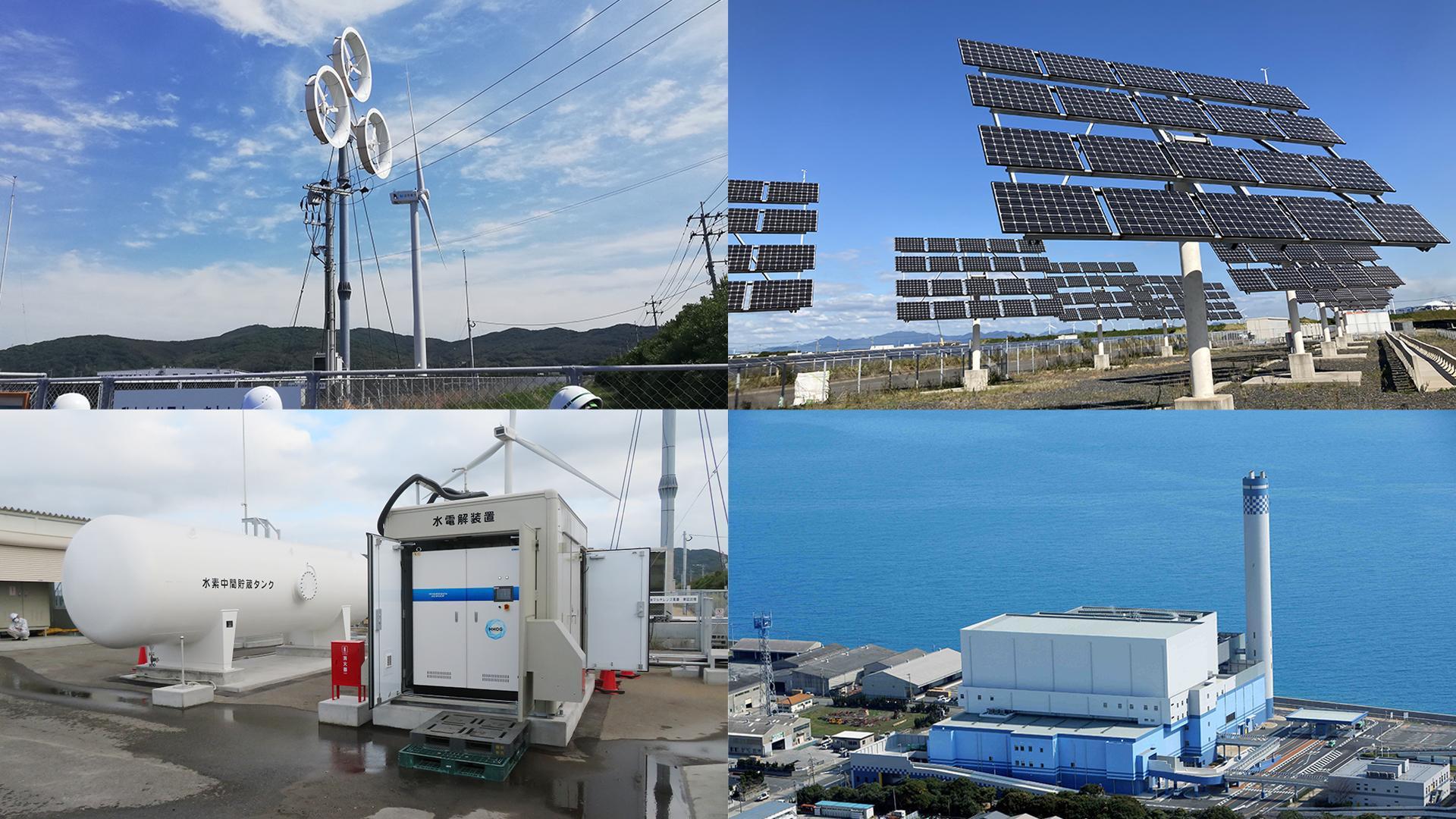
Partners involved with transportation include Toyota Transportation’s biofuel trucks and Commercial Japan Partnership Technologies’ (CJPT) FC light-duty trucks, which are taking on the challenge of carbon-neutral fuel transportation.
In particular, the latter’s FC light-duty trucks have increased transportation efficiency by a factor of 5.5 and can transport a large amount of hydrogen at one time. Transport will be further refined through racing and accelerate the achievement of a hydrogen society.
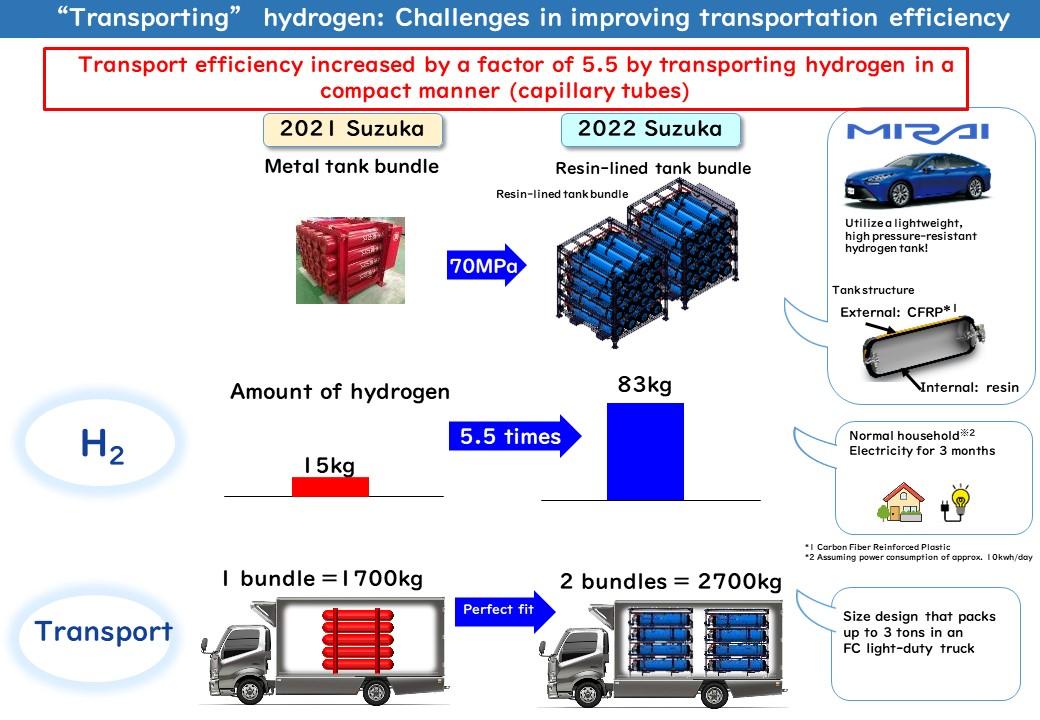
The group of partners involved in use comprises the four major motorcycle manufacturers of Yamaha, Kawasaki, Suzuki, and Honda, joined by Denso and Toyota, all of whom are conducting joint research on hydrogen engines with a view toward installing them in motorcycles.
In September, Kawasaki unveiled a buggy equipped with a hydrogen engine for motorcycles.
Efforts aimed at carbon neutrality are expanding beyond just producing, transporting, and using hydrogen.
Efforts to reduce CO2 generated in the production of parts for the hydrogen-powered Corolla have started, with Kobe Steel and Tokyo Steel joining the circle of like-minded partners.
Starting from the second race, the 24-hour race at Fuji Speedway, the team has used the low-CO2 blast furnace for steel materials developed and commercialized by Kobe Steel to manufacture the suspension member.
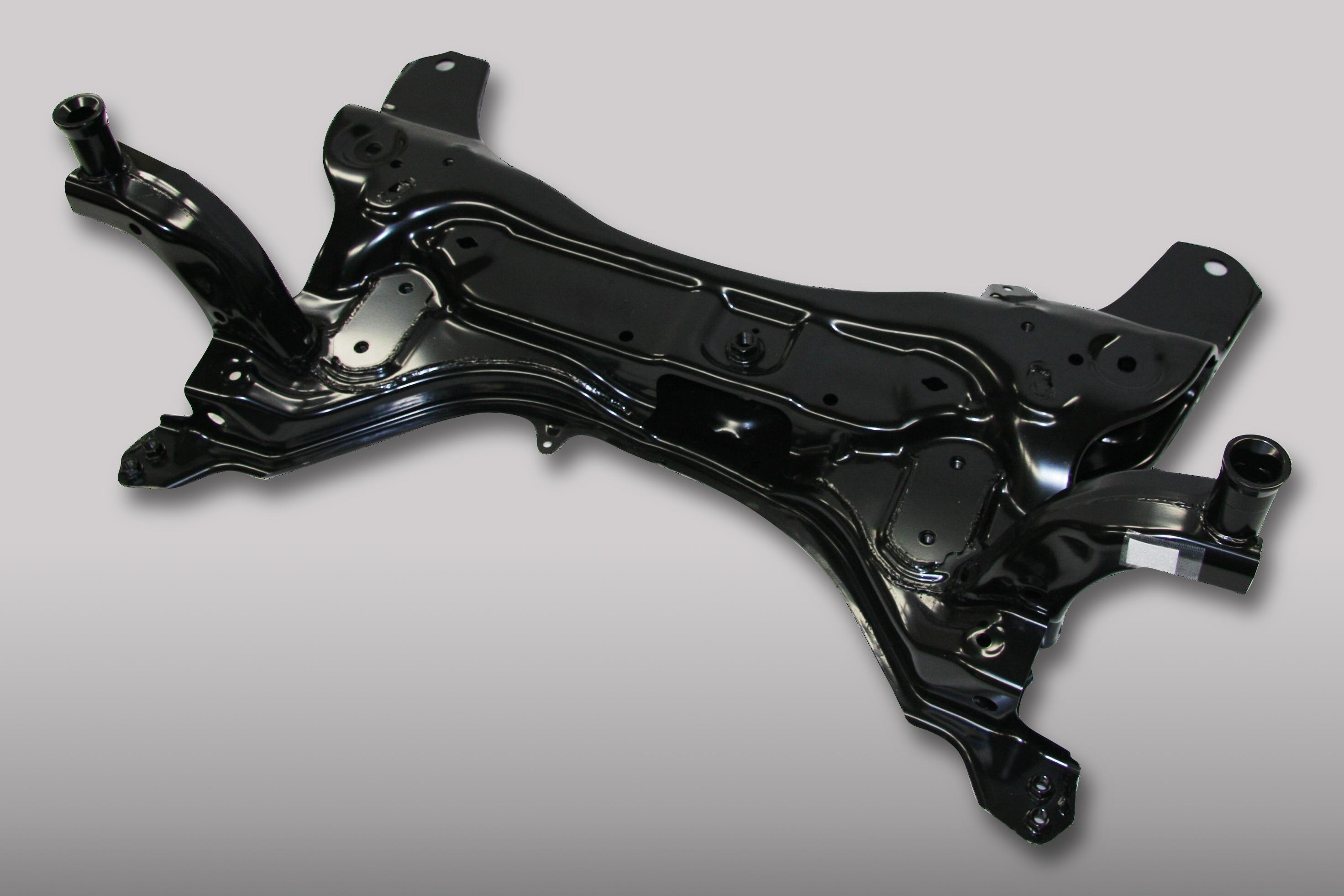
Furthermore, the team used a lower suspension arm made by Tokyo Steel from scrap iron for the sixth race, held at the Okayama International Circuit in Mimasaka City, Okayama Prefecture.
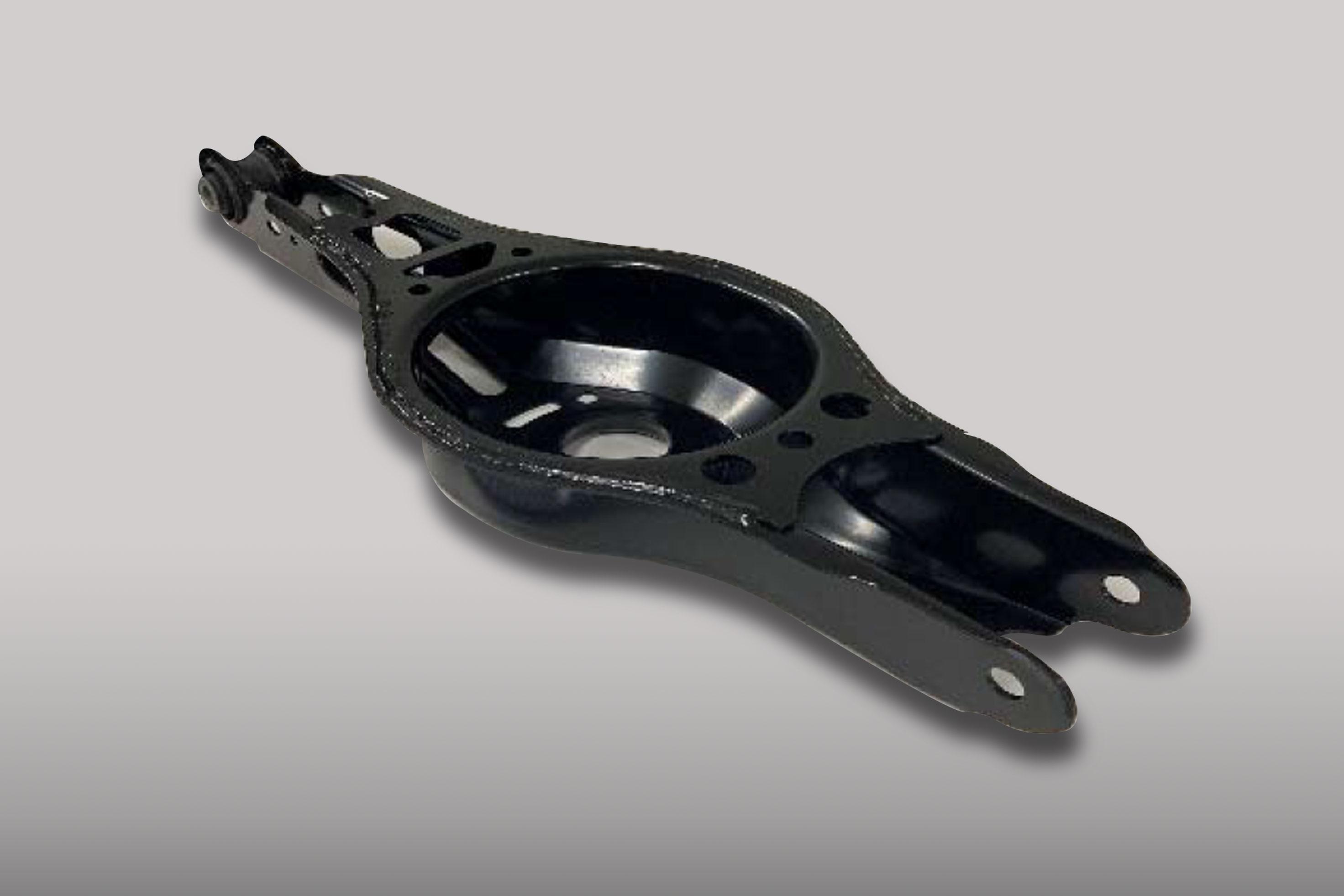