
This story shares an experience at a seafood processing company Toyota helped to improve productivity by applying the Toyota Production System (TPS). How does TPS make frozen squid fresher?

Touni Town is located in Kamaishi City of Iwate Prefecture, in the Tohoku region (northern part of Japan). Facing Sanrikuoki known as one of the top three fishing grounds in the world, it is a quiet fishing town blessed with a natural harbor formed by the ria coastline.
Apart from the landing of salmon, sea urchins and abalones, seaweed and scallops are also farmed, and many of the locals are involved in the fishing industry.
However, the tsunami from the Great East Japan Earthquake in 2011 washed over the 12-meter-high sea embankment and swallowed up the entire town. Almost all of the 470 fishing boats were also destroyed.
But a small seafood processing company, Kamaishi Hikari Foods, stood up to take on the challenges of restoring the fishing industry in the town. The company was founded after the earthquake with the aim of creating employment and a purpose in life for the local people.
As Toyota’s Executive Fellow Shigeki Tomoyama’s visited this company, Toyota Times Reporter Kyonosuke Morita accompanied him and reported on the situation.
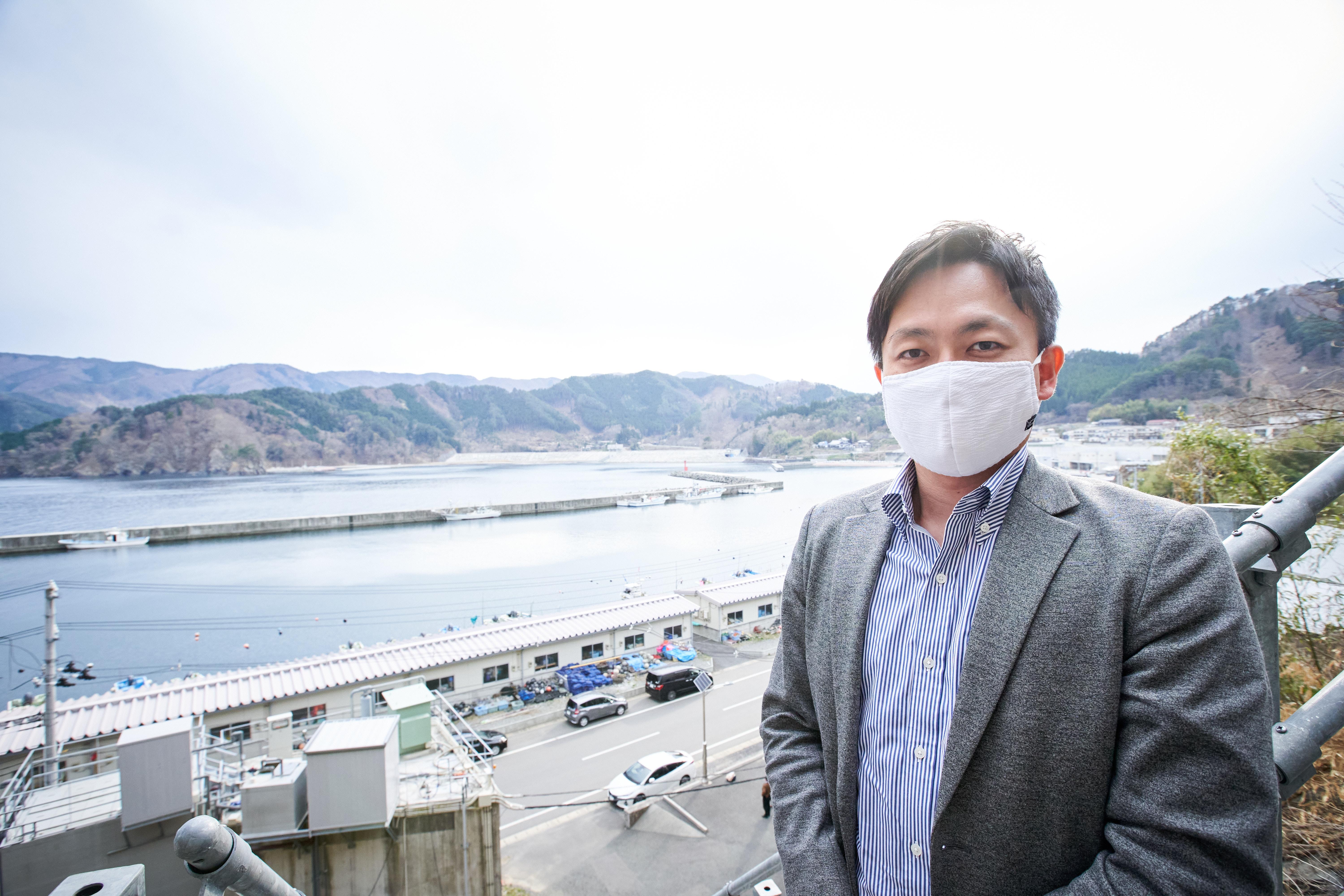
How Did Toyota Get Involved with a Seafood Processing Company in Kamaishi?
Kamaishi Hikari Foods is a small company of seafood processing that holds 51 employees.
Tomoyama decided to visit the company with the intention of “promoting kaizen activities.” Tomoyama built his career as a “kaizen person” in the Operations Management Development Division where the Toyota Production System (TPS) is being promoted. He is a professional in this area, having been Chief Officer of the TPS Group before. To begin with, how did the relationship between Toyota and Kamaishi Hikari Foods start?
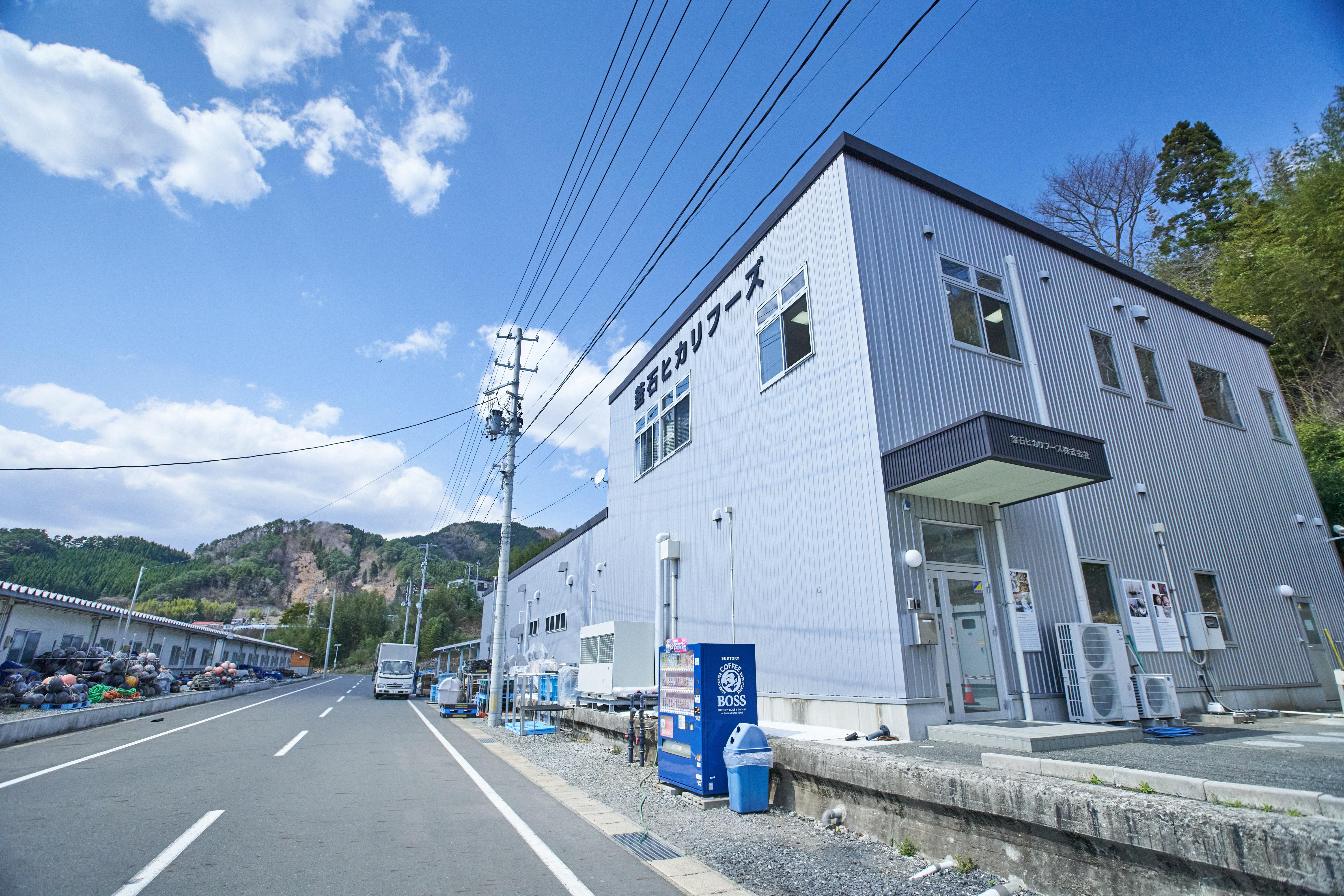
In 2011, President Akio Toyoda visited the disaster-stricken region and came up with the idea that “the best way to become the driving force behind the restoration of Tohoku was to create a future for the region by working with the local people, to establish the foundations for manufacturing and create employment.” This led to the birth of Toyota Motor East Japan (TMEJ) the following year.
After that, TMEJ received an inquiry from Iwate Prefecture asking if they could “help save a disaster-stricken seafood processing company in Sanriku area through deployment of TPS.”
Numerous seafood companies had been damaged by the tsunami. Furthermore, they faced a serious shortage of labor, combined with inadequate supply of seafood, making it extremely difficult to continue their businesses. The fishing village had already been faced with the problem of an aging and declining population, and now they faced the danger of loss of employment.
Despite these difficulties, the people in the area were striving and looking toward the future as they struggled to recover and do everything they could to contribute to the restoration effort.
This prompted Toyota (TMEJ) to take action. Based on a belief that there was something they could do to help, they began the initiative for mutual learning among companies of different industries, even though seafood processing was a completely unfamiliar industry to them.
Why was this initiative called “mutual learning”? It was because the aim was not for Toyota to implement unilateral kaizen activities.
There were also advantages for the employees of TMEJ in that they could expand their horizons by engaging in kaizen activities, while working with people of a different company and coming into contact with their principles. It was hoped that this would lead to fostering people who could inspire others and become dynamic leaders capable of working in any environment.
Tomoyama had the following to say about what this means:
Tomoyama
In evolving from a car company to a mobility company, Toyota needs to collaborate more with companies of different industries in the future. It is not enough for Toyota members to be someone who can only work within Toyota. Their (social) skills can be honed through engagement in these projects by allowing them to see things from new perspectives and acquire skills in building interpersonal relationships.
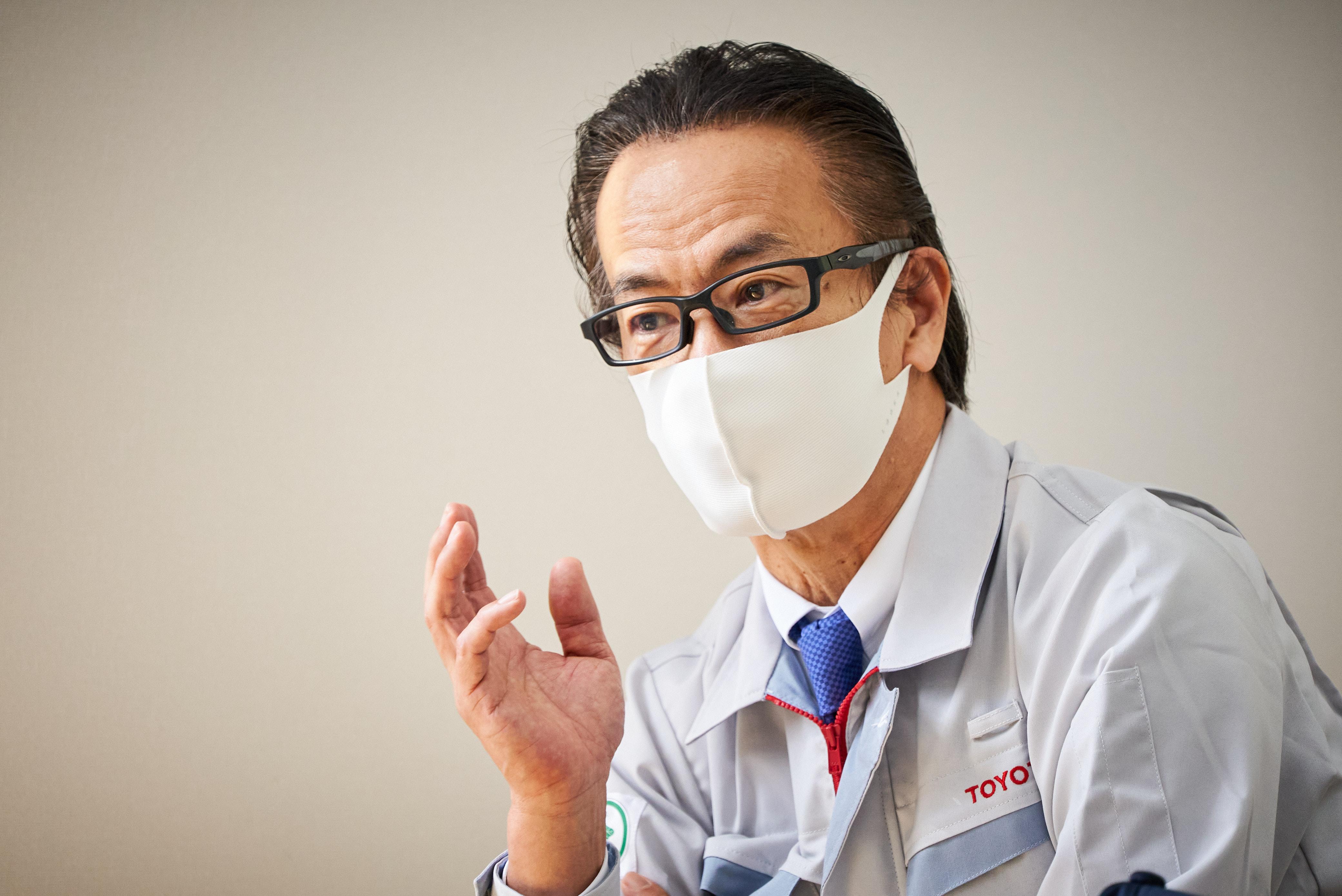
TMEJ has been promoting a variety of learning initiatives through the local governments of six Tohoku prefectures and Niigata Prefecture. They have so far engaged in kaizen activities with a total of 119 companies, as of the end of 2020.
Kamaishi Hikari Foods was one of the first to show interest in taking part in this initiative for mutual learning among companies of different industries.
TPS Dramatically Changes On-site Seafood Processing
In this initiative, two members from the TPS Promotion Department of TMEJ dispatched to engage in each project. They must strive to make the people of the other company realize that “kaizen is fun.”
This is because when they start having fun, it leads to “further kaizen”, so that it does not stop even when the project ends. It results in the firm establishment of kaizen based on TPS.
The launch of this initiative at Kamaishi Hikari Foods is said to have led to dramatic changes on-site. For example, kaizen was made to the procedures even before the processing work starts.
[Before kaizen]
The staff were not told what they would do that day until they arrived at work.
▼
[After kaizen]
Work was assigned on a weekly basis, allowing the staff to confirm their roles on a whiteboard by the entrance.
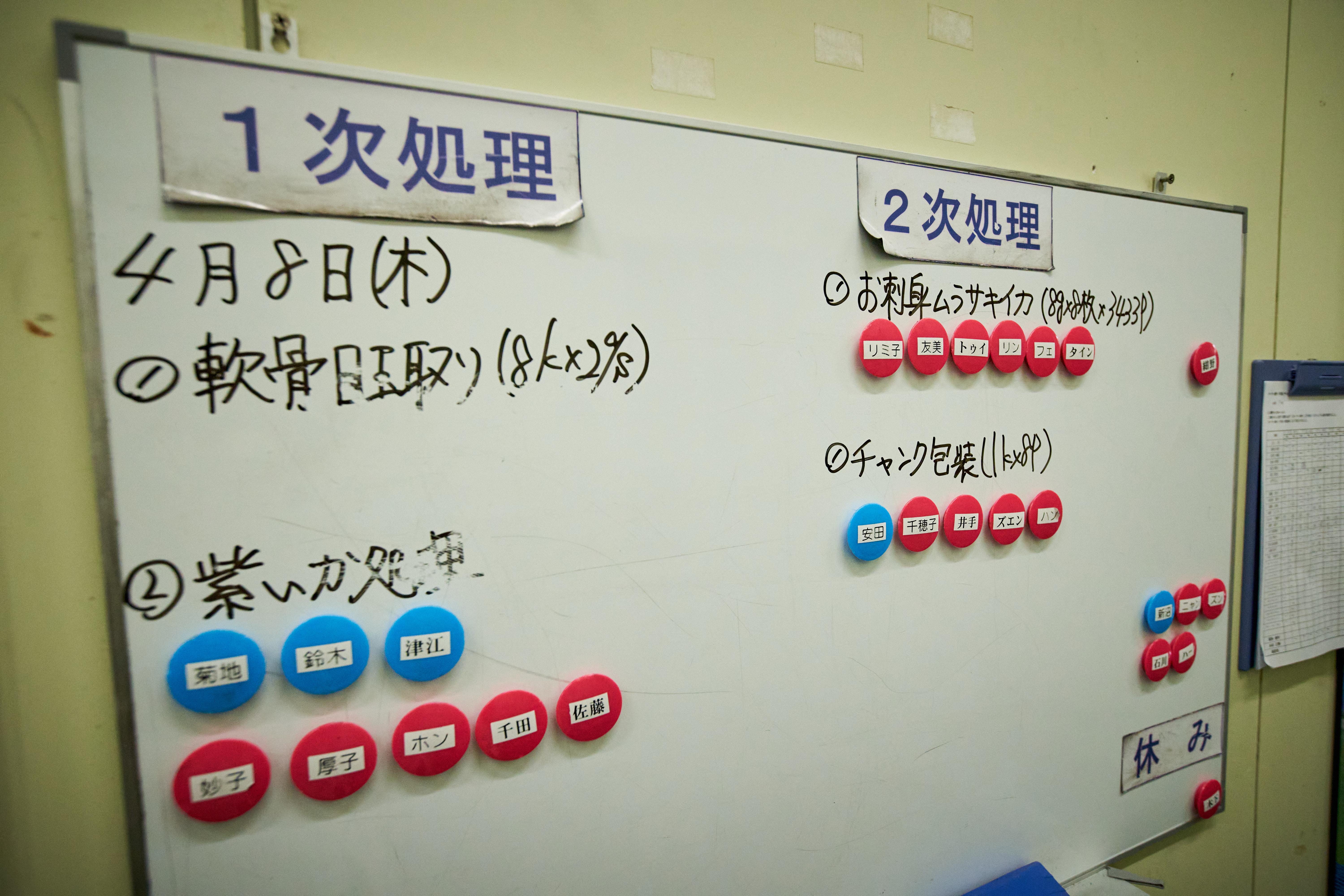
This enabled the visualization of all kinds of information. It not only clarified what each individual had to do, but it also allowed easy ascertainment of the workload on staff.
Every procedure was also standardized by the setting of a standard time required to carry out the work. Furthermore, it prevented “goods in process” being abandoned for completion the following day. This eliminated inconsistencies in quality, as well as extra work in taking out or placing products in the freezer.
[Before kaizen]
Everyone gathered to work in one location.
▼
[After kaizen]
The processes were divided to ensure a one-way flow of products as in a production line.
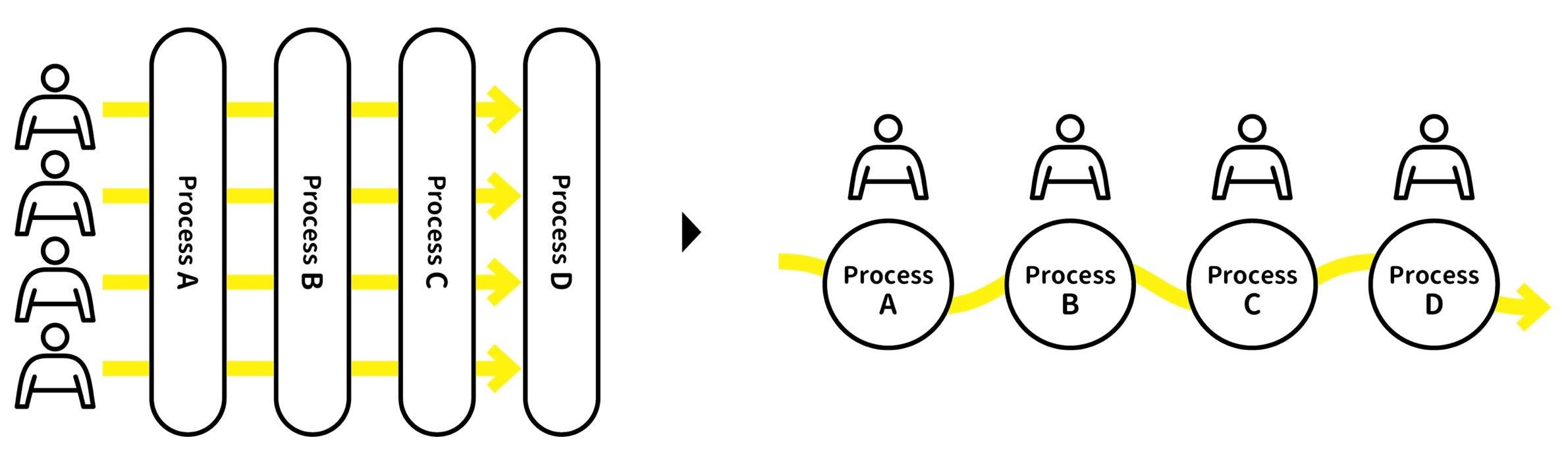
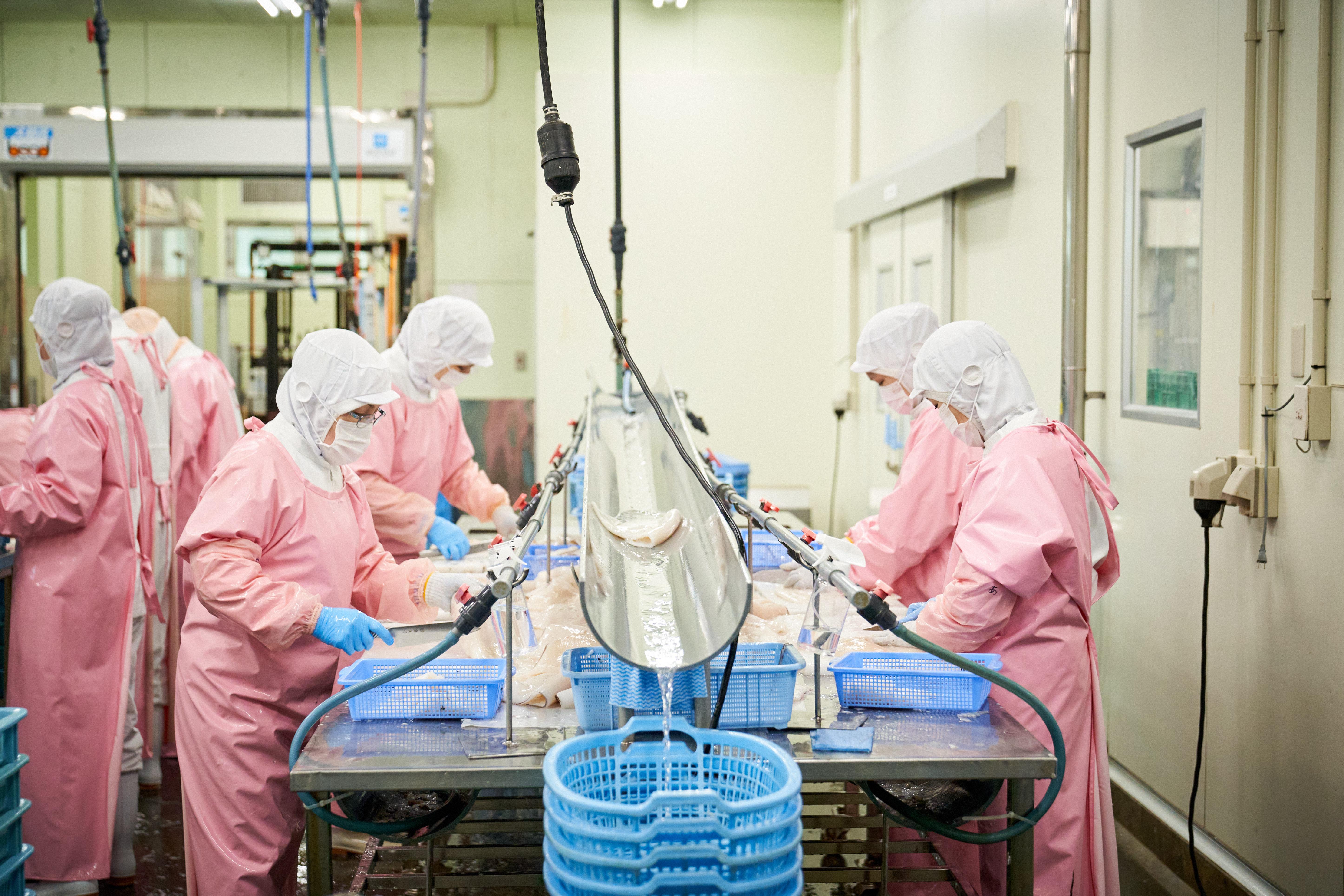
This dramatically increased the amount of products that could be processed. The elimination of waste in transporting products, the setting of quality standards, and carrying out inspections after each process also reduced the rate of defective products. With a total of 51 employees, today, it processes up to three tons of food in a single day.
[Before kaizen]
Power cables were plugged into outlets on the ceiling using stepladders.
▼
[After kaizen]
Extension cords were hung from the ceiling, allowing cables to be plugged in without using stepladders.
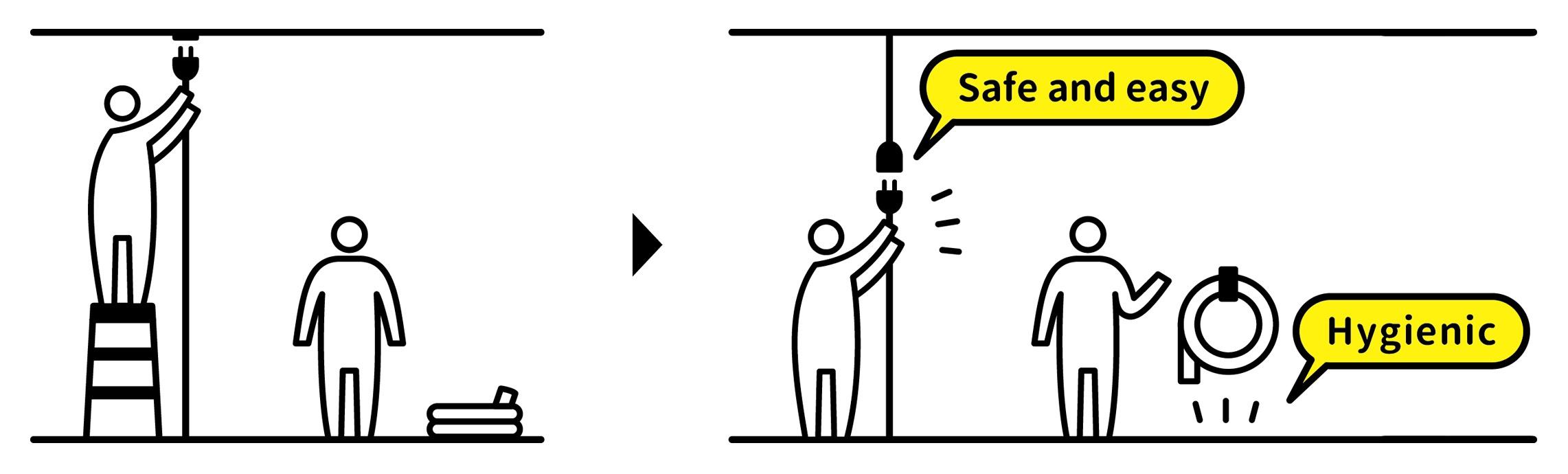
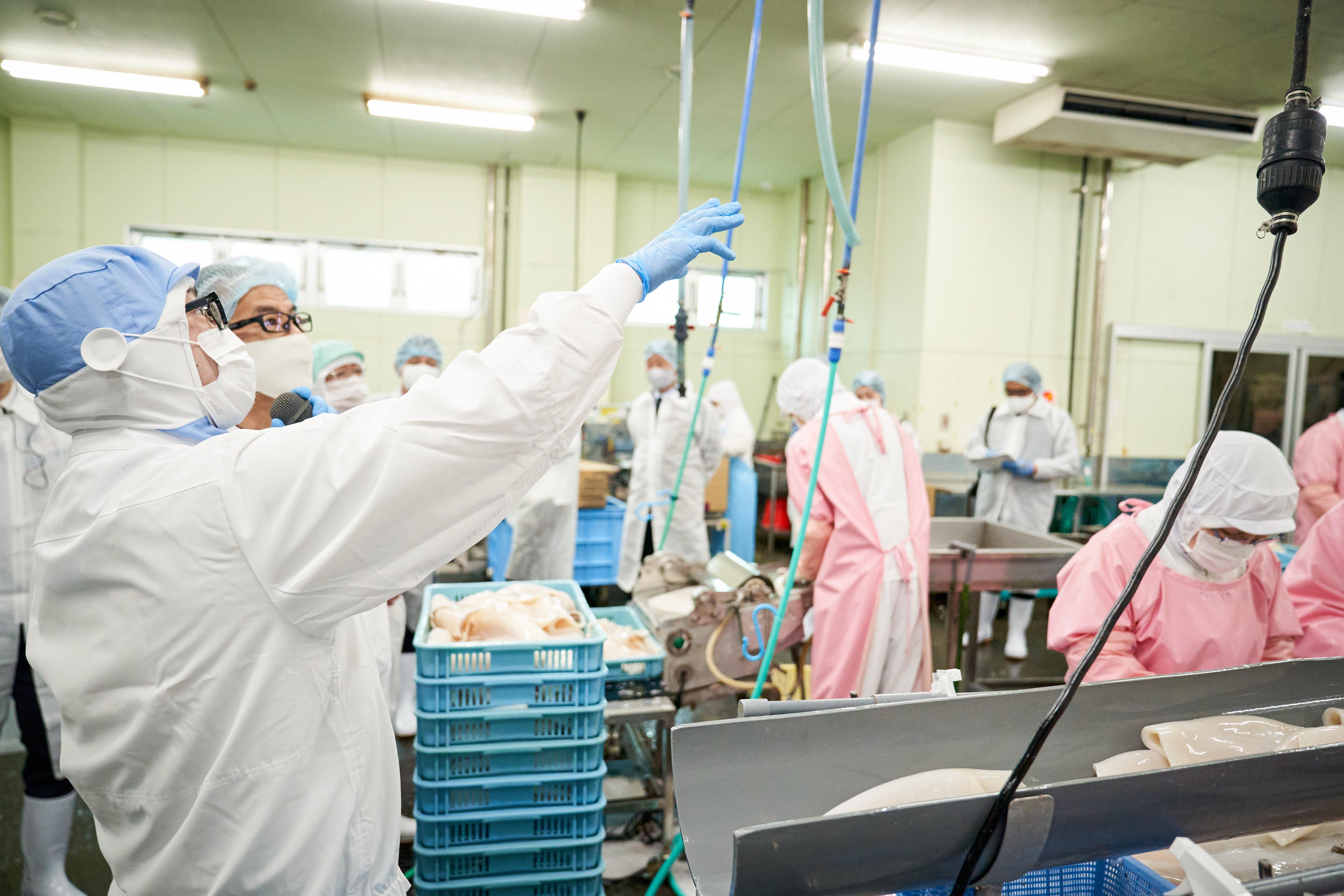
Power cables previously had to be plugged in by using stepladders whenever there was a change in procedures, but with the improvement in how to locate them, they could be plugged in by simply reaching out with hands of the workers. This improved safety by eliminating the need for climbing stepladders placed on the wet floor of a seafood processing factory. Hanging water hoses on the wall, instead of leaving them on the floor, also ensured an uncluttered foot space and eliminated unnecessary movements.
[Before kaizen]
Worked in a silent factory with no background music.
▼
[After kaizen]
Music ranging from the latest J-POP to Japanese enka and Western music is played.
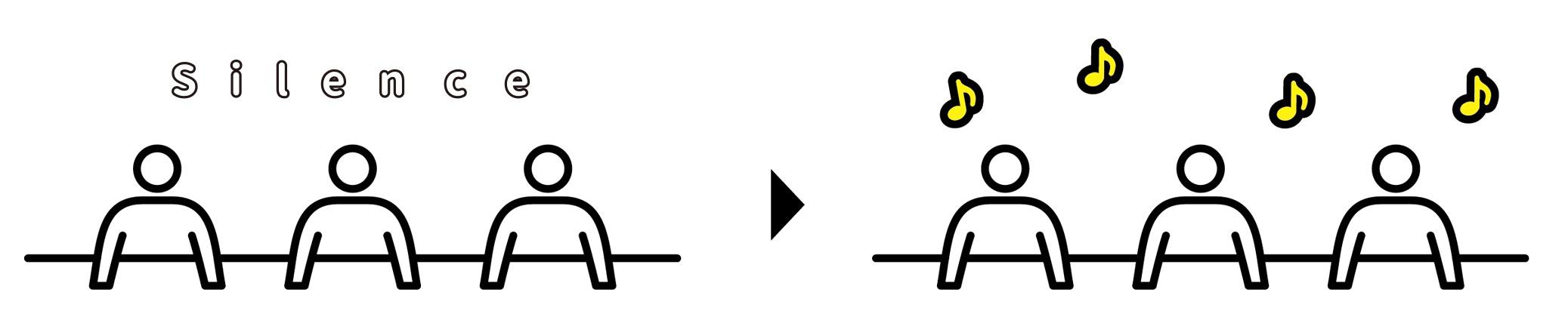
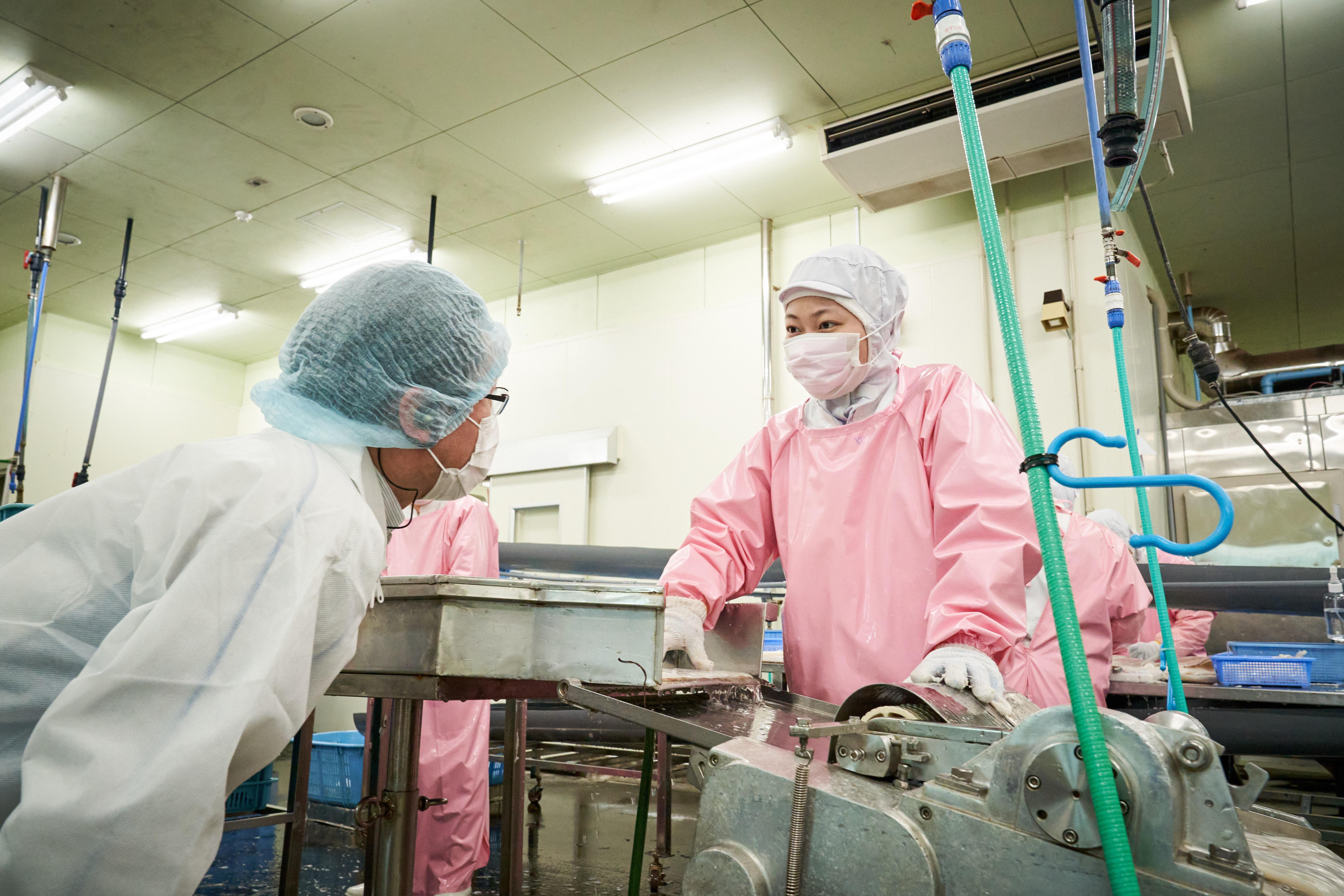
The music was chosen in consideration of the fact that the employees ranged greatly in age from those in their teens to their 70s, and were multinational. Many of the staff also lived in temporary housing, so the background music was changed every day according to their requests to make sure they could relax and enjoy their work. On the day of the visit too, the factory was filled with nostalgic J-POP music. This is an example of the small improvements they have been striving to make at the workplace.
These are only some of the examples, but three changes were observed as the result of implementing TPS according to President Shoichi Sato of Kamaishi Hikari Foods.
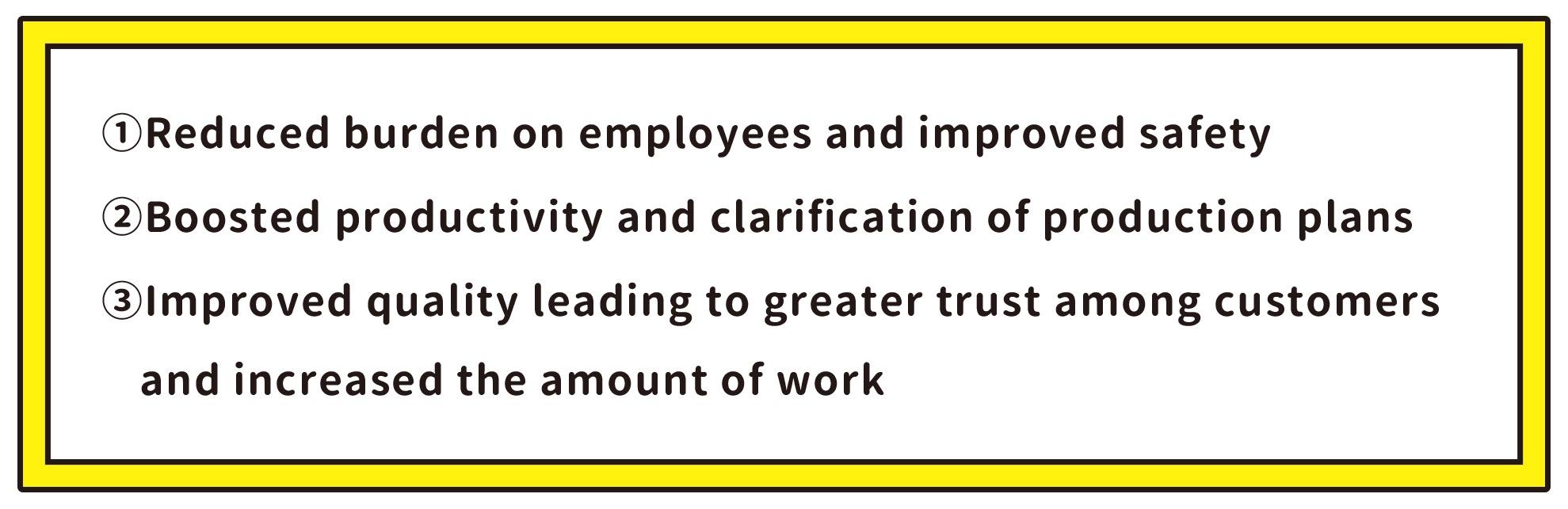

These kaizen activities may not be anything special, but in the seafood industry where priority is placed on experience and skills that are passed down through the generations at genba, employees are often reluctant to make changes for the sake of kaizen.
It was under such circumstances that kaizen through TPS managed to achieve solid results. It also had intangible effects such as greater pride and motivation among employees.
As the work environment improved, on-site staff began taking the initiative to make changes themselves, coming up with numerous ideas on how they wanted to make improvements. The initiative not only streamlined operations, but it also changed the attitudes of staff. Toyota has a slogan that says, “Making things (monozukuri) means making people,” and these episodes testify to this.
This effort in mutual learning with TMEJ began in October 2018, and continued until March 2019. Attitudes at the genba remained unchanged even after the project ended.
The words, “Kaizen, keizoku, doryoku (improve, continue, strive),” displayed throughout Kamaishi Hikari Foods stood out.
Sharing the Common Language of TPS
For some reason, Tomoyama seemed to enjoy himself upon entering the processing factory. Section Manager Mitsuru Shirato of Kamaishi Hikari Foods began explaining the details of their kaizen activities, and Tomoyama was quick to ask him about the boxes of seafood stacked in front of the freezer.
Tomoyama: “Can you tell when these boxes were placed inside the freezer?”
Section Manager Shirato: “Oh, we need kanban for those.”
Boxes containing seafood were being placed inside the freezer after delivery, until it was time to process them. Labeling the boxes with kanban (cards with information on the time of production and information necessary for transportation) to indicate when they were placed inside the freezer allowed the staff to manage the boxes, preventing boxes from being left inside for too long.
Tomoyama noticed this and asked about it, while Shirato understood what he meant and responded immediately. Tomoyama looked pleased as he uttered, “You know what to do.” This conversation alone testified to just how firmly TPS has become established on-site.
After that, Tomoyama continued coming up with numerous new kaizen ideas, offering advice such as, “You should use a (sliding) chute to dispose of the guts,” “Bringing these lines closer together will make the work easier,” “You can streamline operations by deciding how long knives can be used for to maintain their sharpness,” and so on.
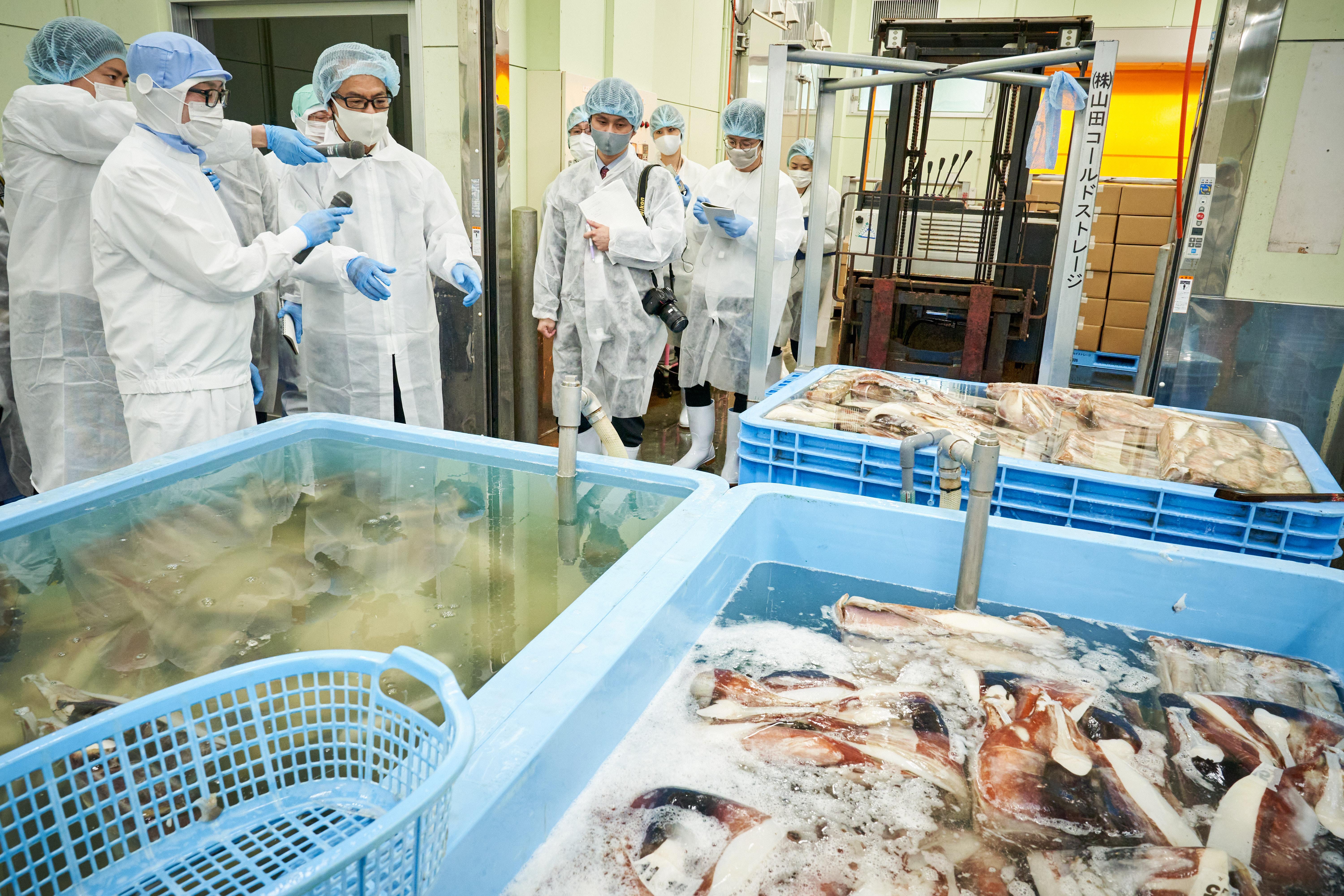
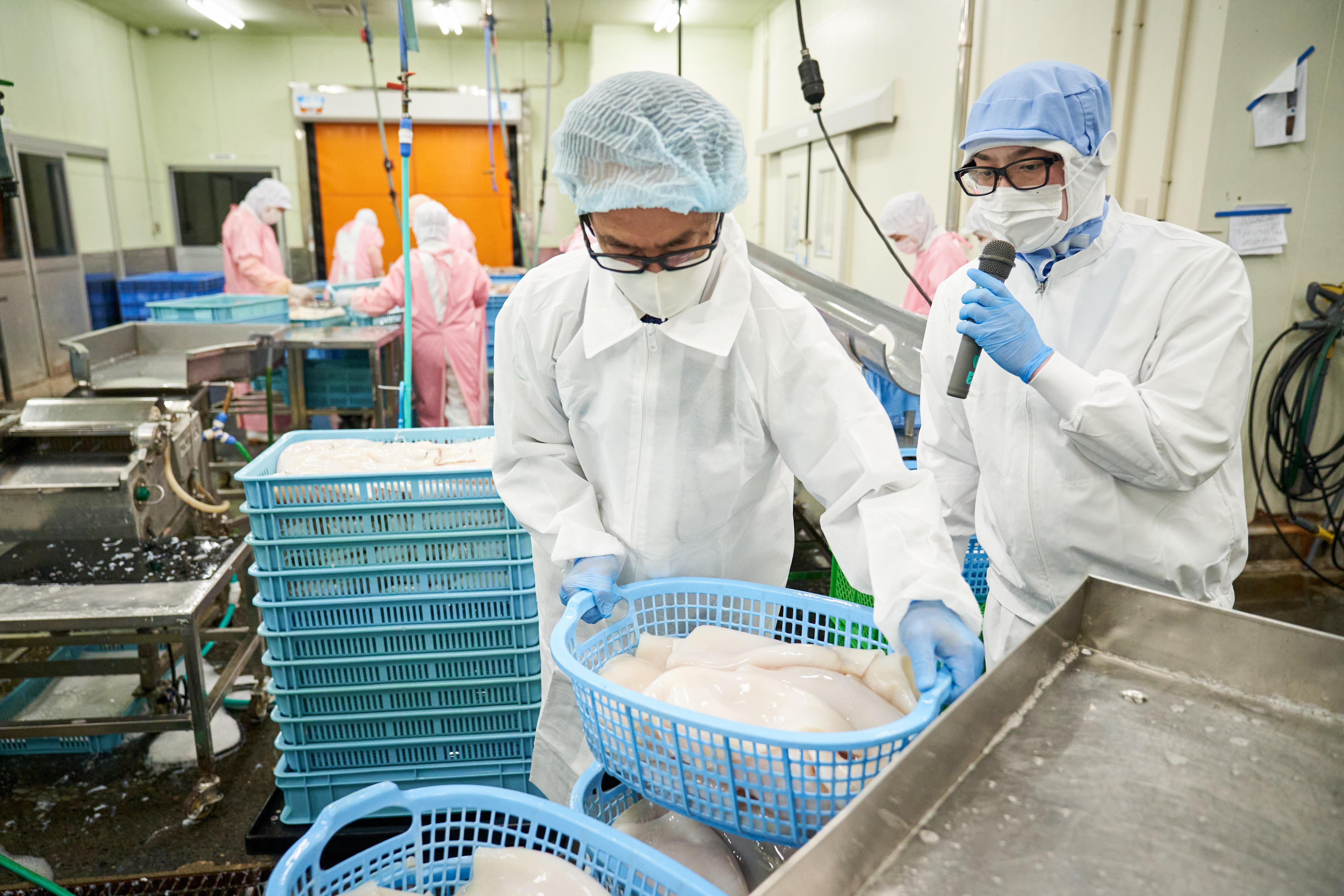
This prompted Sato and Shirato from Kamaishi Hikari Foods to immediately decide which ideas to adopt to their work place. They understand terms somewhat unique to Toyota, such as kanban and karakuri, allowing them to communicate with Tomoyama. It was a true demonstration of “how to make use of on-site knowledge”.
Seafood processing and car manufacturing are completely different industries, but Tomoyama says they are both founded on the same concept of manufacturing. They share the common language of TPS.
The first change that was brought about by adopting TPS, according to Sato, was the lightening of the workload on employees. It seemed he had a good understanding of the main purposes of TPS to “make someone’s work easier” and “give meaning to the work of employees.”
The Difference between the Two Meanings of the Word, Teichaku; “to Become Established” and “to Stop and Settle Down”
After discussing the kaizen situation on-site, Tomoyama said the following:
Tomoyama
“Becoming established” doesn’t mean you continue doing the same thing. Establishment of TPS means you continue identifying on-site problems and making improvements as much as you can. Simply continuing to do the same thing is the other meaning of the word teichaku; to stop and settle down.
Every job involves processes. The quality you aim for at the end of each process determines the quality of the finished product. So, you lay down standard procedures for every process. You do this one step at a time, and it naturally leads to improved quality and productivity.
This not only improves your business, but it also boosts customer satisfaction. TPS can achieve results in not only manufacturing, but also all other jobs.
But the simple deployment of TPS (by anyone) is not enough to achieve results. It’s important to make preparations in advance. This involves identifying the work system, human resources and corporate culture that the company wants to aim for. The system should be as clean as possible (slim with no waste) and allow easy identification of problems. Human resources should have the ability to improve themselves, and the corporate culture should cherish these virtues. This is not something that can be copied easily by other companies, which is why companies that adopt TPS are able to become so competitive.
In the processing of neon flying squid, production efficiency was boosted by around 30 percent as the result of applying TPS. But it was not the end. Adopting the ideas that Tomoyama came up with on this day could improve efficiency by a further 10 percent or so.
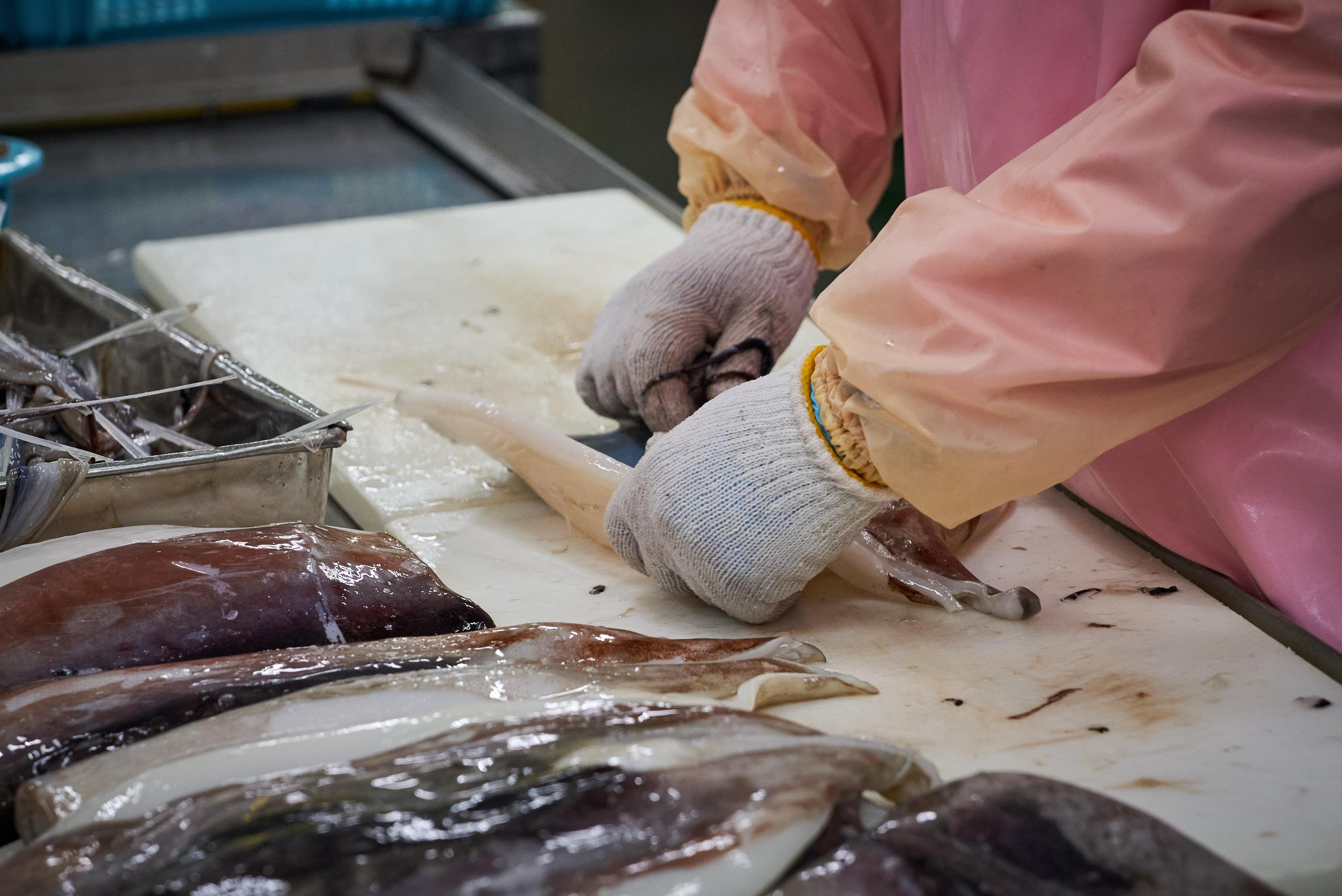
Tomoyama came up with many kaizen ideas and shared them on-site. As often stated in TPS, “After kaizen is the state of before kaizen,” and Tomoyama’s words and actions at the genba exactly represented the thinking that there is no final goal in TPS.
So, why is it that Toyota does not keep TPS to itself, but promotes it among other industries?
Tomoyama
Under Toyota’s philosophy, it is said that “Producing happiness for all” is the corporate mission.
When you think about what happiness is, you realize it’s about making something, having customers use it, or in the case of the seafood industry, having customers eat it, and enjoy it. In other words, this is what makes everyone, including customers and the manufacturer happy.
TPS is an asset that creates a shared sense of value spanning all industries. By promoting the spread of TPS, Toyota will not only contribute to society, but it’s also important for society to feel that Toyota is an indispensable part of it.
Furthermore, to collaborate with other industries as a mobility company, Toyota, unlike IT companies, is able to achieve some form of differentiation by promoting the spread of TPS among other companies. I think that’s why we have to foster human resources through the initiative for mutual learning among companies of different industries.
Group Leader Kudo of the TPS Promotion Department of TMEJ, who is in charge of promoting mutual learning among companies of different industries, had the following comment about how his members have grown:
Group Leader Kudo
People are dispatched to companies in completely unfamiliar industries, so they have to start by building their partners’ trust. You watch experienced members, and see how much they’ve honed their skills in motivating others to get involved. Before, they may have tried to do everything on their own, but they learn to take the initiative in approaching and consulting with other unfamiliar departments in carrying out their work.
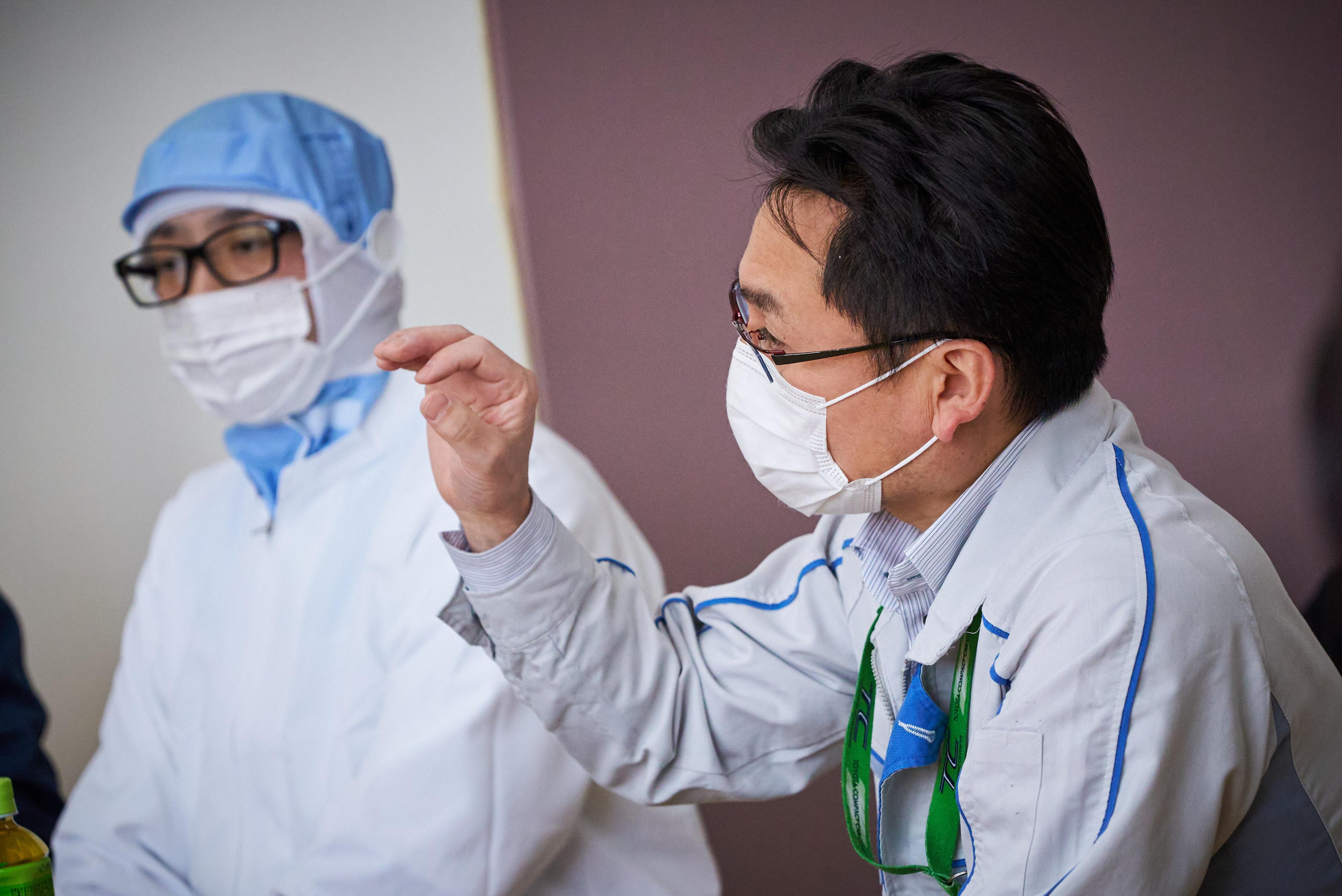
In response to this, Tomoyama says, “That’s how dangerous it is to foster people only within Toyota.” The team of reporters broke out in laughter over this, and Tomoyama continued:
Tomoyama
For most of office staffs, they join Toyota after graduating good universities. Some of them tend to somewhat be arrogant or think they know better than others. So, it’s important for them to experience a workplace where the Toyota brand has no meaning. We have to foster such human resources (by dispatching them to companies of different industries), or Toyota won’t survive in the future when it becomes more than just a car manufacturer.
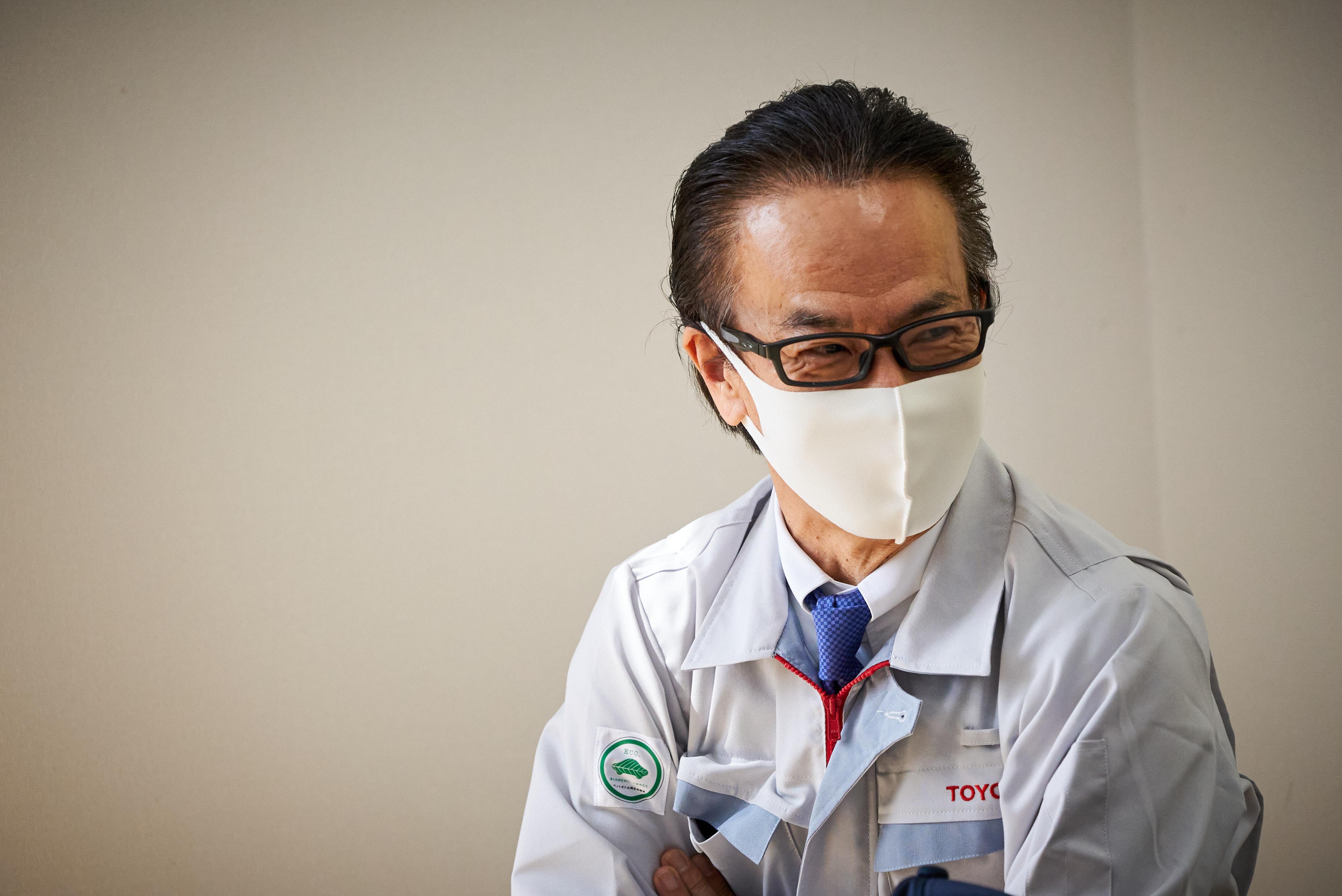
This further clarified the aims of the initiative for mutual learning among companies of different industries. At first, some may wonder why the promotion of TPS among other companies was a “mutual” learning experience. But it was actually Toyota that was acquiring important skills needed to collaborate with companies of different industries.
Shirato of Kamaishi Hikari Foods was grateful that the employees of TMEJ involved in the learning initiative did not try to impose their methods on his company, but showed understanding for everyone while working alongside them.
Tomoyama wrapped up by asserting, “Colleagues are naturally drawn to people who strive to do something for others.”
Turning TPS into a Driving Force behind Manufacturing in the Tohoku Region
Kamaishi Hikari Foods was named after their desire to not only restore the disaster-stricken seafood industry of Kamaishi, but make it thrive, offering a ray of hope in the restoration efforts (as Hikari means light and hope in Japanese).
At the time the company was founded in 2011, everything from finding land for the factory to gathering funds and staff was an uphill struggle. But they have now reached a stage where they receive orders from large izakaya (Japanese pubs) and revolving sushi bar chains. Kaizen made in small increments through TPS has grown to give them great competitiveness.
President Sato says, “I want to offer the people of Kamaishi peace of mind through the seafood industry, as well as economic security, so everyone can feel proud of the local community. That’s what will lead to restoration of the town. I want to change people’s preconceptions of the seafood industry as being heavy work that stinks of fish.”
During the visit, it was highly notable that immediately after arriving on-site, Tomoyama talked about the lead time, from receiving an order to delivering products and services, as being critical to “freshness”. In the seafood processing industry, shortening the lead time in each process ensures greater freshness, which in turn ensures greater added value. This directly showed the relevance of TPS to this industry.
As with our previous, report on Kuzumaki Town of Iwate Prefecture, Sato also had a strong desire to “solve challenges” and “do something to help others.” This resonated with the Toyota Group’s attitude of involvement.
Toyota Times had reported on the power of automobile manufacturing cultivated after the earthquake in Tohoku, and this time, even in a different industry, there was something similar. The spread of recovery efforts, and the universal nature of TPS were evident in the small seafood processing company.
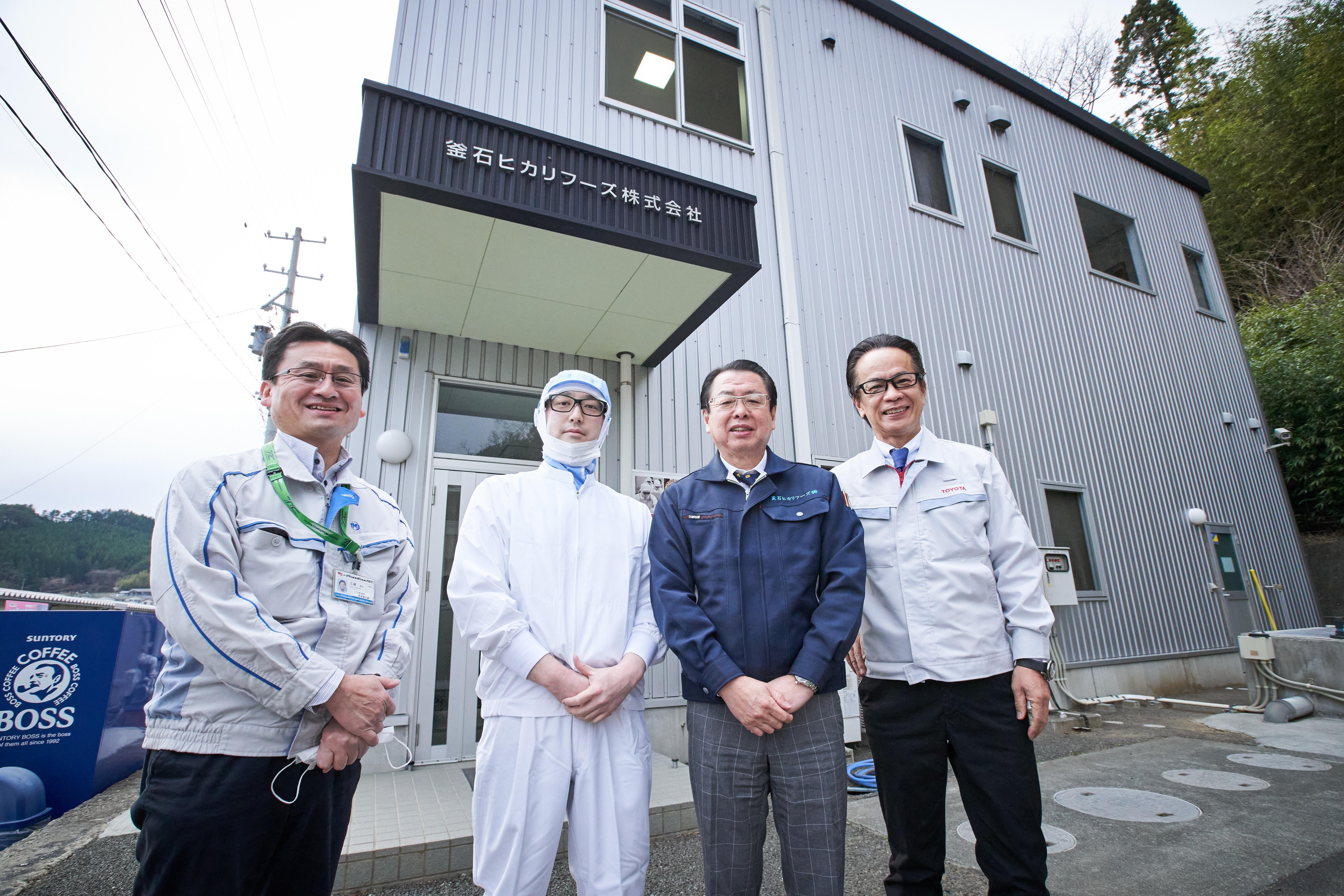