
A week before the 10th anniversary of the Great East Japan Earthquake , Akio paid a visit to the Tohoku region. New Toyota Times reporter Kyonosuke Morita, who was given the chance of close coverage, describes Akio's actions and words there.

Ten years have passed since the ground shook like never before. Immediately after the Great East Japan Earthquake, Akio Toyoda made an enormous, long-span decision to support the reconstruction of the devastated Tohoku region.
The announcement came in July 2011, only four months after the earthquake: the three companies of Kanto Auto Works, Central Motor, and Toyota Motor Tohoku would merge to form Toyota Motor East Japan (TMEJ) in 2012 and turn Tohoku into Toyota’s third domestic production base following Chubu (Central Japan) and Kyushu.
Two years later, in 2013, TMEJ opened the in-house Toyota East Japan Technical Skills Academy, which has been supporting the growth of human resources who play a central role in manufacturing in the Tohoku region.
By making full use of the power of the workplace, its skilled workforce, and technological leadership hitherto cultivated, Toyota was quick to raise the banner of “non-temporary reconstruction support” in the form of building Tohoku industry, creating employment and supply chains, and paying local taxes.
Against this backdrop, Akio has visited the disaster-stricken areas of Tohoku every year.
On March 4 of the milestone year of 2021, Akio visited Miyagi Ohira Plant of TMEJ, which has continued to grow as Toyota’s third domestic production base, and Miyagi Plant of Primearth EV Energy (PEVE), a hybrid battery manufacturer and Toyota subsidiary. How does Akio look back on the road to reconstruction so far?
Kyonosuke Morita, a new Toyota Times reporter who recently joined Toyota mid-career, closely followed Akio on his latest visit to Tohoku. So, let’s start this report with a self-introduction by reporter Morita.
New Toyota Times reporter Kyonosuke Morita
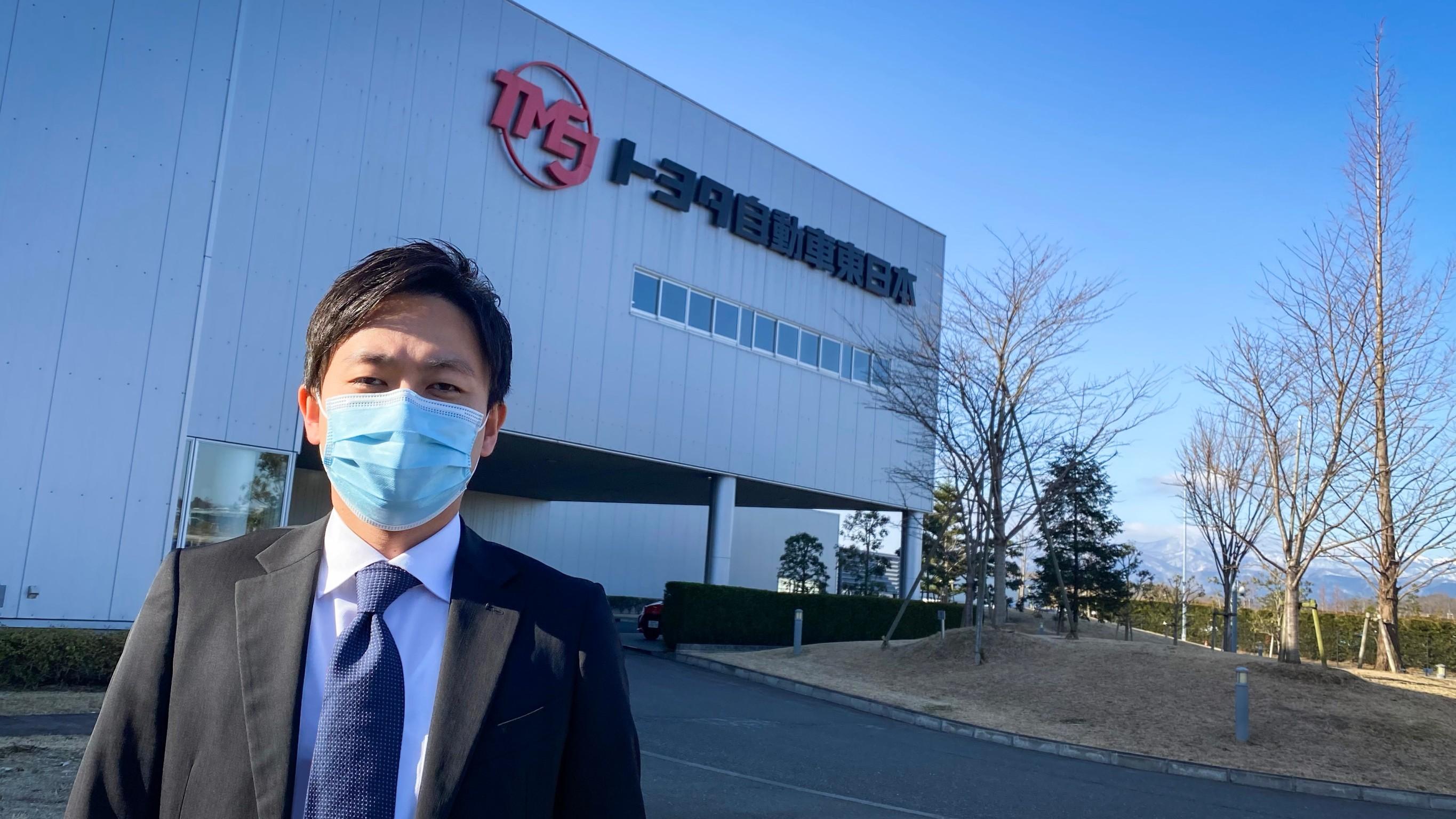
Until last year, I had worked at a TV station in Tokyo. While working as a newscaster for business news programs, during my times reporting from the field, I could keenly sense the influence Toyota has in Japan and abroad.
That was one of the reasons I wanted to work for Toyota. I decided to change jobs, and from this year I actually started working at Toyota.
At this milestone of the 10th anniversary of the earthquake, I wanted to see with my own eyes the role Toyota has been playing in the reconstruction of Tohoku, and I was able to accompany Akio this time.
I had imagined that—under the headwinds of production activities not going as liked due to the earthquake, coupled with a strong-yen economic slump—it was not easy at the time to decide to raise the call for reconstruction support in the form of strengthening Toyota’s system of domestic production bases.
I will report on how Akio, who made the decision to provide long-term support, looks at and looks back on the Tohoku region now that 10 years have passed. I will also report on what I felt during my reporting trip.
Akio’s inspection style: Going to where the action takes place to hear about problems first-hand
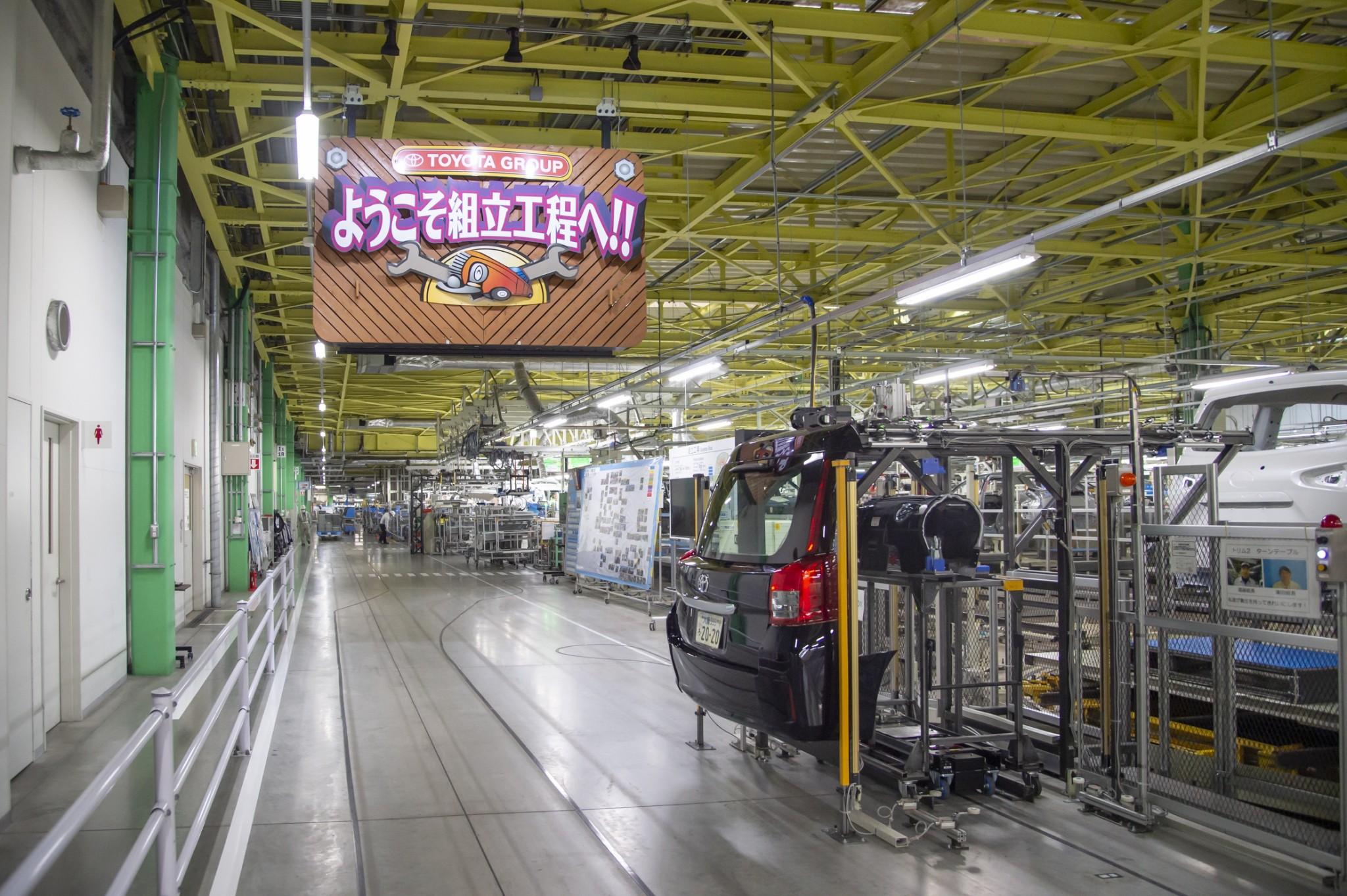
On this trip, Akio’s first stop was TMEJ’s Miyagi Ohira Plant. He visited vehicle assembly processes and where production equipment is developed.
Ten years after the earthquake, TMEJ has grown into a major base for the production of compact cars, including the Yaris, which won the European Car of the Year 2021 award.
The number of TMEJ employees in the Tohoku region has increased from 3,100 (in 2010) to 4,500 (in 2019), and the shipment value of its products has increased from 30 billion yen (in 2011) to 800 billion yen (in 2019) (including expansion due to the integration of the three companies mentioned above).
Along with this, the number of related suppliers and their employees has steadily increased.
Also, many teams transferred from TMEJ’s Higashi-Fuji Plant (in Susono City, Shizuoka Prefecture), which closed in 2020, are working at Miyagi Ohira Plant. Speaking of Higashi-Fuji Plant, that is where Woven City is being built, which Toyota Times reported on the other day.
At Miyagi Ohira Plant, Akio stopped to talk to a team member who had transferred from Higashi-Fuji. That is what Akio does—when visiting a plant, he usually suddenly calls out to people he meets on site.
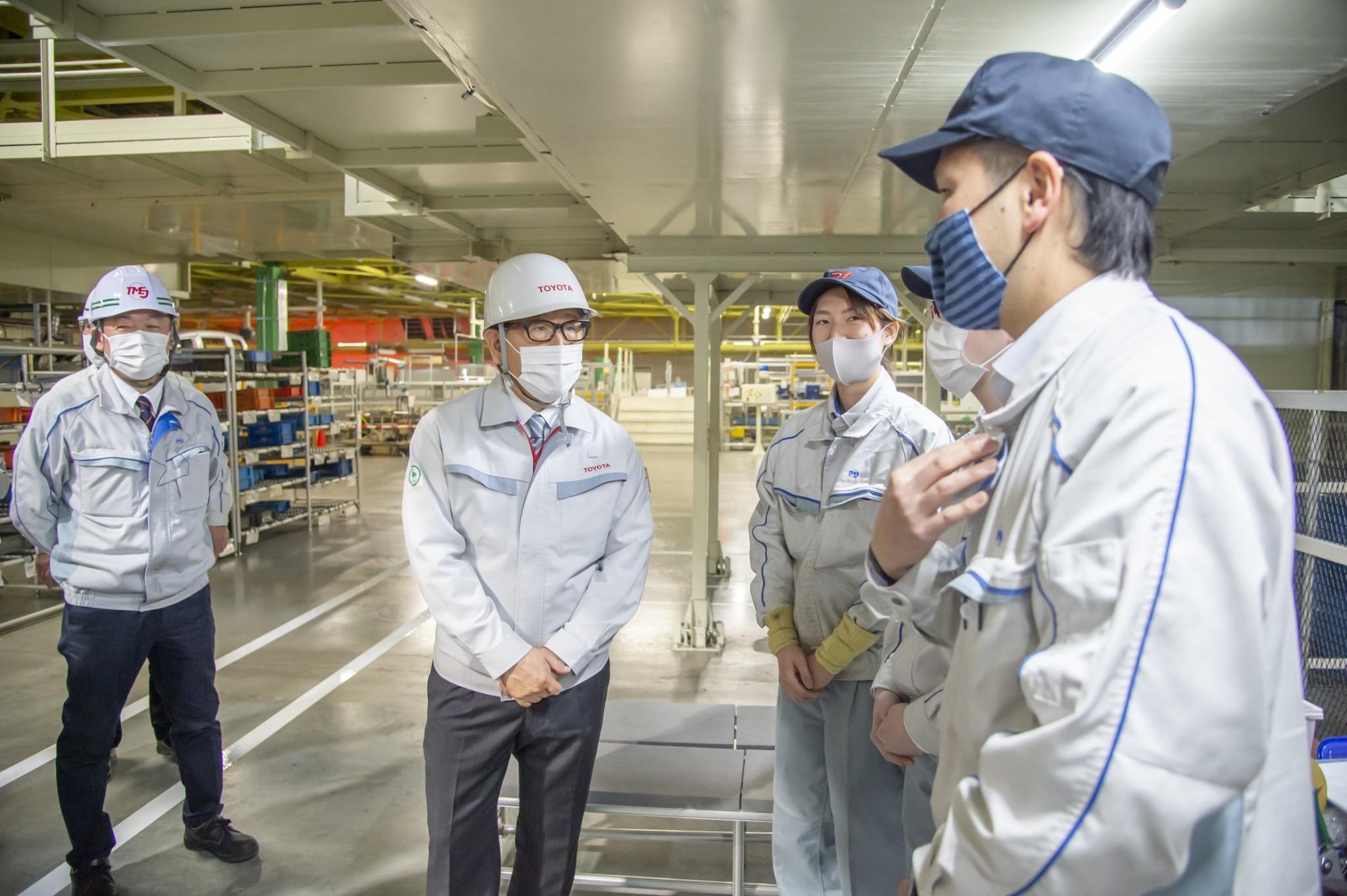
Akio seemed to breathe a sigh of relief when the team member said: “I'm finally getting used to life in Tohoku.”
Every time he called out to team members, Akio not only asked about their work but also checked on their families’ situations. Through such conversations, it seemed that Akio was able to feel that the people who were at the center of the enormous decision he made were truly walking forward and that the smiles they showed were reassuring to him.
Also, accompanying Akio on this day was Toyota Motor Executive Fellow Mitsuru Kawai, who had worked his way up throughout his career and now has the title of “Oyaji”, or “Old Man”.
If you’re with “Oyaji Kawai”, who knows the production worksite inside and out, nothing can be hidden. "That’s why I’m able to hear what the problems really are,” said Akio, explaining the significance of having an “old man” by his side.
“I don’t want to miss the chance to hear what the worksite is having trouble with,” said Akio. Hearing that, I was able to understand Akio’s inspection style, which is to make such visits a time for being close to worksites rather than a time in which worksites become nervous or stiff.
Innovating manufacturing using equipment that can be fixed rather than equipment that should not be broken
At the production equipment development site, members were developing robots for use in their own plant. In fact, doing so represents both the originality and strength of Miyagi Ohira Plant.
Akio seemed to observe with great interest the evaluation process of a small robot the members were developing on their own.
During the inspection, Akio and Kawai had the following exchange about the in-house making of robots.
Kawai: Since they make it themselves, they can fix it themselves even if the equipment breaks. And that gives you a chance to make it better (and allows you to keep on improving it).
Akio: That’s right. And that’s how to gain competitiveness.
This exchange about the merits of in-house robot production made me sense that such was one of Tohoku’s manufacturing strengths.
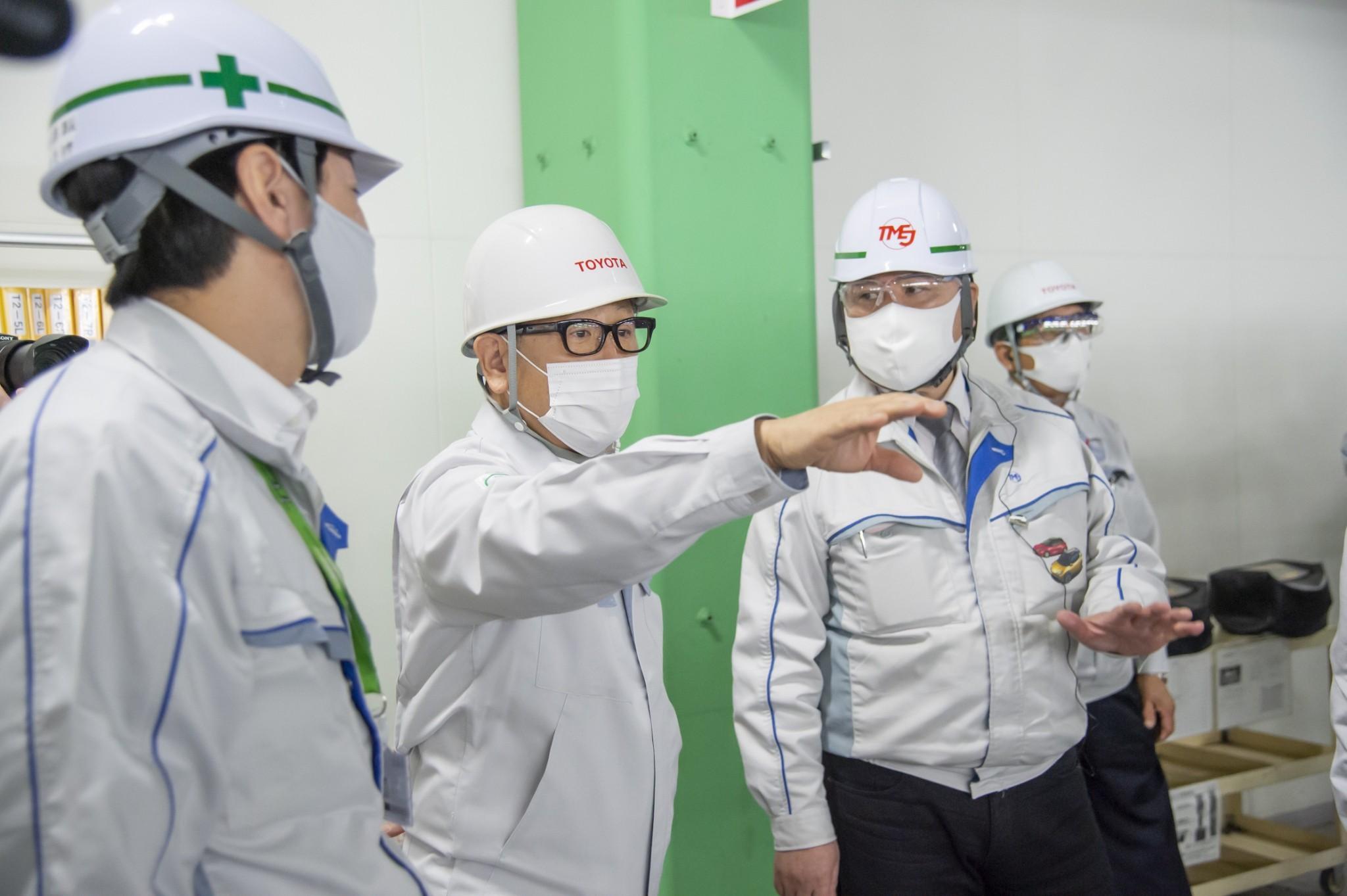
What has taken hold in the decade since the automotive industry planted roots in the disaster area and Tohoku
After inspecting TMEJ’s Miyagi Ohira Plant, while looking back on the past 10 years, Akio spoke in front of accompanying reporters about the Yaris’s successful big leap from Tohoku after the earthquake disaster.
Akio:
At the time of the earthquake, we had no way to handle it, making me feel just how little we human beings are.
It’s not easy to approach the deep sorrow felt by those who were direct victims. That’s why I have always thought that what is important is to not forget.
Our wish has been that developing the automobile industry in the Tohoku region would give victims hope. As it has turned out, the shipment value of TMEJ increased to 800 billion yen, and we were able to steadily increase employment and the number of related suppliers.
And, the other day, the Yaris was chosen as the European Car of the Year for 2021. We are confident that the competitiveness that Tohoku has built up has been rightly evaluated in Europe, which is the main battlefield for compact cars.
Also, 80 percent of the cars manufactured in Tohoku are electrified vehicles. I believe that it is this Tohoku region that has driven the electrification of automobiles.
Creating together in Tohoku a future that shifts to electrification
Next, Akio visited Miyagi Plant of PEVE, which is the world leader in hybrid battery output.

With the electrification of automobiles having gained much attention over the past several years, it is significant that Akio chose PEVE as one of his Tohoku destinations. That is because PEVE is an important base not only for reconstruction after the Great East Japan Earthquake but also for surviving the challenges of the profound changes that lie just one step ahead.
Electrified vehicles account for 80 percent of all vehicles made in Tohoku. It seemed that, in addition to expressing gratitude as from before, this visit included expectations for the future.
Another reason for the visit was that in February this year the inside of the plant was flooded after pipes were damaged by an earthquake with a seismic intensity of weak five (on the Japanese scale of zero to seven). The temblor was thought to be an aftershock of the earthquake of 10 years ago.
However, based on the experience of 10 years ago, the site had strengthened its disaster countermeasures. Fortunately, thanks to the hard work of those at the site, recovery was completed in about one week.
Akio went around the plant and its office building, cafeteria, and others, actively talking with employees. At the same time, while surveying the pipes that had been damaged, he listened to stories about power outages and electrical leaks that occurred during recovery efforts.
Those working at the site said that, in a single-hearted effort to “never cause our customers any inconvenience”, it took a week to sort by hand the batteries that got wet and those that did not.
With an intent to encourage and a sense of gratitude, Akio began talking to the plant team members who worked hard at recovery.
Over these past 10 years, everyone’s efforts and hard work have enabled you to build up the ability to increase productivity with your current people and production lines.
Once again, I would like to thank everyone for their 10 years of hard work. During those 10 years, the automobile market also greatly accelerated toward electrification.
The electrification rate of cars produced in Tohoku has exceeded 80 percent, and the number of battery plants that form the core of this has increased from only one at the time to seven. I think this is because you have felt that you are on the front line.
Toward the realization of carbon neutrality in 2050, even though electrification might step on the accelerator, it will never step on the brakes.
Toyota and one other company are the only companies in the world to produce batteries in-house. It’s hard going it alone, but we can improve what we make and make it better.
We hope that Primearth EV Energy and Toyota will continue to work as one to take on the once-in-a-century profound transformation that stands before us.
I have visited Tohoku every year to never forget what took place 10 years ago. As a new start following the 10th year, I hope that you will again join us in creating the future together in Miyagi.

The understanding gained by visiting Tohoku every year
At the end of my close-coverage newsgathering at both plants that day, I was finally able to ask Akio a question.
Reporter Morita: You visit Tohoku every year. What have you learned and noticed by visiting every year without fail?
Akio: What I’ve learned after keeping an eye on the situation for 10 years… What they’re doing at the worksites is nothing showy. The ongoings are ordinary and plain, but by continuing to do what they’re doing, their actions become extraordinary.
That’s also reflected in the data (such as growth in shipment value), but such is no more than only the results. Those results depended on the people working here who achieved them.
Today, I had many opportunities to talk at worksites. No matter which worksite I was at, my final words were always: "Please lend me a hand."
Toyota Motor Corporation can accomplish nothing on its own.
However, for these 10 years, I have thought that one plus one would not necessarily come to two but could possibly become a three or four if we worked hard together with our friends of this area starting from a difficult situation. With such expectations, I visit Tohoku every year.
Looking at it the other way around, I need to make sure that I, myself, am doing my best so that I am worthy of coming to Tohoku every year.
If not, I’d be told: "What did you come here to do? We’re busy. Don’t bother us!" I don’t think I’d be accepted if I became like that.
And I want the Tohoku worksites to continue to do the ordinary and turn it into the extraordinary. I think this kind of thing is important, and I want many people to understand it.
For that, I place my expectations on Toyota Times.
About the significance of Akio’s words to those working at Tohoku worksites and of his continuing to visit every year without fail… It seemed to me that his words and actions in Tohoku were connected as a message for the future.
The speed of recovery from the big earthquake that struck in February in the run-up to the 10-year milestone showed that worksites had become stronger over the last 10 years. Rather than just moving from minus territory back up to zero, the situation had been raised to the realm of the positive.
The fact that the Tohoku region has grown into a major production base for compact cars, for which competitiveness is a must, is also significant in terms of creating the future together with the people of Tohoku through continued manufacturing.
This enabled me to feel the significance of Toyota’s “non-temporary reconstruction support”.
With each year’s visit, while looking back on the past, Akio at the same time looks forward little by little. Tohoku, where reconstruction is constantly progressing, may seem to have undergone big changes if you look back using a 10-year interval.
But for Akio, who has been visiting every year to keep an eye on the situation, I imagine that the achievement is one of an accumulation of steady continuous improvements and does not seem like something over the top.
In Part 2 of this article, I would like to deliver a report on Fukushima, which I visited as a place that embodies the spirit of another message that Akio has been sending since the earthquake of 10 years ago: “I want to make Tohoku a place that will drive forward the future of Japan.”
(Continued in Part 2.)